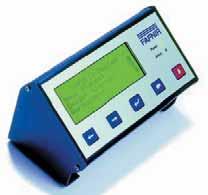
20 minute read
Press Releases
Articles clients continue to benefit from.
OAMPS have been consistently providing cover and support services to this important and specialised area of industry.
Advertisement
Product Focus from Overseas… 3 companies from Germany will be participating this year – Fafnir GmbH, Duerr Technik GmbH and Union Technik GmbH. All bring with them to the event innovative products and services from Europe.
Fafnir will be showing the automatic monitoring system VAPORIX which supplies information on the functional state of the active vapour recovery. As an automatic monitoring system for the active vapour recovery it serves as protection for people and environment. VAPORIX is especially designed for the application in gas stations. Due to its modular structure it can be applied in all known active vapour recovery systems and dispensers.
Union Technik is a leading contractor for the petroleum and petrochemical sector. Currently Union Technik is organising the national roll-out for the EVR (enhanced vapour recovery or monitoring) project for more than 3.500 petrol stations in Germany. They have extensive knowledge of the German market and are looking to expand its services to the UK and other European countries. Come and meet them at APEA2006!
Dürr Technik, the manufacturer of oilfree compressors and vacuum pumps, will be at APEA2006 to promote its piston pump MEX, especially developed for Vapour Recovery Systems Phase II mounted in the dispensers.
Elaflex showcases nozzles & hoses…
Elaflex will be promoting its ZVA Slimline, ZVAX 200 GR Stage II VR nozzle, ergonomically designed with the motorist in mind as well as its lightweight petrolpump hoses. All its hoses and couplings are suitable for LPG, AdBlue, BioFuels, Ethanol and more.
Product Innovation from Risbridger…
Along with their comprehensive range of petrol forecourt valves and fittings including vapour recovery equipment, Risbridger will be exhibiting its new range of flanged fittings at this year’s APEAevent. This latest product innovation from one of the industry’s leading manufacturers is designed to eliminate large threaded joints and minimise the total number of connections inside the man chamber. The compact design of the RIS-FLANGE systems components allows maximum flexibility and choice for tank lid layouts to suit both suction & pressure delivery systems. The swivel joint at the base of each tank lid allows easy rotation through 360 degrees and alignment with any containment entry face.
Fafnir’s Vaporix Master Oilfree vacuum pumps of Dürr-Technik
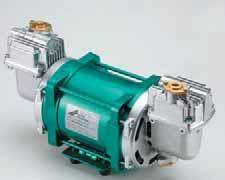
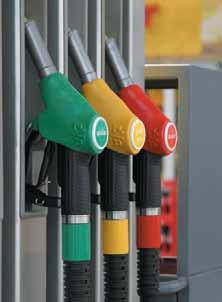
Elaflex hoses & nozzles

ABB provides a managing contractor service for both the maintenance and repair and the demolition and remediation of petrol stations. It is currently the managing contractor for Esso for the demolition and environmental remediation of petrol filling stations in the UK and Ireland. The organization has extensive environmental expertise and, working in conjunction with the Environmental Consultants, this has enabled value improvement opportunities to be realized. ABB looks forward to meeting you at APEA2006.
Gilbarco Veeder-Root will be displaying the latest technology and products with emphasis on its range of solutions to help manage the impact of the upcoming vapour recovery legislation. You can find Gilbarco Veeder-Root in the entrance foyer.
Adler and Allan Limited (A&A), the nationwide oil and environmental services group, will be exhibiting with its subsidiary company Industrial Water Jetting
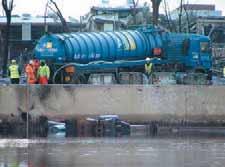
Systems Limited (IWJS) at APEA 2006. The group’s core activities now include: fuel distribution, product uplifts, tank installation, tank cleaning, spill response, land remediation, environmental auditing, tank and line testing, tankering, high-pressure water jetting and drain/sewer/tunnel cleaning.
Exhibitors
ABB
Adler & Allan
BPBovis
Berry & Co
Best Safety Solutions
Blueline Technologies
Duerr Technik GmbH
Elaflex
Environ
Eurotank Fafnir GmbH
Fairbanks Environmental
Global Retail Petroleum Solutions
Global MSI
Gilbarco Veeder Root
Goodyear
Ledbury Welding
Liquid Cargo Management
OAMPS
OPW UK
Pipex PetroTechnik
Petroman
Purfleet Forecourt Solutions
Risbridger
Suresite
Tokheim
Torex Retail
Total
Toureen Mangan
Union Technik GmbH
Urgent Technology
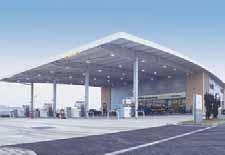
Suresite Limited – ‘managing business risk’
Suresite will be promoting its range of unique and affordable services Articles for the petrol forecourt and vehicle workshop sectors. Its services are aimed at providing businesses with the necessary controls to manage operating risks.
Find out about the latest in GLOBAL-MSI’s design of canopy, carwash and 'system build' shop structures. Global-MSI offers design, construction and installation services to the petroleum retail sector.
With Thanks to the Sponsors of APEA2006

Sponsor of the Conference
Sponsor of the APEAAward for Health, Safety & Environment Sponsor of the APEAAward for Customer Service
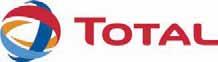
Sponsor of the APEAAward for Innovation

Sponsor of the APEAAward for Quality Sponsor of the Pre-Dinner Drinks


Sponsor of the Evening Entertainment Pre, Post and During Dinner
To Participate….
To reserve your conference or dinner place please email Emma or Fiona at Downstream Events Ltd at info@downstream-events.com or call on 020 8932 4505.
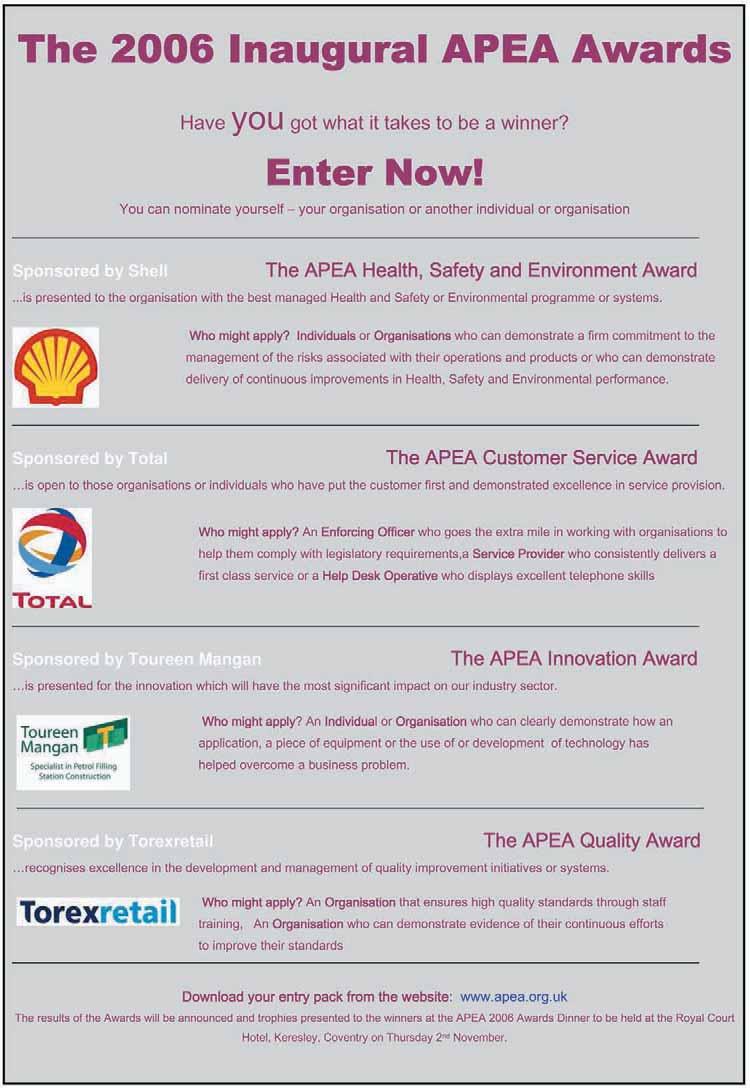
By Anton Martiniussen, Elaflex
The UK Government consultation paper in respect of Stage II Petrol Vapour Recovery stated a deadline for compliance with Stage II controls by January 1st 2010. The paper posed a number of questions offering several threshold options, with the Governments preference being 3.5 million litres, although there was a view that a threshold below that figure should be considered given the current concerns regarding controlling VOC’s. All new build or significant site upgrades would have to convert to Stage II as part of the programme. There was also reference to introduce measures to ensure that Vapour Recovery systems are working correctly. The VR controls would be covered under the existing Pollution Prevention and Control Act of 2000 and enforcement would be through the offices of local authorities.This requirement may come into effect during 2006.
Stage II is a means to capture evaporative emissions which are normally displaced to atmosphere during the process of refuelling a petrol engined motor vehicle. The vapours are sucked back into the underground storage tank (UST) by a vacuum pump fitted inside the dispenser. The dispenser is fitted with a vapour recovery nozzle such as the ZVA200 GR which has a vapour annulus on the spout through which the vapours pass. A coaxial hose is connected to the nozzle where the inner hose carries the vapour back to dedicated pipe work within the dispenser; this in turn i s connected to a vapour return line below ground level on the forecourt. It’s a prerequisite for Stage II that the site has an operational Stage IB system in place and that the necessary vapour return lines have been preinstalled. The proposed regulations do not apply to diesel.
T h e technology surrounding dispensers equipped with Stage II vapour recovery is mature. Approved Stage II equipment has been

in use in many European countries for years, indeed in some countries laws dating back to the early nineties exist. The main component’s for the dispenser is the nozzle, hose, vacuum pump, regulation devices with miscellaneous valves and fittings. Increasingly systems with integral monitoring facilities are being installed. The general view of the industry appears to be that these existing proven and approved systems should be used in the UK, thereby minimising the regulatory cost.
Assuming that installing Stage II will now become mandatory in the UK a number of questions are posed in order to meet the deadline for full compliance of 1st January 2010:
•What equipment to use?
What monitoring has to be undertaken whilst the equipment is operational (automatic checking or manual checking)? •How to test the system? •Is it necessary to install new dispensers or can existing equipment be upgraded or retrofitted? •Have contractors/ service engineers undergone the necessary training?
Etc.

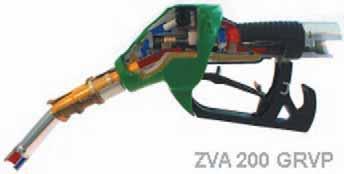
Vapour Control Systems
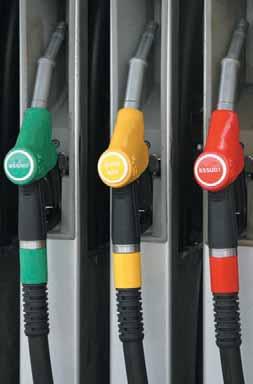
Development history of Vapour Recovery
California introduced vapour Recovery Stage II in1972. It first came to Europe in the late 1980s, first in Sweden and then in Switzerland. Stage II was not initially adopted or enforced by national laws but by local governments in the Swedish cities of Gothenburg, Malmö and Stockholm. In the German cities of Munich, Stuttgart and Bremen, the initiative to introduce Stage II also came from the local authorities. When politicians became aware of this development some quickly decided to adopt the requirements nationally. This has been a growing trend and laws requiring Stage II Vapour Recovery have now existed in most European countries since the early nineties. The UK is late in this regard but will have the benefit of installing equipment which has been tested and approved and has been proven to give reliable service in the field. In the UK one should look at what was done in other European countries and learn from their experiences.
System Types
In 1990 there was considerable discussion on the pro’s and cons of “balanced systems” (with a market share of more than 90% in the United States) as opposed to the Open Active systems (which was favoured in Europe). This discussion is over. Today only Open Active systems are used in Europe. The American balanced systems required a tight seal with the car filler neck, rubber bellows fitted to the nozzle spout were used to achieve this, but the equipment was largely considered too difficult and unwieldy to use. The European market preferred the “Open Active” system and this is what is in use today. As there is no need to achieve a seal, the handling of the nozzle is exactly the same as it is for standard nozzles in use today. They also fit into existing dispenser nozzle booths. Work has also been done by the vehicle manufactures over the years to optimise the design of the vehicle filler neck interface.
Control systems
The heart of the vapour recovery system is a device used to control the volume of vapour recovered relative to the liquid dispensed. For new pumps, electronic control devices are most often used. Special valves interfaced to the pumps electronics to ensure that vapour is only sucked back when the nozzle is in use and is in proportion to the amount of fuel dispensed.
According to most laws the volumetric return rate should be between 95-105%. If the recovery rate is more than 105% or lower than 95% the system is considered to be not working correctly. For test purposes, the volumetric return of vapour is measured with a special joint in the vapour recovery line connected to a gas meter. The gas meter is connected to a “socket” which is slipped over the entrance of the vapour return line of the nozzle. Instead of vapour (hydrocarbons) air is sucked in.
There are also mechanical and electronic proportional devices. Electronic controls have the great advantage that the systems can easily be calibrated during dispenser manufacture and later on site as part of a routine check using an electronic hand set. This is done by simulating the pulses from the flow meter and sucking in air, this so-called “Dry Test” eliminates the necessity to draw test measures from the dispensers.
Mechanical flow controlled systems are mainly used for retrofitting of pumps where the installation of electrical controls is cost prohibitive. As an example the ZVA200 GRVPnozzle as opposed to the ZVA200GR nozzle has an integrated proportional valve in the nozzle which is easily adjustable. The GRVPnozzle can also be fitted to new pumps as a lower cost option
Efficiency test
According to European law a “type approval” test of the vapour recovery system applies. The type approval efficiency test sets all the parameters to which the equipment must comply. In Germany, to allow for product innovation and development, the law says that the systems must operate according to the current “state of the art.” There is in place a recognised test and approving scheme for vapour recovery equipment by independent test authorities This is the so called 30 vehicle test, now revised as design criteria has significantly improved. In Germany TUV Rheinland, SPin Sweden and EMPAin Switzerland have adopted this test system The TUV certification is considered to be the main reference point and has published substantial test research and reference documents as well as certifying equipment.
Dry Test (Field Test)
Atest performed on site where a gas meter is used to measure AIR flow back to the tank on a simulated delivery. Used for calibration and checking of the VR system. This test method checks the volumetric recovery rate of vapours without dispensing any fuel. Only the measured air volume recovered is calculated. The routine tests are normally carried out as volumetric tests with air sucked in (“Dry Test”). Service companies may test the systems on a periodical basis or as required by the service station operator. The system simulates the fuel flow at 40 l/min +/5% by reading the electronic data from the dispenser using a type-approved handset. If the test shows the system is outside of this tolerance the error can generally be corrected by pushing a few buttons on the handset. As the viscosity of air is different from hydrocarbon vapour, a so-called correction factor (Kfactor) must be established. This

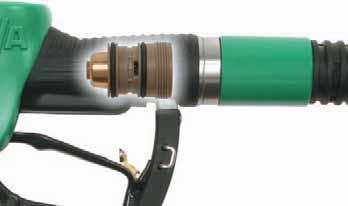
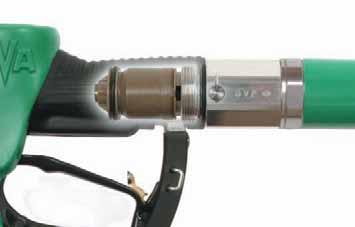
method is now used in most of the countries where vapour recovery systems are in operation. With full electronic control systems the method provides benefits and reduces costs and workload and also reduces exposure to fuel vapours for the tester.
It is only necessary to test one nozzle per side of the dispenser which means you do not have to test every single nozzle on the dispenser. The regulations for routine tests vary from country to country although generally these are conducted as part of the routine maintenance programme.
Some main components : The ZVA200 GR active vapour recovery nozzle
The ZVA200 Is a modular designed Automatic Nozzle designed to control the flow of fuel into a vehicle tank. The nozzle closes against the flow to give a soft shockless shut off and enables the so called “to the penny dispensing”. It also incorporates safety devises. The venturi effect on the sensing port cuts off the fuel once the tank is full and prevents overfilling. The attitude device in the nozzle body stops the liquid flow if the nozzle if held upright. An integral safety break coupling protects the dispenser in the event of a drive off. Within the vapour recovery nozzle body is cast a dedicated vapour channel. A special valve prevents any vapour return without liquid flow. As with all ZVA’s the nozzle is fully ATEX approved and certified by third party Notified Body with product audit. All ZVA’s can be completely rebuilt and serviced.
Vapour Recovery Hose
Avapour recovery hose is a hose within a hose and is known as a “coax hose”. The vapour is sucked back through a small bore inner hose. The design aspect of a coax hose is important. It needs to be customer friendly, lightweight and flexible and practically needs to be suitable for modern MPD’s as well as the more traditional high hose dispensers. There are different inner hose constructions available. Some are of the traditional construction with rubber compounds and others with wire braiding and plastic type inner tubes. It is important to avoid kinking as this impairs the efficiency of the system. From experience the traditional textile construction is preferable (Slimline 21 COAX). The design of the Elaflex VR hoses is today well proven. Agood indicator is to see what is being used in the market place. Another important aspect to ensure long service life of the hose in the field and reduce maintenance cost is to fit anti kinking sleeves. Coloured sleeves can also be added to show grade identification which assist in reducing misfuellings. Tests have proved that the hose lifetime may be prolonged by at least a third. For modern MPD’s with internal hose retractors the low temperature flexibility of the hose is of special importance for oil companies and customers when writing specifications. Practical experience has shown that the traditional rubber compounds do not offer sufficient flexibility when used with internal hose retraction systems, from -15ºC and below. You could with much effort get the hose out of the retractor system, then have difficulty getting it to go back in!
Monitoring
The implementation of vapour recovery in the UK may require that systems installed without Automatic Monitoring systems are manually checked on a regular basis, and records kept in the site logbook. Generally the more sophisticated the monitoring system, the less manual checking and recording. Basic forms of Vapour Recovery fault detection also exist. These may simply turn on an error indicator in the event of electronics controlling the Vapour Recovery system not seeing information from the dispenser main calculator, or not seeing the Vapour Recovery motor turn on during a petrol sale transaction. Another is a handheld harmonica functionality checking device (Elaflex Quick tester QT92). This is not regarded as “monitoring systems” but is a low cost device to check whether there is suction or not.
Note that such systems will still require operators to regularly check the equipment to ensure that there are no error indications, and to ensure that the equipment is repaired within seven days should an error be detected. Generally the more sophisticated the monitoring system, the less manual checking and recording required.
More advanced monitoring systems may incorporate a kiosk control unit that communicates with the vapour recovery systems in the dispensers, and provide a single point from which the status of all dispensers can be determined. Such systems may provide a continuous log that records dates and times on which vapour recovery systems were working correctly, and when there were faults, thus reducing the need for any manual logbooks.
More sophisticated monitoring systems may provide data communication facilities. Such systems may allow a company with several sites to remotely monitor the vapour recovery status of all their sites, possibly via the internet. Such systems may also automatically send alerts to a service/repair company when a vapour recovery system failure is detected, ensuring that the equipment is repaired within the seven day period.
In conclusion companies should discuss their requirements for Stage II systems with their equipment suppliers / service contractors and plan ahead. As a word of caution, do not leave it to the last moment - this may mean that there is insufficient time or service contractors available to do the necessary work. It is also wise to look at equipment which has been in use on European forecourts for many years providing years of reliable service. For more information please contact below.
Anton Martiniussen ELAFLEX Ltd Hoddesdon Herts EN 11 0PA Tel :01992 452 950 Fax:01992 452 911 Mobile: 07831 505 620 email: elaflex@aol.com www.elaflex.co.uk

By Terence Barker, Terence Barker Ltd
I can well remember the first oil storage tank our Company, well, me actually, manufactured; it was approximately 250 gallons capacity. I welded it up on a Saturday morning in a small building of about 1300 square feet of floor space, this was shared with a steam engine enthusiast who kept his small traction engine there when he was not showing it at rallies. After making the first tank I had to get home quickly to wash and change in order to catch a train up to White Hart Lane to watch Spurs play their first home game of the season. That was in August 1962 and we have, of course, been making tanks of every shape and size since. Today we are based in Haverhill, Suffolk and no longer have to share our workshop with a traction engine!
In the autumn of 2003 we were granted a license to manufacture the ConVault aboveground protected tank in the UK, and it’s the ConVault tank which is at the heart of our portable fuel station which you can review here.
Petrol stations, as I am sure most people are aware, have been closing down for several decades now, for example: In 1976 there were 30,383 petrol stations in the UK and 17.3 million registered vehicles, at year end 2004 there were just 10,351 petrol stations left serving a staggering 31.9 million registered vehicles, this trend continues. As a result of all these closures people living in rural areas must travel sometimes many miles to buy fuel, and then if it is the wrong time of day, sit in a queue for 10 minutes or more before they reach the pump. The only western European market not to have experienced a decline in the number of petrol station over the last 5 years are Finland and the southern European markets of Spain, Greece and Portugal. In Finland, new petrol stations are generally low-investment unmanned sites, while in Spain and Portugal relatively new market entrants such as Italy’s AGIPand supermarkets are responsible for many of the new builds. **
Our modular unmanned, self service fuel station could answer many of the problems that people living in rural areas are now faced with. These units can be erected on an owner's prepared base in a matter of hours; there will be no civil engineering works involved and no underground tanks to possibly pollute the soil and groundwater. They are free standing, debit / credit card operated, can hold up to 3 products and allow 4 vehicles to fill simultaneously.
But how safe is an aboveground protected ConVault tank?
The History
In 1986, a businessman trying to meet the growing requirements of the environmental and fire protection regulations for storing petroleum products in California designed and introduced the first protected aboveground storage tank (AST) system under the brand name of ConVault. The result was to provide a safe durable means of storing flammable and combustible liquids (specifically petroleum products) aboveground within close proximity to buildings and property lines that met the requirements of all regulators.
ConVault has proved its structural design and its operational superiority for the past 20 years. Over 30,000 ConVault ASTs are currently in service at extremely diverse locations in at least 24 countries including every state of the US, every province of Canada and every state and province of Australia. The list of owners includes all levels of US and Canadian government (including the White House, all branches of the military and several embassies), Coca Cola, AnheuserBusch, Pepsi, AT& T, Sprint, Prudential and many more. Over 60 of the Fortune 100 companies h a v e purchased ConVault ASTs.
Design
The steel primary tank is contained within a HDPE (high density polyethylene) wrap and 150mm of reinforce concrete for fire and impact protection. The high-strength monolithic concrete shell protects both the steel primary tank and built in secondary containment from fire and vehicle impact, as well as making them bullet proof. Additionally it provides a heat/cold barrier that keeps the temperature of the fuel stable resulting in less fuel loss through vaporisation, and less water condensation in the tank.
Performance
The ConVault ASTis an extremely safe means for the storage of volatile liquids (we consider it is the safest) both from the environmental and fire resistant view. They have survived many disasters, structural fires, forest fires, natural-gas pipe-line fires, floods, hurricanes, lightening strikes and tornados with winds exceeding 261 miles per hour. ConVault have been shot at (a terrorist attack at a Russian embassy) and run into by vehicles. In August 1988 lightening started a natural gas pipeline fire in Florida. Duel towers of flames reportedly reached about 600 feet in the air and hundreds of feet horizontally from each side of the pipe. One observer said it was like being under the Challenger space shuttle at lift-off. The fire burned for over 7 hours and temperatures were estimated to have reached 3,000 – 4,000 degrees Fahrenheit.