How to Ensure Product Compliance in a Global Environment
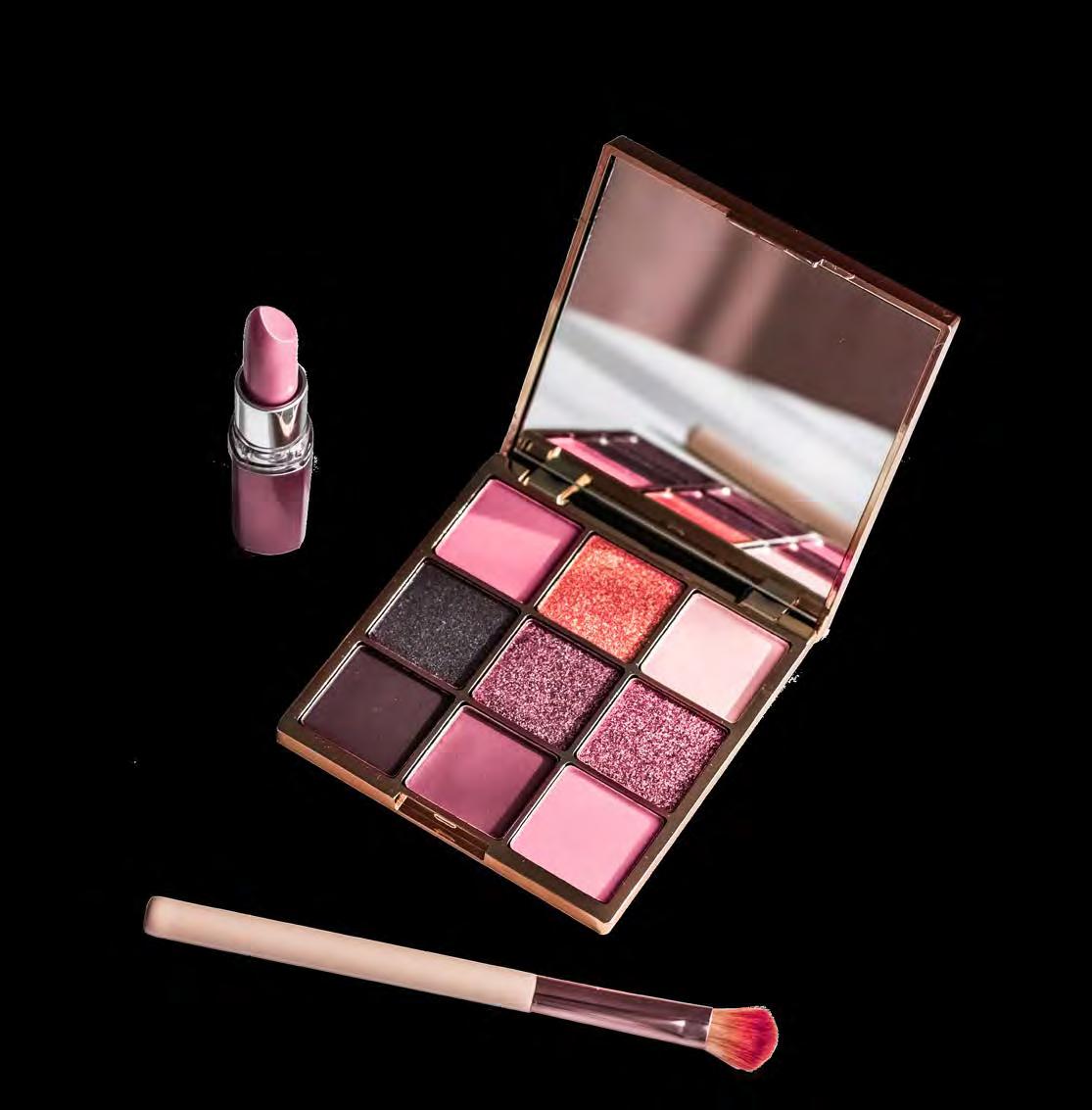
Each cosmetic product sold in the world must be compliant with current regulations. They can be very complex and time consuming to set up for business. Each country and sometimes state has its own regulations that manufacturers have to follow.
The European Union has the most strengthened and structured regulations around cosmetic products and many businesses, in the world, are using it as a standard. On the other hand, North America has less rules and laws for manufacturers to respect.
With globalization and brands expanding all over the world, businesses are held to different laws, each of which have to be understood, and respected.
Product categories can determine which law or act to respect for example, haircare with hairsprays have different rules compared to makeup.
Manufacturers have thousands of different references in different product categories and with each new product development the regulatory compliance process has to be started all over.
In this whitepaper, you will get more information about the main regulations to follow in North America and in the EU when commercializing cosmetic products followed by experts’ best practices on how to ensure product compliance through its entire lifecycle.
Nowadays, major manufacturers and brands are commercializing their products all over the world, through their website, physical stores and retailers.
International compliance is very complex but also sensitive as it involves product recalls or bans and fines. Before considering globalization, regulations enforced in the country where the product will be commercialized needs to be implemented. It can be expensive, time consuming and ruin a brand reputation if not done properly.
During product formulation all the substances used in the product formula must be authorized in the country where it will be sold. Banned ingredients are frequent in many countries and regions but they vary according to regulations being implemented.
In addition, some products are completely banned and some others have to be used in maximum concentration. Concentration can be different in each country but also per product category. For example, a face moisturizer won’t have the same regulations as a fragrance.
During product testing and compliance stages teams have to do the required safety tests which can differ from one country to another. For example, the EU requests all manufacturers do specific tests such as toxicology, etc whereas in the US no specific tests are required but manufacturers must ensure product safety.
Once product testing proves that the product is safe to be sold, manufacturers have to gather all the results in different mandatory dossiers (PIF, SDS, etc.).
In order to complete required documents and dossiers such as SDSs or the PIF, manufacturers need to collect all the information regarding the product, including raw materials In the cosmetic industry, it could quickly become a nightmare to collect the right information.
Most of the time, many different stakeholders are involved in the product development process either internally from other departments or externally with agencies and suppliers.
Retrieving the information can be complex and time consuming Information must be accurate, organized and complete to avoid re processing and losing time.
Each time a new product is developed, the same process has to start all over again. Making sure all ingredients are safe and compliant with each country in which it will be sold.
In a fast evolving market, new product releases have never been that quick. As trends and consumer needs change frequently, manufacturers and brands have to follow up and create adapted products.
But each time, a new product is launched, the same regulatory processes are applied to it. Most regulations concern finished products and raw materials. For example, a Product Information File must be submitted for each product and information on each ingredient that should be included That makes the teams work even more complicated and increases the risk of mistakes.
When launching a new cosmetic product, manufacturers do not need the FDA’s pre approval but must ensure product safety and compliance with regulations being implemented. The only exception is for color additives which need FDA approval and follow different rules.
The FDA authority will check the product only if they receive complaints from consumers and if it does not comply with the laws in forced.
Legal authority still encourages manufacturers to submit their product only the ones sold to consumers, but on a voluntary basis the Voluntary Cosmetic Registration Program (VCRP).
It allows the FDA to assess product safety, ingredients, frequency of use and maintain a list of registered businesses involved in the cosmetic industry The VCRP will not provide manufacturers an approval or disapproval for a cosmetic product to be on the market but support the FDA work on product safety for consumers
VCRP offers three ways to participate
› Register cosmetic manufacturing and packaging establishments
› Fill Cosmetic Product Ingredient Statements (CPIS)
› Amend or Discontinue a product formulation
As mentioned earlier, the FDA does not require manufacturers to register cosmetic products before commercialization, unlike the European Union.
Manufacturers and businesses have the legal responsibility to ensure product safety and labeling. No specific tests are recommended or compulsory but the manufacturer should do anything in its power to make sure products are safe to be used by consumers. In addition, they do not have to submit any proof of testing or safety information to the FDA. But these documents can be reviewed if the FDA randomly visits the manufacturing facility.
However, the legal authority has put together a list of prohibited and restricted ingredients considered harmful if used in cosmetic products.
The list contains 8 prohibited and 2 restricted ingredients and is not as strict as the one in the EU – with more than 1000 ingredients banned, or the one enforced by the state of California, Proposition 65.
The FDA does inspect products and facilities on a regular basis but manufacturers are not required to notify them of customer complaints.
In addition, the FDA does not have the right to order recalls. They need to be initiated by the manufacturer and will be, then, monitored by legal authority.
If a cosmetic is considered misbranded or adulterated and has received several complaints from customers, the FDA can pursue action through the department of Justice and order the recall of the product.
The FDA under the Fair Packaging and Labeling Act ( regulates cosmetic product labeling to ensure that package and labels give consumers accurate information about the product.
Labeling information must be written in English except for U.S. regions where another language is predominant (e.g. Puerto Rico).
The FPLA gives detailed information on the cosmetic labeling regulations and what must be shown on the product label outer and inner packaging. Font, label size, font size, information layout and more guidance that can be found in the Cosmetic Labeling Guide.
and use of
Each of the 50 states of the U S are under national and federal regulations. It is not uncommon that states have different regulations from others. This is exactly the case in the state of California. In addition to FDA regulations, California has its own rules that all businesses selling in the state must follow.
Most of those regulations concerns product safety for consumers with more specification and control in California than in any other state.
Thanks to the Sherman Food, Drug, and Cosmetic Law also known as the Sherman Law, the CDPH* through which the Food and Drugs Branch, has full authority over cosmetics, drugs and foods. In other words, the state of California, can decide of any regulations and rules that apply to cosmetic products.
*California Department of Public HealthFirst published in 1986, Proposition 65, also known as California’s Safe Drinking Water and Toxic Enforcement Act, first goal is to protect drinking water sources from toxic substances that may cause cancer, birth defects or other reproductive harm and overall reduce exposures to harmful chemicals.
Over the years, it has become a resource to increase consumer safety towards any chemicals identified in products. The OEHHA* is responsible to publish and update, at least once a year, the Proposition 65 list that now includes over 900 substances.
The list contains information on the substance, type of toxicity, listed date, the safe harbor level level of hazardousness, CAS number, etc.
If any of your product contains at least one of these substances, you must warn the consumers by:
› Adding a specific label on the product e.g. – “Warning this product contains a chemical known to the State of California to cause cancer”
› Posting signs at the workplace
› Distributing or publishing notices
The warning should be easily understandable, readable and prominently placed.
Exemptions:
› Businesses with nine or fewer employees
› Governmental agencies and public water utilities
› Products that contain chemicals below the safe harbor level
*Office of Environmental Health Hazard AssessmentIn addition to Prop 65, in 2005 California released its Safe Cosmetic Act and became the first state to pass a legislation around safety and on the reporting of cosmetic ingredients. The program aims to protect consumers and promote the safe manufacture of cosmetic products.
It requires manufacturer, packer and distributor, with at least $1 million annual revenue, to identify any cosmetic products that contain ingredients known to be potentially harmful or harmful to consumers – e.g. ingredients that could cause cancer, birth defects, etc. They also have to report ingredients concentration within the product and continuously update the report in the case of any change.
Hazardous and potentially hazardous ingredients are then identified within the list of chemical ingredients including chemicals listed under California’s Proposition 65 as well as those listed by the U.S. Environmental Protection Agency (EPA), the Center for Evaluation of Risk to Human Reproduction (CERHR) and the International Agency for Research on Cancer (IARC).
Created in 1967 the CARB is the California Air Resources Board California is the only state that has its own board because, the Clean Air Act regulates the rest of the country.
The main goals of this agency are to protect the public from the harmful effects of air pollutants and developing programs to fight climate change.
The National Organic Program (NOP) under the Organic Foods Production Act regulates nationwide, organic products. A set of rules and conditions have been established in order to determine if a product is organic or not.The NOP, only concerns food and beverage products and nothing has been set nationally to regulate cosmetics.
That is why, California launched in 2003 COPA. In alignment with the NOP, it does not only concern food but also cosmetic products. It requires that cosmetic products sold as organic must contain at least 70% of organically produced ingredients. Californian state, also considers that any product that follows the NOP regulations with proofs can also be sold as organic.
More recently, in February 2018, California introduced the Cruelty Free Cosmetics Act, SB 1249 to ban animal testing on cosmetic products.
After January 2020, cosmetic manufacturers will not be able to sell or import any final product or any component of the product that has been tested on animals. California was already in the year 2000 the first state to encourage manufacturers to avoid animal testing, since then it is illegal to use animal testing when an appropriate alternative method is available. In 2013, it was the turn of the European Union to prohibit importation and selling of cosmetic products that had been tested on animals.
Canadian regulations are slightly different from those of the U.S.A. but not as strict as the ones implemented in the European Union. For example, we count more than 1700 ingredients prohibited or restricted in the EU whereas there are only 573 ingredients listed in the Canadian’s Cosmetic Ingredient Hotlist.
As defined by The Food and Drugs Act, a cosmetic product is a “substance or mixture of substances manufactured, sold or represented for use in cleansing, improving or altering the complexion, skin, hair or teeth, and includes deodorants and perfumes”. All cosmetics products sold in Canada must be manufactured, prepared, preserved, packed and stored under sanitary conditions. Manufacturers should submit evidence to establish the safety of the product only upon request from the minister.
› The cosmetic regulations under the Food and Drugs Act includes global regulations around cosmetic products in Canada such as importation specificities, sales, labeling, product and packaging safety
› The Consumer Packaging and Labelling Act details how a product should be advertised including labeling, packaging and product ads
› The Canadian Environmental Protection Act (CEPA) is related to any chemicals found in the cosmetic product and its respect of the environment following the Project Green engagement
› New Substances Notification (NSN) concerns all chemical or polymers that are not registered on the Domestic Substances List They should be submitted as a new substance on the NSN and provided to the Minister of the Environment to protect consumers’ safety
› Globally harmonized system of classification and labeling of chemicals (GHS) is aligned with the Workplace Hazardous Materials Information System ( to define and classify hazards with an international format implemented by the United Nations
Each country has its own labeling regulations and Canada is no exception In fact, we can find few specificities to the Canadian cosmetic product labeling.
Product labeling should be compliant with the Consumer Packaging and Labeling Act and the Cosmetic Regulations under the Food and Drugs Act.
Except for INCI ingredient names, all labels must be written in English and French and clearly readable and legible during the entire product life:
› Name an address of the manufacturer must be Canadian
› Identity of the cosmetic generic name and function
› List of ingredients only by its INCI name – it must be listed in descending order of predominance
› Product formulation
› Product net quantity in metric units of measure in English and French
› Avoidable hazards and cautions
As defined per section 30 and 31 of the Cosmetic Regulations under the Food and Drugs Act, each new cosmetic product sold in Canada must be notified, within 10 days to Health Canada by submitting a Cosmetic Notification Form (CNF).
It not only concerns new products but also any changes affecting the CNF such as: modification of the formulation, change of the product name, discontinuation of sale or new company name, address or contact information, etc.
In each of these cases, the manufacturer or importer should amend and resubmit the CNF to Health Canada.
Filling the CNF does not guarantee that your product is safe to use and sell in Canada it must comply with the requirements of the Food and Drug Act and its Cosmetic Regulations.
The CNF, is an online form including 9 different sections requesting the following information:
1. Name/address of the manufacturer
2. Name of the product
3. Product function and area of application e.g. body, eyes, face, etc.
4. List of ingredients with exact concentration
5. The form of the cosmetic e.g. is that a cream or a gel?
6. Name and address in Canada of the manufacturer, importer or distributor
7. Name and address of the formulator if different from the manufacturer
The European Union has one of the most severe regulations for cosmetic products in the world. In 2009, the Regulation (EC) No 1223/2009 also known as the Cosmetic Product Regulation was voted to be put into effect in 2013.
As defined by the Cosmetic Product Regulation, it applies to “any substance or mixture intended to be placed in contact with the external parts of the human body (epidermis, hair system, nails, lips and external genital organs) or with the teeth and the mucous membranes of the oral cavity with a view exclusively or mainly to cleaning them, perfuming them, changing their appearance, protecting them, keeping them in good condition or correcting body odors”.
A Responsible Person should be assigned to each cosmetic product and will be the main point of contact with authorities if more information around the product is needed. He or she will also be in charge of the product compliance and safety (e.g. keep the Product Information File updated). The assigned person will also be responsible to track cosmetovigilance and customers claims.
The person assigned could be the manufacturer, the importer, the distributor or any third person assigned by the manufacturer or the importer well known in the market such as a consulting agency.
The EU has put together a list of prohibited, restricted and allowed ingredients that manufacturers must check on a regular basis to make sure each substance used is compliant and safe.
The list contains different categories that defines the status of the substance and its level of danger for the consumer. All these substances can be found in Annex II of the Regulation 1223/2009.
In addition to ingredient screening, the manufacturer should be able to prove that the product is safe to be used by consumers.
Each product must have a Product Information File (PIF) associated with it and each chemical should have a Safety Data Sheet (SDS).
Before being placed on the European market, each cosmetic product must be submitted to the Cosmetic Products Notification Portal (CPNP).
The CPNP was created as a reinforcement to the Cosmetic Product Regulation to collect information about the product that is being placed on the market. It helps the European commission to monitor, analyze the market and inform consumers.
It is an online and open-to-public platform where the RP or distributor fill in information about their product.
Before being placed on the European market, each cosmetic product must be submitted to the Cosmetic Products Notification Portal (CPNP).
The CPNP was created as a reinforcement to the Cosmetic Product Regulation to collect information about the product that is being placed on the market. It helps the European commission to monitor, analyze the market and inform consumers.
It is an online and open-to-public platform where the RP or distributor fill in information about their product.
Example of information requested:
› Product name(s) and category
› Name and address of the RP or distributor
› Country of origin if product has been imported
› Country of commercialization
› Contact details of the person to be contacted if necessary
› Notify presence of nanomaterials and CMR substances
› Product formulation
› Name and address of the person responsible of the PIF only if the distributor is doing the registration
All cosmetic product labeling must comply with the Regulation (EC) No 1223/2009.
All information contained in product labeling must be indelible, easily legible and written with visible lettering. Language chosen should be the country’s official language(s) where the product is placed.
› Name and address of the responsible person
› The country of origin if the product is imported from countries outside of the EU
› Nominal content of the product given by weight or volume
› Date of minimum durability or period after opening
› Precautions for use
› Function of the cosmetic product
› List of ingredients
› Identification number
Enforced by the European Cosmetics Regulation 1223/2009 article 11, the Product Information File concerns all cosmetic products sold within the European Union. Industry professionals have to create and store the dossier for each product placed on the market and intended for consumption.
The RP placing the cosmetic product on the market has to submit to competent authorities – ANSM, the Directorate General of Health or DGCCRF, the PIF, as well as the risk assessment of the product and keep these documents updated for at least 10 years.
In order to compile the PIF, product information has to be gathered from several stakeholder: suppliers, laboratories, safety assessor, and internal product information system.
Product information: The exact name and all names in the national language where the product will be placed, identification code and a description of the product function.
Cosmetic Product Safety Report (CPSR): Is the scientific review of cosmetic product safety and is divided into two parts:
› Part A: Cosmetic Product Safety Information
» Quantitive and qualitive composition of the product exact percentage
» Physical and chemical characteristics as well as stability of the product
» Microbiological quality
» Impurities, traces, and information about the packaging
» Normal and reasonably foreseeable use
» Product’s exposure
» Substances’ exposure
» Toxicological profile of the substances
» Undesirable and serious effects
» Information on the product
› Part B: Cosmetic Product Safety Assessment, must be done by a qualified person and is the proof that the product is safe to be use It includes:
» Statement on the safety of the cosmetic product
» Statement on the need to label any particular warnings and instructions of use
» Statement on the need to label any particular warnings and instructions of use
» Explanation of the scientific reasoning of the substances contained in the product and on the Safety Information documentation
» Justification of the consideration and non consideration of the raw materials’ toxicological profiles
» Assessor’s credentials and approval name, address, proof of qualification, date and signature
Good Manufacturing Practice (GMP): Each PIF should include a declaration of compliance with the GMP a set of requirements based on workers safety and health during the production process. The cosmetic product’s manufacturing method has to be aligned with those specific requirements to be compliant and sold within the EU.
Evidence of the claimed effect of the cosmetic product: In order to be compliant with regulations, the company has to furnish proofs of effects claimed. Several methods can be used: Experimental studies, investigator evaluation, consumer perception tests and past scientific publications. All of which have to be reliable and reproducible.
In addition to country and regional regulations, several guidelines are in place in order to harmonize the global regulatory landscape. The most used and well known ones are the Good Manufacturing Practices (GMP) and the Global Harmonized System (GHS).
Originally created for pharmaceutical products, the GMP is now used for most manufactured products cosmetic, food, dietary supplements, etc It gives manufacturers standards to ensure product safety and quality for their intended use.
Cosmetic guidelines are based on the original GMP and from ISO 22716/2007 agreed to be followed by the USA, Canada, Japan and European Union in 2009.
The GMP includes different guidelines during the whole production process such as:
» Maintain a clean and hygienic manufacturing area
» Control environmental conditions to prevent raw materials adulterations and allergens
» Train workers on the procedures in place
» Create and update documents about manufacturing processes, ingredients, tests, etc
» Processes must be checked to ensure procedures are respected
» Track and analyze complaints from consumers
» Put in place a product recall system
» Tests of raw material and finished product samples must be executed by external laboratories
» Evaluate all processes on a regular basis using internal audit
» Ensure product and packaging uniformity, integrity, adequacy of mixing and accurate fill of mixing containers
The Globally Harmonized System of Classification and Labeling of Chemicals (GHS) is an international system created by the United Nation in order to standardized classification and labeling of chemical substances and mixtures.
The GHS by the United Nations includes several regulations such as, product testing following specific criteria, universal warning pictograms and safety data sheet for each hazardous chemical.
GHS is now followed by many countries all over the world such as Canada, the U.S.A., the EU, etc. Most of which use it as a reference but mix it with their own local regulations.
In the USA, they use the Harmonized Communication Standard (HCS) that is monitored by the Occupational Safety and Health Administration (OSHA) since 2012.
In the EU, it’s under the CLP Regulation (EC) No 1272/2008 and it was first implemented in 2009.
Canada launched it in 2015 under the Hazardous Products Regulations (HPR).
Three countries and regions and three different regulations in place but all of them are based and include most of the GHS standards.
U.S.A. Canada EU
Safety Data Sheets (SDS) also known as Material Safety Data Sheets (MSDS), contains information on potential health hazards associated with exposure to chemicals or other substances that are potentially hazardous.
The Safety Data Sheet:
› Specifies the composition of a chemical (substance or mixture),
› Identifies hazards
› Recommends preventive measures (collective and individual) and first aid
In other words, it is a crucial piece of documentation for the health and well being of consumers. It is mandatory in many countries such as the European Union, USA and Canada.
SDSs include several documents about the hazard of a product and advise users on its safety precautions.
Most of the time, they are written by manufacturers or products’ supplier and have to be made accessible to every person in contact with the hazardous chemical.
The Global Harmonized System defines basic requirements of the SDS with local regulation adjustments.
U.S.A.
Canada EU
Supervised by OSHA WHMIS REACH regulation
Enforced since 2012 2015 2008
Language English English and French Of the destinations country
Section
Section
Section
Section
Section
Section
Section
Section
Section
Section
Section
Section
Section
Section
Section
Section
Accurate information is key for the regulatory affairs department during the product development process. Collecting the right information, at the right place and at the right time is usually a struggle for teams.
Managing a large amount of data can be very complex without a defined process. Especially when documents have to be gathered from different sources suppliers and internal departments.
The brand, retailer or manufacturer depending on who’s selling the product to consumers, have the responsibility to provide every documents and dossiers to the assigned authority. Collecting all the data is just one part of the process as it usually needs to be reworked to match regulations requirements.
When it comes to product design and strategy, cosmetic businesses have several options available such as:
› Buy and resell finished products only retailers’ case: Finished products are bought from different manufacturers and brands to be sold in stores directly to consumers
› Use contract manufacturers: Brands send their product specifications and claims to the manufacturer to create the finished product under a private label
› Produce the finished product in house but using different suppliers for raw materials, container and packaging
Retailers need to make sure they collect the right information from brands, as they will be responsible of the compliance of the product they sell. Collected information could represent hundreds of documents for a single product.
When using different suppliers, manufacturers have to deal with many stakeholders, and it can easily become time consuming to collect all the documents. Human error can easily be made leading to losing, or false information.
› Collect from each supplier all the data and documents about each raw material and substance used including information about the container and packaging
› Secure information and documents collected and check its accuracy collected to make sure its complete and match regulation requirements
› Process the collected information in order to complete required dossiers and forms, data has to be transformed to fit requirements from each country
Creating a unique source of information will enable you to quickly access and find the right information at the right time. Once the product information is gathered and consolidated, it is easy, when needed, to retrieve, re-use and share this information.
Product information includes data (ingredients and allergens lists, requirements, claims), and documents (certification, specifications, SDSs, quality reports, etc.)
Sharing Excel files and Word documents are no longer sufficient and can lead to data loss. Cosmetic businesses have to use a proper software to help them and optimize their product information management.
Product development and launch processes generate various data and documents. Managing all this information can quickly become overwhelming. In addition, the change or substitution of one element, such as a raw material containing a new allergen, requires additional attention because a minor change can affect several finished products.
Understanding the relationship between each component, have all specifications readily available anytime, and to avoid duplication of information is essential.
It is necessary to gather and structure all the data and documents in a consistent way. The repository should be adapted and include organized product datasheets.
Being regulatory compliant requires creating and generating various documents such as product labeling, the PIF, CNF, etc. which may have to follow specific frameworks defined by the regulations.
To effectively manage and be able to generate these documents, it is important to have data dematerialized in a single place, create templates defining which information is needed, and automatically fill in those templates with the required information.
For example labeling or Quali Quanti formula has to respect clearly defined regulations (cf. labeling per country pages) and not following them could lead to recalls and fines With a software like a Product Lifecycle Management (PLM), document creation is automated, framed and conforms to the regulations.
When developing a new product, cosmetic businesses deal with many different service providers raw material suppliers, testing laboratories, packaging suppliers, creative agencies, regulatory agencies, etc. Having many different stakeholders in the product development process makes it very difficult to collect and share information in an efficient way.
In addition, every department is working with several suppliers. Optimizing collaboration between every single supplier is key in order to save time, money and energy. When teams are confident with data and documents they are using it allows them more time to work on value added task.
The first step is to gather all data and documents received from external stakeholders – e.g. substance components, regulatory documents, product testing results, etc. In order to optimize it, you should set up a specific process and template to be used by suppliers. By defining templates for raw materials and finished product datasheets – information can come from several suppliers, they all follow the same order and format. Processing documents and data will be easier, quicker and more efficient.
Centralizing information is key in order to maintain information that is up to date, accurate and easily accessible when needed. Using the same platform for finished products and all the raw materials used to compose it will help save tremendous time.
The best way to give suppliers more responsibility is to implement a dedicated portal for them.
An interface dedicated for exchange between business departments and suppliers is necessary. Through the portal, they will be able to fill in and upload requested documents while they are tracked and stored.
The platform should include pre-defined templates in order to avoid back and forth and send automated alerts if a folder is incomplete.
Product compliance must be ensured from the very start of the New Product Development process. The formulation stage is one of the most complicated one, because requirements from the marketing team need to match compliance of the country of commercialization.
Indeed, in addition to product requirements and claims, marketing also defines the country of commercialization. Which is very important to create a compliant formula.
As presented before, countries have different restrictions when it comes to raw materials use. Some of them are completely banned different lists in the US, Canada and the EU, and others are banned when exceeding defined thresholds.
Managing both marketing requirements and compliance for each country of commercialization can be very complex for the R&D teams. But to do it manually can be time consuming and risky, as regulations are evolving quickly and are tough to understand when you are not an expert.
Having the support of a PLM solution can be the key to ensure formula compliance, match marketing requirements and save time.
As soon as formulators have created prototypes, they can be checked automatically to match regulations enforced in the country of commercialization Results are immediate, the product is either compliant or not. If not, reasons are given so that it can be easily changed.
An adapted software should both use regulatory experts’ knowledge to update the INCI library, restrictions, etc and automated calculations features.
Quali/Quanti formula can be calculated directly through the software. If a substance exceeds the maximum threshold, it will be automatically highlighted. In addition, lists of allergens, traces and impurities, INCI ingredients are generated directly through the solution.
Creating a compliant formula is the first step to the finished product compliance. When checked at an early stage, the rest of the development process can proceed safely reducing risks of formula changes.
Businesses must ensure the compliance of their products during their entire lifecycle. Every department of a company R&D, quality, compliance, marketing, procurement and so on, is impacted by regulations therefore, information continuity and collaboration is crucial.
Objectives and challenges can be different from one department to another. For example, marketing is focused on the consumer and its needs while making sure to have a shorter time to market. On the other hand, procurement teams have to find the right raw material from the right supplier at the right cost R&D must follow requirements provided by marketing teams and ensure formula compliance per country of commercialization. Even if challenges are different, both R&D and marketing have to work together as both of them need information from the other.
And this is exactly the same with each department of the company. Each product development stage is closely related and each change affects the whole team In addition, each department might be using multiple sources of information such as software or Excel files making information continuity more difficult. To facilitate a product’s compliance, creating a strong collaboration through information continuity is crucial, to:
› Quickly track the product development and validation
› Avoid human errors by automating calculation and document generation
› Limit delays by setting up workflows and notifications
Sharing a single source of information will enforce collaboration through processes and workflows, and structure similar product information in a consistent way.
Only a few companies are using IT tools, such as a PLM, tailored to each of their business unit problems. But, in order to be effective, information systems have to be designed for each business unit and allow access to product information anytime by authorized users. The PLM allows businesses to have an adapted information system that centralizes and manages data to optimize product development and ensure its compliance.
Existing solutions, mostly manual, non shared, over specialized or generic, are often inadequate to provide timely and useful information.
Businesses need a flexible and transversal tool for the development of new products that is able to meet the specific requirements of each service.
When commercializing a product many rules have to be respected to be compliant with the country and even the state where your product is sold.
It is about getting all the information you can around regulations that apply to your product and business.
As we have seen earlier, each country, state and even each product category has their own particularities. Having a deep knowledge of the ones that applies to your case is essential.
Businesses have several possibilities to ensure product compliance such as the following.
Some businesses may only use their regulatory affairs department as they have the required knowledge and skills. This is something rarer as regulatory compliance is getting more and more complicated. Plus, it is evolving very fast and needs to be monitored on a regular basis. And, the more product references you have the more complicated it can get.
One of the most common options, because it gives businesses the expertise and lowers the risk of mistakes, is to get an external contractor. Contractors offer several services from advisory on formulation conformity to lab testing including detailed support to commercialize cosmetic products and they can submit any required dossier for you.
In addition to an external contractor and regulatory affairs department, implementing a PLM solution allows businesses to use the power of a software to centralize data, orchestrate processes, and automate calculation and document creation.
Combining a software, such as a PLM, with external services offers you the best coverage to develop products and ensure their compliance. It will help you organize, collaborate, collect and check product information while external services will track and check regulations. They will ensure compliance and update information, which will automatically be integrated within your software.
Regulatory compliance can be very complex when it comes to personal care and cosmetic products. With recent studies highlighting the hazardousness of a large range of chemicals consumers request more transparency and governments are strengthening their regulations. Globalization also highlights the need to have a complete understanding of the local rules and it is becoming more difficult to follow regulation updates while maintaining the right collection turnover.
It is, therefore, essential to set up and follow regulatory frameworks and ensure an efficient product development process with a faster time to market It requires structured information, data continuity from suppliers to consumers, and an efficient collaboration facilitated by optimal processes. This framework will not only facilitate each stage of the product development, but also support the entire product life cycle, from marketing brief to product end of life.
In addition, starting the compliance review process from product design and using experts’ knowledge are success keys to be regulatory compliant It mean businesses must combine the expertise from a regulatory ecosystem with a business software tailored to each department.
Aptean is one of the world’s leading providers of industry-specific software. Our enterprise resource planning and supply chain solutions are uniquely designed to meet the needs of specialized manufacturers and distributors, while our compliance solutions serve specific markets such as finance and life sciences. With both cloud and on-premise deployment options, Aptean’s products, services and unmatched expertise help businesses of all sizes, across many industries, to scale and succeed.
For more information, visit www.aptean.com.