
13 minute read
THE NEED FOR LICENSING
by apeauk
As distinct from the concept of self-regulation the petroleum licence is an aide-memoir for the safe keeping of petroleum, enforceable at law. It can be tailored to reflect the conditions applicable to particular premises and updated to include alterations and modifications to the premises when they are completed to a prescribed standard.
It ensures that the premises are individually scrutinized and provides the medium for rapid feed-back and coordinated action in the event of:-
Advertisement
• suspected loss of stock.
• leakage.
• failure of items of equipment.
• problems associated with delivery and the associated conveyance regulations.
• complaints from members of the public.
In addition to the pro-active policy of close monitoring, the licence creates and maintains a continuing and all important dialogue regarding safety at the site for which it is issued. Such dialogue may involve the licensee, contractors, architects and oil company engineers. Dialogue with the licensee occurs at least once annually through the medium of the annual inspection, and transfer of the licence enables the new licensee to have an instant overview of the requirements specific to his new premises.
Dialogue promotes on-going co-operation between the
licensee and the licensing authority through the medium of the petroleum officer to maintain high, uniform standards of safety in the area concerned. (Appropriate revisions of legislation, previously mentioned, will ensure that uniformity is applied nationwide.)
In conclusion, I submit that the strengths of an updated licensing system would provide the necessary focus to optimize public safety, rather than the alternative selfmanagement system which would prove to be as expensive in application as it would be vague as a means of control.
by John Munday
In recent years, around the world, service station owners and operators have become increasingly concerned about the piping and tanks beneath the ground at their premises. There are, of course, excellent reasons for this interest.
People of the world, as well as environmental agencies have gained increasing insight into .the problems of soil contamination and its effects. Peoples and governments need to work together to protect the environment from contamination.
Smith Fiberglass Products Inc., from the U.S.A., has served the service station industry for more than 25 years. The Company has recently introduced a new concept in flexible dual-wall underground piping; the new design addresses problems faced by the owner/operator and helps fulfil governmental requirements.
The new piping system, SMITHFLEXn1 , consists of a 2inch primary pipe made entirely of 3 I 6L low carbon corrugated stainless steel. It is impermeable, nonpitting, and corrosion resistant. A corrugated 3-inch containment pipe is constructed of specially formulated polyethylene. The coITugated material has superior deformation resistance. Continuous Containment
When installation time is of concern to the owner/operator, a flexible piping system may be the choice. The corrugated stainless steel primary pipe is completely contained and secured within the outer polyethylene jacket of the SMITHFLEX System. The flexible system is 111stalled as a single unit. This reduces installation time and eliminates the need for joining the pipe outside of a tank or dispenser sump. From product dispenser to storage tank, all fittings are accessible from inside containment sumps. Testing and Quality Assurance
SMITHFLEX primary pipe is I 00 per cent pressure tested both before and after being contained in the outer polyethylene jacket. The outer jacket is I 00 per cent pressure tested after being extruded over the primary pipe.
The primary pipe, adapters and fittings are Listed by Underwriters Laboratories Inc. (UL) for use in the conveyance of petroleum products, alcohols and alcoholgasoline mixtures underaround at pressures up to I 00 psi at 110°F (43.3°C). The SMITH FLEX product meets UL vibration test requirements and is the first flexible piping to meet UL fire test requirements.
The SMITHFLEX primary pipe meets British Standards Institute BS 1449: Part 2 - Specification for stainless and heat-resisting steel plate, sheet and strip and BSI Standard 6501: Part I - Specification for corrugated hose assemblies. . SMTTHFLEX pipino b is desioned b for under<>rob und 111stallation in accordance with the National Fire Protection Association (NFPA) Code No. 30, Flammable and Combustible Liquids Code, and 30A, Automotive and Marine Service Station Code. Easy Installation
SMITHFLEX piping requires no special tools or equipment to install. The only tools needed are basic wrenches, hacksaws. drills. utility knives and tubing cutters. The system is easy to field-fabricate in all kinds of weather. Experience has shown that the product handles extremely well in cold temperatures. Product Differentiation
SMITHFLEX piping is impern~eable - very important
when considering environmental cntena.

The SMITHFLEX system is installed as one _cont i1~uou s . umt; no ·01·11ts J or fittin<>s o a.re required outside ot the dispenser or tank sumps.
SMITHFLEX piping is designed to handle ALL commercially available fuels and blends.
TI 1e t 1 sys en ca ' n . be installed . easily . in all . , kings of
h weat e1.. , d an ·t 1 1·equires only basic tools - no spec 1 1<1 . tools or equipment.
The product is available from a stable, innovative manufacturer ·t11 w1 · a lon 0 a history of excellent quality and service.
General Information . . . -
Smith Fiberglass Products l~ c . , is a lead 111g supplier ol composite products. notably t1berglass reinforced piping stems. The sy ranaina from company manufactures · 48 . 1 L-111ch through -me 1es tubulars . . 111 diamet in er. sizes . Smith Fib~ralass Products Inc. is a wholly-owned subsidiary of A. o. Sn~ith Corporation. For more information. contact:-
A o Smith [nternational Castle Hill House. Windsor. SL4 I PD. England. Tel: +44 17'53 840000. Fax +44 1753 83 111 3.
By Peter Edgington
I have read with some interest the correspondence generated between various manufacturers following the article on Overfill Prevention Devices published in issue 3 Volume 32 of the APEA Bulletin. Having noted some of the statements made I could not let them pass without adding a further view point and correcting some misconceptions. My own views are based on using such equipment in operational service and are the result of assessing, testing and recommending such equipment for a major oil company over a 25 year period worldwide. During this time I have examined systems operating on a variety of principles including mechanical, hydraulic, pneumatic, electrical and hybrids of them for installation in both above and below ground tanks and road tankers. In all cases the methods of operation are similar. Rising fuel level is detected in a tank or compartment by a sensing device which relays a signal to a shutdown valve. The valve may form either an integral part of the sensing unit or be located remotely from it.
The main issues raised in the correspondence are:
1. The relative merits of mechanical and electromechanical systems for overfill prevention.
2. The preferred point at which to shut down the flow of fuel should this be necessary.
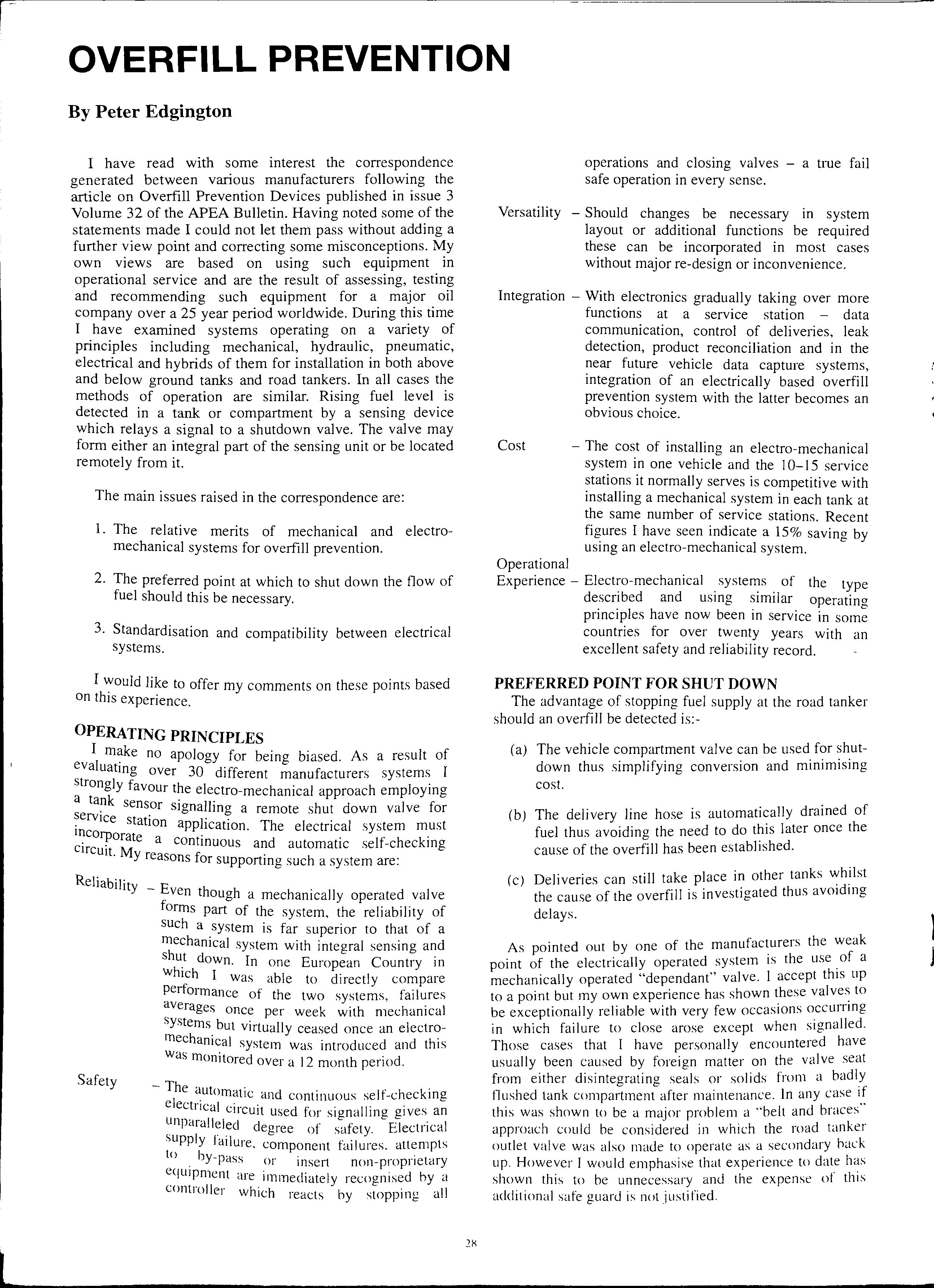
I "."ould like to offer my comments on these points based on this experience.
OPERATING PRINCIPLES
I make eval · uatmg no apology for being biased. As over 30 different manufacturers a result systems of I strongly favour the electro-mechanical approach employing a sensor signalling a remote shut down valve for station application. The electrical system must Ircuit My · a continuous and " reasons ior supporting automatic self-checking . such a system are: Reliability E ven though a mechanically operated valve
Safety forms part of the system, the reliability of such a system is far superior to that of a mechanical system with integral sensing and shu.t down. In one European Country in which I was able to directly compare performance of the two systems, failures averages once per week with mechanical systems but virtually ceased once an electromechanical system was introduced and this wasm · · onitored over a 12 month period.
- The and continuous self-checking electrical circuit used for signalling gives an unparalleled degree of safety. Electrical supply failure. component failures. attempts to . by-pass or insert non-proprietary equipment are immediately recognised hy a controller which reacts hy stopping all operations and closing valves -a true fail safe operation in every sense.
Versatility - Should changes be necessary in system layout or additional functions be required these can be incorporated in most cases without major re-design or inconvenience.
Integration - With electronics gradually taking over more functions at a service station - data communication, control of deliveries, leak detection, product reconciliation and in the near future vehicle data capture systems, integration of an electrically based overfill prevention system with the latter becomes an obvious choice.
Cost - The cost of installing an electro-mechanical system in one vehicle and the I 0-15 service stations it normally serves is competitive with installing a mechanical system in each tank at the same number of service stations. Recent figures I have seen indicate a 15% savincr by using an electro-mechanical system. 0
Operational Experience - Electro-mechanical systems of the type described and using similar operating principles have now been in service in some countries for over twenty years with an excellent safety and reliability record.
PREFERRED POINT FOR SHUT DOWN
The advantage of stopping fuel supply at the road tanker should an overfill be detected is:-
(a) The vehicle compartment valve can be used for shutdown thus simplifying conversion and minimising cost.
(b)
The delivery line hose is automatically drained of fuel thus avoiding the need to do this later once the cause of the overfill has been established.
Deliveries can still take place in other tanks the cause of the overfill is investigated thus avmdmg delays.
As pointed out by one of the the weak point of the electrically operated system 1s the use . of a mechanically operated "dependant" valve. I accept this up to a point but my own experience has shown t_hese to be exceptionally reliable with very few occas10ns o_ccurrmg in which failure to close arose except when signalled. Those cases that I have personally encountered have usually been caused by foreign matter on the valve seat from either disintegrating seals or solids from a badl_y_ flushed tank compartment after maintenance. In any case If this was shown to be a major problem a "belt and braces" approach could be considered in which the road tanker outlet valve was also made to operate as a secondary hack up. However I would emphasise that experience to date has shown this to be unnecessary and the expense of this additional safe guard is not justified.
(c)
A further point in support of using the compartment bottom valve for shut down is that on an average working day the valve would be operated for up to 2--4 loadings and as many off loadings. Compare this with the same incidence of use for an integrated mechanical valve in an underground tank which may only be required to operate should an overfill situation arise. It is this comparative lack of use which causes many of the operating problems with integrated mechanical valves.
STANDARDISATION AND SYSTEM COMPATIBILITY
The lack of standardisation and compatibility between electrical systems offered by different suppliers is of concern and a valid criticism but in practice it has been overcome because of the attractiveness of the electromechanical system and the advantages it offers.
To achieve cross compatibility between systems it is necessary for government agencies/petroleum industry or similar_ to issue a standard specification which all suppliers in a given country should meet. To date this has been impossible to achieve as equipment has come on to the market before the authorities have had time to react and produce such requirements. Once equipment is in use it is then too late to obtain acceptance of a standard specification as no manufacturer is neither prepared to back track or modify equipment in order to comply nor is he prepared to release proprietary information such as methods of electrical signalling which must be disclosed. In practice the problem has been solved by those oil companies who wish to ad?pt an system specifying their own reqmrements which have to be met by all those contracted to supply product to them.
However attempts are now being made in Europe to produce a common standard covering overfill prevention systems for use at service stations when offloadincr from road tankers, this is known as CEN 221. Yariousc- study groups have been formed to draft requirements for different applications and the U.K. are well represented on these groups.
I would now like to comment on specific points raised by the two mechanical equipment manufacturers which I find difficult to accept.
OPW claim that mechanical equipment has a low incidence of reported failure. This is not my experience, but perhaps the key word is "reported". Not all incidents are reported for obvious reasons as no driver will willingly do this as it reflects adversely on his competence to do his job. Invariably only major incidents get reported i.e. those involving a large fuel spillage or where the incident is witnessed by other parties. I am also surprised that the failures when diagnosed were invariably due to incompetent or incorrect installation. I find this statement extraordinary. Again my experience shows that poor installation only represents a small percentage of the total failure rate. What about failures in service caused by sticking/jamming of moving parts due to solids contamination, gum deposits from fuel, corrosion, floats losing buoyancy and ice built up in winter. On several occasions I have encountered problems at service station rebuilds in which a new mechanical device had to be replaced several times before an acceptable one was found so there could also be a quality control problem with some manufacturers.
The major criticism I have with mechanical systems is that when you connect up to off load a vehicle you never know with confidence whether the overfill device will operate when required to do so in an emergency. Some companies have attempted to introduce procedures which require a daily check of mechanical equipment by physically making sure that floats and moving parts_ etc are free to operate. However you can imagine the reception that such a procedure receives from fore-court personnel and the willingness to do this soon lapses once the problem of accessibility to do this have to be faced.
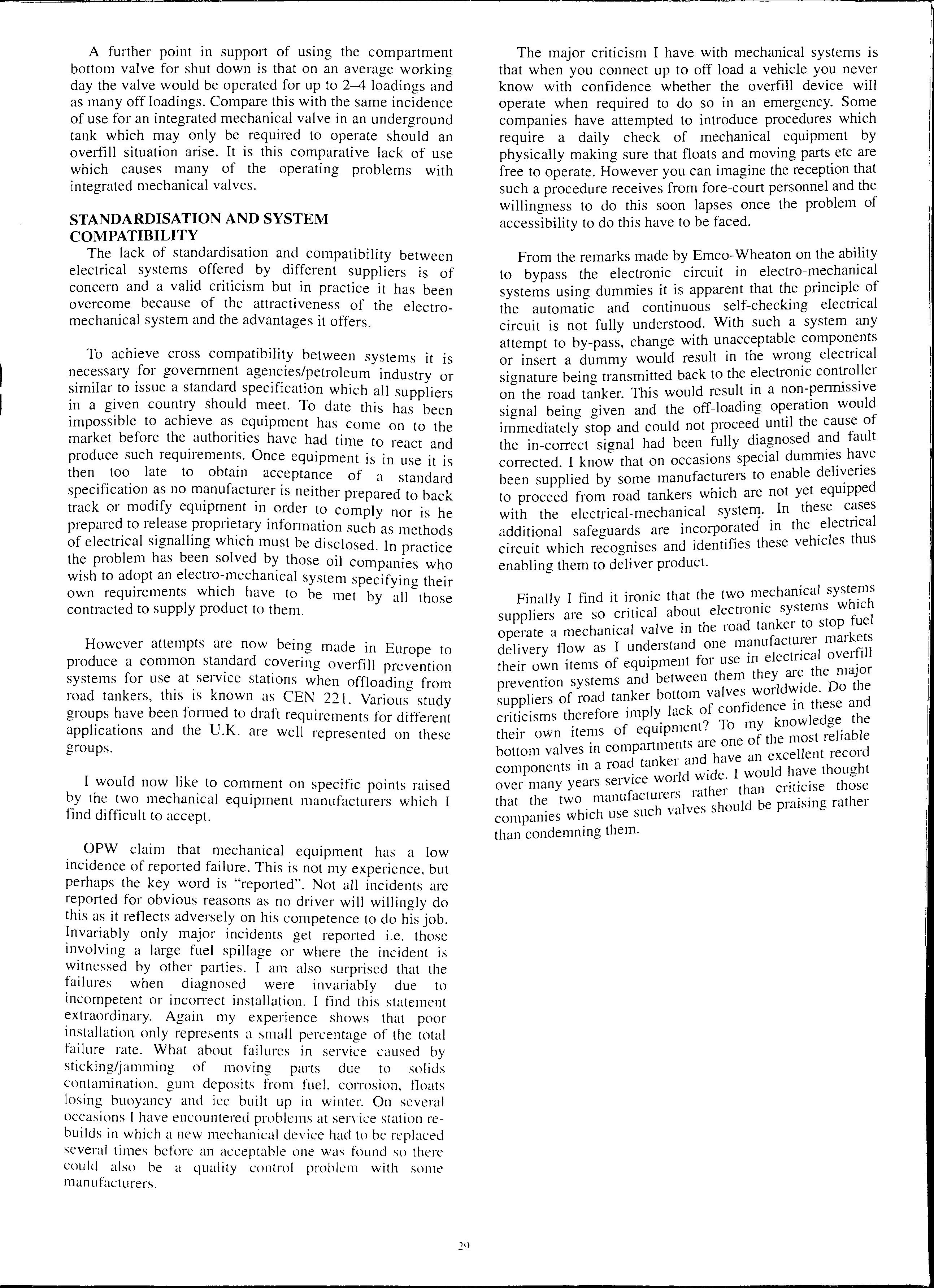
From the remarks made by Emco-Wheaton on the ability to bypass the electronic circuit in systems using dummies it is apparent that of the automatic and continuous self-checking electncal circuit is not fully understood. With such a system any attempt to by-pass, change with unacceptable or insert a dummy would result in the electncal signature being transmitted back to the on the road tanker. This would result m a non-permissive signal being given and the off-loading would immediately stop and could not proceed until the cause of the in-correct signal had been fully diagnosed fault corrected. I know that on occasions special been supplied by some manufacturers to enable to proceed from road tankers which are not yet eqmppe with the electrical-mechanical systell!· In these additional safeguards are incorporated in the _electnhca circuit which . d recogmses an "d t'fi s 1 en 1 ie these vehicles t us enablincr them to deliver product.
b
Finally I find it ironic that the two m_echanical suppliers operate a . . I b t lectromc systems w IC are so cnuca a ou e ., 1 . h d tanker to stop i ue mechanical valve m t e roa facturer markets delivery flow as I one ove1fill their own items of eqmpment for are the major prevention systems and between t I em eyldwide Do the . d k suppliers of roa er bottom , va ves wor f confidence in · these and criticisms therefore imply. lack 0 . f qmpment? their own 0 e nts .,... knowledcre the io my cone of the most reliable bottom valve_s m and have an excellent record components m a road tan Id ·de I would have thought vice wor WI • over many years ser ther than criticise those nufacturers ra .. that the two . ma h . 1 . should be prmsmg rather companies which use sue va ves than condemning them.