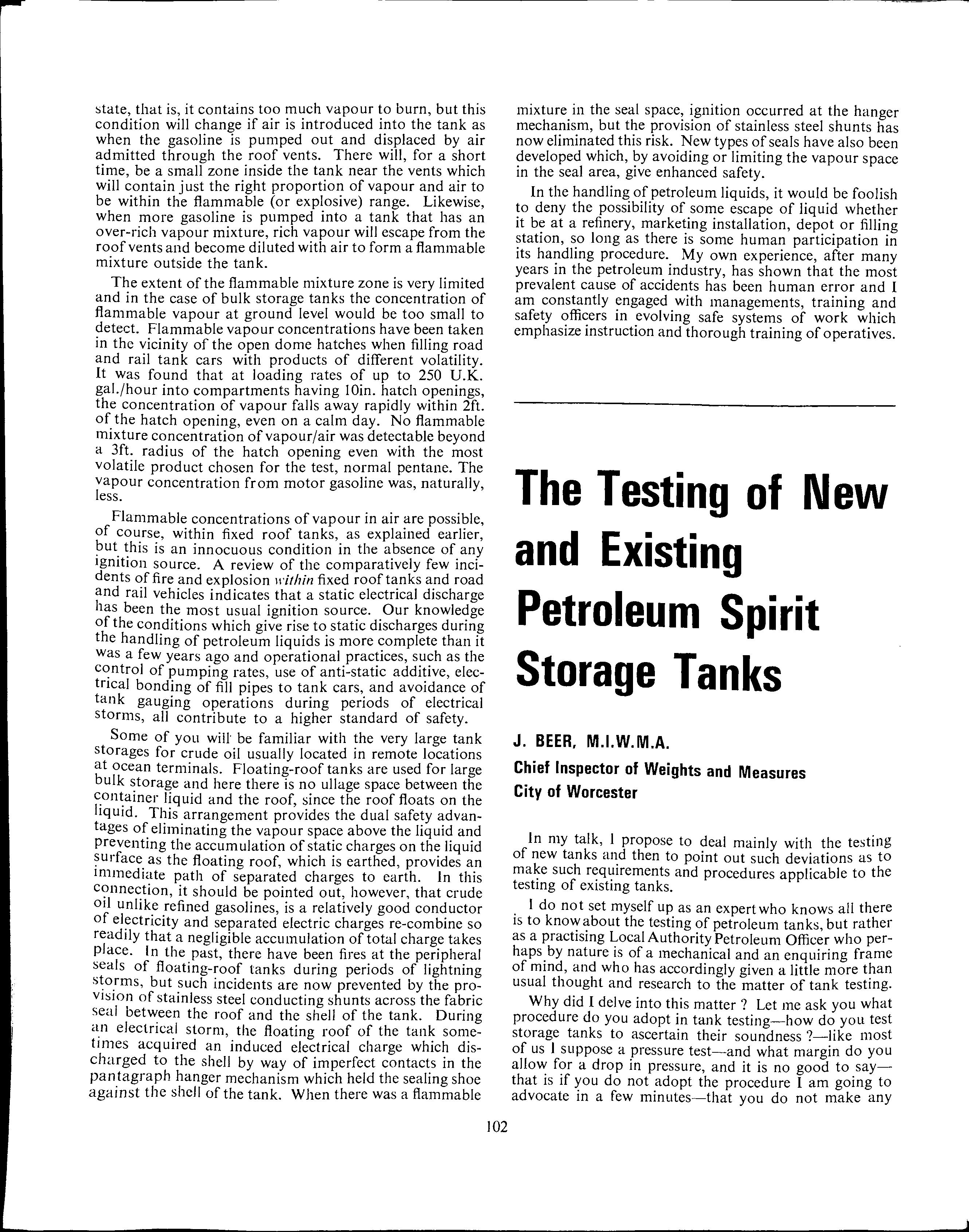
21 minute read
THE TESTING OF NEW AND EXISTING PETROLEUM SPIRIT STORAGE TANKS-J. BEER
state that is it contains too much vapour to burn, but this condition will change if air is introduced into the tank as when the gasoline is pumped out and displaced by air admitted through the roof vents. There will, for a short time, be a small zone inside the tank near the vents which will contain just the right proportion of vapour and air to be within the flammable (or explosive) range. Likewise, when more gasoline is pumped into a tank that has an over-rich vapour mixture, rich vapour will escape from the roof vents and become di! uted with air to form a flammable mixture outside the tank.
The extent of the flammable mixture zone is very limited and in the case of bulk storage tanks the concentration of flammable vapour at ground level would be too small to detect. Flammable vapour concentrations have been taken in the vicinity of the open dome hatches when filling road and rail tank cars with products of different volatility. It was found that at loading rates of up to 250 U.K. gal./hour into compartments having lOin. hatch openings, the concentration of vapour falls away rapidly within 2ft. of the hatch opening, even on a calm day. No flammable mixture concentration of vapour/air was detectable beyond a 3ft. radius of the hatch opening even with the most volatile product chosen for the test, normal pentane. The vapour concentration from motor gasoline was, naturally, less.
Advertisement
Flammable concentrations of vapour in air are possible, of course, within fixed roof tanks, as explained earlier, but this is an innocuous condition in the absence of any ignition source. A review of the comparatively few incidents of fire and explosion ll'ithin fixed roof tanks and road and rail vehicles indicates that a static electrical discharge has been the most usual ignition source. Our knowledge of the conditions which give rise to static discharges during the handling of petroleum liquids is more complete than it was a few years ago and operational practices, such as the of pumping rates, use of anti-static additive, electrical bonding of fill pipes to tank cars, and avoidance of tank gauging operations during periods of electrical storms, all contribute to a higher standard of safety.
Some of you will be familiar with the very large tank storages for crude oil usually located in remote locations at ocean terminals. Floating-roof tanks are used for large bulk storage and here there is no ullage space between the liquid and the roof, since the roof floats on the hqu1d. This arrangement provides the dual safety advantages of eliminating the vapour space above the liquid and preventing the accumulation of static charges on the liquid as the floating roof, which is earthed, provides an immediate path of separated charges to earth. Jn this C<;mnec:tion, it should be pointed out, however, that crude 01! unhke refined gasolines, is a relatively good conductor of and separated electric charges re-combine so readily that a negligible accumulation of total charge takes place. In the past, there have been fires at the peripheral seals of floating-roof tanks during periods of lightning but such incidents are now prevented by the prov1s1on of stainless steel conducting shunts across the fabric seal between the roof and the shell of the tank. During electrical storm, the floating roof of the tank sometimes acquired an induced electrical charge which discharged to the shell by way of imperfect contacts in the pantagraph hanger mechanism which held the sealing shoe against the shell of the tank. When there was a flammable mixture in the seal space, ignition occurred at the hanger mechanism, but the provision of stainless steel shunts has now eliminated this risk. New types of seals have also been developed which, by avoiding or limiting the vapour space in the seal area, give enhanced safety.
In the handling of petroleum liquids, it would be foolish to deny the possibility of some escape of liquid whether it be at a refinery, marketing installation, depot or filling station, so long as there is some human participation in its handling procedure. My own experience, after many years in the petroleum industry, has shown that the most prevalent cause of accidents has been human error and I am constantly engaged with managements, training and safety officers in evolving safe systems of work which emphasize instruction and thorough training of operatives.
The Testing of New and Existing Petroleum Spirit Storage Tanks
J. BEER, M.1.W.M.A. Chief Inspector of Weights and Measures City of Worcester
In my talk, I propose to deal mainly with the testing of new tanks and then to point out such deviations as to make such requirements and procedures applicable to the testing of existing tanks.
I do not set myself up as an expert who knows all there is to know about the testing of petroleum tanks, but rather as a practising Local Authority Petroleum Officer who perhaps by nature is of a mechanical and an enquiring frame of mind, and who has accordingly given a little more than usual thought and research to the matter of tank testing.
Why did l delve into this matter ? Let me ask you what procedure do you adopt in tank testing-how do you test storage tanks to ascertain their soundness ?-like most of us I suppose a pressure test-and what margin do you allow for a drop in pressure, and it is no good to saythat is if you do not adopt the procedure I am going to advocate in a few minutes-that you do not make any
102
allowances-I used to, but 1 was not really satisfied with this procedure and that is what caused me to make the change.
After the change it always annoyed me when a fitter after there has been a small drop in pressure in a tank test with which he has been concerned, to say "Oh that should be alright, I expect you will allow me a quarter of a pound, they always do in so and so". 1 experienced this remark in one particular instance where, after correcting for temperature and barometer there had been a drop of one eighth of a pound. As it was a Saturday I suggested that nothing would be lost if we left the test on over the weekend, and if everything was in order the pressure would revert back to the original knowing of course that as there was a leakage there would be a more noticeable drop over the weekend. 'The site was at the bottom of a small hill from each direction and over the weekend, due to violent thunderstorms the excavations half. filled with. water. This found our leak for us and 1t was m the weldmg of a seam. It is true that it was only a pin hole and may not happen frequently but I think it is apparent that such small leakages could get through and could create unnecessary hazards.
I have gone to some lengths to make this point because I feel we should approach the matter of tank testing with a little more prec1s10n. I feel we should have more of a laboratory approach rather than allowing some small arbitrary figure of a quarter or half a pound for possible errors.
In other words, we should make the necessary corrections but should make no allowances.
It is really about such corrections and simple apparatus for applying them that I want mainly to talk.
I do not propose to deal in my initial remarks with special tests on special tanks but rather with the everyday gas, be it air or nitrogen, testing of ordinary 500-5,000 gallon underground tanks.
Basically all we have to do is to apply a pressure generally IO lb./sq: in. which i.s regist.ere? on a pressure gauge, and if there is no drop m the md1cated pressure after a period, usually twenty-four hours, the tank is passed as sound.
How delightfully easy it would be if it was as simple as that. But I am afraid this is not so.
You see, as in our schooldays, we are still troubled with Boyles and Dalton or Charles Laws.
I am sure it is not necessary for me to go into these in detail, always provided that I was able, but you will remember that in:
Boyles Lall' the volume of a given mass of gas at constant temperature is inversely proportionate to its pressure.
In other words, PV = P1V1.
In Dalton or Charles Law the volume of a given mass of gas at constant pressure is proportionate to its temperature. I n other words, v v - = ____!. T T1
No w bcorn . . mmg both Laws PV = P1 -V1 T Ti

Where P = initial pressure V = initial volume T = initial temperature P1 = final pressure Vi = final volume Ti = final temperature (The temperatures and pressures being stated as absolute)
As in the case of a tank we may have under test the volume is a constant then we have ' P P1 - = - or P x T1 = T x Pi· T T 1
What, therefore, I suggest we must do is to take both the pressure and temperature of the gas in our tank accurately and in absolute figures-and it is here that l may run into some lack of agreement. .But let me get one thing out of the way. l think you will agree that a drop in temperature will cause a drop in pressure, and vice versa, but how much. I will explain the mathematics a little later but would ask you here to accept a figure of .09 lbs. or 1/11 lb. for each 1° Centigrade variation and as you will be aware such variation can be directly ascertained by an ordinary mercury thermometer, absolute zero being 273° C. below zero, usually marked on centigrade thermometers or the melting point of ice. . The other point which usually presents some argument is on the question of absolute pressure. . Now absolute zero pressure is a perfect vacuum and is m fact the height of the barometer below its level at the time of reading. Unfortunately we have no fixed point as with the thermometer from which to start as the ordinary, or Bourden tube pressure gauge is simply a comparitor of the pressure in the vessel which is being measured and the. pressure of the gas-in our case the atmosphere-in which the whole thing is situated.
To state some figures the height of the standard mercury barometer is 30 inches, which represents a pressure of 14.7 lbs./sq. in.
If, therefore, atmospheric pressure varies between the start and finish of a tank test, our comparitor-the gauge -will be affected. In other words, we must make a correction for barometric variations.
Nothing can convince like a practical demonstration and I have therefore brought along a little bit of homemade apparatus and here I should say "with apologies to Mr. Heath Robinson".
First of all to demonstrate a temperature fluctuation.
Here we have a small airtight container connected to a pressure gauge into which we put a pressure and then will vary the temperature.
Now to demonstrate fluctuations of barometric pressure.
Here we .have a small container with gauge attached. both of which are in an outer container to which also a gauge can be attached.
A yressure can be put in the inner container (from the outside) representing a tank under test, around which the pressure can be varied in the outer container, representing atmospheric pressure.
If now I pressurise the inner container with a certain mass of gas as there is no leakage will remain a constant, and without any outside influence other than
103
changing the outside pressure, the inner gauge moves down or up according to whether I increase or decrease the outside pressure; this, I think, clearly demonstrates that barometric variations affect the indicated pressure of a tank under test.
Having, I hope, convinced you that variation of temperature and barometer do affect the issue, it now remains for me to show whether the variations which are experienced in practice are significant, and I think I will also be able to do this.
You will remember at the start of my talk I gave a personal experience of one eighth of a pound drop i~dicating a leakage which was subsequently found, provmg, I think, that a variation as small as that is significant.
Now we can revert back to our formula PT1 = P1T and
Assume we start with a pressure of 10 lb./sq. in. which rounding off our 14.7 to 15 is 25 lb./sq. in.abs.
That our initial temperature is 12° C. or 285° C. abs. and there is an increase to 17° C. or 290° C. abs. We have 25 x 290 = 285 x P1 p - 25 x 290 1 - 285 7250 285 = 25.44 for 5u C. rise which in round figures is .09 or l / 11 lb. for ea~h. I" C. variation, which is quite significant, becaus;: I~ is not at all uncommon to get temperature vanat10ns of 5° C. and more. do not need to use formula to show significance of barometric variations.
As mentioned previously, the height of the standard mercury barometer is 30 inches and represents a pressure of 14.7 lb./sq. in. Converting one to the other and again rounding off 14.7 to 15 lb./sq. in. then two inches of mercury = I lb./sq. in. In other words, a change of barometer of two inches makes a variation on the gauge of one pound, one inch of half a pound, half an inch of a_ quarter of a pound, and proportionately. Such variat10ns are bound to be significant as in time of meteorological deep depression variations of up to one inch in twenty-four hours are not infrequently experienced and with a large temperature change as well, I have now a correction of as little as one pound ! ! !
This I think you will agree proves the necessity for making such corrections.
Now for the apparatus and procedure to do the job.
We will assume we have arrived at that part of the progress of the installation when the tank is to be tested.
I suggest it should be tested when in position.
I suggest a definite drill so that members of our own staff and the pump and tank fitters know what exactly is needed and confidence is set up on both sides.
I suggest also we should provide ourselves with a couple of accurate and reliable gauges of 15 lb./sq. in. capacity together with a portable barometer to ascertain pressures.
A I 5 lb./sq. in. gauge seems to be about the most suitable size because it is able to withstand the initial surge when the valve is opened to a tank under 10 lb./sq. in. pressure which a JO lb./sq. in. gauge is not so able to do. The gauge should have about a 6in. or 9in. diameter dial so that the graduations can be in relatively small increments.
We should have a supply of what I call temperature tubes which may be borrowed by fitters, etc., when preparing tanks for test, together with other sundry apparatus the need for which will become apparent to you as you do your work.
Having received information that a tank is to be tested a temperature tube is made available before the fitter applies the pressure. He will quickly become accustomed to this drill.
If such pressure is applied to the tank by air pump there will be a heating up. If by air or nitrogen released from a pressure bottle there will be a cooling. I wou'd therefore suggest that three or four hours must elapse between the application of the pressure and the start of the test in order that the temperature may stabilise.
As l feel it is always better to try and reduce the possibility of change of temperature as much as possible, whenever I can I always endeavour to start and finish a test as early in the morning as can be. The reason for this being that night time temperatures are more likely to be similar to each other than those of daytime when the effects of sun and cloud can create quite large variations. It is also better to cover the tanks wherever possible.
Having personally taken the temperature, barometer and tank pressure, of which careful note is made and ascertained by a soap and water test that the control valve is not leaking, the gauge should be r.!moved and the fitting scaled to prevent tampering.
J\fter the lapse of twenty-four hours the readings are agam taken, the corrections applied, and ifthere is no drop the tank passed as sound.
If there has been a drop in the corrected pressure the tank will rectified, be leaking and usually ?Y the it will fitter, be necessary for this to be and the whole procedure gone through agam.
On t.he second .visit l like to ascertain and apply the correct10ns, workmg out what the pressure should be shown on the gauge before turnincr on the control valve as this seems to be far more effective than to afterwards work out something that will justify a variation in pressure.
Having done all this l am of the opinion that NO allowance should be made. The tank is either SOUND or
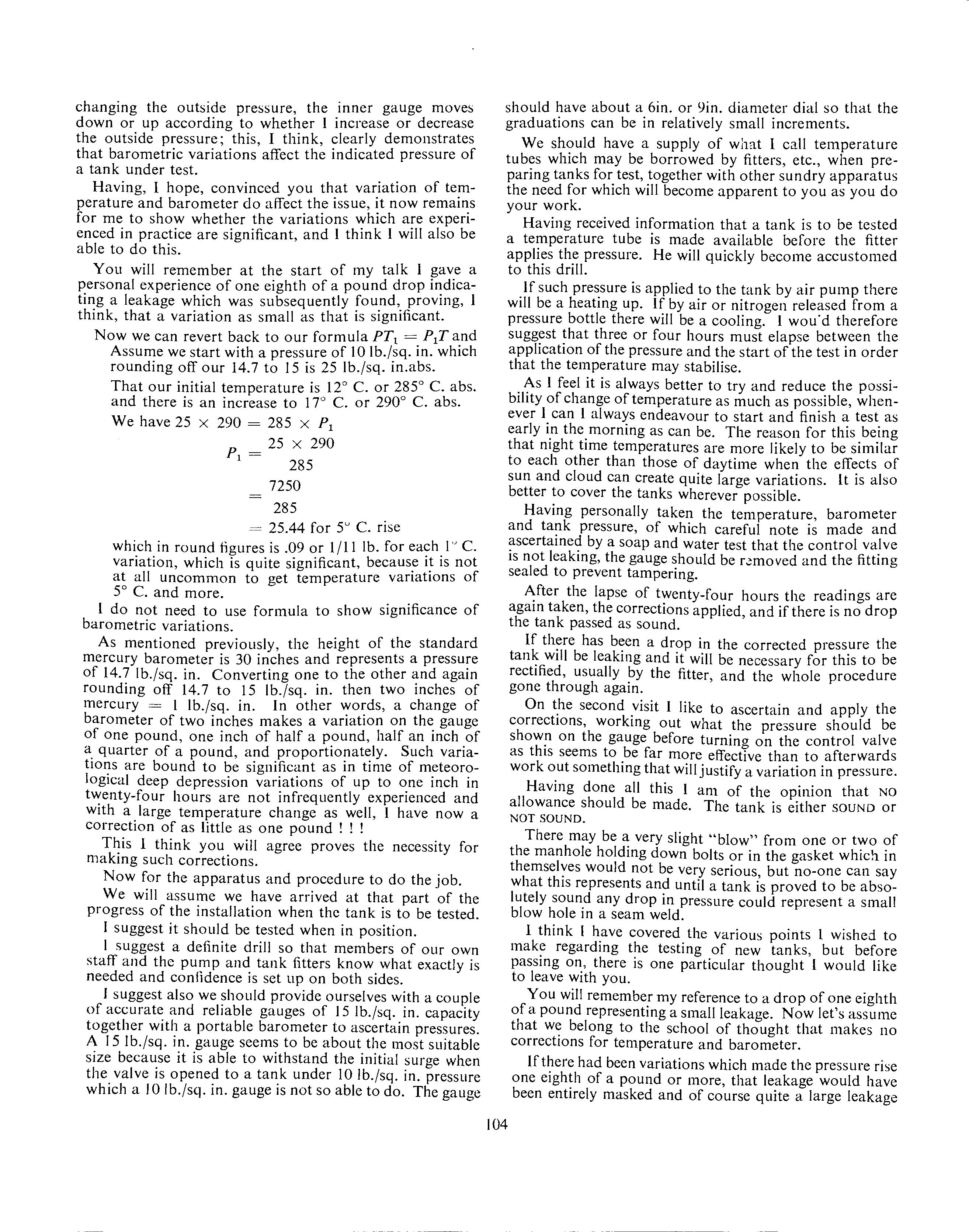
NOT SOUND.
There may be a very slight "blow" from one or two of the manhole holding down bolts or in the gasket which in themseI:--es would not be very serious, but no-one can say what this represents and until a tank is proved to be absolutely sound any drop in pressure could represent a small blow hole in a seam weld.
I think 1 have covered the various points L wished to make regarding the testing of new tanks, but before passing on, there is one particular thought 1 would like to leave with you.
You will remember my reference to a drop of one eighth of a pound representing a small leakage. Now let's assume that we belong to the school of thought that makes no corrections for temperature and barometer.
If there had been variations which made the pressure rise one eighth of a pound or more, that leakage would have been entirely masked and of course quite a large leakage
104
could be masked if variations are large, maybe representing an increase of up to half, three quarters or even one pound, and far more than that if we are also prepared to allow half or three quarters of a pound as well.
Cases also arise where there should be an increase in pressure of "so much" but ~here in fact the p~es~ure has remained the same or has mcreased, but a s1gmficantly less amount, in which case there would of course be a leakage.
On the other hand, the testing of tanks takes up valuable time and fitters' wages, so that if the variations cause a drop in pressure then it is only fair that we should acknowledge this also.
Before it was my practice to make the corrections to which I have referred, there were many occasions where there were somewhat unexplained variations about which I was not entirely happy. Since, however, adopting the correction procedure some 16 or 17 years ago, I get a personal satisfaction that I am now passing only really sound tanks and at the same time being fair to the other side. You know it is quite a sobering thought that if we make an allowance instead of applying corrections we may be passing a leaking tank as being sound.
I think it is true to say, if we have said a tank is leaking, then one or more leaks have always been found.
Pipe lines
Although the quantities which could get away through a leaking pipeline would most likely be nothing like as serious as from a leaking tank, there still would be little point in assuring the soundness of one without the other.
Owing to the small mass of gas in pipelines as compared with a tank, the same problems do not arise although the question of temperature can give considerable variation if we use the two hour duration test.
As I see it there are two methods, both using a pressure of ten or more pounds per square inch, the one where the pressure must hold for two hours and the other a soap and water test. Personally, I prefer the latter. It is quicker, saves a second visit or hanging about for two hours and certainly picks out the smallest of leaks.
All that is required after the pressure has been applied is to go over all joints, elbows, sockets and connectors using a good paint brush and a supply of water to which detergent has been added, using a looking glass to see underneath or at the back of pipework. Any leakage of course will be shown up by soap bubbles.
I always insist on testing vent lines.
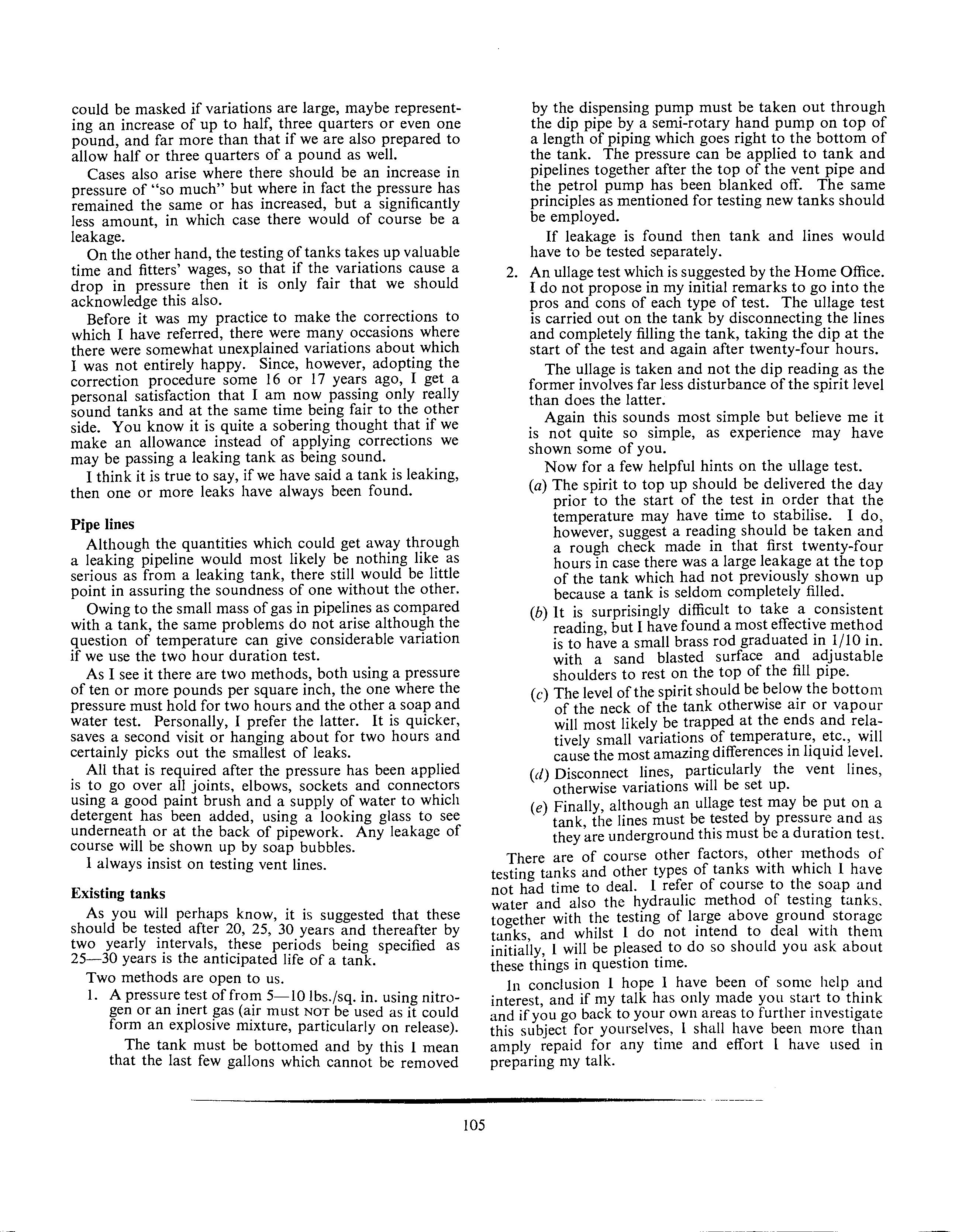
Existing tanks
As you will perhaps know, it is suggested that these should be tested after 20, 25, 30 years and thereafter by two yearly intervals, these periods being specified as 25-30 years is the anticipated life of a tank.
Two methods are open to us.
I. A pressure test of from 5-10 lbs./sq. in. using nitrogen or an inert gas (air must NOT be used as it could form an explosive mixture, particularly on release). The tank must be bottomed and by this l mean that the last few gallons which cannot be removed by the dispensing pump must be taken out through the dip pipe by a semi-rotary hand pump on top of a length of piping which goes right to the bottom of the tank. The pressure can be applied to tank and pipelines together after the top of the vent pipe and the petrol pump has been blanked off. The same principles as mentioned for testing new tanks should be employed.
If leakage is found then tank and lines would have to be tested separately. 2. An ullage test which is suggested by the Home Office.
I do not propose in my initial remarks to go into the pros and cons of each type of test. The ullage test is carried out on the tank by disconnecting the lines and completely filling the tank, taking the dip at the start of the test and again after twenty-four hours. The ullage is taken and not the dip reading as the former involves far less disturbance of the spirit level than does the latter. Again this sounds most simple but believe me it is not quite so simple, as experience may have shown some of you. Now for a few helpful hints on the ullage test. (a) The spirit to top up should be delivered the day prior to the start of the test in order that the temperature may have time to stabilise. I do, however, suggest a reading should be taken and a rough check made in that first twenty-four hours in case there was a large leakage at the top of the tank which had not previously shown up because a tank is seldom completely filled. (b) It is surprisingly difficult to take a. consistent reading, but I have found a most effecti~e meth?d is to have a small brass rod graduated m 1/10 m. with a sand blasted surface and adjustable shoulders to rest on the top of the fill pipe. ( c) The level of the spirit should be J:>elmy the bottom of the neck of the tank otherwise air or vapour will most likely be trapped at the ends and rel~tively small variations o~ tempera~ur~,
e~c., will cause the most amazing differences m liquid level. (d) Disconnect line.s, par.ticularly the vent lines, otherwise variat10ns will be set up. (e) Finally, although an ullage test may be put on a tank the Jines must be tested by pressure and as they ~re underground this must be a duration test.
There are of course other factors, o~her 111:ethods of testing tanks and other types of tanks with which I have not had time to deal. I ref~r of course to the. soap and water and also the hydraulic method of testmg tanks, together with the testing of l~rge above groun~. storage tanks, and whilst l do not mtend to deal with them initially, l will be pl~ase~ to do so should you ask about these things in quest10n time. ln conclusion l hope I have been of some help and interest and if my talk has only made you start to think and ify~u go back to your own areas to further investigate this subject for yourselves, l shall have been more than amply repaid for any time and effort l have used in preparing my talk.
105