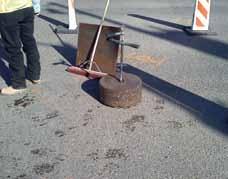
6 minute read
Keyholing and core farming: the perfect match
Murv Morehead, Right-of-Way Coordinator, City of Overland Park, Kansas; Al Field, Owner, Al Field and Associates LLC, Phoenix, Arizona; members, APWA Utility and Public Right-of-Way Committee
tility repairs, which take place far too often in our public streets, are a fact of life. We can, however, minimize the detrimental effect they have on pavement. This can be accomplished by using the Keyhole, Coring and Reinstatement (KCR) process. KCR consists of core drilling through asphaltic or concrete pavement (core diameters of 6 inches to 24 inches are normally used); removing the pavement core/coupon and then using vacuum excavation to remove subgrade material until the utility in question is found. Following utility repair or other activity, the subgrade is replaced, usually with a ½-sack slurry, and the previously removed core/coupon is replaced into the core hole and secured with a bonding agent (the reinstatement step). While the KCR process has already yielded numerous benefits for various utilities and service providers, it provides other benefits to the municipality in which the process is used as well. The two most notable and noticed advantages, from the perspective of a municipal ROW Inspector/Coordinator, are:
Advertisement
Removed core Top hat street plate

• Reduction in impacts to the motoring public
• Reduction in excavation impacts
Prior to the advent of KCR, a typical excavation performed to locate and/ or repair a buried utility meant a minimum of three days of impact to traffic due to time required for setting up traffic control to saw-cut or jackhammer out the existing pavement, which is removed and hauled to a disposal or reclamation site; the activity within the exposed area takes place; backfill is placed; cold-mix is installed or a street plate is placed over the excavation; and traffic returns to normal, with a temporary pavement patch to drive over for who knows how long. When the cold-mix temporary patch is replaced is anybody’s guess unless specified in the permit, but usually not until the number of permanent patches justifies ordering of a truckload of hot-mix, rental of a compactor and roller, another mobilization of traffic control and final restriping. The impacts manifest themselves in the form of cold-mix/ temporary pavement degradation, or lane closures during the day and the noise generated by vehicles driving over a street plate through the night. While KCR still requires a traveled lane closure, it rarely lasts more than one day with no further closures needed. If core holes need to be left open for an extended period of time (i.e., used to observe directional drill
installation and verify no damage occurred to existing located facility), they can easily be covered with a small (18” x 18”) plate that has a pilot tube welded on the bottom that drops into the core hole to prevent it from sliding or otherwise moving. These small “top-hats” can easily be placed or removed by one person— no machine needed. Traffic can then be restored following curing of the bonding agent which achieves full strength in less than an hour. The original paving material and even the striping are replaced as they were.
Benefit #2 – a reduction in excavation impacts
Through the KCR process, benefit #2 mentioned above is realized. The major excavation impact reduction is in the form of a much smaller opening in the street. Most of the cores drilled are diameters of six inches to 18 inches which, when compared to a typical traditional saw-cut/jackhammer excavation that would be two-feet by two-feet or larger, have already reduced the pavement area affected by as much as 90 percent. Additionally, the “loss of confining stresses” (loss of lateral support that allows trench walls to sag into new opening) that is typically encountered with any open trench cut is significantly reduced or eliminated. And the circular nature of the pavement cut reduces stress points to zero. Problems encountered with traditional excavation and repair methods including cracking of surrounding pavement due to the percussive effects of jackhammers and open saw-cuts at corners of the excavation are eliminated as well.
As an example, in Overland Park’s Standard Street Repair Detail, the “traditional” excavation must be over-cut by 12 inches through pavement depth on all four sides. High-early strength concrete is placed and topped with a two-inch asphalt overlay. Each of these joints between new and old pavement are vulnerable to water infiltration. Over time, the asphalt overlay likely will deteriorate, becoming a maintenance issue. This is important since the City’s ROW Management Ordinance requires the utility/contractor to be responsible for their repair work for two years

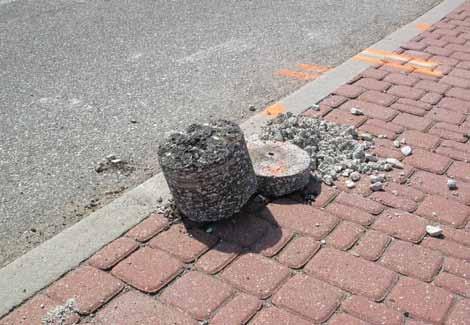
following the completion of repairs. Beyond two years the repair becomes the responsibility of the street maintenance department, meaning taxpayer dollars are being used. All of these problems are eliminated with KCR. The properly completed core reinstatement is virtually invisible, impervious to water infiltration and will be maintenance free. The replaced core exactly matches the composition of the original road and also reinstates the road to its original weight-bearing capacity. Pavement markings are replaced as they were.
Finally, the core reinstatement represents the permanent repair. Winter in the Midwest can pose significant problems when trying to complete street repairs. Snow, ice and subfreezing temperatures for extended periods may prevent any permanent placement of asphalt (depending on mix design specifications, asphalt will require an air temperature of 50 degrees Fahrenheit or higher to allow placement) and may also be severe enough that concrete can’t be placed without danger of freezing. These conditions can easily push a typical street repair into the following spring, leaving the city to deal with a street plate and the problems it creates for snow removal operations throughout the winter. Core bonding agents meanwhile can safely be used down to 32 degrees Fahrenheit and, as mentioned previously, should achieve adequate strength in less than one hour.
It is a given that all buried utility infrastructure will at some time need repairs, and these repairs can range across a wide spectrum of involvement from a simple leak clamp or valve repair to major line replacement. The vast majority of repair activities fall into the “point repair” category and the KCR method is perfectly suited for this type of repair work. While this method is ideal for point repairs, it is rapidly being accepted as the preferred method of exposing buried utilities under pavement.
It is possible that a core/coupon may be found, upon removal, to be unusable. The most common cause of this condition is a delamination of the asphalt layers, likely due to aging asphalt. Another problem that can arise during the KCR process is that the removed cores may be damaged, discarded or lost. Whatever the case, the contractor is left with a hole in a street and no core with which to repair it.
Enter core/coupon farming. Core/ coupon farming is a very simple but effective concept and is, as the name implies, “farming” or growing cores/coupons. An asphalt “field” (i.e., small area of asphalt placed in an unused portion of the keyhole contractor’s utility/storage yard) is needed. As replacement cores are required, the contractor simply takes the core machine to the yard and “harvests” a core/coupon of the required diameter and thickness which is taken to the job site and reinstated into the core hole. When the field has yielded all the cores it can, the remaining asphalt is then recycled and the farming starts over again.
Additionally, when a core is taken from a location where it will not be needed for replacement, it may be taken to the farm and saved for future use.
The combination of KCR and core farming offers a complete method of under-pavement excavation and street restoration that will leave the pavement in a far better condition than traditional excavation methods could have ever achieved.

Core farm
Murv Morehead can be reached at (913) 895-6189 or murvyn.morehead@ opkansas.org; Al Field can be reached at (602) 616-3618 or AlField@AlFieldAssoc.com.