Are You Getting the Best from Your Workforce?
How to optimize utilization and efficiency through fashion-specific automation
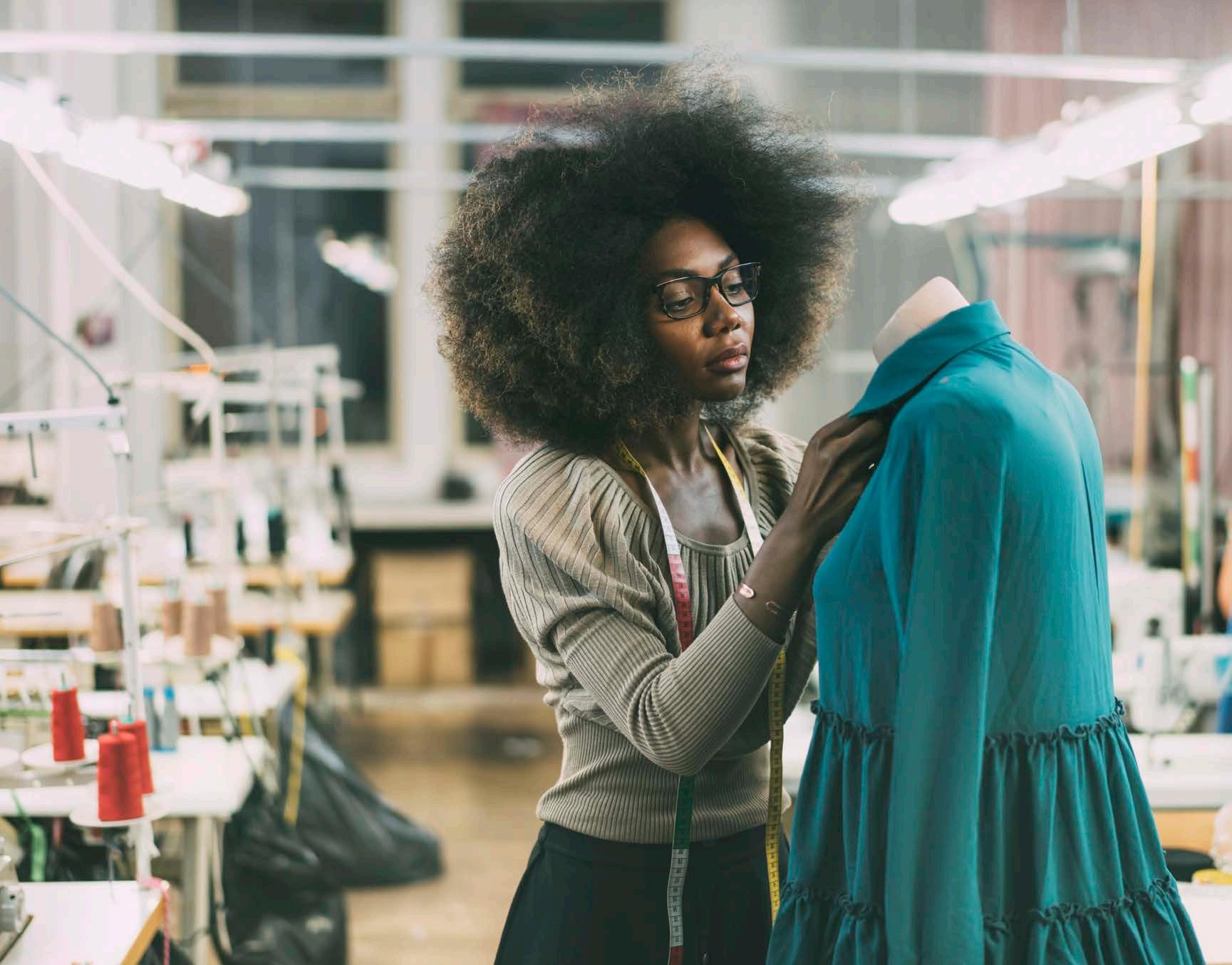
Table of Contents
› Industry-specific Technology to Streamline Your Fashion Business and Drive Efficiency
› Enhance Creativity and Gain Efficiency in Design
› Reduce Administrative Hassle and Errors in Sales Order Processing
› Produce Faster, More Accurate Demand Forecasts and Reduce Manual Inventory Counts
› Power Up Manufacturing Productivity
› Optimize Inventory and Warehouse Management for Efficient Fulfillment
› Leverage Omnichannel Fulfillment Automation to Expand Revenue but Not Headcount
› Empower Faster, Smarter Decision Making with Integrated Financial Management
› Automation Pays Both Business and Workforce Dividends
Is Your Business Feeling the Pinch of Rising Labor Costs and Staffing Shortages?
Aptean recently surveyed North American apparel manufacturers, and 42% said their number one concern over the past 12 months has been staffing and labor shortages. Inflation has driven up the price of labor and materials, and a tight labor market has made it difficult to find and retain skilled workers. Your people drive your company’s success. Right now, staffing challenges might be holding you back from landing the next big customer or meeting critical production deadlines.
Are You Searching for New Answers to Workforce Challenges?
Many companies can’t find enough qualified candidates to fully staff their operations. Even when they can find the right people, their labor budgets may not always be sufficient in an atmosphere of rising costs. Many successful companies approach this problem by not only stepping up recruiting efforts but also by pursuing automation strategies that boost workforce utilization in order to increase production without adding headcount.
In this eBook, we will:
› Introduce apparel-specific technology solutions that help companies drive greater efficiency and streamline business processes.
› Follow an order through the entire apparel workflow, from product design through production and fulfillment, showcasing the impact of end-to-end automation.
› Demonstrate how automation can increase staff utilization, improve accuracy and help companies create a better employee experience.
Industry-Specific Technology to Streamline Your Fashion Business and Drive Efficiency
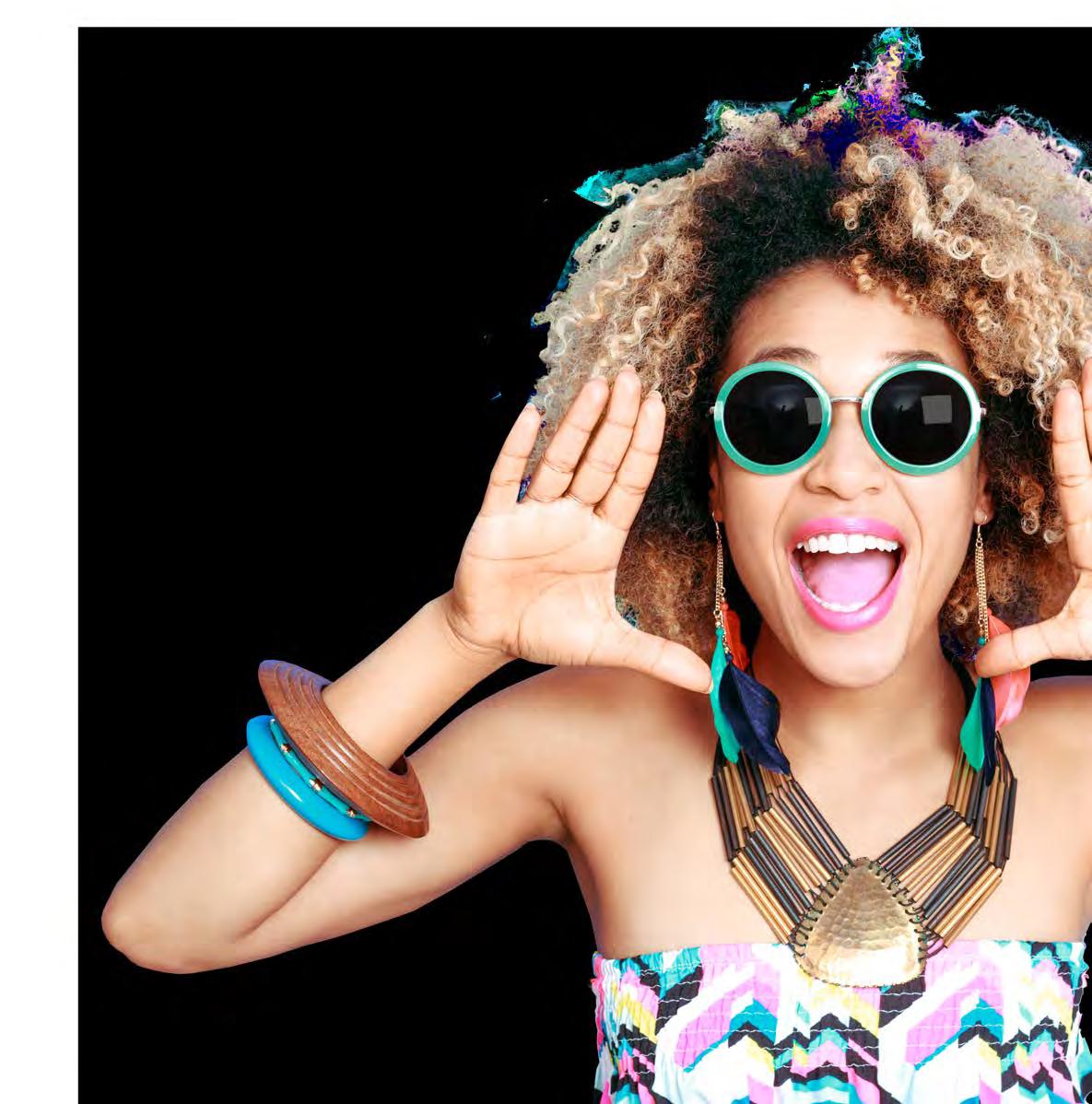
Through automation and streamlining operations, companies can increase efficiency and productivity. Automation can help companies control labor costs by reducing or eliminating routine tasks and administration.
In the Aptean 2023 Fashion and Apparel Manufacturing Report for North America, 53% of companies surveyed are pursuing technology to automate more tasks. Similarly, McKinsey & Company forecasts that companies adopting digitally-enabled value chain solutions could see a 50% reduction in time to market and a 20% decline in manufacturing costs.i
A comprehensive suite of apparel-specific technology solutions can help brands infuse end-to-end automation across the business. The recommended software solutions include:
› Enterprise Resource Planning (ERP) is the core business management solution that centralizes business data, improves financial control and standardizes business processes to create efficiencies.
› Shop Floor Control streamlines shop floor processes by tracking, scheduling and reporting on labor productivity and product manufacturing, assembling and processing.
› Product Lifecycle Management (PLM) accelerates the concept-to-product lifecycle by eliminating data entry and automating key tasks during design and development.
› Electronic Data Interchange (EDI) automates the exchange of transactional data between trading partners.
In this eBook, we will explore how automation improves efficiency in each area of an apparel business, starting with product design and development and moving through production, fulfillment and financial management. As you will see, enhancing productivity across your organization can provide many opportunities to improve workforce utilization and help mitigate staffing challenges.

Enhance Creativity and Gain Efficiency in Design
Most companies experience the challenges associated with managing multiple designs, lines and vendors. How can you help apparel designers leverage automation without cramping their creativity?
From sourcing materials and tracking orders in real-time, to accelerating approval workflows, a cloud-based PLM makes it easier than ever to launch new collections while streamlining global operations. McKinsey & Company predicts companies that adopt digitally-enabled value chain solutions could see a 50% reduction in time to market.
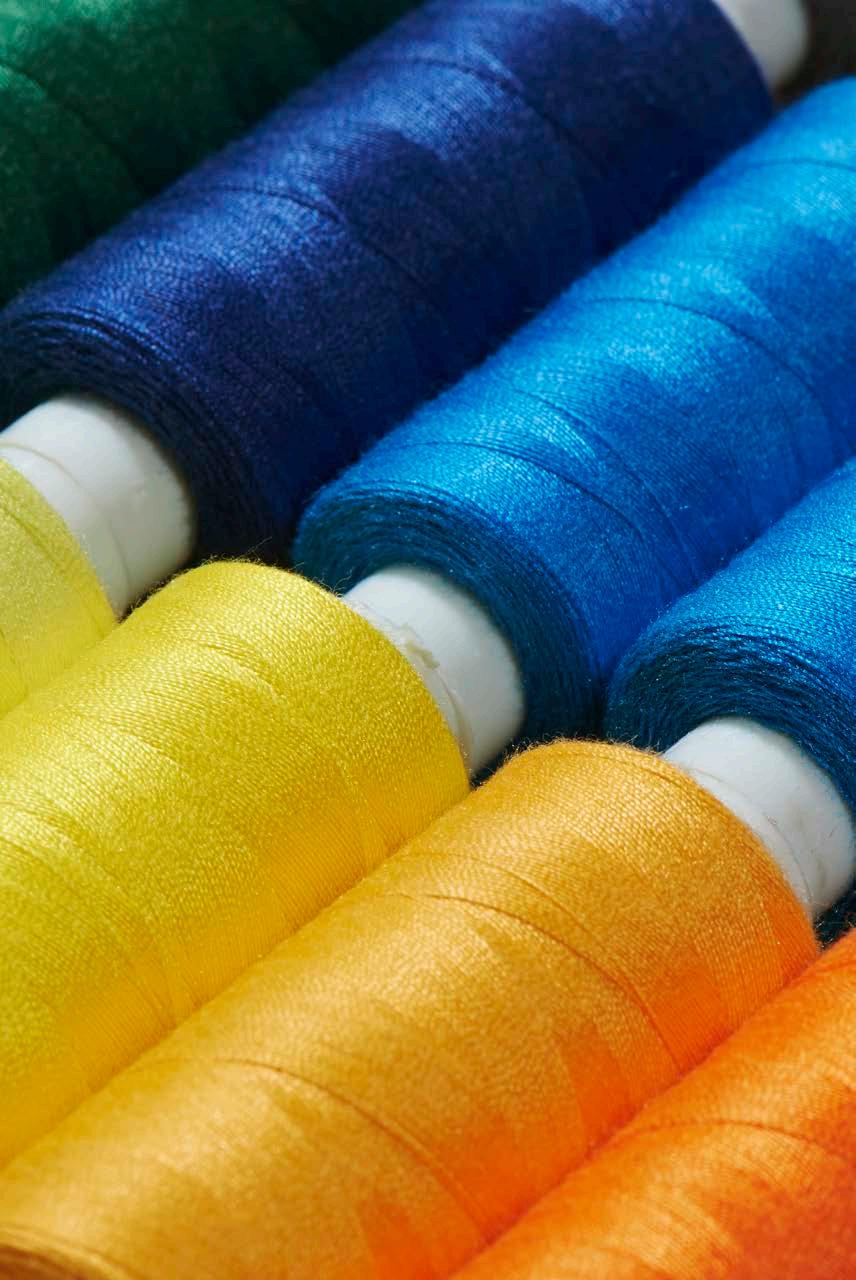
PLM fosters efficient internal collaboration, allowing designers to make better decisions faster while enhancing accuracy throughout the development process. It allows fashion designers to work anywhere and organizes their workflow for better productivity.
A comprehensive apparel PLM should integrate with preferred design tools, freeing designers to focus on creating beautiful pieces rather than tedious data entry. It should also offer functionality to handle multi-dimensional sizing.
After design, integration between PLM and ERP ensures new products smoothly transition to the sales order and production phases of the revenue cycle. Here’s the automation journey within the product design and development stage:
1. All prior designs reside in a centralized PLM database that can be accessed by all teams.
2. Designers can quickly find what they need, make modifications and create new designs.
3. Approvals move seamlessly across the organization, captured in the PLM instead of emails.
4. The PLM automates advanced tech pack development through seamless creation of multiple BOMs, measurements, grading views, templates and more.
5. Designers collaborate with vendors in the PLM by sharing designs and PLM also automates the tracking of samples.
6. Finished designs get pushed to the ERP system and new products are ready for production.
Dollars & ‘Sense’ Impact: PLM
Company: ADPL
Products: Garment manufacturing

Solution: Aptean Apparel PLM
Efficiency: 189% uptick in order volume handled by a 40% smaller design team.
Quality: Better communication with vendors improved sample process.
Experience: Instead of searching paper design books and waiting for hand-made patterns, the team designs quickly and publishes digital tech packs.
Savings: Significant time savings for staff with centralization of files and information. Eliminated the need for on-hand pattern makers.
“Everything is in one place from development through production. Messaging in Aptean Apparel PLM keeps everything together and reduces the e-mail madness for day-to-day follow up—especially sample status for development samples. Also, the communication with sales to get feedback from buyers is easier.”
- Michelle Heyman, Senior Technical Designer, ADPLRead their story
Reduce Administrative Hassle and Errors in Sales Order Processing
Imagine you’ve just received your first order for the new seasonal line. In less automated environments, the ordering and sales process can be very paper- and time-intensive. Fortunately, when you invest in order processing automation through Aptean Apparel ERP with integrated EDI capabilities, your team can enjoy reduced hassle and spend less time on administrative tasks.
EDI is used to seamlessly exchange info with vendors and customers in a secure, standardized format. EDI replaces paper - or email - based documents such as purchase orders, quote requests and invoices, and as a result, it improves order accuracy and reduces order processing times. Both employees and customers save time and benefit from streamlined communication. Some large vendors will no longer do business with trading partners that do not use EDI.
Here’s the automation journey within the sales order processing stage:
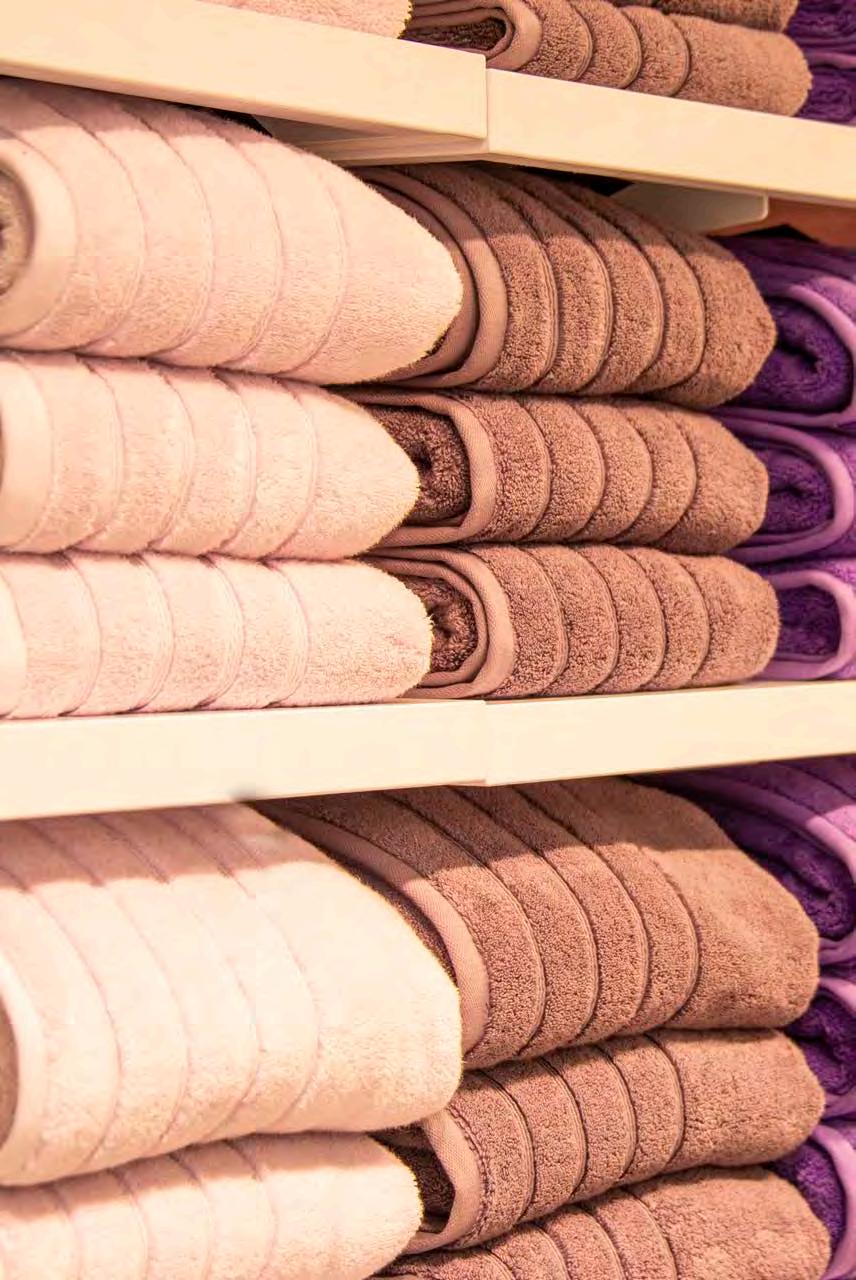
1. Retail customer order is received through EDI.
2. ERP processes the sales transaction and automates the workflows for production planning and materials procurement (more on that next).
3. Sales order information flows to the shop floor control system for manufacturing.
Dollars
& ‘Sense’ Impact: EDI
Company: MindsInSync, Inc
Products: Furniture and home décor wholesale distribution
Solution: Aptean Apparel ERP with EDI
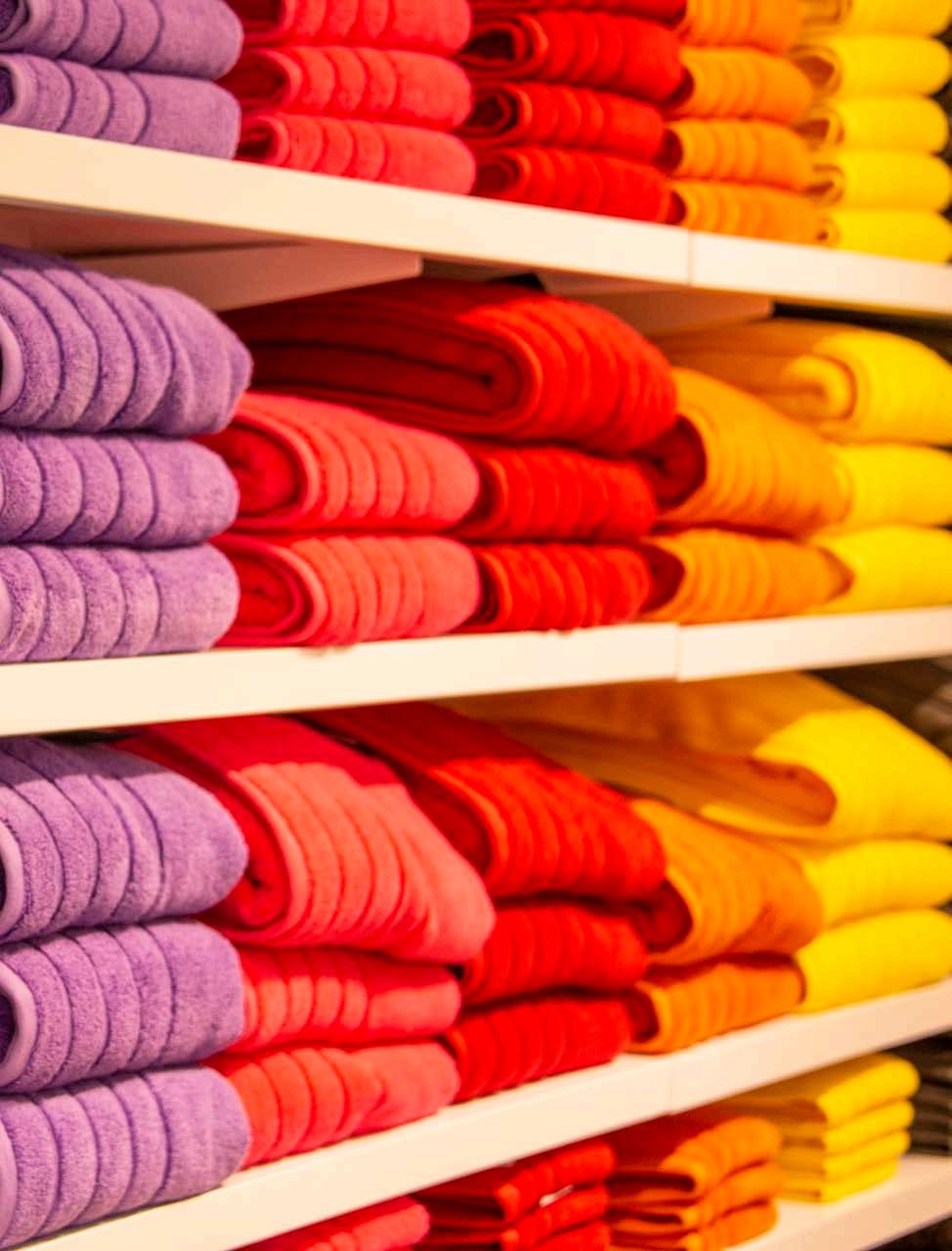
Efficiency: 10X greater volume of transactions processed by a leaner team.
Quality: 90% fewer chargebacks with EDI transactions.
Experience: Employees that used to spend most of their time processing tasks now spend 90% of their time on product development.
Savings: Work that required a staff of 50 is now accomplished by 3, enabling a reallocation of human resources.
Read their story
“Aptean Apparel ERP gave us more confidence to go after more new customers, because we didn’t have to hire a hundred people to deal with more customers. We knew the system could handle it.”
- Iain Scorgie, CEO and Founder, MindsInSync, Inc
Produce Faster, More Accurate Demand Forecasts and Reduce Manual Inventory Counts
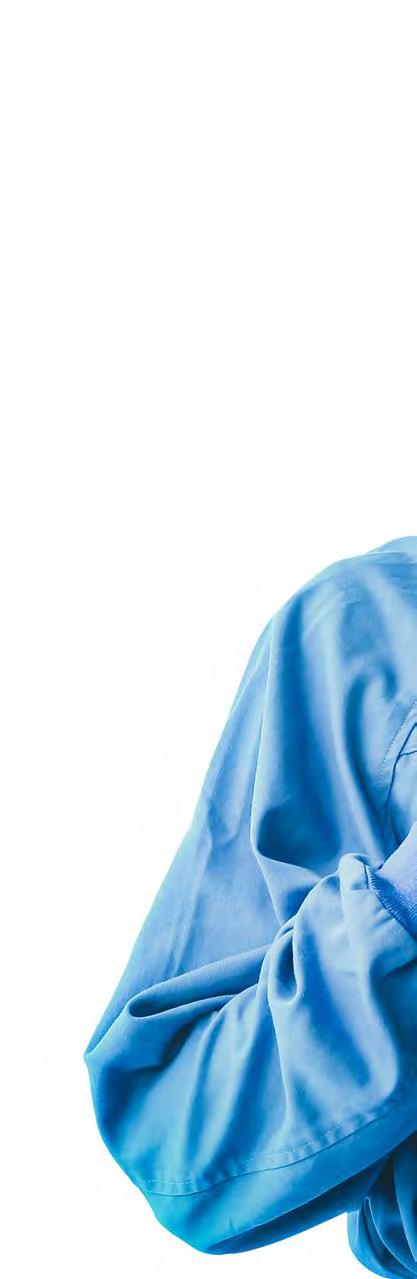
To delight your customer, you will want to move their new order quickly to production, but first you must ensure you have all the right materials on hand to complete the order. An apparelspecific ERP like Aptean Apparel ERP includes flexible material requirements planning (MRP) functionality that can help you reduce inventory costs while optimizing demand forecasting, raw materials procurement and production planning.
With MRP, you are able to purchase the right amount of materials to avoid stock outs that can cause production delays while also avoiding over purchasing that can result in waste. If suppliers also use EDI, you can automate the purchase order process to them. Automated triggers notify when it is time to buy more stock, so there is no need to manually analyze raw materials, nor conduct frequent time-consuming stock counts in the warehouse.
1. After a customer order is received, the ERP assesses order and designs to determine the amount and types of materials required for production.
2. The ERP analyzes what materials are already available in inventory. If supplies are needed, the ERP automates creation of a purchase order and sends for approval.
3. The EDI sends purchase orders (POs) to appropriate suppliers.
4. When stock is received, the ERP conducts three-way matching—between the supplier’s invoice, the PO and the delivery receipt—automates verification, receiving and payments for materials.
5. With raw materials in stock and reserved, the production run for our order is ready to commence.

“For us, it’s very critical that our data that we have in our systems is accurate so that when I’m forecasting, I can forecast the raw materials we predict we will need over the next 12-month period.”
- Shelley White, President, Lac-Mac
Power Up Manufacturing Productivity
It is time to manufacture the goods that will fulfill your order. The combination of an integrated apparel ERP and shop floor control automation can help enable your organization to increase production by boosting manufacturing and quality.
You can also improve shop floor productivity and profitability without adding more production workers when you use shop floor control to gain visibility into production status, incentivize performance and streamline management processes.
Management visibility: Shop floor control provides full visibility throughout production with realtime data collection and web-based dashboards. This lets management see what’s going on with order tracking, line balancing and production planning so they can better allocate limited resources and avoid productivity bottlenecks.
Worker engagement: Shop floor control improves the worker experience by providing feedback about their personal productivity and performance. With this real-time information visible at their workstation, workers don’t need to manually record their production. Using handheld scanners as work moves across the floor eliminates paper gum sheets and saves time for both workers and managers.
Incentive pay: Shop floor control automatically calculates pay and enables management to apply performance pay incentives for individual and team productivity. Providing productivity visibility and incentive pay helped Carhartt achieve 13% improvement in average efficiency with their workforce.

Here is how automation impacts our order during the production stage:
1. Workers clock in at their stations using handheld tablets and receive their assignments.
2. As they sew, workers scan each piece. Piece counts update in real-time and productivity displays on the tablets.
3. If our order production falls behind schedule, managers can apply productivity-based incentive bonuses, which workers then see on their tablets.
4. Shop floor control automatically tracks work through the shop floor.
5. Shop floor control updates earnings information to the payroll system.
Dollars & ‘Sense’ Impact: Shop
Floor Control
Company: Grand Forest, Inc.
Products: Chainsaw protective garment

manufacturing
Solution: Aptean Apparel ERP and Aptean Apparel Shop Floor Control
Efficiency: Faster turnaround time on orders.
Quality: Operators record quality assurance checks on the floor. Management sees real-time data on defects and repairs.
Experience: Reduced managerial and administrative time by approximately 80%, enabling one full-time employee to be reassigned to a more strategic role.
Savings: Reallocated 40 hours per week, one full-time employee, to sourcing and business development which increased revenue opportunities.
“Aptean Apparel Shop Floor Control is amazing! The interface is so clean and clear that it is easy to implement and adopt. It has translated into higher job satisfaction and increased productivity, so much so that Grand Forest achieved a 10% increase in productivity in the first month alone.”
Read their story
Optimize Inventory and Warehouse Management for Efficient Fulfillment
Inventory management and fulfillment are key components of a successful apparel company, and the right ERP can make them more efficient. By automating key inventory tasks and providing real-time visibility into stock levels, an ERP helps you avoid stock-outs and fulfill customer orders efficiently.
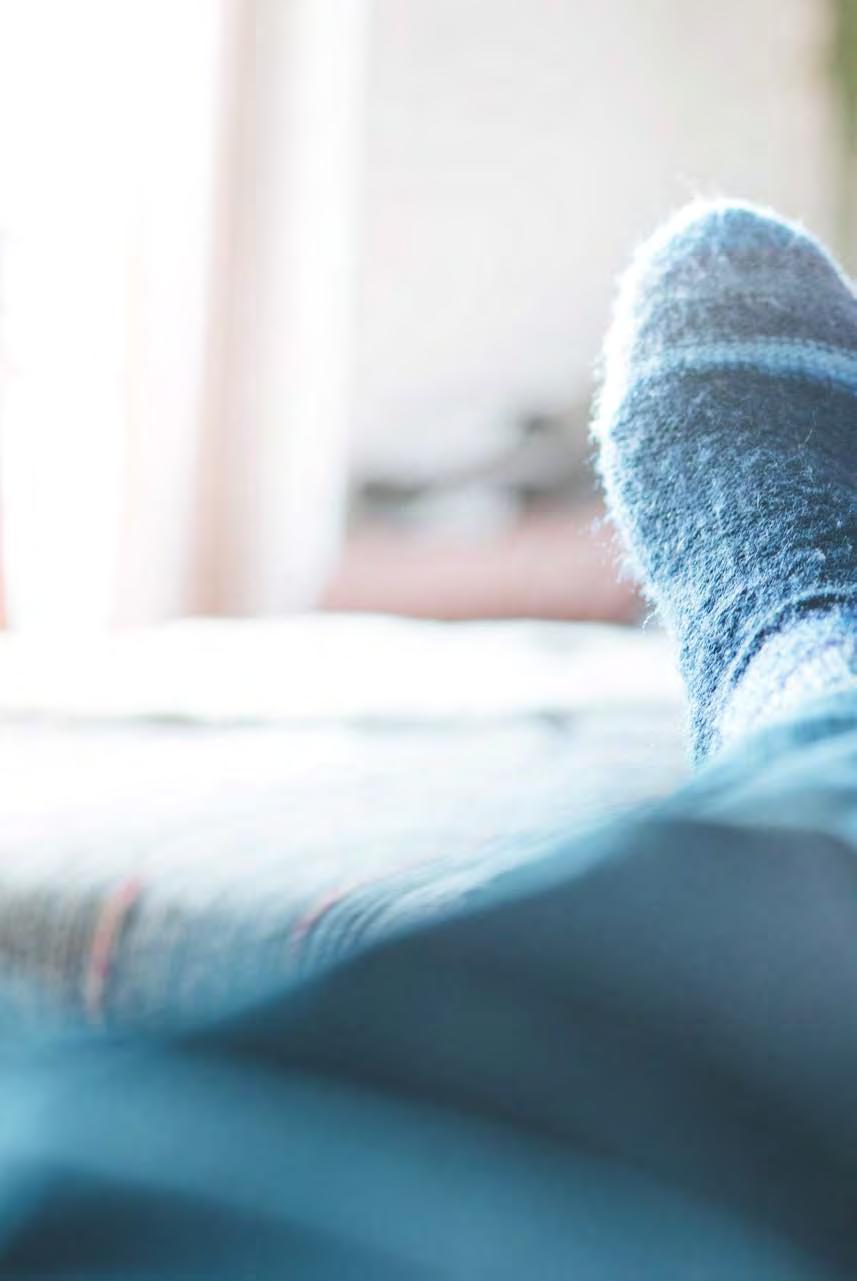
Apparel companies benefit from the operational efficiency of a style-based ERP that includes functionality to create pre-packs through kitting and support multi-retailer same SKU production. An apparel-specific ERP with warehouse management functionality reserves finished goods in the correct sizes, styles and colors for each order. Pick, pack and ship automation supports efficient modes of directed picking and saves time by guiding workers along an optimized route through the warehouse.
Here’s the automation journey as our order heads out the door:
1. Shop Floor Control registered completed production orders in the ERP and finished goods were received back into inventory in the warehouse.
2. The ERP reserves products needed to fulfill our order within the inventory.
3. Warehouse management functionality within the ERP directs pickers efficiently through the warehouse to collect items for the order.
4. The order is packed for delivery to the customer and the ERP tracks the shipping information.
5. EDI creates shipping labels and sends an advanced shipping notice (EDI 856) to the customer.
Dollars & ‘Sense’ Impact: Warehouse and Inventory
Management
Company: Royce Too
Products: Hosiery, socks and legwear

Solution: Aptean Apparel ERP
Efficiency: The warehouse is now entirely paperless. The ERP automatically creates pick tickets and employees pick with handheld RF scanners.
Quality: Inventory is automatically allocated to orders, reducing fulfillment orders.
Experience: Pickers no longer have to be trained to pick for specific customers, so coverage during absences is no longer a problem.
Savings: 20% of warehouse employees’ time was reallocated to other key initiatives.
“Based on what the shipping window is, you can match against available inventory or against inbound production. There used to be a full-time person doing this, and there were still lost orders or out-of-stock situations. They were reserving inventory against an order that might not ship for a month.”
- Larry Warehime, Vice President of IT, Royce TooRead their story
Leverage Omnichannel Fulfillment Automation to Expand Revenue but Not Headcount

An ERP should also help you master omnichannel fulfillment by acting as a system of record for all data—whether sales come from orders from retailers or through e-commerce. Built-in integrations to major e-commerce software, such as Shopify and Amazon, can open multiple consumer channels for expanded revenue opportunities without the need to hire many additional employees.
Here is the automation journey involved in B2C e-commerce:
1. Styles are pushed from the ERP into the e-commerce platform (Shopify, Amazon).
2. Online shopper places order, then the ERP automatically retrieves the order and updates it as an order in the ERP.
3. The ERP generates a pick ticket and updates information for the warehouse or third-party logistics provider (3PL).
4. After fulfillment, the ERP automatically updates the e-commerce platform’s order status to ‘fulfilled’, triggering an email to the end consumer with shipment and tracking information.
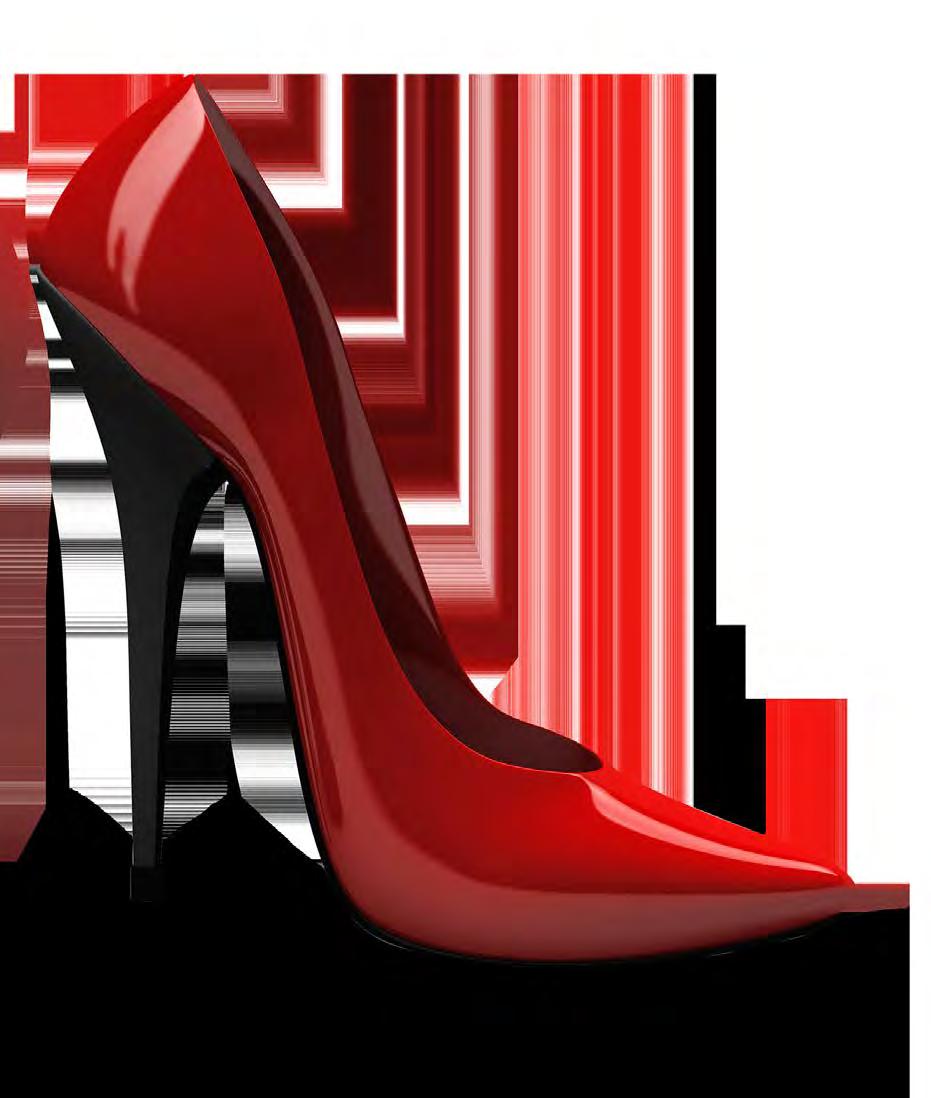
“Omnichannel retailing certainly has added complexities for our business to navigate. It used to be, you would receive an order and ship the goods out to a brick-andmortar store, and that was the end of it.”
- Michael Weinberger, Director of Operations, Trend Marketing
Empower Faster, Smarter Decision Making with Integrated Financial Management
The benefits of automation go beyond operations. With all business data flowing into the ERP, it serves as the single source of truth for back-office professionals, decision-makers and executives.
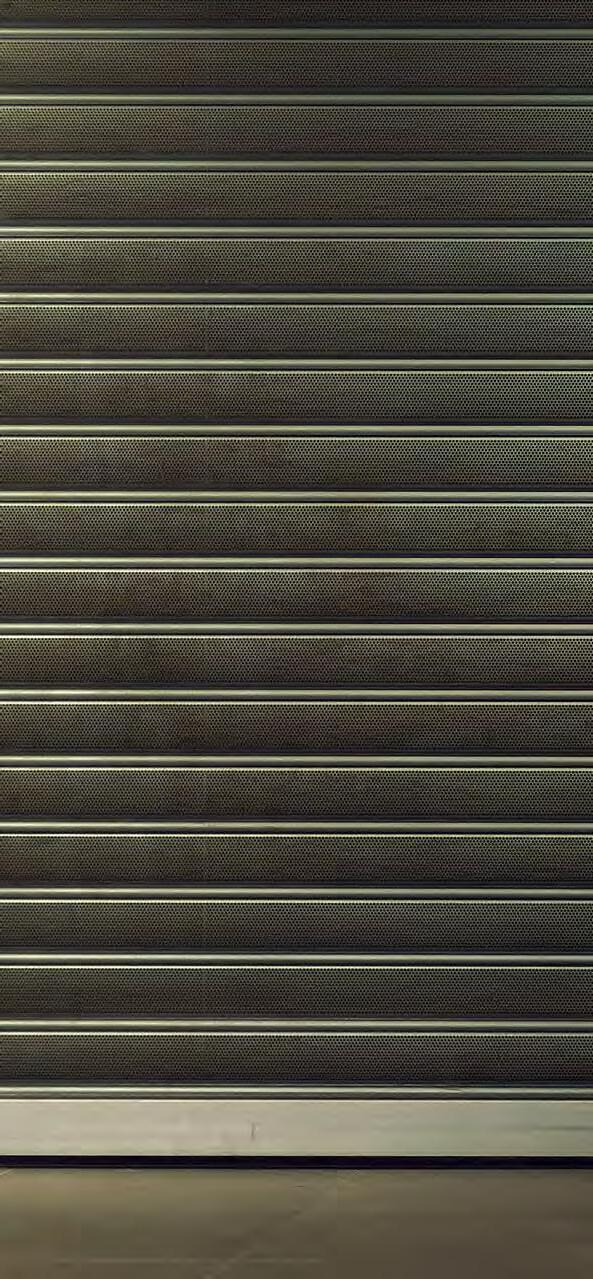
Automated reporting can improve visibility and helps you make smarter, faster decisions. Pre-built management dashboards in the ERP help you make rapid assessments about priorities. This allows you to direct human and financial resources where they’ll make the greatest impact.
Finally, an ERP can save the finance and accounting teams time that can be applied to more strategic analysis. An ERP streamlines financial processes including AP/AR, financial statements, costing analysis, invoicing and additional time-consuming data-entry tasks.
“
I use Aptean Apparel ERP on so many levels—obviously for the accounting portion—but I really look at the data that goes in there to make decisions on the business. I look at it like I look at our P&L statement, at least every couple days, just to see how things are tracking and how things are looking… Everything is reconciled. It’s incredibly powerful because you know down to the penny exactly how much money you should have or do have. There’s no loss of money, nothing can escape Aptean Apparel ERP.”
- Josh D, CEO, REBEL8
Automation Pays Both Business and Workforce Dividends
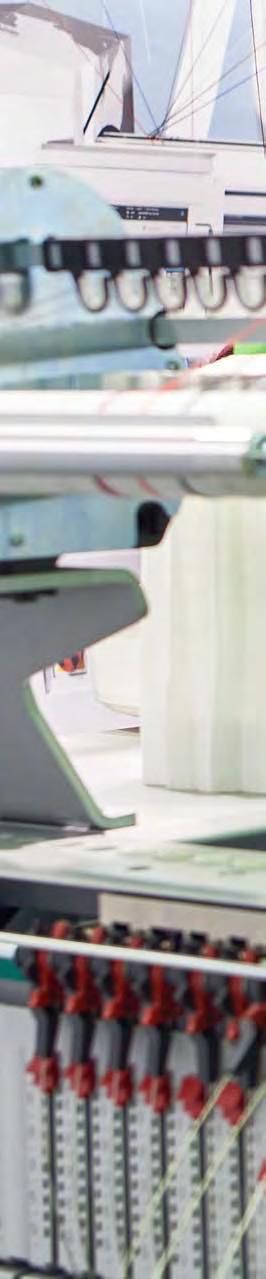
Companies are turning to automation to help mitigate staffing shortages, improve workforce utilization, contain labor costs and support employee satisfaction. Integrated, automated solutions, including ERP, PLM, Shop Floor Control and EDI, improve workforce efficiency and help companies avoid adding headcount while accommodating more orders. In turn, management can put additional dollars toward new product development and business expansion initiatives.
Integrated ERP, Shop Floor Control, PLM and EDI drive efficiency by optimizing workflows, communication and processes across the organization. Productivity gains help apparel companies keep up with rising customer expectations while reducing the need for overtime.
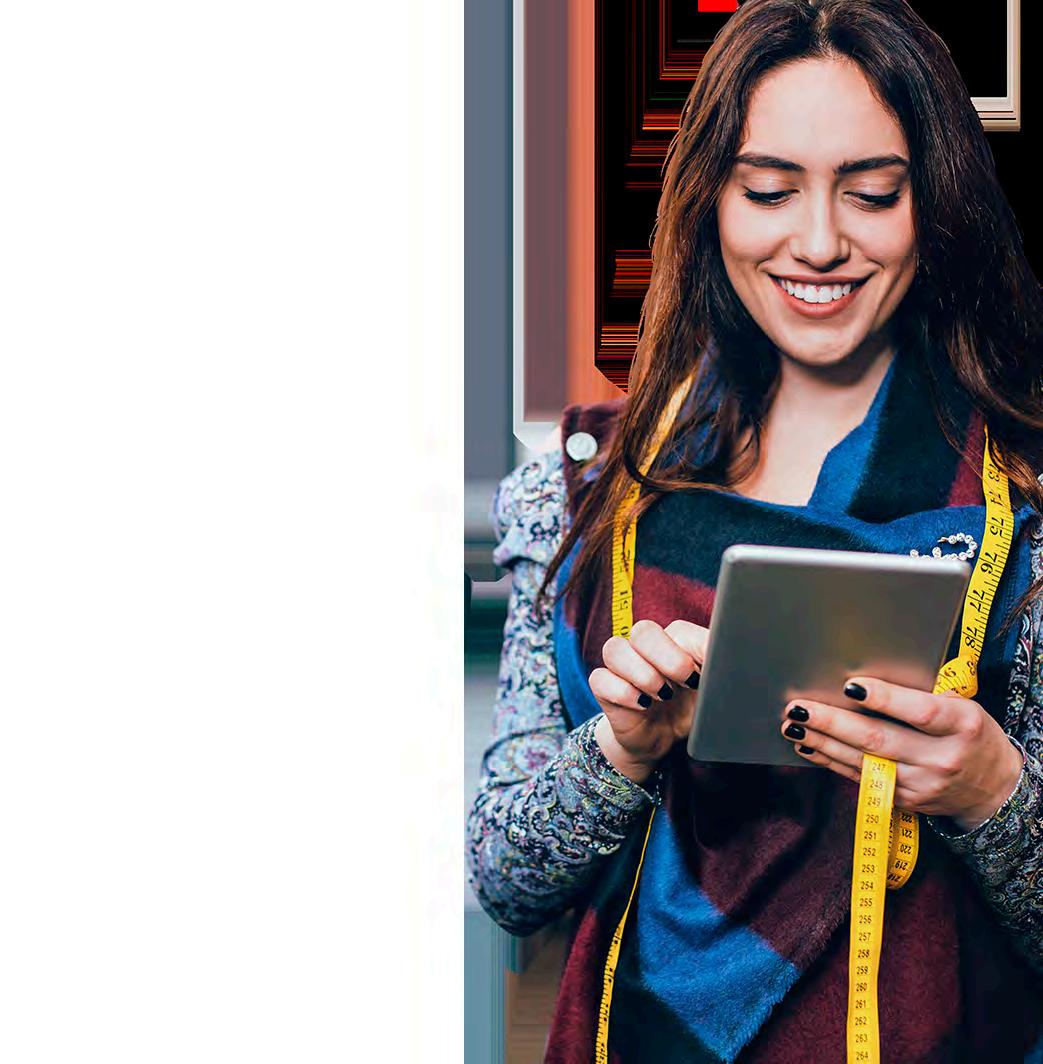
Automation frees up employees to focus on value-added tasks and strategic initiatives that improve the customer experience and support the bottom line. Furthermore, automating tasks prone to human error can improve product quality and customer service.
Giving employees the tools to optimize their personal productivity can enable professional growth that supports workforce retention. Automating repetitive or low-value tasks can improve employee satisfaction and free up time to learn new skills that can lead to career advancement. Shop floor control also has the ability to monitor worker performance data which can identify issues early on and help with staff training.
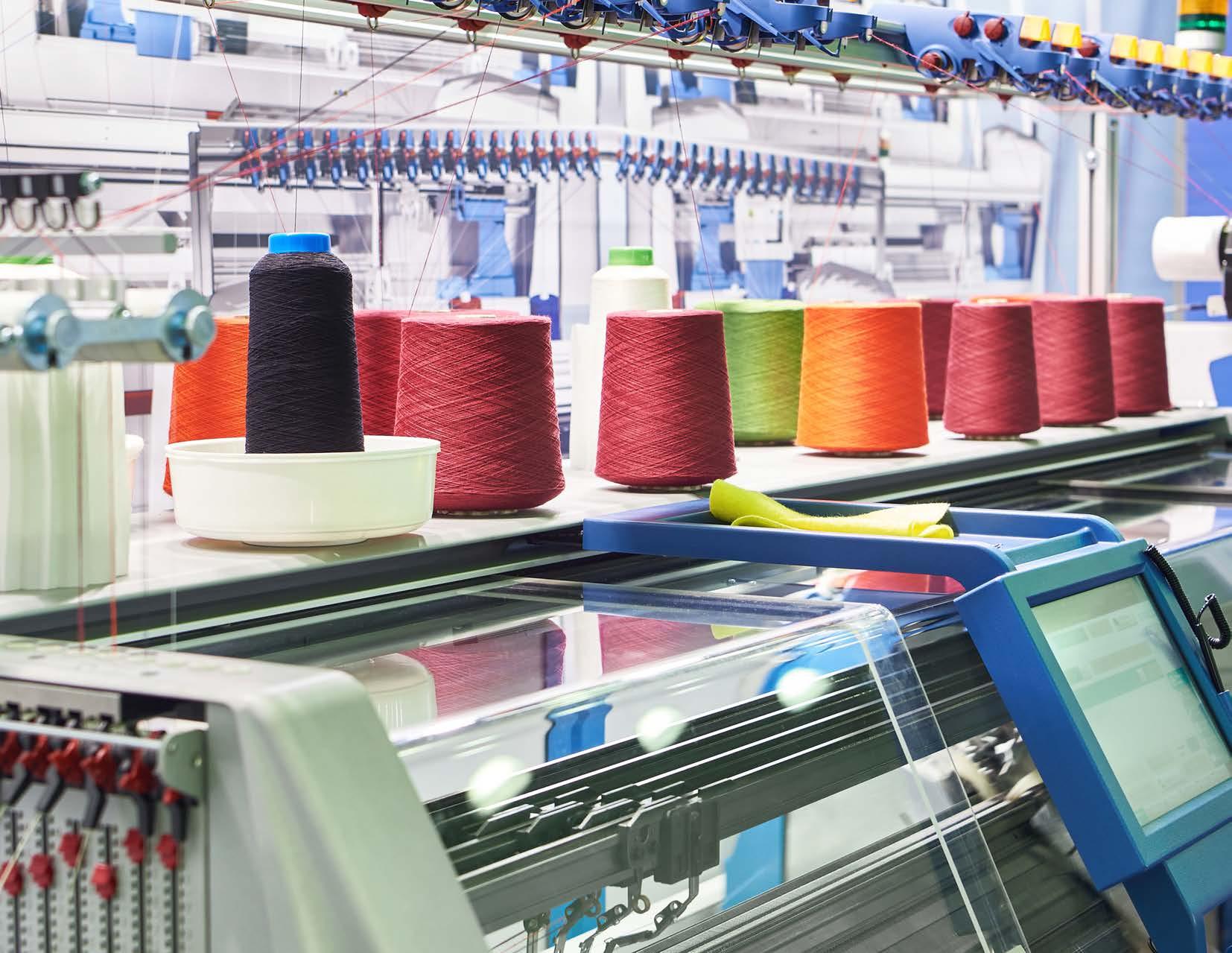
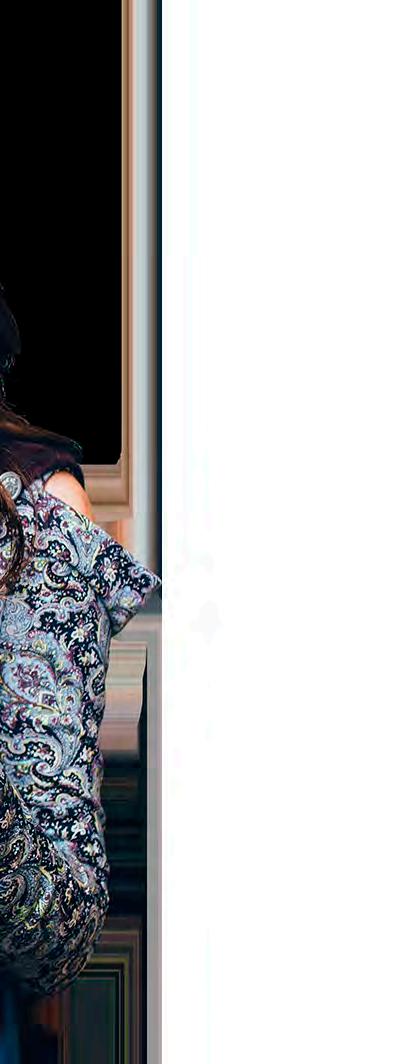
Aptean is one of the world’s leading providers of purpose-built, industry-specific software that helps manufacturers and distributors effectively run and grow their businesses. With both cloud and on-premise deployment options,
services and unmatched expertise help businesses of all sizes to be Ready for What’s Next, Now®. Aptean is headquartered in Alpharetta, Georgia and has offices in North America, Europe and Asia-Pacific.
To learn more about Aptean and the markets we serve, visit www.aptean.com.