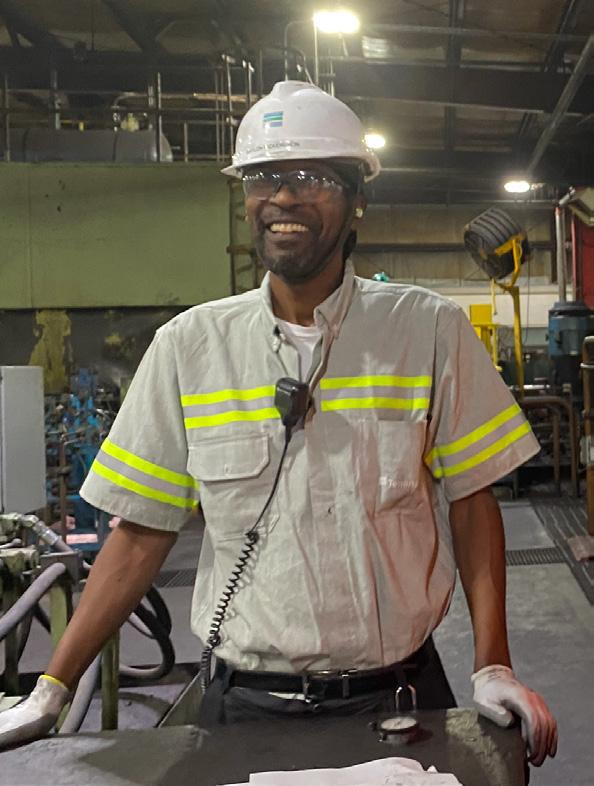
10 minute read
HOT JOBS!
from BluePrint 2023
PIPE FITTER
Company: The Systems Group
Starting Salary: Up to $29/hour
WHAT DOES THE JOB DO?
Plans the installation of piping system components, cuts pipe to lengths as determined by isometric drawings using a portable bandsaw, cutting torch and pipe cutting machine.
Threads pipe, mounts pipe hangers and brackets on walls and ceilings to hold the pipe, assembles and installs pipes and pipe fittings. Observes and complies with all safety, project rules and company policies and procedures.
WHY IT’S IMPORTANT:
Pipe fitting is important because pipe fitters build and maintain complex piping systems in refineries, energy plants and steel mills. The piping system carries a range of substances such as steam, oil and chemicals.
ESSENTIAL SKILLS AND ATTRIBUTES:
Pipe fitters need to be able to read blueprints, use advanced math and be able to operate industrial tools safely.
WHAT MAKES THIS POSITION IN HIGH DEMAND?
Pipe fitters are in demand because of the lack of training available and little public knowledge about this craft. There are very few training programs for pipe fitting in Arkansas technical colleges and schools.
HOW DO I LEARN MORE? www.tsg.bz
PIPE WELDER
Company: The Systems Group
Starting Salary: Up to $29/hour
WHAT DOES THE JOB DO?
Weld metal piping systems composed of pipe and tube as specified in blueprints and isometric drawings, follow welding procedures to ensure a quality weld.
WHY IT’S IMPORTANT:
Metal piping is used in almost every factory, industrial plant and shipyard in the country. Because piping is used in so many industries, pipe welders are vital to the building and maintaining of manufacturing facilities that support our way of life.
ESSENTIAL SKILLS AND ATTRIBUTES:
Experience in the use of various types of electric arc welding equipment, good hand-eye coordination, attention to detail and the ability to read a tape measure. A good attitude, patience and a willingness to work are important.
WHAT MAKES THIS POSITION IN HIGH DEMAND?
Pipe welding calls for a high degree of technical skill, manual dexterity and strong hand-eye coordination. The training to become a pipe welder is extensive.
HOW DO I LEARN MORE? www.tsg.bz
GAYLON NICKERSON
Auto Buckler, Tenaris
Hometown: Osceola
Age: 53
Tenure with Tenaris: 7 months
BLUEPRINT: What does your job entail at Tenaris?
GAYLON NICKERSON: The line I work on, we put all the markings and couplings on the pipe, and we do the threading. And that’s the beginning of the line, the threading. I’ve been doing that for about three months.
BP: What got you interested in joining Tenaris? Did you have family members working there?
GN: It was a career change. I didn’t know anybody who worked here personally, but I’d heard about it. When there’s a strong company in town, a lot of people know about it. There was a lot of talk about Tenaris being a good place to work.
BP: What emphasis is put on the safety program there?
GN: We have a safety meeting every morning before we start work. Every safety meeting always starts off by asking if anybody has anything they want to say about something they experienced on the production floor. I appreciate having the opportunity to give that input. There are also procedure books at all the workstations; if you follow the procedures, you can’t go wrong.
If something does happen, Tenaris has a program where they look into the incident thoroughly as far as what happened, why it happened, how it happened and what could have been done differently. They record it and if it’s not already in the safety manual, they will make changes right away to make the working environment better.
BP: What do you like best about working at Tenaris?
GN: I am a former NBA player, and our team is like a basketball team; you depend on your teammates. Your success relies on how well you work with and help your teammates. The better you are as a team, the more successful you will be.
That’s the same thing with Tenaris. Everybody has the same goal and that’s to put out good quality pipe. For that to happen, everybody has to do what they’re supposed to do. It’s a great team atmosphere. We work as a team and that makes you feel safe. It’s a good place to work.
BP: What would you tell high schoolers about working at Tenaris, and what would you tell them about what it takes to be successful?
GN: I would tell the kids that it’s a great career. I’d also tell them to prepare by learning some math. Pick up some kind of mechanics course, auto mechanics or some kind of mechanical work. Do that, you’ll be great for Tenaris.
DUSTIN DICKENS
Base Maintenance Group Supervisor, Tenaris
Hometown: Campbell, MO
Age: 25
Years with Tenaris: 6
BLUEPRINT: You are an electrical worker by trade, how did you train for that job?
DUSTIN DICKENS: You do four years on the job and then four years in a trade school where it’s one day a week. Then you have to have so many on-the-job hours. Two years of that training was at my previous job, an industrial contracting company. Those two years carried over when I came to Tenaris.
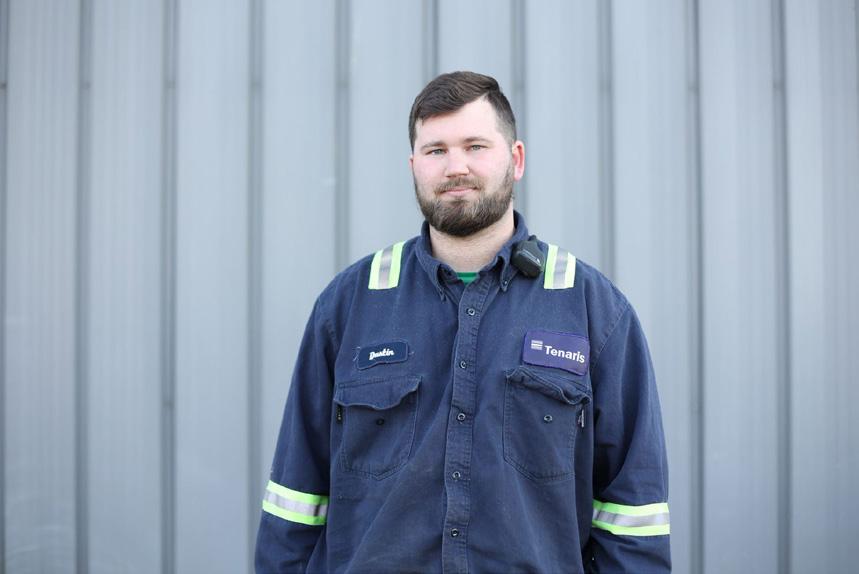
I’m now a journeyman electrician and I’m waiting on my affidavit to test as a master electrician.
BP: How did you decide on this particular career path?
DD: Almost everybody in my family has some sort of skilled trade. I have people in my family who are roofers, construction workers, electricians. I knew this type of work was what I wanted to do through working with my family and seeing the kind of benefits they saw from it.
BP: Do you typically work by yourself on issues or are you typically part of a team?
DD: There’s hardly ever a time when you don’t have a team with you out here. Primarily I’m with a group of six guys. We have production goals we’re supposed to meet, we have preventative maintenance activities we do where we go around and look at the equipment, talk to operators, look at possible downtimes we’ve had and look for solutions to fix them.
BP: What does your work week look like?
DD: It’s five days a week, minimum 10 hours a day. Normally it’s 50 hours but if the line’s down, I stay until it’s fixed. My set shift is 7 a.m. to 5 p.m., Monday through Friday. But, of course, I can get called in throughout the night, as needed.
BP: If you could talk to a roomful of young people about the things it takes to be successful in this job, besides the technical skills, what would you say is most important?
DD: I think just dedication. I think anybody can learn the job, it’s just the dedication and willingness to learn. Understanding that you are not above doing anything, that’s the biggest thing. You may think that you understand something, but when somebody else has a different point of view, that’s not necessarily wrong, it’s just a different way of looking at it. Being able to take that into account and learn together is the mark of a really great employee.
LANA SMITH
HVAC Student, Arkansas Northeastern College
Hometown: Blytheville
Age: 41
BLUEPRINT: What inspired you to go back to school?
LANA SMITH: I have been in or around the HVAC industry for the past 16 years. Never in a technical capacity, always clerical or management. Currently I am the office manager for a national HVAC manufacturing company in Blytheville. The company is rapidly expanding and we’re taking on more manufacturing from our home office, which is in Europe.
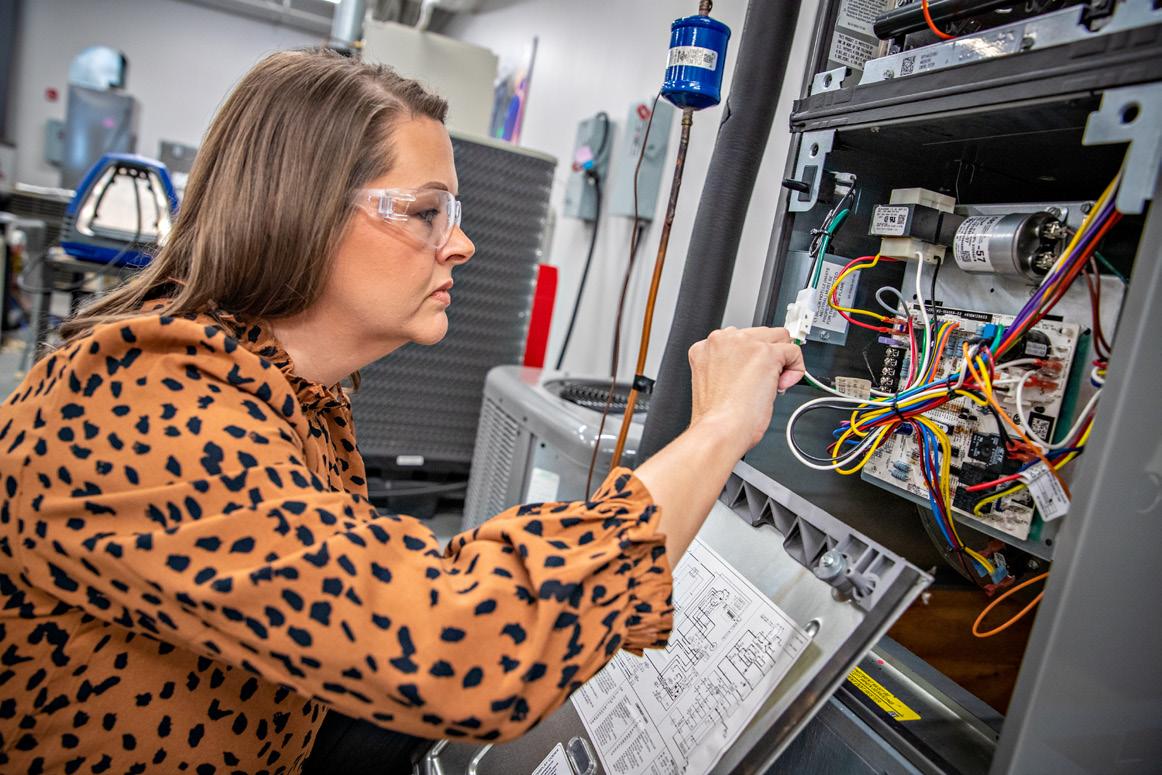
With that increase in manufacturing brings an increase in employees both skilled in HVAC as well as manufacturing. For me, if I’m going to operate a manufacturing facility, it was important for me to understand what my employees’ job duties are.
BP: So, the goal is not necessarily to start doing installs, but to understand the process and identify how to maintain quality control for employees and customers, right?
LS: Absolutely. There are times that I’ve gone out to the steel mills here in Mississippi County and I’ve gone out to see areas where HVAC systems are needed. I was there just to observe at that time, but I absolutely intend to take the knowledge that I get from this course. I intend to use that to go to our customer sites and be knowledgeable while I’m there of what I’m seeing and what their needs are.
BP: What technical skills did you bring into the educational program? LS: Prior to me deciding to do this, my technical background was very limited. We do manufacture here in our facility, so I don’t spend 100% of my time in my office. I am out in the warehouse, I am out on the floor. I fill parts orders for our company. So, I’m aware of what components the equipment takes.
Prior to taking this course, I also had a little knowledge on how an HVAC system operates, how it works. But as far as being able to go out and put my hands on a piece of equipment and diagnose it, I had no prior knowledge.
BP: What’s the job market like for someone who graduates from the program you’re currently in?
LS: The job market is very lucrative at this time. For a while now, the trade industries have kind of been shunned or pushed aside so everyone who’s currently in the industry is getting older. They’re retiring and we’re having trouble finding new technicians because we’re just not getting enough interest in the trade industries. Right now in the trade industries, for HVAC especially, the market for jobs is just wide open.
Student, aviation program
Arkansas Northeastern College
Hometown: Clinton
Age: 19
BLUEPRINT: What’s the job market like for a graduate of this program?
SAM APPLEBY: I’m actually employed right now, at age 19, by Midcontinent Aviation up in Hayti, Missouri, which is just 20 miles up the interstate from the college. What I do from 8 a.m. to 3 p.m. is I work on airplanes. I’m slotted to take over the body shop within a year or two.
BP: How did you get interested in this career field?
SA: I got into repairing vehicles, and later airplanes, by helping my grandpa keep his farm truck running. It was a 1978 Dodge and it always had issues. I got into aviation because my grandma, aunt and my other grandfather all worked in aviation maintenance. My mom’s dad was in the Air Force for aviation maintenance; when he was about my age, he was given the option of either going to jail or join the Air Force, so he joined the Air Force and spent 22 years being a C-130 mechanic. My dad’s mom and his sister both worked for Falcon Jet in Little Rock in the late 1990s and early 2000s. Grandma worked quality control and I’d been to work with her a couple times to see what it was like.
BP: What classes or experience in high school helped prepare you for this course of study in college?
SA: At my high school, and most high schools in Mississippi County, you have the ability to go to ANC on the high school side and take certain trade classes like welding, criminal justice, construction and aviation maintenance.
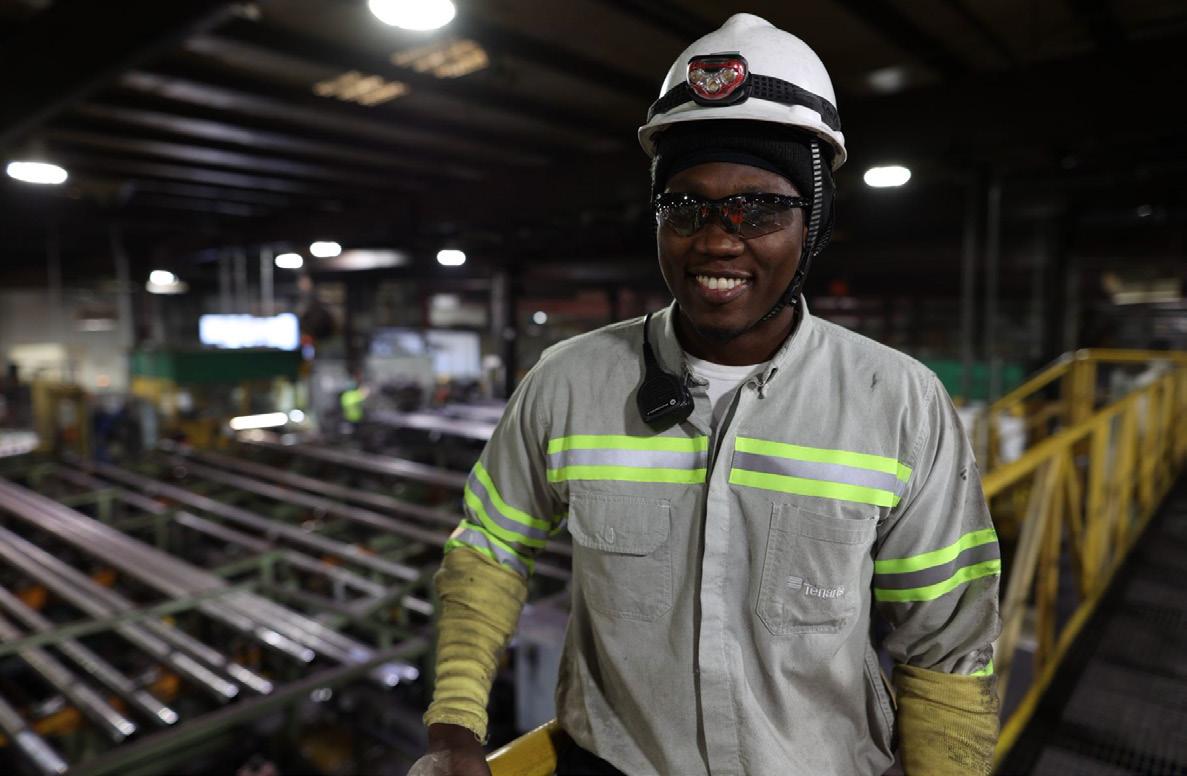
BP: Are there other classes high schoolers can take that will help them get a leg up on their college coursework?
SA: Take ag classes or shop classes; anything dealing with maintenance or motors or bodywork or sheet metal will get you into the routine of what I currently do every day. For anybody who’s concerned about their skills background, most personal airplanes are really just redesigned car motors put on a stainless steel chassis and wrapped in aluminum. There’s really not much difference between a car motor and an aviation motor until you get into jets and turboprops. Plus, if you can do body work on a car, you can do body work on an airplane. It’s not very different at all.
FERRIEL HARVEY
Team Leader PMC, Tenaris
Hometown: Blytheville
Age: 45
Years with Tenaris: 21
BLUEPRINT: Describe the personal growth you’ve experienced working for Tenaris.
FERRIEL HARVEY: The biggest thing that has changed over the years, I would say, is being open-minded and being patient. In the beginning, I really didn’t have a lot of patience. I felt like things weren’t coming fast enough and, on a few occasions, I almost wanted to quit.
It was a few guys who really took me under their wing and really coached me up. That allowed me to see things a lot differently. I began to understand every job is important no matter if you’re at the bottom entry level or the top as a supervisor or general manager. Every job is important.
BP: How did you wind up working here?
FH: I didn’t graduate high school, actually. I went to the 12th grade, but I got into some trouble and it caused me not to finish out my last year of school. I was kind of bouncing around, wasn’t sure if I wanted to stay here in Arkansas or move to Chicago. I’ve got family there.
I decided I needed to try to get a job but there was no job really trying to hire me at the time because I didn’t have a diploma. So, I went back to get my GED and, at the time, one of my dad’s friends was telling me it’s possible I could get on here at Tenaris.
The thing was, when I interviewed, every time they asked me a question, I went blank, like clockwork. At the end, I knew I’d bombed out, but the guy who was training us was a really nice guy. I guess he could tell that I wanted to work, because when a slot became available, he decided he was going to allow me to fill that slot. By the grace of God, he saw something in me. I kid you not.
BP: Now that you’re in a role that manages others, how do you invest in their success?
FH: Our new hires, we try to be patient when we’re training them. Like I said, a couple guys took me under their wing and that’s what I try to do for the people on my team now.
Being successful is a learning curve. When I first came into the field, I was kind of like, “Man, I wouldn’t do that.” The day I decided I wanted to be different from that type of mindset and accept doing what was asked of me, I found out being openminded opened so many doors.