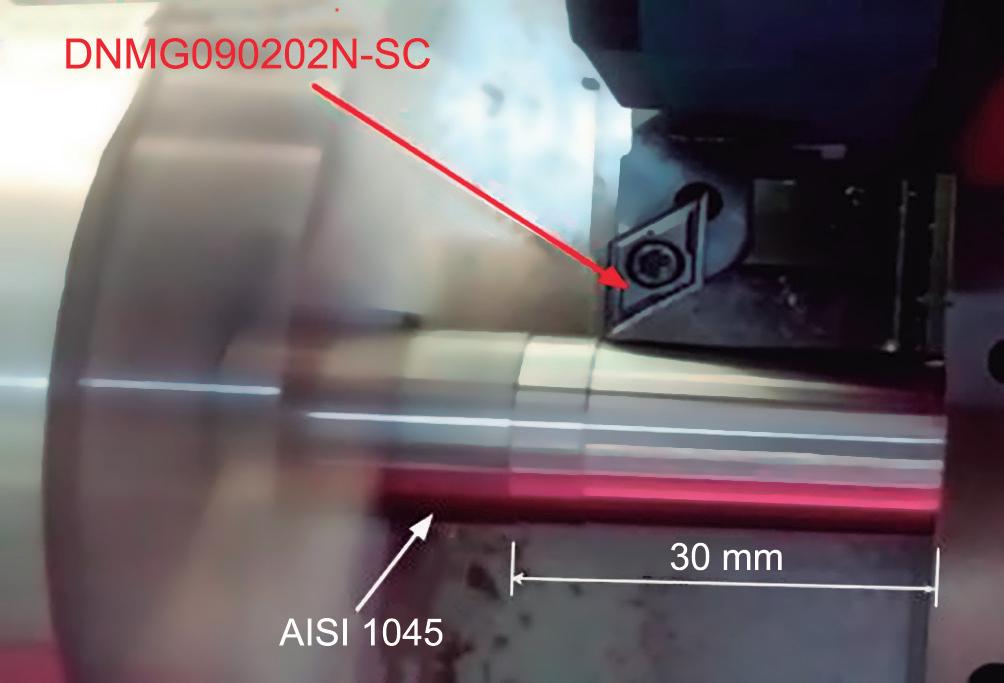
12 minute read
ANÁLISE
Integridade da superfície no torneamento a seco do aço AISI 1045
L. C. Magalhães e G. C. Carlesso
As operações de usinagem a seco podem representar uma vantagem competitiva, uma vez que os custos com meios lubrificantes refrigerantes são reduzidos, assim como os impactos ambientais e aqueles relativos à saúde dos operadores. No presente trabalho, o aço 1045, de relevante emprego na indústria metalmecânica, foi torneado a seco com insertos de cermet (material compósito cerâmico e metálico), microgrãos, e sem revestimentos, sendo variados a velocidade de corte e o avanço. Análises pelo método dos elementos finitos foram realizadas para se prever a distribuição de calor na zona de formação do cavaco, bem como os esforços de corte. A rugosidade das peças usinadas foi avaliada quando usados gumes novos, por meio de interferometria de luz branca, e em função do desgaste de flanco dos insertos, com um rugosímetro de contato. Os mecanismos de desgaste também foram avaliados, e a microdureza foi examinada a partir da superfície usinada, em cada fase microconstituinte do material. Como esperado, o avanço é decisivo para a qualidade final da superfície torneada, em função da própria cinemática do processo, e a velocidade de corte teve pouca influência neste sentido. A superfície foi significativamente danificada com a progressão do desgaste de flanco do inserto, com o desgaste abrasivo sendo predominante durante os experimentos. Não foram observados defeitos de microestrutura, propagação de trincas ou deformações acentuadas próximas à região da superfície usinada. Com efeito, a rota do torneamento a seco do aço 1045, com insertos de cermet não revestidos, se mostrou viável do ponto de vista da vida útil da ferramenta, integridade da superfície, formação de cavacos e sustentabilidade.
No presente trabalho, o aço 1045 foi torneado a seco, com insertos de cermet (material compósito cerâmico e metálico) sem revestimentos. O objetivo foi avaliar se a combinação do uso de cermets modernos no torneamento a seco de aços de médio carbono é viável, do ponto de vista da integridade da superfície usinada e da vida útil da ferramenta. Optou-se pela não utilização de meios lubrificantes refrigerantes, uma vez que estas substâncias podem causar problemas ambientais, tais como contaminação da água e do solo, quando descartadas de forma inapropriada. Com efeito, ao se optar pelo processo a seco, os custos podem ser reduzidos pela simplificação de toda a logística relacionada aos meios lubrificantes refrigerantes, incluindo compra, armazenamento, tratamento e descarte. Além disso, efeitos adversos na estrutura da máquina-ferramenta e na peça usinada, tais como corrosão, podem ser atenuados. Em tempo, o uso de lubrificantes refrigerantes pode causar efeitos adversos à saúde humana(4) . Os cermets se destacam por sua alta dureza a quente, baixa reatividade com aços e outros metais e, principalmente, baixa condutividade térmica em comparação com o metal duro(5). Estas características, bem como desempenho e custo, tornam as ferramentas de cermet uma alternativa competitiva para a usinagem de pré-acabamento e acabamento de aços e ferros fundidos(1) . A rota do torneamento a seco tem sido bastante explorada em pesquisas recentes. Yang et al(6), por exemplo, realizaram o estudo do mecanismo de desgaste de flanco de cermets (Ti,W)C-Mo2C-Co durante a usinagem de um aço de alta liga de carbono endurecido a 62 HRC. No estudo, foi considerado
Laurence Colares Magalhães (laurence.magalhaes@ufes.br) e Gabriel Catarino Carlesso são pesquisadores da Universidade Federal do Espírito Santo (UFES). Este artigo foi apresentado no XXIV Colóquio de Usinagem, realizado entre 25 e 27 de maio de 2022, em Curitiba (PR) e organizado pelo Laboratório de Pesquisa em Usinagem da Pontifícia Universidade Católica do Paraná (PUCPR). Reprodução autorizada.
Figura 1 – Esquema de fixação ferramenta-peça durante os testes
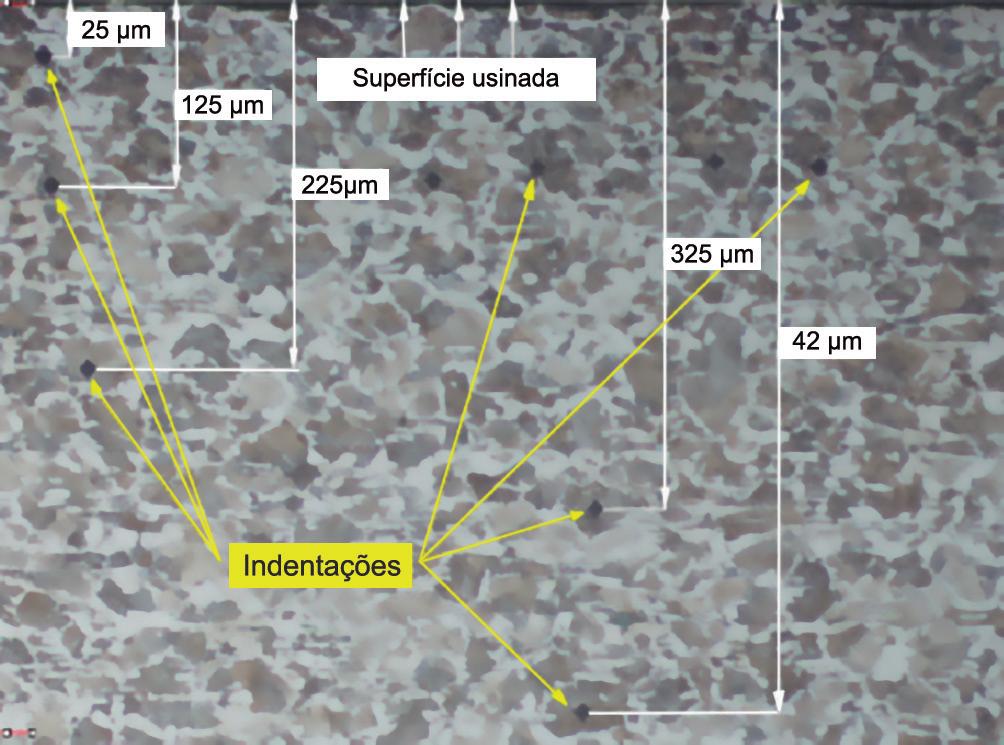
Figura 2 – Indentações de microdureza na fase perlita em uma amostra usinada com Vc = 275 m/min e f = 0,1 mm/rev
como critério de fim de vida da ferramenta o desgaste de flanco médio igual a 0,3 mm, obtendose uma vida útil da ferramenta de cerca de 33 minutos para uma velocidade de corte de 180 m/min e vida útil cerca de 40% menor quando a velocidade de corte foi aumentada para 280 m/min. O objetivo do presente trabalho é contribuir para um processo de usinagem mais sustentável.
Materiais e métodos
O torneamento externo a seco foi realizado em barras cilíndricas de aço AISI 1045 (% em peso - 0,48 C, 0,73 Mn, 0,25 Si, 0,016 P, 0,05 S, 0,02 Al, 0,02 Cr, 0,01 Ni – dados do fabricante) com 30 mm de diâmetro e 55 mm de comprimento em um torno CNC Boxford 160 VMCi (0,5 kW de potência e 3.200 rpm máxima). As propriedades mecânicas do material são mostradas na tabela 1. Os insertos de cermet não revestidos, positivos (ângulo de saída de 6°) classe T1200A, geometria DNMG090202N-SC e porta-ferramentas SDACR062B, fornecidos pela Sumitomo Tools, foram usados nos experimentos, conforme ilustrado na figura 1. De acordo com o fabricante, os insertos apresentam uma fase tenaz composta de grãos grossos, uma fase dura e tenaz rica em tungstênio e uma fase de grãos finos com TiCN na fase ligante. Os parâmetros de corte empregados estão apresentados na tabela 2. Um novo gume foi utilizado para cada teste, sendo cada um deles reproduzido duas vezes. Uma ferramenta dedicada foi utilizada para uniformizar a superfície antes de cada teste.
Tabela 1 – Propriedades do material
Resistência à tração (MPa) 793 Limite de escoamento (MPa) 718 Dureza Brinell (HB) 248
Análise por elementos finitos (FEA)
Análises por elementos finitos (finite elements analysis, FEA) foram realizadas para prever forças de corte e o fluxo de calor na zona de corte e formação de cavacos. O software AdvantEdge V7.1 foi usado para simular o corte ortogonal. O coeficiente de atrito foi estabelecido de acordo com a geometria da ferramenta e configurações padrões do software para ferramentas cerâmicas. O software Tecplot 360 R2 foi utilizado para análise e tratamento dos dados. O estereomicroscópio Carl Zeiss Discovery V12 equipado com software AxioCam 305 e AxioVision V4.7 foi usado para medir a espessura do cavaco e comparar esses resultados com as análises por elementos finitos.
Rugosidade da superfície e desgaste de flanco
A topografia das superfícies usinadas foi avaliada por interferometria de luz branca. Foi empregado o interferômetro New View 7300, da Zygo, com taxa de varredura de 100 µm/s e uma ampliação de 20 vezes. Em um segundo momento, avaliouse a rugosidade da superfície
Vc (m/min) 175 Tabela 2 – Parâmetros de corte
f (mm/rev) 0,025; 0,05; 0,075 e 0,1 ap (mm)
0,2 (100% do raio de quina)

Figura 3 – Distribuição de calor e espessura de cavacos em análises FEA para f = 0,025 mm/rev: Vc = 175 m/min (à esquerda) e Vc = 275 m/min (à direita)
Figura 4 – Distribuição de calor e espessura de cavacos em análises FEA para f = 0,1 mm/rev: Vc = 175 m/min (à esquerda) e Vc = 275 m/min (à direita)
Figura 5 – Rugosidade 3D da superfície para o menor avanço (à esquerda) e maior avanço (à direita) para Vc = 175 m/min
Figura 6 – Rugosidade 3D da superfície para o menor avanço (à esquerda) e maior avanço (à direita) para Vc = 275 m/min a cada 150 mm de intervalo de comprimento usinado juntamente com a avaliação do desgaste da ferramenta, para que pudesse ser traçada uma curva rugosidade x desgaste de flanco. Nesta etapa foi empregado um estereomicroscópio Carl Zeiss Discovery V12 equipado com software AxioCam 305 e AxioVision V4.7 para aquisição e processamento das imagens digitais do desgaste e um rugosímetro Taylor Hobson Surtronic 25. Seguiu-se a norma ISO 4288. Os resultados são uma média de três medições realizadas em cada amostra e foram comparados com a rugosidade teórica. Os mecanismos de desgaste foram avaliados junto a um microscópio eletrônico de varredura (MEV) JEOL, modelo JSM 6610 LV equipado com detector de energia dispersiva de raios-X (EDS) Bruker, modelo Xflash detector 6. O critério de fim de vida da ferramenta utilizado foi desgaste de flanco médio VBB = 0,1 mm, de acordo com a norma ISO 3685.
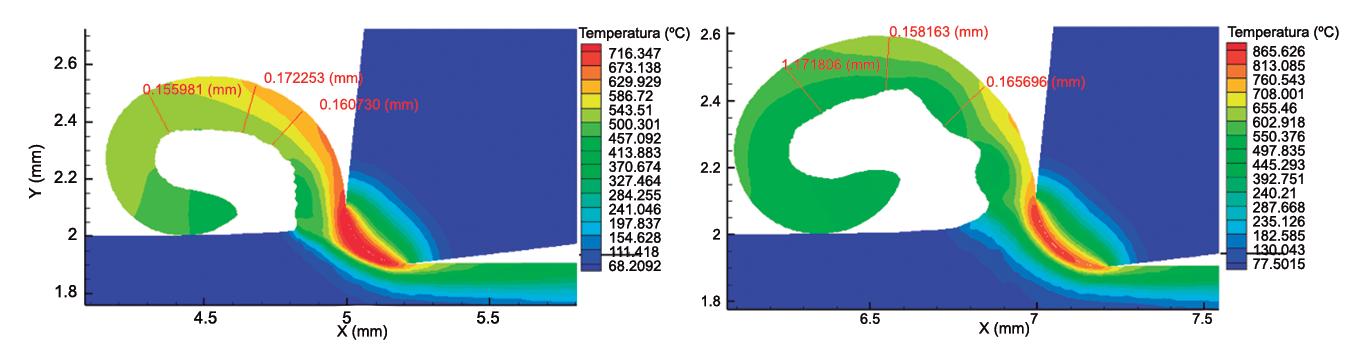
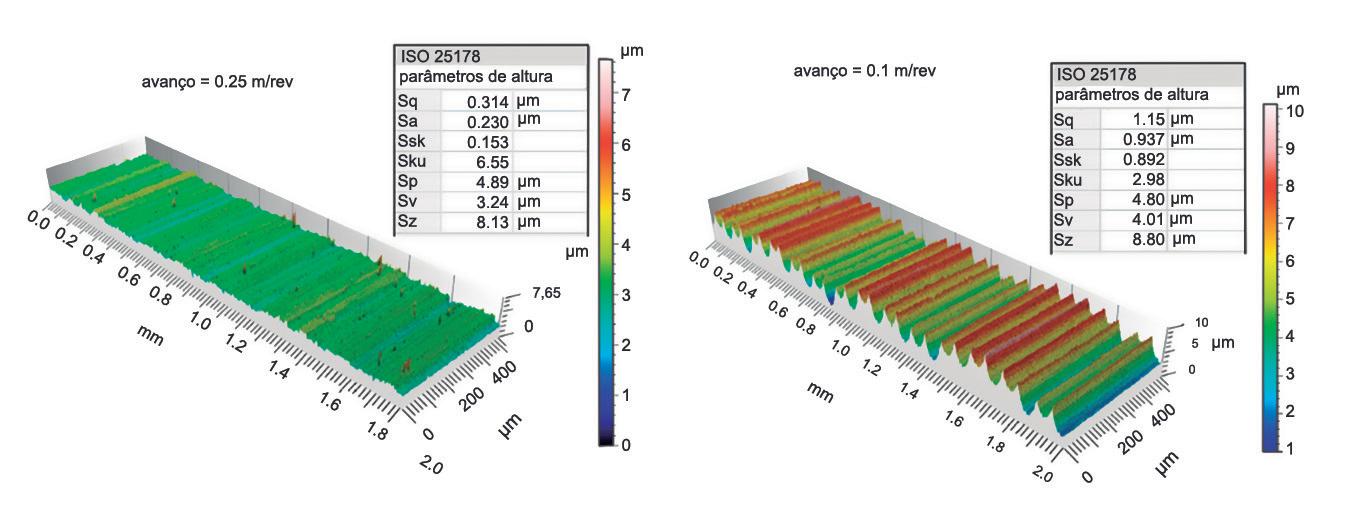

Avaliação da microestrutura e da microdureza
Foram realizados testes de microdureza em cada microconstituinte do material (perlita–fase escura e ferrita–fase branca). Os cortes metalográficos foram imersos em solução de ácido nítrico com concentração de 2% (Nital 2%) durante 10 segundos. Um penetrador Vickers com carga de 25 g, durante 12 s, foi utilizado no teste para todas as medições que foram realizadas abaixo da superfície usinada nas profundidades de 25 µm, 125 µm, 225 µm, 325 µm e 425 µm, conforme mostrado na figura 2. O microscópio Nikon Eclipse MA200 foi usado para analisar a microestrutura do material após o ensaio de microdureza.
Figura 7 – Altura média aritmética (Sa) em função do avanço e velocidade de corte (nova aresta de corte)

Resultados e discussão
Análise por elementos finitos (FEA) Os valores de temperatura são 17% menores quando se compara a configuração de velocidade de corte e avanço empregando os maiores valores, com a configuração com os valores mais baixos para estes parâmetros de corte, conforme demostrado nas figuras 3 e 4. Quanto menor o avanço, menor o ângulo de cisalhamento do cavaco. Comparando a espessura dos cavacos quando avaliados por microscopia com os valores obtidos por análise FEA, respectivamente, tem-se para Vc 175 m/min e f 0,025 mm/rev, 0,045 mm contra 0,043 mm de espessura dos cavacos. Já para f 0,1 mm/ rev, tem-se 0,12 mm contra 0,15 mm. Quando Vc é igual a 275 m/ min, para o menor avanço tem-se 0,028 mm contra 0,035 mm e para o maior avanço, tem-se 0,18 mm contra 0,17 mm, sendo possível verificar uma boa concordância entre os valores de espessura dos cavacos estimados por FEA e avaliados por microscopia. Na tabela 3 estão ilustradas imagens dos cavacos gerados para os parâmetros de corte utilizados. Os cavacos são predominantemente gerados na forma de fitas torcidas do tipo contínuo, para todas as configurações de teste. Rugosidade da superfície e desgaste da ferramenta As topografias das superfícies usinadas, em função do menor e do maior avanço de corte, estão ilustradas nas figuras 5 e 6, onde é possível notar a influência do avanço na qualidade da superfície usinada, como esperado, em função da cinemática do processo. Os resultados resumidos e comparados com a rugosidade teórica estão ilustrados na figura 7. A relacão da altura média aritmética (Sa) com o desgaste de flanco são mostrados na figura 8. A curva de vida da ferramenta é mostrada na figura 9. A figura 10 mostra o flanco principal dos insertos no critério de fim de vida quando empregadas as velocidades de corte de 175 m/min e 275 m/min, respectivamente (avanço 0,025 mm/rev e profundidade de corte 0,2 mm). Observa-se que o desgaste abrasivo foi predominante.
Microdureza e microestrutura Os resultados da microdureza a partir da superfície usinada são mostrados na figura 11. Para a velocidade de corte de 175 m/min, houve uma leve redução na dureza da ferrita a 25 µm em relação à superfície usinada. O mesmo ocorreu
Tabela 3 – Imagens dos cavacos formados após a usinagem ao empregar os parâmetros de corte em análise 0,025 f (mm/rev) 0,05
175 0,075 0,1
Vc (m/min) 275

Figura 8 – Deterioração da superfície usinada com o aumento do desgaste de flanco Figura 9 – Curva de vida útil para o inserto de cermet na usinagem a seco do aço AISI 1045
Figura 10 – Desgaste do flanco principal no critério de fim de vida: (a) Vc = 175 m/min (ampliação de 400 x); (b) Vc = 275 m/min (ampliação de 400 x)
Figura 11 – Microdureza a partir da superfície usinada para diferentes avanços em cada fase do material: (a) Vc = 175 m/min; (b) Vc = 275 m/min
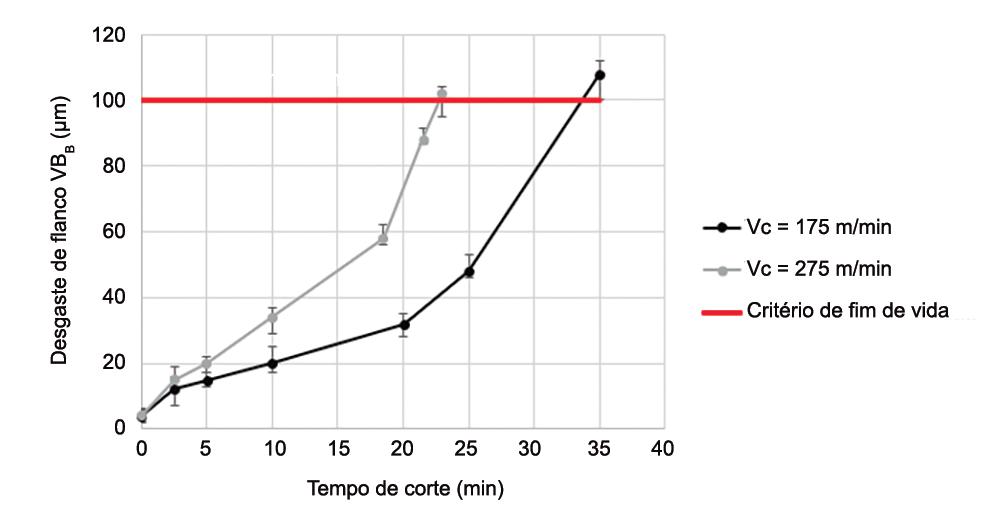
na perlita para Vc = 275 m/min. As temperaturas na zona de corte, próximas à faixa de austenitização do material, em conjunto com as pressões específicas de corte, podem ter contribuído para esse leve “amolecimento”.
Conclusão
De acordo com as análises por elementos finitos (FEA), a temperatura na zona de corte atinge a faixa de 860 °C para os maiores valores de avanço e velocidade de corte usados nos experimentos. A espessura e o formato dos cavacos previstos pela análise FEA estão muito próximos do observado nos cavacos obtidos nos experimentos. As forças de corte não ultrapassaram 120 N pela análise FEA, principalmente devido às pequenas seções de corte utilizadas. O avanço é um fator-chave na rugosidade da superfície, devido à própria cinemática do processso de torneamento, enquanto a velocidade de corte mostrou pouca influência sobre este fator. Valores da ordem de Sa 0,23 µm podem ser obtidos quando se utilizam os menores valores de avanço, empregando um gume novo. Como esperado, o aumento do desgaste de flanco prejudica a rugosidade da superfície usinada. Quando o desgaste atinge VBB = 0,1 mm, o valor de Ra aumenta para 2,92 µm. O desgaste de entalhe nos flancos primário e secundário é decisivo para este fato. O desgaste abrasivo é predominante. Observou-se redução dos valores de microdureza, próximo à superfície usinada (até 100 µm de profundidade), tanto na fase perlita quanto na ferrita. Não foram observados defeitos, trincas, deformações ou alterações na forma dos grãos.
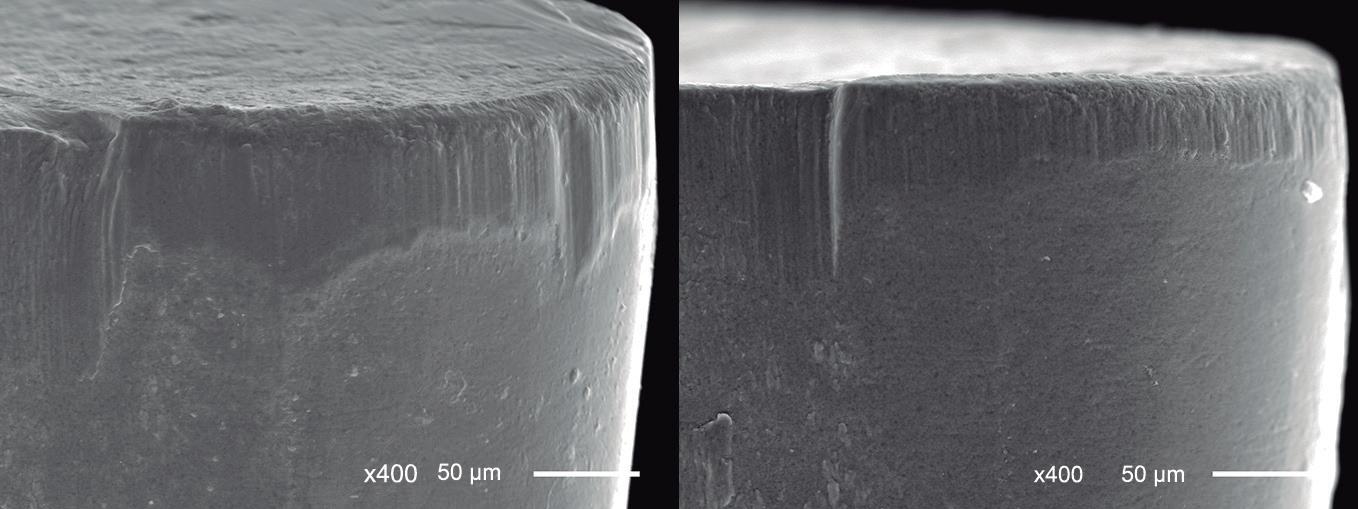

O torneamento a seco do aço 1045, com insertos de cermet não revestidos, mostrou-se bastante viável do ponto de vista da qualidade da superfície, vida útil da ferramenta, microestrutura, morfologia do cavaco e sustentabilidade.
1) Chen , X.; Xu, J.; Xiao, Q. Cutting performance and wear characteristics of Ti(C,N)-based cermet tool in machining hardened steel. Int J
Refract Met Hard Mater 2015, vol. 52, pp. 143-150. 2) ISO 3685: Tool life testing wit single point turning tools, International
Organization for Standardization, 1993.
Agradecimentos
Os autores agradecem às equipes do Tricormat e do Laboratório de Caracterização de Superfícies de Materiais do CT – UFES, ao Laboratório de Ultraestrutura Celular Carlos Alberto Redins (LUCCAR – UFES) e ao edital MCT/FINEP/ CT – INFRA – PROINFRA 01/2006. Ao LABMAT – UFSC.
Referências
3) ISO 4288: Geometrical product specification (GPS)—Surface texture: Profile method — Rules and procedures for the assessment of surface texture, International
Organization for Standardization, 1996. 4) Klocke, F.; Eisenblatter, G. Dry
Cutting. Annals of the CIRP 1997, vol. 46/2. Responsabilidade pelas informações Os autores são os únicos responsáveis pelas informações incluídas neste trabalho.
5) Peng, Y.; Miao, H.; Peng, Z.
Development of TiCN-based cermets: mechanical properties and wear mechanism. Int J. Refract Met Hard
Mater 2013, vol. 39, pp. 78-89. 6) Yang, T.; Ni, L.; Xiong, J.; Shi, R.;
Zheng, Q. Flank wear mechanism and tool endurance of (Ti,W)C-Mo2C-Co cermets during dry turning. 2018. vol. 44, pp. 8447-8455.
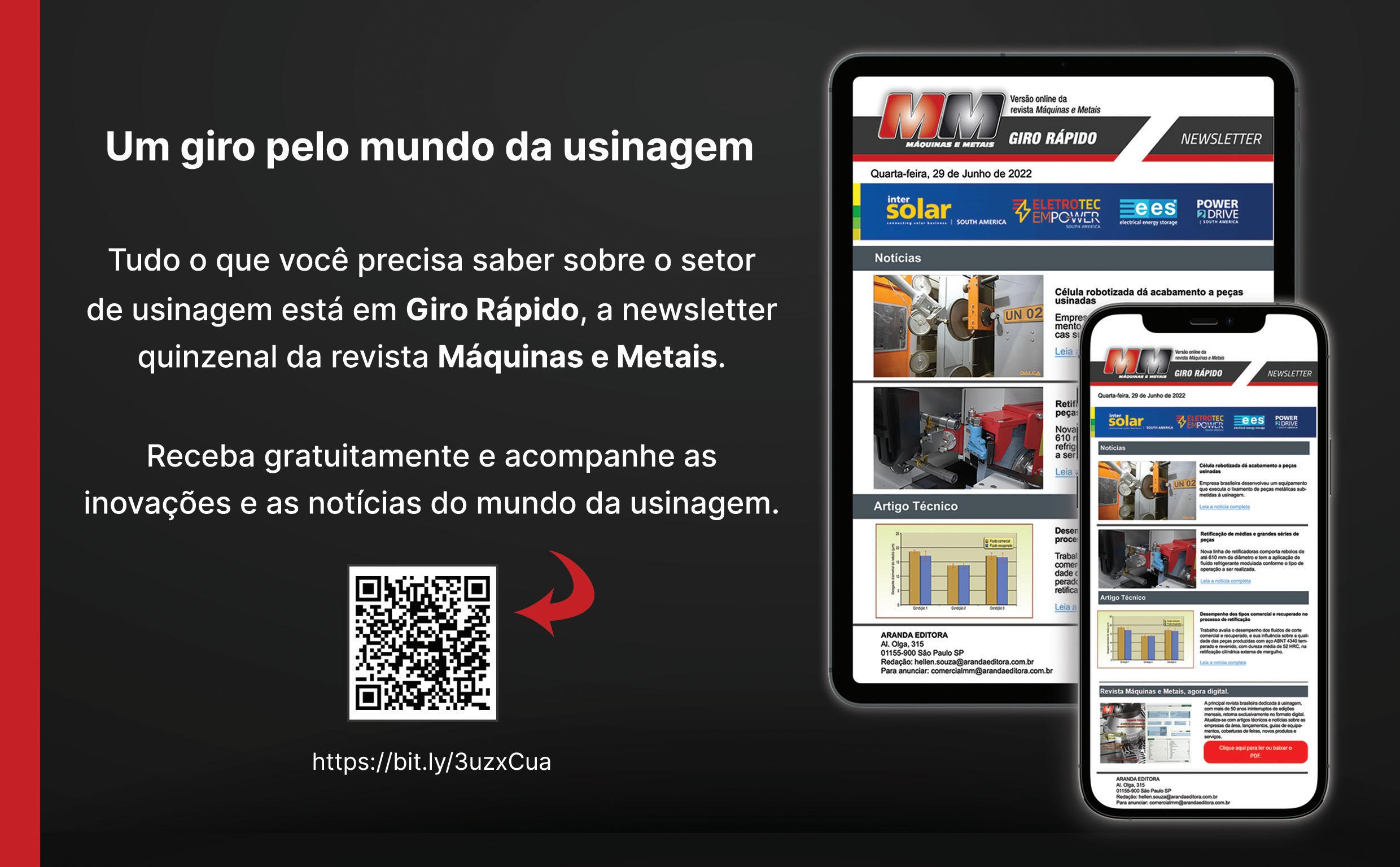