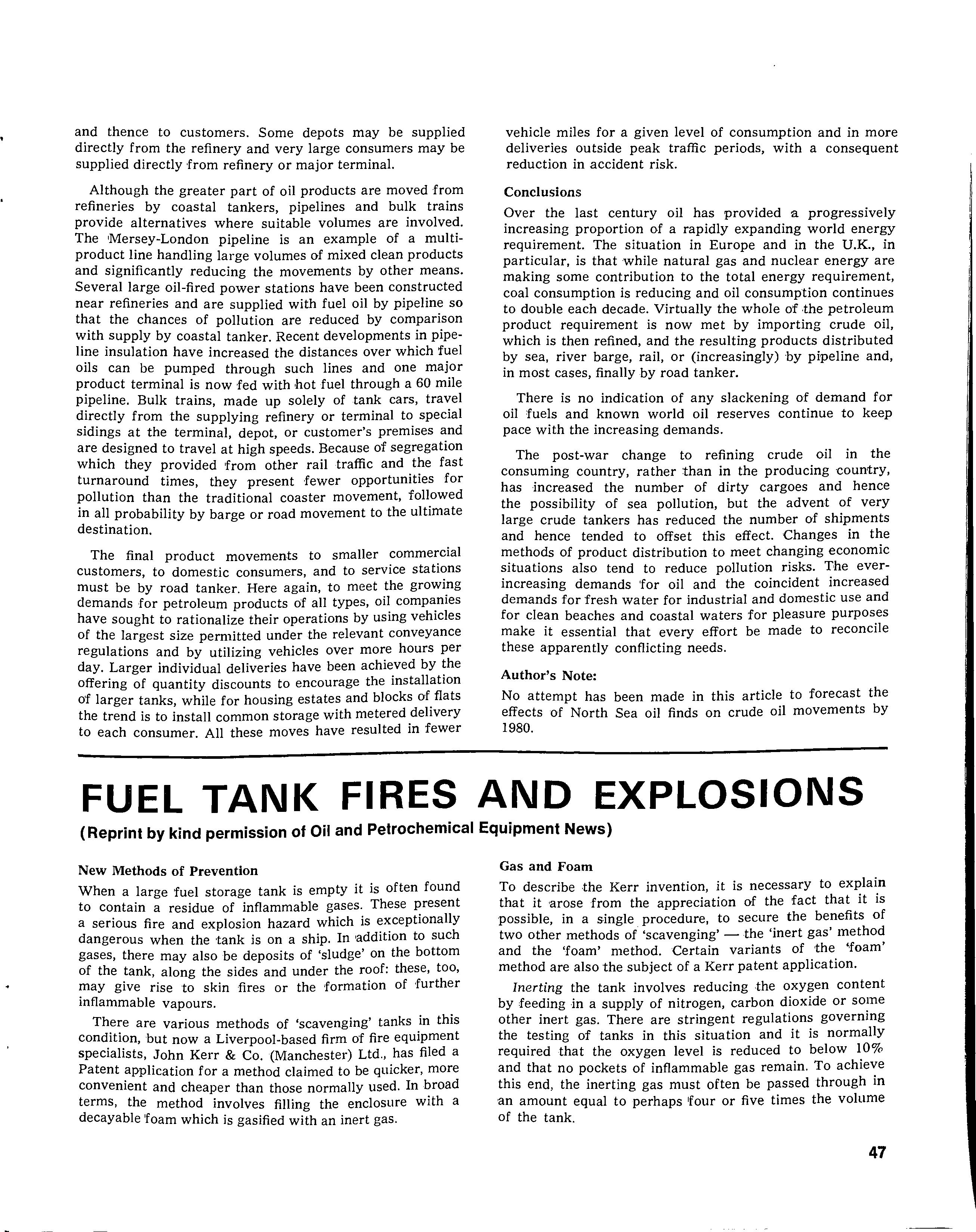
9 minute read
Fuel Tank Fires
by apeauk
and thence to customers. Some depots may be supplied directly from the refinery and very large consumers may be supplied directly from refinery or major terminal.
Although the greater part of oil products are moved from refineries by coastal tankers, pipelines and bulk trains provide alternatives where suitable volumes are involved. The Mersey-London pipeline is an example of a multiproduct line handling large volumes of mixed clean products and significantly reducing the movements by other means. Several large oil-fired power stations have been constructed near refineries and are supplied with fuel oil by pipeline so that the chances of pollution are reduced by comparison with supply by coastal tanker. Recent developments in pipeline insulation have increased the distances over which fuel oils can be pumped through such lines and one major product terminal is now fed with hot fuel through a 60 mile pipeline. Bulk trains, made up solely of tank cars, travel directly from the supplying refinery or terminal to special sidings at the terminal, depot, or customer's premises and are designed to travel at high speeds. Because of segregation which they provided from other rail traffic and the fast turnaround times, they present fewer opportunities for pollution than the traditional coaster movement, followed in all probability by barge or road movement to the ultimate destination.
Advertisement
The final product movements to smaller commercial customers, to domestic consumers, and to service stations must be by road tanker. Here again, to meet the growing demands for petroleum products of all types, oil companies have sought to rationalize their operations by using vehicles of the largest size permitted under the relevant conveyance regulations and by utilizing vehicles over more hours per day. Larger individual deliveries have been achieved by the offering of quantity discounts to encourage the instaIlation of larger tanks, while for housing estates and blocks of flats the trend is to install common storage with metered delivery to each consumer. All these moves have resulted in fewer vehicle miles for a given level of consumption and in more deliveries outside peak traffic periods, with a consequent reduction in accident risk.
Conclusions Over the last century oil has provided a progressively increasing proportion of a rapidly expanding world energy requirement. The situation in Europe and in the U.K., in particular, is that while natural gas and nuclear energy are making some contribution to the total energy requirement, coal consumption is reducing and oil consumption continues to double each decade. VirtuaIly the whole of .the petroleum product requirement is now met by importing crude oil, which is then refined, and the resulting products distributed by sea, river barge, rail, or (increasingly) by pipeline and, in most cases, finaIly by road tanker.
There is no indication of any slackening of demand for oil fuels and known world oil reserves continue to keep pace with the increasing demands.
The post-war change to refining crude oil in the consuming country, rather than in the producing country, has increased the number of dirty cargoes and hence the possibility of sea pollution, but the advent of very large crude tankers has reduced the number of shipments and hence tended to offset this effect. Changes in the methods of product distribution to meet changing economic situations also tend to reduce poIlution risks. The everincreasing demands for oil and the coincident increased demands for fresh water for industrial and domestic use and for clean beaches and coastal waters for pleasure purposes make it essential that every effort be made to reconcile these apparently conflicting needs.
Author's Note: No attempt has been made in this article to forecast the effects of North Sea oil finds on crude oil movements by 1980.
FUEL TANK FIRES AND EXPLOSIONS
(Reprint by kind permission of Oil and Petrochemical Equipment News)
New Methods of Prevention When a large 'fuel storage tank is empty it is often found to contain a residue of inflammable gases. These present a serious fire and explosion hazard which is exceptionally dangerous when the tank is on a ship. In 'addition to such gases, there may also be deposits of 'sludge' on the bottom of the tank, along the sides and under the roof: these, too, may give rise to skin ,fires or the formation of further inflammable vapours.
There are various methods of 'scavenging' tanks in this condition, but now a Liverpool-based firm of fire equipment specialists, John Kerr & Co. (Manchester) Ltd., has filed a Patent application for a method claimed to be quicker, more convenient and cheaper than those normally used. In broad terms, the method involves filling the enclosure with a decayable 'foam which is gasified with an inert gas. Gas and Foam To describe .the Kerr invention, it is necessary to explain that it arose from the appreciation of the fact that it is possible, in a s.jngle procedure, to secure the benefits of two other methods of 'scavenging' - the 'inert gas' method and the 'foam' method. Certain variants of the method are also the subject of a Kerr patent application.
Inerting the tank involves reducing the oxygen content by feeding .jn a supply of nitrogen, carbon dioxide or some other inert gas. There are stringent regulations governing the testing of tanks in this situation and it is normally required that the oxygen level is reduced to below 10% and that no pockets of inflammable gas remain. To achieve this end, the inerting gas must often be passed through in an amount equal to perhaps four or five times the volume of the tank.
The foam method uses a high expansion foam, (produced by combining a chemical foaming agent in liquid form with air) which is blown through a massive hose into the tank or enclosure. This method is already widely used to fill and flood enclosed areas such as cellars or warehouses in conjunction with fires involving solid organic substances or inflammable liquids.
Of its use for scavenging tanks, the Department of Employment and Productivity's technical literature has stated that 'it is very probable that any vapour would be effectively removed as the foam built up. Certainly with a vapour-freed tank complete filling with high-expansion foam and the maintenance of a slight positive flow into the tank should completely obviate any risk of fire or explosion'.
The implication is that the use of the inert gas method followed up by high expansion foam would achieve the most satisfactory results. Kerr's have taken the unique step of, in effect, combining the two, in one operation.
'Combined Operation' Recently Kerr's experts were called in, along with a host of other specialists and consultants from various fields to work on a badly damaged tanker lying outside a continental port. Seven of the tanks were still full of gas in the explosive range and had to be safe before repairs could start. It was decided as a general principle to use ,the inert gas method to bring these tanks to a safe condition before using a high expansion foam, though some tanks were indeed so badly fractured that .the inerting method was not practicable.
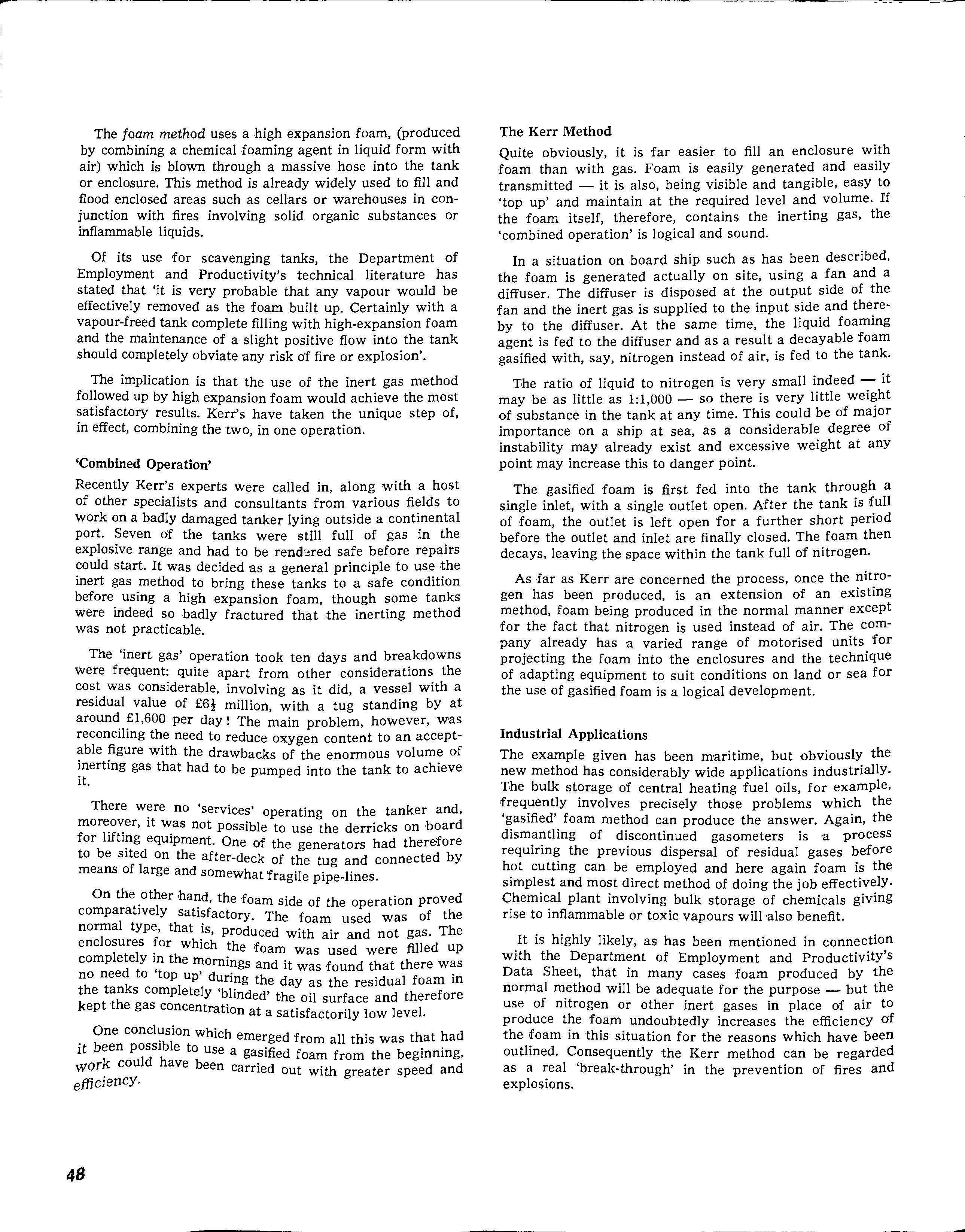
The 'inert gas' operation took ten days and breakdowns were frequent: quite apart from other considerations the cost was considerable, involving as it did, a vessel with a residual value of £61 million, with a tug standing by at around £1,600 per day! The main problem, however, was reconciling the need to reduce oxygen content to an acceptable figure with the drawbacks of the enormous volume of inerting gas that had to be pumped into the tank to achieve it.
There no 'services' operating on the tanker and, moreover, It was not possible to use the derricks on hoard for equipment. One of the generators had therefore to be SIted on the after-deck of the tug and connected by means of large and somewhat fragile pipe-lines.
On the .other the foam side of the operation proved comparatively satIsfactory. The foam used was of the normal type, that is, produced with air and not gas. The enclosures which the foam was used were filled up completely d t no nee 0 ID the mornings 't, op up during and it w f d that there was as oun the day as the residual foam in the tanks completely 'blinded' the oil surface and therefore kept the gas concentration at a satisfactorily low level.
One which emerged 'from all this was that had it been to use a gasified foam from the beginning, work cou d ave been carried out with greater speed and etliciency. The Kerr Method Quite obviously, it is far easier to fill an enclosure with foam than with gas. Foam is easily generated and easily transmitted - it is also, being visible and tangible, easy to 'top up' and maintain at the required level and volume. rf the foam -itself, therefore, contains the inerting gas, the 'combined operation' is logical and sound.
In a situation on board ship such as has been described, the foam is generated actually on site, using a fan and a diffuser. The diffuser is disposed at the output side of the fan and the inert gas is supplied to the input side and thereby to the diffuser. At the same time, the liquid foaming agent is fed to the diffuser and as a result a decayable foam gasified with, say, nitrogen instead of air, is fed to the tank.
The ratio of liquid to nitrogen is very small indeed - it may be as little as 1:1,000 - so there is very little of substance in the tank at any time. This could be of maJor importance on a ship at sea, as a considerable degree of instability may already exist and excessive weight at any point may increase this to danger point.
The gasified foam is first fed into the tank through a single inlet, with a single outlet open. After the tank is full of foam, the outlet is left open for a further short period before the outlet and inlet are finally closed. The foam then decays, leaving the space within the tank full of nitrogen.
As far as Kerr are concerned the process, once the nitrogen has been produced, is an extension of an existing method, foam being produced in the normal manner except for the fact that nitrogen is used instead of air. The company already has a varied range of motorised units for projecting the foam into the enclosures and the technique of adapting equipment to suit conditions on land or sea for the use of gasified foam is a logical development.
Industrial Applications The example given has been maritime, but obviouslY the new method has considerably wide applications industrially. The bulk storage o'f central heating fuel oils, for example, frequently involves precisely those problems which the 'gasified' foam method can produce the answer. Again, the dismantling of discontinued gasometers is a process requiring the previous dispersal of residual gases before hot cutting can be employed and here again foam is the simplest and most direct method of doing the job effectively. Chemical plant involving bulk storage of chemicals giving rise to inflammable or toxic vapours will 'also benefit.
It is highly likely, as has been mentioned in connection with the Department of Employment and Productivity's Data Sheet, that in many cases foam produced by the normal method will be adequate for the purpose - but the use of nitrogen or other inert gases in place of air to produce the foam undoubtedly increases the efficiency of the foam in this situation for the reasons which have been outlined. Consequently the Kerr method can be regarded as a real 'break-through' in the prevention of fires and explosions.