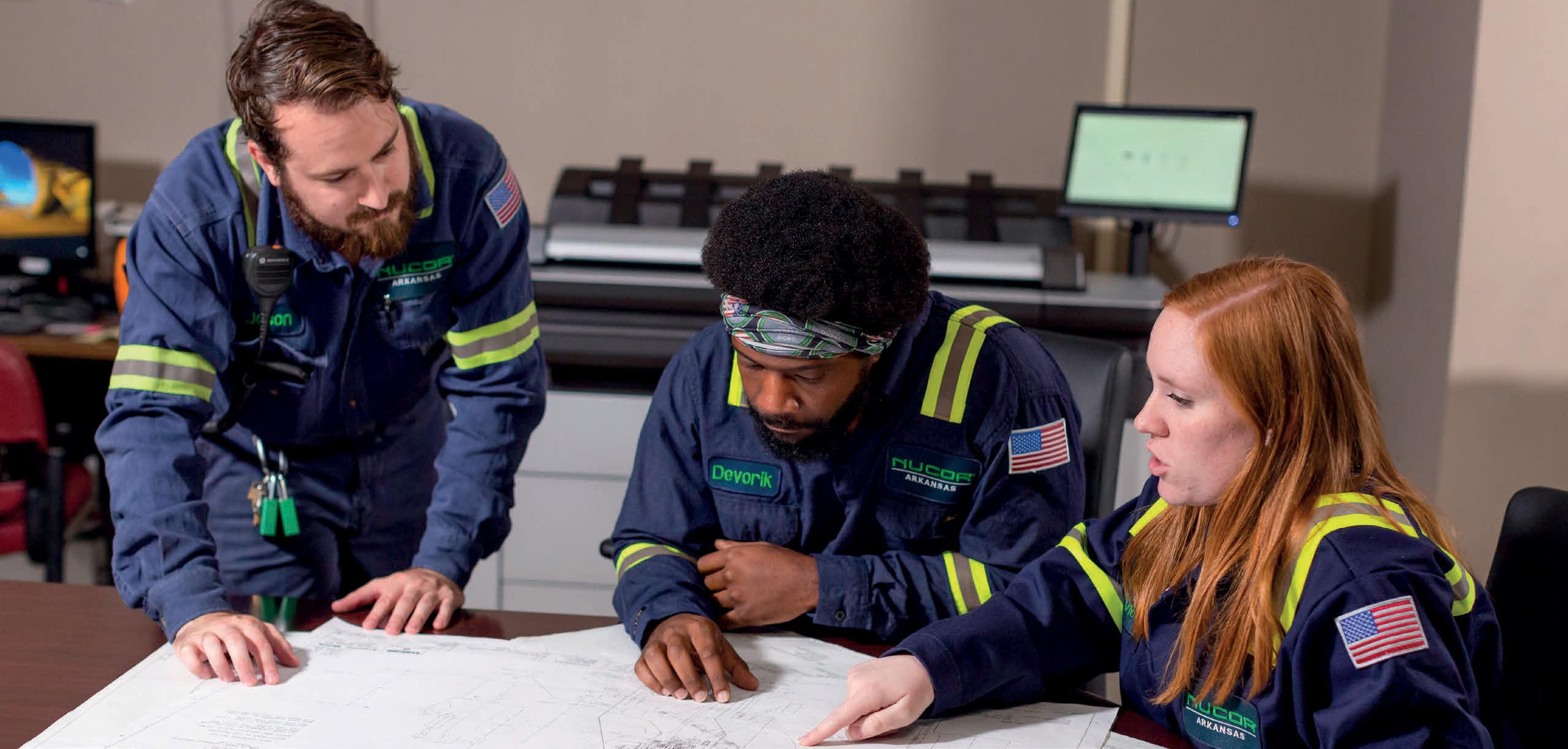
1 minute read
TECHNOLOGY FORWARD
from BluePrint 2023
TECHNOLOGISTS IN DEMAND AS COMPUTERS POWER TODAY’S STEEL MILLS, MANUFACTURING
A couple of generations ago, working in a steel mill was among the dirtiest, most physically demanding and potentially dangerous careers a person could have. But times have changed, as has the steel industry itself.
Today’s mills bear little resemblance to the fire-breathing factories of old, as computerization, robotics, artificial intelligence, and the Internet of Things help to run the show.
It’s a bold new chapter in manufacturing, demanding that employees with wide-ranging skill sets operate, troubleshoot and maintain high-tech equipment and the network backbone behind it.
Logan Nielsen, IT Leader for the Software Development team with NucorYamato Steel, has been with the company for five years.
“The software my team writes generally creates dashboards and interfaces for users to work with data,” he said. “Our customer is everyone out in the mill. I get a request every week for an application that needs to be written to display data or work with data to make the job out there easier.
“We create analytics and program a lot of reporting applications to show how well a crew is working, and if there were any issues or downtime. Probably the most fun part of my job is creating interfaces and dashboards that are easy to use as well as useful.” she said. “That could be something like an electric vehicle company needing a higher-strength steel or a thinner steel to build a new car. We can use the data we’ve collected from our mills here to design and develop new processes and new materials to meet our customers’ needs.”
Katie Behrendt, Sales Metallurgist with Nucor Steel Arkansas, said the massive amount of data captured continuously in the mill feeds even more sophisticated technology to keep the plant running at peak proficiency, right down to individual machines.
Technology is also leveraged throughout the plant to help the company maintain its strict safety standards in an environment featuring furnaces that reach almost 3,000 degrees Fahrenheit, said Damilola Balogun, Plant Metallurgist for Nucor-Yamato Steel.
“We use a lot of robots in safety,” he said. “We don’t want teammates close to the furnace while working. I don’t have to go to the front of an electric arc furnace to take temperatures, we have a robotic hand that goes into the steel, takes temperatures and comes out.”
Managing this new, highly advanced workplace requires a different set of skills than steel teammates of the past might have had, but it’s not all keyboards and coding that Nucor leadership is looking for. Soft skills, such as the ability to work as a team and the ability to communicate well, are equally critical.