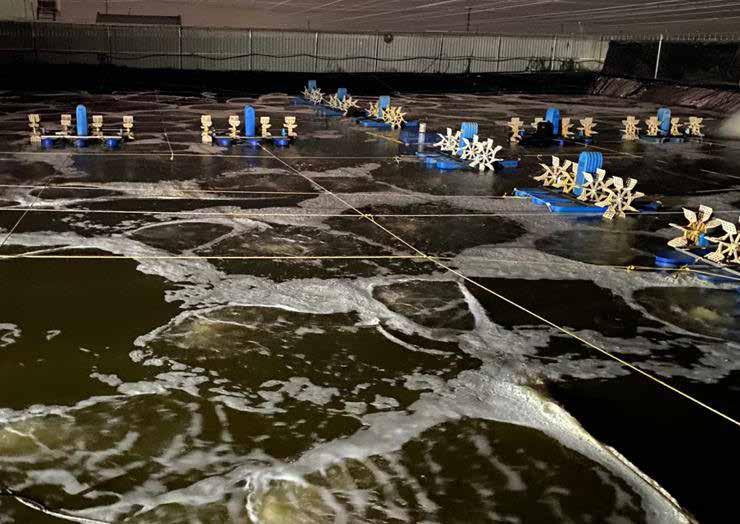
5 minute read
Changing the farming model
The Gokuldham farm in Gujarat did an infrastructure revamp, involving a four- step water treatment process, frequent sludge removal and a 2-phase nursery system
Nursery ponds and 1.35g juveniles after phase 1 nursery.
Second generation farmer, Hetal Shantila Patel, had specifically equipped himself with a MSC in Aquatic Biology to enhance his skills in aquaculture management and to take over the family’s company, Mindhola Foods, LLP which focuses on shrimp farming, trading and an export business. He has been farming for 26 years. However, in 2020, he faced issues with diseases caused by the microsporidian Enterocytozoon hepatopenaei (EHP) and white faeces syndrome (WFS); Hetal knew that that he had to change the way of farming vannamei shrimp in his farm.
“We just could not continue in the same way. Creeks were contaminated. We had already added a nursery phase in 2016, but this was just not enough. In 2020 we started a two-phase nursery system at the Gokuldham farm. The idea is to reduce the time in the grow-out phase,” said Hetal, during a presentation at the 2-day webinar conducted by the Society of Aquaculture Professionals on “Overcoming the hardships in shrimp farming -Lessons from India” in January 2021.
The company has two farms, one of them is the 170ha Gokuldham farm, which has a total of 220 ponds and production in 2020 was 390 tonnes from 34ha.
New model to improve productivity
Key to this new culture model is the refinement of several shrimp farming principles. Among these are clean and clear water, small ponds for easy management, aeration with long arm aerators at 10HP/10,000kg, recirculation to reduce disease risks and wastewater management. “Sludge removal is based on 2-3 hours/100kg of feed and we exchange water at a rate of 3-4 tonnes. We want to reduce any risk from the external environment and so we decided to recirculate water through our reservoirs.” “Why did I need to restructure my farm? In the Gokuldham farm, in 2016 and 2017, productivity was good. I could harvest 154-159 tonnes from eight ponds at 20-21 tonnes/ ha. But in 2018 and 2019, the situation became bad. In 2018, I harvested only 133 tonnes (17 tonnes/ha) and then in 2019, with 11 ponds, I could harvest only 109 tonnes (13.7 tonnes/ha). Feed conversion ratio (FCR) increased over these years from 1.39 to 1.71. Average survival rates were lower at 83% in 2019, from 96% in 2017. Stocking density was a constant 73-78 PL/m2,” explained Hetal.
In 2019, Hetal restructured his farm, comprising eight culture ponds and four nursery ponds. The water area ratio was 70:30 (culture ponds: treatment ponds). But it was not enough, and in 2020, he restructured again, reducing to 40% culture area and 60% water area, i.e. sacrificing culture ponds for water treatment ponds. The previously 1ha ponds with 1.8-2.0m depth were divided into 0.2ha and 1.2-1.4m deep ponds for grow-out and nursery culture.
Hetal Shantila Patel started farming in 1994. Faced with issues of diseases, Hetal knew that he had to change the way of farming vannamei shrimp in his farm.
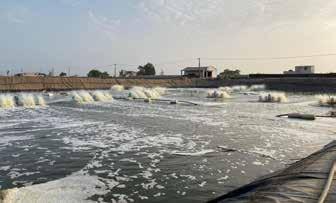
Grow-out pond with aeration devices - blowers and paddlewheels totalling 24HP. Check tray and a harvest.
Cleaning and recirculating water to reduce risks
Hetal detailed the process of water treatment and how he recirculates the water. “We draw water from the Mindhola River, about 1.5km away. Water passes through a series of sedimentation ponds, then to a sequence of treatment, firstly with 3ppm potassium permanganate (PP), then 10ppm poly aluminium chloride (PAC) and finally 30ppm chlorine treatment. Water is then channelled to the ready to use holding ponds before going to nursery and grow-out ponds. We developed a process of slow and fast mixing of PP and PAC in the treatment ponds.
“We use the same source of water for both the nursery and grow-out phase. All ponds have shrimp toilets, and the sludge is pumped to a sludge pond. Used water is channeled back into our treatment system and we start cleaning the water again. We clean these ponds once fortnightly.”
Water quality is critical and after the primary and secondary treatment, water quality improves from the very high 264NTU of creek water to 37.2NTU after the second settlement pond. (NTU= nephlometric turbidity units and is a measure of drinking water quality).
“By the time it is ready to use, we have really clean and clear water at 2.29NTU. As a comparison, drinking water is <1NTU. We started with 70.68 dissolved organic carbon (DOC) in the creek which is really polluted with many mills upstream and end up with DOC 5.58. This is a reduction of 12 times. This is how we have been managing,” said Hetal.
Two phase nursery system
Five lined nursery ponds (900m2) are used for phase 1 stocking at 1,500 PL/m2 for 30 days to reach 1.35g juveniles. In the next nursery stage, these juveniles are stocked at 500/m2 into 0.2ha ponds for 29 days to reach 9.1g. Finally, only 120 PL/m2 are stocked in 23 growout ponds of 0.2ha. In both nursery phases, aeration is supplied by blowers and paddlewheels totalling 34HP. Blowers run over 24 hours and paddlewheels for 13 hours.
“In terms of survival, it was high at 91% after the first nursery phase and 89% in the second nursery phase. The average daily growth (ADG) was 0.05g during phase 1 and the cost to produce one 1.35g juvenile was INR1.25 in 2020.”
Key lessons
All in all, the new culture model worked well for Hetal. The 2020 cycle took an average of 53 days in the grow-out phase at a stocking density of an average of 123PL/m2 . ADG was 0.42g. Production was 127.6 tonnes (27.7 tonnes/ ha). Survival was 78% for 31.3g shrimp and FCR was 1.59. At an ex-farm price of INR369/kg (USD 5/kg), the return on investment (ROI) was 42%.
“This total survival was low and the lesson I learnt was that we need to shift out all juveniles from the nursery after each batch and clean up. In large farms, I recommend batch stocking for an effective utilisation of all facilities, to determine precisely the days of culture for harvesting and not to drag the culture duration.,” concluded Hetal.

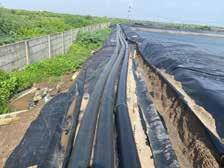
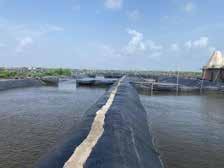
The different stages in water treatment include, from left, ponds for fast mixing of potassium permanganate and poly aluminium chloride, pipes to move water around for recirculation and right, ready to use water reservoirs.