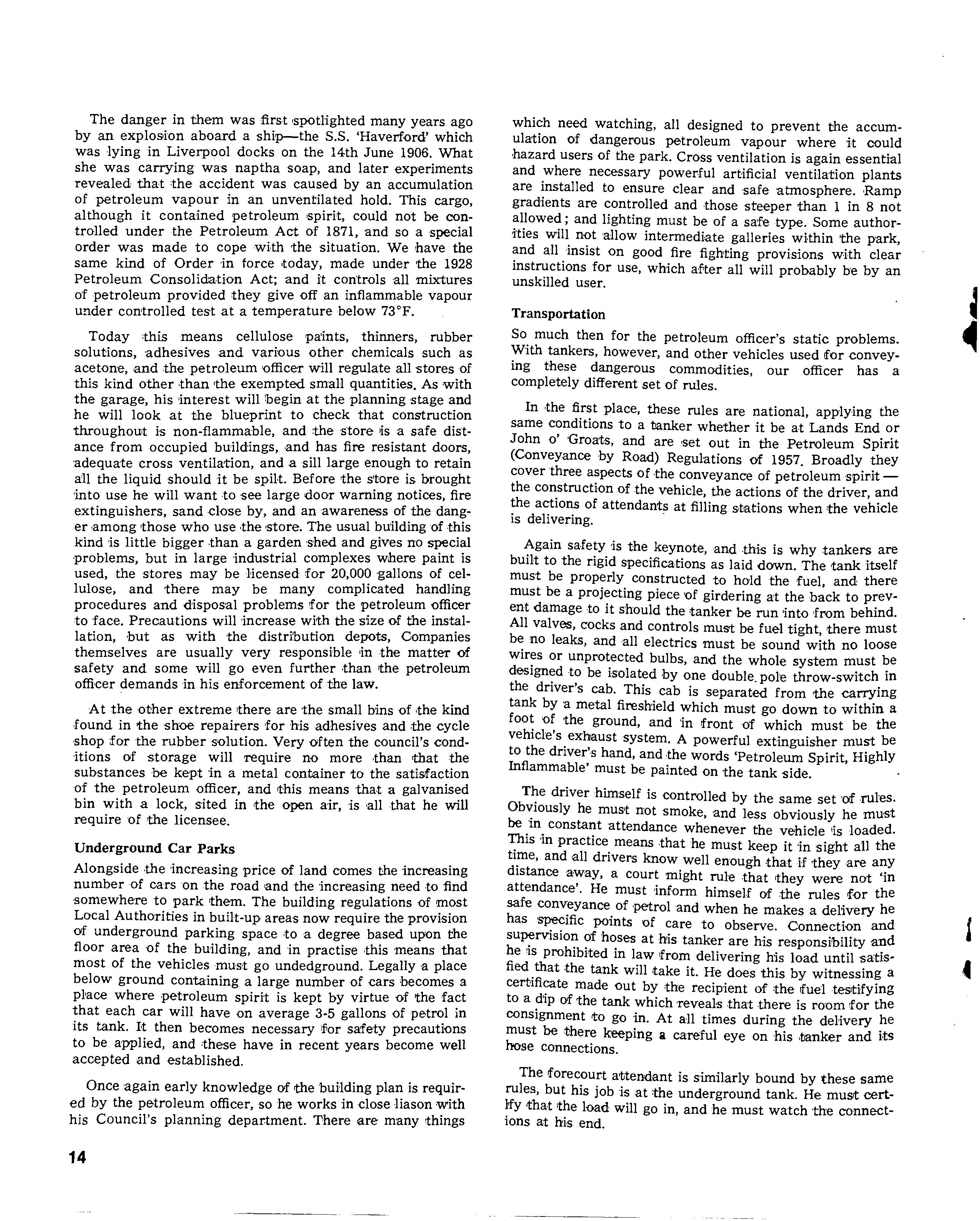
72 minute read
VOLUME
by apeauk
The danger in them was first ,spotlighted many years ago by an explosion aboard a ship-the S.S. 'Haverford' which was lying in Liverpool docks on the 14th June 1906. What she was carrying was naptha soap, and later experiments revealed that the accident was caused by an 'accumulation of petroleum vapour in an unventilated hold. This cargo, although it contained petroleum 'spirit, could not be controlled under the Petroleum Act of 1871, and so a special order was made to cope with the situation. We have the same kind of Order in force today, made under the 1928 Petroleum Consolidation Act; and it controls all mixtures of petroleum provided they give off an inflammable vapour under controlled test at a temperature below 73°F. _
Today this means cellulose p8:ints, thinners, rubber solutions, adhesives and various other chemicals such as acetone, and the petroleum officer will regulate all stores of this kind other ·than the exempted small quantities. As with the garage, his interest willibegin at the planning stage he will look at the blueprint to check that constructIOn throughout Is non-flammable, and :the store lis a safe distance from occupied buildings, and has fire resistant doors, adequate cross ventilation, and a sill large enough to retain 8:11 the liquid should it be spiLt. Before the s't;ore is brought into use he will want to see large door warning notices, fire extinguishers, sand dose by, and an awareness of the danger among 'those who use the 'store. The usual building of this kind is little bigger than a garden shed and gives no 'problems, but in large industrial complexes where paint is used the stores may be licensed for 20,000 'gallons of eeland there may be many complicated handling procedures and disposal problems for the petroleum officer to face. Precautions will increase with the size of the installation, but as with the distribution depots, Companies themselves are usually very responsible ,in ,the matter of safety and some will go even further than the petroleum officer demands in his enforcement of the law.
Advertisement
At the 'Other extreme Ithere are the small bins of 'the kind .found in the shoe repairers for his adhesives and the cycle shop for the rubber solution. Very often the council's conditions of storage will require no more than that -the substances be kept 'in a metal container to the satisfaction of the petroleum officer, ,and rthis means that a galvanised bin with a lock, sited in the open air, is 'all ,that he will require of the licensee.
Underground Car Parks Alongside ,the increasing price of land comes the increasing number of ca'rs 'on the road and the 'increasing need ,to find somewhere to park them. The building regulations of most Local Authorities in built-up areas now require the provision of underground parking space to a degree based upon the floor area 'Of the building, and 'in practise this means that most of the vehicles must go undedground. Legally 'a place below ground containing a large number of cars 'becomes a place where petroleum spirit is kept by virtue of 'the fact that each car will have on average 3-5 gallons of petrol in 'its tank. It then becomes necessary !fior safety precautions to be applied, and these have in recent years become well accepted and established,
Once 'again early knowledge of the buHding plan is required by the petroleum officer, so he works in dose Uason -with his C'Ouncil's planning department. 'I'here are many things which need watching, all designed t'O prevent the accumulati'On of dangerous petroleum vap'Our where it could hazard users of the park. Cross ventilation is again essential and where necessary powerful artificial ventHati'On plants are installed to ensure clear and safe 'atmosphere. Ramp gradients 'are contr'Olled and th'Ose steeper than 1 in 8 not all'Owed; and lighting must be 'Of a safe type. Some authori'ties will not 'allow intermediate galleries within the park, and aU insist on good fire fighting provisions with clear instructions for use, which afiter all will probably be by an unskilled user.
Transportation So much then for the petroleum officer's static problems. With tankers, however, and other vehicles used for c'Onveying these danger'Ous commodities, our officer has a c'Ompletely different set 'Of rules.
In ,the first place, these rules are national, app:lying the same conditions to a tanker whether it be at Lands End or John 0' Groats, and are 'set out in the Petroleum Spirit (Conveyance by Road) Regulations of 1957. Broadly they cover three aspects of the conveyance 'Of petroleum spiritthe construction of the vehicle, the actions of the driver, and the actions of attendants at filling stations when the vehicle is delivering. -
Again safety is the keynote, 'and ,this is why tankers are built to the rigid specifications as laid down. The tank itself must be properly constructed to hold the fuel, and there must be a projecting piece 'Of girdering at the back to prevent damage to it should the tanker be run 'into from behind. All valves, cocks and contr'Ols must be fuel tight, there must be no leaks, and 'all electrics must be sound with no loose wires or unprotected bulbs, and the wh'Ole system must be designed to be is'Olated by one double. pol'e throw-switch in the driver's cab. This cab is separated from the carrying tank by a metal fireshield which must go down to within a foot 'Of the ground, and in front 'Of which must be the vehicle's exhaust system. A powerful extinguisher must be to the driver's hand, and the words 'Petroleum Spirit, Highly Inflammable' must be painted on the tank side. .
The driver himself is controlled by the same set 'Of ,rutes. Obviously he must not smoke, 'and less 'Obviously he must be in constant 'attendance whenever the vehicle lis loaded. This in practice means that he must keep it 'in sight all the time, and 1811 drivers know well enough that if they are any distance away, a C'Ourt might rule that they were not 'in attendance'. He must inform himself of the rules for the safe c'Onveyance of petrol and when he makes a delivery he has specific points 'Of care to observe. Connection and supervision of hoses at his tanker are his resp'Onsibility and he lis prohibited in law from delivering his load until satisfied that the tank will take it. He does this by witnessing a certificate made 'Out by the recipient of :the fuel testifying toa dip of the tank which Teveals that there is room f'Or the consignment <to go in. At all times during the delivery he must be Ithere keeping a careful eye on his .tanker and hose connections.
The forecourt attendant is similarly bound by these same rules, but his job 'is at the underground tank. He must certIfy that the load will go in, and he must watch 'the connections at his end.
With 'all these precautions one would wonder however accidents on delivery could occur, but every petroleum officer knows ,thaot they do. Both forecourt attendants and drivers get slack; they do not always bother with these undoubtedly irksome restrictions, 'and s'Ometimes something goes wrong. Sometimes <they find themselves 'in the emarrassing posWon of having a full tank below ground and a tanker with some petrol still 'in. With the two connected, they have a real problem because a tanker can not pump back the petrol, and it all could be ,avoided by careful dipping in the first place. This cartoon situation is far from funny when the danger it presents to life and limb is realised.
A recent set of Regulations brought in 'in 1968 has extended This type of control to many other dangerous liquids which are not in law petroleum spirits or mixtures - though similar and just as dangerous. The keen observer of motor transport will have already spotted the red and black diamond on the back ,and front of every vehicle which carries these hazardous liquids. Known as the 'Torch Symbol' 'it marks well a wise new widening of the legal control of such commodities.
What of the Future? The overriding wish of all petroleum officers is for National Regulations to control storage as well as transportation. It seems right to no-one that a garage one side af an authority's boundary should be governed by a different set of conditions from a garage at 'the other, and is a fair eX'ample of 'the sort of thing <that brings iocal Government into disrepute. Uniformity must <:ame sooner or later, and the Association for Petroleum and Explosives Administration, an organisation which is very widely acclaimed by both Authorities and Officers, has administrative uniformity as one vf its aims. * As our readers are well aware responsibility is now vested throughout the V.K. with the Greater London Councll and the County Councils.
THE INSTALLATION OF UNDERGROUND TANKS
An Oil Company Engineer's View
What can be said to be the prime considera:Hons when installing underground spirit storage. It is suggested they 'are nO't necessarily in order of priority, as follows: 1. To provide against leakage from the tank. 2. To protect the tank from external corrosion. 3. Permanency and stability. 4. Simplicity O'f design. 5. Economy of design.
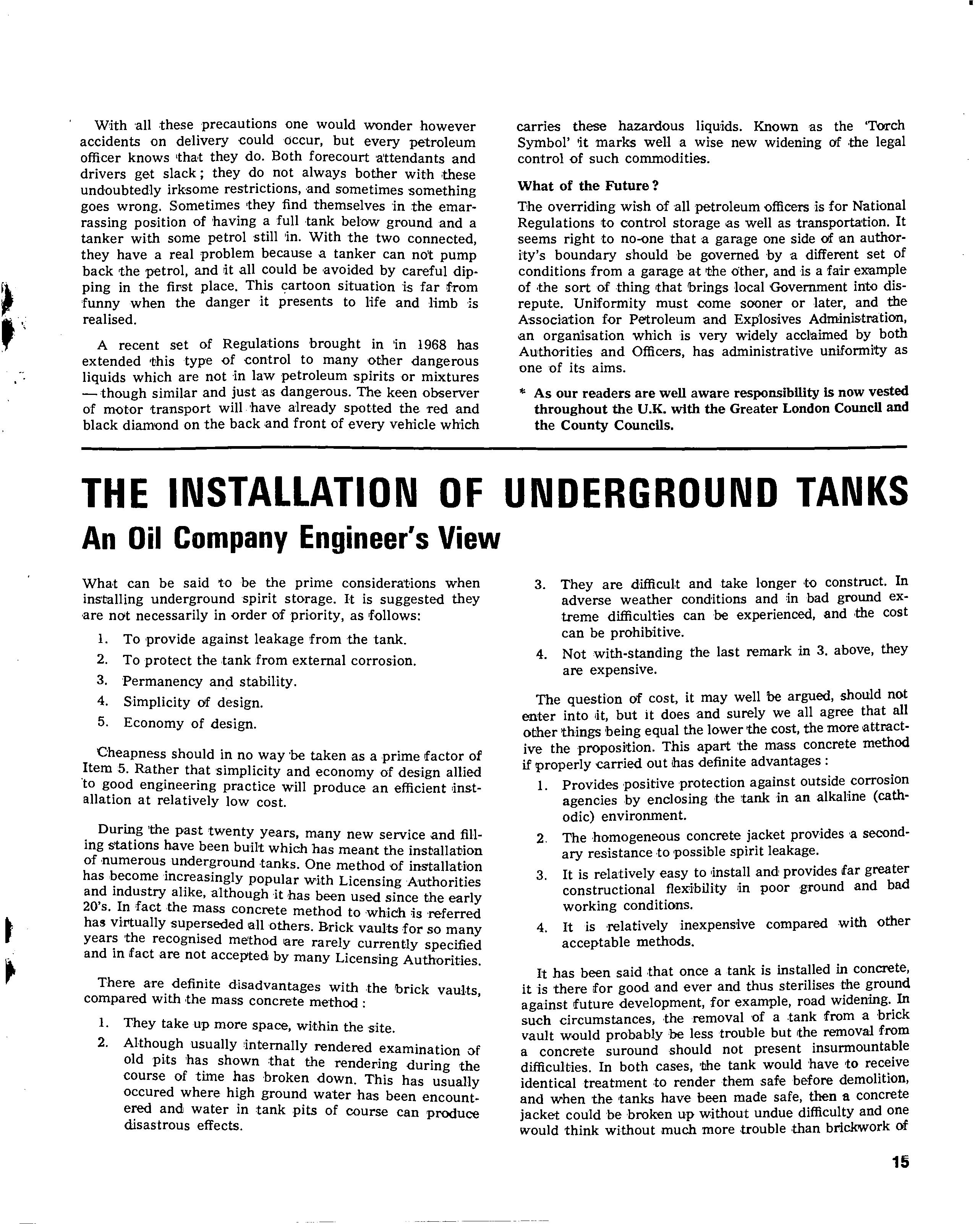
Cheapness should in no way be taken as a prime factor of Item 5. Rather that simplicity and economy of design allied to good engineering practice will produce an efficient linstallation at relatively low cost.
. Durin.g 'the past twenty years, many new service and fillmg stations have been built which has meant the of numerous underground tanks. One method of installation popular with Licensing Authorities an,d mdustry alike, although it has been used since the early 20 s. fact the mass concrete method to which is referred
Virtually superseded !all others. Brick vaults for so many the recognised method are rarely currently specified and In fact are not accepted by many Licens'ing Authorities.
There are definite disadvantages with ,the brick vaults, compared with the mass concrete method : 1. They take up more space, wIthin the site. 2. Alth0';lgh usually jnternally rendered examination of old Pits shown that the rendering during the COurse of tlffie has hroken down. This has usually occured where high ground water has been encountered and water in tank pits of course can produce disastrous effects. 3. They are difficult and take longer to construct. In adverse weather conditions and :in had ground extreme difficulties can be experienced, and .the cost can be prohibitive. 4. Not with-standing the last remark in 3. above, they are expensive.
The question of cost, it may well be argued, should not enter into lit, but it does and surely we all agree that all other things being equal the lower 'the cost, the more attractive the proposition. This apart the mass concrete method if properly carried 'Out ihas definite advantages: 1. Provides positive pr'Otection against outside conos'ion agencies by enclosing the !tank in an alkaline (cathodic) environment. 2, The hom'Ogeneous concrete jacket provides 'a se<:ondary resistance to possible spirit leakage. 3. It is relatively easy to ,install and provides far greater constructional flexibility in poor ground and bad working c'Onditions. 4. It is 'relatively inexpensive compared with 'Other acceptable methods.
It has been said that once a tank is installed in concrete, it is there for good and ever and thus sterilises the ground against future development, for example, road widening .. In such circumstances, ,the removal of a tank fr'Om a brick vault w'Ould probably be less trouble but ,the removai from a concrete suround should not present insurmountable difficuHies. In both cases, 'tJhe tank would have to receive identical treatment to render them safe before demolition, and when the tanks have been made safe, then a concrete jacket could be broken up without undue difficulty and one would think without much more trouble than brickwork 'Of
a vault. Some Authorities have specified that under such circumstances, the tanks should be fi1.led with water.
This whilst the tank is being ftfeed from its surround, be it sand or concrete, and also whilst it is being lifted out of the ground. Practically, this presents d'iffiiculty, for even a 'relatively small 5,000 litre tank fuH of water would weigh in ·the region of 6 to 7 'tonnes whereas a 15,000 Htre tank would weigh close on 16 tonnes. It is suggested a far more convenient and safer way would be 'to have the ltanks gasfreed before any work whatsoever is carried out on them. The usual fate of an old tank is ,the scrapyard. This in itself means that it must be gas free to permit cutting up operations; why not ·therefore gas free initially 'and permit foHowing operations Ito be carried out ·in safety and without undue difficulty?
To return from the improbable resurrection of a tank to its installation, it would probably be best to review the various stages of the work, making appropriate references to materials and fittings and where better to start than the tank itself.
The ,tanks purchased and installed by ·the major Petroleum Companies are made of steel of British manufacture and in accordance with British Standard 2594: 1955. This covers ,the construction of horizontal mild steel storage tanks, and specified thickness of plate for shells and dished ends, method and standard of welding seams etc. In no .case, however, Slhould its shell thickness be less than 6mm.
There are one or two points concerning ,the manufacture of the tanks worth special mention, although obviously there would be little point in reviewing the Standard as a whole.
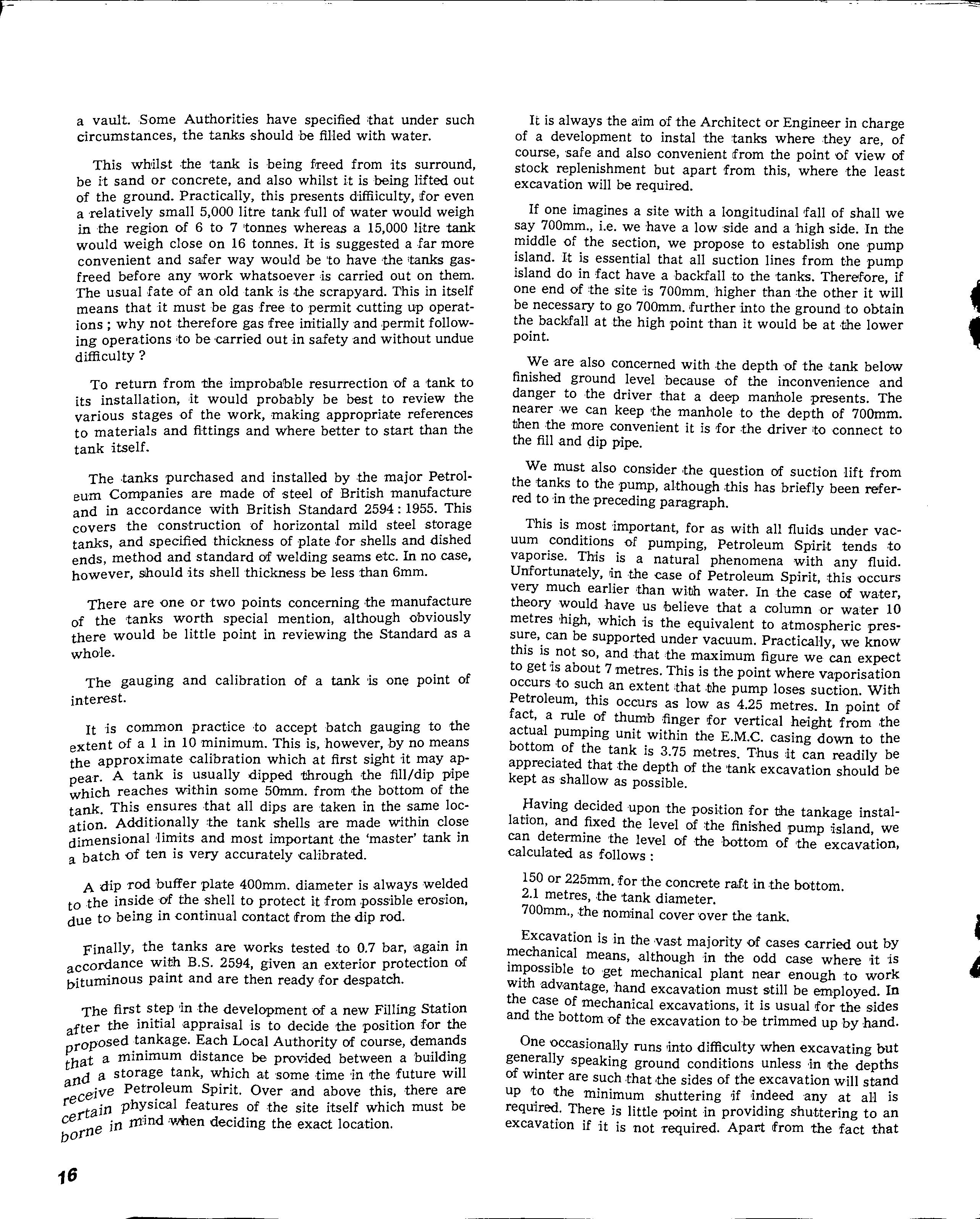
The gauging and calibration of a tank is one point of interest.
It is common practice ,to accept batch gauging to the extent of a 1 in 10 minimum. This is, however, by no means the approximate calibration which at first sight it may pear. A tank is usually dipped through the fill/dip plpe which reaches within some 5Omm. from the bottom of the tank. This ensures that all dips are 'taken in the location. Additionally the tank shells are made withIn dimensional ,limits and most important the 'master' tank m a batch of ten is very accurately calibrated.
A dip rod buffer plate 400mm. diameter is always welded to the inside 'of the shell to protect it from possible eros'ion, due to being in continual contact from the dip rod.
Finally, the tanks are works tested to 0.7 bar, again in accordance wi.th E.S. 2594, given an exterior protection of bituminous pamt and are then ready for despatch.
The first step 'in the development of a new Filling Station fter the initial ,appraisal is to decide the position for the a roposed tankage. Each Local Authority of course, demands Pbat a minimum distance be provided between a t d a storage tank, which at some time in the future wIll all eive Petroleum Spirit. Over 'and above this, there are features of the site itself which must be ce ill mInd 'YMen deciding the exact location. bOrlle
It is always the aim of the Architect or Engineer in charge of a development to instal the tanks where ,they are, of course, safe and also convenient !from the point of view of stock replenishment but apart from this, where the least excavation will be required.
If one imagines a s'ite with a longitudinal fall of shall we say 70Omm., i.e. we have a low 'side and a high side. In the middle of the section, we propose to establish one pump island. It is essential that all suction lines from the pump island do in fact have a backfall to the tanks. Therefure, if one end of the site is 700mm. higher than 'the other it will be necessary to go 700mm. further into the ground to obtain the bacI«all at the high point than it would be at ,the lower point.
We are also concerned with ,the depth 'of the .tank below finished ground level because of the inconvenience and danger to the driver that a deep manhole presents. The nearer ,we can keep the manhole to the depth of 70Omm. tJhen the more convenient it is for the driver to connect to the fill and 4ip pipe.
We must also consider ,the question of suction Hft from the tanks to the pump, although this has briefly been referred to ,in the preceding para'graph.
This is most important, for as with all fluids under vacuum conditions of pumping, Petroleum Spirit tends ,to vaporise. This is a natural phenomena with any fluid. Unfortunately, ·the case of Petroleum Spirit, this occurs very much earlier than witJh wa·ter. In the case of water, theory would have us believe that a column or water 10 metres high, which 'is the equivalent to atmospheric prescan be SUpported under vacuum. PracticaHy, we know thIS IS. not so, and that 'the maximum figure we can expect to get 'IS about 7 metres. This is the point where vaporisation occurs to such an extent ,that ,the pump loses suction. With Petroleum, this occurs as low as 4.25 metres. In point of fact, a rule of thumb finger !for vertical height from the actual pumping unit within the E.M.C. casing down to the of the tank is 3.75 metres. Thus lit can readily be appreCIated that the depth of the 'tank excavation should be kept as shallow as possible.
decided upon the position for the tankage installatIOn, and .fixed the level of the finished pump island, we can determIne the level of the bottom of the excavation, calculated as follows:
150 or 225mm. !for the concrete ra.f.tin the bottom. 2.1 metres, ,the tank diameter. 700mm., the nominal cover over the tank.
Excavation is in the 'Vast majority of 'cases carried out by means, although 'in the odd case where it 'is to 'get mechanical plant near enough to work WIth advantage, hand excavaotion mll'st still be employed. In the case of mechanical excavations, it is usual for the sides and the bottom of the excavation to he trimmed up by hand. One occasionally runs ,into difficulty when excavating but speaking ground conditions unless oln the depths of WInter are such that 'the sides of the excavation will stand up to the minimum shuttering if indeed any at aH is required. There is little point in providing shuttering to an excavation if it is not Tequired. Apart from the fact that
this is added expense, it is often a difficult job to position the tanks within the excavation and still retain the horizontal members to the 'shuttering which, of course, are necessary.
Where bad ground is encountered this, however, is a different matter and one can usually rely upon the Contractor, ,if he is a reputable man, to take whatever action is necessary 'and to take '1.t quickly. Certainly it is necessary that any loose ground is supported, to prevent ,it faHing into the concrete when this is eventually poured. , Occasionally, bad ground is encountered and this can take a number of forms and can vary from average difficulty to almost the impossible.
Water is, of course, common to any excavation over a metre deep. One may be fortunate and not encounter it at all but it is common and any Contractor is well experienced in dealing with it. He acts with 'commonsense, makes a sump in one 'corner of the excavation and trimps ;the bottom so that all the water runs into that corner, and pumps it out.
Loose soil can present difficulties, but this in 'itself is usually easily dealt with by immediate action with shuttering as work proceeds.
When one gets loose soil or sand and water together, It can be a nigihtmare. As with all civil engineering works underground, speed of action is the essence of good practice and this appHes where loose sand and water are concerned, more than in any other condition. This condition is usuaUy referred to, as 'running sand or blowing sand, and although quite stable, bef.ore construction 'and after construction is difficult indeed during construction.
There are a number 'Of methods of dealing with this particular condition, but one above all 'is favoured where relatively shallow excavations are involved. This is ;the "well point de-watering system". The system consists of a number of well points, each consisting 'Of a number of fluted steel tube covered by a gauze screen ,and having a shoe screwed on the end. The well 'points are jetted into the ground by water under pressure linto the well point, from which It 'IS at the tip. This washes a hole in the ground an? sinks ,the well point to the required depth. The well pomts placed in a ring around the excavation and spaced accordmg to the ground and quantity of water to be handled.
Bach well point is connected ,to a main suction pipe which acts as a manifold and which is in turn connected to a pumping unit, driven usually by diesel engine. The effective depth of this system is limited but lit is more than adequate ,to deal with Ithe usual excavation for underground The 'advantages of such a system 'are considerable solt,lce 'ID. the first place, there is no flow 'Of water! Itoo excavatIon at a.11 - 'the flow is always 'away from it _ secondly, IS always carried out in ,the dry and thirdly well pomts are. put down from ,the sUl"face which is mdeed soever. very convement and 'requires no excav t' a IOn 'h w at-
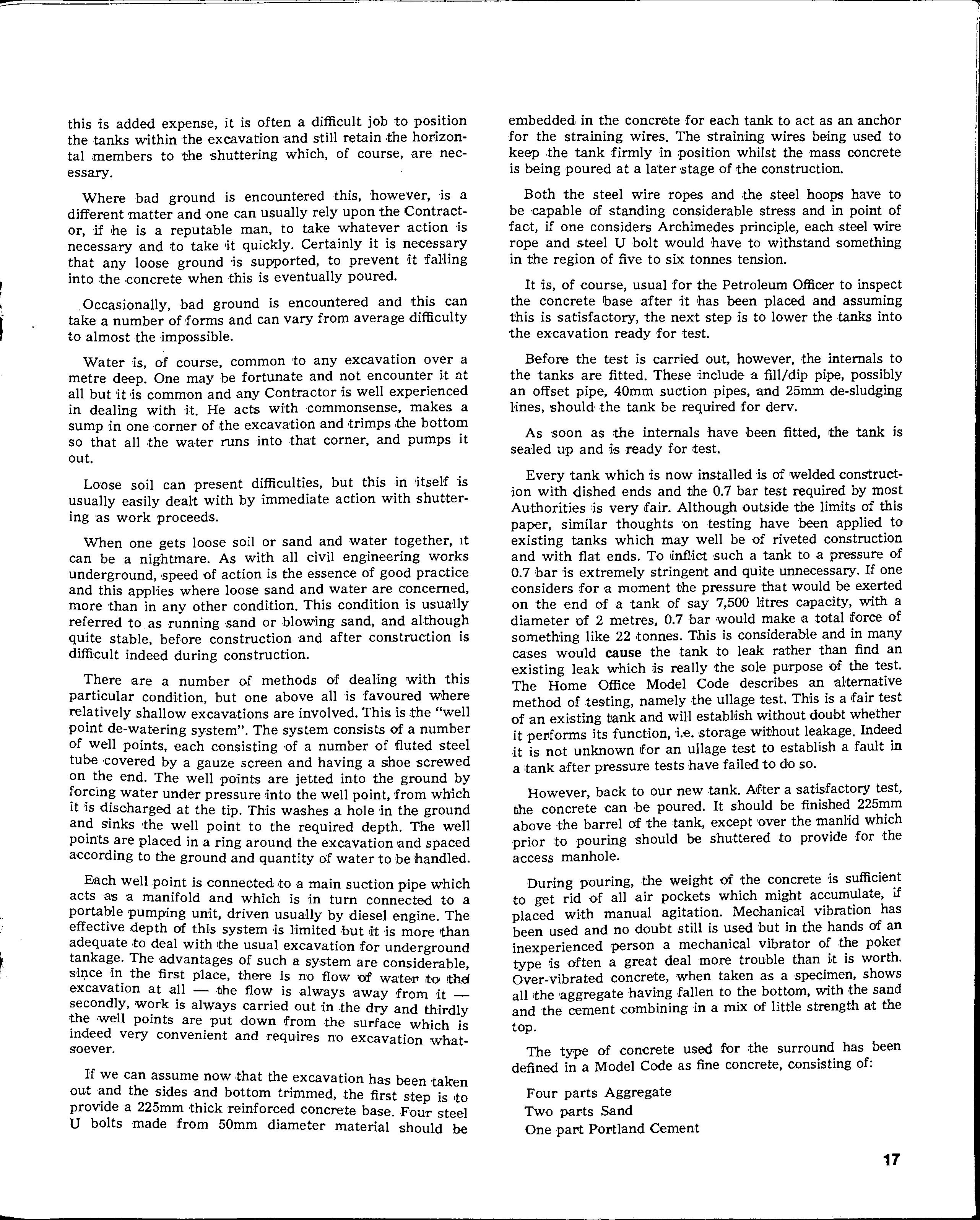
If we can as.sume now that the excavation has been taken out the SIdes a,?d trimmed, the first s'rep is ,to prOVIde a 225mm 'thIck remforced concrete base. F'OUT steel U bolts made from 50mm dIameter material should be embedded in the concrete .for each tank to act as an anchor for the straining wires. The straining wires being used to keep ,the tank firmly in position whilst the mass concrete is being poured at a later stage of the construction.
Both the steel wire ropes and ,the steel hoops have to be 'capable of standing considerable stress and in point of fact, if one considers Archimedes principle, each steel wire rope and 'steel U bolt would have to withstand something in the region of five to six tonnes tension.
It is, of course, usual for the Petroleum Officer to inspect the concrete base after it has been placed and assuming this is satisfactory, the next step is to lower the tanks into the excavation ready for test.
Before the test is carried out, however, the internals to the tanks are fitted. These include a fill/dip pipe, possibly an offset pipe, 40mm suction pipes, and 25mm de-sludging Hnes, should the tank be required for derv.
As s'Oon as <the internals 'have been fitted, the tank js sealed up and is ready for test.
Every tank which is now installed is of welded construction with dished ends and the 0.7 bar test required by most Authorities lis very [air. Although outside the limits of this paper, ,similar thoughts 'on testing have been applied to existing tanks which may well be of riveted construction and with flat ends. To dnfHct ,such a tank to a pressure of 0.7 bar is extremely stringent and quite unnecessary. If one 'considers for a moment the pressure that would be exerted on the end of a tank of say 7,500 litres capacity, with a diameter of 2 metres, 0.7 bar would make a total force of something like 22 ,tonnes. This is considerable and in many cases would cause the tank to leak rather than find an existing leak which ds really the sole purpose of the test. The Home Office Model Code desoribes an aHemative method of testing, namely .the ullage test. This is a fair test of 'an existing m,nk and will establtish without doubt whether it pel1forms its function, i.e. storage without leakage. Indeed -it is not unknown [or an ullage test to establish a fault in a :tank after pressure tests have failed to do so.
However, back to our new ,tank. After a satisfactory test, bile concrete can be poured. It should be finished 225mm above the barrel of the tank, except over the manHd which prior :to pouring should be shuttered ,to provide for the access manhole.
During pouring, the weight of the concrete is sufficient to get rid of all air pockets which might accumulate, if placed with manual agitation. Mechanical vibration has been used and no d'Oubt still is used 'but in the hands of an inexperienced person a mechanical vibrator of ,the poker type is orten a great deal more trouble than 1.t is worth. Over-vibrated concrete, when taken as a specimen, shows all the 'aggregate having fallen to the bottom, with -the sand and the cement combining in a mix of little strength at the top.
The type of concrete used for the surround has been defined in a Model Code as fine concrete, consisting of:
Four parts Aggregate Two parts Sand One part Pordand Cement
In the greater majority of installations, it is quite satisfactory to use Portland Cement concrete. It has been known, however, for quite a number of years that sulphates in solution are liable to attack ordinary concrete. This is a problem of long standing in many localities and severe cases of attack by soluble sulphate salts have been known to result in serious concrete damage. The sulphates most likely to be met with, particularly :in clay sub-s'oii and in ground water ,contained in the soil, are mainly due to the presence of Gypsum, Epsom Salts and Glauber's Salt. Ordinary concrete made with the usual Portland type 1S generally resistant enough, provided the sulphate concentrations are moderate and the concrete dense and strong.
In cases where a high concentration is experienced, then it is necessary to -take special precautions, i.e. 'by using sulphate-resisting cement.
Ordinary Portland Cement contains a certain amount of alumina which is susceptible to attack by sulphates. In the sulphate-resisting cement, the aluminacontent is reduced and the iron oxide ,content of ,the cement is increased so that :the components :in the set concrete which are most susceptible to a'ttack by sulpha-tes are present in only negligible ,amounts. This 1s achieved by <the 'Use of. special and more expensive raw materials in the manufacture of the cement.
To determine whether sulphate-resisting cement should be used, it would be necessary to make an analysis of the ground water collecting lin the excavation. This, however, would .interrupt work and a:s ground water and bad working conditions go hand in hand, the interruption would come at a time when it could be least afforded. Although the cost of sulphate-resisting cement over ordinary cement is appreciably higher, when considered over the overall cost of the concrete an :increase of approximately 4 to 5% is involVed. In view of this, 'it is quite obviously best and safest to specify the higher priced product in all 'cases. The in being a'ble to progress ilhe job without undue Interruption outweigh the eJctra ,cost in this case.
At this stage, we have the tanks 'installed in ilheir concrete joackets and the next step is to lay the suotion ,and vent pipes to their respective positions.
The pipes and fittings should be to British 'Standard 1387: 1967, ,the p'ipes for the spirit and vent lines 'being galvanised, that for the derv line being black iron.
The internal dips and fill lines are made in aluminium and are taken down to within 50mm of the bottom of the tank. This is to provide the required liquid seal to 'an unvented opening. Aluminium for this purposes, apart from the obvious advantage ·of 1ightness in fitting, does not rust as would a ferrous material.
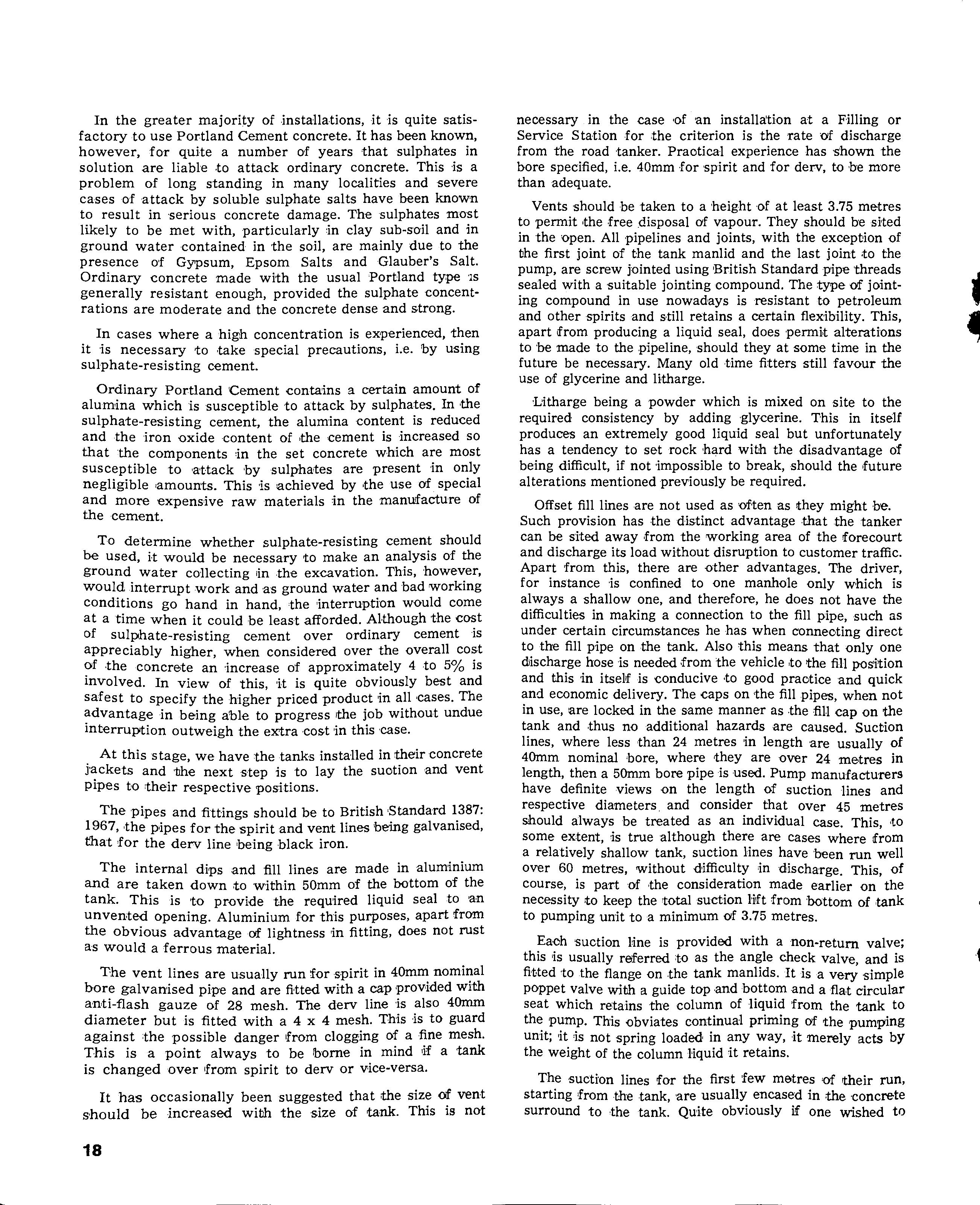
The vent lines are usually run for spirit in 40mm nominal bore galvanised pipe and are fitted with a cap provided with anti-flash gauze of 28 mesh. The derv line is also 40mm diameter but is fitted with a 4 x 4 mesh. This is to guard against :the possible danger lfrom clogging of a fine mesh. This isa point always to be iborne in mind ,if a tank is changed over from spirit to derv or vice-versa.
It has occasionally been suggested that the size of vent should be jncreased wibh the size of tank. This is not necessary in the case of an installation at a Filling or Service Station for the criterion is the rate 'Of discharge from the road tanker. Praotical experience has shown the bore specified, i.e. 40mm for 'spirit and for derv, to he more than adequate.
Vents should be taken to a height of at least 3.75 metres to permit ,the free .disposal of vapour. They should be si,ted in the 'Open. All pipelines and joints, with the exception 'Of bhe first joint of the tank manlid and the last joint to the pump, are screw jointed using British Standard pipe threads sealed with a suitable jointingcompound. The type of jointing compound in use nowadays is resistant to petroleum and other spirits and still retains a certain flexibility. This, apart from producing a liquid seal, does permit alterations to be made to the pipeline, should they at some time in the future be necessary. Many old ,time fitters still favour the use of glycerine and litharge.
Utharge being a powder which is mixed on site to the required consistency by adding 'glycerine. This in itself produces an extremely good liquid seal but unfortunately has a tendency to set rock hard with the disadvantage of being difficult, if not impossible to break, should the future alterations mentioned previously be required.
Offset fill lines are not used as 'Often as they might be. Such provision has the distinct advantage that the tanker can be sited away from the 'Working area of the forecourt and discharge its load without disruption to customer traffic. Apart from this, there are other advantages. The driver, for instance is confined to one manhole only which is always a shallow one, and therefore, he does not have the difficulties in making a connection to the fill pipe, such as under certain circumstances he has when connecting direct to the fill pipe on the tank. Also this means that only one dJischarge hose is needed from the vehicle ,to the fill pos'ition and this 'in itself is conducive to good praotice and quick and economic delivery. The caps on the fill pipes, when not in use, are locked in the same manner as .the fiU cap on the tank and ,thus no additional hazards are caused. Suction lines, where less 'than 24 metres 'in length are usually of 40mm nominal bore, where they are 'over 24 metres in length, then a 50mm bore pipe is used. Pump manufacturers have definite views on the length of suction lines and respective diameters, and consider that over 45 metres should always be treated as an individual case. This, ,to some extent, is true 'although there are cases where from a relatively shallow tank, suction lines have been run well over 60 metres, without difficulty in discharge. This, 'Of course, is part of the consideration made earlier on the necessity to keep the t'Otal suction Hft from 'bottom of ,tank to pumping unit toa minimum of 3.75 metres.
Eaoh suotion line is provided with a non-return valve; this 'is usually referred to as the angle check valve, and is fitted to the flange on .the tank manlids. It is ,a very simple poppet valve with a guide top ,and bottom ,and a flat circular seat which retains the column of liquid from the tank to the pump. This obviates c'Ontinual priming ()If the pumping unit; ,it is not spring loaded in any way, -it merely acts by the weight of the column liquid it retains.
The suction lines for the first few metres 'Of their run, starting from the tank, 'are usually encased in the concrete surround to ,the tank. Quite obviously if one wished t'O
install an additional suction line at a future date, some unnecessary difficulty would be encountered. This can quite easily be overcome 'by providing at the time of ,the initial installation additional suction lines fitted to the tank manlid and blanked off in the soft ground outside the limits of the concrete surround, It is good practice to provide such an area often known as an exchange pit, and there to terminate all additional suction lines from the tank 'and any future lines which have been provided to the pump islands themselves. Quite often this area, which takes the shape of a trench when excavated, possibly 1 metre deep by 700mm wide by the length of the tankage installation, is backfilled with sand to permit easy excavation.
Suction, vent and offset fill Hnes all require to be supported throughout their underground run. It is usual to provide a trench in which the pipes run and for the pipes themselves to be supported 'in a temporary fashion until after they have been completed and tested, then they can be surrounded with fine concrete, it being usual to provide a minimum cover af 100mm -in all directions. This specification is ideal for Hnes on the forecourt, but where a line is running in soft ground, it 'is usually only necessary to take out a trench and surround the pipes with sweet sand. It is essential that the pipes are protected 'in some way or ather for not only are they susceptible to the pressure of forecourt traffic, but also to corrosive agencies in the ground. Clay and ash have a particularly detrimental effect on the life of a pipe.
At the other end of the suction line from the tank, with which we have just been dealing, we have the pump island. The normal pattern of pump island has a cavity below ground level to permit joints to be made in the suction lines and electrical cables to be drawn -in, finished off at forecourt level with a concrete plinth of substantial construction. Openings are left in the plinth so that the Hnes and cables may be taken up into the pump body. It has been suggested that the cav1ty under each pump should be filled in some way or other to guard against possible leakage.
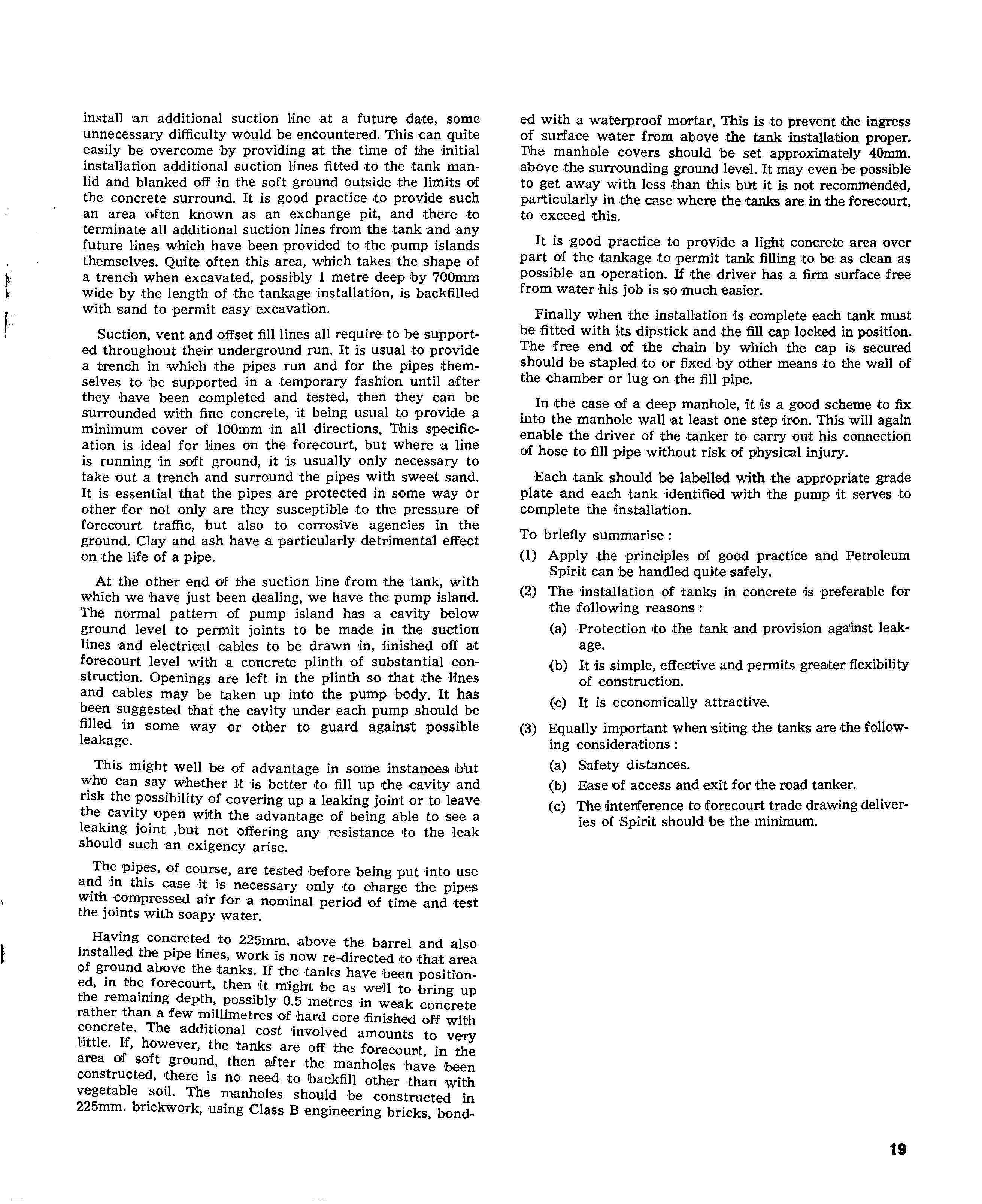
This might well be of advantage in some instanceS! but who can say whether it is better to fill up the cavity and risk the possibility of covering up a leaking jOint oar to leave the cavity open with the advantage 'Of being able to see a leaking joint ,but not offering any resistance to the leak should such -an exigency arise. pipes, of 'course, are tested -before being put into use and m this case it is necessary only to oharge the pipes with compressed air for a nominal period of ,time and test the joints with soapy water.
Having concreted to 225mm. above the barrel and also installed the pipe '!'ines, work is now re-<iirected to that area of g:ound above the tanks. If the tanks have been positioned, 10 then 'it might be as We'll to bring up the remammg depth, possibly 0.5 metres in weak concrete rather than a few millimetres -of hard core ,finished off with The additional cost 'involved amounts to very l'lttle. If, however, the tanks are off the forecoul't, in the area of soft ground, then after the manholes have been constructed, ·there is no need to ibackfill other than with vegetable soil. The manholes should be constructed in 225mm. brickwork, using Class B engineering bricks, bonded with a waterproof mortar. This is to prevent the ingress of surface water from above the tank installation proper. The manhole covers should be set approximately 40mm. above ,the surrounding ground level. Lt may even be possible to get away with less ,than this but it is not recommended, particularly in -the case where the tanks are in the forecourt, to exceed this.
It is good practice to provide a light concrete area over part of the tankage to permit tank filling to be as clean as possible an operation. If the driver has a firm surface free from water his job is so much easier.
Finally when the installation is complete each tank must befitted with its dipstick and the fill cap locked in position. The free end of the cha:in by which the cap is secured should be stapled to or fixed by other means to the wall of the ,chamber or lug 'On -the fill pipe.
In ,the case 'Of a deep manhole, it is a good scheme to fix into the manhole wall at least one step iron. This will again enable the driver of the tanker to carry out his connection of hose to fill pipe without risk of physical injury.
Each tank should be labelled with ,the appropriate grade plate and each tank identified with the pump it serves to complete the installation. T'O briefly summarise: (1) Apply the principles of good practice and Petroleum 'Spiritcanbe handled quite safely. (2) The 'installation of tanks in concrete is preferable for the following reasons: (a) Protection to the tank and provision aga:inst leakage. (b) It is simple, effective and permitsgre<l!ter flexibility of <:onstruction. (<:) It is economically attractive. (3) Equally important when 'Siting the tanks are the follow'ing considerations : (a) Safety distances. (b) Ease of 'access and exit for the road tanker. (c) The interference to forecouIi: trade drawing deliveries of Spirit should be the minimum.
Fiberglas Reinforced Underground Tanks for Storage of Gasoline
Dr. N. Sprecher, Project Manager, Tank!s and Pipes, Owens·Corning Fibreglas
INTRODUCTION Since its founding in 1938, Owens-Corning Fiberglas CorporDration Research, Development and Marketing has created new products for the construction industry to provide savings in installation, operating and maintenance costs. Owens-Coming today has annual sales in excess of $500 minion.
Capitalising on ·the inherent properties of fiberglas products, thousands of applications have been discovered for this unique man-made material. Utilised as reinforcement fDr resins -it has stimulated the development of one of the fastest growing industries in the world today, fiberglasreinforced plastics (FRP). FRP will not corode nor contaminate andtherefDre meets the present day needs for protection of tile environment. To develop the products, mass production manufacturing methods and markets, Owens-CDming Fiberglas Corporation has pioneered in the research and development of fibreglass products and has engaged 'in specific area's of FRP fabrication.
Particularly, in 1963, Owens-Coming 'initiated 'a research and development programme to develop a non-corroding underground storage tank to meet the petroleum industry's needs lforcorrosion and contamination-free storage at service stations. Having successfully developed the first underground FRP tank, Owens-Corning established the non-corrDsive products division in 1965 to market the product.
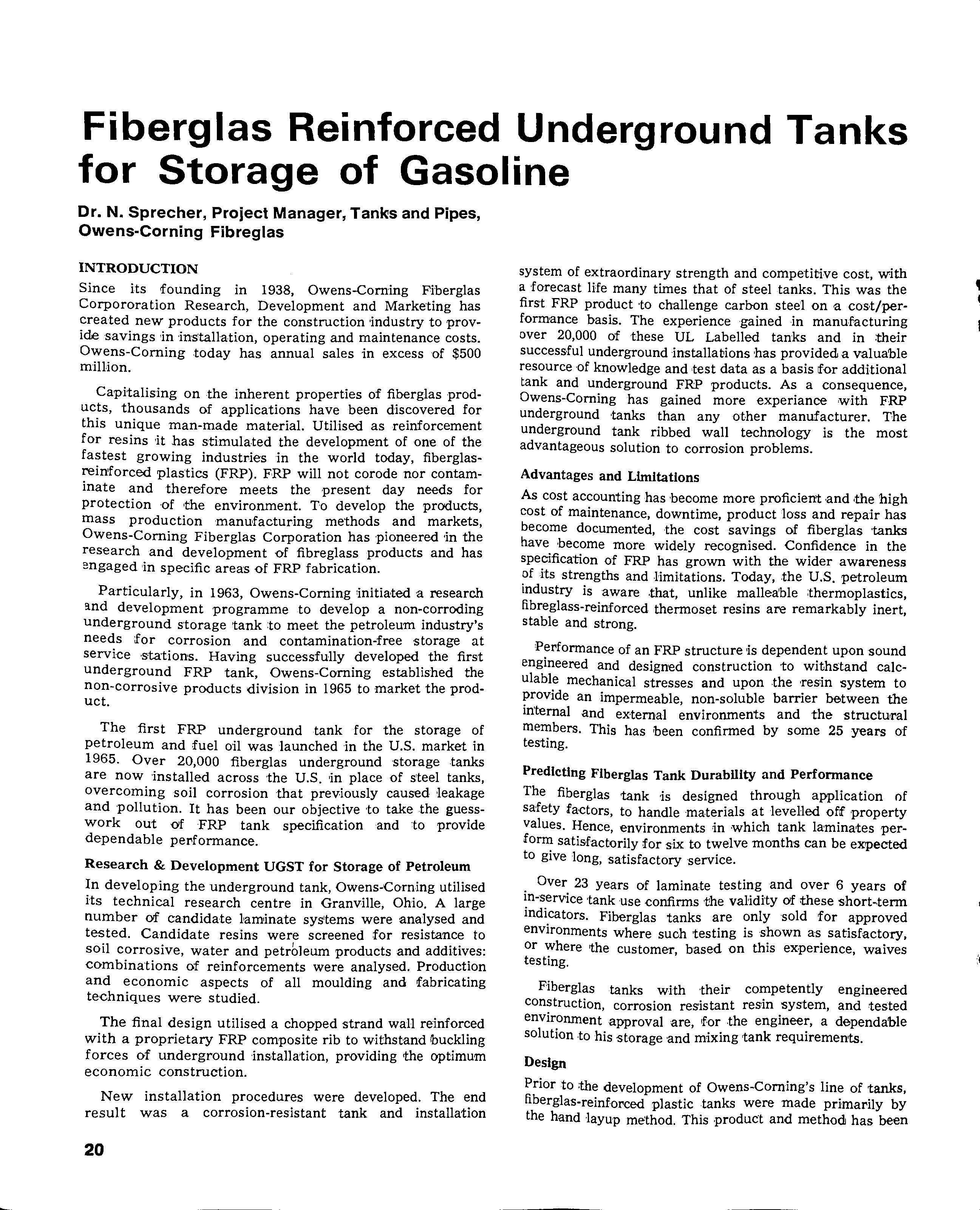
The first FRP underground tank for the storage of petroleum and fuel oH was launched in the U.S. market in 1965. Over 20,000 fiberglas underground storage tanks are now installed across the U.S. in place of steel tanks, overcoming soil corrosion that previously caused Ieakage and pollution. It has been our objective to take the guesswork out of 'FRP tank specification and to provide dependable peI'formance. Research & Development UGST for Storage of Petroleum In developing the underground tank, Owens-Corning utilised its technical research centre in Granville, Ohio. A large number of candidate loaminate systems were analysed and tested. Candidate resins were screened for resistance to sDil corrosive, water and petroleum products and additives: cDmbinatiDns of reinforcements were analysed. Production and economic aspects of all moulding and fabricating techniques were studied.
The final design utilised a chopped strand wall reinforced with a proprietary FRP composite rib to withstand /buckling forces of underground installation, providing the optimum econ'Omic c'Onstruction.
New installati'On procedures were developed. The end result was a corrosion-resistant tank and installation system of extraordinary strength and competitive cost, with a forecast life many times that of steel tanks. This was the first FRP product to challenge carbon steel on a cost/performance basis. The experience gained in manufacturing 'Over 20,000 of these UL Labelled tanks and in their successful underground installallions has provided a valuable resource of knDwledge and 'rest data as a basis for additional tank and underground FRP products. As a consequence, Owens-Corning has gained mDre experiance with FRP undergrDund tanks than any other manufacturer. The underground tank ribbed wall technology is the most advantageous sDlution to corrosion problems.
Advantages and Limitations As cost accDunting has heoome more proficient and ,the high cost of maintenance, downtime, product loss and repair has becDme documented, the cost savings of fiberglas tanks have become more widely recognised. Confidence in the specification of FRP has grown with the wider awareness 'Of its strengths and limitations. Today, the U.S. petroleum industry is aware ,that, unlike malleable :thermoplastics, fibreglass-reinforced thermoset resins are remarkably inert, stable and strDng.
Performance of an FRP structure is dependent upon sound engineered and designed construction t'O withstand calculable mechanical stresses and upon ·the Tesin system to prDvide an impermeable non-soluble barrier between the internal and and the struoturoal members. This has been confirmed by some 25 years of testing.
Predicting Flberglas Tank DurabUlty and Performance The fiberglas tank is designed through application of safety factors, tD handle materials at levelled off property values. Hence, environments in which tank laminates perform satisfactorily for six to twelve months can be expected to give long, satisfactDry service. . Over 23 years of laminate testing and over 6 years of m-service tank use confirms the validity of these indicators. Fiberglas tanks are only sold for approved environments where such testing is shown as satisfactory, or the customer, based on this experience, waives testmg.
Fiberglas tanks with their competently engineered construction, corrosion resistant resin system, and tested environment approval are, for the engineer, a dependable solution tD his storage 'and mixing tank requirements. Design Prior to the development of Owens-Corning'S line of tanks, fiberglas-reinforced plastic tanks were made primarily by the hand layup method. This product and method has been
developed 'into the NBS voluntary products standard PS 1569. It was evident to Owens-Corning fiberglas that the manufacturing advances provided by filament winding offered superior performance advantages. So it was in this new, 'Second Generation' area that Owens-Corning decided to concentrate its efforts.
This new approach allowed greater control of the manufaoturing process for increased product uniformity and quality. The use of filament winding and automated equipment permitted material and other cost reductions to make these tanks an even better value in ,the market place.
As a result, Owens-Corning developed design criteria and standards fora new generation of fiberglas tanks: the industrially produced FRP UGST for the storage of petroleum products.
Due to long term Ioading 'requirements and 'the importance of the corrosion liner in the tank performance, design properties were determined using dynamic loading with 'failure' defined not as ultimate failure, but rather when the corrosion liner cracked--exposing the strength member to the chemical stored. Thus, the controlling design parameter is allowable tens.iJe strain 'Of the corrosion liner. Cyclic pressure tests were used to determine this allowable tensile strain. Scale model tanks were tested at pressures ranging from 150-2,000 psi,up to 2,500,000 cycles and lining failure indicated by a leak detector wound between chopped strand and filament wound layers. Safety factors to allow for chemical and aging effects, were then applied to both allowable tensile modulus and strain to arrive at a design figure.
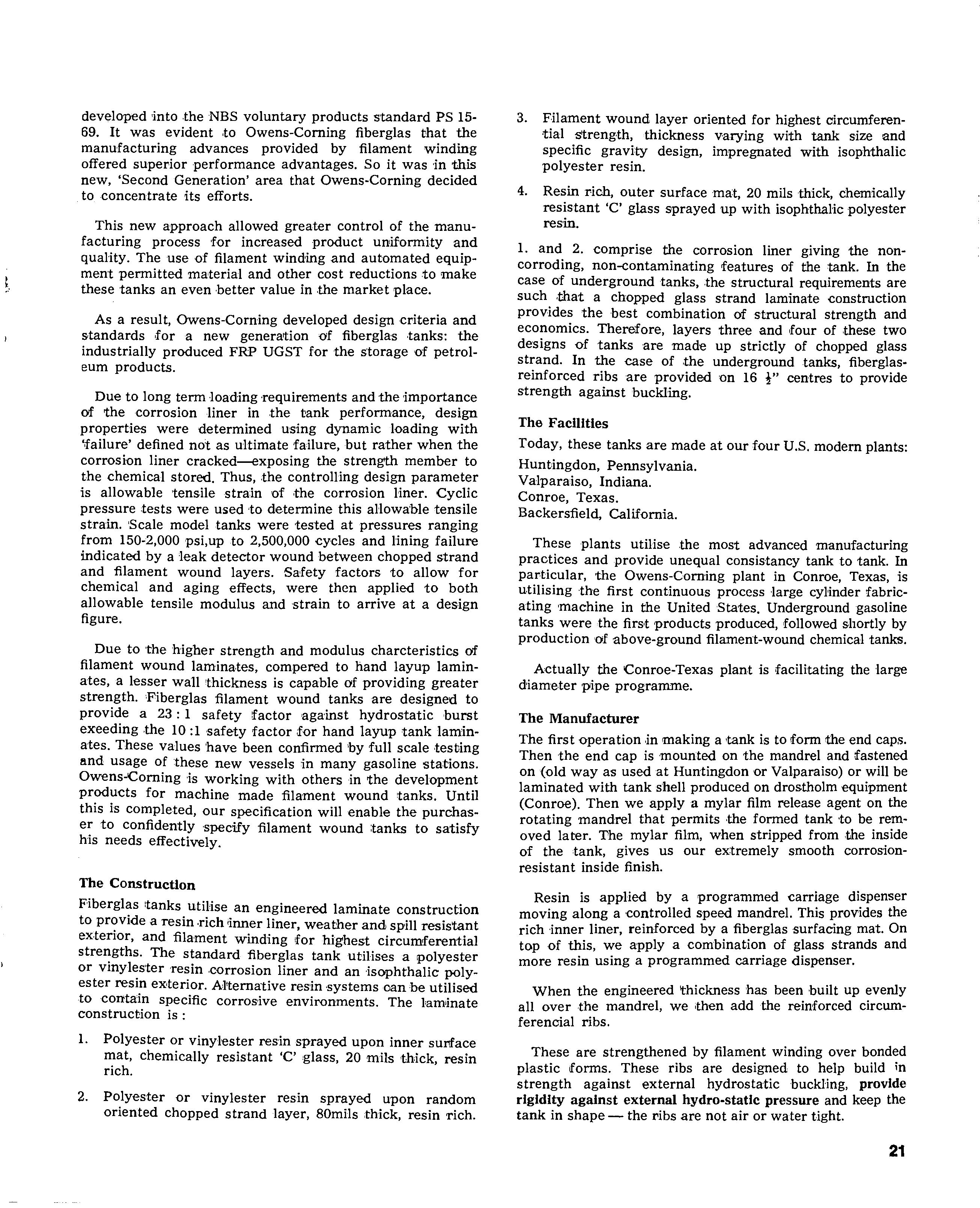
Due to the higher strength and modulus charcteristics of filament wound laminates, compered to hand layup laminates, a lesser wall thickness is capable of providing greater strength.,piberglas filament wound tanks are designed to provide a 23: 1 safety factor against hydrostatic burst exeeding ,the 10:1 safety factor for hand layup tank laminates. These values have been confirmed 'by full scale testing and usage of these new vessels in many gasoline stations. Owens-Corning is working with others in the development products for machine made filament wound tanks. Until this is completed, our specification will enable the purchaser to confidently specify filament wound tanks to satisfy his needs effectively.
The Construction Fiberglas ttanks utilise an engineered laminate construction to provide a resin ,rich linner liner, weather and spill resistant exterior, and filament winding for highest circumferential strengths. The standard fiberglas tank utilises a polyester or vinylester resin ,corrosion liner and an 'isophthalic polyester resin ex,terior. Al'ternative resin systemsoan be utilised to contain specific corros'ive environments. The Iamlinate construc1Jion is :
1. Polyester or vinylester resin sprayed upon inner surtface mat, chemically resistant 'c' glass, 20 mils ,thick, resin rich.
2. Polyester or vinylester resin sprayed upon random oriented chopped strand layer, BOmils thick, resin rich. 3. Filament wound layer oriented for highest circumferential strength, thickness varying with tank size and specific gravity design, impregnated with isophthalic polyester resin.
4. Resin rich, outer sudace mat, 20 mils thick, chemically resistant 'c' glass sprayed up with isophthalic polyester res'in.
1. and 2. comprise the corrosion liner giving the noncorroding, non-contaminating features of the tank. In the case of underground tanks, .the structural requirements are such ,that a chopped glass strand laminate construction provides the best combination of structural strength and economics. Therefore, layers three and ,four of ,these two designs of tanks are made up strictly of chopped glass strand. In the case of the underground tanks, fiberglasreinforced ribs are provided on 16 tu centres to provide strength against buckling.
The Facilities Today, these tanks are made at our four U.S. modern plants: Huntingdon, Pennsylvania. Valparaiso, Indiana. Conroe, Texas. Backersfield, California.
These plants utilise the most advanced manufacturing practices and provide unequal consistancy tank to tank. In particular, the Owens-Coming plant in Conroe, Texas, is utilising the first continuous process large cyl'inder fabricating machine in the United States. Underground gasoline tanks were the first products produced, followed shortly by production '()If above-ground filament-wound chemical tanks.
Actually the Comoe-Texas plant is facilitating the large diameter pipe programme.
The Manufacturer The first operation ,in making a 'tank is to form the end caps. Then the end cap is mounted on the mandrel and :fastened on (old way as used at Huntingdon 'Or Valparaiso) or will be laminated with tank shell produced on dros,tholm equipment (Comoe). Then we apply a mylar film release agent on the rotating mandrel that permits ,the formed tank to be removed later. The mylar film, when stripped from ,the inside of the tank, gives us our extremely smooth corrosionresistant inside finish.
Resin is applied by a programmed carriage dispenser moving along a 'controlled speed mandrel. This provides the rich inner liner, reinforced by a fiberglas surfacing mat. On top of this, we apply a combination of glass strands and more resin using a programmed carriage dispenser.
When the engineered 'thickness has been built up evenly all over the mandrel, we then add the reinforced circumferendal ribs.
These are strengthened by filament winding over bonded plastic forms. These ribs are designed to help build in strength against external hydrostatic buckling, provide rigidity against external hydro-static pressure and keep the tank in shape - the ribs are not air or water tight.
At Huntington and Valparaison, after the tank half has been cured in an oven that comes down over the mandrel, the tank is removed from .the mould. Each half tank is identical in size and shape. This gives exellent volume control when tanks are joined. within plus or minus 1%.
At this point, the two halves of the tank are bonded together with eight layers of fiberglas and resins. This bond is stronger 'than the wall itself.
At Conroe, ,the drostholm tubular shells are cut at required length and the cnd caps are laminated on the sheH. The last born new non-corrosive products Backersfield plant (California) is now in producDion. Shells produced at Conroe, Texas, are cut lengthwise and shipped with FRP end caps to Backersfield where they are reassembled. The UL approved tanks are available in 1300, 4000, 6000, 8000, 10000 and 12000 gallon sizes at price very close to the 'one of application at Conroe (Texas).
Fittings are tapered to assure tight fit. These are shipped with cast iron bungs to protect .the threads, making pressure testing easier on 'the job site, and preventing foreign matter being thrown into the tank, final inspection at the plant assures they will be shipped with two 'threads showing. The tank is now measured at over 562 points, every 12 ins. between each rib to ascertain that it meets the thickness requirements. It is also tested to assure proper glass to resin ratios.
This is supplemented by ignition loss tests. As each tank is completed, it 'is tested under half an atmosphere of vacuum to assure structural integrity. Soaped 100%. Tank is then pressurised to 5 psi. This is held one hour to confirm that the 'tank is completely leakproof. The UL number appears on the top of every tank under the lift lug. The label is now being bonded in this location. The UL number is also stencilled on each tank end. This number is utilised as the tank number to make life easier for everyone.
Installation instructions and calibration charts are shipped along with the <tank.
Prior to installation in the hole, the tank is pressure tested to 5 psi to ,check ,against vandalism or mechanical abuse <that may have occured while ;the tank was waiting for installation.
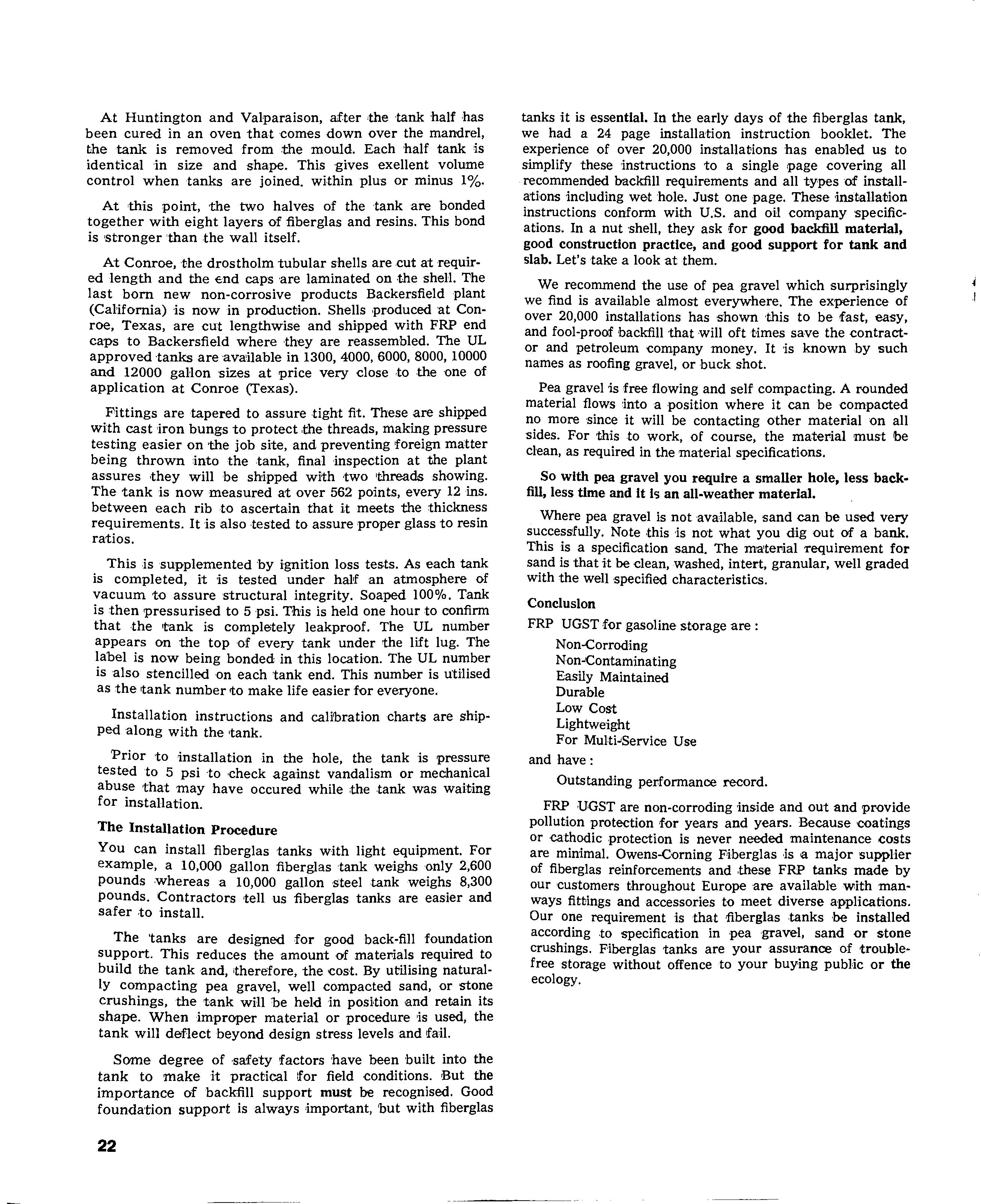
The Installation Procedure You can install fiberglas tanks with light equipment. For example, a 10,000 gallon fiberglas tank weighs only 2,600 pounds whereas a 10,000 gallon steel tank weighs 8,300 pounds. Contractors tell us fiberglas tanks are easier and safer ,to install.
The tanks are designed for good back-fill foundation support. This reduces the amount of materials required to build the tank and, 'therefore, the cost. By utilising naturally compacting pea gravel, well compacted sand, or stone crushings,the tank will be held in posi,tion and retain its shape. When improper material or procedure 'is used, the tank will deflect beyond design stress levels and fail.
Some degree of safety factors have been built into the tank to make it practical for field conditions. But the importance of backfill support must be recognised. Good foundation support is always important, but with fiberglas tanks it is essential. In the early days of the fiberglas tank, we had a 24 page installation instruction booklet. The experience of over 20,000 installations has enabled us to simplify these Instructions to a single 'Page covering all recommended backfill requirements and all types of installat10ns including wet hole. Just one page. These installaDion instructions conform with U.S. and oil company specifications. In a nut shell, they ask for good backfill material, good construction practice, and good support for tank and slab. Let's take a look at them.
We recommend the use of pea gravel which surprisingly we find is available almost everywhere. The experience of over 20,000 installations has shown ,this to be fast, easy, and fool-proof backfill 'that will oft Hmes save the contractor and petroleum company money. It is known by such names as roofing gravel, or buck shot.
Pea gravel is free flowing and self compacting. A rounded material flows !jnto a position where it can be compacted no more since it will be contacting other material on all sides. For this to work, of course, the material must be dean, as required in the material specificatiOns.
So with pea gravel you require a smaller hole, less backfill, less time and it ie;; an all-weather material.
Where pea gravel is not 'available, sand can be used very successfully. Note this js not what you dig out of a bank. This is a specification sand. The material Tequirement for sand is that it be clean, washed, intert, granular, well graded with the well specified characteristics. Conclusion FRP UGST for gasoline storage are:
Non-Corroding
Non-Contaminating
Easily Maintained
Durable
Low Cost
Lightweight
For MultiJService Use and have:
Outstanding performance record.
FRP UGST are non-corroding inside and out and provide pollution protection for years and years. Because coatings or ,cathodic protection is never needed maintenance costs are minimal. Owens-Ooming Fiherglas ,is a major SUpplier of fiberglas reinforcements and ,these FRP tanks made by our 'customers throughout Europe -are available with manways fittings and accessories to meet diverse applications. Our one requirement is that fiberglas tanks be installed according to specification in pea gravel, sand or stone crushings. Fiberglas tanks are your assurance of troublefree storage without offence to your buying pubHc or the ecology.
LIQUID PETROLEUM GAS
A Safety Conference on Liquid Petroleum Gas was recently held at Sulton Coldfield We present two of the papers presented. Further papers will be presented in our next issue.
D. E. TISDALE, Eltra Gas Ltd.
The object of this Conference is to discuss the aspect of L.P.G. used as a road vehicle fuel. The installation and engineering to the molor vehicle. Installation and dispensing of fuel from the filling station or roadside pumps, the correct procedure for maintenance and action necessary as a result of any accident or a similar occurrence.
L.P.G. automotive 'installations at this moment in 'time are governed by the Motor Vehicle Construction and Use Regulations, Schedule 3, and a voluntary Code of Practice issued by the LPGITA, As 'the ultimate in'terpretaHon of the Construction and Use Regulations with regard to converted vehicles varies from Looal Authority to Local Authority, we have numerous 'types of installations which are classed as legal in 'the loose term in the area in which they operate. Each person interpreting the law to suit as is convenient.
The most important aspect of a gas 'conversion to a motor vehicle is to ensure that 'the correct equipment 'is in fact available at the commencement of the conversion and that the fittings used are of a standard suitable for the condrtion under which they shall operate.
The most important working part of a conversion from the propUlsion point of view is of course the regulator vaporiser which is specifically mentioned in the Code of Praotice but is not covered by the Construction and Use Regulations except that in Part I of Schedule 3 it could be interpreted as a reducing valve, in which case altered propane regulators are illegal. In the Code of Practice, vaporisers are speoifically mentioned but of course again, there is no compulsion to comply with this regulation as at 'this date. Mention ,is made of a freeze plug or other means of relief for the internal expans'ion resulting from water freezing. From time to time, air from exhaust gas to air heat exohanger may be used and it specifically states that direct use of exhaust gas to vaporise L.P.G. is not recommended and there again, stating if exhaust gas is used, special provision for corrosIon protection should be made. Many of the standard vaporisers offered for sale by reputable Companies with minor adaptions are suggested for, use by direct passage of exhaus't gas as a means of heat. The Code of Practice Iays down regulations to seal the fuel supply once the engine has ceased to rotate. This is in different forms on many different types of vaporIser, some more or less effective than others. A specific mention is made of some form of electrical sensitive switch as an additional safeguard for this purpose, and although offered for sale these are not in some cases recommended by the suppliers of the equipment.
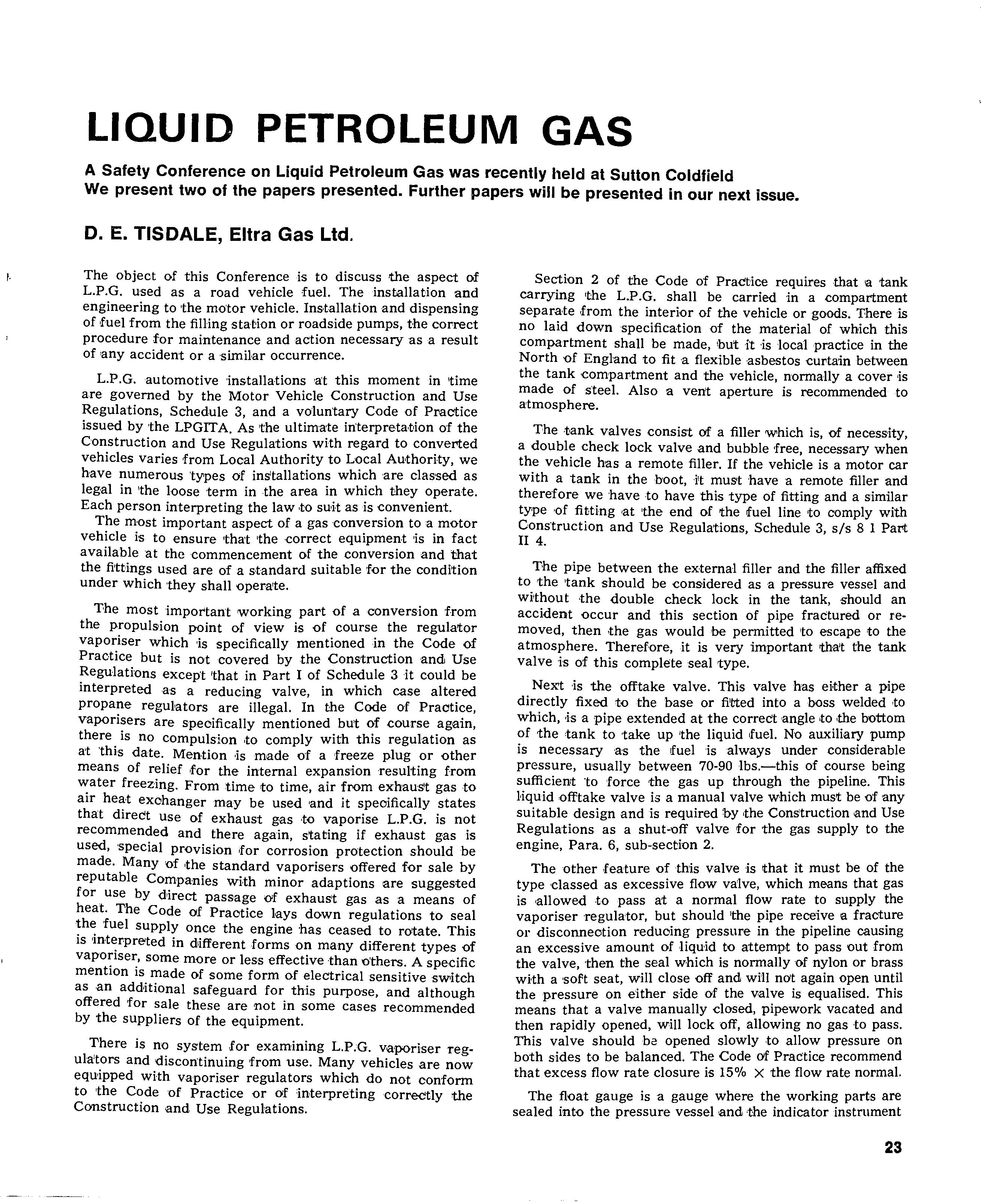
There is no system for examining L.P.G. vaporiser regula'tors and discontinuing from use. Many vehicles are now equipped with vaporiser regulators which do not conform to the Code of Practice or of 'interpretingcorreetly the Construction and Use Regulations.
Section 2 of the Code of Practice requires ,that a tank carrying 'the L.P.G. shall be carried in a compartment separate from the interior of the vehicle or goods. There is no laid down specification of the material of which this compartment shall be made, but it is local practice in the North of England to fit a flexible 'asbestos cUl'tain between the tank compal'tment and the vehicle, normally a cover ,is made of steel. Also a vent aperture is recommended to atmosphere.
The ,tank valves consist of a filler which is, of necessity, a double check lock valve and bubble free, necessary when the vehicle has a rem{)te filler. If the vehicle is a motor car with a tank in the hoot,i't must have a remote filler and therefore we have to have this type of fitting and a similar type 'Of fitting ,at 'the end of the fuel line to comply with Construction and Use Regulations, Schedule 3, sl'S 8 1 Part 11 4.
The pipe between the external filler and the filler affixed to the 'tank should be cons,idered as a pressure vessel and without ,the double check l{)ck in the tank, should an accident {)ccur and this section of pipe fractured or removed, then ,the gas would be permitted to escape to the atmosphere. Therefore, it is very important that the tank valve is of this complete seal type.
Next -is the offtake valve. This valve has e1ther a pipe directly fixed to the base or fl'tted into a boss welded ,to which, ,is a pipe extended at the correct 'angle ,to ,the bottom of the tank to take up the liquid fuel. No auxiliary pump is necessary as the fuel is always under considerable pressure, usually between 70-90 'lbs.-this of course being sufficient 'to force the gas up through the pipeline. This Hquid 'Offtake valve is a manual valve which must be of any suitable design and is required by .the Construction and Use Regulations as a shut-off valve for the gas supply to the engine, Para. 6, sub-sect:ion 2.
The other ,feature of this valve is that it must be of the type classed as excessive flow va'lve, which means that gas is ,allowed to pass at a normal flow rate to supply the vaporiser regulator, but should 'the pipe rece'ive a fraoture or disconneotion reduoing pressure in the pipeline causing an excessive amount of Uquid to attempt to pass out from the valve, then the seal which is normally of nylon or brass wi,th a sort seat, will close off and wi'll not again open until the pressure on either side ()If the v,alve is equalised. This means that a valve manually dosed, pipework vacated and then rapidly opened, will lock off, allowing no gas to pass. This valve should ba opened slowly to allow pressure on both sides t{) be balanced. The Code ()If Practice recommend that excess flow rate closure is 15% X the flow rate normal.
The float gauge is a gauge where the working parts are sealed into the pressure vessel and the indicator instrument
is driven by a magnet operating under a brass face. This is to comply with Section 7 of the Construchlon and Use Regulations. This valve Is ,a guide :and is not to be used as -the final indicator for filling.
The valve is a hydrostatic relief valve and is set normally at a safety relief pressure which is within the safety pressure design for tile L.P.G. vessel. When used on the vessel fitted internally to a vehicle, it is 'Obviously necessary to pipe away from this valve from the inside of the vehicle in a pipe of a size suitable to carry the capacity of the gas sh'Ould the pressure in ,the tank build up sufficieDJt to opera:te the relief valve. The circumstances for this effect would be severe, such as if the vehicle was involved in a fire causing the gas pressure to rise and open the valve. This would 'allow .the pressure to be relieved through 'the escape pipe and ,to ignite away from 'the side of the vehicle. If this condihlon is observed, 'then cold water applied directly to the 'tank would cool,adequately to anow this valve to close off. It is !therefore quite obvious that rubber piping, plastic piping or material which will support combustion is of no value for ,th'is type of ins'tanation.
The bleed valve or maximum liquid level indicator is a valve specifically designed to indicate that on filling, a tank has 'received its capacity of liquid gas. A probe extends into the vessel directly connected to a relief ,tube which passes 'out by ·the external filler and is opened whilst the tank is 'being filled. when the float gauge indicates an approximate 50% fill, and will release vapour ,to atmosphere. Once liquid gas ,is seen 'to leave this tube, filling should cease and 'then the valve closed. As this valve is only operational during filling, 'it is common pl"actice to use nonmetallic tubing as a pipe away, but again, non-combustible material would be more suitable but not necessarily a safer installation. The bore size to be below 1.5 mm.
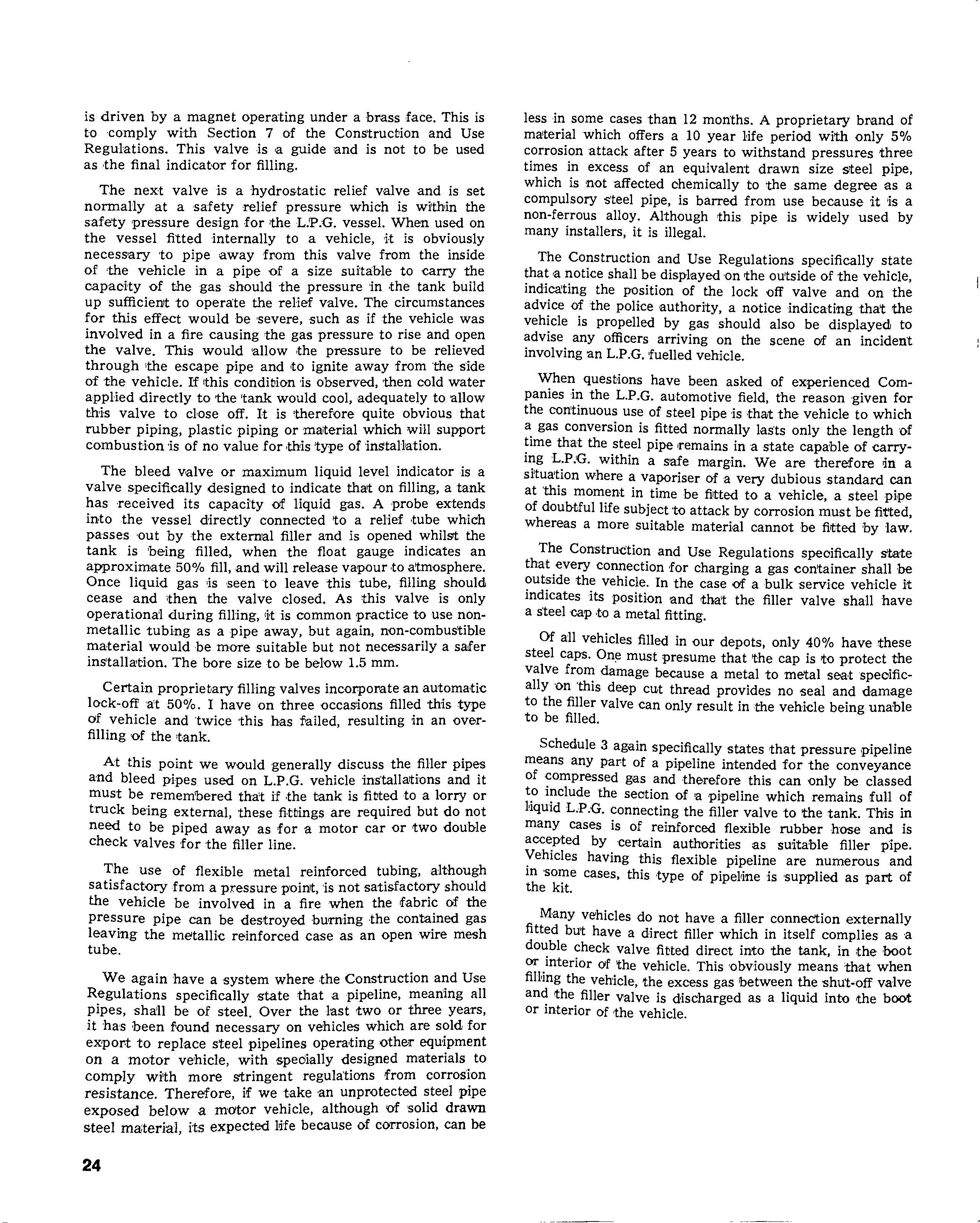
Certain proprietary filHng valves incorporate an automatic lock-off 'at 50%. I have 'On three occas!ions filled this type of vehicle and 'twice this has fiailed, resulting in an overfilling 'Of the 'tank.
At this point we would generally discuss the filler pipes and bleed pipes used on L.P.G. vehicle installations and it must be remem'bered that if the tank is fitted to a lorry or truck being extern-aI, these fittings are required but do not need to be piped away as for a motor car or two double check v'alves for the finer line.
The use of flexible metal reinfiorced tubing. although satisfactory from a pressure poin1t, 'is not satisfactory should the vehicle be involved in a fire when the fabric of the pressure pipe can be destroyed burning 'the contained gas leaving the metallic reinforced case as an open wire mesh tube.
We again have a system where -the Construction and Use Regulations specifically state that a pipeline, meaning all pipes, shall be of steel. Over the l'ast two or three years, it has been found necessary on vehicles which are sold for expor.f: to replace steel pipelines operating othea- equipment on a motor vehicle, with specially designed materials to comply wi'th more s'tringentregulations from corrosion resistance. Therefore, if we take 'an unprotected steel pipe exposed below a motor vehicle,although of 'Solid drawn steel ma:terial, its expected Hfe because of corrosion, can be less -in some cases than 12 months. A proprietary brand of material which offers a 10 year Hfe period with only 5% corrosion attack after 5 years to withstand pressures three times in excess of an equivalent drawn size steel pipe, which is not affected chemically to the same degree as a compulsory steel pipe, is barred from use because it is a non-ferrous alloy. Although this pipe is widely used by many installers, it is illegal.
The Construction and Use Regulations specifically state that a notice shall be dispI'ayed on the outside of the vehicle, indicating the position 'Of the lock off valve and on the advice of 'the police 'authority, a notice indicating that tile vehicle is propelled by gas should also be displayed to advise any officers arriving on the scene of an incident involving an L.P.G. fuelled vehicle.
When questions have been asked 'Of experienced Companies in the L.P.G. automotive field, the reason given for the continuous use of steel pipe is that the vehicle to which a gas conversion is fitted normally las'ts only the length 'Of time that the steel pipe in 'a state capa'ble of carrying L.P.G. within a s'afe margin. We are therefore qn a situation where a vaporiser of 'a very dubious standard can at 'this moment in time be fitted to a vehicle, a steel pipe of doubtful life subject to attack by corrosion must be fitted, whereas a more suitable material cannot be fitted 'by law.
The Construction and Use Regulations specifically S'tate that every connection for charging a gas container shall be outside the vehicle. In the case of a bulk service vehicle it indicates its position 'and that the filler valve shall have a s'teel cap .to a metal fitting.
Of an vehicles filled in cur depots, only 40% have these steel caps. On!'l must presume that the cap is '1'0 protect the valve from damage because a metal to metal sea-t speoifically on 'this deep cut thread provides no seal and damage to the filler valve can only result in the vehicle being unable to be filled.
Schedule 3 again specifically states that pressure pipeline means any pal't of a pipeline intended for the conveyance of compressed gas and therefore this can only be classed t? i?clude the section of 'a pipeline which remains fun of hqUld L,P.G. connecting the filler valve to the tank. This in many cases is of reinforced flexible rubber hose and is by 'certain authorities as suita:ble filler pipe. yehICles having this flexible pipeline are numerous and In 'some cases, this type of pipel1ne is 'supplied as part of the kit.
Many vehicles do not have a filler connection externally fitted but have a direct filler which in itself complies a's a double check valve direct into the tank, in -the boot or interior of the vehicle. This obviously means that when filHng the vehicle, the excess gas between the shut-off valve and the filler valve is discharged as a liquid into the boot or interior of the vehicle.
D. COMLEY, Esso Petroleum Company
As an oil company we are only directly involved in large bulk installations and not necessarily small ones as we only opemte four vehicles of minimum 13 tones -capacity. The safety features that apply to large bulk however, apply equally to ,the small ones and our experience over the last year leads us to believe that many small ins'taUations do not conform to the correct codes of practice. I shall discuss how small installations should be designed and what hazards they have to cater for.
When designing an L.P.G. storage plant the potential hazards involved must be considered 'and the design 'and iilstalla:tion of the plant must reduce such hazards to a minimum. What are these hazards? Firs,tly there are two L.P.G. gases, propane and hutane. I intend to concentrate purely on propane, this being the most popular fuel for automotive use. Tohe major point about propane is its low boiling point. This 'is so low that it exists as a vapour at normal ambient tempemtures. It 'Oan, however, he liquified by application of pressure or cooling and therefore we can transport it in liquid form. The boiling point of liquid propane 'is minus 45°C and you 'can imagine that is a most dangerous temperature to get liquid propane spilt on ones skin because it ,can 'give cold bums. In boiling, one gallon of propane will give 250 gaHons of propane vapour. Now the density of liquid propane vapour is 1 1 times heavier than thwt of air so it will tend to hug ground levels and ducts, etc. Your insulation has ,to be designed therefore so that if there is a vapour leak it can dissipa'te very quickly and not enter drains or other confined spaces. In Sltill air conditions concentration can remain in such enclosed spaces for quite a considerable time. On the other hand liquid propane 'is only half as dense 'as water so it will float. Also when you have a lliquid propane gas, jf it in a proportion between 2% 'and 10% in air, then you have a combustible mix:ture. Remember when you are designing an installation that propane vapour is coldest, but leaks can be detected by smell because oil companies do add a stenching agent. You can 'also see it, for it will cause icing on pipes adjacent to any leaks and can sometimes be seen as dancing vapour or 'in a moist atmosphere it will cause the formation of water vapour. Finally you have to remember that L.P.G. is nontoxic but as I said before, ,the spirit of L.P.G. liquid can in fact cause severe cold burns.
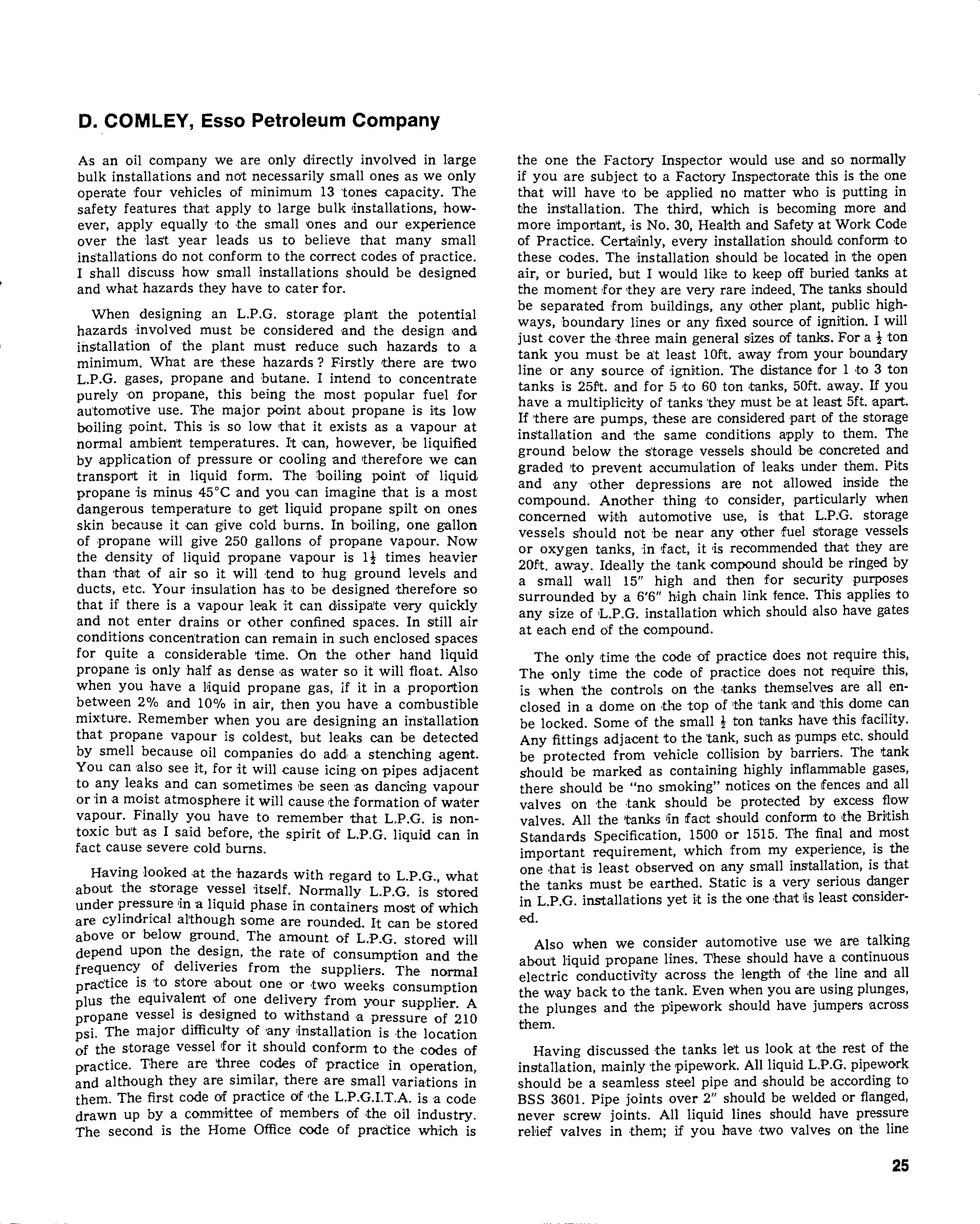
Having looked at the hazards with regard to L.P.G., what about the storage vessel itself. Normally L.P.G. is stored under pressure ,in a liquid phase in containers most of which are cylindri-cal although s'ome are rounded. It can be stored above or below ground. The amount of L.P.G. stored will depend upon the design, the rate of consumption and the frequency of deliveries from the suppliers. The normal practice is ,to store 'about one or two weeks consumption pluS one from your supplier. A propane vessel IS deSIgned to wIthstand a pressure of 210 psi. The major difficulty of 'any 'installation is ,the location of the storage vessel for it should conform to the codes of practice. Tohere are codes of practice in operation, and although they are SImIlar, there are small variations in them. The first code of practice of the L.P.G.I.T.A. is a code drawn up by a committee of members of the oil industry. The second is the Home Office code of practice which is the one the Factory Inspector would use and so normally if you are subject to a Factory Inspectorate this is the one that will have ,to be applied no matter who is putting in the installation. The thIrd, which is becoming more and more impoJ.1tant, ,is No. 30, Health and Sa:fety at Work Code of Practice. Certalinly, every installation should conform to these codes. The installation should be located in the open a:ir, or buried, but I would like 00 keep off buried tanks at the moment for ,they are very rare indeed. The tanks should be separated from buildings, any other plant, public highways, boundary lines or any fixed source of ignition. I will just cover the .three main general siizes of tanks. For a 1 ton tank yoOU must be at least 10ft. away from your boundary line or any source of ignition. The distance for 1 toO 3 ton tanks is 25ft. and for 5 to 60 ton .tanks, 50ft. away. If you have a multiplidty of tanks 'they must be at least 5lt. apart. If there are pumps, these are considered parot of the storage in5'tallation and the same conditions apply to them. The ground below the storage vessels should be ,concreted and graded ,to prevent accumulation of leaks under them. P1ts and any 'Other depressions are not allowed inside the compound. Another thing to consider, particularly when concerned w11lh automotive use, is that L.P.G. storage vessels should not he near any other fuel storage vessels or oxygen tanks, in fact, it 1s recommended that they are 20ft. away. Ideally the tank compound should be ringed by a small wall 15" high and then for security purposes surrounded by a 6'6" high chain link fence. This applies to any size of L.P.G. installation which should also have gates at each end of the compound.
The oOnly time the code 'of practice does not require this, The only time the code of practice does not requoire this, is when the controls on the ,tanks themselves are all enclosed ina dome on ,the top of 'rhe tank and 'this doOme can be locked. Some of the small loon tanks have this facility. Any fittings adjacent to the tank, such as pumps etc. should be protected from vehicle collision by barriers. The tank should be marked as containing highly inflammable gases, there should be "no smoking" notices on the fences and all valves on the ,tank should be protected by excess flow valves. All the 'tanks lin !fact should conform to ,the British Standards Specification, 1500 or 1515. The final and most important requirement, which from my. . is the one ,that is least observed on any small mstallatIon, IS that the tanks must be earthed. Static is a very serious danger in L.P.G. installations yet it is the one that lis least considered.
Also when we consider automotive use we are talking about liquid propane lines. These should have a continuous electric conductivity across the length of the line and all the way back to the tank. Even when you are using plunges, the plunges and the pipework should have jumpers across them.
Having discussed the tanks le't us look at the rest of the installation, mainly 'the pipework. All liquid L.P.G. pipework should be a seamless steel pipe and should be according to BSS 3601. Pipe joints over 2" should be welded or flanged, never screw joints. All liquid lines should have pressure reHef valves in them; if you have ,two valves on the line
you should have a pressure relief valve between them. It only requires a temperature rise of 10° to get something like 20,000 Ibs. pressure increase in the line, it is certainly a fantastic increase. With our own vehicles, we can make certain that when we have finished off-loading weaotually bend our hoses to make certain there is no liquid in them for we have had hoses split in the short distance from a customer 'to our terminal when liquid has been left in the lines. All underground pipes should be wrapped and also welded, you should only have welded joints underground and even then they should be regularly inspected because even with prop'I'ietary wrappings we have found corrosion taking place underground. Some lines have 'Corroded within a year of being put into the ground. Last but not least n1> galvanised pipe should be used. Having talked about 'storage facilities let us now consider operating them. T1> ensure maximum safety in the storage of L.P.G. the following points and procedures must be observed. I cannot stress these too strongly.
Firstly you must keep the storage area clean and free from weeds and any 'combustible materials. This is quite straightforward for one of the basic defences on any L.P.G. installation is th'all: we do not need to worry about the installation itself. We 'are worried about fires from adjacent buildings and areas and that is why weeds must not be allowed to encroach upon the compound itself. All pipework etc., should be protected from corrosion and where painted should be re-painted each year to prevent corrosion. This is very simple, but I would say again, not very well observed in some installations. All joints and flanges should be reguIoarly checked for leaks using a soap solution, a very simple 'operation but not always carried out. Tanks should be reguIoarly drained to remove heavy ends. You will cel'lt:ainly find industrial customers do this because 'they are handling a 11>t of L.P.G., some customers may take 200 or 300 tons of L.P:G. a week and they know the inconveniences caused if they get a heavy end build up. We find 'the small customer tends to completely ignore this, then suddenly realises, when he gets gunge coming out of the L.P.G. tank, that he has not drained it for two or three years.
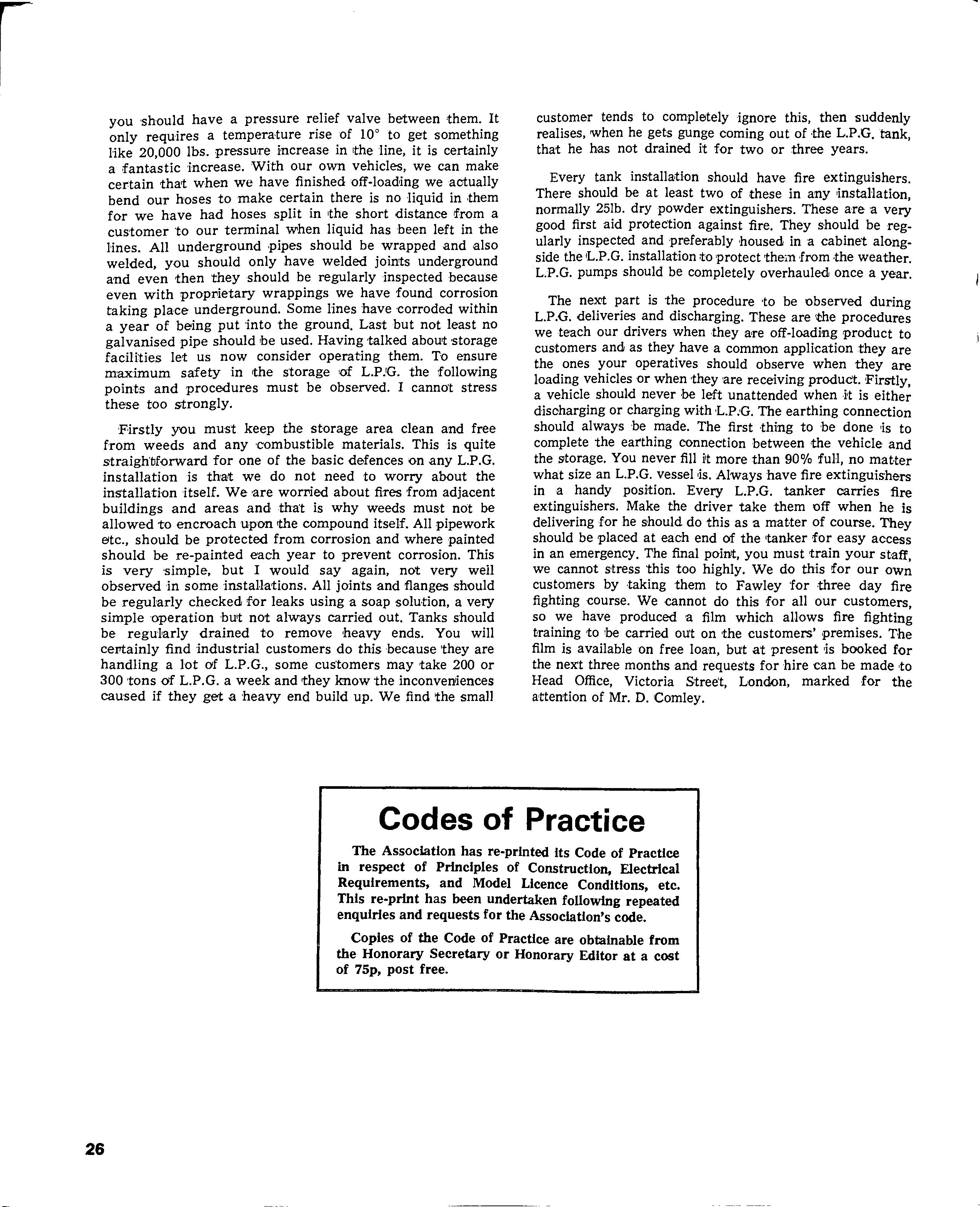
Every tank installati1>n should have fire extinguIshers. There should be at least two of these in any mstalIation, normally 251b. dry powder extinguishers. These are a very good first aid protection against fire. They should beregularly inspected and preferably housed in 'a cabinet alongside the 'L.P .G. installation to protect them from ,the weather. L.P.G. pumps should be completely overhauled once a year.
The nem part is the procedure to be observed during L.P.G. deliveries and dis'Charging. These are the procedures we teach our drivers when they a're off-loading product to customers and as they have a common appli'Cation they are the ones your operatives should observe when they are loading vehicles or when ,they 'are recetiving product. Firstly, a vehicle should never ,be left unattended when .jt is either discharging or cha'l"ging wIth L.P.G. The earthing connection should always 'be made. The first thing to be done 'is to complete the earthing connection between the vehicle and the storage. You never fill i't more than 90% full, no matter what size an L.P.G. vessel iis. Always have fire extinguishers in a handy position. Every L,P.G. tanker carries fire extinguishers. Make the driver take them off when he is delivering ,foor he should do this as a matter of course. They should be placed at each end of the tanker for easy access in an emergency. The final point, you must train your staff we cannot stress this too highly. We do this for our customers by taking them to Fawley for ,three day fire fighting course. We cannot do this for all our customers, so we have produced 'a film which allows fire fighting training to he carried out on the customers' premises. The film is available on free loan, but at present ,is booked for the next three months and requests for hire can be made ,to Head Office, Victoria Street, L'Onoon, marked f'Or the attention of Mr. D. Comley.
Codes of Practice
The Ass'Ociati'On has re-printed its Code 'Of Practice In respect 'Of Principles 'Of COnstruCtl'On, Electrical Requirements, and Model Licence C'Onditions, etc. This re-print has been undertaken f'OlI'Owing repeated enquiries and requests for the Ass'Ociation's code.
C'Oples 'Of the Code of Practice are obtainable from the H'Onorary Secretary 'Or Honorary Editor at a cost 'Of 75p, post free.
TECHNICAL CORNER
For a number of years this Journal published a series of technical articles by 'OUo'. These were greatly appreciated by our readers and we re. produce them duly updated under the appropriate pen name of PHOENIX.
HOW DID IT ALL BEGIN?
We are :told that the of human knowledge ,is doubling every seven years. Cons'ldered in this light the development of the petroleum industry has taken 'aeons.
Perhaps it all started in 1850 when Dr. Young took out his patent for paraffin (or oil containing paraffin) from the slow combustIOn of bituminous coal. The company he formed, Young's Paraffin Company, started the Scottish oil industry. WIth the finding 'of oil ,in the North Sea this industry now appears for rebirth.
In 1865 the first successful pipeline was constructed m America. In that year the total amount of petroleum products exported b.y the U.S.A. was approximately 25 million gallons, of which more than half was for Hlumination purposes.
Seven .years later, in 1872, the Bray ton Engine was m the U.S.A. The moving spirit of rh at engine was kerosme .. I.t was ?ot until the following year that Hock patented hiS gasolme engine in Vienna.
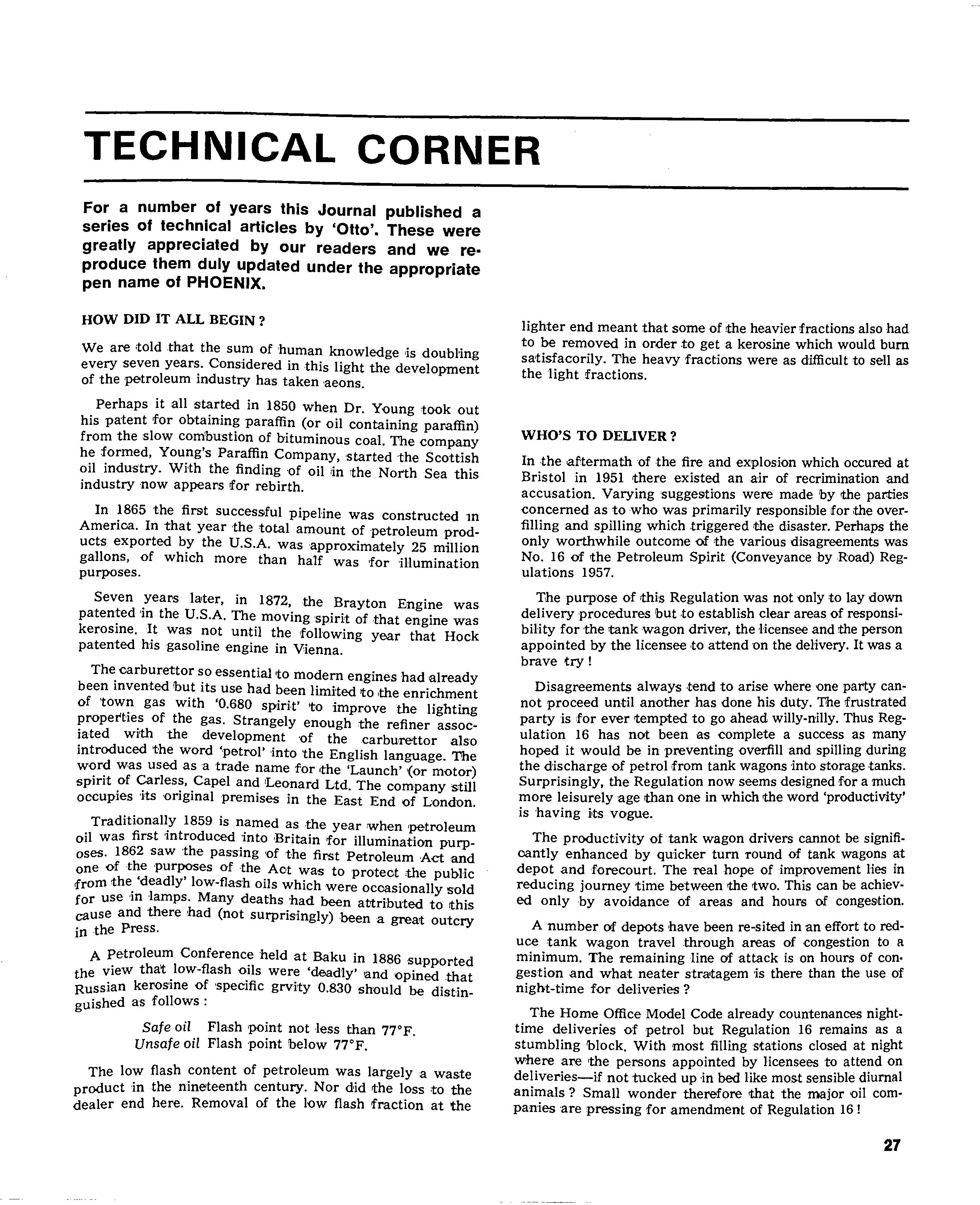
The. carburettor essential to modem engines had already been mvented but ItS use had been limited to the enrichment of toW? gas with '0.680 spirit' 'to improve the lighting ?ropeI'tIe.s of the gas. Strangely enough the refiner assocIated wrth the development of the carburettor also introduced 'Che word 'petrol' jnto the English language. The was used as a trade name 'for the 'Launch' (or motor) SpIrIt .of .Capel and Leonard Ltd. The company still occupies 'Its 'ongmal premises in the East End of London.
Traditionall.y 1859 is as ·the year when petroleum oil was first mtroduced :mto Britain for illumination purposes. 1862 saw the passmg of the first Petroleum Act and one of of the. Act ,:,as to proteot the public from the. deadly low-flash OIls which were occasionally sold for use m lamps. Many deaths had been attributed to this cause and there had (not surprisingly) been a great outcry in the Press.
A Petroleum Conference held at Baku in 1886 supported the view that .low-flash o.ils were 'deadly' 'and opined that Russian kerosme of 'speCific grvity 0.830 should be distinguished as follows: Safe oil Flash point not less than 77°F. Unsafe oil Flash point below 77°F.
The low flash content of petroleum was largely a waste product ,in the nineteenth century. Nor did the loss to the dealer end here. Removal of the low flash fraction at the lighter end meant that some of the heavier fractions also had to be removed in order to get a kerosine which would burn satisfacorily. The heavy fractions were as difficult to sell as the light fractions.
WHO'S TO DELIVER?
In the aftermath of the fire and explosion which occured at Bristol in 1951 there existed an air of recrimination and accusation. Varying suggestions were made by the parties concerned as to who was primarily responsible !for the overfilling and spilling which triggered the disaster. Perhaps the only worthwhile outcome od' the various disagreements was No. 16 of the Petroleum Spirit (Conveyance byRoad) Regulations 1957.
The purpose of this Regulation was not only to lay down delivery procedures but to establish clear areas of responsibility for 'the tank wagon driver, the Hcensee and the person appointed by the licensee to attend 'Cnthe delivery. It was a brave try!
Disagreements always ,tend to arise where one party cannot proceed until another has done his duty. The frustrated party is for ever tempted to go ahead willy-nilly. Thus Regulati'on 16 has not been as complete a success as many hoped it would be in preventing overfill and spilling during the discharge of petrol from tank wag'Ons 'into storage tanks. Surprisingly, the Regulation now seems designed for a much more leisurely age than 'One in which the word 'productivity' is having i.ts vogue.
The productivity of tank wagon drivers cannot be significantly enhanced by quicker turn round of tank wagons at depot and forecourt. The real hope of improvement lies in reducing journey time between the two. This can be achieved only by avoidance of areas and hours 'Of congestion.
A number of depots have been in 'an effort to reduce tank wagon travel ,through areas of congestion to a minimum. The remaining line of attack is on hours of congestion and what neater stra.tagem is there than the use of night-time for deliveries ?
The Home Office Model Code already countenances nighttime deliveries of petrol but Regulation 16 remains as a stumbling block. With most filling stations closed at night where are 'the persons appointed by licensees to attend on deliveries-if not tucked up -in bed like most sensible diurnal animals? Small wonder therefore that the major oil companies are pressing for amendment 'Of Regulation 16 !
What the companies have in mind is a recasting of the Regulation ,so as to make the tank wagon driver .wholly ponsible Ifor the aotual delivery of The hcensee wIll be responsible as at present for provldmg lo,osely be called the 'tool's for the job' on the filhng statlon ltself.
Many who 'suspect the wisdom of the divided responsibil ity ,inherent in the present system will w7 lcome the l?roposed change. Not ,least among the arguments m favour wlll be the suspicion that tank wagon drivers are far more competent in handling petrol than the inexperienced attendants who grace some filling stations.
Thus, there rose a great temptation to flout law. Perhaps flouters of the law were consoled by the Vlews of suc? well-known authorities as Sir Frederick Abel -and Slr Boverton Redwood, who as late as 1890 (in a report to H.M. Chief Inspector of Explosives) doubted whether lamp explosions were mostly caused by low-flash oil. This was the same Sir Frederick Abel who devised ,the two 'statutory tests which bear his name-firstly, the open cup (lOO°F.) test and latterly the compamble closed cup (73°F.) ,test, which is still used for statutory purposes in ,this country today.
In these random facts one sees the simple beginnings !iTom which has grown a complex international industry. ,Legislation in this country has kept pace with developments within ,the industry 'only because the temptation to control by regulation has been ,largely 'resisted. Wisely, use has 'been made of 'empowering' Acts of which the Petroleum (Consolidation) Act 1928 is the latest. These empowering Acts have enabled local authorities to consider each case and proposal un its merits and saved them from having to impose rigid restrictive regulations which of-ten become outdated and out-modedas rapidly as they are framed.
Report of the Consumer Services Committee of the Association of County Councils-October, 1974
Dangerous and Inflammable Substances A report by the Secretary about incidents brought to the Associ'ation's notice by the Berkshire, Hampshire and Nottinghamshire County Councils, toge'ther with the Flixborough disaster, concerning 'the need for improved inspect1:0'11 'and ,control of potential hazards and the administration of the petroleum Acts. The Cummittee noted tha,t I\:he Health and Safety at W'ork Act, and to a lesser extent the Control of Pollution Act, had p-rovided the framework fur more effective surveiUance in which it was vi'tal 'that county councils' existing expertise was to be fully employed, but that the details of the new controls under the Health and SaJfety a<t Work remained to be settled in Regulations. They sawconsoiderable room for improvement meanwhile in British Rails re'gulations governing the storage and transport of petroleum 'and a need fur new consulta:tive machinery with industry on standards in the enforcement of existing statutory controls over petroleum. Resolved:
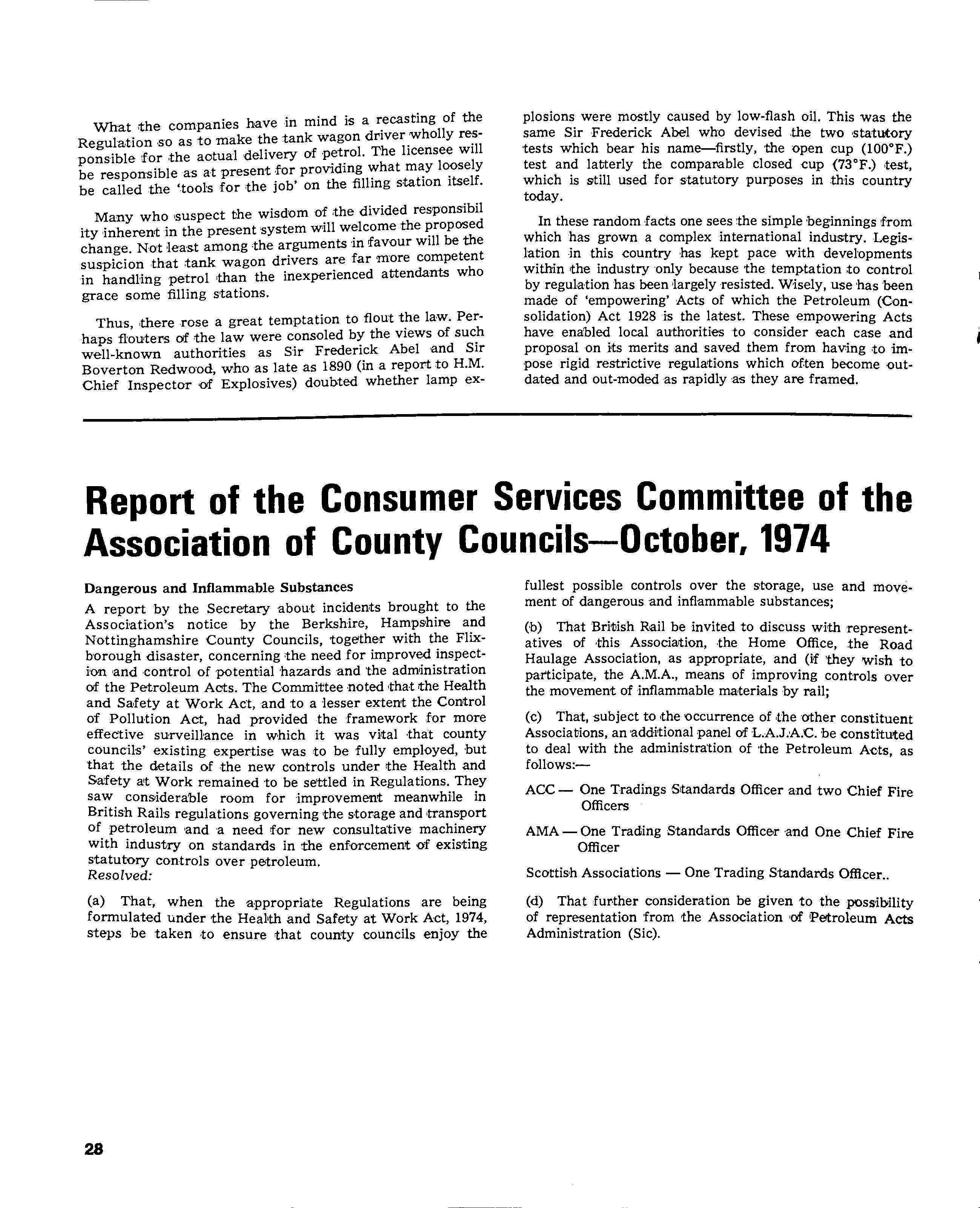
(a) That, when the appropri,a:te Regulations are being formulated under the Heal1th and Safety at Work Act, 1974, steps be taken to ensure that county councils enjoy the fullest possible controls over the s'oorage, use and movement of dangerous and inflammable substances; (ob) That British Rail be invited to discuss with representatives of this Association, ,the Home Office, the Road Haulage Association, as app-ropriate, and (if 'they wish to participate, the A.M.A., means of improving controls over the movement of inflammable materials by rail; (c) That. subject to -the occurrence of the other constituent Ass'ociabions, an 'additional panel of L.A.J.A.C. be constituted to deal with the administration of the Petroleum Aots, as foUows:-
ACC - One Tradings Standards Officer and two Chief Fire Officers
AMA - One Tradiing Standards Officer 'and One Chief Fire Officer
Scottish Associations - One Trading Standards Officer ..
(d) That further consideration be given to the possibiility of representation from the Association of Petroleum Acts Administration (Sic).
Telephone 021-236 0347
w. J. FINCH (Installations) Ltd.
Steam ing out and de-gassing petrol tanks; issuing gas free certificates Complete petrol and fuel oil bulk storage tank installations Petrol and fuel oil tank cleaning service Pressure tanks and pipe work
Heaton House, Camden St., Birmingham B13BZ
EAST MIDLANDS
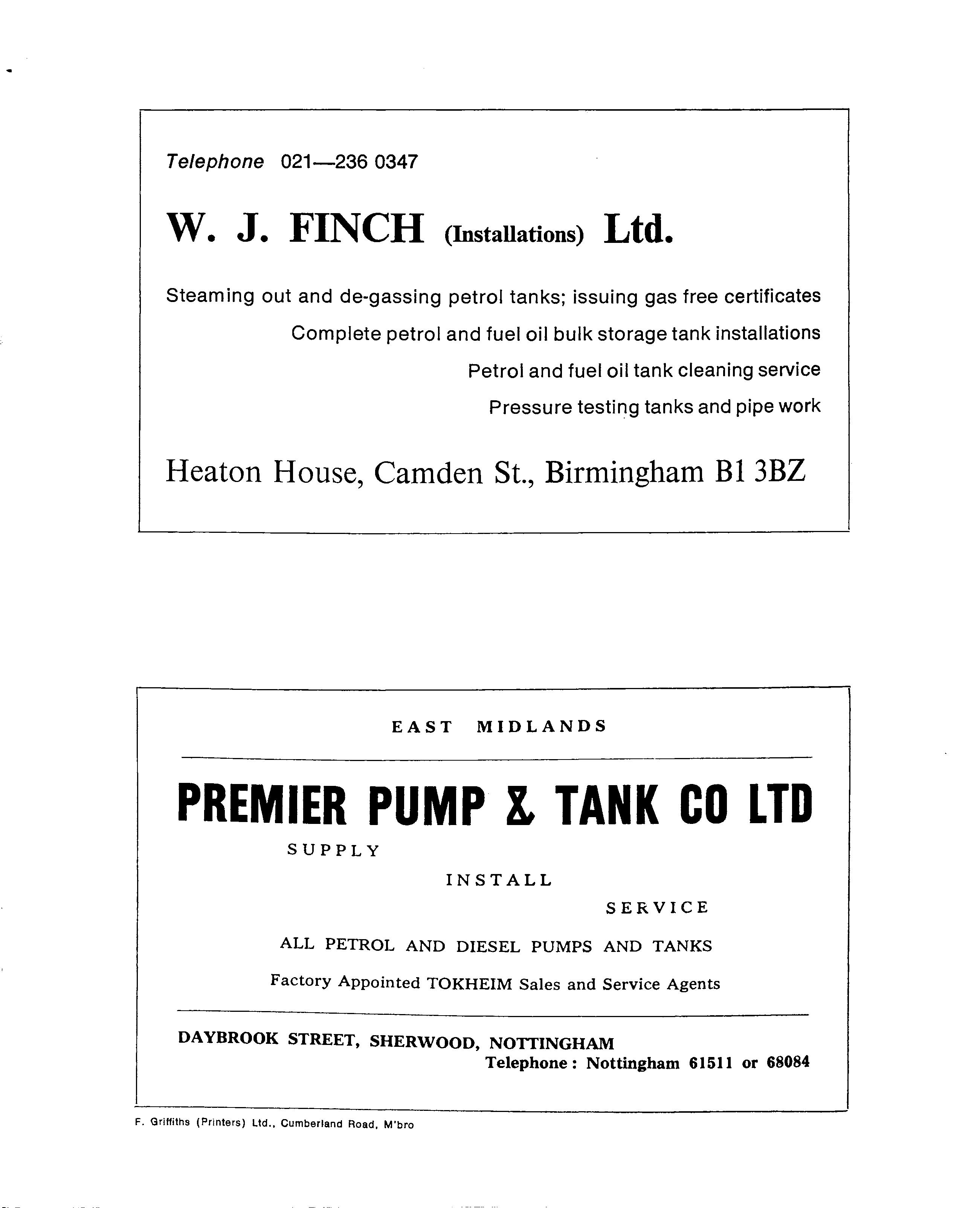
PREMIER PUMP X, TANK CO LlD
SUPPLY
INSTALL
SERVICE
ALL PETROL AND DIESEL PUMPS AND TANKS
Factory Appointed TOKHEIM Sales and Service Agents
DAYBROOK STREET, SHERWOOD, NOTIINGHAM Telephone: Nottingham 61511 or 68084