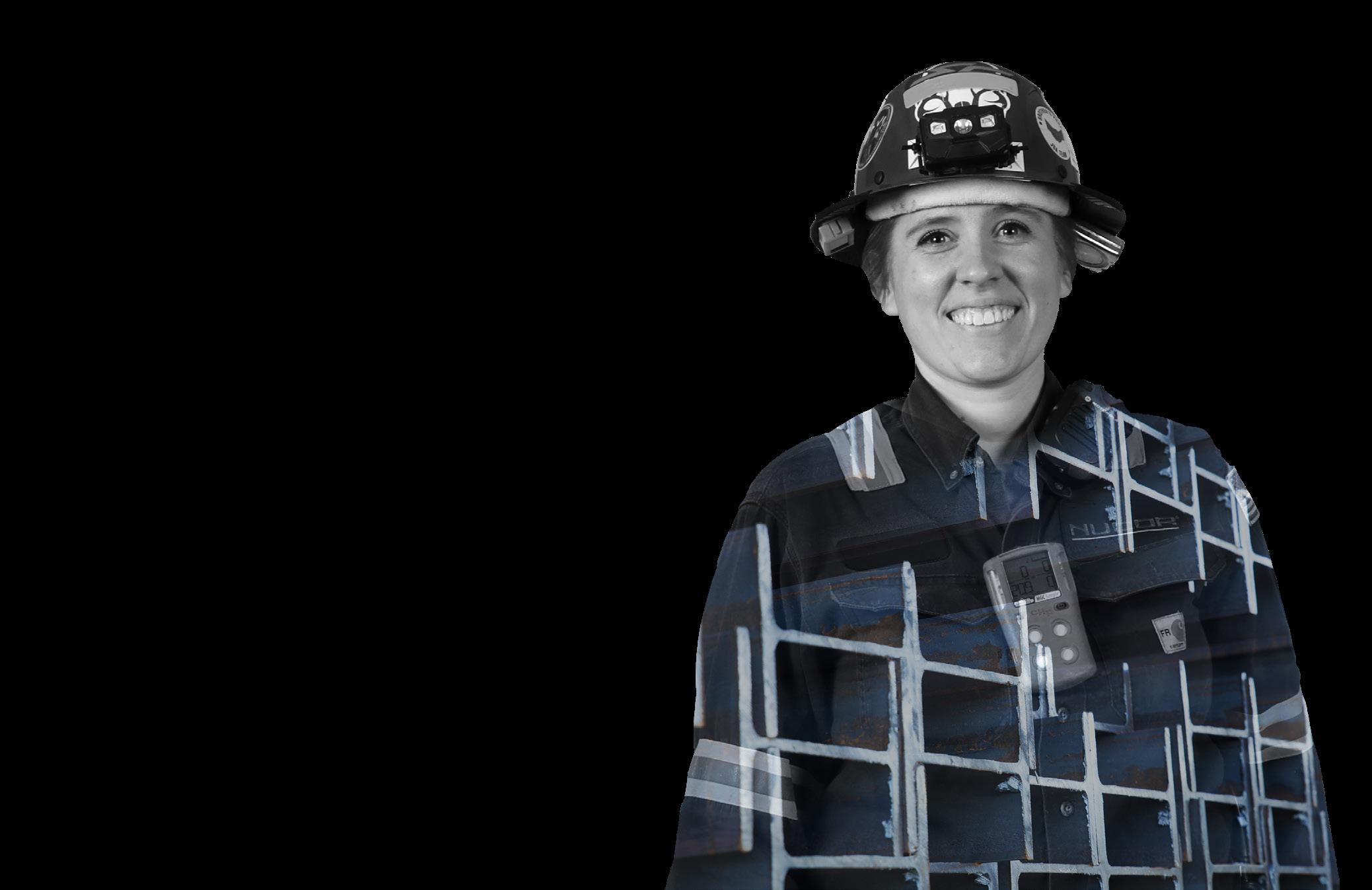
7 minute read
TRAINING DOESN’T END AT GRADUATION
from BluePrint 2023
Companies have to keep up with changing equipment, shifting regulations and rapidly expanding technology, and they need a workforce that is willing and able to consistently keep up. Blueprint talked to Scottie Smith, training manager with The Systems Group in Blytheville, to get a better sense of the training demands for that company.
BLUEPRINT: What’s the minimum skills education you prefer in new hires?
SCOTTIE SMITH: We prefer a new employee have a certificate or certification in the craft they are being hired for. However, if they are hired as a skilled helper for us and they want to learn a craft, we will train them in that craft using our internal training programs.
BP: What are some examples of internal training employees can access?
SS : All of our employees attend safety training, which we conduct throughout the year at each job site and fabrication shop. We also have a welding training program and a pipefitting training program for our employees. These programs are designed to upskill current workers or train employees who want to learn a craft but have little to no experience in them.
BP: What technical classes would you recommend a high schooler take to give them a jump on their career?
SS: We recommend students attend any type of shop class exposing them to working in an industrial craft. Students should also learn good safety habits, know how to read a tape measure and be able to add and subtract fractions.
Metal
FABRICATOR
Company: The Systems Group
Starting Salary: Up to $29/hour
WHAT DOES THE JOB DO?
Layout, fabrication and assembly of angle iron, I-beams and various other shaped metals.
Repair products by dismantling, straightening, reshaping and reassembling parts using a cutting torch and other hand tools.
WHY IT’S IMPORTANT:
Anything made out of metal was built by a metal fabricator. Metal fabricators build our world and all of the things in it.
ESSENTIAL SKILLS AND ATTRIBUTES:
Welding skills using various arc welding processes, plus the ability to read blueprints and understand weld symbols.
WHAT MAKES THIS POSITION IN HIGH DEMAND?
Metal fabrication is a demanding job requiring patience and attention to detail. There are very few high-quality fabrication training programs available.
HOW DO I LEARN MORE? www.tsg.bz
COME ONE, COME ALL
Lana Smith, HVAC student at Arkansas Northeastern College in Blytheville, is a unique sight in her classes. Smith, who works in an office role for a local HVAC company, is one of few women in her classes. But, as she’s quick to point out, she’s not the only woman here, which she takes as a sign of progress.
“In our company, we have two technicians who are male and we recently hired a new apprentice who is female,” she said. “She is in the last part of the HVAC program with me here in school, which I was very excited about. I was afraid I was going to be the only female, but there are actually two other females in my class.”
Despite making up half of the labor force, women are vastly underrepresented in skilled professions, with particularly low percentages of women among plumbers, electricians and carpenters, according to U.S. Department of Labor statistics.
However, the loss of trades workers through retirement and COVID in recent years has driven up pay and benefits to where more women are looking into skilled careers. The National Association of Women in Construction reported women represent 11% of the construction workforce, higher than the average of all skilled professions, which is closer to 8.9%.
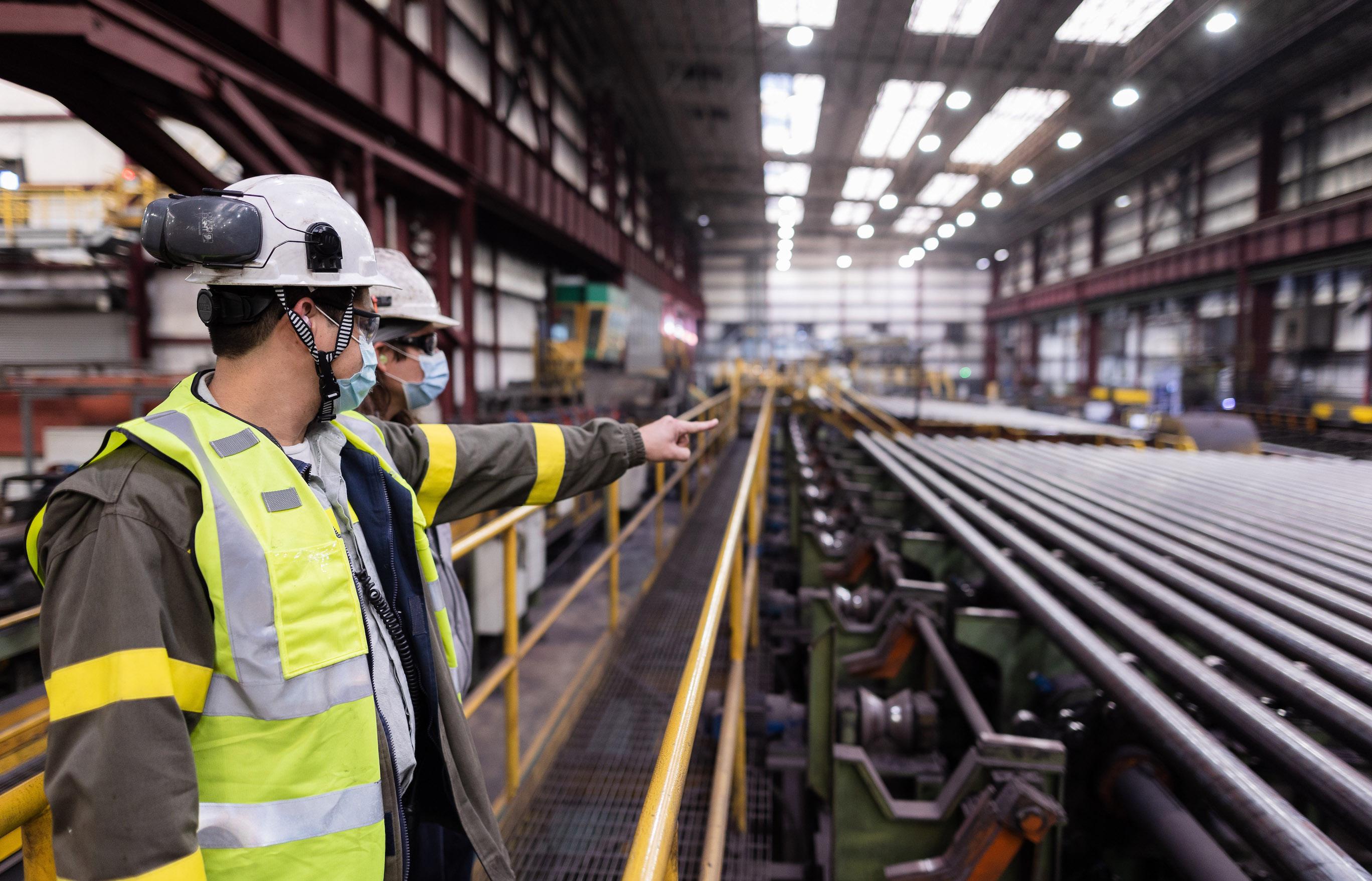
And a recent career survey by the National Kitchen & Bath Association found among high school students, the percentage of females interested in a skilled career is approaching that of their male classmates. Experts said the survey showed interest among high school girls in remodeling and renovation work is particularly strong.
Smith said more women should consider the trades as a lucrative career option, especially HVACR, which stands for heating, ventilation, air conditioning, cooling and refrigeration.
“This industry is absolutely open to females,” she said. “There are females out there who don’t see themselves sitting in an office every day. There are females who like to work with their hands and who like the challenge of having to figure out wir- ing issues. This is absolutely an industry that females can do well.”
In fact, Smith said, women often make better technicians than men in many ways. “Females make excellent HVACR technicians and installers because attention to detail is very important in our industry,” she said. “Your customer’s issue may come down to a small wire connected in the wrong place. A lot of times, I find women are much more detail-oriented than men.”
Minority trade workers outnumber women, meanwhile, but still only account for 40% of the skilled labor population. As the worker shortage drags on and companies sweeten pay and benefits, however, it’s attracting more Black and Hispanic employees looking for a rewarding job and advancement.
“I didn’t have a clear-cut direction on what I wanted to do,” said Ferriel Harvey, who has 20 years with Tenaris. “But I did look to some of my family members who had a trade. My dad worked in a mill for the majority of his life, and I really did look up to him. I know what he did and how hard he worked and how it paid the bills and took care of us.
“When I came in to Tenaris, I came in at an entry level. Now, I’m a team leader on the PMC side.”
Harvey credits the company culture not only for a source of livelihood, but for helping him grow up, take constructive criticism and bide his time for advancement opportunities. He said that development was invaluable to his long-term development and it’s what he tries to pass down to the people he manages today.
“You’ve got to take time with employees, the new hires, and talk them through things sometimes,” he said. “I understand that now, after being employed here for a few of years. This is more of a family atmosphere where you get to know people.
“I had a couple of guys take me under their wing, coached me up on the do’s and the don’ts. A lot of this plays a part in the growth that has to happen in a person if they want a career in this type of industry.”
Oran Johnson
Team Leader/Mill 6, Tenaris
Hometown: Manila
Age: 26
Years with Tenaris: 5
BLUEPRINT: What’s the length of your workday and how many hours do you put in during a typical work week?
ORAN JOHNSON: We’re working about 60 hours a week; we do five 12-hour shifts Monday through Friday. That’s pretty much year-round, 60 hours a week. A lot of my teammates have an hour drive one-way to and from work, so it can be a pretty long, demanding day.
BP: What does your day consists of as a team leader?
OJ: The team leader’s responsibilities are to manage the line itself. I’m responsible for making sure we’re producing quality pipe, making sure everybody’s being safe and following procedures. Any issues we have, I’m the guy to go try to fix those. I’m in kind of a relief position, you might say. I fill in vacancies when people take vacation or have to miss work.
BP: Sounds like you’re pretty versatile.
OJ: I have to be. I have to know how to run every piece of the process that we have here.
BP: What kind of training have you gone through over the past five years to build up that kind of skill set?
OJ: The company has training set up for us and that gets us certified for whatever job or task that we’re doing. I not only have to do that for myself, but as a team leader I have to make sure that everyone on my team gets the training they need.
BP: What’s the transition been like from a team member to a team leader? How did you learn the skills you needed to lead others?
OJ: I’d say having good leadership skills helps me out a lot as far as being respectful with my teammates. We all treat each other with respect. That and communication helps us out a lot out here. In fact, my favorite thing about my job is to sit down with my coworkers. It’s just like a family up in here. I have no issues coming to work. I love being here.
Demond Jones
General Foreman, The Systems Group
Hometown: Blytheville
Age: 46
Years with The Systems Group: 20
BLUEPRINT: Where did you start off with The Systems Group, job-wise?
DEMOND JONES: I started off as a welder and then I progressed to pipe fitter, which led to me being a lead man and then to fore man and general foreman.

BP: When did you first get interested in welding as a career?

DJ: I worked at other factories before, and my work shut down unexpectedly. My wife and my mother-in-law were looking in the paper one day and they saw “Welders Needed.” So, my wife came to me and said, “Why don’t you do this; they’re always needing welders.”
So, I decided to enroll in welding school and things took off from there. I owe all the credit to my wife and mother-in-law, though, for introducing me to the trade. And I had no idea that I would be that good at welding or I would really like it.
BP: As general foreman, how big of a crew are you responsible for?
DJ: It varies with the size of the job. With the job I have now, I’m like second in command and I’m over a lot of area. For one job I may need three guys. If it’s a bigger job, I’ll have anywhere from six to eight guys.
BP: What’s your workday like and where does your work take you, location-wise?
DJ: I’ve always had pretty much just a set schedule. It’s been 10 hours a day pretty much, five days a week. You can get overtime if you want. The hours are out there for you. I’ve worked all the different hours, but for the most part Monday through Friday, 10 hours a day.
We’re a contractor and we have a set area where we actually work out of. We’ll build everything in that area, and as they go down to where we can install it, we’ll install it. But we’ve got different areas set up at this site and we’ve got different crews in different areas.
BP: As a foreman, you get the chance to assess applicants and hire for the team. Are you generally looking just at experienced welders, or can someone hire on and learn the trade on the job?
DJ: The Systems Group is now set up where they do apprenticeships. In fact, they just finished one and those folks are being put to work now. That’s something new that the company is doing; they’re advertising now to train people to come in to get in this field.
