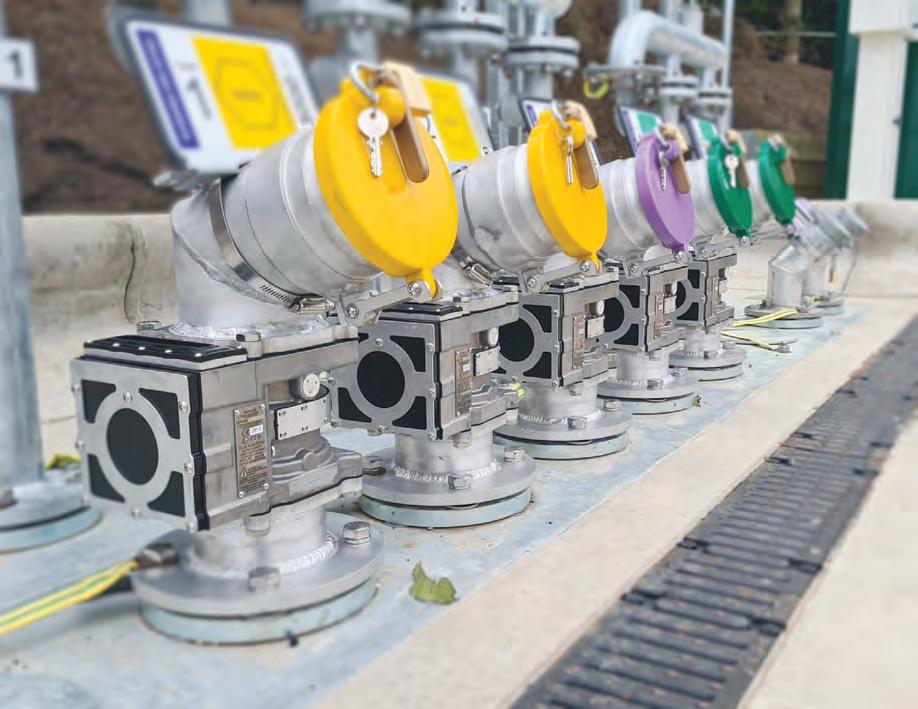
6 minute read
GRP Storage Tanks - Where Are They Now…?
by apeauk
By Simon Procter, Tanks & Pipeworks Ltd
Over the last twelve months we have been involved with refurbishment work on buried Fibreglass petrol and diesel underground storage tanks and thought fibreglass fuel tanks deserve some focus since they are still in service on many sites 30 years after installation. Like steel tanks they can be cleaned, inspected and up cycled as they provide a sound structural base from which to build the patented FASS-UK “Try-line” leak detection tank lining system.
Advertisement
Fibreglass tanks are a very sound construction. As a designer I like the way that you can almost create any shape and form using fibreglass matting and just add resin and a catalyst which creates an exothermic reaction to harden off the resin and set the shape. The strength, properties and flexibility of the finished product can be designed in by varying the thickness, resin type or glass fibre reinforcement. In the home it is likely that your bath, shower tray, sink and pond liner could be made from glass fibre or similar composite nontoxic material. The toughness of the material is well proven in marine use which include yachts, submersibles, surf boards and water skis. Similar composite products were used in the space programme as an ablative material to take the heat away from the Apollo command module as it scrubbed off its incredible speed during reentry to earth.
Process:
There are processes/methods to make GRP storage tanks. One is to lay up Fibreglass matting and resin inside a mould to the required thickness or number of layers; this is similar to how we, at FASSUK, build our TRI-LINE system using the original tank as the mould whether it is a steel tank or a GRP tank - the finished product on the inside is shiny, squeaky clean and extremely resistant to internal pressure.
The other way GRP tanks can be made is to cast the shape on to a rotating mandrel where a glass fibre filament and the correct amount of resin is added as it is wound in a spiral and built up in layers to the required thickness - as a steel man I would describe the finished product as a cross between a continuous casting and a flow forging.
So, in basic terminology, the glass fibre yarn would be fed off a big cotton reel, through a resin bath to saturate the threads and the thread would feed on to a guide head which moves at a controlled rate back and forth along the rotating mandrel to build up the thickness of the tank. Like everything these days there is likely to be a computer programme behind the process so that every product you produce is a consistent and exact size, shape and mass. I expect the quality control for these products to be very high.

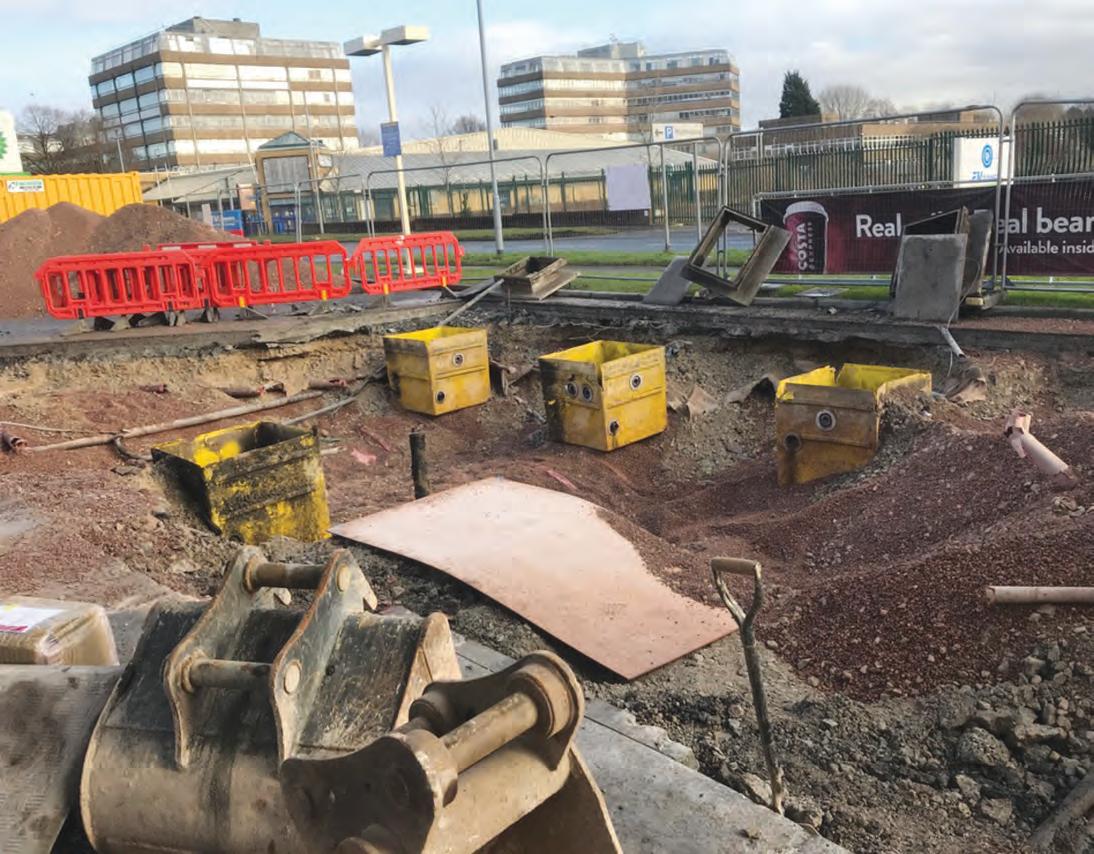

A key difference between steel and Fibreglass petrol tanks is the shapeFibreglass tanks are generally externally ribbed, a bit like vacuum tankers, and they have nicely shaped spherical ends and baffles like a football cut in half. Steel tanks have shallow domed ends and have no external profiles - the bodies have the appearance of a big tube, the properties of the material versus the design scope dictate the final shape of the product.
Performance:
The performance of any tank depends on the standard of construction and the materials that you use. For buried steel tanks the UK and European standard is BS EN 12285-1 which is a very comprehensive build plan that any steel fabricator can use with the caveat that this is a harmonised standard used across Europe so you build to the standard without deviation. The idea is that you can purchase a tank to this standard from any participating country and it should be exactly the same. For performance you have to consider corrosion rates on the inside versus how aggressive the stored product is going to be in contact with the steel. You are permitted to add internal coatings which would give additional corrosion resistance over time.

The outside of a steel tank is corrosion protected and if double walled then generally dried air pressure or vacuum leak detection systems are used to monitor for any leaks on new tanks.
As a comparison there are many single walled Fibreglass petrol tanks still in use and there were also double walled fibreglass petrol tanks developed that generally use vacuum leak detection systems; at FASS-UK we use vacuum leak detection for our TRI-LINE system.
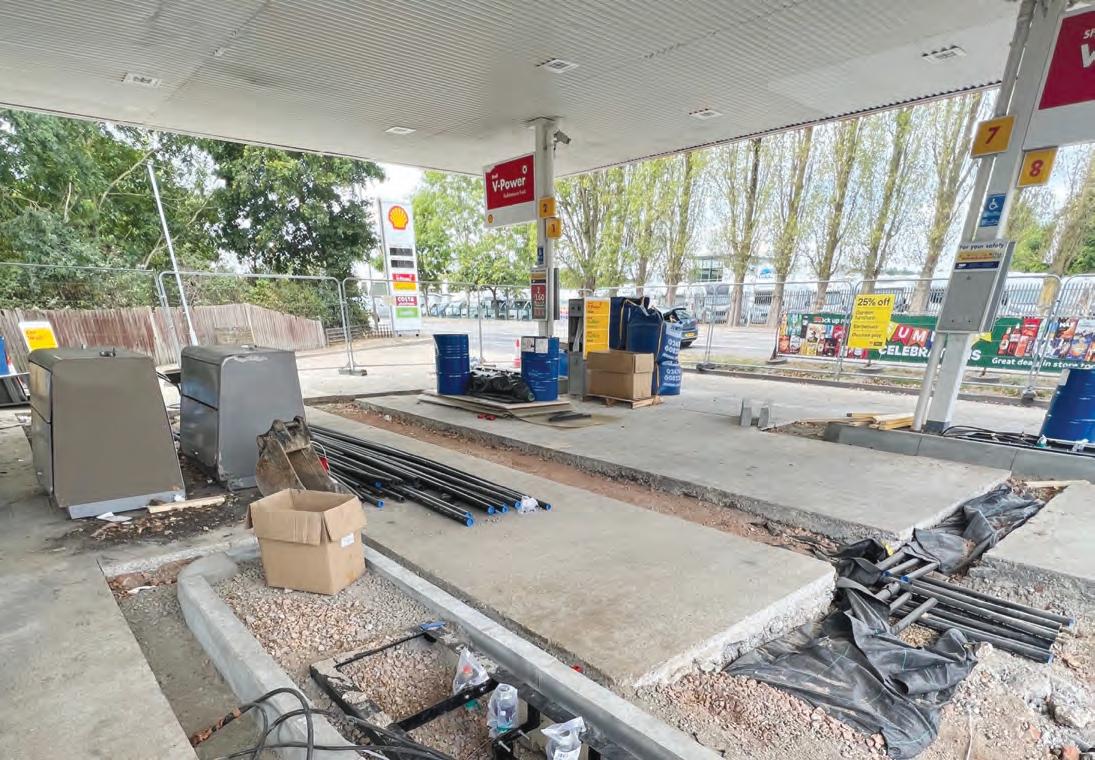
On a recent Fibreglass tank ‘up cycle’ our site team discovered that a double walled fibreglass tank had been glycol filled using the old-style steel tank liquid leak detection system. Our team pumped out the liquid before installing the TRI-LINE installing the TRI-LINE with our vacuum monitoring system. When working on old tank farms there can always be something odd that you have not commonly discovered.
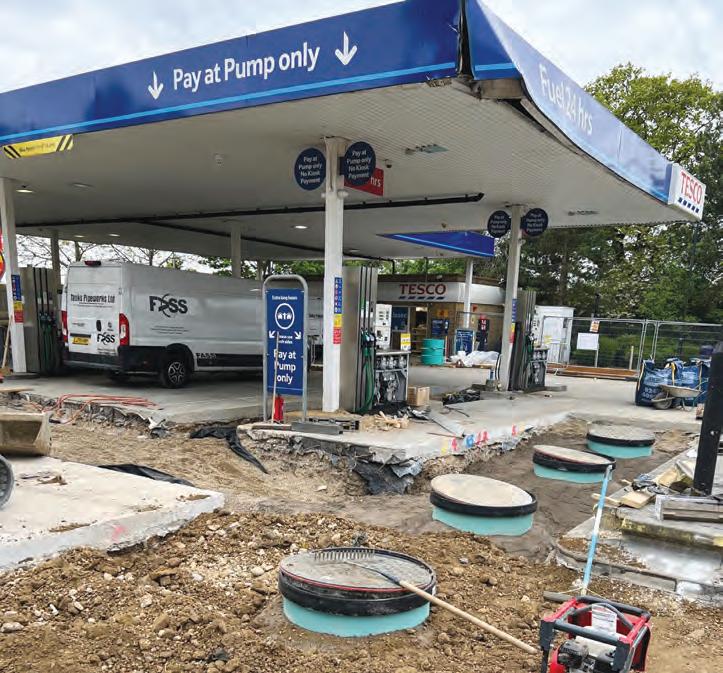
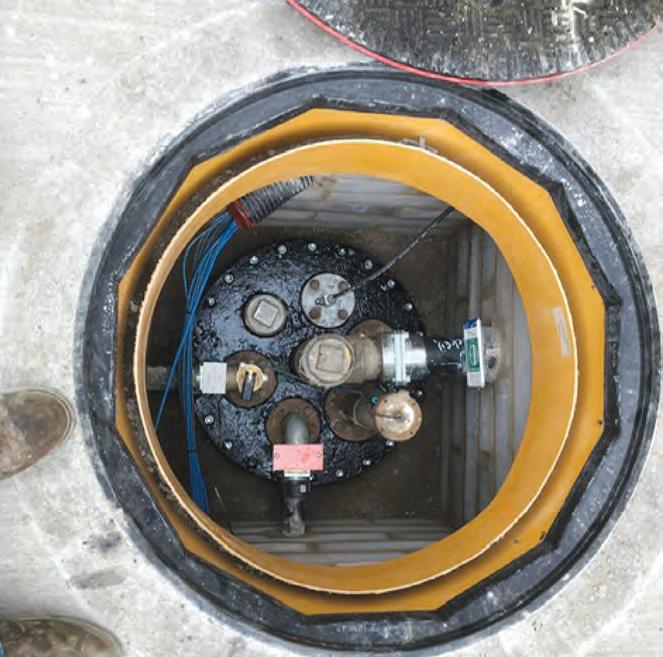
When using Fibreglass products corrosion is never going to be a consideration, we are more interested in chemical resistance. The chemical resistance stands and falls on the quality of resin that is used. America has been using Ethanol based fuels for a lot longer than the UK so many of the Fibreglass petrol tank products and processes are generally under licence from American manufacturers who have many years of experience to sell on.
As a young technician working at Joseph Ash one of my responsibilities was to design and build vats for the pre dipping pickling processes within the galvanizing process. So, we built open topped externally stiffened steel vats which could be 15M long x 1.5M wide x 2.5M deep as an example and these vats held hydrochloric acid which was used to strip the mill scale from steel products prior to hot dip galvanizing. We needed a tough material to line these vats with a high chemical resistance so we successfully used fibreglass linings which layered up to a decent thickness resisted the knocks from the steel beams and maintenance to the lining could easily be carried out.
Articles
From a tank manufacturer’s perspective in the late 1980s and early 1990s when fibreglass petrol tanks appeared as direct competition to our steel tanks and having prior knowledge of successfully using fibreglass to create composite tanks, we thought they would start to corner the market for filling station tank farms. This has not happened and looking back there was some market share between steel and fibreglass tanks for a period of time. I think generally now the trend is to install steel double walled tanks for new petrol filling station tank farms. Back in the day Fibreglass was very high-end technology versus steel which was a relatively cheap and easy to fabricate. We always used to say you can build a steel tank with a barn and a welding set (many steel tank manufacturers started out in large engineering sheds and barns). So, I think long term it came down to economics and installation knowledge.
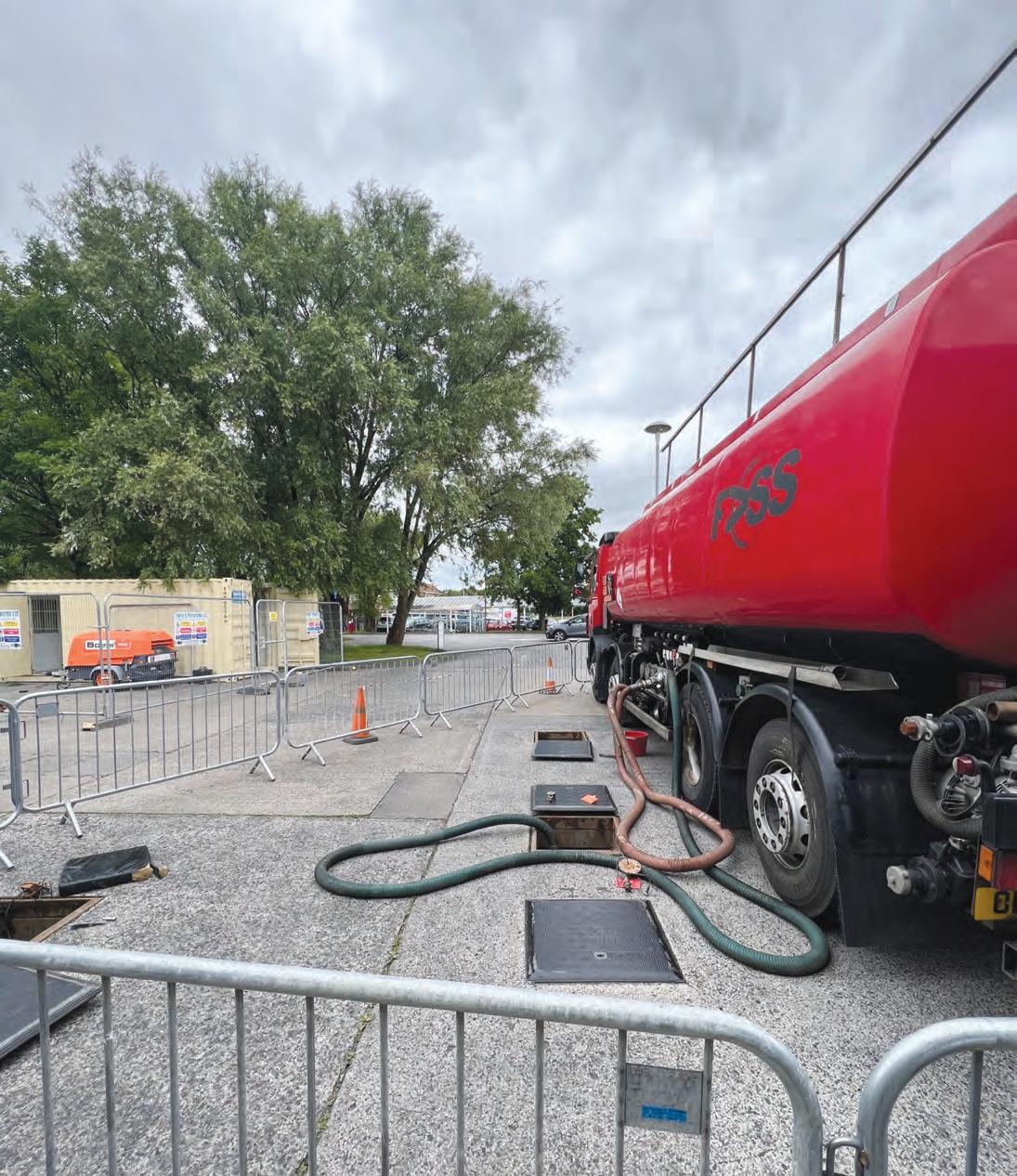
Installation:
Installing steel tanks in the ground is relatively straight forward and they will resist the knocks and the dinks and still hold test - steel is a very forgiving material. The method used for installing steel and fibreglass tanks in the ground is very similar. Both tank types are strapped down and installed in a pea shingle surround; however, I think the differences are to install your GRP tank. You really don’t have the same strength or mass to assist compared to steel. So your installers need to wear their soft gloves and avoid cross winds - GRP tanks are sensitive to windage, each tank needs to be correctly cradled during the lift and carefully placed into position within the excavation rather than just offloaded!
When it comes to strapping down with pea shingle installations the straps must be non-corrosive and also be designed to last the expected life of the tank and also have the correct breaking strain for the tank size (the straps are normally heavy duty or doubled up and calculated for the job).
The strap is embedded into the concrete foundation at the bottom of the excavation (cast in the correct positions) and there is always a layer of pea shingle between the tank and concrete slab to avoid point loading. After strapping down the GRP tank has to be stabilised as it is back filled with pea shingle usually with a water fill to maintain the roundness of the tank. Once back filled the tank farm is very stable.
This is an important note for buried tank installations – the tanks are living in a giant soakaway drain and the only restraint to keep the tank farm buried when empty is the strapping system which includes the base slab. So, the straps form part of the base slab and all the pea shingle and ground cover is acting with gravity to keep the tank farm in the ground - as long as the strapping system holds - so an extra strap on your tank is only a very marginal extra cost within the grand scheme.
Finally, installers always ask about floatation of a tank (probably the guys that did not purchase the extra strap!). We are talking about displacement and like a ship the displacement of a tank is its total mass, when the force acting upwards equals the force acting down - that’s the stage at which moving forward your tank farm is going to float (Archimedes syracuse - 287 BC). Therefore, due to a much lower mass the Fibreglass tank is going to float before the steel tank.
To finish I heard a story of a contractor that installed a tank farm on a motorway site and the thought was ‘lets go home and strap the tanks tomorrow’ - tomorrow they came to find the tank farm floating around the parking area like ships in a storm!
Simon Procter B Eng (Hons), C Eng, MIET, MIMechE, MEI
Tanks and Pipeworks Ltd, Phone: 01474 855587

Email: office@fassuk.com
Web: www.fassuk.com