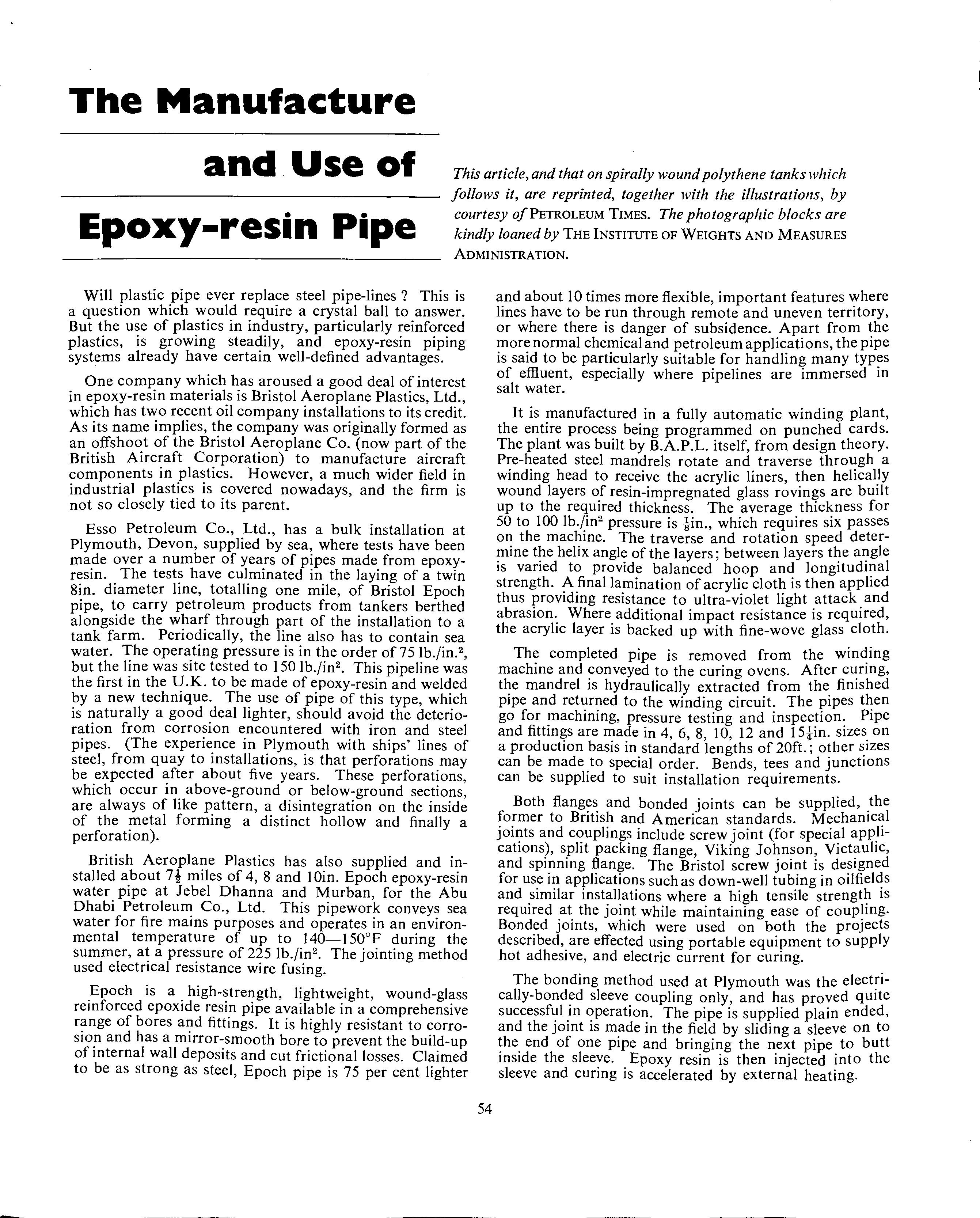
4 minute read
THE MANUFACTURE AND USE OF EPOXY-RESIN PIPE
by apeauk
This article, and that on spirally wound polythene tanks which follows it, are reprinted, together with the illustrations, by courtesy of PETROLEUM TIMES. The photographic blocks are kindly loaned by THE INSTITUTE OF WEIGHTS AND MEASURES ADMINISTRATION.
Will plastic pipe ever replace steel pipe-lines ? This is a question which would require a crystal ball to answer. But the use of plastics in industry, particularly reinforced plastics, is growing steadily, and epoxy-resin piping systems already have certain well-defined advantages.
Advertisement
One company which has aroused a good deal of interest in epoxy-resin materials is Bristol Aeroplane Plastics, Ltd., which has two recent oil company installations to its credit. As its name implies, the company was originally formed as an offshoot of the Bristol Aeroplane Co. (now part of the British Aircraft Corporation) to manufacture aircraft components in plastics. However, a much wider field in industrial plastics is covered nowadays, and the firm is not so closely tied to its parent.
Esso Petroleum Co., Ltd., has a bulk installation at Plymouth, Devon, supplied by sea, where tests have been made over a number of years of pipes made from epoxy-resin. The tests have culminated in the laying of a twin Sin. diameter line, totalling one mile, of Bristol Epoch pipe, to carry petroleum products from tankers berthed alongside the wharf through part of the installation to a tank farm. Periodically, the line also has to contain sea water. The operating pressure is in the order of 75 lb./in.2 , but the line was site tested to 150 lb./in2• This pipeline was the first in the U.K. to be made of epoxy-resin and welded by a new technique. The use of pipe of this type, which is naturally a good deal lighter, should avoid the deterioration from corrosion encountered with iron and steel pipes. (The experience in Plymouth with ships' lines of steel, from quay to installations, is that perforations may be expected after about five years. These perforations, which occur in above-ground or below-ground sections, are always of like pattern, a disintegration on the inside of the metal forming a distinct hollow and finally a perforation).
British Aeroplane Plastics has also supplied and installed about 71 miles of 4, 8 and lOin. Epoch epoxy-resin water pipe at Jebel Dhanna and Murban, for the Abu Dhabi Petroleum Co., Ltd. This pipework conveys sea water for fire mains purposes and operates in an environmental temperature of up to 140-150°F during the summer, at a pressure of 225 lb./in2• The jointing method used electrical resistance wire fusing.
Epoch is a high-strength, lightweight, wound-glass reinforced epoxide resin pipe available in a comprehensive r~nge of bores ai:id fittings. It is highly resistant to corrosion and has a mirror-smooth bore to prevent the build-up of internal wall deposits and cut frictional losses. Claimed to be as strong as steel, Epoch pipe is 75 per cent lighter and about 10 times more flexible, important features where lines have to be run through remote and uneven territory, or where there is danger of subsidence. Apart from ~he morenormal chemical and petroleum applications, thep1pe is said to be particularly suitable for handling many typ~s of effluent, especially where pipelines are immersed m salt water.
It is manufactured in a fully automatic winding plant, the entire process being programmed on punched cards. The plant was built by B.A.P.L. itself, from design theory. Pre-heated steel mandrels rotate and traverse through a winding head to receive the acrylic liners, then helical_ly wound layers of resin-impregnated glass rovings are bmlt up to the required thickness. The average thickness for 50 to 100 lb./in2 pressure is Mn., which requires six passes on the machine. The traverse and rotation speed determine the helix angle of the layers; between layers the ar.igie is varied to provide balanced hoop and longitud1~al strength. A final lamination of acrylic cloth is then apphed thus providing resistance to ultra-violet light attack and abrasion. Where additional impact resistance is required, the acrylic layer is backed up with fine-wove glass cloth.
The completed pipe is removed from the win~ing machine and conveyed to the curing ovens. After curmg, the mandrel is hydraulically extracted from the finished pipe and returned to the winding circuit. The pipes t~en go for machining, pressure testing and inspection. Pipe and fittings are made in 4, 6, 8, 10, 12 and 15!in. sizes. on a production basis in standard lengths of 20ft.; other ~1zes can be made to special order. Bends, tees and junct10ns can be supplied to suit installation requirements.
Both flanges and bonded joints can be supplied, _the former to British and American standards. Mechamcal joints and couplings include screw joint (for special appJications), split packing flange, Viking Johnson, Vict~uhc, and spinning flange. The Bristol screw joint is designed for use in applications such as down-well tubing in oilfiel~s and similar installations where a high tensile strengt~ is required at the joint while maintaining ease of coup~mg. Bonded joints, which were used on both the pro3ects described, are effected using portable equipment to supply hot adhesive, and electric current for curing.
The bonding method used at Plymouth was the elect~ically-bonded sleeve coupling only, and has proved quite successful in operation. The pipe is supplied plain ended, and the joint is made in the field by sliding a sleeve on to the end of one pipe and bringing the next pipe to butt inside the sleeve. Epoxy resin is then injected into the sleeve and curing is accelerated by external heating.
54