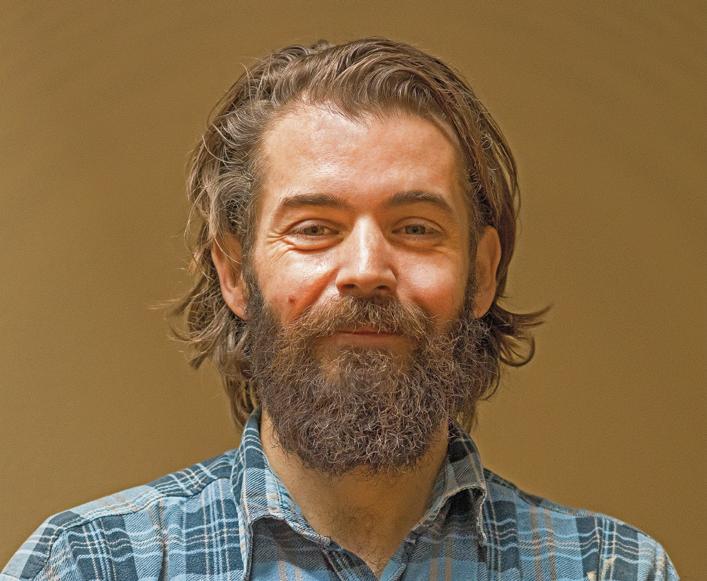
68 minute read
MASTER BUILDERS BUILDING INDUSTRY FOUNDATION OPEN FOR APPLICATIONS
Trudie Balthazaar Foundation Coordinator
The Foundation was established by Master Builders Victoria (MBV) with the aim of giving financial support to people wanting to develop their skills and careers within the building and construction industry. Since it commenced allocating scholarships in 2010, the Foundation has provided financial assistance to nearly 200 individuals completing studies to enter our industry or seeking to enhance their technical, business and leadership capabilities. The Foundation helps to build a stronger, more skilled industry by attracting more diverse talent and supporting our leaders of the future. The Foundation currently provides financial assistance to individuals through three scholarships: 1. The Early Career Scholarship – available to individuals undertaking a pre-apprenticeship, apprenticeship or further training in a construction or related field, such as plumbing, carpentry, plant machinery that supports studies as well as the purchase of equipment. 2. The Career Advancement Scholarship – for those pursuing an above Certificate 3 level or approved professional development in a construction or related field. 3. The Leadership Scholarship – supporting people with an aim to be a leader and a pioneer within the industry, including those undertaking tertiary studies and research trips, domestic and overseas. The scholarships are available to those studying an approved course provided by TAFEs, RTOs, and universities. The Foundation Board assesses all applications received and awards the scholarships on merit and need. In addition, the Foundation provides bursaries and prize money to support other agencies that have a similar purpose of building capabilities within the building and construction industry. For the financial year 2020/21 the Foundation awarded 25 scholarships to the value of $115,485. In addition, the Foundation provided a $3,000 prize for the State Apprentice of the Year Awards. As an independent registered charity, the Foundation relies on donations to be able to achieve its overall vision of ‘building tomorrow’s leaders – today’. In 2021/2022 the Foundation will embark on a broad marketing and promotion campaign to encourage more industry partners and members to make taxdeductible contributions and expand the reach of the Foundation. For more information on The Foundation, contact Foundation Coordinator Trudie Balthazaar on (03) 9411 4555.
“Without these funds I simply would not have been able to undertake the course given the financial hardships from COVID. It gave me the confidence I needed to pursue this career. The validation I felt to be a recipient of the Foundation was a real boost and gave me the final push I needed.” Luke Apswoude – recipient of the Building Industry Foundation Career Advancement Scholarship in 2020/21. “The knowledge I have gained through the course (which the scholarship paid for) has enriched my knowledge of the domestic building industry and prepared me for my upcoming DBU computerbased test; and the following interview and VMIA requirements. Obtaining my DBU licence will enable me to take my career to the next level. Quite often financial constraints prevent people from being able to access the resources they need to progress their career. If this burden is minimised or eliminated, the individual can allocate more of their own finances towards other things that could help them build their business. I would recommend the Foundation to those who are serious about expanding their qualifications and doing something with them to consider applying for the Master Builders Foundation scholarship.” Jarred Laukart – recipient of the Building Industry Foundation Career Advancement Scholarship in 2020/21.
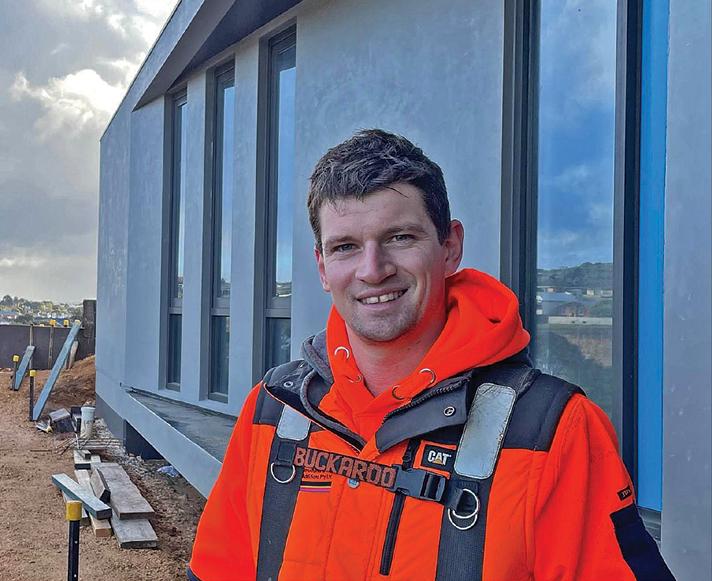
Master Builders Victoria in the news
Over the past three months, MBV has proactively engaged the media to publicly communicate our position across a range of issues, enhancing our reputation as the leading industry voice. MBV CEO Rebecca Casson was especially vocal on the supply chain issues affecting the industry and the need for more financial support during circuit-breaker lockdowns. Ms Casson appeared in more than 30 radio, television, print and online interviews that built government and consumer confidence in our industry’s robust health and safety practices. This helped to keep our sector open for business, and to advocate for stimulus measures to boost building and construction and Victoria’s economic recovery. Please find enclosed a small sample of our recent activity in the media.

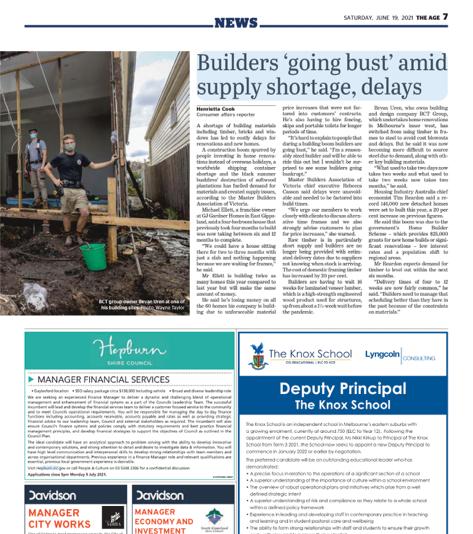

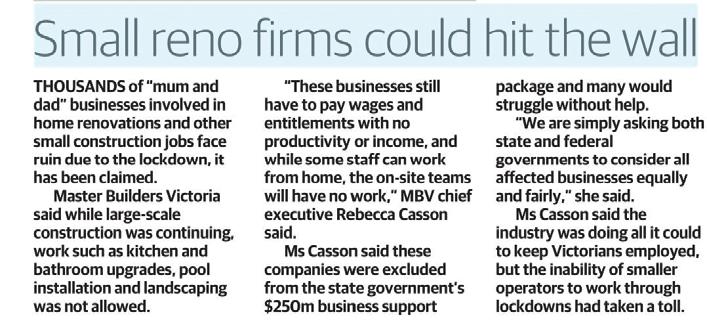
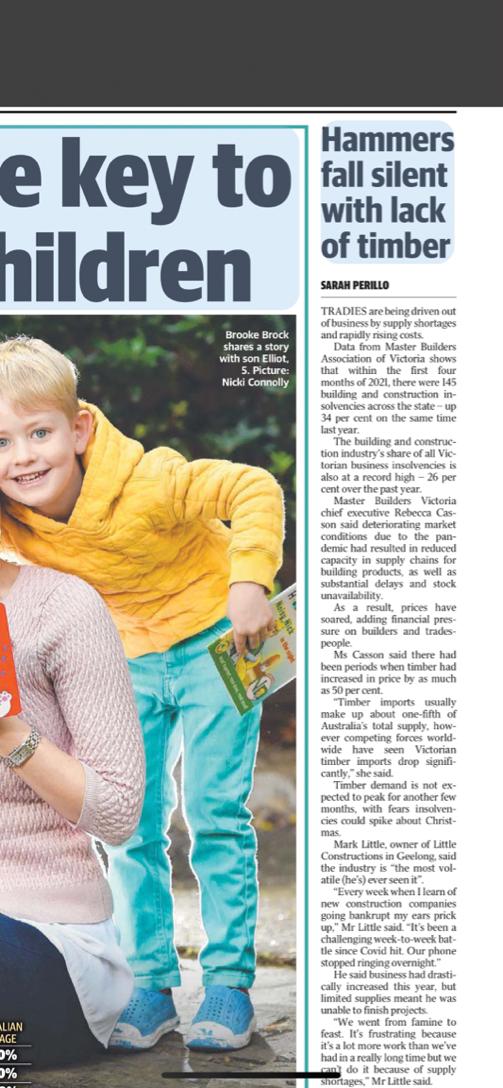
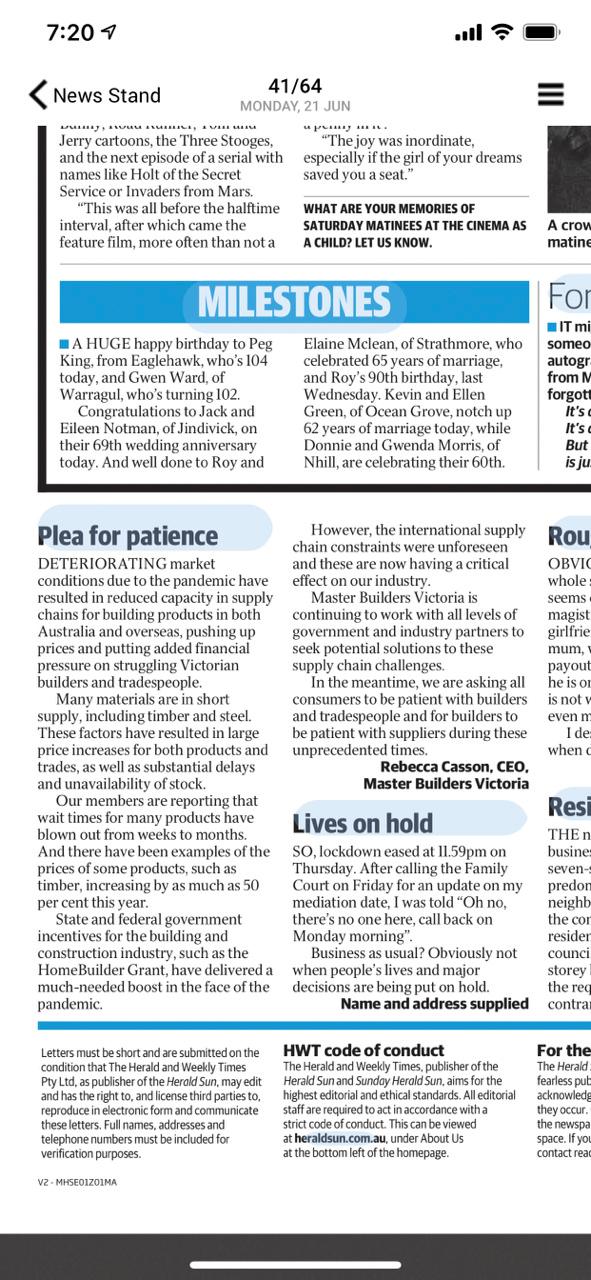

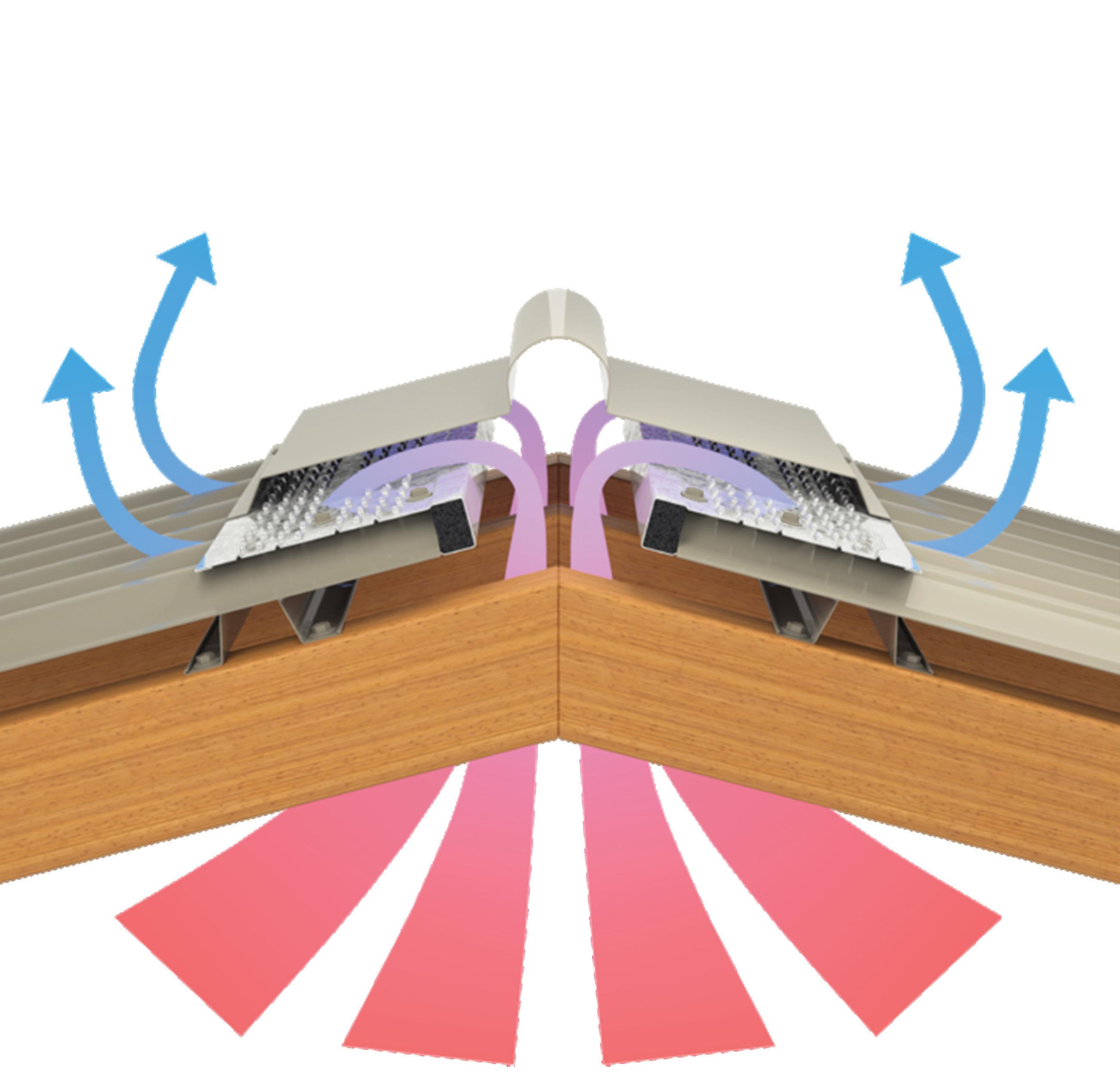

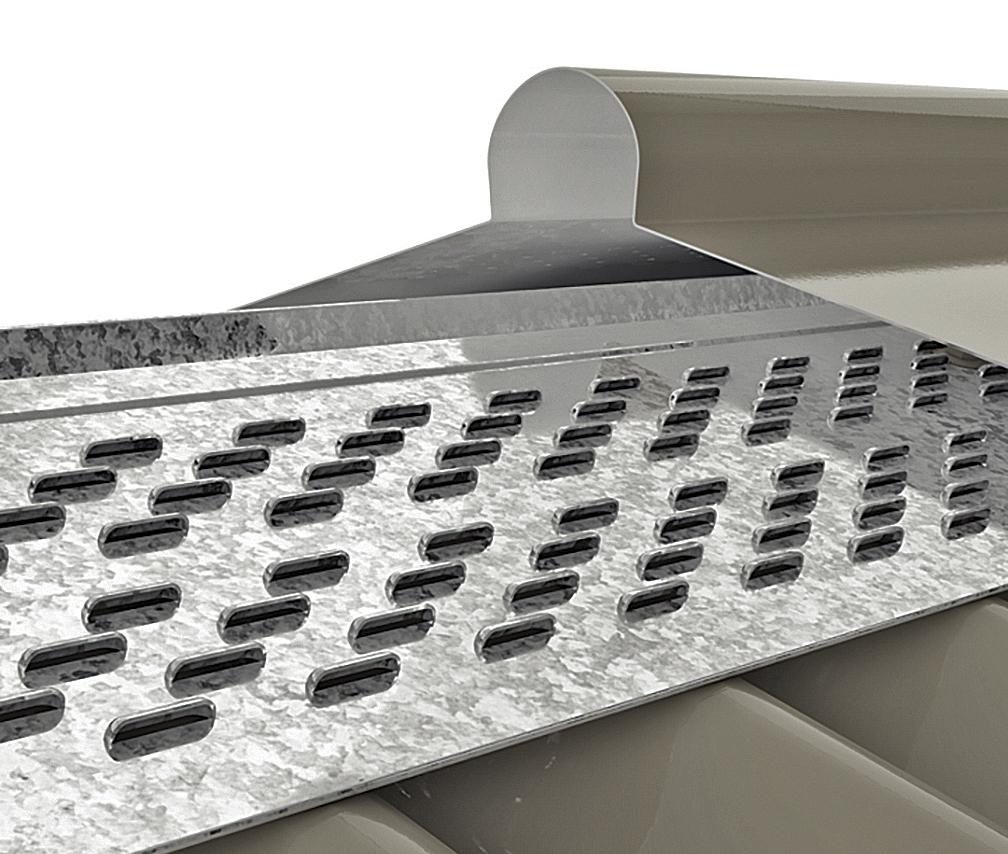
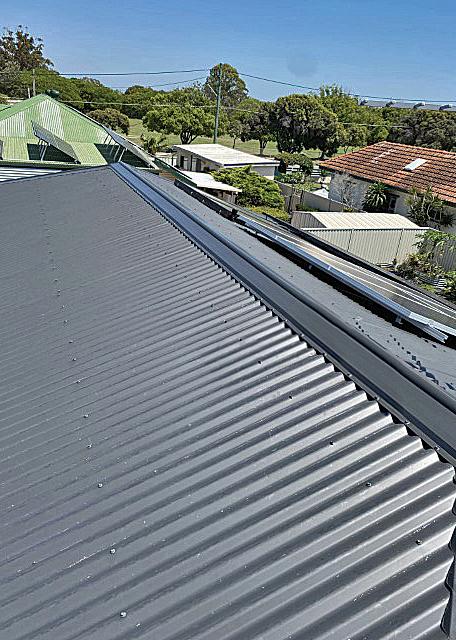
LEFT: VENT-A-ROOF® is manufactured from Australianmade COLORBOND® and ZINCALUME® steel; ABOVE: The VENT-A-ROOF® system is installed under traditional ridges, hips and barges.
VENT-A-ROOF® from Lysaght – easy installation and no moving parts
There’s no doubting the benefits of roof ventilation, especially in a country like Australia with our extremely hot summers, and in some states, year-round heat. Just a few days of moderate to high temperatures can result in heat build-up, and that becomes trapped in the roof cavity as the sun beats down, while warm air from inside the house also rises. Turning on the aircon is usually the first course of action when the temperature rises, but it’s not the best one. Running air conditioning for long periods isn’t cheap, and with ducted systems – which are often routed through ceiling spaces – efficiency is lost because the cool air moving through the ducting ends up cooling the ceiling cavity rather than just the living spaces. Good ventilation is also needed in the cooler months when humid air can get caught in roof cavities – if there’s no escape, it gradually turns to liquid clinging to timber trusses and moistening insulation and plaster, which can lead to damage. What if there was an easy-to-install system that could help to cool roof cavities leading to a cooler building in summer, while also providing airflow during lower temperatures to minimise condensation? It would be even better if it was a ‘passive’ solution, that didn’t need energy to do the job. VENT-A-ROOF® is a concealed roof ventilation system that uses the power of natural airflow to ventilate residential, commercial and light industrial buildings with metal rooves. It’s installed under traditional ridges, hips and barges, making it extremely versatile while not leaving rooflines with ugly bolt-on systems. And because VENT-A-ROOF® has no moving parts, it’s completely silent. “VENT-A-ROOF® uses the same principles as other natural ventilation systems. As the roof space heats, hot air is drawn towards the highest natural point and expelled through the VENT-A-ROOF® integrated louvre and down the pan creating a passive, natural and continuous flow of air,” Lysaght National Specification Manager, Tony Jamieson, explained. “At the same time, any positive airflow across the ridge of the roof creates a negative pressure which pulls air out from the ridge vent and brings in fresh air from intake vents in the eves or below. Basically the two thermal effects create a continuous flow of air, allowing cool air into the roof space and extracting hot air.” According to Tony, another benefit for building owners – and installers – is that the two piece VENT-A-ROOF® system is cost effective to install and much easier to fit than comparable ventilation system, plus needs little to no maintenance. “Installers will really appreciate the fact that unlike products such as wind-driven rotary ventilation systems, VENT-A-ROOF® doesn’t need any penetrations of the roof – this avoids leaks, maintenance issues and call-backs. It also means a faster install because there’s no need for flashings,” he said. As with all Lysaght products, builders and installers can rest easy knowing that VENT-A-ROOF® has been developed for demanding Australian conditions and extensively tested here. The system is BAL and Cyclone-rated, meets ‘Form 15’ compliance and is compliant with 2019 NCC ventilation requirements. Available in all COLORBOND® steel colours VENT-AROOF® is available nationally from all Lysaght branches or visit lysaght.com/vent-a-roof
Understanding safety obligations
Andrew Jefferson Editor
Master Builders has launched My Safety Essentials, a comprehensive, interactive educational resource, in conjunction with WorkSafe Victoria. Funded by WorkSafe Victoria, My Safety Essentials provides a complete learning resource to support builders, employers and building trades (end-users) within the residential construction sector. This comprehensive online resource helps domestic builders understand their key legal OHS obligations through all the critical construction phases. It will provide an educational experience for builders to identify and manage the critical risks presented throughout a domestic building project. The learning experience is enhanced through a diverse range of mediums, including videos, virtual reality applications, forms, case studies, quizzes, and photography. My Safety Essentials is hosted on a webpage within the Master Builders Victoria website at www.mbav.com.au and is available free of charge to all builders within the residential construction sector. Master Builders of Victoria OHS manager Sam Smith said the project is important because the construction industry is a high-risk industry. “Our industry is heavily regulated; however, the construction industry records a high number of fatalities and serious incidents each year,” Mr Smith said. Mr Smith said small business is the backbone of the Australian economy and the building and construction industry. But statistics highlight that the domestic sector records many serious incidents and fatalities compared to the commercial construction industry. “Small businesses often don’t have the time or resources to understand the whole OHS landscape in which they operate,” he said. “Consequently, they need access to practical, easily accessible and understood solutions to ensure they always create and maintain a safe working environment for themselves and all those around them. “The safety of workers in our industry and our industry’s reputation regarding its steadfast commitment to the health and safety of all workers, subcontractors, and the community is a top priority for Master Builders Victoria. “Everyone fittingly owes a duty under the OHS legislation – My Safety Essentials ensures everyone in the domestic construction industry can now be fully informed and equipped to meet their OHS obligations.” For more information, phone Sam Smith on (03) 9411 4555.
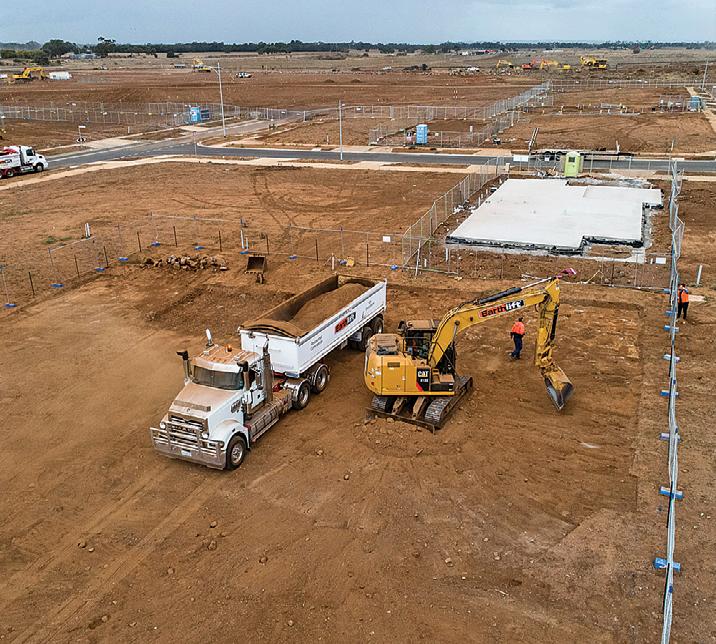

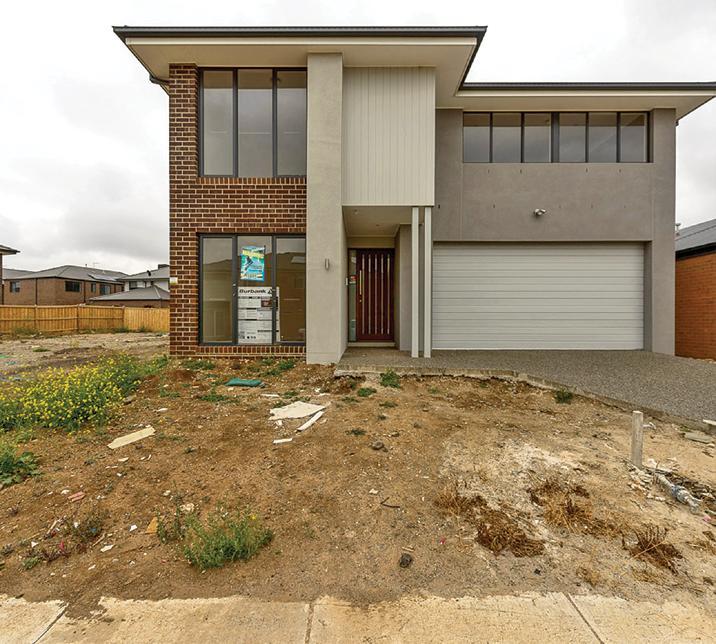

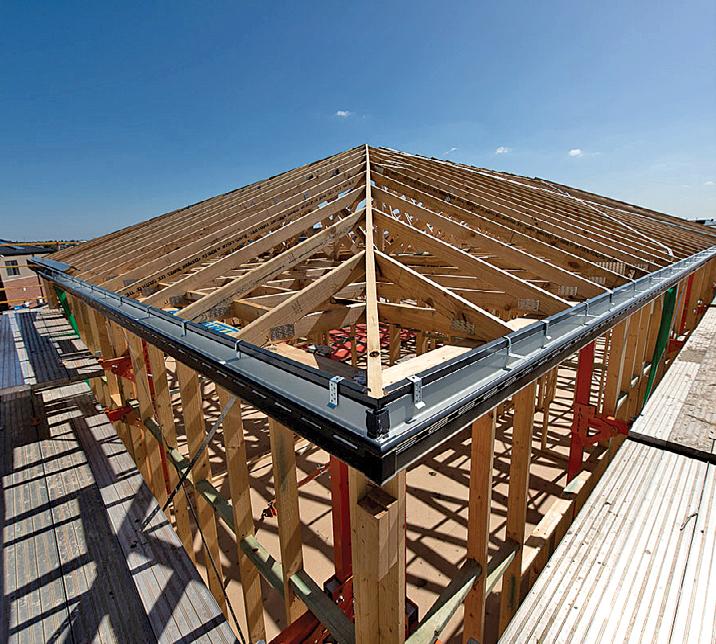
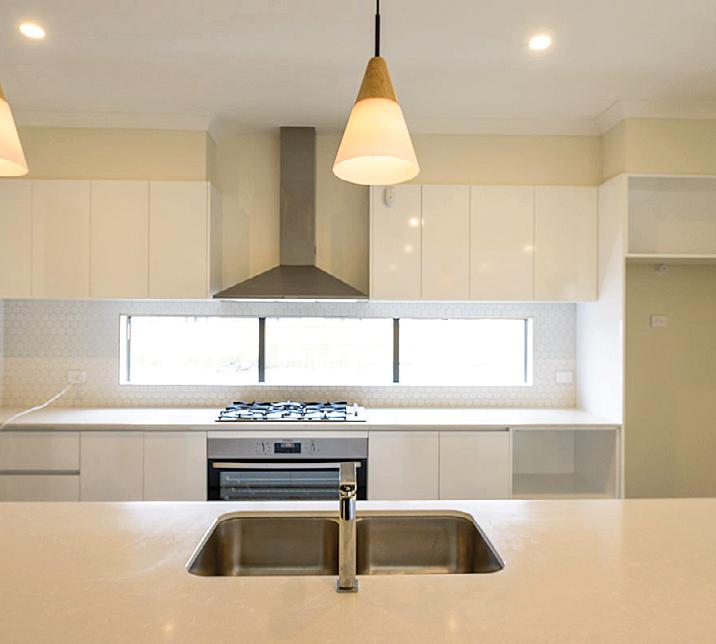

Master Minds – the case for prevention led approaches to mental health in the building and construction industry
Adrian Panozzo
To see what is possible in the future, look back into the past and see how much has changed.
From Smokescreen to Systems Change
During the last century, cigarette companies sought to market menthol cigarettes as healthier than nonmenthol cigarettes, and even claimed that by smoking them you could protect yourself from colds. Such was the misperception in relation to smoking that arguably the greatest cyclist of all-time Eddy Merckx was reported to say that: “I liked to smoke a cigarette, even during the Tour de France. It calmed my nerves”. I’m sure that for most of you reading this now, such beliefs seem unbelievable. So why (or how) have attitudes to smoking changed so much? Decades of advocacy, education and awareness campaigns have seen smoking rates among Australian men reduce from more than 70 per cent in 1945 to 30 per cent in 1989. In fact, so effective have recent prevention initiatives been that the smoking rates of Australian men and women aged 18 plus have more than halved over the past 30 years and are now as low as 13 per cent. Knowing this should give us optimism and hope in terms of our ability to improve the ways in which we can create and manage mentally healthy workplaces in the building and construction industry and prevent mental injury to workers. A sensible place to start is to leverage the important work done over the past 10-20 years by organisations that have developed and are delivering awareness and support programs for mental health in the workplace. We can use their experience and learnings to increase the focus on and investment in prevention-led approaches to mental health at both the systems and business level in the building and construction industry.
Governments and regulators could incentivise employers that develop and implement prevention focused mental health programs by giving them priority access to work, reduced insurance premiums and providing them with grants to further develop and measure the effectiveness of their efforts. To ensure the integrity of any incentives, evidencebased practice that highlights prevention approaches should be developed as a core component of building and construction industry training, certification and capability frameworks. Specific topics aimed at companies, business owners, supervisors and apprentices to support mentally healthy workplaces could include mental health literacy, leading prevention-led mental health strategies and managing and re-designing job demands. Another opportunity to drive the change and improvement in the mental health of workers in the building and construction industry are communities of practice led by peak bodies and professional associations in order to develop robust, practiced and skilled practitioners that are able to provide real-world support and advice to industry leaders and businesses that address the common organisational, environmental and individual factors that contribute to work related stress from a prevention perspective.
What do you do?
When you meet someone for the first time – how often are you asked: “What do you do?” Having a job can and should be something that adds value and meaning to your life. The sense of purpose and community contribution linked to employment can provide you with a positive sense of self, economic independence and social connection. However, this is where we encounter our first challenge in relation to positive mental health in the building and construction industry. Stigma and a lack of understanding or appreciation for the diversity of roles, career opportunities, job satisfaction and even financial security can make working in the industry seem undesirable, and those that work in it typecast and maligned. How we talk about the building industry presents as one opportunity to mitigate mental health issues before they emerge. The building industry would not be the first to develop an integrated marketing and communications campaign in order to improve its image in order to retain and attract suitable and diverse workers.
Men, Mental Health, and the Building Industry
As the issue of mental health in the building and construction industry becomes more understood, there are some key learnings that should encourage us to consider a greater focus on prevention led approaches to mental health. These include:
It is an industry with higher than average workrelated stress
There is growing evidence that workers at all levels in the building and construction industry report higher levels of work-related stress than most other industries and occupations.
It is a male dominated industry
While there are concerted efforts to make the industry more inclusive, most roles and trades are still dominated by men, and women remain underrepresented in senior and more technical roles.
Barriers to accessing help
Stigma, cost and wait times are just some of the barriers that result in a majority of men not actively seeking mental health support.
A Pathway to Prevention?
As it currently stands, the construction industry is made up of occupations that are likely to cause above average levels of work-related stress to workers that are unlikely to seek help. This strengthens the case for more support for prevention-led approaches to preventing mental injury in the building and construction industry. Proposing an increased focus and investment in prevent-led initiatives should not come at the cost of reducing resources for support, treatment and recovery programs. These resources, in the form of campaigns, clinical interventions and workplace initiatives are fundamental elements of an integrated approach to creating mentally healthy workplaces. It is important that we see more practical examples and case studies of prevention led approaches to mental health in the building and construction industry. Examples of this could include: • Businesses are able to describe their efforts to manage and improve the mental health of their workplaces and workers in their Capability
Statements. • Business owners and supervisors develop a social and economic understanding of the benefits of creating a mentally healthy workplace and preventing mental injury of their workers. • Business owners and supervisors develop leadership skills and model the behaviours conducive to creating mentally healthy workplaces and preventing mental injury to their workers. • Work is planned in a way that acknowledges and identifies how it will reduce specific organisational and environmental factors that are likely to cause
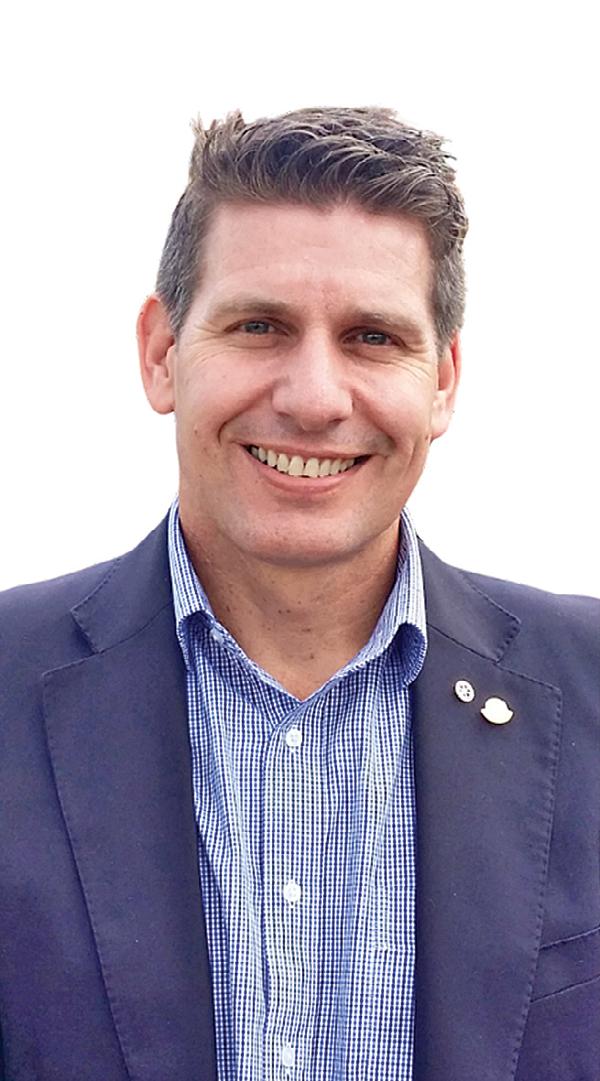
Adrian Panozzo
Adrian has spent over 30 years developing social impact programs for businesses, and individuals and communities experiencing disadvantage. He was awarded a Churchill Fellowship for his work in the areas of homelessness, mental health and addiction, and is the co-Founder of Better Life Mobile a telecommunications company that has been recognised globally for its innovative and ethical approaches to social and digital inclusion. Adrian’s interest in the building and construction industry relates to supporting leaders and organisations to create mentally healthy workplaces through the implementation of prevention focused workplace mental health initiatives. LinkedIn - https://www.linkedin.com/in/ adrian-panozzo-7023267/
work-related stress. • Businesses develop an annual program of integrated activities that contribute to the positive mental health of their managers and workers. • Businesses actively participate in communities of practice and seek out research opportunities that measure the effectiveness of their prevention led approaches to creating a mentally healthy workplace.
Compliance made easy
Pre-qualification of ACRS steel makes compliance with AS/ NZS Standards easy

The significant growth in major infrastructure and construction projects which has occurred over the past 18 months – together with the associated growth in demand for construction materials – have also resulted in an increased chance of inferior products and materials finding their way onto construction sites in place of materials which conform with the relevant Australian and New Zealand Standards. As such, matters relating to product conformity and certification of construction materials such as structural and reinforcing steels to Australian and New Zealand Standards is perhaps now more important than ever before. Ensuring that the construction steels being used throughout all stages of construction or fabrication conform with all relevant Australian and New Zealand Standards and Building Codes - irrespective of their country of origin - is of paramount importance. After all, these Standards have been considered and developed to ensure that buildings and other structures are not only ‘fit for purpose’, but are also capable of meeting their design life requirements. Unfortunately, in this day and age, it’s simply not enough to think that just because steel has been ordered to an Australian or New Zealand Standard that the delivered product will automatically conform with that Standard and be fit for purpose. Increasingly, this is not the case. In fact, there are some instances where even though the materials have been specified and ordered to an Australian Standard, the materials that arrive are non-conforming. The product may meet the Standard; it may be supplied with documents for “an equivalent Standard” (but which Standard and is it really equivalent?) or it may not meet any Standard at all. Importantly, whether this non-conformance is an intentional act of deception or ‘counterfeiting’ on behalf of the materials supplier, the builder or the contractor; or simply a matter of non-conformance through lack of correct process or an innocent misunderstanding of what constitutes conformance with Australian Standards, is effectively a moot point. Using non-conforming building materials carries a high risk of ‘built-in’ failure - and the results can be disastrous.

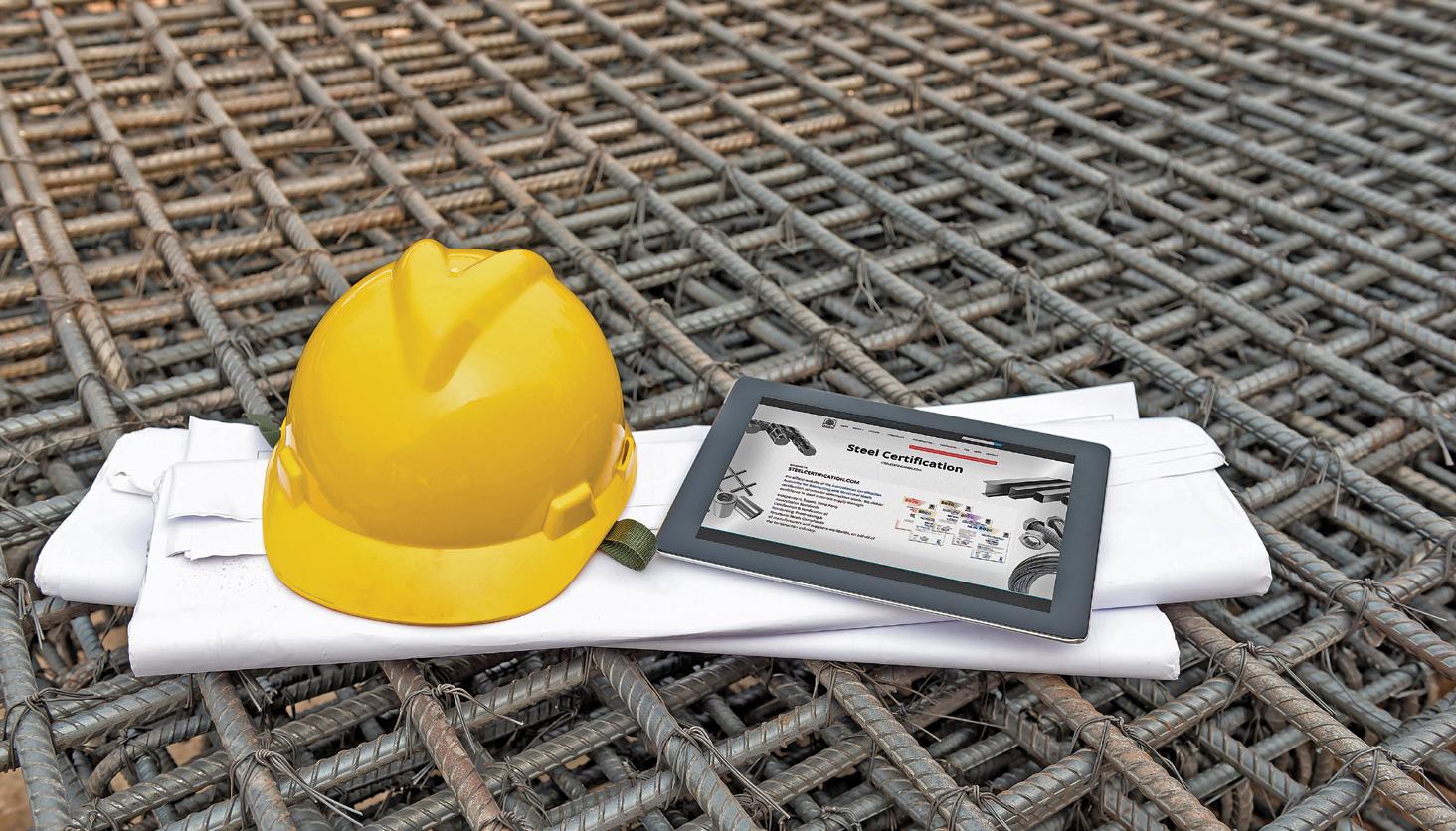
INDEPENDENT, EXPERT, THIRD-PARTY CERTIFICATION
The only way to be truly sure that the materials being used conform fully with the appropriate Australian and New Zealand Standards and are fit for purpose, is through independent, expert third party certification with ongoing validation. ACRS provides a fully independent, expert assessment and certification to AS/NZS Standards for both Australian and internationally sourced construction steels, including reinforcing steels, structural steels and prestressing steels. ACRS steel is pre-qualified. The manufacturers and processors have already demonstrated compliance with the relevant Australian and New Zealand Standards. By using ACRS certified construction steels, builders and contractors can be confident that they are getting the AS/NZS compliant materials that they ordered, and engineers and building certifiers can be confident that the steel meets the requirements of the Building Codes and associated Standards and is fully traceable from the point of manufacture to the point of delivery. All ACRS certification personnel are fully-qualified metallurgists and engineers with many years of direct experience in manufacture, processing, or design and construction of the steel materials it certifies. In addition to factory production control audits and independent testing, the ACRS scheme provides regular review and analysis of all products manufactured and supplied by the certified supplier. All testing is observed and verified by independent NATA test laboratories, and all processes, including the use of traceability tags, are audited. The ACRS scheme operates as a verification-based system modelled on international best-practice standards. Where some certification systems might accept the suppliers’ own quality management systems certification and test reporting without further checking, ACRS doesn’t. ACRS assessors independently select the samples for testing during the audit to prevent any chance of “cherry picking” by the supplier. It then manages the subsequent verification process though independent qualified laboratories selected by ACRS, not the supplier. The process is further bolstered by ACRS conformity checking on the suppliers’ raw production data, which is undertaken every three months. ACRS certification makes checking for compliance with the relevant Australian and New Zealand Standards easy. It demonstrates INDEPENDENTLY and EXPERTLY that the supplier consistently meets the Standards stated on the certificate. The bottom line... with ACRS it’s easy for your suppliers, easy for your customers and easy for you! For further information please email ACRS at: info@ steelcertification.com or visit the website www.steelcertification.com
Environmental Protection Amendment Act 2018
Dr Phillip Alviano Sustainability Advisor
The Victorian Government has introduced the most significant reform to Victoria’s environment protection laws and regulations in the 50 years of the Victorian Environment Protection Authority (EPA). The Environmental Protection Amendment Act 2018 (the Act), which amends the Environment Protection Act 2017 commenced on 1 July 2021. It focuses on establishing a more preventative and risk-based approach toward environmental protection. The Bill will also introduce increased penalties and enforcement against those who cause environmental harm. The legislation introduces the new general environmental duty to minimise the risk of harm to health or the environment. The general duty requires that “reasonably practicable” steps must be taken to prevent harm from pollution and waste. The government has introduced criminal or civil penalties for failure to observe the duty. Much like the Building Act, the full impact of the legislation depends on the regulations that support it. Statutory measures in the legislation such as ‘proportionality’ and ‘reasonably practicable’ are discretionary terms and will need clarification as the legislation becomes operational. It is highly likely that Codes of Compliance will be developed for different sectors. Several guides referenced later in this document provide some guidance in these areas.
General environmental duty
Central to the Bill is the General Environmental Duty (GED) which will require people to have a reasonable knowledge about the risks your activities pose to the environment. You will need to undertake reasonably practicable steps to eliminate or, if elimination is not possible, minimise pollution or waste deemed harmful to human health. This allows for a more preventative, rather than reactive approach to environmental protection. This changes the focus from punishment for causing pollution to requiring reasonable steps to be put in place to eliminate or reduce the risk. Unlike other states and territories with similar laws, any breach of the GED could lead to criminal or civil penalties.
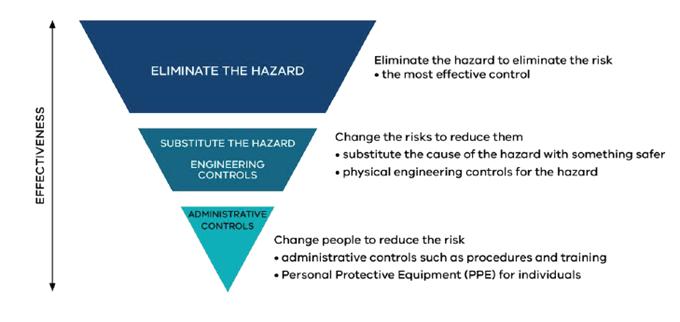
Source: Environment Protection Authority (2020), Reasonably Practicable, Publication 1856.
Reasonable practicable
Reasonably practicable means putting in controls that are proportionate to the risk in order to mitigate or reduce the risk of harm to the environment. Being proportionate means the greater the risk of harm, the greater the expectation for you to manage it. You do this by demonstrating that you have considered and implemented the most suitable controls that are available to eliminate or minimise the harm. Controls that eliminate or substitute the source of the risk are the most effective. If this is not possible then use engineering or building controls, training and site practices to reduce the risk as much as possible. Often a combination of all these controls will be needed. When you are dealing with a common risk or harm, you can show that you have implemented actions that are reasonably practicable if: • you have adopted well established effective practices or controls to eliminate or manage risk; and/or • where well established practices or controls do not exist, you show you have assessed and adopted effective controls. This may be recorded as part of your Environmental Management Plan (EMP). The Master Builders Green Card Training provides a basic environmental induction that explains the environmental impacts of building and construction and makes it clear what their obligations on site are in terms of managing those impacts. It also includes a spill kit demonstration.
In Practice
If you already have an Environmental Management System in place, then you should already have procedures and plans in place. Otherwise for larger sites and projects this generally means the production of an EMP. The management plan will include an identification of areas of risk and a documented plan to eliminate or control that risk. Risks to consider will depend on the site but will most commonly include discharges to stormwater or
Building Site Examples
Identify Hazard Assess Risk Implement Controls
Eliminate Manage Check Controls
Sediment discharge High Retain vegetation, prevent vehicle movement onsite
Fuel/Chemical spills Low Do not store onsite or minimise Sediment control fencing, rumble grid, protect stormwater points, training,
Store in bunded areas, spill kits, training Monitor daily, check protection in place, Monitor storage, spill kit access
waterways, litter, dust, noise or chemicals. Other less common aspects may include significant trees or vegetation and animals. For smaller sites developing a simple environmental policy may be enough to address your risk. This might consist of a number of statements including: • Stormwater drains on site will be identified and marked • Contractors will be instructed to use bins provided for all litter • All materials will be stored onsite • Vehicles not to enter when site is wet • No tools or equipment to be washed where water can run off site • Any sediment, mud, screenings, sand to be removed from footpaths, crossovers, or roads immediately. It may be an idea to include the above conditions in your contracts and on signage around the site. The Environmental Protection Authority (EPA) has several guides that can help guide you through this process and develop an EMP. These include: • Publication No. 1820 – Construction: Guide to preventing harm to people and the environment • Publication No. 1834 - Civil construction, building and demolition guide • Publication No. 1695.1 - Assessing and controlling risk for business • Publication No. 480 - Environmental Guidelines for
Major Construction Sites
Waste Management and Contaminated land
Incorrect waste disposal is now a criminal offence. Everybody in the chain must understand the nature of waste and the appropriate transfer and disposal methods. This means having a record of the disposal facility and confirmation that it was delivered to the correct facility. Below are the waste categories:
Reportable Priority Waste
• Includes Category A, B, C and D (that contain asbestos) contaminated soils. The EPA needs to be notified and this needs to be disposed of as per current practices. This must be only sent to a facility that is authorised to accept the waste and tracked using the EPA waste transfer certificates and system.
Priority Waste
• This includes for example e-waste, building rubble, bricks, timber, etc. Notification of EPA is not required but need to track and dispose of it lawfully. Keep records of who transferred it and where it was sent.
Industrial waste
• This includes soil for fill or surplus soil that potentially could be reused, for example in landscaping. • Clean fill material can be disposed of with an agreement in writing between generator and receiver. This is material that is chemically inert. • Don’t need to notify the EPA. • Keep records of your assessments, agreements, transfer and place of disposal. More detailed information on this can be found in EPA Publication No. 1834 - Civil construction, building and demolition guide.
Conclusion
The Environmental Protection Amendment Act 2018 (the Act) came into effect on July 1st 2021. Source: Environment Protection Authority (2020), Civil construction, building and demolition guide, Publication 1834.
It aims to enable more effective investigation, enforcement and compliance. The Act has new compliance and enforcement measures for the EPA including: • Modernising, clarifying, and strengthening the powers for EPA Officers to enter premises and investigate breaches of the law. • Improving the investigation capability of the EPA. • Higher penalties for obstructing, assaulting or impersonating an EPA Authorised Officer. Penalties have been increased and sanctions strengthened. The proposed Bill would increase penalties for environmental offences. Breaching the GED would attract a penalty of up to $317,000 for an individual or $1.6 million for a corporation. Intentional or reckless breach of the GED that results in material harm will attract a penalty of up to $635,000 and/or five years imprisonment for an individual, or $3.2 million for a corporation. The illegal dumping of industrial waste will also attract penalties like the level associated with breaches of the GED.
References and Further Information
Australian Environment Business Network Webinars: https://aebn.com.au/aebn-events/event/trainingwebinars-on-the-new-victorian-environmentalprotection-laws/ Environment Protection Authority (2020), Reasonably Practicable, Publication 1856, State of Victoria. Environment Protection Authority (2020), Construction: Guide to preventing harm to people and the environment, Publication No. 1820, State of Victoria Environment Protection Authority (2020), Civil construction, building and demolition guide, Publication No. 1834, State of Victoria Environment Protection Authority (2020), Environmental Guidelines for Major Construction Sites, Publication No. 480, State of Victoria Environment Protection Authority (2018), Assessing and controlling risk for business, Publication No. 1695.1, State of Victoria Environment Protection Authority Webinar: https:// www.epa.vic.gov.au/for-community/get-involved/ past-events/victorias-new-environment-protectionlaws-update Norton Rose Fulbright (2021), Contaminated Land Reform in Victoria, 33217_AU – 05/21
TOYOTA FOR BUSINESS
Lead with elegance and flexibility in your business
Grande Hybrid model shown.
* Discount available across the Toyota Kluger range. T&Cs apply. 1 Driver assist feature. Only operates under certain conditions. Check your Owner’s Manual for explanation of limitations. Please drive safely. 2 CarPlay® is a trademark of Apple, Inc. registered in the U.S and other countries. Functionality varies depending on device. See www.toyota.com.au/connected/infotainment/apple-carplay-android-auto for compatibility. Available on certain models and grades only. 3 Android Auto™ is a trademark of Google LLC. Functionality varies depending on device. See www. toyota.com.au/connected/infotainment/apple-carplay-android-auto for compatibility. Available on certain models and grades only.
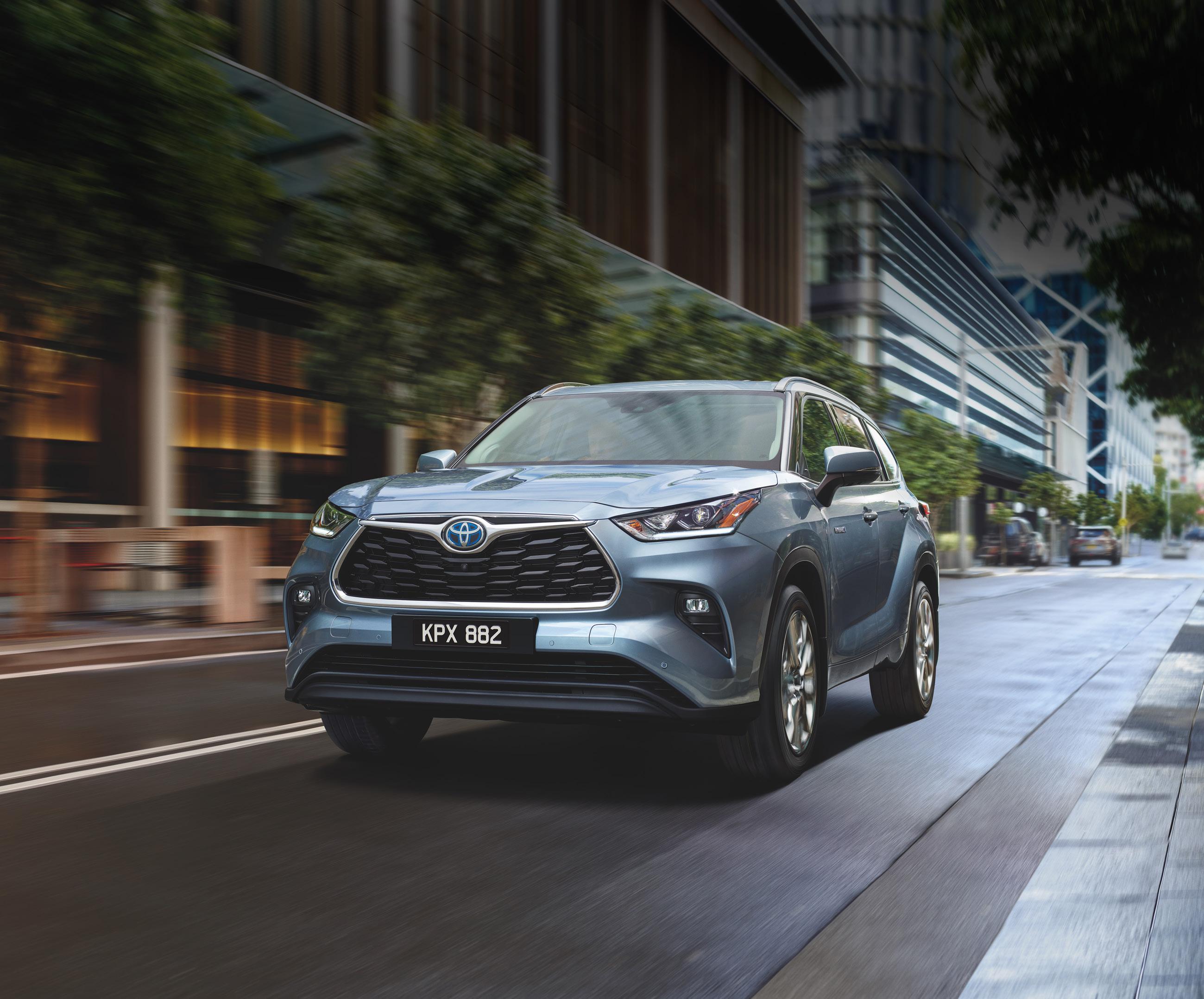
Save $3,900* on the All-New Kluger range with your Gold Fleet Discount
Take advantage of your Gold Fleet saving of $3,900* on the All-New Kluger, enhancing your business with style and ample cargo space to handle whatever the work day throws at you. Intelligent road monitoring scans your surroundings using our latest Toyota Safety Sense features1, while connecting your commute to an 8” touchscreen system featuring Apple CarPlay®2 and Android Auto™3 .
Outside, an impressively elegant and professional exterior gives way to the spacious cabin. The All-New Kluger’s flexible 7-seat configuration allows you to pack it all in, effortlessly reshaping to your work day.
To find out more, visit your local Toyota Dealer or call 1800 679 247
toyota.com.au/fleet
Are you familiar with the changes to the Building and Construction Award? Here’s how we can help
There have been some recent changes to the Building and Construction General On-site Award 2020 (the Award). The changes affect the minimum rates of pay, the quantum of certain allowances and the operation of the distant travel allowance. If you have employees covered by the Award (or an Enterprise Agreement that incorporates it), we recommend that you review your practices to ensure you are still complying with your industrial obligations.
1 July 2021 – a wage increase of 2.5 per cent
The Fair Work Commission (FWC) has determined the Award minimum rates will increase by 2.5 per cent from the first full pay period commencing on or after 1 July 2021. Other construction-related modern Awards have similarly increased from 1 July 2021. Several allowances under the Award have also increased from 1 July 2021. These include the travel allowance, the overtime meal allowance, and the first aid allowance. We explore the travel allowance in more depth below.
Travel allowance
From 1 July 2021, the fare and travel pattern allowance (travel allowance) increased to $17.88 per day. Apprentices will receive a percentage of this rate, based on the stage of their apprenticeship. The travel allowance is applicable when an employee starts and finishes work on a construction site or is required to perform prefabricated work in an open yard and then required to erect steel on-site. There is no requirement to pay a travel allowance when employees are not starting and finishing work on a construction site. This includes where employees are on leave, such as annual leave, personal leave or RDOs, or when apprentices attend TAFE. Similarly, travel allowance is not payable where employers provide a fully maintained vehicle to the employee free of charge.
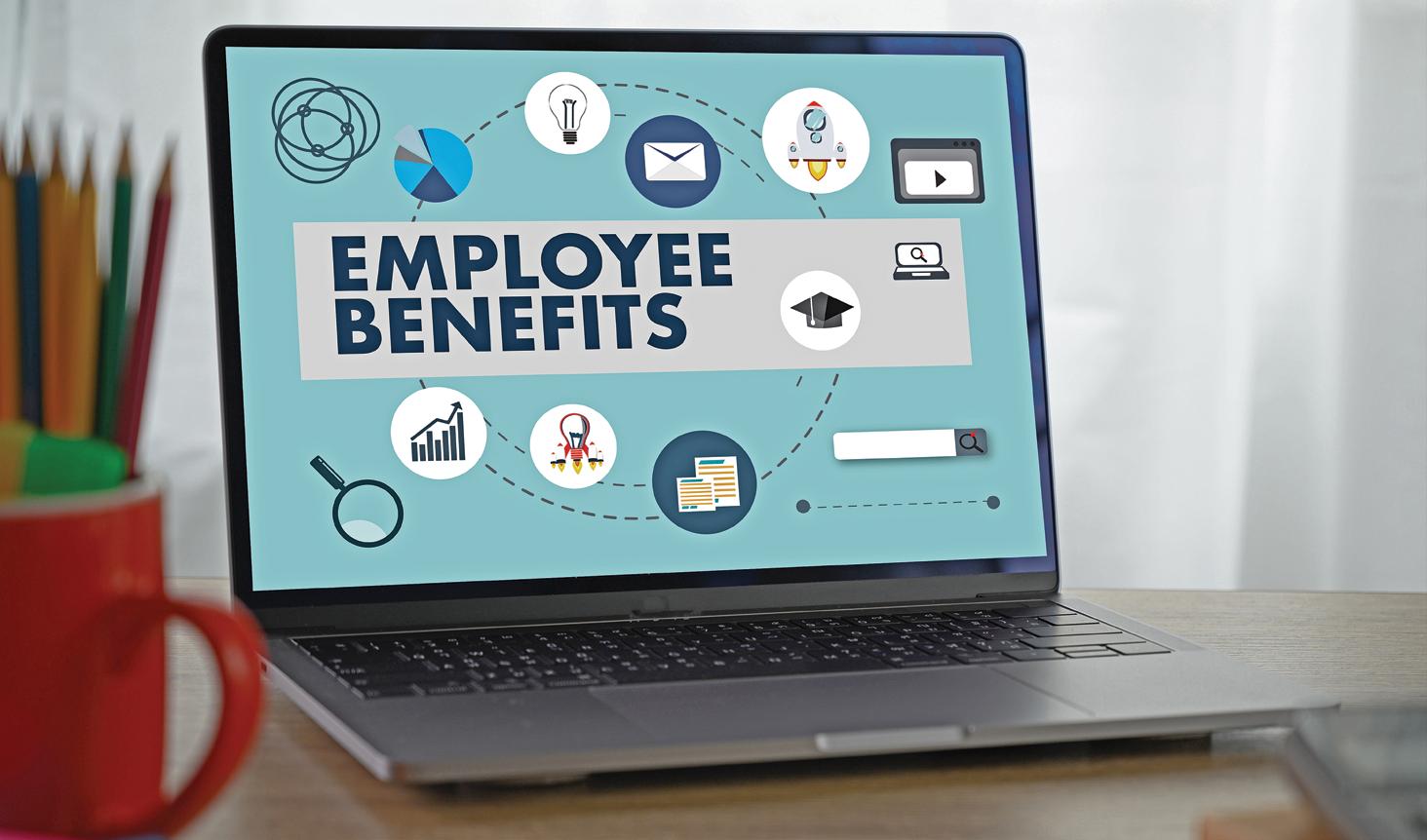
Distant travel
The MBV EIR team frequently receives questions on the distant travel allowance. This component of the travel allowance can be confusing and difficult to calculate. In 2021, the FWC has updated the operation of distant travel to try and simplify it.
When is distant travel applicable?
The distant travel allowance is applicable when an employee is required to work on a construction site that is: • Not located within the 50 km metropolitan radial area in which the employee’s usual place of residence is located: and • More than 50 km by road from the employee’s usual place of residence. To be considered distant travel, both limbs must be satisfied. This means that an employee must travel outside the 50 km radial boundary and have travelled more than 50 kms from their usual place of residence.
What is the payment for distant travel?
When distant travel allowance is applicable, an employee does not receive the standard travel allowance of $17.88 per day. Rather, the employee will be paid the following: • The time reasonably spent in travel at the employee’s ordinary time rate calculated to the next quarter of an hour; and • The cost of travel is $0.48 per km (if the employee uses their own vehicle). These allowances will be calculated from the employee’s usual place of residence to the distant construction site and return. The time spent in travel is paid as an allowance and is not included in the calculation of overtime. We understand that distant travel allowance can be difficult to calculate. If members have specific questions about the operation of the travel allowance, or the wage increase, we recommend they contact the MBV EIR team on (03) 9411 4555.
Owners not paying, builders not complying, let’s talk about how to resolve domestic building disputes
Mika Singh Junior Legal Counsel Master Builders Victoria
When undertaking domestic building works, parties may find themselves in a position where owners may not make payment, builders may deny defective building work and a raft of other issues. These types of common situations may lead to disputes and disagreements between parties, be that between the owner, builder, or other related party. This article aims to: • explore who the parties to a dispute can be; • define what constitutes a ‘dispute’ in relation to domestic building work; and • provide possible available avenues for parties to resolve disputes.
Who can be parties to a dispute?
Under section 44 of the Domestic Building Contracts Act 1995 (Vic)(“Act”), a domestic building work dispute arises between an owner and: • a builder; or • a building or quantity surveyor; or • a building inspector; or • a draftsperson who carries on a business of preparing plans for building work or preparing documentation relating to permits or permit applications; or • a person who erects or supervises the erection of prescribed temporary structures; or • a person responsible for a building project or any stage of a building project and who belongs
to a class or category of people prescribed to be building practitioners; or • an engineer engaged in the building industry; or • a sub-contractor; or • an architect, together known as Eligible Parties.
A ‘dispute’ in relation to domestic building works relates to a domestic building contract or the carrying out of domestic building work, including any of the following: • an alleged breach of a warranty set out in section 8; • an alleged failure to maintain the standard or quality of building work specified in a domestic building contract; • an alleged failure to complete the domestic building work required by a domestic building contract; • an alleged failure to complete the domestic building work required by a domestic building contract within the times specified in the contract; • an alleged failure to pay money for domestic building work performed under the contract.
Possible avenues to resolve disputes
There are various ways to resolve a dispute in relation to domestic building works, generally, the resolution process follows the below order:
Informal negotiations
When initially faced with a dispute, it is always a good idea to take reasonable steps to resolve the dispute informally between the relevant parties. This would include things like, having a conversation with the owner or builder to understand and discuss the issue(s) and ultimately reach a mutual resolution as to how parties intend on resolving the dispute. If you are considering resolving a dispute this way, we strongly advise you to: • seek appropriate legal advice before negotiating a resolution; • document the terms on which the dispute was resolved; and • keep copies of all relevant documents (for example, contracts, invoices etc).
Dispute Resolution clause
Should resolving the dispute informally fail, parties should refer back to the contract in place, and look for any dispute resolution clauses. Parties may have contractually pre-agreed on the process of how disputes would be resolved when signing the contract and would need to follow that dispute resolution method. For example, Master Builders Victoria’s New Homes Contract (HC7 Edition 2 – 2018) requires parties (either owner or builder) to apply to the Domestic Building Dispute Resolution Victoria (DBDRV), if the informal negotiations fail.
Domestic Building Dispute Resolution Victoria (DBDRV)
Parties may consider making an application directly to the DBDRV. This can only be done after the parties have made a genuine attempt at resolving the dispute among themselves first. The DBDRV can only help homeowners and Eligible Parties who have particular domestic disputes. Once the DBDRV have assessed if your matter can be heard by them, they (in line with section 45C of the Act) will make an assessment as to whether the dispute is suitable for conciliation. If the matter is suitable for conciliation, the parties will go through the conciliation process, the outcome of which may be that parties: • reach an agreement, and a formal agreement is prepared and signed by the parties; or • fail to reach an agreement, and a: » dispute resolution order is made against one or
Eligibility to use DBDRV
DBDRV assesses matter
Refers to Conciliation
Parties agree on outcome Parties do not agree on outcome
LEGAL
Parties enter formal agreement Dispute Resolution Order is made Certificate of Conciliation is issued The dispute resolution process through Domestic Building Dispute Resolution Victoria (DBDRV).
both parties; or » a certificate of conciliation is issued, stating parties were unable to resolve their dispute via conciliation.
Victorian Civil and Administrative Tribunal (VCAT)
If conciliation through the DBDRV was unable to resolve the domestic building dispute, parties may consider making an application to VCAT. Pursuant to section 56 of the Act, parties can only make an application to VCAT if they have been issued a certificate of conciliation, a point highlighted in Angele Homes Pty Ltd v Barbara (Building and Property) [2019] VCAT 1825 (20 November 2019) where a proceeding in relation to a domestic dispute commenced in VCAT but was stayed until a certificate of conciliation was issued by the DBDRV.
Conclusion
Resolving disputes can sometimes be simple and other times be complicated. To ensure you are taking the appropriate steps to suit your situation, we encourage you to seek specific legal advice. For further information, please feel free to contact the Master Builders Victoria - Legal Department on (03) 9411 544 or email us at legalenquiries@mbav.com.au.
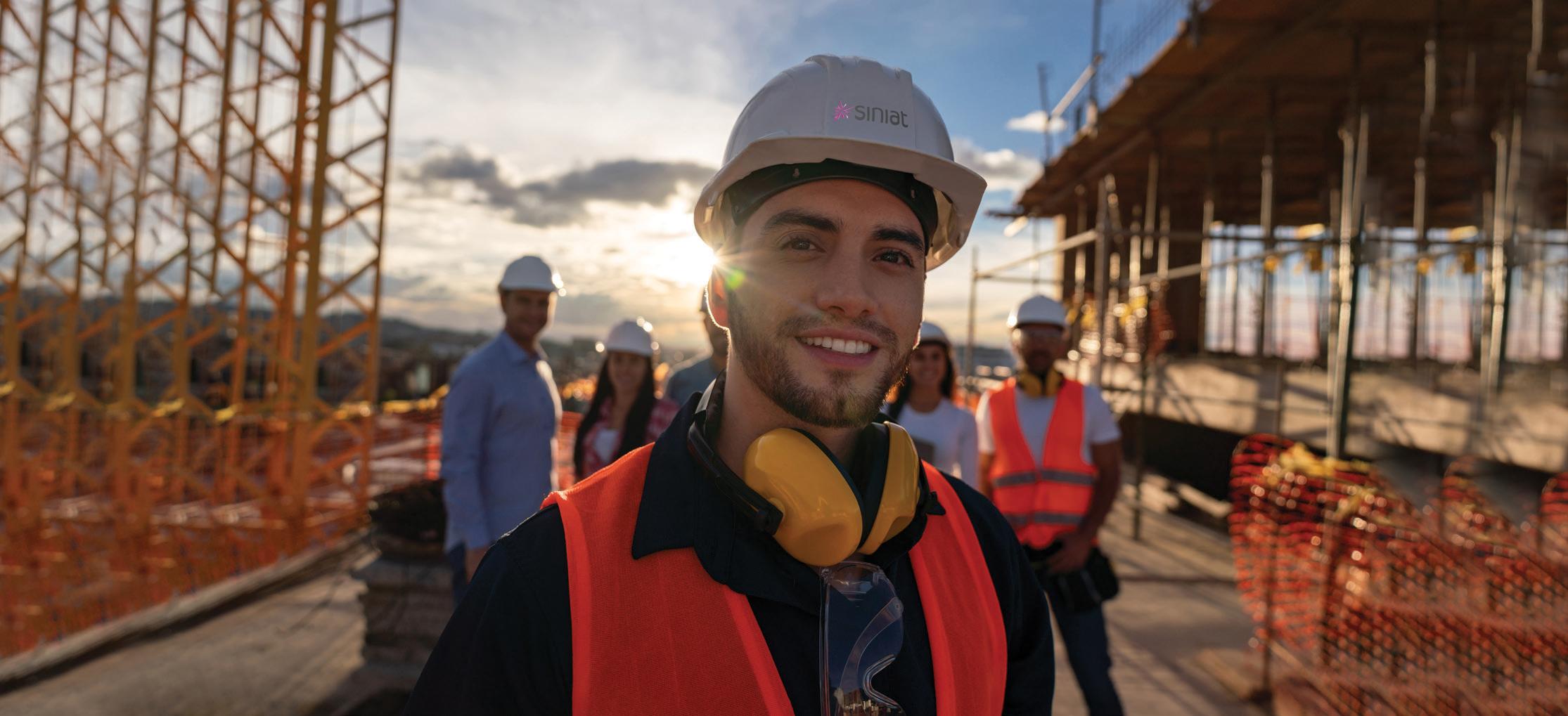
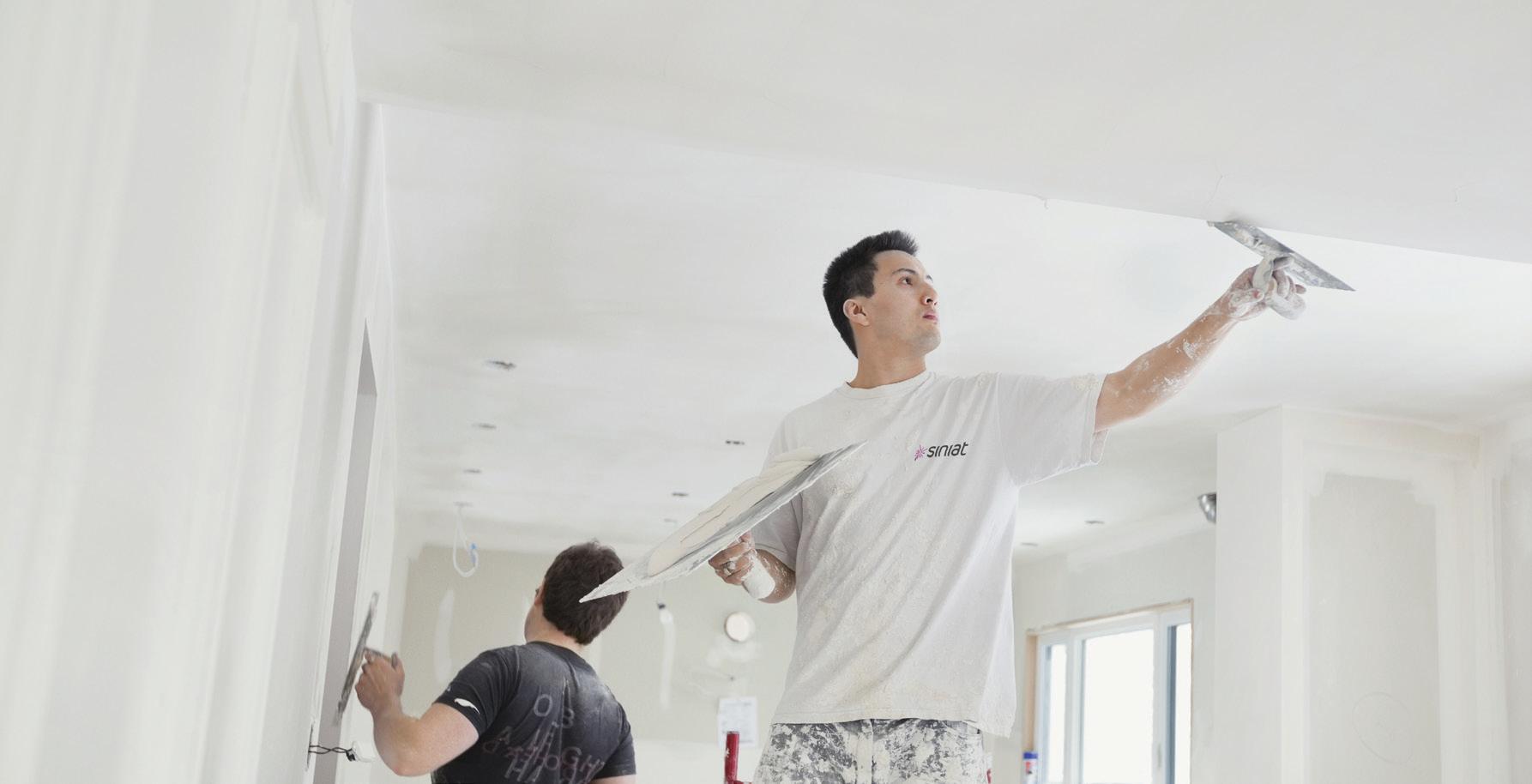
Cbus Super delivers biggest return in fund’s history
Cbus Super has announced a 19.34% return for its Growth (Cbus MySuper) option, the largest ever annual return in the fund’s 37-year history. Cbus Super Chief Investment Officer Kristian Fok said the outstanding result was a demonstration of the fund’s strategic approach to markets during COVID-19 volatility. “I’m proud of the way that our investment teams have negotiated market volatility over the last 18 months,” Mr Fok said. “Cbus was one of a small group of funds to achieve a positive result (0.75%) during the previous 2019/20 financial year. To then have the confidence to get back in the market is testament to the people and structures that we have put in place over the last five years. “We managed our cashflow exceedingly well during the initial COVID-19 volatility which meant that we could invest for our members on the upswing.” Cbus Super now manages 35% of assets in-house. Mr Fok said building up this internal capacity has provided the fund greater insights into markets and allowed for a significant reduction in investment fees. “We have reduced investment fees by $400M since 2017 which has helped add to our returns,” he said. “We have seen the cost of managing a dollar of savings fall by 8% compared to last year which is a really strong outcome. “Results like this are strong indicator of the significant benefits of being involved in a fund of this scale.” Mr Fok said the fund’s focus on increasing scale and reducing fees should serve members well as market conditions become more difficult. “Obviously we would love to see strong double-digit returns like this every year but indications are that conditions will become tougher,” Mr Fok said. “That’s why increasing scale and reducing investment costs is so important. Superannuation is a long-term game and the gains members see from fee savings will compound over time.” Cbus Super CEO Justin Arter said the fund’s expertise in property and the built environment benefitted both members and the wider economy as the country struggled with COVID-19 lockdowns. “There were stages last year where quality developments were struggling to get the finance they needed,” Mr Arter said. “As banks were tightening lending, Kristian and his team were able to support successful developments to keep going at a pivotal time for the construction industry. Cbus Property has also been able to commit to new projects during the height of the pandemic.

Annual statements
Cbus members will receive their annual statements in September by email or post. Members can also log on to their account at cbussuper.com.au/login to check their super balance. For more information about your super please call 1300 361 784 or visit www.cbussuper.com.au
“We are proud of the record result we have achieved for members and of the way we have supported construction jobs and property supply at such an important time for the country.” The Growth (Cbus MySuper) investment option return is based on the crediting rate, which is the return minus investment fees, taxes, and until 31 January 2020, the percentage-based administration fee. Excludes fees and costs that are deducted directly from members’ accounts. Past performance is not a reliable indicator of future performance. Cbus Property Pty Ltd is a wholly-owned subsidiary of United Super Pty Ltd and has responsibility for the development and management of Cbus’ direct property investments. This information is about Cbus. It doesn’t take into account your specific needs, so you should look at your own business needs, objectives and requirements before making any financial decisions. Read the relevant Cbus Product Disclosure Statement and related documents to decide whether Cbus is right for you.
Call 1300 361 784 or visit www.cbussuper.com.au for a copy.
Cbus’ Trustee: United Super Pty Ltd ABN 46 006 261 623 AFSL 233792 Cbus ABN 75 493 363 262
Supply shortages have critical impact
Megan Peacock Policy Manager, Master Builders Association Of Victoria
Master Builders Victoria has been working tirelessly to understand the cause and impact of the supply shortages on our industry. State and Federal Government incentives for the building and construction industry, such as the successful HomeBuilder Grant, have delivered a muchneeded boost in the face of the COVID-19 pandemic. These incentives have generated billions of dollars in economic activity and helped to secure the viability of thousands of businesses and jobs through this pandemic. However, the international supply chain constraints were unforeseen, and these are now having a critical impact on our industry, which may adversely affect the broader Australian economy if not addressed. Current conditions have seen a reduced capacity in supply chains for building products in both Australia and overseas. Usually, timber imports make up about one-fifth of Australia’s total supply. However, competing forces worldwide – such as increased demand in the US - have seen our timber imports drop significantly. In addition to this, other conditions contributing to the current shortages in Australia include: • Increased global demand for building products because of COVID stimulus across the US and Europe. • A demand surge created by State and Federal Government incentives, such as the Federal
Government’s successful HomeBuilder grant. • Imported materials are still being delayed due to shipping and logistics challenges. • Bushfires have impacted timber production for structural timber. • Train derailments on the Nullarbor. • Shipping delays due to the Suez Canal blockage. • Industrial action at ports including Melbourne holding up material. • Compulsory shutdown of timber mills at Christmas time for scheduled safety maintenance. • Dated equipment at timber mills. This overlap of events has led to real pressures on the domestic building sector within Victoria and across Australia. In addition to these supply constraints, there has been increased demand due to the various stimulus measures and increased spending capacity from ordinary Australians. Australians who would normally have spent money on overseas travel have instead turned their attention to home renovating or purchasing new homes. MBV have been successful in our advocacy with Treasurer Tim Pallas appointing Commissioner for Better Regulation and Red Tape Commissioner Anna Cronin to investigate supply shortages and their impacts on building and construction in Victoria. We have facilitated two forums between members and Ms Cronin’s team, and we continue to work closely with them on this critical issue. If you have anything to add to this conversation, please feel free to email: policy@mbav.com.au
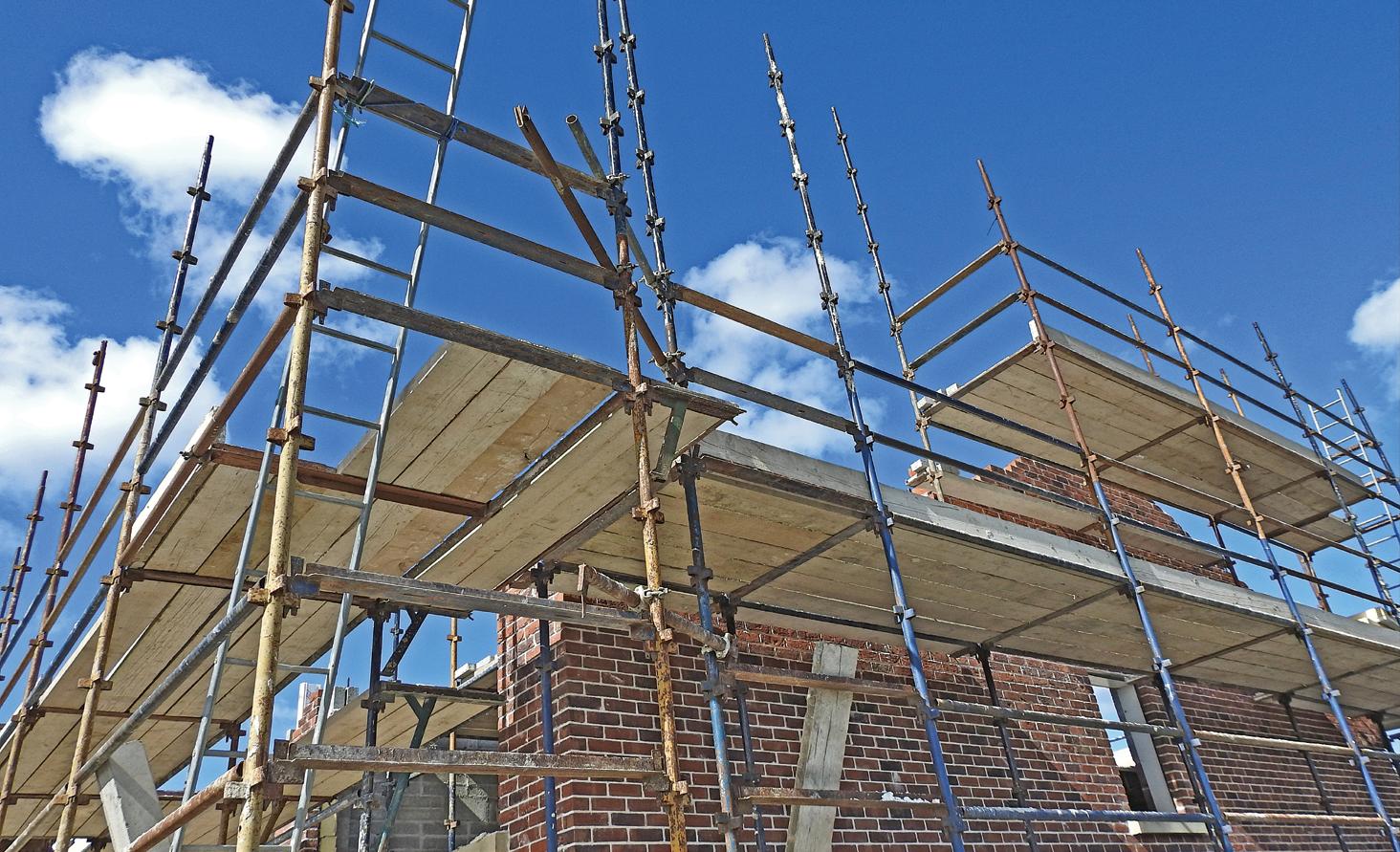
Building and Construction Lawyers
• Contract Advice and Management • Project Implementation • Building Disputes & Defects • Professional Liability & Negligence • Security of Payment Claims • Litigation & Dispute Resolution
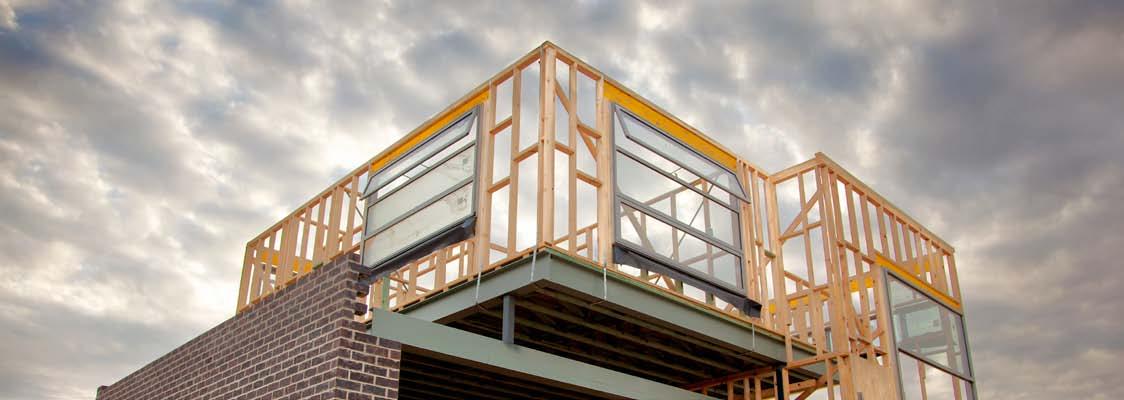
Andrew Whitelaw - Director awhitelaw@wflawyers.com.au

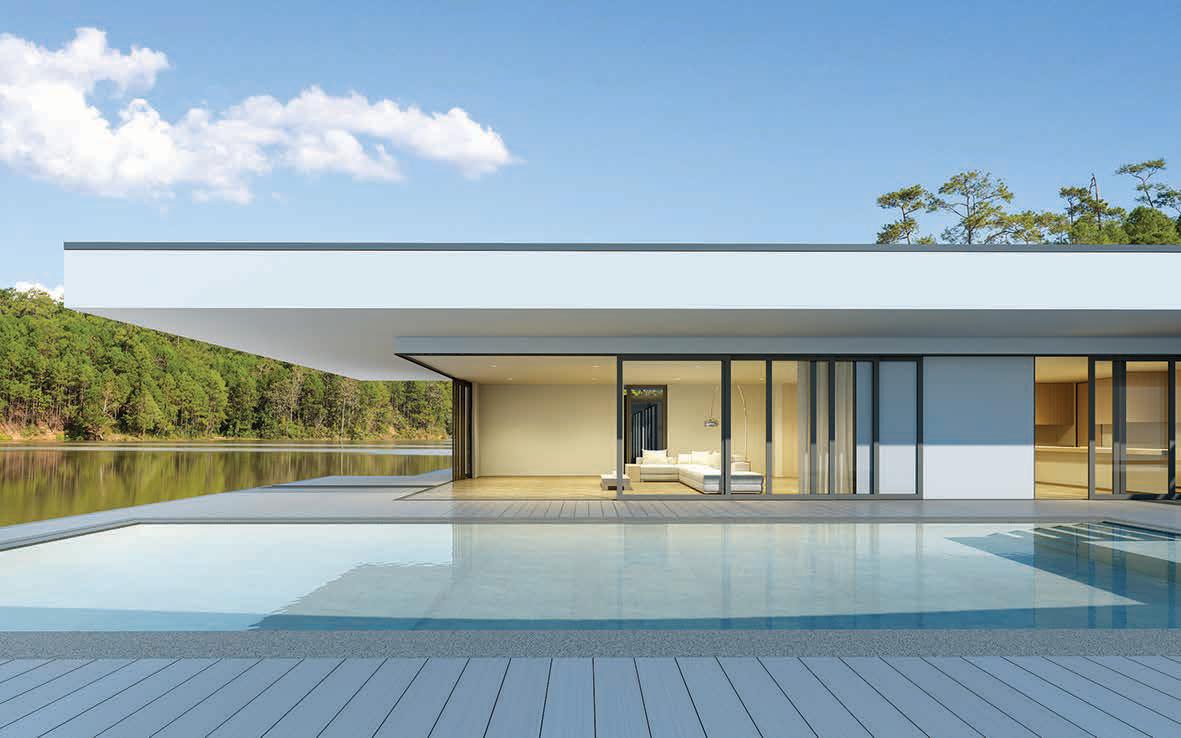
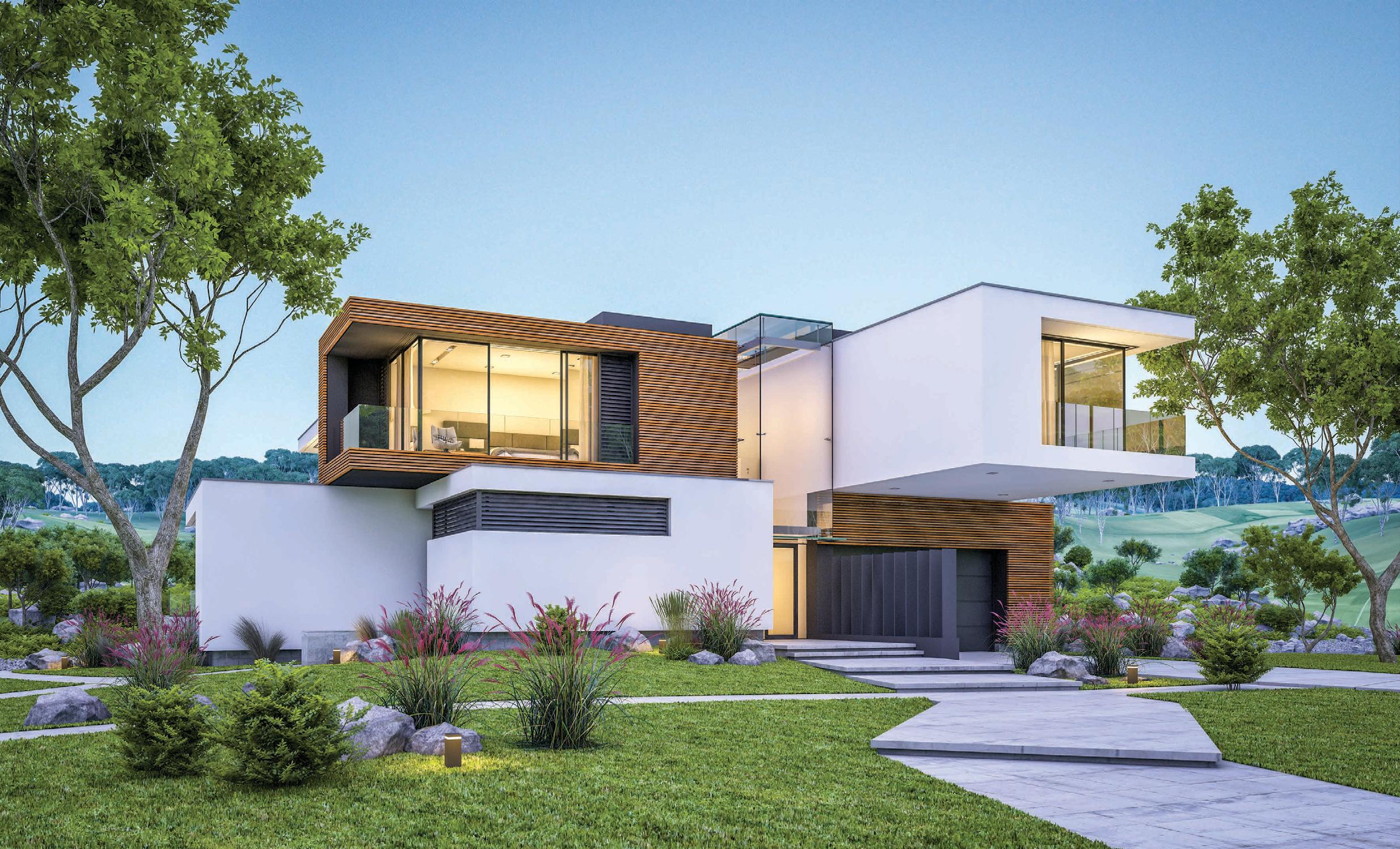

Save time and money with advanced cladding technology
The new generation of Magnesium Oxide cladding is set to save on material and labor costs while offering peace of mind to property owners
For many trades in the building and construction industry, the change from plasterboard and CFC cannot come quickly enough. Citing deficiencies in exterior weather to the multiple layers required for some fire walls, costs can additionally blow-out, with many of these materials requiring expensive and specialised tools for application and installation. The new generation of Magnesium Oxide cladding (MgSO4) and sheeting by FireCrunch is the answer to most forms of internal and external cladding. It is lightweight, can be used on a variety of surfaces, is installed easily requiring less labour and can be used as a fire wall offering a total fire block. While the earlier types of MgSO4 board were effective protection from fire, they had a poor surface finish and a tendency to absorb moisture if not properly sealed. Through new technology, FireCrunch has achieved high loadbearing (55kN) CSIRO-tested and compliant, verified fire-proof building products, while offering high-quality, double-slurry surfaces and giving a first-class finish. It can be used as underlay flooring, tile backers, shower bases and once primer-sealed can be painted with normal water-based paints, texture paints or renders. With costs as low as $18 per sqm, MgSO4 offers top fire rating from NATA, CSIRO and Resolute Labs. MgSO4 cladding will handle up to FRL 90/90/90 (NATA Labs tested) with a single sheet each side of a 90mm cavity frame. MgSO4 cladding will handle up to FRL 90/90/90 (NATA Labs tested) with a single sheet each side of a 90mm cavity frame. It has endured real-time bush fire simulation tests and full-scale furnace tests at 1000. MgSO4 is regularly recommended by architects, specifiers and QS/surveyors, and fire engineers and certifiers. The board contributes 95% less C02 than plasterboard. The material is suitable for fire separation walls in high-rise residential and commercial construction and for bushfire BAL FZ and flood-prone areas and available to clients Australia-wide.

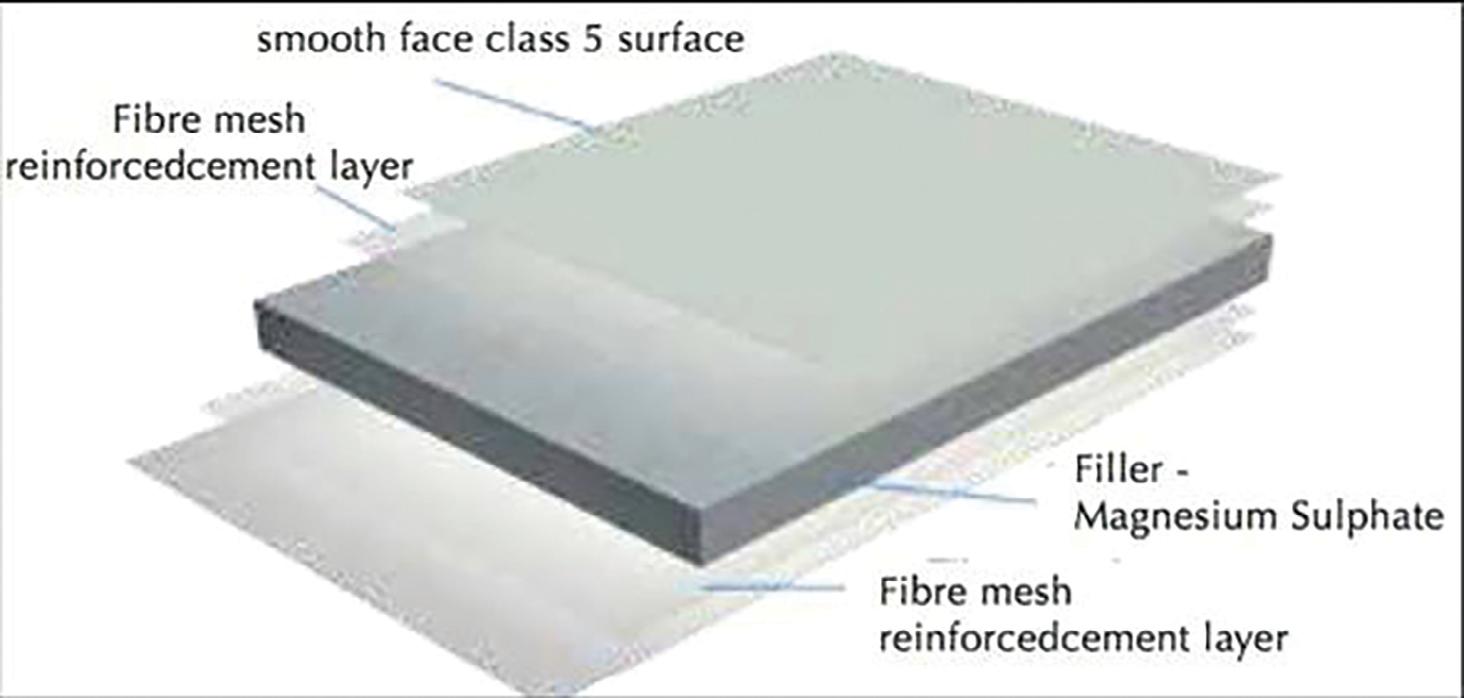


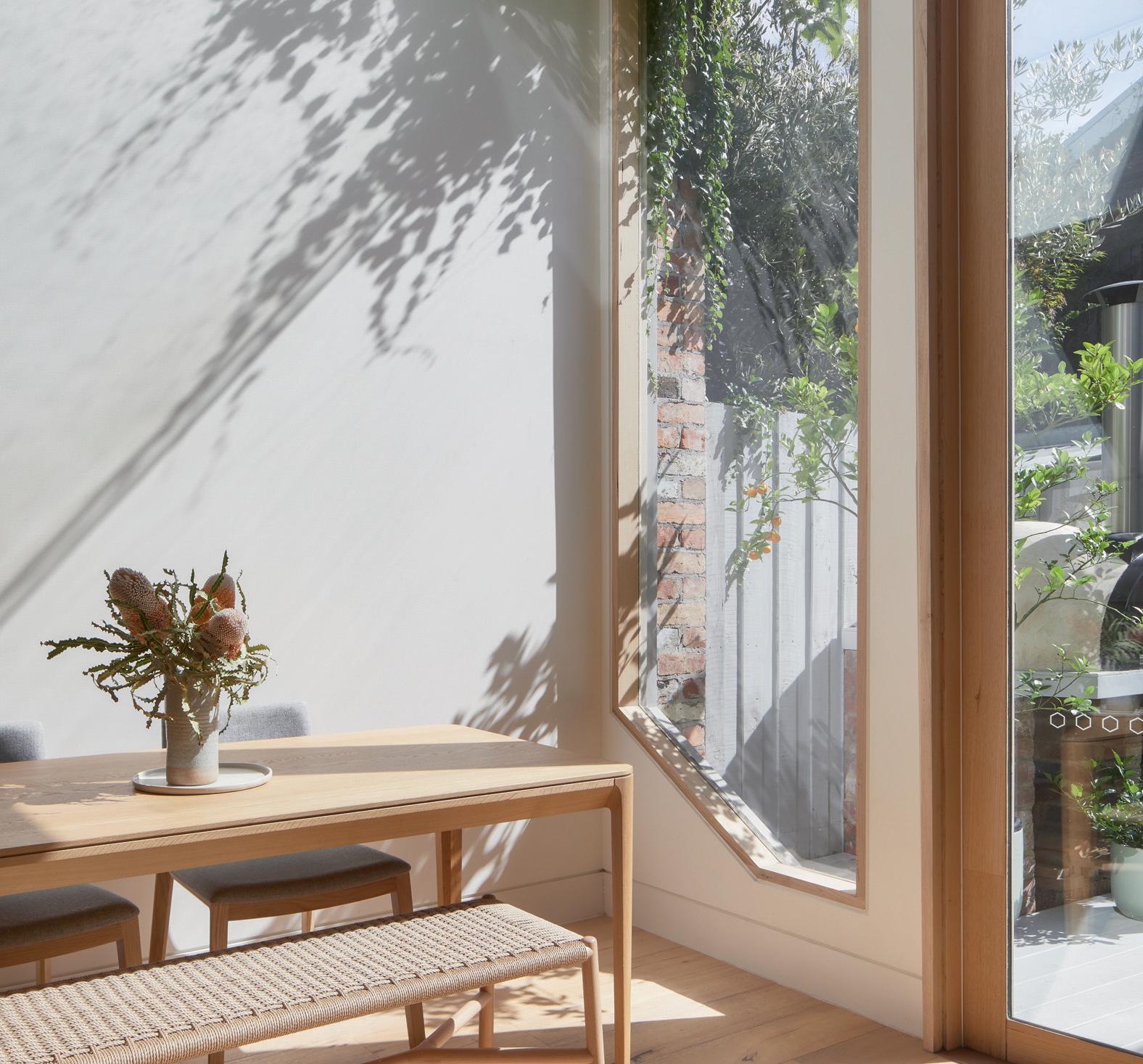
Ph: 9768 3944
16 Healey Rd, Dandenong South, VIC 3175 sales@aspectwindows.com.au www.aspectwindows.com.au u
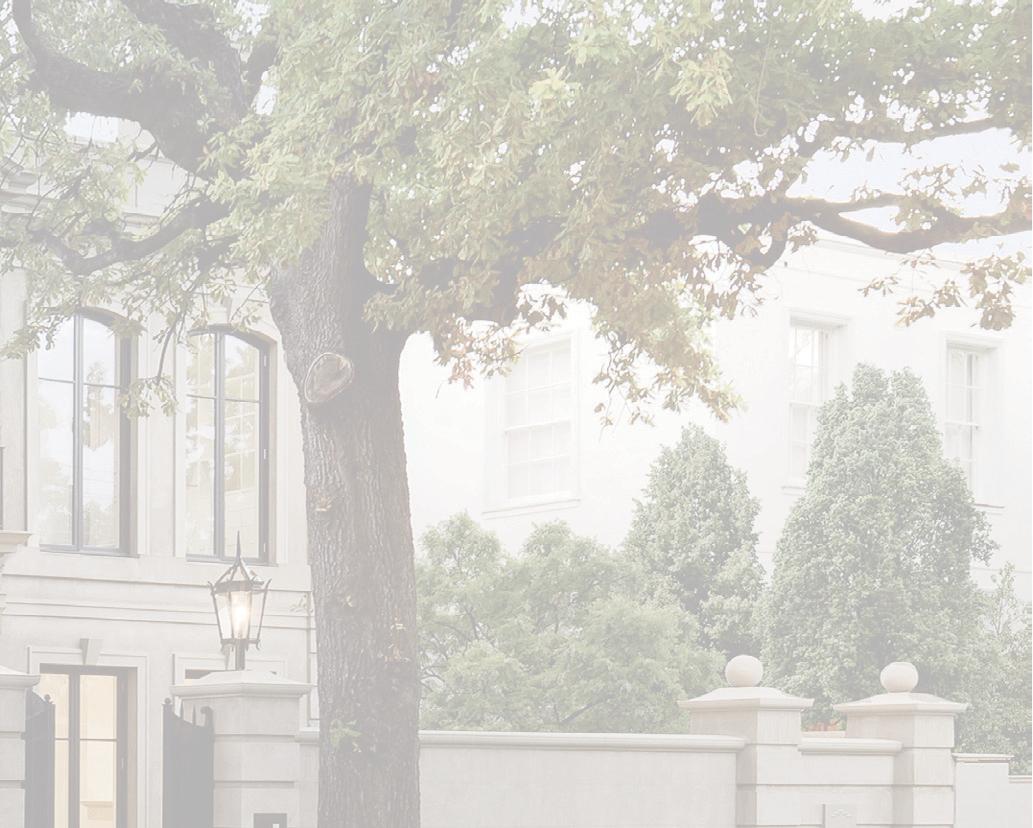
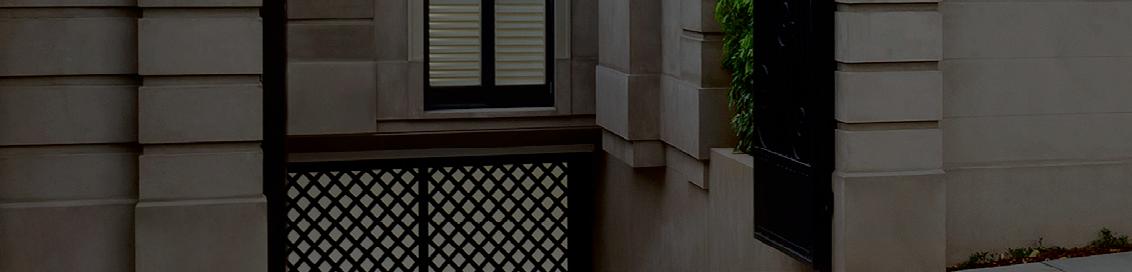
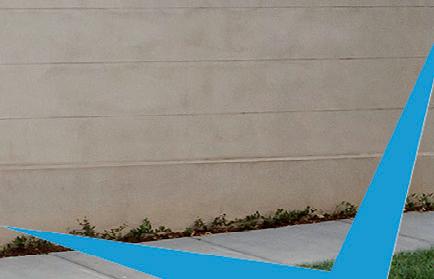


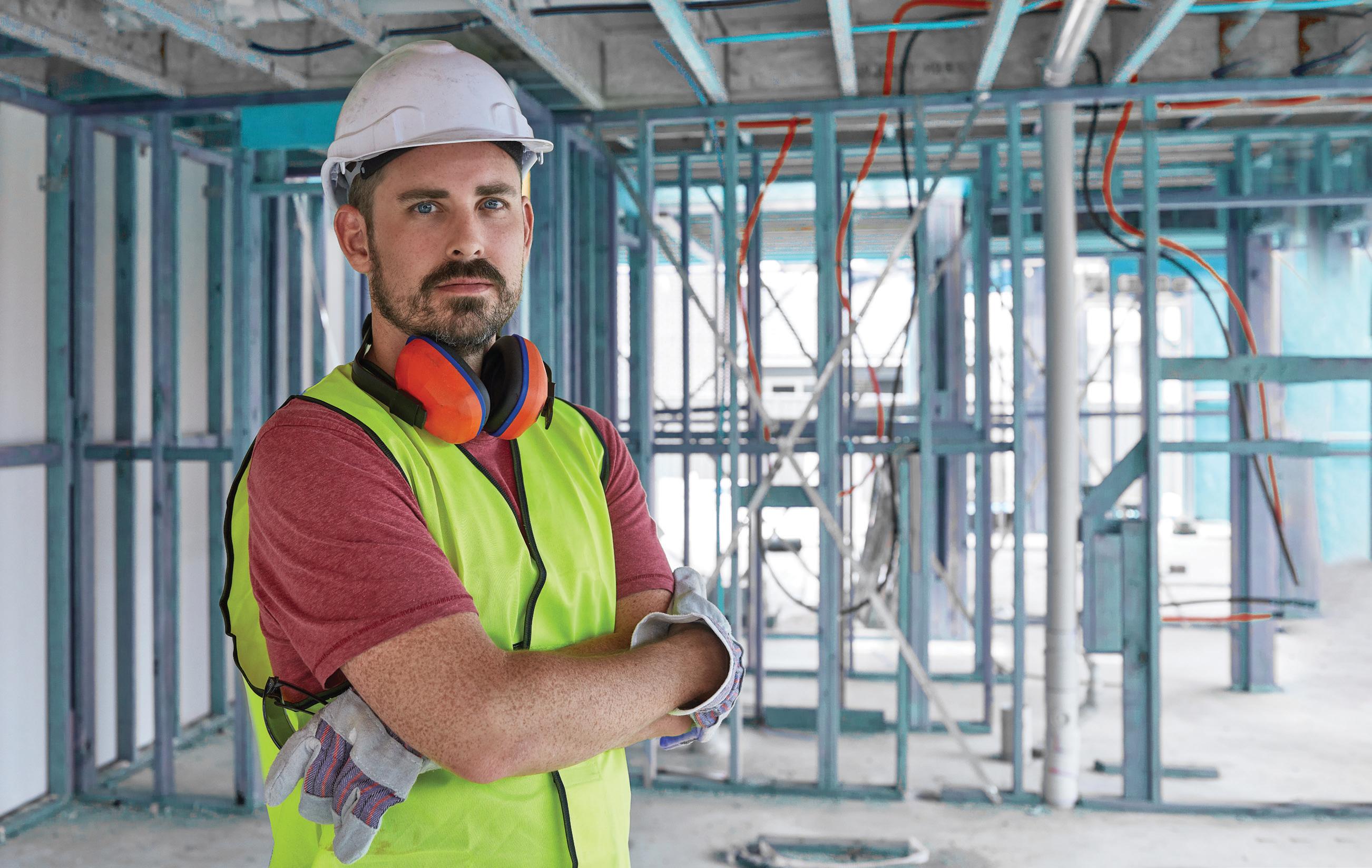
The Lysaght Professionals website is the complete technical resource for the building professional. The site contains detailed product, compliance and installation information for the complete LYSAGHT® steel building products range.
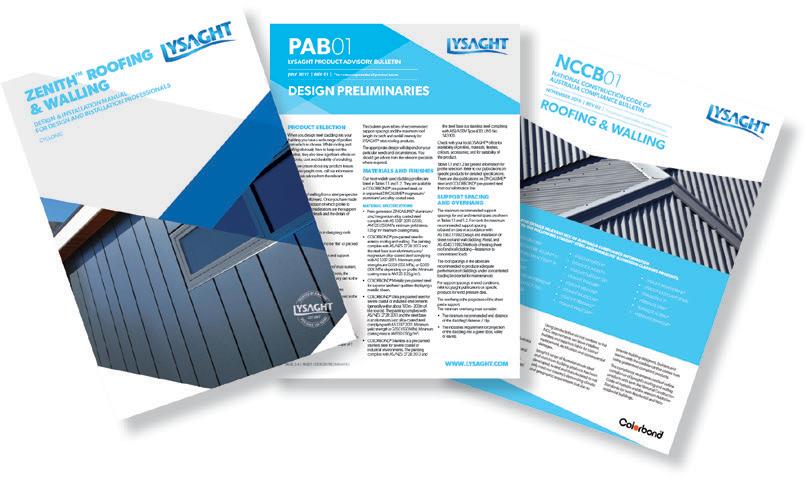
DESIGN AND INSTALLATION MANUALS:
Detailed technical manuals for all the products in the LYSAGHT® range.
PRODUCT ADVISORY BULLETINS:
A growing range of easy-to-read fact sheets covering a range of specification, design and installation topics.
NCC COMPLIANCE STATEMENTS:
To support your own design and approval submissions Lysaght has a suite of NCC Compliance bulletins covering the complete LYSAGHT® product range. PRODUCT LITERATURE:
A complete range of LYSAGHT® product brochures for your reference and client discussions
CASE STUDIES:
Explore a range of projects incorporating LYSAGHT® building products.
For more on the Professional’s Resource, visit: PROFESSIONALS.LYSAGHT.COM

Lysaght has a number of product solutions that can assist with condensation management in steel clad buildings.
Lysaght breaks the mould with condensation management solutions
Condensation build-up in roof and wall cavities can cause long term aesthetic, health and structural problems in buildings if not managed properly. This problem is caused by changes in temperatures – when the surface temperature falls below the dew point of the surrounding air, condensation in the form of water vapour will take place on the colder surface. Generally, small quantities of condensation can be tolerated so long as it is given the opportunity to dry out. If the environment remains wet for longer periods though, issues may arise. If not kept in check, condensation causes mould build-up on surfaces and in HVAC systems, can result in plaster deformities, and in severe cases, can cause damage to framing in the form warping and rotting. New provisions under the National Construction Code (NCC) 2019, have removed ambiguity and have outlined minimal requirements for residential buildings covering how much ventilation is needed and where it should be placed (Clause F6.4 NCC 2019 Volume One and 3.8.7.4 of NCC 2019 Volume Two). A key ingredient in minimising condensation is to provide adequate ventilation to help extract moisture, or allow it to escape naturally. In areas like kitchens, laundries and bathrooms where water, steam and cold hard surfaces most often meet, extraction systems are important, particularly those that duct the moist air outside rather than into the roof. While ducted extraction systems do a great job in removing steam from wet areas, installing roof cavity ventilation will further reduce condensation, providing additional peace of mind. As a leading producer of steel building products, Lysaght offer several roof ventilation solutions, ranging from traditional turbine ventilators, through to the VENT-A-ROOF® system. VENT-A-ROOF® is a concealed roof ventilation system that uses the power of natural airflow. It’s installed under traditional ridges, hips, barges, making it extremely versatile and inconspicuous. The use of insulation and how it’s installed can also assist to minimise condensation. In the roof space, insulation and membrane should be fitted so that it doesn’t block ventilation paths. Roof level insulation such as blanket and foil is also useful, particularly in cooler climates. For architects, engineers and builders, Lysaght can assist in developing effective moisture management solutions for buildings that will be clad with LYSAGHT® products. Lysaght has produced a comprehensive Technical Guide and supporting Product Application Bulletins as useful design and construction references for building industry professionals. The detailed recommendations contained therein take into account the building location’s climate zone, as well as the type of cladding used – this covers supported or unsupported cladding (ie does the cladding need continuous support such as plywood or can it free span between batten or purlin supports) and whether it’s open or closed profile. ‘Open’ profile claddings are those that allow airflow; ‘closed’ profiles typically have closed ribs that won’t allow easy airflow. Style of roof construction is also addressed: trussed and skillion roofs with self-supporting metal claddings or trussed and skillion roofs with supported metal claddings. NCC 2019 condensation requirements are also applicable to walling cavities as well, with similar principles applying and are also covered in Lysaght’s reference materials. To download “Condensation Control in Australian buildings constructed with LYSAGHT® claddings” visit https://professionals.lysaght.com/resources/manuals
Framework for Reform: Modernising
Tony Bugeja Senior Adviser — Technical
The building and construction industry is a significant industry to the Victorian economy and that of the broader community, so it is essential that our industry has a robust and pragmatic regulatory framework to ensure our buildings meet a satisfactory standard. In December 2019 the Victorian Government appointed an “Expert Panel” to lead a review of the building legislative and regulatory system as a commitment to deliver safe, quality buildings, through a sustainable building and construction industry, that includes effective consumer protection. The Expert Panel members leading the review are: • Anna Cronin - Chair (Commissioner for Better
Regulation and Red Tape Commissioner) • Melanie Fasham - (Past President of the Master
Builders Victoria and member of the Building
Regulations Advisory Committee) • Dame Judith Hackitt - (Chair of the UK
Independent Review of Building Regulations and
Fire Safety and former Chair of the UK Health and
Safety Executive) • Lauren Solomon - (CEO of the Consumer Policy
Research Centre) • Dr Gerry Ayers - (Health and Safety Manager of the Construction, Forestry, Maritime, Mining and
Energy Union (Construction and General Division –
Victorian/Tasmanian Branch)) • Professor Ian Bailey AM SC - (Founding Chair of the Society of Construction Law Australia and professorial fellow at the Melbourne Law School) The primary reason for the review is the government’s concern there are system failures in our current regulatory system which have continued to play a part in delivering low quality and defective building work that increases risk to public safety. These concerns are a consequence of the findings and recommendations from the Victorian Ombudsman, the Victorian Auditor-General’s Office, the Victorian Cladding Taskforce, and the Shergold-Weir Building Confidence Report. The key objectives of the review are to strengthen the Victorian regulatory system to: • Deliver safe, compliant, durable, affordable, and sustainable housing and buildings efficiently and effectively. • Protect consumers and improve confidence in the industry and its regulators. • Support skilled and experienced practitioners to carry out compliant and safe practices. • Provide support to regulators so they can effectively, and efficiently enforce compliance. The Expert Panel advice is to be released in three stages over the next two years, with progressive implementation of reform through meaningful engagement with industry stakeholders. In April 2021, the review – “Framework for Reform: Modernising Victoria’s Building System” was made available for public comment. A copy of the review can be sourced from www.vic.gov.au/building-system-review Stage one focuses on four key elements: • Practitioner registration. • Building approvals system. • Regulatory oversight. • Consumer protection. Master Builders Victoria (MBV) has advocated on behalf of industry and our members for initiatives that will raise standards in our industry. The built environment is an essential foundation of our community. We acknowledge there are some well published examples of failings in our system that must be addressed if we are to continue improving and deliver the built environment of the future. There are multiple reasons for these failures including shortcomings in government policy, regulation, and various professions. These weaknesses have become systemic through a failure to adapt to the changing face of building and
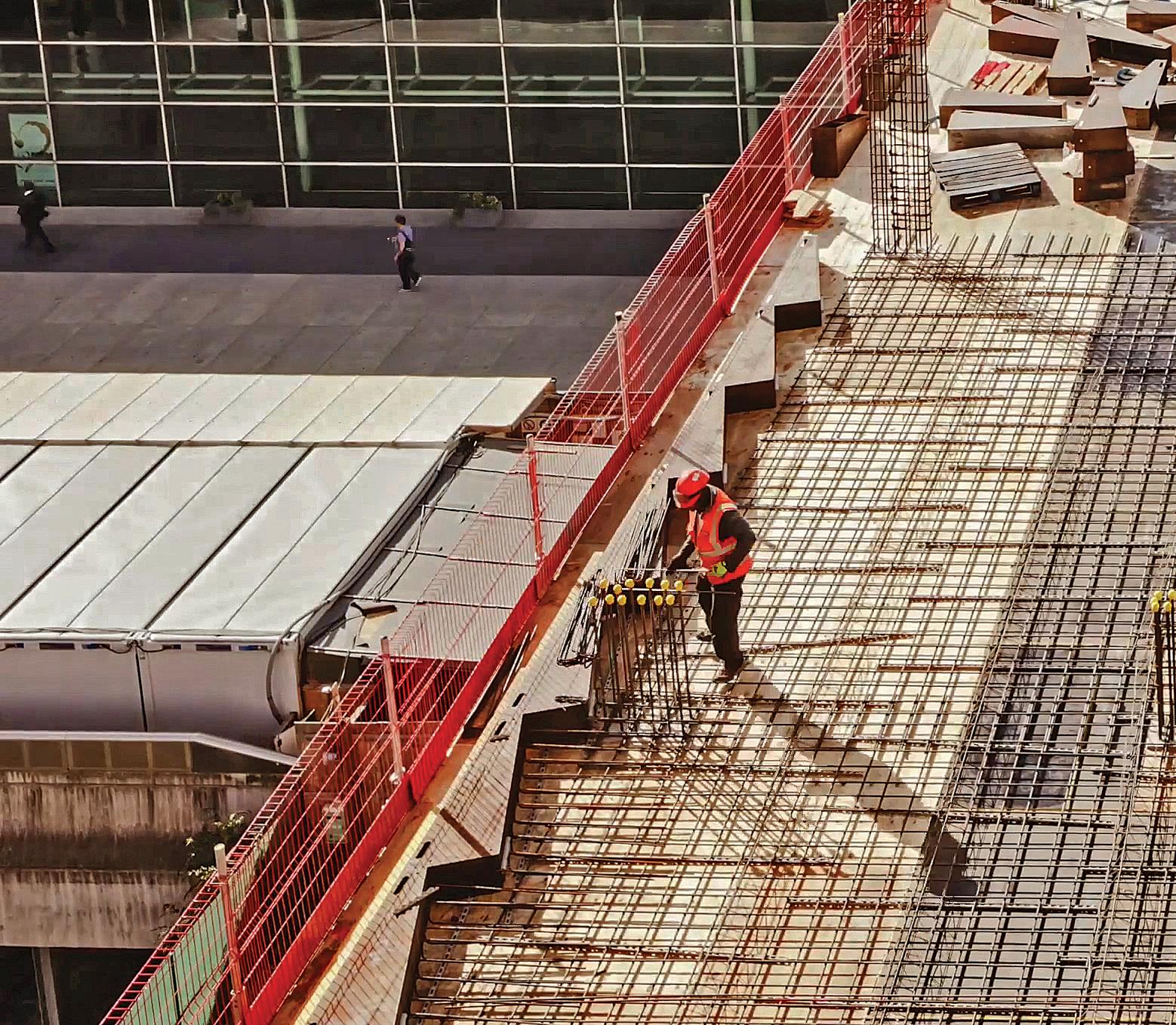
Victoria’s building system
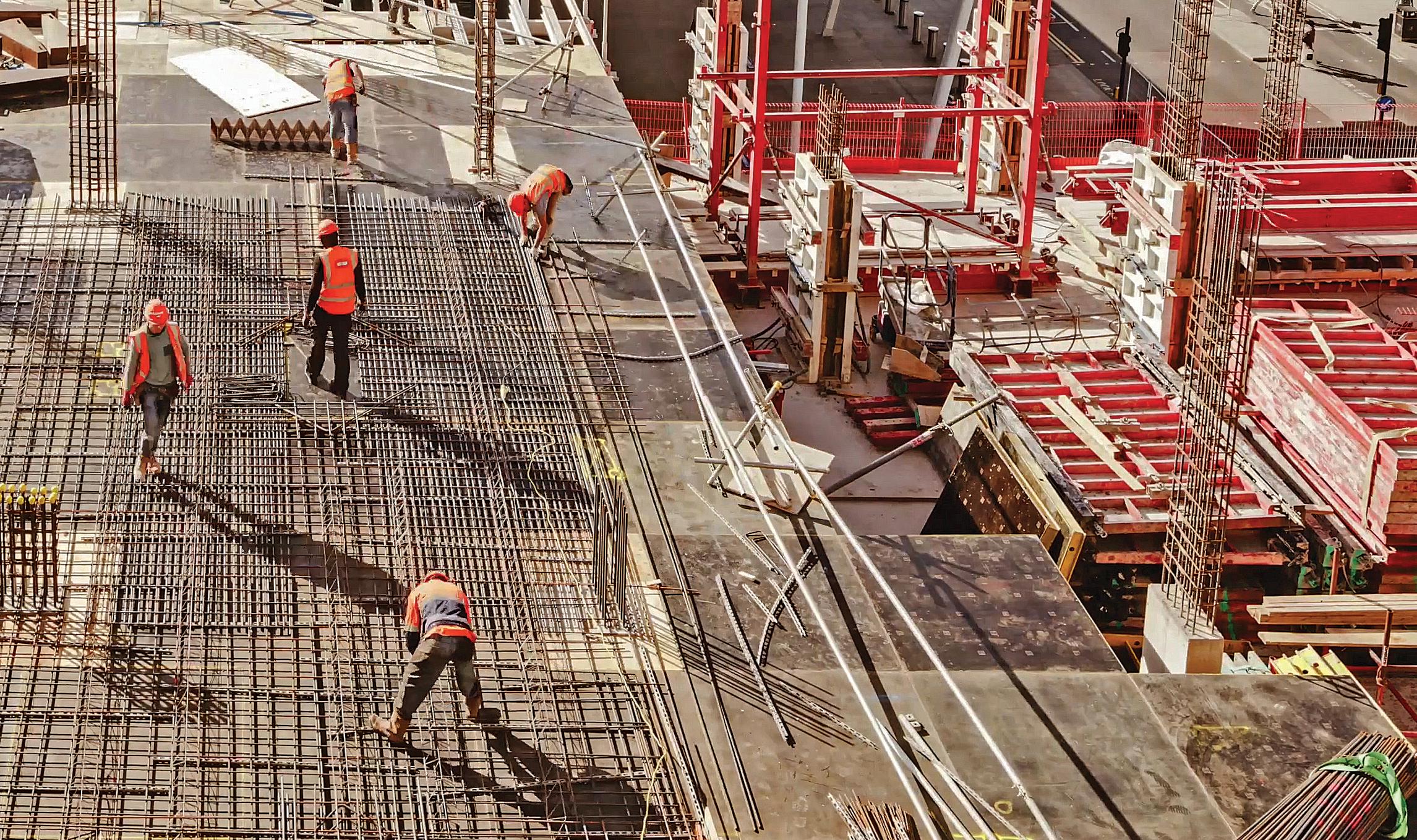
construction over time. MBV’s vision is to create a future ready industry that contributes to a better built environment for all Victorians. We have indicated that the Expert Panel needs to continue to address these deficiencies as part of whole-scale reform. MBV believes the options contained within the review have the potential to move our industry forward. However, our view is that the options need to be considered holistically to bring about effective change. An overview of our submission to the Expert Panel proposed that the following elements should form the base of future systemic change: • Revise the existing registration system, applying a risk-based approach based on contemporary industry practice. This should include closing the gaps in the existing registration system and widening scope to currently unregistered parties. • Re-balance the responsibilities through the building and construction process via improved design documentation and design declarations.
The quality of design documentation compounds throughout the building and construction process. • Increase regulatory oversight at a practitioner level through a mandatory auditing process for all building surveyors. This should complement the
Proactive Inspection Program (PIP), which should equally monitor the role of all other industry professions. • The risk-based approach should also extend to increased oversight on ‘high-risk’ buildings, through independent review of design documentation, strengthened mandatory inspections by the Relevant Building surveyor (RBS) and random inspections by the regulator. • Ensure the effective implementation of the
Mandatory Registration of Trades and Continuing
Professional Development (CPD) for all industry professions. • Bring together the oversight of all industry practitioners under one regulator to facilitate clear scopes of work for practitioners, consistent guidance and expectations and holistic monitoring
of industry performance. • This regulator - informed by data - should offer a single, objective source of truth for consumers and practitioners alike. This will enable improved education and awareness of roles and responsibility, which in turn will raise industry confidence. • It is essential that the regulatory environment establish adequate data to monitor industry performance and identify systemic changes and innovations. This data must be shared with industry, including collaboration with industry associations to coordinate training and CPD. • A Minister for Building and Construction should be appointed with specific responsibility for the functions and outcomes of our industry. MBV believes the above steps, combined with recent regulatory and legislative changes, will bring about the improvements in oversight required to raise standards in our industry, and ensure that our sector continues to build a vibrant and sustainable industry and community.
MBTI: Leading a future-ready industry that builds a better world
Tyson Imms Instructional Designer Master Builders Training Institute (MBTI)
In late 2020, as part of the CPC training package update, the government published new versions of the: • Certificate IV in Building and Construction (Building); and • Diploma of Building and Construction (Building) qualifications. After a lengthy review, the new qualifications were released to incorporate the building and construction industry’s ever-changing environmental, legislative and technological landscape into the Construction, Plumbing and Services (CPC) training package. The majority of people who apply for builder registration in Domestic Builder Unlimited (DB-U) and Commercial Builder Limited (CB-L) categories will study one (or both) of these qualifications.
Our response
Over the past six months, the Master Builders Training Institute (MBTI) has consulted various stakeholders to design the new qualifications. We started with the Victorian Building Authority – well over half of our students study these courses to become registered, so ensuring our new courses met their needs was essential. We analysed feedback from past and current students to see how we can adapt our training and assessment methods to suit the needs of a tradesperson working full time and studying on the side, as well as gathering further insight into areas of study they would have liked us to cover more fully. We also spoke with our trainers — who still work as builders, estimators and other construction professionals — to inform our clustering and sequencing of training. Finally, we spoke to employers in the construction industry to ensure our training practices meet their expectations for construction professionals working in their organisations.
What did you tell us?

1. The quality of MBV trainers is excellent and using our ‘specialist’ trainers for different subjects is a superior training model to the alternative ‘one trainer per class’ used by most RTOs. Rest assured, we work hard to engage only the highest-quality trainers and continue to do so. 2. Students see the advantages of both remote and face-to-face training. So, we’ve planned our new qualifications with a mixture of both forms of learning so you can still network in class while also being able to learn from the office or at home. 3. The three most significant issues in the industry right now are dispute resolution, ensuring quality materials and legally managing building permits. We’ve incorporated all three into our elective selection. 4. Students want to learn about the software they’ll be using once they’re on the job. We’re working with industry to source estimating, scheduling and occupational health and safety and quality management software to use in our courses. 5. Our Building Leadership Simulation Centre (BLSC) delivers world-class training and real results. We’re increasing the amount of simulation-based training and assessment in our qualifications so you can get more bang for your buck. If you’ve been on the fence about studying for the Certificate IV or Diploma Building and Construction (Building), there’s never been a better time to study with the Master Builders Training Institute (MBTI). Get in touch with us now at training@mbav.com.au or call (03) 9411 4555.

Building 4.0 Cooperative Research Centre
Dr Phillip Alviano Sustainability Advisor
Master Builders Victoria is a part of the Building 4.0 Cooperative Research Centre. The CRC 4.0 aims to help the construction sector become more efficient by conducting industry driven research into new technologies and techniques. It will focus on digitally enabled solutions and new manufacturing products to develop an internationally competitive, dynamic, and thriving Australian advanced manufacturing sector. This will deliver better buildings at lower cost and the human capacity to lead the future industry. Current projects that Master Builders Victoria is a part of:
• ePlanning and eApprovals – Scoping Study
(Commenced March 2021).
Planning and building approval processes are still largely paper (PDF) based, which makes them inefficient and time-consuming, imposing significant costs on both industry and government. The longer-term objective of the CRC’s work in this area is to embrace the opportunities that digital workflow and digital twin technology provide. This will help to design, develop, and deliver an innovative digital platform to facilitate effective, efficient, and timely planning, building permits, approvals, ongoing compliance with planning controls, building regulations and other regulatory requirements. • Virtual Reality/Augmented Reality technologies
in vocational education and training (scoping study) (Commenced April 2021)
Vocational Education and Training (VET) is a major part of Australia’s education system. It is crucial to train practitioners with innovative technologies to gain fundamental skills in critical and creative thinking, information and communication technology capability, and intercultural understanding for meeting Australia’s future workforce. This project aims to explore the integrated utilisation of VR/AR technologies in the VET system. Innovative vocational education based on VR/AR can provide initial skilling and help workers to retrain as jobs and industries evolve. The scoping study will be used to define desirable extended reality technologies for design and development/evaluation of appropriate skill training platforms in building construction. The CRC is made up of several project partners including Lendlease, Monash University, the University of Melbourne, BlueScope, CSR, Schiavello, Master Builders Victoria and others. If you would like more information or would like to contribute, please contact Philip Alviano via email at palviano@mbav.com.au or phone (03) 9411 4577.


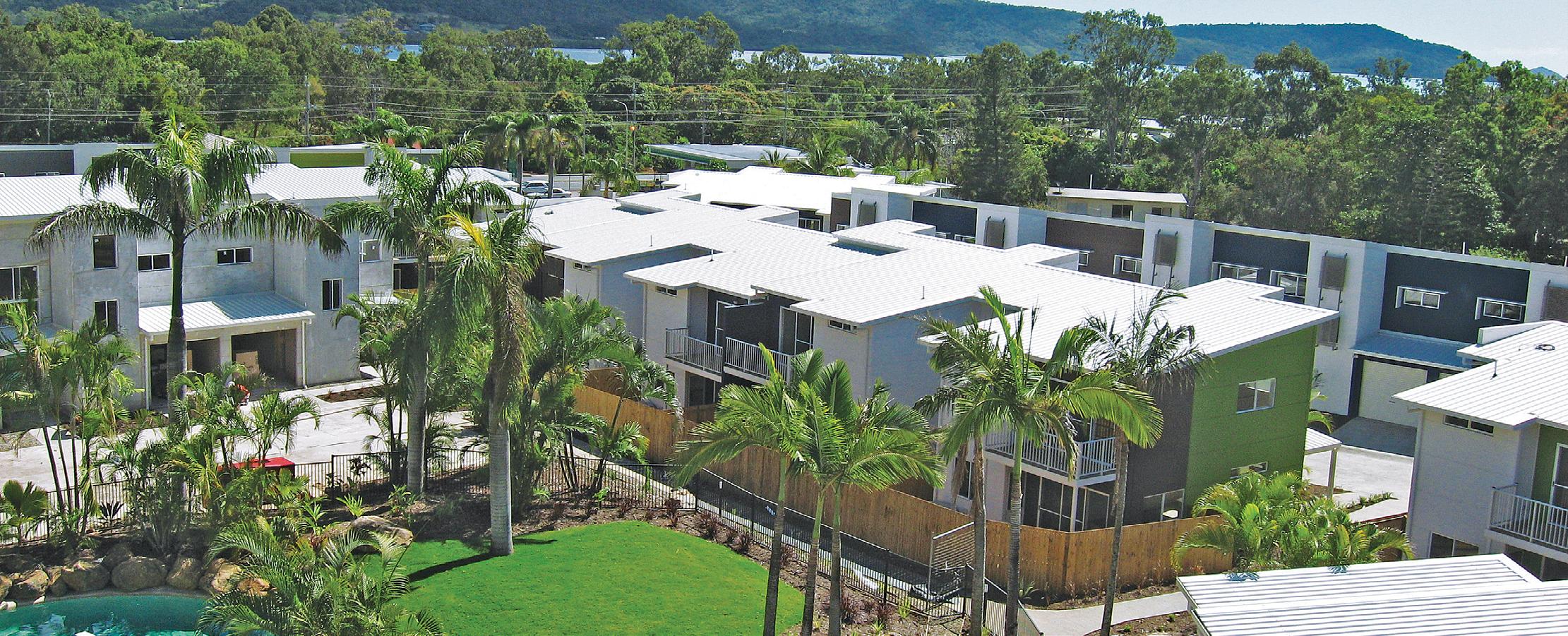
Higher NCC compliance levels for building products in effect
Changes to the National Construction Code (NCC) 2019 Amendment 1 came into effect on 1 July 2021 which formalises the performance solution process. Using CodeMark™ accredited products will save time in developing performance solutions for residential, commercial and industrial projects. In general, the NCC sets out what is allowable and arguably more importantly what is not an allowable building practice. The introduction of A2.2(4) is one measure that will assist in ensuring higher levels of compliance with the NCC. The introduction of A2.2(4) is a way of formalising the performance solution process. It identifies the process and documentation required in order to develop performance solutions. The process demonstrates clear expectations, better information to end users and a greater auditing ability through improved record keeping and documentation. However, this stringency could be challenging given the increased level of documentation. One ready-made solution is CodeMark™. The CodeMark™ Certification Scheme is a voluntary third-party certification scheme for building products that provides a method for verifying that a building product meets the nominated requirements of the Building Code of Australia (BCA). As well as allowing a certificate to attest compliance with relevant Deemed-to-Satisfy (DTS) Provisions, the scheme permits a CodeMark™ Certificate to attest the compliance of a building product with relevant performance requirements of the BCA. CodeMark™ simplifies the performance solution process, as the conformity body who issued the certificate has undertaken analysis to demonstrate the products meet nominated performance requirements. As a manufacturer of innovative building products, the Bondor® Metecno® Group gained its first CodeMark™ Certificate in April 2013. Since then, the Group has witnessed an increasing demand for CodeMark™ certified products, which provide the most stringent form of “Evidence of Suitability” under the BCA, and is top of the list for a possible hierarchy of evidence to be introduced in 2022. The process of obtaining and maintaining a CodeMark™ certificate is not easy, nor can it be fast tracked. This reassures the building industry of the suppliers’ commitment to ensuring better compliance with Australian regulations. Bondor® Metecno® has 13 CodeMark™ certificates for its products with each certificate covering several properties such as structural, fire, energy efficiency and weatherability. The process involves undertaking detailed technical reviews of: • Product technical information and specifications
• Product test results by accredited laboratories • Independent assessments or appraisals • The product’s scope of use • Relevant BCA provisions to be covered The certification process also involves regular and ongoing: • Audits of the manufacturing facility • Audits of any identified critical components • Installation and construction site audits • Review of technical documentation and
CodeMark™ Certificate by an Unrestricted Building
Certifier (UBC) • Suppliers declarations, technical specifications and supply chain control • Regulatory oversight by ABCB & JAS-ANZ (The
Joint Accreditation System of Australia and New
Zealand) When a CodeMark™ Certificate is used to demonstrate compliance with a performance requirement, a lot of the hard work has already been done. Using the right product with the right CoC can save a massive amount of time in the process. Bondor® Metecno® have the largest CoC range covering insulated walling and roofing sandwich panels in residential and commercial and industrial applications. Find out more at http://bondor.com.au/codemark
Quality and safety of the highest priority for Victoria’s Cladding Rectification Program
Victoria’s world-leading $600 million Cladding Rectification Program is tackling the issue of risky combustible cladding on the highest risk residential apartment buildings across the state. Progress of the program has been rapid — to date, Cladding Safety Victoria (CSV) has met with 536 owners corporations and completed detailed inspections on 391 buildings, with work under way or complete on 200 buildings. An additional 53 buildings have signed funding agreements and will be progressed during the remainder of 2021. Independent project managers have been appointed to 246 buildings to assist owners corporations through the complex rectification process to ensure works run smoothly. Sitting at the forefront of these activities is a safety and quality program to ensure cladding rectification works are safe, while quality of works is of the highest industry standard. Leading the way for Cladding Safety Victoria is construction quality and safety manager Jo Tyrrell. With more than 10 years’ experience in the construction industry and having previously worked as the safety health and environmental manager on the Westgate Tunnel Project Eastern Zone from 2017 until joining CSV in 2021, Ms Tyrell brings a wealth of knowledge and experience to the Cladding Rectification Program. “The quality and safety of works is a key priority for Cladding Safety Victoria. A strong culture of supporting a healthy, safe and quality work environment will have a direct impact on the success of the program,” she said. “We’re developing and embedding strong proactive and preventative occupational health and safety and quality culture into all levels of the organisation, and we’re already noticing the positive outcomes achieved as a result. “The clerk of works program is of high importance to CSV and I really enjoy being on site engaging with project managers, builders and contractors. “It is important that CSV leads the way and sets the standards. “I’m always encouraging staff, contractors and others that if something isn’t quite right, or if you’re not sure, to speak up and get involved in quality and safety.” Ms Tyrell is passionate about embedding safety and quality into all levels of the organisation. “Safety and quality are everyone’s business. It doesn’t matter if you work in the office, you’re the cleaner on the construction site or the site manager, if everyone takes an active role, we will see lower risk, higher employee morale and healthier productivity,” she said. “The program has brought together a wide range of talent to deliver outcomes that will have lasting positive impacts on the Victorian community – making Victorians safer by reducing the risk associated with combustible cladding, and I’m proud to be part of this.” Ms Tyrell is also passionate about female participation in the workforce, especially in the construction industry. While working for the Westgate Tunnel Project Eastern Zone, Ms Tyrell was the Chair for the Women in Construction committee. The committee and charter support greater female participation in non-traditional roles. It aims to educate and inform on issues regarding gender equality, set tangible targets to attract and retain women in both blue and white-collar roles, celebrate success while recognising achievements and to bring about change and advancement for women in the construction industry. “I am proud to advocate for positive changes for women in the construction industry, it’s something I have a real passion for,” she said. Ms Tyrell is also a member of the National Association of Women in Construction (NAWIC) and Women in Design and Construction (WIDAC). “I love the challenges of this program. Each building presents its own unique set of challenges — there is no one-size-fits-all approach to cladding rectification,” she said. “I am really looking forward to seeing the clerk of works program embedded as Cladding Safety Victoria’s program of works continues to roll out.” For more information about Cladding Safety Victoria and the Cladding Rectification Program visit the website: https://www.vic.gov.au/cladding-safety.
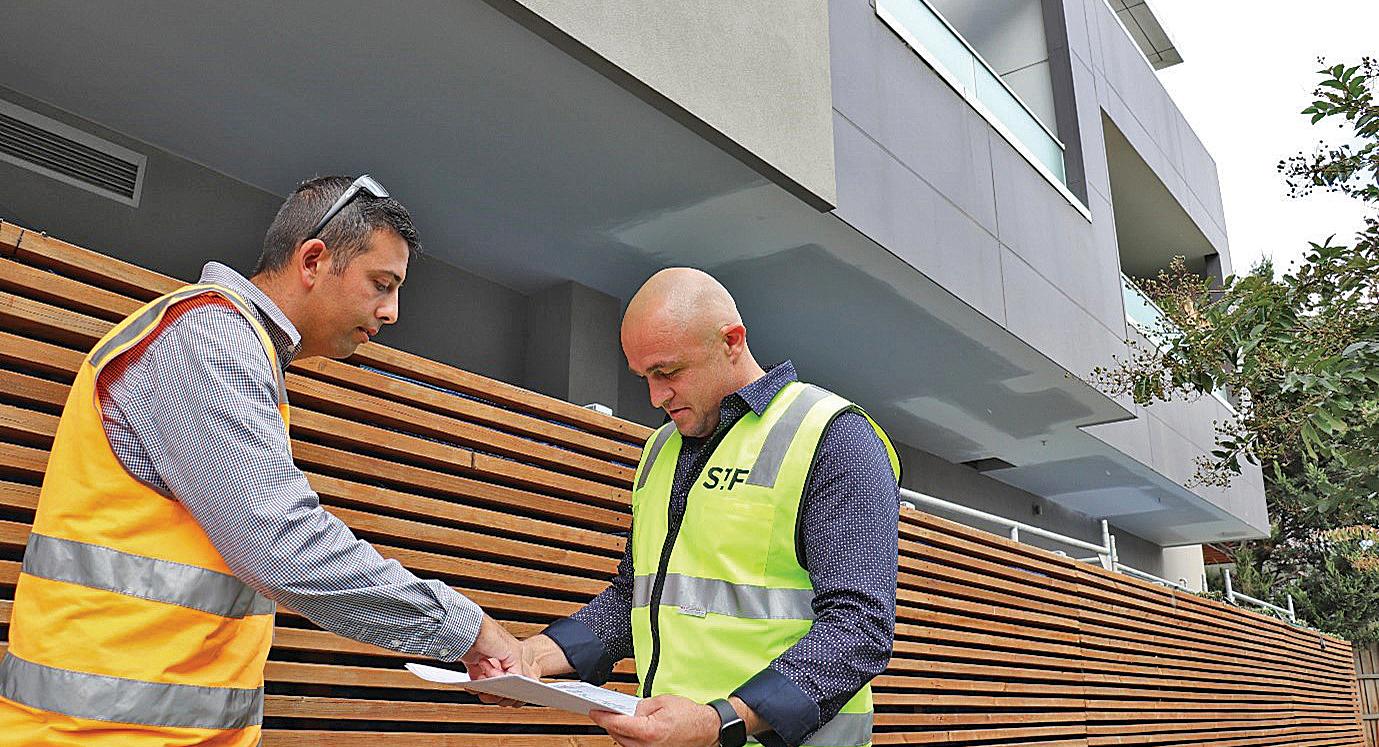
Collaboration with builders the key to success of Victoria’s Cladding Rectification Program
The expertise of builders involved in Victoria’s $600 million Cladding Rectification Program is at the core of the program’s success. To date, there are 200 buildings under way or complete. Cladding Safety Victoria (CSV) Chief Executive Dan O’Brien said innovation and collaboration with builders in the program has been a highlight and driving force behind the program. “The collaboration between Cladding Safety Victoria and builders on site to get the job done has been a critical part of the success of the program,” Mr O’Brien said. “Looking for better ways to work and innovate is continually front of mind for us. For example, it’s been fantastic to see tiered scaffold designs to improve access to façades, and the use of hoists to transport replacement cladding and waste materials. “We’ve also seen some great examples of signage and site noticeboards to assist communication with residents.” St Ferrer project manager Michael Gibbs said communication with residents was critical to the success of a recently completed project at Cheltenham, where existing sprinkler systems were extended from inside apartments to the exterior of the building to protect against fire. “Two weeks before starting on site we had a meeting with tenants, and discussed the work program with them,” Mr Gibbs said. “We discussed the daily work that would be going on at each apartment. “After that meeting, we contacted everyone individually to notify them of the date work would be happening at each apartment. “It was invasive work as it involved working inside apartments, so clear communication and open dialogue was critical.” A site noticeboard displaying the daily work schedule for each apartment was posted in the foyer of the building. Abseils were also used to access exterior sections of the building and reduce further impacts to residents. The safety of residents during the pandemic was also a top priority, apartments were entered only when it was safe to do so and where apartment occupiers consented to the entry. Independent project manager Darren Vella from MBB Consulting ran the tender process for a builder on behalf of owners and superintended works at the building. He said collaboration between all parties was key to the project’s success. “We’re working with all stakeholders to deliver these works for the owners corporation,” Mr Vella said. “We had some apprehensive occupants, as you could understand given that their sprinkler system was being extended from their living room or dining room out to the balcony. Good communication between CSV, owners and occupants, the builder and MBB Consulting was critical from the start.” For more information about the Cladding Rectification Program, visit: https://www.vic.gov.au/ cladding-safety.
SCREW PILES & BORED PIERS SCREW PILES & BORED PIERS

• • • • • • • • • • Concrete House Slab Specialists Multi Unit Site Development Factory Floors and Carparks Bored Pier Holes and Screw Piles Bondek and Suspended Slabs Concrete House Slab Specialists Multi Unit Site Development Factory Floors and Carparks Bored Pier Holes and Screw Piles Bondek and Suspended Slabs
Harbour Concreting Services Harbour Concreting Services 6 Keppler Circuit PO Box 686 6 Keppler Circuit Seaford VIC 3198 PO Box 686Patterson Lakes VIC 3197 Seaford VIC 3198 Patterson Lakes VIC 3197
Phone: (03) 9770 8224 Phone: (03) 9770 8224Mobile: 0418 138 820 Mobile: 0418 138 820Fax: (03) 9770 8225 Fax: (03) 9770 8225Email: admin@harbourconcrete.com.au Email: admin@harbourconcrete.com.auWebsite: www.harbourconcrete.com.au Website: www.harbourconcrete.com.au
CDB-L 50966 | CDB-U 51487 CDB-L 50966 | CDB-U 51487
The perfect timber mouldings for quality home builders
Demand for designer choices in new home builds and renovations has never been higher with customers looking to emulate styles from their favourite social media house flippers, interior designers or TV show. This has been a challenge for many builders who find efficiencies in offering a relatively standard package, but are now looking to adapt their offering and ensure they are keeping pace with these trends and market demands. This is where Intrim Group are helping home builders with the Essentials range of skirting and architraves, in addition to the Intrim range of upgrade options to meet the demand for these stylish finishes. Providing their clients with a choice to create their own visual masterpiece in their new home’s interior with taller skirting, wider architraves and a profile design that enhances their chosen interior style. Taller and more decorative skirting boards along with wider architraves deliver an elegance and sense of luxury missing from standard trims. They also provide visual balance for rooms with taller ceilings, and create a welcoming entrance way to a house. Not only are customers looking for premium skirting and architraves, but they are also looking for wall & ceiling features such as VJ Board and decorative lining boards like Intrim’s new Cavetto Wall. Wainscoting, coffered ceilings and decorative timber moulding finishes on kitchens, feature walls and more are all on trend and in high demand. Timber mouldings have never been so popular and are a large feature of the hugely popular Hamptons style, through to modern, coastal, and country farmhouse. Customers are now demanding this level of finish and options in premium homes and are investing in bigger, bolder and more impactive timber mouldings. Intrim are supporting builders through selecting bespoke ranges for their unique project, providing marketing materials such as brochures, samples for their colour selection rooms and collaborative marketing initiatives and more. As an Australianowned timber moulding specialist manufacturing locally, Intrim are able to lead the market for product design, production, service and quality. Offering products in sizes that are designed for builders such as up to 5.4m lengths on VJ Board Pro to provide a no-joins finish. Investing in stateof-the-art machinery and processes means they can provide fast and high-quality timber mouldings to their clients nationwide. Intrim have displays and people on the ground in Sydney, Melbourne and Brisbane guarantee four days from order to dispatch for unprimed, and six days for primed profiles. “Our products are delivered on site when you need them, as we understand meeting your deadlines is of utmost importance” said Fred Quinsey, CEO & founder. A major game changer for builders is the recently launched exclusive Fast Trim, an idea developed by former chippy CEO Fred. “This revolutionary system of pre-scribed skirting and pre-mitred architraves save an additional 40%-55% of the fix out time. The quality is far superior for a machine scribe versus hand scribe. We understand time is money at the closing stages of the project, and Fast Trim delivers significant labour and cost savings right when you need it.” Fred continued. It’s no wonder Fast Trim has sparked significant interest with home builders since its launch earlier in the year. There has never been a better time to explore the opportunities that Intrim timber mouldings provide — from the Essentials Collection to the Intrim Upgrade options for skirting, architraves, wall panelling, VJ and timber mouldings. To learn more visit intrimmouldings.com.au or call 1800 622 081.
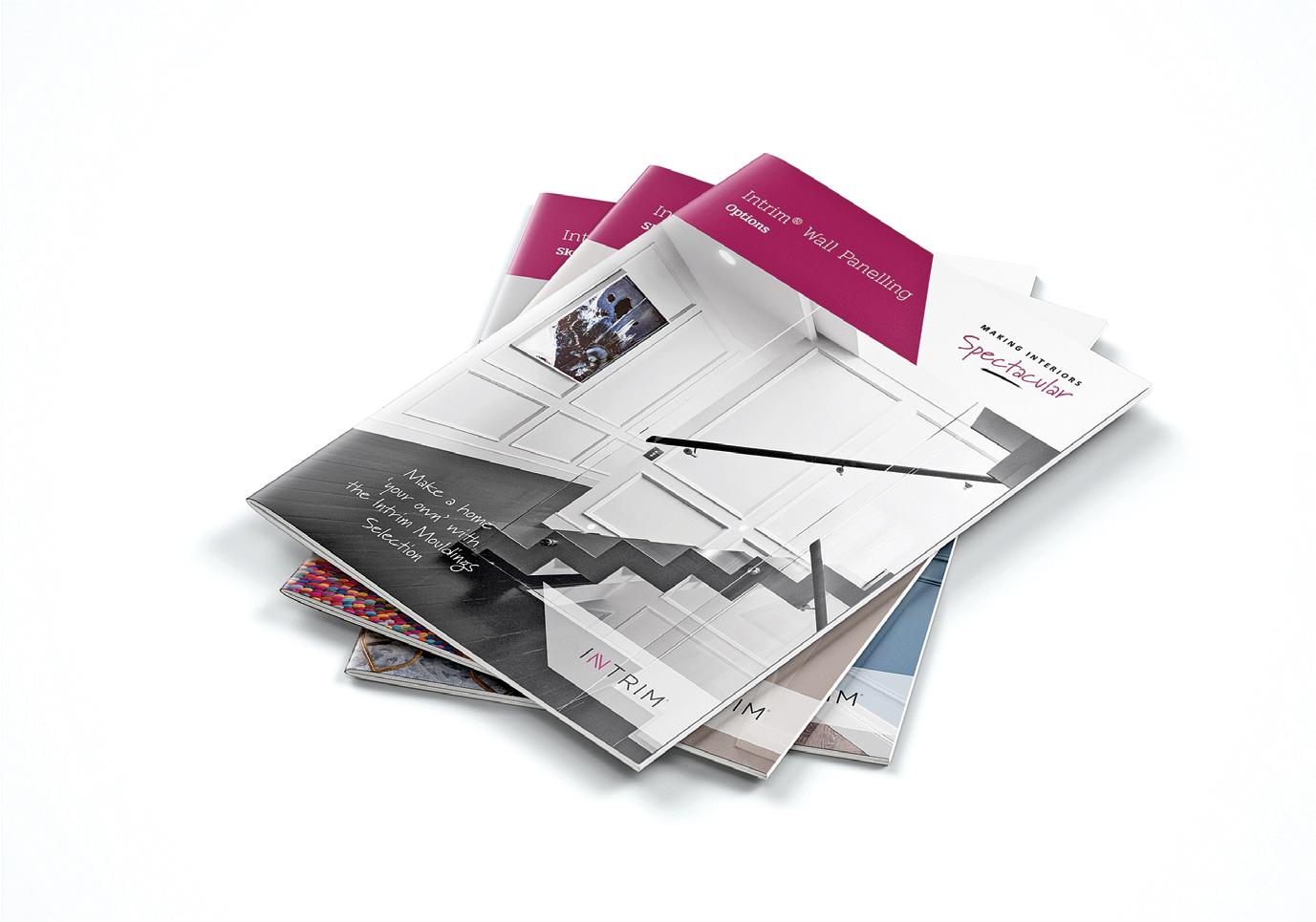
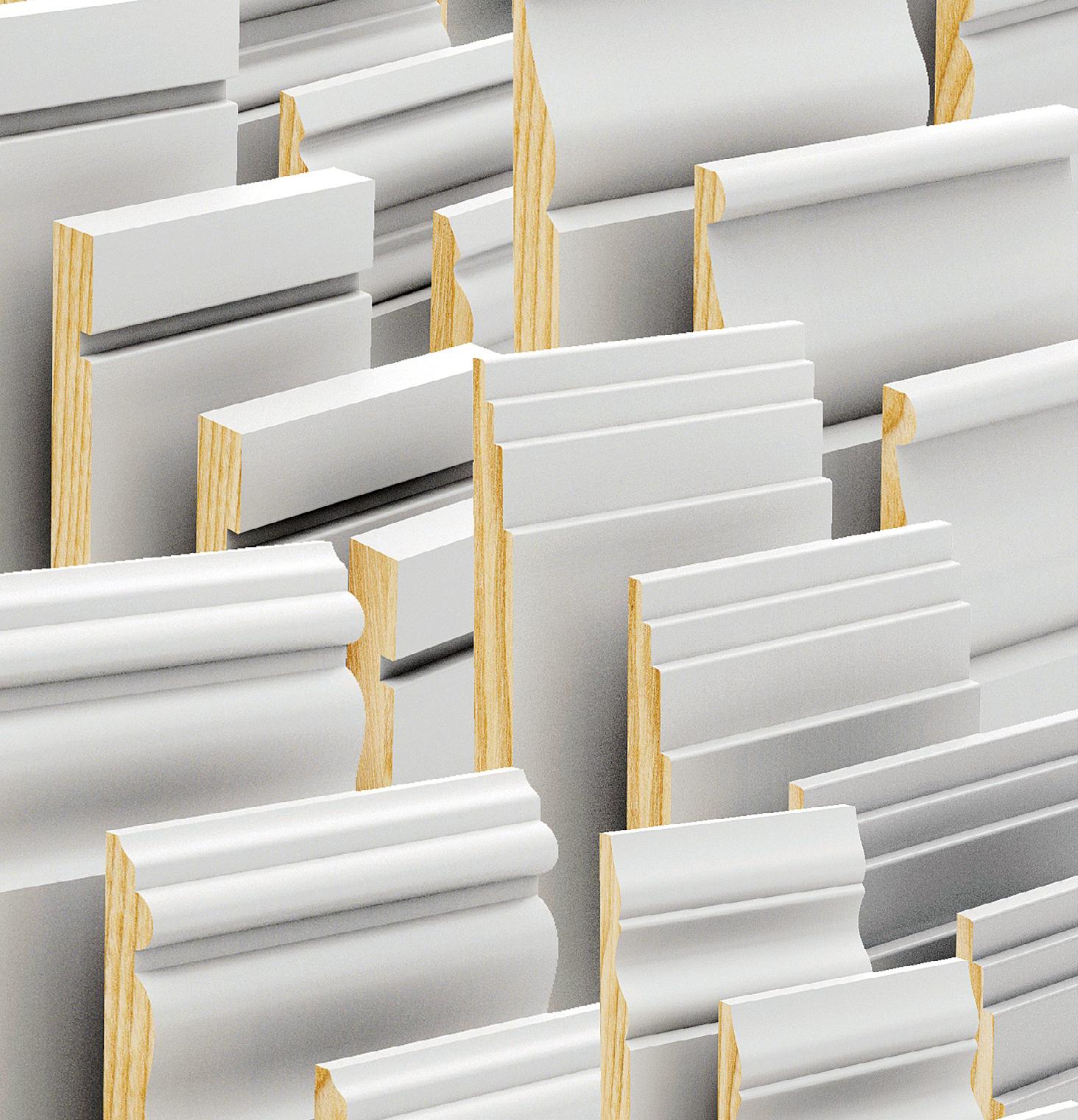
If you would like more information about this topic, please call Jenny Brown, Head of Marketing on 0414 882 982 or email jenny.brown@intrimgroup.com.au Intrim was founded in 1993 by the Quinsey family in Picton and has grown to become one of Australia’s leaders in finely crafted quality timber mouldings, skirting, architraves & handrails for residential homes and commercial buildings. Australian owned and operated, we are committed to manufacturing locally, supporting our local community through job creation and investing in state-of-the-art equipment and processes. Innovation, reducing environmental impact, helping customers make their interiors spectacular are what drives us. We love to share our customers projects using Intrim Mouldings on our website Gallery and Instagram, Facebook, LinkedIn . Find out more at www.intrimmouldings.com.au