
13 minute read
Car wheel falls through forecourt
By Marshall T. Mott-Smith, Administrator, Storage Tank Regulation Section Bureau of Petroleum Storage Systems Florida Department of Environmental Protection
Editorial Comment
Advertisement
The APEA,in this issue of The Bulletin, is sharing some disturbing news from the USA, Marshall MottSmith a regulator from Florida has produced an extensive insight into some of the problems experienced with flexible pipe work. This flexible pipe work is not new to Europe where the more common pipe work installations are the more rigid polyethylene systems. However, where these flexible systems have been used we are not aware of similar problems in Europe, perhaps there are some difference is use (exclusively pressure in US) or poor contractor installation as suggested by the manufacturers, which has caused these concerns.
Introduction
There are two types of thermoplastic pipes, semi rigid and flexible.
One type of thermoplastic piping could be best characterised as “semi-rigid”. These are constructed with high-density polyethylene and the joints are electro-fusion welded. These semi-rigid pipes are not involved in the analysis and investigation of this paper. There are two manufacturers approved for use of semi-regid piping in Florida (UPP and NUPI) one has been in use for four years, and no incidents have been reported to Department of Environmental Protections (DEP) to date.
Incidents and discharges involving thermoplastic flexible piping (flexpipe, for brevity's sake) connected to underground petroleum storage tanks have recently become more numerous, particularly in the southeastern United States. This problem has become a significant issue for a number of interests. Facility owners are angry because their relatively new flexpipe systems are failing within five years of installation. Piping installers are frustrated with having to perform frequent site visits to respond to the incidents and repair the systems. Piping manufacturers insist that faulty installation or inadequate operation and maintenance caused the problems. Regulators are caught in the middle. However, it is the regulators that must deal with the facility's non-compliance and the cleanup of petroleumcontaminated soils and groundwater.
Unlike rigid fiberglass reinforced plastic and steel piping systems, which have been in use for many years, flexpipe is a relatively new technology and its limitations are not widely known. The purpose of this article is to provide information regarding those limitations and dispel the myth that flexpipe is a "bury it and forget it" system. Due to the large numbers of thermoplastic flexible piping systems being installed, the Department of Environmental Protection (DEP) wants installers, owners, and operators of such systems to become educated about the problems associated with flexpipe and encourage better installation, monitoring and maintenance of these systems.
Background Information
In Florida, the regulation of underground and aboveground storage tank systems is the responsibility of the DEP's Bureau of Petroleum Storage Systems. Florida began its regulatory efforts in the early 1980s after a leaking underground storage tank contaminated the city of Belleview's drinking water supply well. In 1983, the Florida Legislature responded by passing laws that enabled the DEP to adopt rules for aboveground storage tanks (ASTs) and underground storage tanks (USTs). Florida's rules initially only required that tanks and piping be protected from corrosion or be constructed with corrosion-resistant materials. In 1990 and 1992, the rules were amended to require secondary containment for new tanks and piping. The rules also established deadlines for existing storage tank systems to upgrade to secondary containment by deadlines established in the rules based on the age of the storage tank system. The first deadline was 1989, and the last deadline will be December 31, 2009.
Facility owners upgrading their tanks and piping to meet the 1989 and 1992 deadlines typically chose double-wall fiberglass pipe. In Florida, this piping was usually manufactured or sold by Ameron or Smith Fiberglass. Flexpipe was just emerging as an option in the early 1990s, and was not commonly available for the 1992 deadline. Before any piping integral to a storage tank system is installed in Florida, the piping must be third party certified by a nationally recognized laboratory as meeting the DEP's standards, or it must be approved and listed by Underwriter's Laboratories (UL) and subsequently approved by the DEP. The Florida DEP first allowed flexpipe as "approved equipment" in 1995. Total Containment, Inc. (TCI) manufactured that piping. As with TCI's piping, other manufacturer's equipment (Bufflex, Environ, APT, Western Fiberglass, OPW, UPP, and NUPI) obtained approval as it came on the market. Many owners chose flexpipe to meet Florida's 1995 deadline (for tanks and piping installed between 1976 and 1980), as well as in 1998 (for tanks installed between 1980 and 1984).
Florida's Storage Tank Program contracts with county-level governments to implement a legislatively mandated effort called the "Compliance Verification Program". The contracted-counties perform routine compliance, installation, closure, and discharge inspections of all storage tank facilities within the state, with a goal of inspecting every facility once a
Articles year. Over 380,000 inspections have been performed since 1983, and the average number of inspections for the each of the last two years is approximately 25,000.
The Compliance Verification
Program has significantly improved facility compliance. It also helps tanks program managers stay in touch with emerging issues and problems. The county inspectors document the status of each facility's compliance by using digital cameras. The photographs and inspection information are entered into DEP's database management system. These photographs and inspection reports have been the source of much of the Department's data for flexpipe incidents.
One final background note that is pertinent to this issue is the difference between "incidents" and "discharges". An incident is a condition indicating that a discharge may have occurred and further investigation is required, whereas a discharge is a confirmed release to the environment. Florida's rules require that owners and operators of storage tank systems report incidents and discharges within 24 hours of discovery. After 2009, all Florida facilities should have secondary containment systems. About 11,000 of the 32,000 registered regulated USTs currently have secondary containment. When these facilities perform their monthly leak detection checks, they are looking within the interstice (the space between the primary wall and the secondary containment) for petroleum products or water. Examples of interstices include piping sumps, dispenser sumps or liners, and the space between the inner and outer wall of double-wall tanks or piping.
When a problem is discovered in an interstitial space, it must be reported as an incident because the product or water may be contained in the interstice. If further investigation finds stained soils, free product, a sheen, or laboratory analytical data that indicates there is a release then this is reported as a discharge. Because most of the flexpipe in Florida is double-wall or has secondary containment, the majority of the problems have been incidents and not discharges. Some flexpipe failures have resulted in discharges. Regardless, the problems with flexpipe that have been reported are serious concerns for DEP.
Manufacturers
Other than as specified in the background information above, no mention of manufacturer names will be made in this article. The information reported comes from the DEP's contracted county inspectors as well as from information reported to the DEP by facility owners. It is not the Department's intent to make comparisons between different manufacturers of thermoplastic flexible piping or to discourage or promote the use of any type of piping. The DEP's intent is to report the findings from its field inspectors so this issue can be discussed and further investigated.
Thermoplastics
Thermoplastics are polymers that will become soft and melt if exposed to sufficient heat. The polymers that are utilized in rigid fiberglass reinforced plastic piping and the elastomers that make up the various rubber boots in piping systems are thermosets. Thermosets are cross-linked polymers that will not soften or melt upon the application of heat.
Flex pipe systems are composed of multiple layers of extruded thermoplastics and each layer is intended to perform a specific function. These layers include internal liners, outer walls of the primary pipe, the coaxial jacket or secondary containment of "doublewalled" pipe and outer protective barriers. Thermoplastics commonly utilized as liners include: Polyamides (Nylon), Polyvinylidene Fluoride (Kynar), Aliphatic Polyketone (Carilon) and Polyphenylene sulfide (Fortron). Polyethylenes and Polyurethanes are utilized in the construction of the outer layers of the primary pipe. The secondary jacket of all coaxial flexpipe and the secondary containment systems are constructed of various grades of polyethylene.
Thermoplastics are susceptible to permeation by aromatic hydrocarbons although the rate of permeation varies considerably between different polymers. Many thermoplastics will also swell (increase in volume) when exposed to petroleum products. As with permeation rates, different thermoplastics exhibit widely varying swelling characteristics. Thermoplastics utilized in the construction of flex pipe systems exhibit volume changes ranging from less than 1% to as much as 9%. Some grades of polyethylenes are particularly susceptible to swelling and it is believed that this has caused or contributed to many of the problems Florida is experiencing with flexpipe systems. When some polyethylenes come into contact with hydrocarbons (whether free phase liquids, vapors or dissolved constituents in water) swelling and softening of the material will occur within a relatively short period of time. For this reason, it is essential that flexpipe systems not be externally exposed to hydrocarbons for any length of time.
Florida's experience with polyethylene has given DEP cause for concern when this material comes in contact with petroleum products and vapors, particularly in piping and dispenser sumps. This piping can come into contact with petroleum products and vapors three main ways. If storage tank system's sumps are not properly maintained and drips, leaks, and spills are allowed to remain in the bottom of the sumps, then petroleum products and vapors come into contact with the polyethylene piping inside the sumps. Another source of petroleum products in contact with the flexpipe comes from contaminated stormwater or groundwater that enters the sump through boots, manways, or electrical conduits. Sump integrity can also be compromised by structural deterioration or deformation (some sumps are constructed with polyethylene), and by problems caused by soil movement and groundwater hydrostatic forces. Finally,
petroleum products can come in contact with the outer polyethylene portions of the pipe through the internal coating within the pipe. If there are problems with the inner protective coating that is the barrier between the polyethylene outer layer and the products within the pipe, the polyethylene can degrade. Each flexpipe manufacturer has a specialized system to minimize this possibility.
The Problem
The State of Florida recently published the following list of problems that thermoplastic flexible piping exhibits after it is installed and comes in contact with petroleum products, petroleum contact water, or petroleum vapors in piping sumps, dispenser sumps, or other field applications:
· The piping connections, riser pipes and flex connectors found within the sumps where the piping is terminated may be twisted, overstressed or pushed out of normal alignment. · The pipe may be over bent within the piping sump or folded over on itself (kinked). · The outer jacket of doublewalled (coaxial) piping may extend over the metallic ferrule of the pipe coupling. · The outer jacket of doublewalled (coaxial) piping may split as it attempts to grow over the metallic coupling. · The pipe may be swelling and appear to be bulging or "ballooned". · The pipe may be wrinkling or it may be sticky/spongy and softer than it was originally. · The outer walls of the primary pipe and/or the secondary jacket may be cracking. · The rubber boots that are installed in the walls of the containment sumps may be stretched or torn. · The "donuts" that make up part of the boot of some pipe systems may be dislodged or the clamps may not be in place. · The rubber "test" boots that are installed at the pipe terminations of some coaxial pipe systems may appear to be compressed or distorted. · The metallic connectors that are part of some pipe system couplings may be cracked. · Piping manufactured prior to 1994 that is yellow in color may be delaminating and a fungus/ microbial growth may be attacking the outer walls of the pipe.
This list was prepared after comparing DEP's experiences with the State of Mississippi, and is based on the mutual experiences of both states with reported flexpipe incidents. The DEP's concern with the above problems is that the integrity of the piping has been compromised such that it no longer meets the required performance standards and that it does not provide the necessary protection to the environment.
The Data
The flexpipe problem in Florida did not happen at once. The number of incidents has increased each year, and the 2003 data is only from the first six weeks of the year (see the table below). The Department's main concern is that the number of incidents will continue to increase in frequency. Another concern is that there are many more incidents that have not yet been reported to the DEP.
Table 1
Year
Unknown Date 2000 2001 2002 2003 Total Number of Events 5 1 9 41 5 61 The next table (Table 2) contains information that describes the type of problem encountered at the facilities in Table 1. The description is in the original words of the inspector, owner, or operator, and is taken from the DEP's matrix of incidents in the State of Florida:
Table 2
Description Number of Events Cracking 3 Swelling/Split open 1 Blow out 24 Uncertain 1 Loose Swage 2 Plasticized 1 Pin Hole 1 Breach in Piping 9 Piping failure 5 Burst Pipe 3 Bulging in Piping 9 Piping Split 2 Total 61
Description Number of Events Cracking/Splitting 6 Breach from holes/blowouts 37 Bulging/Ballooning 10 Uncertain 1 Loose Connections 2 Piping Failure 5 Total 61 There are some commonalities in the observations that can be joined together for the sake of minimizing the categories (See Table 3 below).
Table 3
The DEP has received hundreds of photographs from its field inspectors, as well as from UST inspectors in other states that depict each of the conditions and problems mentioned above. This information is a public record in the State of Florida and is available on CD upon request. Information about flexpipe incidents at specific facilities and the affected equipment has not been included in this article. The pictures below are a sampling of what has been seen.
There are two types of thermoplastic flexible piping single-wall carrier pipe that is placed within a secondary containment outer flexpipe, and a double-wall coaxial pipe that is one piece of pipe with an interstice between the pipe walls. From the data above it is clear that the most frequent problem associated with the reported incidents is the breaching of the pipe from "blow outs", "bursting", and similar descriptions. From Florida's data, this has usually been associated with the single-wall carrier pipe systems. The following photographs from two different Florida sites should provide some visual understanding:
The next photographs depict the "bulging" and "ballooning" effect. This condition is usually associated with the coaxial type of flexpiping.
Cracking and splitting can occur in both types of flexpipe - coaxial double-wall and single-wall:
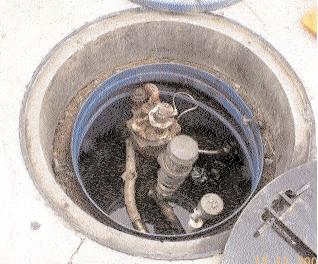
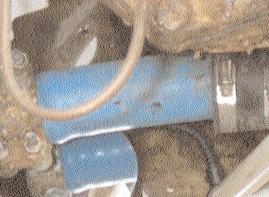
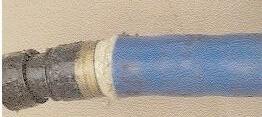

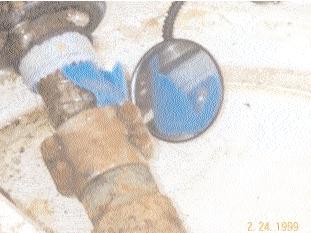
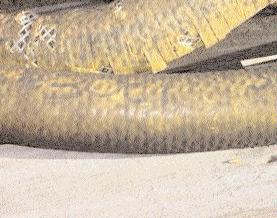
Piping failure is a generally descriptive term, but the following photographs probably best demonstrate this type of condition:
The next two photographs will help show the "softening" condition:
The last two photographs are from other states in the southeast. One photograph shows elongation that can occur, and the other shows problems with loose connections and fittings.
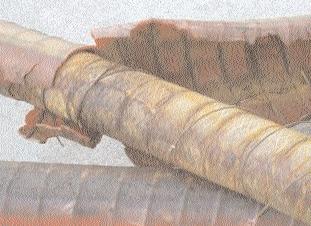
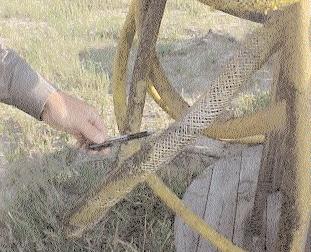
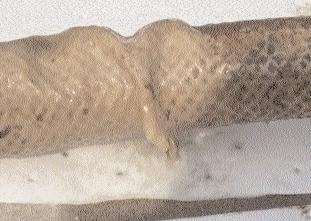
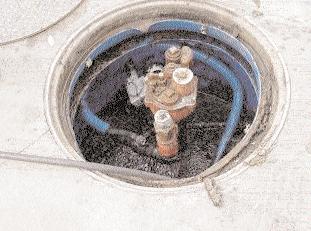
