Bearfields of London
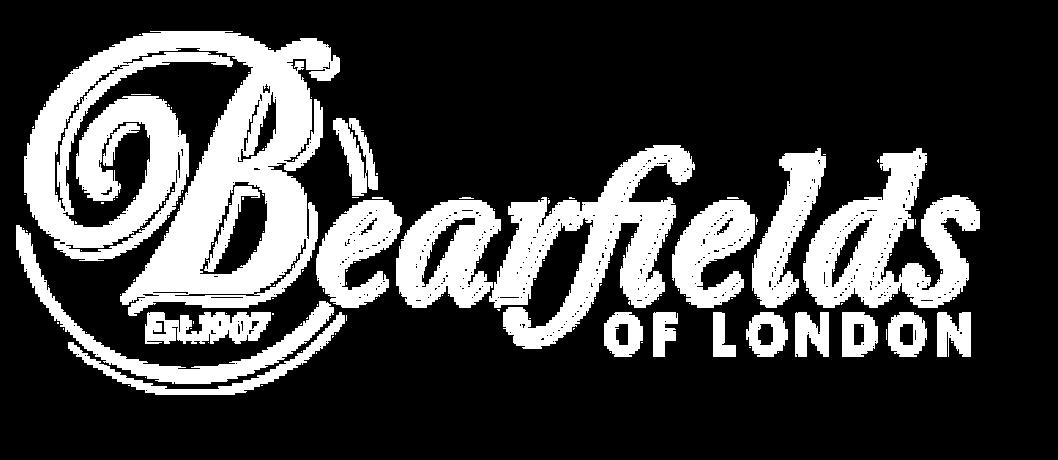
Industry Food & Beverage
Challenges:
» Lack of transparency, visibility and flexibility across the business with current solution
» Reliant on paper to manage operations and QA procedures
Benefits:
» Future-proofed and streamlined operations improving productivity
» Working more effectively by removing human error opportunities
» 100% stock transparency across 5 sites
» Improved paperless QA and traceability
For more than a century and five generations, from a small grocery store in East London to its BRC AA grade accredited premises in Leytonstone, the Bearfields of London family has been producing gammons and hams of the highest standard.
Using traditional curing methods, Bearfields processes and delivers more than 20,000 pork legs every week.
Determined to consistently deliver unrivalled, high-quality service to all of their customers, this award-winning gammon and ham producer constantly invests in its product and staff development, and infrastructure.
Five years ago, Bearfields started its search for a new IT system to help future-proof its business and step up to paperless operations.
As the company’s Operations Director, Neil Edwards, explained, “For some time, various parts of the business had been researching software products that would solve individual departmental problems. However, we quickly realised that this approach would result in a mesh of disconnected products.”
“Strategically, it made far more sense to invest in an all -encompassing solution, and one that would transform us into a paperless business.”
Nigel Cappleman, Senior Account Executive at Aptean continued, “I’d been speaking to Bearfields for quite a while about Aptean’s capabilities. Whilst they had a system in place, it really didn’t fit their business, as it neither controlled or provided stock visibility across its multiple units, or multiple production Work in Progress (WIP) stages.”
“Independent of Aptean, Bearfields sent a team to visit DB Foods, one of our longstanding customers, to see our system in action, together with the instant reporting. As a result of this site visit, they realised they had found a system that was built for their industry.”
Starting with finished good labelling and within a few days of going live, Bearfields had 100% stock transparency and reporting across finished products. Every product now had a unique identifier, and its weights attributed to it.
“As soon as phase one went live, we experienced the many benefits of the Aptean Food & Beverage ERP SI Edition solution. As an example, with one click, we could see everything that had been packed on the lines each day, rather than having to find someone to deliver a report to the management team,” explained Neil.
“The next project challenge was replacing our sales order management system. Our sales team was initially resistant to change since they were used to working with Access but, once the functionality and positive impacts of Aptean’s Sales Order Processing module (SOP) were revealed to them, they soon became advocates! KPI measurements are now transparent, and with SOP linked to picking and despatch, we are confident that the correct stock will be allocated to the right orders.”
“SOP’s detailed reporting also highlighted to sales any customers at risk, by focusing in on any lines that have been lost or where recent customer spend has dropped.”
“With 100% stock and KPI transparency, and sales order processing directly linked to picking and despatch, we’re confident that the right stock is allocated to the right orders.”
Neil Edwards, Operations Director, Bearfields
Every food business understands the mountain of paperwork that has to be undertaken for QA and technical checks.
For Bearfields, as some individual checks generate hundreds of pieces of paper, Neil recognised that digitalisation would provide the best way to eliminate paper-based QA and short interval controls, and manual errors.
To illustrate the scale of the problem and why paperless QA was essential, in advance of a board level discussion about the proposed investment in QA automation, Neil collated a week’s work of paperwork that had been generated for just one technical check.
“I collected up just one week’s worth of paper for a procedural check for packaging labelling. When Steve, our Managing Director, realised how and why this mound of paper had been generated, he was astounded,” explained Neil.
“Seeing the scale of the problem and the opportunity for errors and wasted manpower, it made the decision to buy the Aptean Food & Beverage QA Management very easy.”
“Following the implementation, all of our technical and QA procedures are paperless, and we have realtime visibility on checks, non-conformances, corrective actions and more.”
Neil continued, “Now, whenever the auditors visit, they’re really impressed with the speed and accuracy of the system and our ability to generate comprehensive reports. Whenever they ask for a record to be produced, we can produce the information in seconds.”
“The auditors can then drill down to see all the detail that’s maintained on the application server; whether it’s details of packaging, labelling, or which suppliers provided our raw material, even who signed for it at goods in – it’s all there. Even these days, auditors aren’t used to seeing this level of data all joined up, totally paperless and transparent.”
“If any non-conformances are uncovered, we use Aptean Food & Beverage ERP SI Edition to improve our controls. For instance, by introducing individual pin numbers on procedures to control operator access, it proves exactly who completed the checks and filled in the details.”
“All of our technical and QA procedures are now paperless; we have real-time visibility on checks, non-conformances, and corrective actions.”
Neil Edwards, Operations Director, Bearfields
When Aptean conducted the process review, Bearfields of London also asked for the ergonomics within the factory to be taken into account.
One example of an area where Aptean proposed improvements, that delivered significant savings, was at raw material intake management.
“At intake, the legs of pork are suspended on a tree rail system, approximately 25ft above the factory floor,” explained Aptean’s Nigel Cappleman, Senior Account Executive. “It was a two-man job as operators were required to be stationed at both the printer for labelling at the carcass height, that was housed in a garage, and also at the intake screen on the factory floor.”
“Since we rationalised the process, by enhancing our raw material intake module to print once the scale registered a steady weight, raw material intake can now be managed by one operator.”
Producing hams and gammons is a multi-WIP process, and that’s where Aptean’s Run Manager software comes into its own. Now, all the factory production runs can be set up within the Aptean system to take account of these multiple processes; whether it’s prepping and butchering the legs, brining, tumbling cooking or chilling, forming or packing.
“To eliminate human error, the vision for the system was to display clear operator instructions on screen, on the factory floor. To achieve this objective, we implemented our Run Maintenance module, and at each stage, we ensured that there was just one input and one output. Thanks to these step-by-step screen-led instructions, the operators know precisely what needs to be done next,” explained Neil.
He continued, “Now our operators know exactly which batch of legs next need to be issued to butchery and, if they do scan the wrong barcode, the system flags up that they have done so. When the correct batch is scanned, Run Maintenance verifies that it’s been allocated and then, when the product has been boned out, it will be weighed and labelled, and ready for further processing.”
“Now that the Aptean system is live, we know the precise location of every one of our products.”
Neil Edwards, Operations Director, Bearfields
For any food manufacturing business, your stock position can be make or break. At Bearfields, with stock stored across 5 sites, and without a viable system tracking the position and use-by dates, too much product was at risk of becoming waste.
“Now with Aptean Food & Beverage ERP SI Edition we know the precise location of every one of our products,” explained Neil Edwards, Operations Director at Bearfields.
Neil continued, “With our previous IT system, whenever goods were picked from stock, we were reliant on our pickers writing down all the weights from the printed labels, and then adding these numbers up to calculate the total weights for picked goods. However, as these numbers were then handed over to be inputted again by someone else, inevitably errors crept in every time these calculations were made.”
“We estimated that every picking order involved 4-5 members of staff, which meant there were multiple opportunities for human error. In fact, so much paperwork was being churned out every day that we couldn’t realistically assess just how many errors were being generated.”
“Once the Aptean implementation went live and with pickers using barcode scanners, the precise location of products became available in real-time. The barcode scanner shows exactly where the product is kept and can even help to build the pallets.”
“Any invoices and despatch notes that need to go with the order are automatically generated by the software. We know that it will always be correct. We now had a system that cuts out human error, didn’t make mistakes and it was a revelation.”
“We noticed it at every level. With stock transparency on all finished goods, sales could see in real-time whatever was available, and all the prices. We can dissect by standard cost, average cost and see the real value. But we also uncovered irregularities in the old stock take system. The first time we compared dried goods costs, we found pricing that probably hadn’t been updated in years!”
“Transparency, streamlining operations, working leaner and smarter - these are the biggest benefits we’ve realised with Aptean”
Neil Edwards, Operations Director, Bearfields
“If I was to summarise the biggest benefits we’ve realised since the implementation, it’s all about transparency, streamlining operations, working leaner and smarter. 100% transparency means that we have far less cash tied up in stock,” stated Managing Director, Steve Bearfield.
“Our cost of service has decreased, as we don’t need as many pickers within the despatch area. In fact, the efficiencies delivered by Sales Order Processing has meant we’ve been able to reduce our sales headcount by one. Less tacit knowledge is needed, as the system curates all that technical know-how and instructs the operators every step of the way.”
Nigel summarised, “Bearfields of London is a great example of what can be achieved with Aptean Food & Beverage ERP SI Edition and Aptean Food & Beverage QA Management. By stepping up to a paperless factory and streamlining processes they have increased throughput without having to invest in a bigger factory, gained 100% transparency, and are working as leanly and profitably as possible”.
Aptean is one of the world’s leading providers of purpose-built, industry-specific
that helps manufacturers and distributors effectively run and grow their businesses. With both cloud and on-premise deployment options, Aptean’s products, services and unmatched expertise help businesses of all sizes to be Ready for What’s Next, Now®. Aptean is headquartered in Alpharetta, Georgia and has offices in North America, Europe and Asia-Pacific.
To learn more about Aptean and the markets we serve, visit www.aptean.com