The Factory of the Future
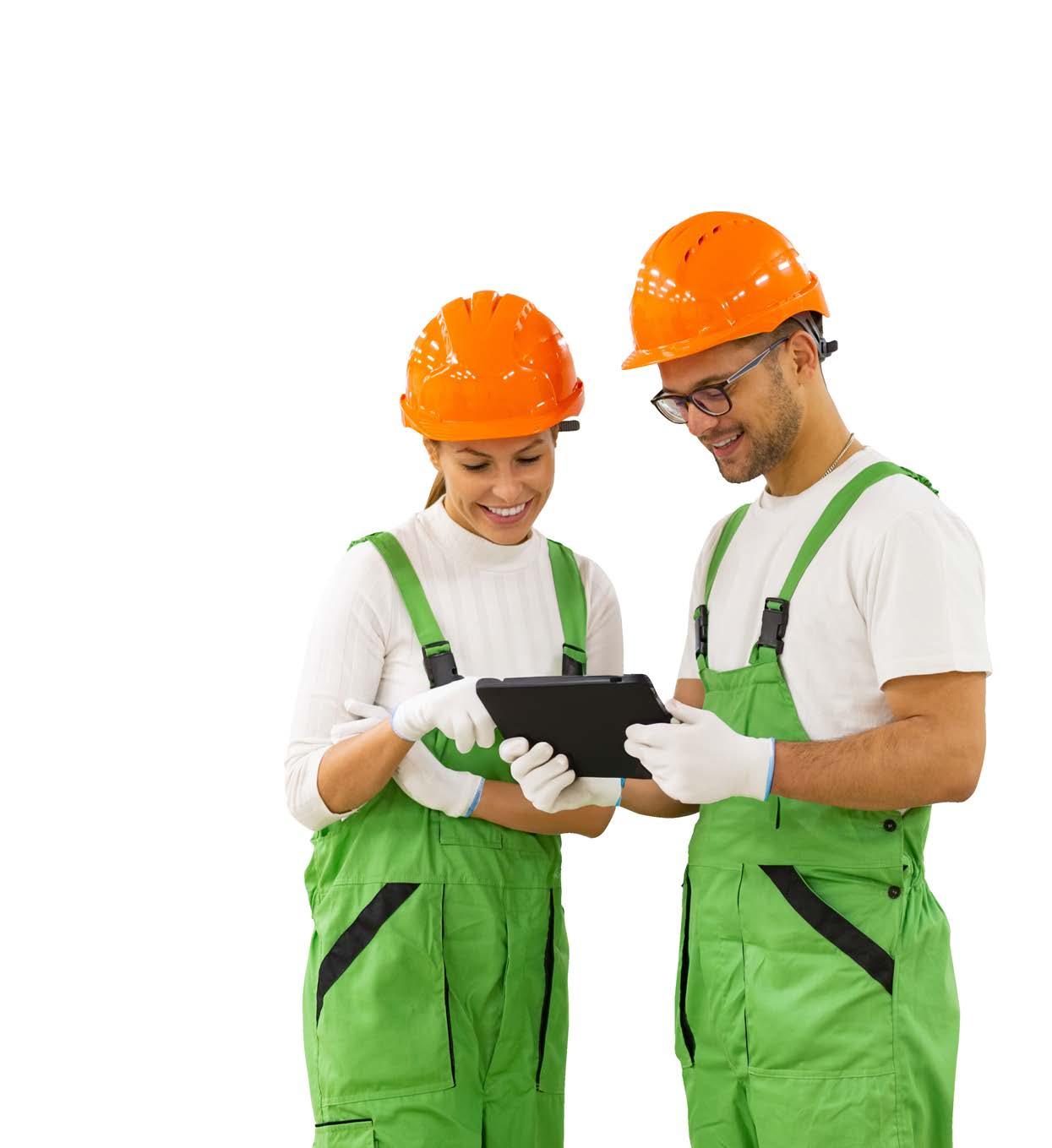
Main Ingredient ‘DATA’: What Connectivity Means for Food Production
In the food industry, no two recipes are alike. And yet, all successful and modern food production facilities will have one main ingredient in common that can make them successful: data.
Industrialisation and new technological possibilities have led to an enormous increase in processing possibilities and productivity – something that not only applies to the food industry. The highly dynamic market under which the industry must operate makes agility a decisive factor for success.
The objective is a fully connected production line with a focus on workers and consumers as people. The necessity for digital transformation has already arrived in the food industry, as a large proportion of food manufacturers are already implementing a digital strategy. However, food production facilities seem to be far from bringing the smart factory to life. A study among international food companies showed that only 35% of companies have integrated digital transformation into everyday production operations following the pilot project (CSB Digitization study 2020).
It seems that the need for digitalisation is not compatible with the current realities of production for most food production facilities. This presents the industry with major challenges that cannot be overcome without software solutions. Increasing Overall Equipment Effectiveness (OEE) is undoubtedly one of the most important challenges for production managers in the food industry. This is achieved through greater effectiveness and efficiency in production. And those who can raise their production to the level of maximum efficiency – which is only possible with the use of intelligent technological solutions – will become trailblazers.
The key factors for Industry 4.0 are the reduction of rejects and the increase of process stability, in particular by reducing downtimes. At the same time, consumers’ increased expectations of products in terms of availability and specificity must be met. Ever shorter delivery times, high product variety, small batch sizes combined with short best-before dates place great demands on production planning. High-capacity utilisation through optimised production sequences and low inventories are only possible with intelligent software support.
Additional pressure arises from changing and locally varying legal regulations, with particularly critical requirements concerning product safety, quality, and traceability.
In summary, food producers must simultaneously meet a multitude of requirements and ensure that the extensive product and production-related information is documented – all while production processes are becoming increasingly complex. Production managers may rightly ask themselves: where do we start with digitalisation and how can we drive digital transformation on top of day-to-day business? And the answer is with a modular solution that is easy to implement and intuitive to use.
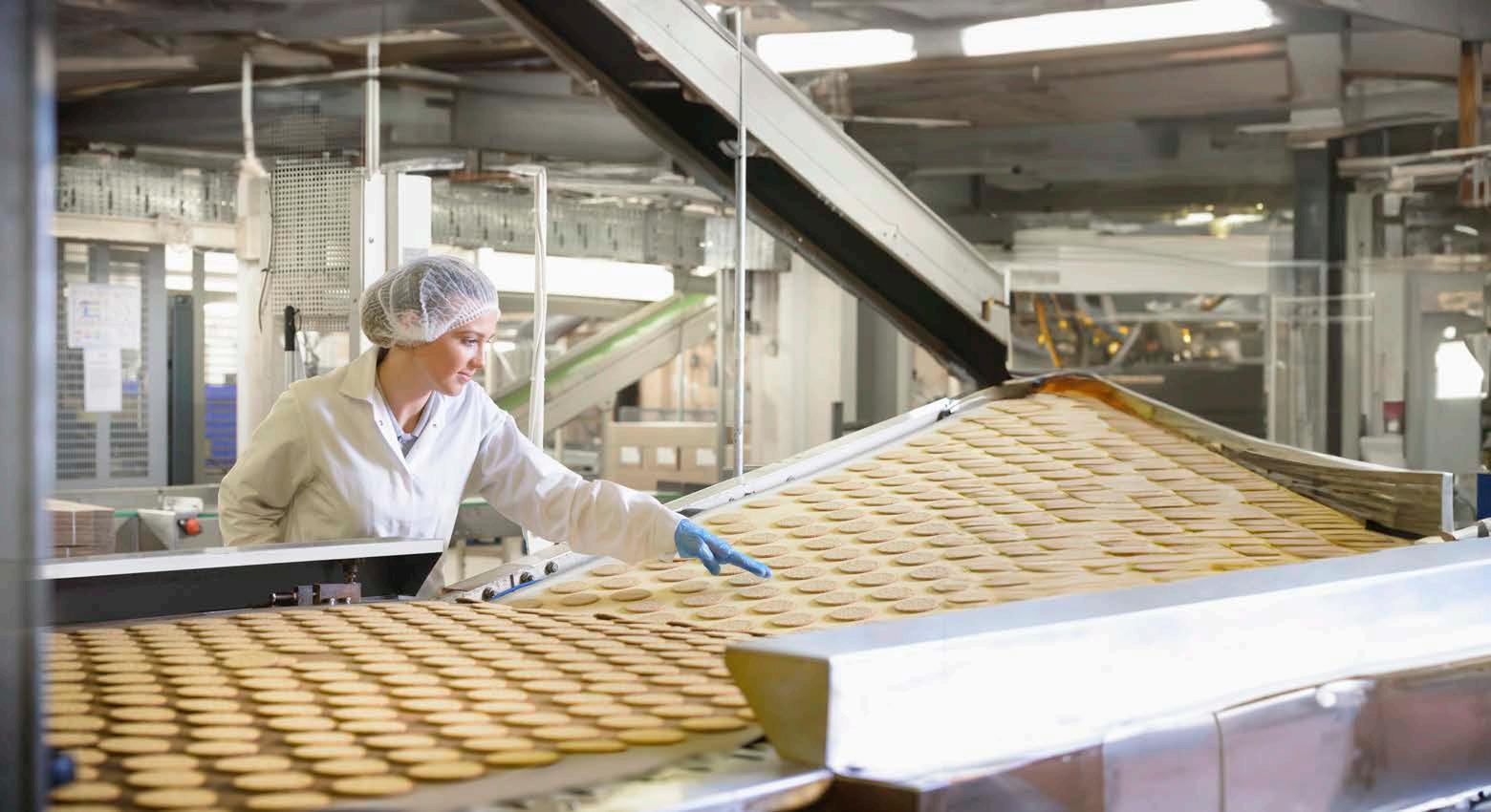
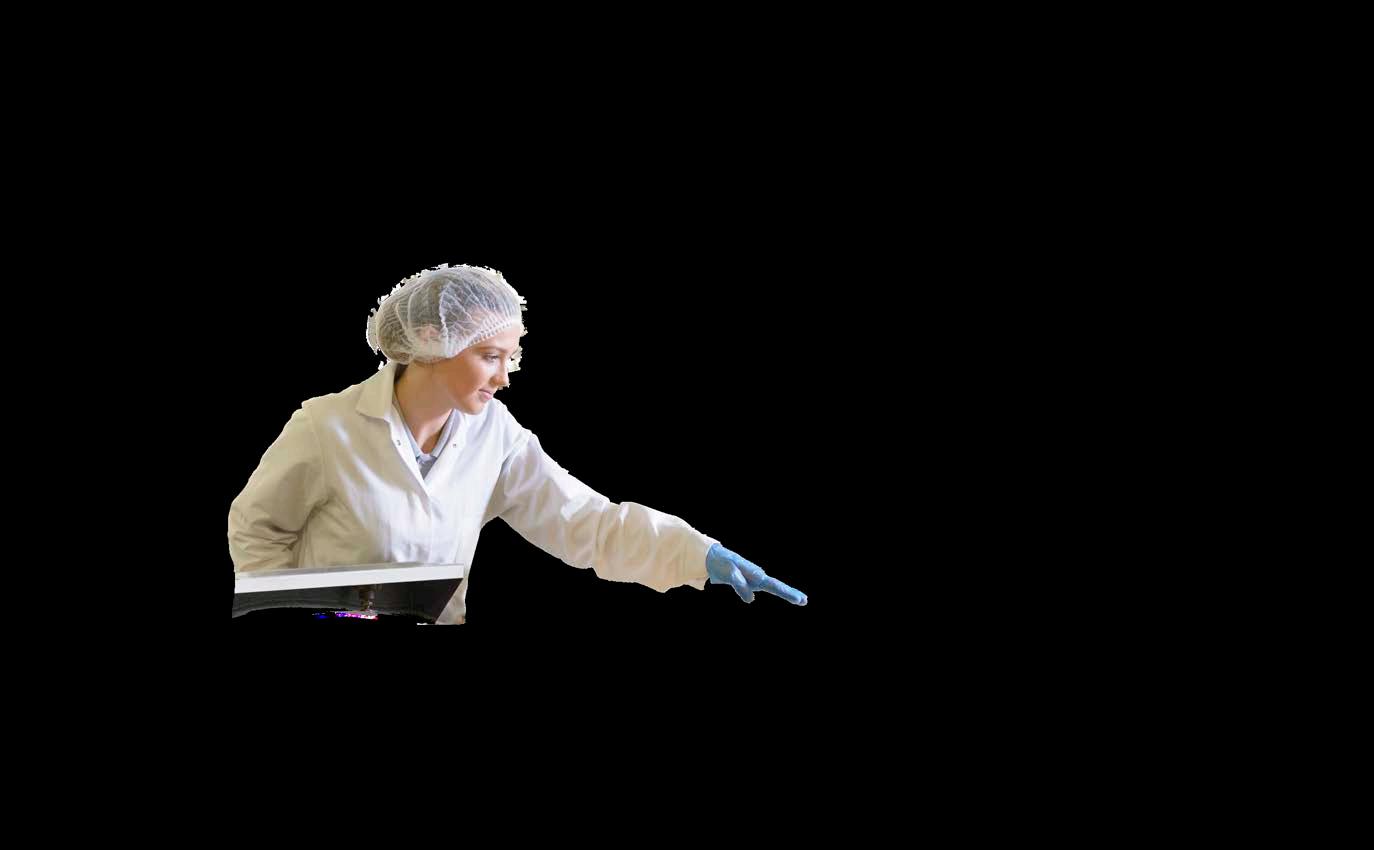
7 Steps to the Maximum Efficient Smart Factory
and integrate business processes
Simulation and visualisation: develop possible scenarios for decision making
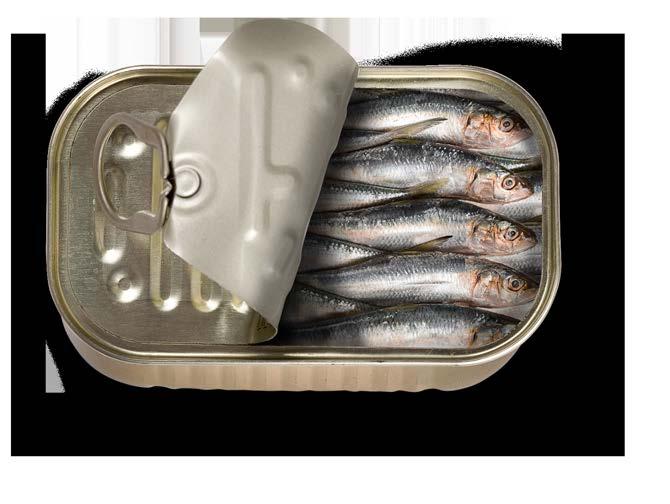
The core idea of Industry 4.0 is the systematic use of data to arrive at better decisions more quickly. This data-driven learning is enabled by integrated information streams throughout the company and the entire global value network. The integration spans all technical and business processes horizontally and extends vertically from the operational to the management level. This reduces data silos, makes dark data visible and enables extensive data exchange.


Integrating Manufacturing Execution (MES) and Warehouse Management Systems (WMS)
Our integrable Aptean MES/WMS Objective Edition solution enables you to supply high-quality food products. The software solutions can be used independently of each other, but they generate the greatest added value when used in combination: The two systems communicate in an integrated manner without any additional administrative effort. This allows you to keep an overview of your warehouse and your production hall and coordinate both equally. This makes loss of information and the inefficiencies that come with it a thing of the past!
The MES solution provides you with intelligent recipe management and reduces waste by using the FEFO principle (First Expiry, First Out), which results in significant savings on ingredient costs.
Our software solution offers you industry-specific functionalities, such as track-and-trace at batch level, the ability to manage your tanks and the prevention of allergen contamination.
With our Warehouse Management Solution, you can track all processes and movements from the receipt of raw materials to the dispatch of finished goods. You maintain a full overview of your stock levels at all times and can deliver to the production line at exactly the right moment.
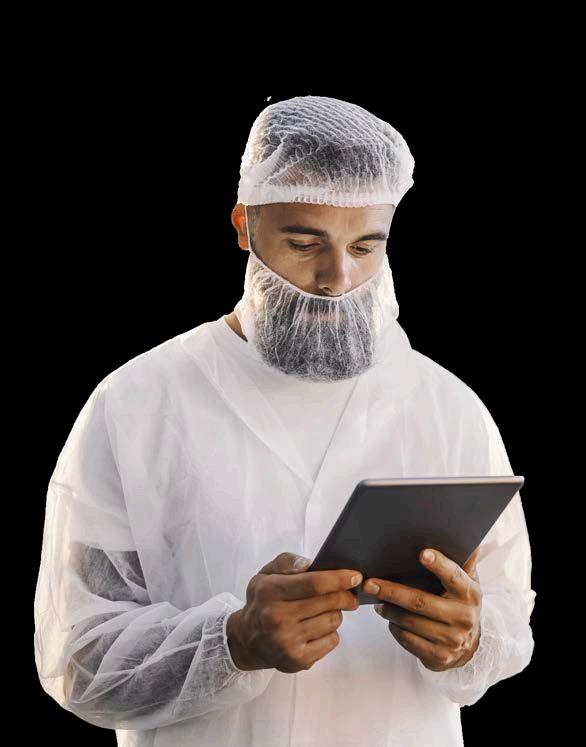
Do you have specific questions about how to optimise your production processes and make your version of the Smart Factory a reality at the same time?
Contact Us
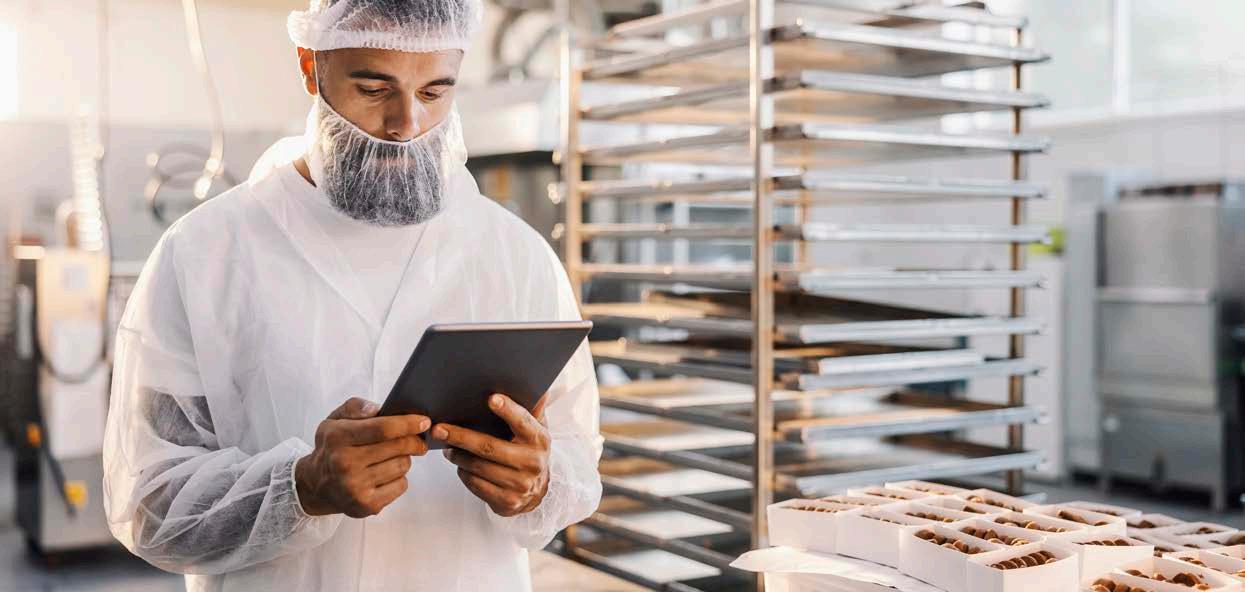
About Aptean
Aptean is one of the world’s leading providers of purpose-built, industry-specific software that helps manufacturers and distributors effectively run and grow their businesses. With both cloud and on-premise deployment options, Aptean’s products, services and unmatched expertise help businesses of all sizes to be Ready for What’s Next, Now®. Aptean is headquartered in Alpharetta, Georgia and has offices in North America, Europe and Asia-Pacific.
To learn more about Aptean and the markets we serve, visit www.aptean.com.
Copyright © Aptean 2024. All rights reserved.