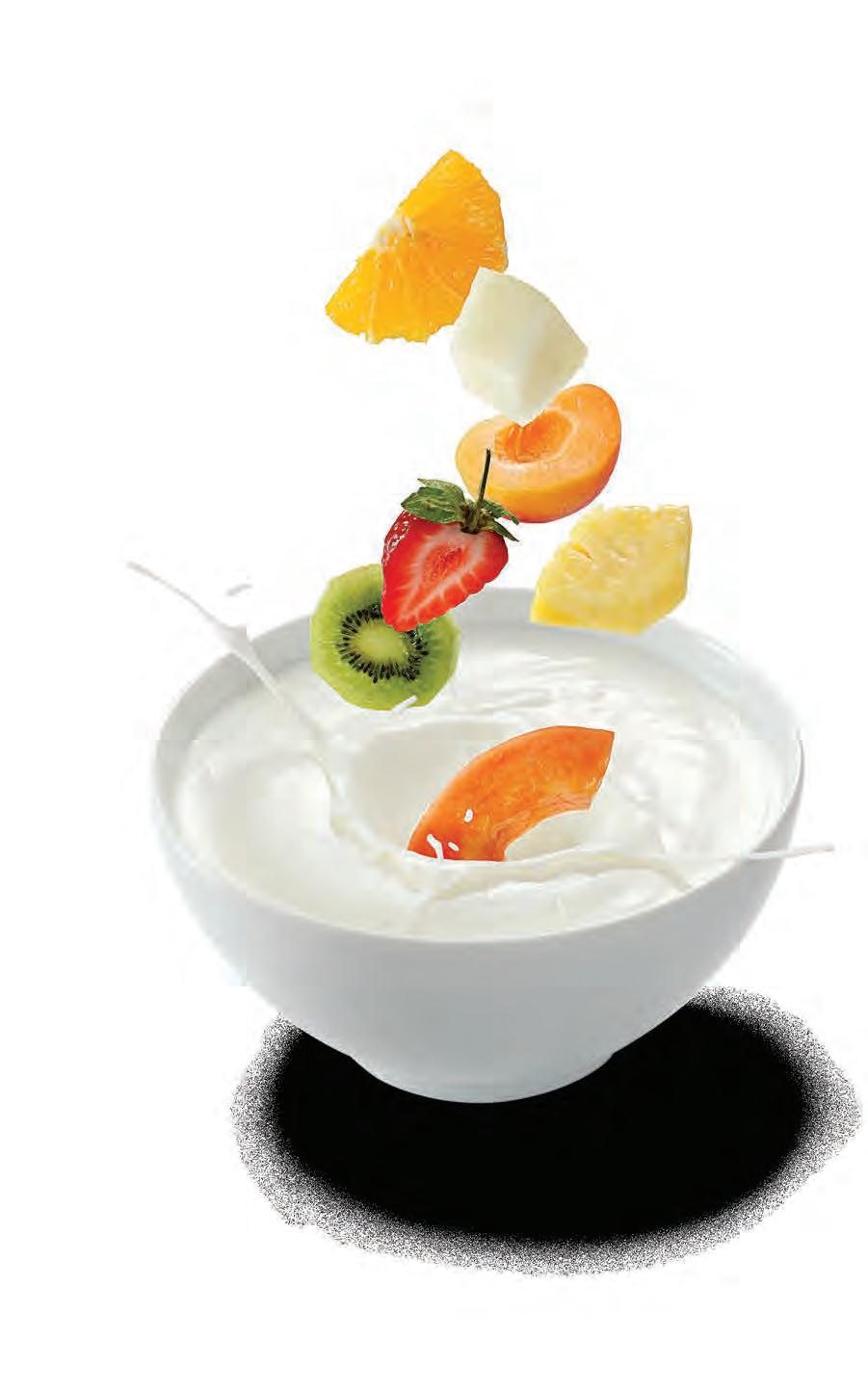
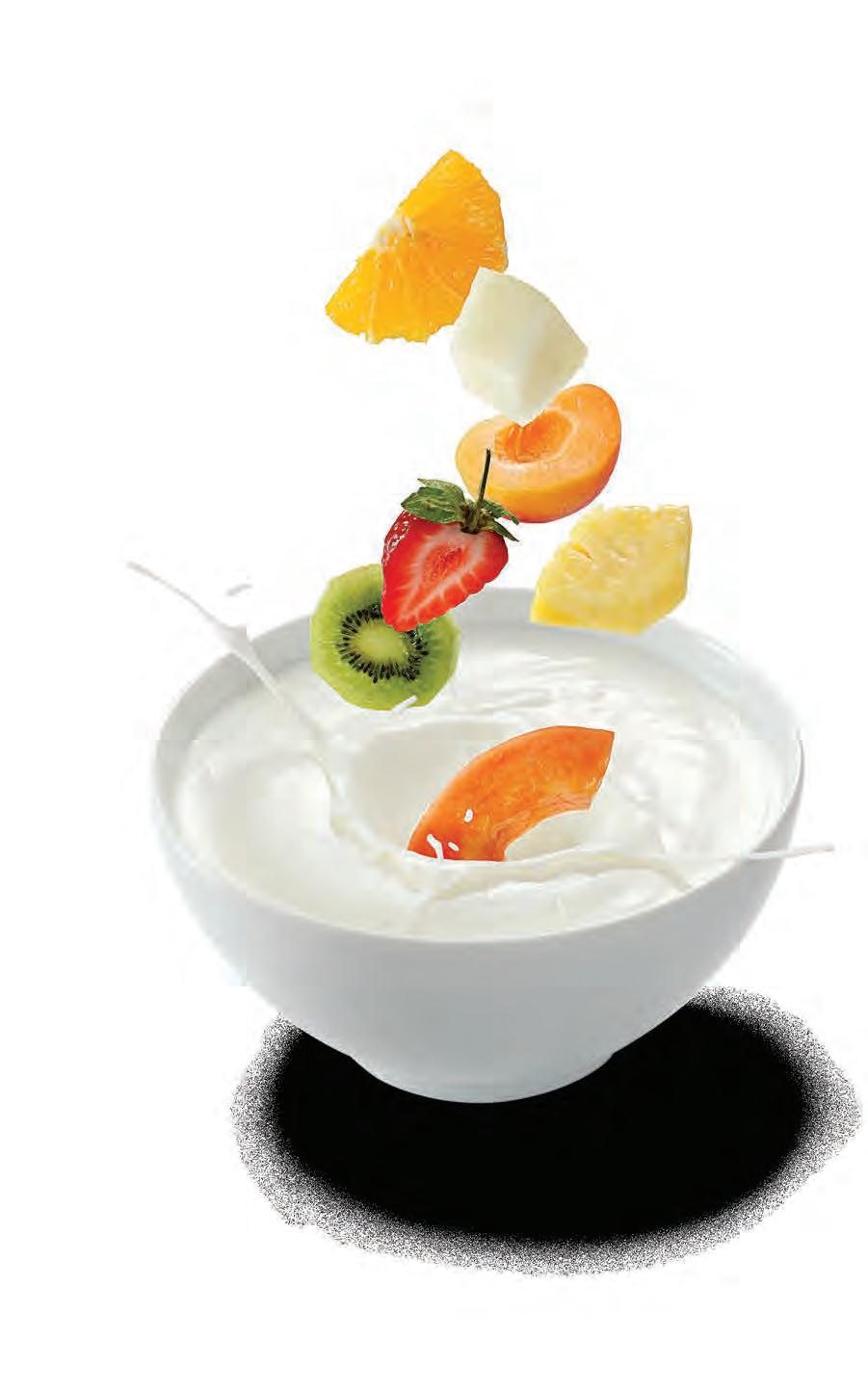
Managing Profitability When Raising Your Prices is Not an Option
Whether it’s due to consolidation or pandemic-related shifts in demand, food businesses are dealing with a near-constant downward pressure on prices. As a professional in the industry, your first reaction is likely to examine your costs and internal processes to trim the fat and maximize profitability.
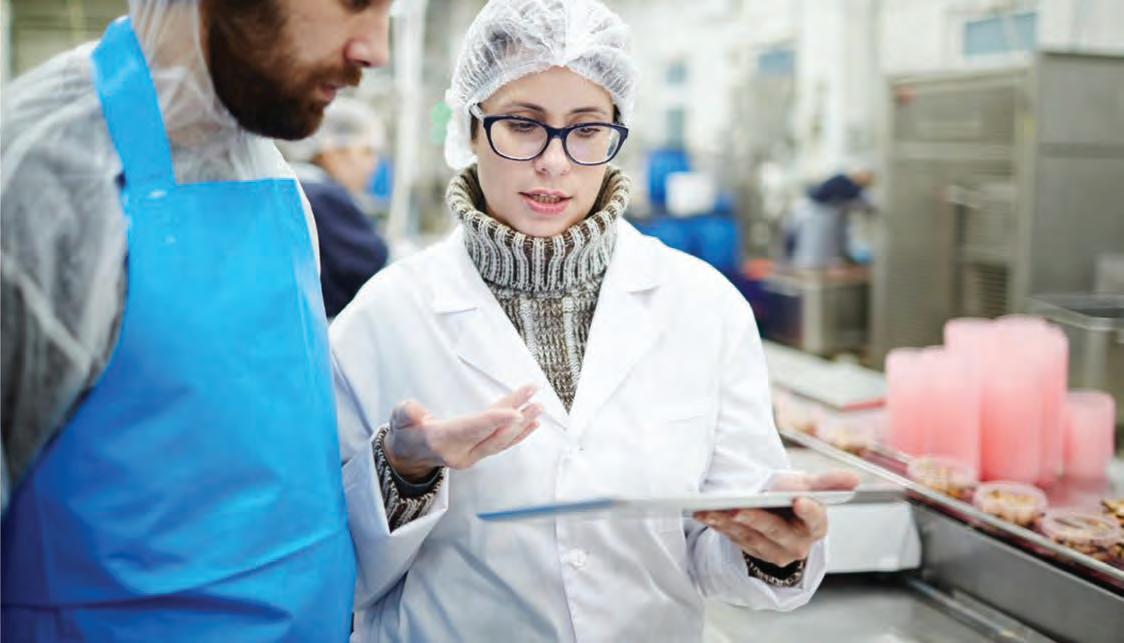
Beware, however, of making changes just for change’s sake. Legendary basketball coach John Wooden said it best: “Never mistake activity for achievement.”
If, for example, you focus solely on reducing your unskilled labor force on the line as a means of increasing your margins, you’d be unlikely to get the results you really want—consider that the USDA Economic Research Service recently conducted an analysis and found that direct labor costs account for only 8% of food production costs for North American businesses.
Clearly, your efforts need to be purposeful and backed by data if you’re going to increase your margins. Let’s examine some best practices, all of which share a common idea—utilizing software solutions to make sense of your numbers and make intelligent, informed decisions.
Profitability When Raising Your Prices is Not an Option
Expiry Management
Waste through expiring unused ingredients is an obvious problem your business wants to avoid. How do you make sure everything gets used at the right time, before it’s too late?
Accurate information collection and total visibility will enable you to watch the dates and create a system that ensures you get the most out of your materials. Just make sure that your data capture starts at the first possible instance—likely at the loading dock as deliveries are received.
Shelf Life Management
Selling your products while they’re still good is the next logical step after making sure your ingredients are utilized optimally. Most enterprise resource planning (ERP) software automatically allocates inventory for orders based on a first-expiry-first-out basis, but the best solutions go a few steps beyond that.
Keep in mind that certain customers have different freshness demands for the products they carry—the ideal system would offer functionality to account for this and manage inventory accordingly. This part of the system should obviously also be integrated with your raw material inventory data to really maximize the shelf life of the goods you ship.
Recipe Management
What other measures can a food business take to tighten up their operations and achieve efficiency? Once the previous two considerations are covered, it’s time to take a closer look at how production is carried out on the warehouse floor.
With sound recipe management, not only will you have visibility into what ingredients are getting used when— critical in the event that an expired material does get used and a recall or rework is issued—you’ll also be able to determine what’s most cost-effective and what calls for allergen management. That allows you to remain agile, get the most bang for your buck, and head off potential complications before they arise.
Accurate information collection and total visibility will enable you to watch the dates and create a system that ensures you get the most out of your materials.
Production and Yield Reporting
You no doubt regularly review and compare expected and actual yields and costs to keep tabs on what’s working and what’s not. But are you doing it often enough? And are your figures reliable?
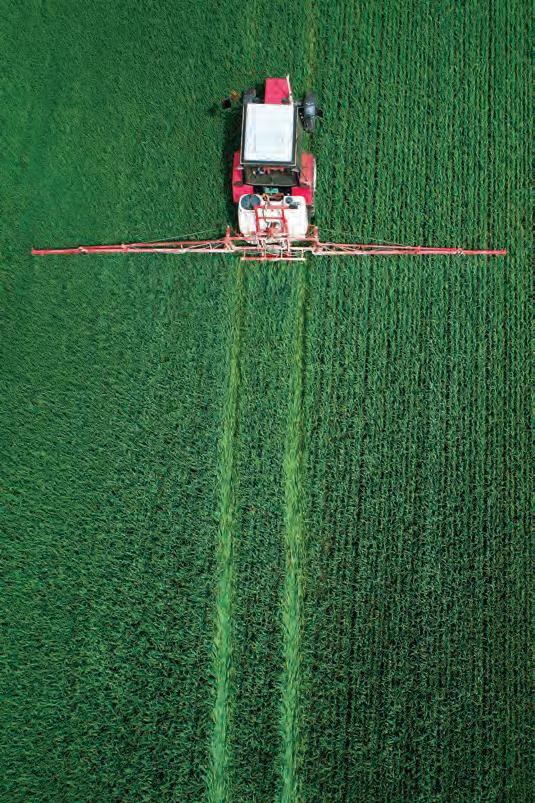
With margins as thin as they are already, this is an area that warrants special attention. Again, technology can give you the insight you need to make smart decisions quickly. Reports should be ready at the touch of a button so that you can react properly to any fluctuations that occur.
Maintenance Management
Food businesses like yours would love if equipment only required its up-front purchase price to guarantee smooth operation. The fact of the matter, though, is that in order to make sure your processes remain uninterrupted, you need to have a robust system in place to ensure all necessary maintenance—including preventative measures—is conducted.
Tracking dates and procedures by hand won’t cut it, especially if your facilities are large and feature a number of different machines. Software can likely handle the scheduling more effectively than an individual employee, as a good system will be able to account for far more factors at once than a human.
Applying Error Trapping
Pilots and software programmers alike are familiar with the concept of “error trapping.” At the heart of this idea is the principle that an ounce of prevention is worth a pound of cure.
An example of error trapping in the airline industry is the capability of on-board systems to alert the crew in the event that the plane has assumed a landing posture with its landing gear still in the “up” position. That way, the proper intervention can be taken, and mistakes can be avoided.
It’s a fact of human nature that individual employees will occasionally forget certain procedures, miss critical details or otherwise neglect a routine responsibility. The best software solutions for food manufacturers are programmed with error trapping technology unique to industry applications.
After all, why deal with a problem after it’s occurred when it can be eliminated beforehand?
Technology can give you the insight you need to make smart decisions quickly. Reports should be ready at the touch of a button so that you can react properly to any fluctuations that occur.
The Thread that Ties It All Together
Implementing an industry-specific ERP solution not only relieves your workers of these burdensome tracking tasks—it also does them quicker, more accurately and with more complete information. That’s the kind of intelligence it takes to squeeze the most out of your business processes.
Are You Ready to Learn More?
If you’re looking to modernize and gain a competitive advantage in the dynamic food marketplace, see how Aptean’s offerings can work for your business. Contact us at info@aptean.com or visit www.aptean.com.
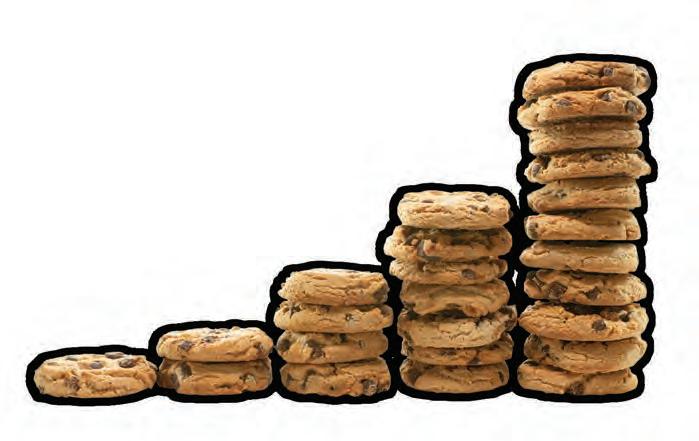
About Aptean
Aptean is one of the world’s leading providers of industry-specific software. Our enterprise resource planning and supply chain solutions are uniquely designed to meet the needs of specialized manufacturers and distributors, while our compliance solutions serve specific markets such as finance and life sciences. With both cloud and on-premise deployment options, Aptean’s products, services and unmatched expertise help businesses of all sizes, across many industries, to scale and succeed. For more information, visit www.aptean.com.