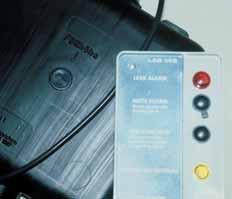
16 minute read
Outdoor Payment Systems - The Forecourt Revival
safety breaks on dispensers and is situated in the hose assembly or incorporated as an integral part of the nozzle swivel.
Shear valves EN 13167-Part3
Advertisement
This standard covers the performance of shear valves (or impact check valves) commonly used where a dispenser may be attached to a pressure pumping system.
Swivels EN 13617 Part 4
This standard covers the performance of the swivel, which is situated between the nozzle and the hose and allows the nozzle to swivel without kinking the hose.
Hoses for Fuel Dispenser EN 1360 with prEN 13483 for vapour recovery hoses
Overfill Prevention Devices EN 13616 2004
Two types are included one the mechanical type which works independent of the tank truck
The other is Truck mounted with a sensor in the storage tank
Leak Detection Devices EN 13160 Part 1 General Principles
This standard has an important role to play for regulators and users alike. The confidence of early detection of leaking tanks or pipes is essential to provide both safety and environmental protection. The standard is divided into classes and they are as follows:
EN13160 Part 2 Class 1 Air-pressure and Vacuum
EN13160 Part 3 Class 2 Liquid systems for Tanks
EN13160 Part 4 Class 3 Sensors for vapour and liquid Automatic Tank Gauges EN 13352:2002
This standard deals with the performance of automatic tank gauges
Submersible pumps prEN 15268
This standard relates to the performance of the submersible pump and the safe installation methods. It is at present in the public comment stage and should be ratified as a full standard early next year.
Details on the exact titles for the standards can be obtained from the “Blue Book” and the standards themselves can be purchased from the British Standards Institute by either phoning +44 (0) 20 8996 7001 to order standards or through the web site www.bsi-global.com
You may be interested to know that the European Countries which have adopted these standards are as follows: - Austria, Belgium, Cyprus, Czech Republic, Denmark, Estonia, Finland, France, Germany, Greece, Hungary, Iceland, Ireland, Italy, Latvia, Lithuania, Luxembourg, Malta, Netherlands, Norway, Poland, Portugal, Slovakia, Slovenia, Spain, Sweden, Switzerland and United Kingdom
EN13160 Part 5 Class 4 Tank Gauge Leak Detection Systems
EN 13160 Part 6 Class 5 Sensors in monitoring wells
EN 13160 Part 7 Covers -Interstitial spaces, jackets or liners
Underground pipe for petrol stations EN 14125:2004
This standard covers the manufacture, performance and testing of thermoplastic and flexible metallic underground pipe for petrol stations.
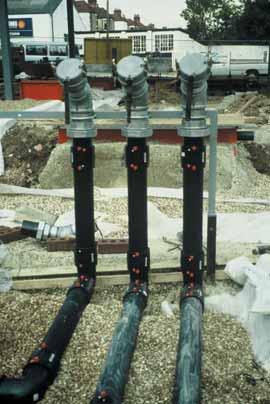
By Bob Taylor, King Tanktechnic
Without doubt, owners and operators of Retail Fuel Sites in the UK have a huge and onerous responsibility to the Environment.
It is a mandatory requirement that site owners and operators carry out a full and detailed risk assessment of their fuel storage and dispensing infrastructure to ensure that they do not contaminate the environment with leaked fuel. Such risk assessments must be regularly carried out and updated with their outcome being properly recorded for presentation to Environmental Officers on demand.
In order to carry out a meaningful risk assessment, common sense dictates that it is of course imperative that those conducting the assessment are aware of any possible risks to the environment.
With huge clean up costs following environmental pollution, (sometimes in excess of £100,000) together with substantial fines being imposed by the Courts, it means that the importance of getting it right first time cannot be over stressed!
This paper is intended to inform the reader of one of the root causes of tank perforations and to attempt to advise and assist in devising a course of action aimed at preventing an environmental incident.
The advent of “Clean” fuels which have been developed to maintain a cleaner running engine for vehicles using these fuels, has in turn resulted in less carbon dioxide being discharged to atmosphere. The detergent component of these products has a cleaning effect on the internal walls of storage tanks which results in rust particles being dislodged from the tank interior, these particles then fall to the bottom of the tank to produce sludge.
This sludge can give rise to major problems in the efficient operation of all types of pumping equipment, (suction or submersible pumps) and can lead to various filters within the system becoming blocked. The resultant equipment down time and the cost of replacement filters cannot be an acceptable running cost to forecourt operators.
In addition to sludge problems another phenomena has now come to the fore – “Microbial Influenced Corrosion” (M.I.C). MIC has only recently become widely discussed but its existence has been recognised for a long time. It always was considered a problem within diesel and kerosene tanks but it is now known to be non selective, affecting nearly all storage tanks holding product. The presence of water within a tank is known to exacerbate its affect.
Initial growth occurs at the fuel/water interface. As the microbes feed off this interface the result is the production of weak organic acids which once formed, will produce the corrosion pattern shown in the accompanying photographs.
Briefly MIC is a result of the formation of Sulphate Reducing Bacteria (SRB.) These microbes are formed by the combination of a number of factors: -
Contamination of the delivered fuel.
Nutrients derived from the fuel additives and contaminating water.
Water is considered to be the key requirement for microbial growth.
The combination of both sludge and SRB working in tandem gives each element the ability to help the other to gain a significant foothold which begins the process of corroding the internal surfaces of the tank. The SRB feed on nutrients extracted from the biodegradable material present in hydrocarbons i.e. petrol or diesel etc., fuel additives and contaminated water.
In our opinion, the primary source of microbes is contaminated fuel delivered into the storage system, with the presence of water being the main catalyst for microbial growth. It can take months for microbes to grow, with the timescale being dependent on the available nutrients within the storage infrastructure.
The sludges on the bottom of tanks make an ideal environment for the SRB to survive and proliferate without being disturbed by liquid turbulence during fuel loading.
The excrement produced by the SRB is acidic slime and, which when trapped in the sludge or beneath the striker plate, baffle plate or dished ends of a tank where the welding has not been fully completed gives rise to very severe corrosion patterns. This corrosion pattern is intense and more rapid than conventional corrosion.
The first indication of a problem within a tank is a degrading of the fuel stock being dispensed often causing the blockage of nozzles and pump filters. In some circumstances the filter blockage becomes endemic and the retail outlet can spend many thousands of pounds in futile efforts to keep the system running by repeated filter cleaning or renewal.
The first step in the remediation process is to eliminate any water ingress into the tanks.
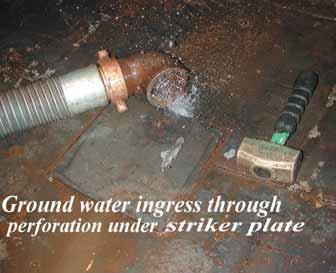
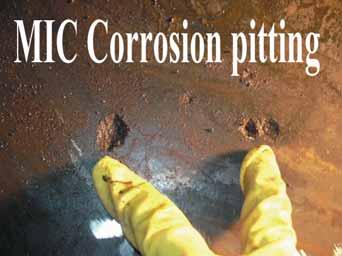
SRB and MIC can only occur if there is water in the tank and the conditions are conducive to supporting and encouraging their production.
The next step is to clean the tank. Once this decision has been made it is necessary to enter the tank and carry out a thorough cleaning process. This must be undertaken safely and in a manner that completely eradicates the microbe bio films. The cleaning process must be aggressive and is generally carried out using high pressure water jetting with detergent additives. Dependant on the degree of corrosion found, the tank may be returned to service without further remediation but only if use is accompanied by periodic preventative treatment by biocide.
Internal inspection will identify the corrosion pattern and depth. Tanks with corrosion patterns in excess of 40% of the nominal tank shell thickness i.e. 6mm plate with recorded corrosion pits in excess of 2.4mm should be considered for remediation by tank lining.
Currently in the UK we do not have a standard for tank downgrading but there is a “European Committee for Standardisation” C.E.N. rule based on the TuV (German Technical Surveyance Association) and the TRbF 503 and 401 Germany standards. These state “Tank corrosion of a depth of more than 40% of the tanks wall thickness shall not be used any longer without repair and installation of a leakage protection lining and control.”
External corrosion to underground storages tanks is often caused by damage to the outside protection coating due to incorrect handling during the installation process. Where tanks have been installed with sand or pea gravel back fill this damage can be the cause of localised areas of corrosion, which can result in tank wall perforations. This type of corrosion is reduced where tanks have been correctly encased in sulphate resistant concrete because any installation damage is immediately covered and not allowed to progress.
As external corrosion cannot be detected by visual examination it is recommended that a full grid pattern Ultrasonic wall thickness test should be undertaken from the tank interior. By employing this method it should be possible to detect and record any wall thickness loss from the exterior surface of the vessel. Where such a loss is identified it is recommended that the same rules are adopted for remediation by protective lining, i.e. 40% wall thickness loss.
Once it has been established that a tank requires remediation how do you now select a suitable lining contractor to carry out the work?
Tank lining is the easiest way to afford protection from leaks and in the opinion of the writer, tank lining should not be considered a temporary solution but a as a long-term permanent upgrade system. There are Adisa lined tanks in Germany & Switzerland which are still in trouble free service after over 25 years.
It must be remembered that tank lining will not destroy or remove SRB. The formation of SRB microbes will still occur in any tank whether lined or unlined irrespective of whether it is single or double skinned given that the conditions are correct for the growth to develop. However, tank lining will protect the tank fabric from further corrosion and, in the opinion of the author, it is the most effective route to tank remediation be it leaking or severely corroded.
There are a number of lining systems available today. To enable you to understand them I have prepared the following synopsis of the most commonly used systems.
Single Skin Systems
The system can be applied both by the hand rolling method using laminating techniques or spray application. The most commonly used lining materials are vinyl-ester or polyester glass flake composites, glass fibre laminates and advanced solvent free epoxy systems.
The lining system is bonded to the existing internal steel tank wall, therefore building a “tank within a tank.” The final thickness of this fully cured lining should be between 1mm and 3mm thick dependant upon the system used.
Double Skin Systems
After the completion of the single skin system (the first stage of a double skin system) the second stage is to build an interstitial space which will form the foundation for the final stage of construction – the forming of the secondary tank using similar materials used in the application of the single skin system.
This system is constantly monitored by an explosion proof fully approved alarm control which monitors the integrity of the interstitial space and sets off both visual and audible alarm in the event of leak being detected. Because the interstice is being monitored it is possible to detect a leak from either the interior or exterior surfaces of the tank.
Bladder In-liner
This system employs a flexible leak protection lining called a “Bag Liner” or “Bladder” which is fabricated from PVC or other approved fabric. The donor tank has a fleece or polystyrene honeycomb fabric installed to form an interstitial space after which the bladder/bag is installed and a vacuum is generated between the tank wall and interior liner. Once installed the system is linked to a leak monitoring system.
For the successful installation of interior liners it is a requirement that the donor tank must be sound and able to withstand a pressure test. For the leak detection system to be effective this may require single skin tank remediation prior to installation of the interior liner.
At KTL we have had installation experience of the typical systems mentioned. These experiences led us to the decision to select the KTL-Adisa system as our preferred product
(A) The materials used are advanced solvent free epoxy. In our opinion the use of advanced composite materials ensures long term protection and excellent chemical resistance. When used on petroleum storage tanks the overall protection is suitable against present and future products that will contain octane boosters such as Methanol, Ethanol, Isobutanol and a range of Ethers capable of replacing toxic lead compounds.
The resin and lining materials have been subjected to approval certification tests by Swiss Standards Organisation

and the German B.A.M and TuV in order to determine the degradation of the mechanical properties due to chemical attack. The test liquids chosen were to cover a wide range of possible applications and, in the most critical case, for petroleum storage, the composition of the C.E.N. future unleaded mixture was used.
The test series showed that even after severe exposure of the laminate to the range of chemicals the mechanical strength remained intact. The system is equally effective when used in above ground flat bottomed tanks as cylindrical UST’s.
We have undertaken mechanical tests to the KTL Adisa lining system to prove the structural properties using the National Approved Measurement Accreditation Services (NAMAS) organisation Material Testing Services Manchester. The results of these destruction tests record that a minimum 240 bar to a maximum 400 bar hydrostatic pressure was required to burst the linings through artificially created tank shell perforations.
The maximum external pressure level which could occur through a corrosion hole in an underground steel tank is at most 0.5 bar. Typically, this would be at the bottom of a tank with a high ground water level. The lining system, therefore, has structural properties capable of withstanding any future external hydrostatic pressure caused by possible on-going external corrosion perforation. (B) We found the use of the vinylester and polyester in the process gave rise to major safety and COSHH concerns due to the styrene emissions during application with personnel exposure limits being far exceeded at all times and, therefore, stopped using this system. Our opinions caused us doubts in respect of the chemical resistance to future fuels.
(C) It was not found possible to obtain a German TuV approval for soft linings for its use on petrol storage. Although there are many thousands of soft liners in service storing diesel and heating oils on a fully approved system. The preparation work to the donor tank precluded economic use and was restricted to diesel use only.
Using the KTL-Adisa system we have to-date lined some 600 tanks within the UK for both the dealer market and the major oil companies. The system we use has been proved over a 25-year period by the manufacturers and developers, ADISA AG of Switzerland and is, we believe, the only system being used in the UK with full European approval.
Our opinion is that coatings and linings are the only protection to stop MIC attacking the tank shell and to provide a chemical barrier by sealing the surface from contact with the local environment and SRB.
Tanks damaged by MIC to a level in excess of the parameters quoted earlier in this paper (pits in excess of 2.4mm in 6mm plate) have been repaired and relined by KTL using the Adisa system up to twelve years ago, to our knowledge there has been no necessity to revisit any of them due to the recurrence or SRB/MIC damage.
KTL/Adisa lining offers total product resistance for all present and future fuels and is impermeable to water. This isolation of the steel surface provides effective protection of the underlying metal provided that the lining has been applied without defect. The coating material does not degrade in service and the lining remains strongly bonded to the donor tank shell surface.
Obviously, it is imperative that the tank owner selects a lining contractor who has all the qualifications, approvals and certification necessary to safely and effectively use the system selected. Careful questioning, sight of approval certificates and taking up references can help you make the right decisions!
Correct selection of a lining system and its application are critical to the ongoing successful protection of an underground storage tank, the writer advises that you make your decisions carefully.
Further to the above, information can be found on the KTL website at www.kingtanktechnic.co.uk
By John Keough
In our opinion tank lining can be a very practical method of refurbishing existing storage vessels, causing the minimum of disruption to site operations, therefore avoiding the subsequent loss of trade whilst the work is in progress.
One of the obvious benefits of lining tanks is that there is not the necessity to dispose of possible contaminated waste from the existing tank farm. Also the old tanks do not have to be disposed of as in effect they are being recycled.
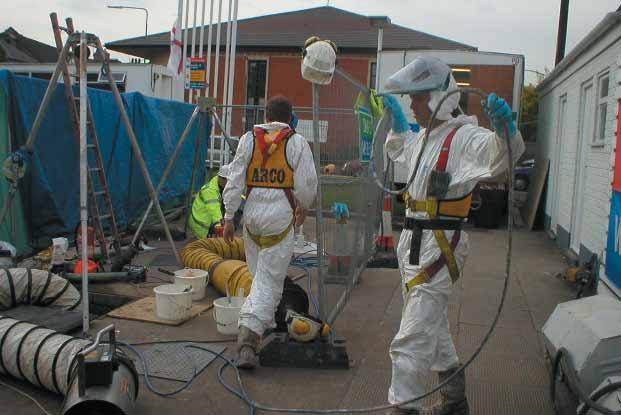
It is the opinion of the writer that when compared with tank replacement, tank lining offers a cost effective solution. Obviously it is a quicker process to line an existing tank than it is to install a replacement. In the majority of instances the site can remain
operational and the works carried out in stages to keep site disruption to a minimum. The author contends that in
many instances lining tanks can cost up to 50% less than replacing existing tanks with new.

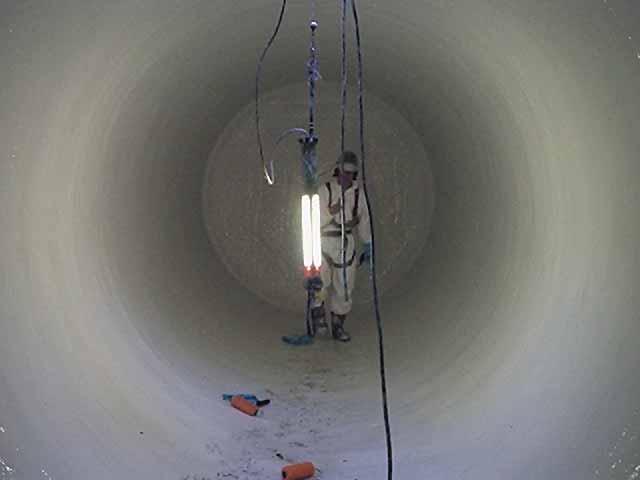
Graphite are able to provide three and five layer systems, with the three layer system being upgradeable to a five layer system should this be a future requirement. The five layer system is supplied complete with a modular tank integrity monitoring system which is also upgradeable at any time to cater for future requirements.
The monitoring system is supplied with varying levels of ‘intelligence’. In its most basic form it is supplied with localised alarms, but it’s capabilities can
contents gauges, pump controllers and point of sale terminals. It also enjoys the capability of sending alarm messages via SMS or e-mail to designated personnel or authorities to ensure that any emergency conditions are quickly responded to.
Obviously it is not possible to ascertain the condition of an existing tank without first entering it and carrying out a detailed inspection and report. Once this initial inspection and report has been carried out it is essential that
the extent and scope of works is
agreed, this should also include the preparation of a full risk assessment and method statement which should
identify the nature and extent of any repairs or remedial works which may be necessary. If for any reason a tank is found not to be suitable to be lined then
the site operator and appropriate licensing authority will be notified and the lining works stopped.
It is the opinion of the writer that lining tanks can be a proactive approach in the ongoing maintenance programme for a site and should significantly extend its operational life.
All of the lining systems offered by Graphite are backed up with a warranty period of up to ten years and have an expected working life in excess of thirty
years.
If for any reason a tank is found to be unsuitable for lining then the site operator and appropriate licensing authority will be notified and the work stopped until a suitable alternative course of action can be agreed.
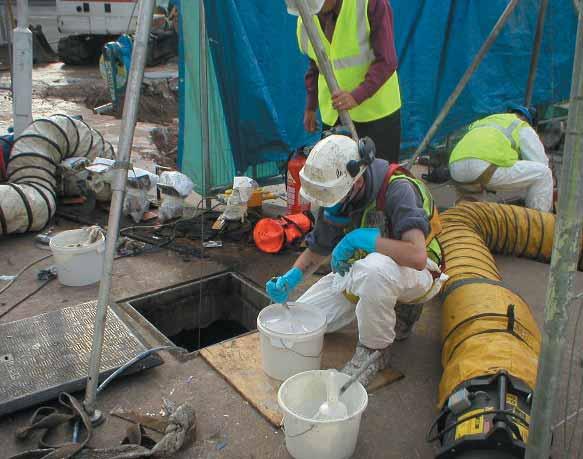

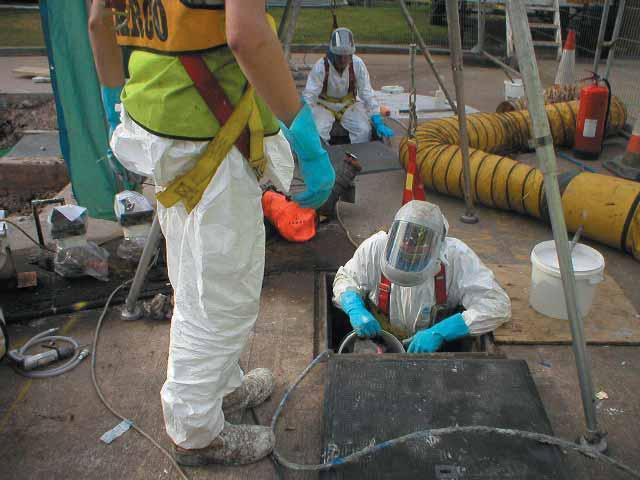