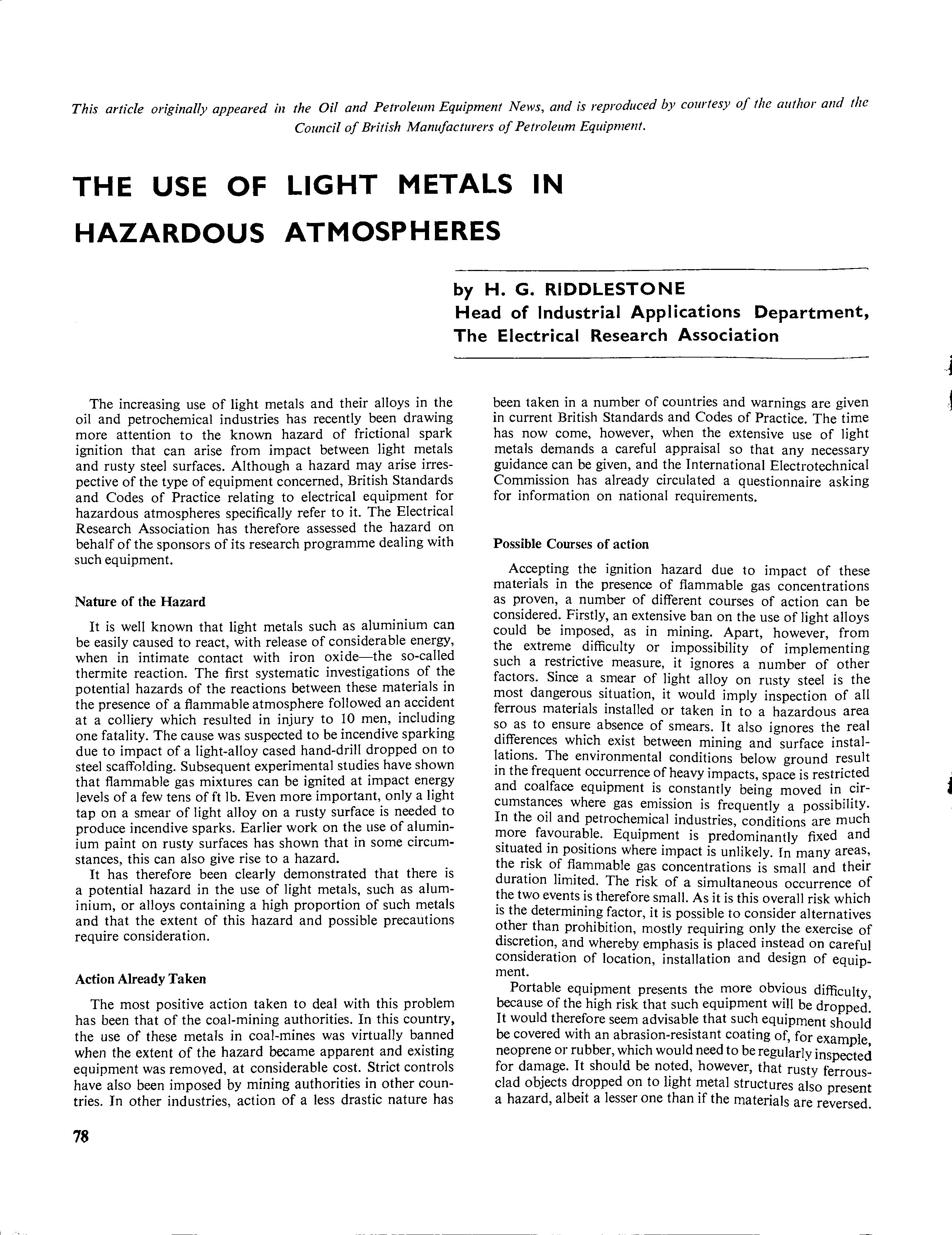
4 minute read
Use of Light Metals in Hazardous atmospheres
This article originally appeared in the Oil and Petroleum Equipment News, and is reproduced by courtesy o.f the author and the Council of British Manufacturers of Petroleum Equipment.
THE USE OF LIGHT METALS IN HAZARDOUS ATMOSPHERES
Advertisement
by H. G. RIDDLESTONE Head of Industrial Applications Department, The Electrical Research Association
The increasing use of light metals and their alloys in the oil and petrochemical industries has recently been drawing more attention to the known hazard of frictional spark ignition that can arise from impact between light metals and rusty steel surfaces. Although a hazard may arise irrespective of the type of equipment concerned, British Standards and Codes of Practice relating to electrical equipment for hazardous atmospheres specifically refer to it. The Electrical Research Association has therefore assessed the hazard on behalf of the sponsors of its research programme dealing with such equipment.
Nature of the Hazard
It is well known that light metals such as aluminium can be easily caused to react, with release of considerable energy, when in intimate contact with iron oxide-the so-called thermite reaction. The first systematic investigations of the potential hazards of the reactions between these materials in the presence of a flammable atmosphere followed an accident at a colliery which resulted in injury to 10 men, including one fatality. The cause was suspected to be incendive sparking due to impact of a light-alloy cased hand-drill dropped on to steel scaffolding. Subsequent experimental studies have shown that flammable gas mixtures can be ignited at impact energy levels of a few tens of ft lb. Even more important, only a light tap on a smear of light alloy on a rusty surface is needed to produce incendive sparks. Earlier work on the use of aluminium paint on rusty surfaces has shown that in some circumstances, this can also give rise to a hazard.
It has therefore been clearly demonstrated that there is a potential hazard in the use of light metals, such as aluminium, or alloys containing a high proportion of such metals and that the extent of this hazard and possible precautions require consideration.
Action Already Taken
The most positive action taken to deal with this problem has been that of the coal-mining authorities. In this country, the use of these metals in coal-mines was virtually banned when the extent of the hazard became apparent and existing equipment was removed, at considerable cost. Strict controls have also been imposed by mining authorities in other countries. Jn other industries, action of a less drastic nature has
78
been taken in a number of countries and warnings are given in current British Standards and Codes of Practice. The time has now come, however, when the extensive use of light metals demands a careful appraisal so that any necessary guidance can be given, and the International Electrotechnical Commission has already circulated a questionnaire asking for information on national requirements.
Possible Courses of action
Accepting the ignition hazard due to impact of these materials in the presence of flammable gas concentrations as proven, a number of different courses of action can be considered. Firstly, an extensive ban on the use of light alloys could be imposed, as in mining. Apart, however, from the extreme difficulty or impossibility of implementing such a restrictive measure, it ignores a number of other factors. Since a smear of light alloy on rusty steel is the most dangerous situation, it would imply inspection of all ferrous materials installed or taken in to a hazardous area s~ as to ensur~ abs~nce of smears. It also ignores the real differences which exist between mining and surface instal!ations. The environmental conditions below ground result m the frequent occurrence of heavy impacts, space is restricted and coalface equipment is constantly being moved in circumstan~es where gas emission is frequently a possibility. In the 01! and petrochemical industries, conditions are much n:ore fa~ouraJ:l~. Equipment is predominantly fixed and s1tua~ed m pos1t1ons where impact is unlikely. Jn many areas, the nsk of flammable gas concentrations is small and their duration limited. The risk of a simultaneous occurrence of the two events is therefore small. As it is this overall risk which is the determining factor, it is possible to consider alternatives other than prohibition, mostly requiring only the exercise of discretion, and whereby emphasis is placed instead on careful consideration of location, installation and design of equipment.
Portable equipment presents the more obvious difficulty because of the high risk that such equipment will be dropped'. It would therefore seem advisable that such equipment should be covered with an abrasion-resistant coating of, for exampl neoprene or rubber, which would need to be regular Iv inspect~ for damage. It should be noted, however, that rus.tv ferro e _ clad objects d~opped on to light i:netal structures al~o pres~~t a hazard, albeit a lesser one than 1f the materials are reversed.