
4 minute read
TECHNICAL GURU: Improving efficiency of existing pump systems
by Amy Stone*
As expenses increase and the markets get even more volatile, everyone is looking to cut costs. While there are many ways to reduce expenses, this article will focus on improving efficiency of existing pump systems. Variable frequency drives are a great tool for optimizing hydraulic systems.
Variable frequency/speed drives, or VFDs/VSDs, are often coupled with water pumps and air blowers to reduce/increase the motor speed while optimizing flow and pressure to intersect the system needs to the pump or blower’s best efficiency point. For many years, many people have oversized their pumps and blowers with the intention of using a valve to create artificial head pressure, moving the system curve far away from the pumps best efficiency point.
A VFD works by manipulating the incoming frequency provided to the motor that it is controlling. This manipulation of frequency also changes the pressure and flow characteristics of the pump or blower. Some VFDs also have an internal transformer which allows it to convert single phase power to three phase power in the smaller horsepower applications.
A very important piece to consider when adding a drive to your system is the type of motor that the pumps have. Not all motors can be used with a VFD. The motor must be rated for 3-phase voltages and inverter duty. If the equipment is not rated for inverter duty applications, it will prematurely fail from overheating the windings in the motor.
Water pumps
Even though this has been an accepted practice that saves in acquisition costs, it translates into wasted energy, electrical expense, and undue wear and tears on the equipment. Using a throttling valve to control flow and create pressure also creates turbulence at the outlet of the pump which can create cavitation conditions that wear down valve bodies and significantly reduce their service life. Cavitation in pumps happens on the suction side and often occurs in higher speed motors (3500 RPM) in suction lift applications operating far to the right hand side of the curve, or outside of an acceptable operating margin of the pumps best efficiency point (BEP). Cavitation reduces the service life of the motor, impeller, and mechanical seals creating costly ongoing maintenance.
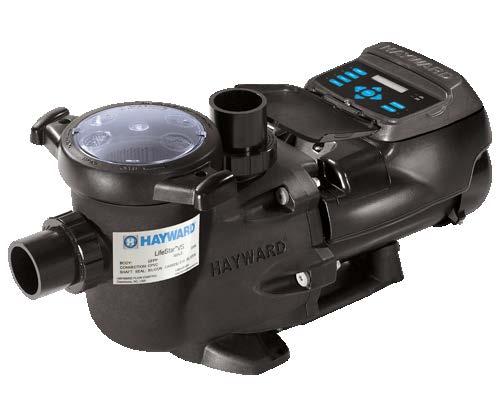
In properly sized systems, a pump is engineered to the duty points of the system requirements. The pump size is calculated based on flow at total dynamic head pressure of the system. This information is used by manufacturers to determine the impeller diameter, wet end sizing and motor frequency thereby allowing the pump to operate at the BEP. Sometimes best efficiency of the pump requires a frequency that is outside of the motor’s synchronized speed without a VFD. Here is when a VFD comes into play.
The VFD allows the user to set the frequency/speed of the motor to the optimal level which ultimately allows the pump to work more efficiently. Friction loss, pressure-drop, and static head are a dynamic part of the system pressure. These dynamics change based on flow demand, filter loading, system stocking levels, changing water volumes, etc. VFD’s can assist with these changes when they are configured with sensors.
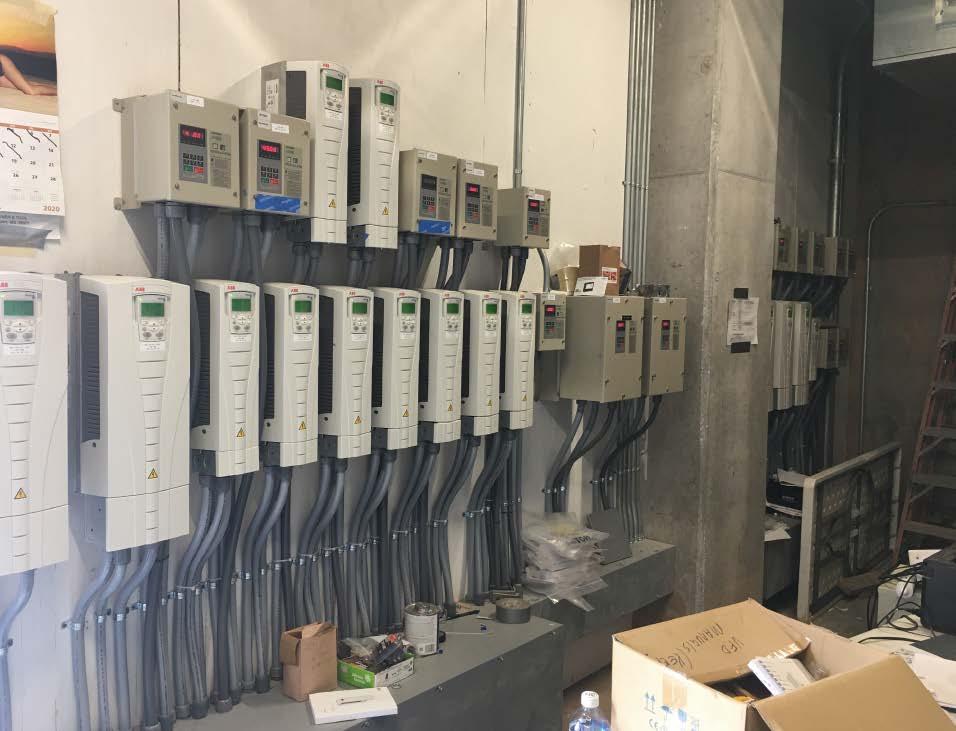
Courtesy of Amy Stone
Depending on the available features of the drive, controls and alarms can be easily integrated into the system to help maintain water quality standards that can help maximize the culture’s growth and yield. As the filter is loaded and flow slows, the VFD can increase the frequency of the motor to accommodate the higher pressure and still maintain the target flow. There are safety features to avoid over pressurizing the system.
Some manufacturers have integrated the VFD onto the pump motor while others prefer stand-alone drives. The stand-alone drives are typically more flexible in programming and can connect to control and alarm systems. The integrated VFDs are generally repurposed pool pumps which are meant to be standalone units and do not have all the input and output options.
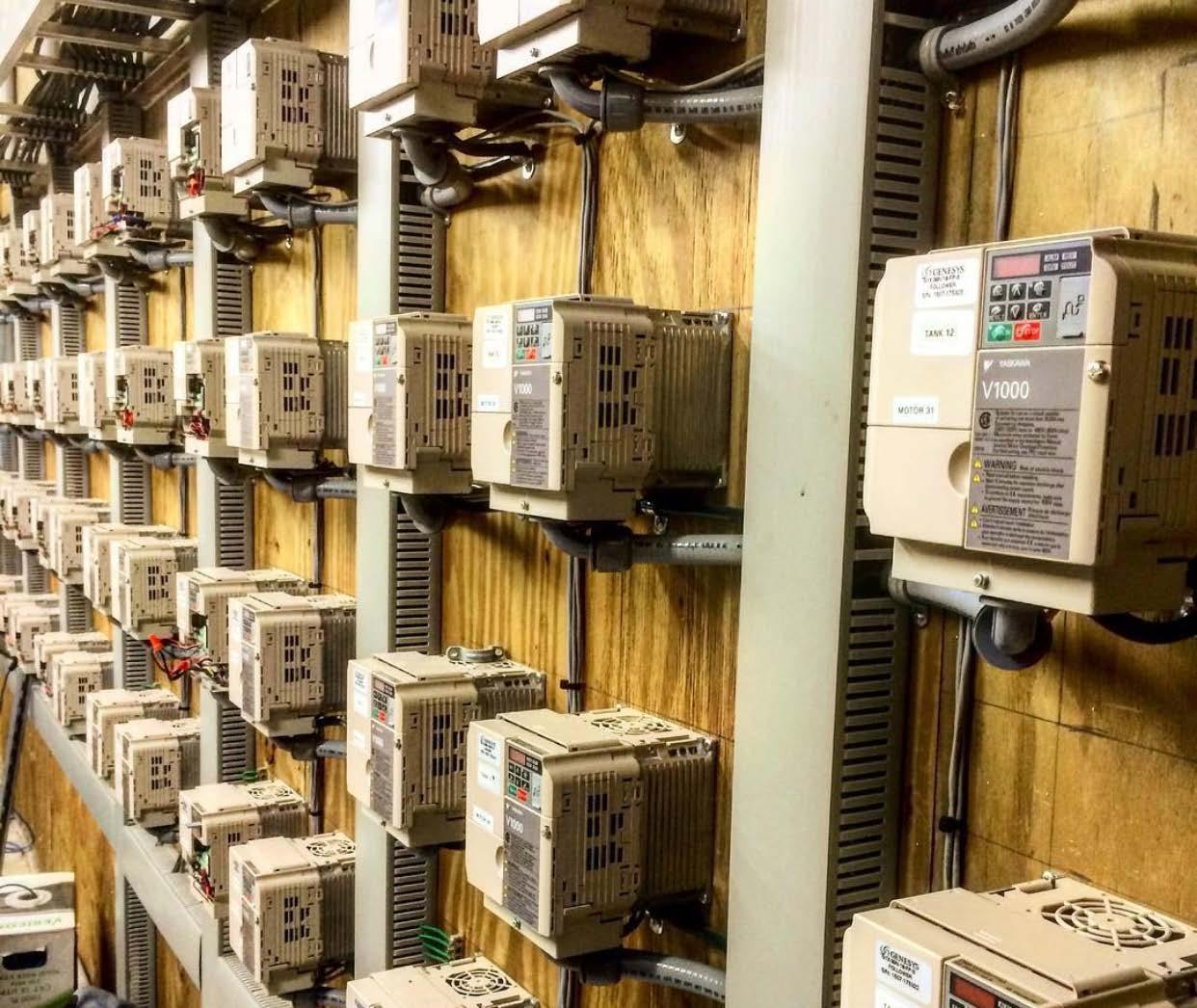
Courtesy of Amy Stone
Blowers
We are now seeing more and more blowers that are available with VFD’s. This is fantastic news given that blowers are often oversized to be able to handle the maximum biomass of a system. Since we are often growing the animals for several months in the same water system, the oxygen demand increases.
While adding or designing a variable frequency/speed drive may not be the first thing you think of when you are trying to increase efficiencies, it is definitely an option to consider.
Amy Riedel Stone is President and Owner at Aquatic Equipment and Design, Inc. She was formerly a Manager at Pentair Aquatic Eco-Systems, and she studied Agriculture at Purdue University. She can be reached at amy@aquaticed.com