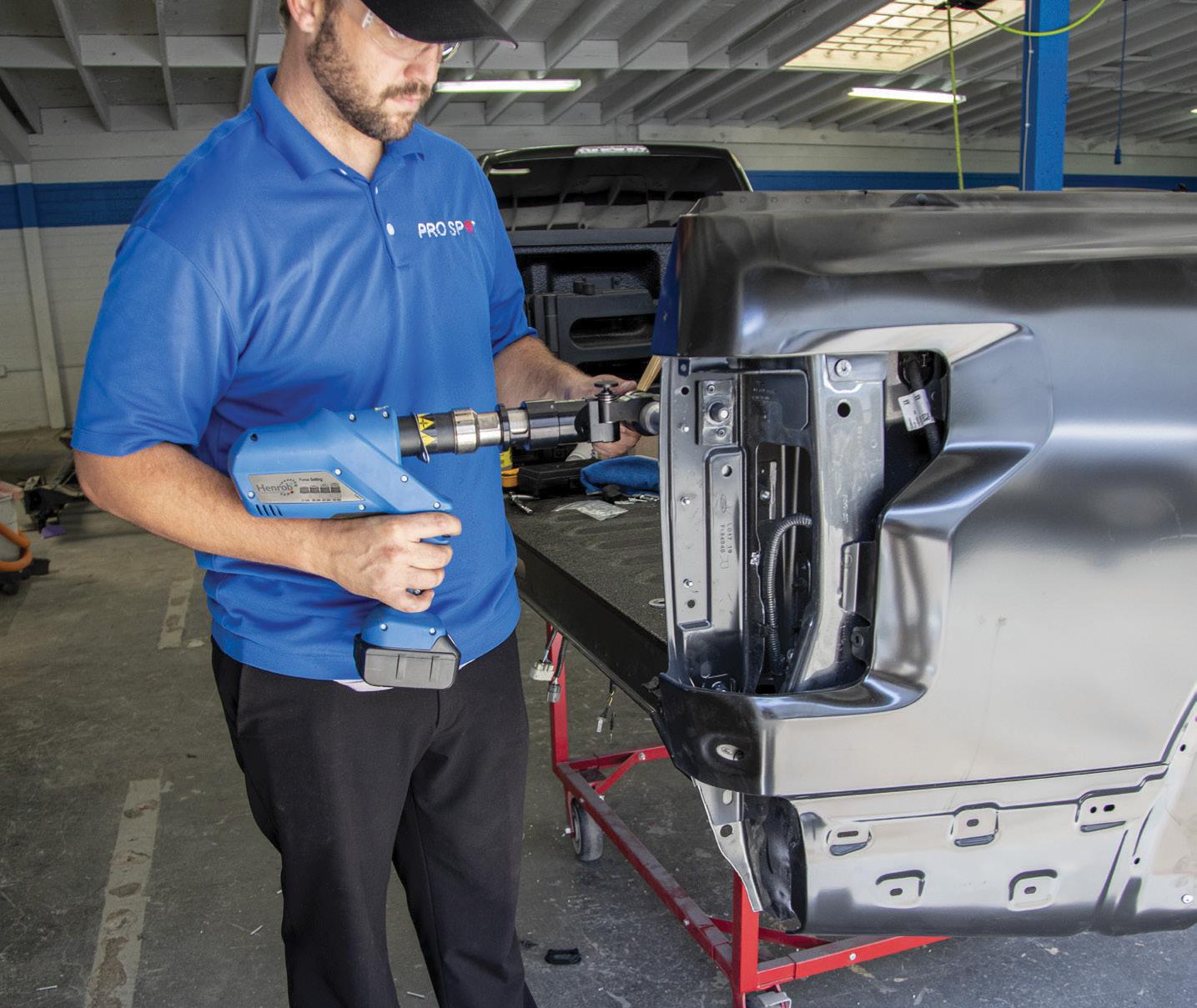
3 minute read
Face Your Fear

from The MSO Project - September 2020
by EndeavorBusinessMedia-VehicleRepairGroup
Tips for Having Tough Conversations
WHEN AN ISSUE ARISES AT ONE OF YOUR SHOPS, THE ONLY WAY TO HANDLE THE PROBLEM IS TO TALK ABOUT IT PROMPTLY
BY DJ MITCHELL
All too often, even the best leaders struggle with conversation. They beat around the bush. They stretch the truth. They downplay the importance of a situation or an event.
Those leaders also tell everyone else how they feel except for the persons involved. They wait for what they feel is the right time to address things. And, all too often, they don’t address things at all. All of these can be detrimental to shop performance, shop morale, credibility, and respect.
When an issue arises the only way to handle the problem is to talk about it now.
I believe most people want to do a good job, and so many times people don’t realize they aren’t doing something right unless they are told. For example, we had a great body man working with us but he was not seeing eye-to-eye with the manager, or so it seemed from the outside. The manager continuously told me how the technician would take two-hour lunches, and how it was hurting the flow of the shop. After this went on for a few weeks, the manager eventually had enough and let the technician go. I was in the area when it happened and the technician blurted out, “Well, if it bothered you so much, why didn’t you say anything?! I may take two-hour lunches, but I work until 7! If you didn’t like it, all you had to do was tell me and I would have stopped!”
Something as silly as not addressing a technician’s lunch hours cost us a great teammate.
When it comes to quality, it should be one of the most important things (if not the most important) in your shop. Yet, so many times I see poor quality go unaddressed.
I often see people tell other employees how so-and-so’s seam sealer is no good, yet we don’t tell the technician we don’t like it. So often we are worried about making someone upset by telling them something doesn’t look quite right.
But, in reality, only three things will happen if you address quality with a technician: 1. They say, “OK,” and they fix it. 2. They disagree with you and say it’s acceptable; you say it isn’t, and they still fix it. 3. They disagree, don’t fix it and disciplinary action is taken.
I can say with 100 percent confidence that option No. 3 is fairly unlikely at most shops.
Issues going unaddressed can often lead to drama on a shop floor. And, drama spreads like wildfire and is unproductive for working toward the goal of the shop. The worst part about having a tough conversation is the dialogue we make up in our heads. If conversations are had with respect, they are easy to have.
I think you’ll find that employees usually appreciate prompt decisionmaking and accountability.
DJ MITCHELL is the vice president and co-owner of MITCHCO Collision Repair, a regional MSO in Florida. He also hosts a podcast for FenderBender’s The MSO Project.
EMAIL: DJMITCHELL@JHCC.COM
Use the Henrob rivet gun with Pro Spot’s Blind Rivet Adapter!

Our Henrob Conversion Kit comes with everything you need to safely convert your Henrob Rivet Gun to the Pro Spot Riveting Platform.
Why Convert Your Henrob? • Install Blind Rivets • Increased Access On F-150 Repairs • Ability To Use Larger Pro Spot C-Arms
Pro Spot Gives Your Henrob Gun A Future.
Part # PRR-HCK on a Henrob Gun

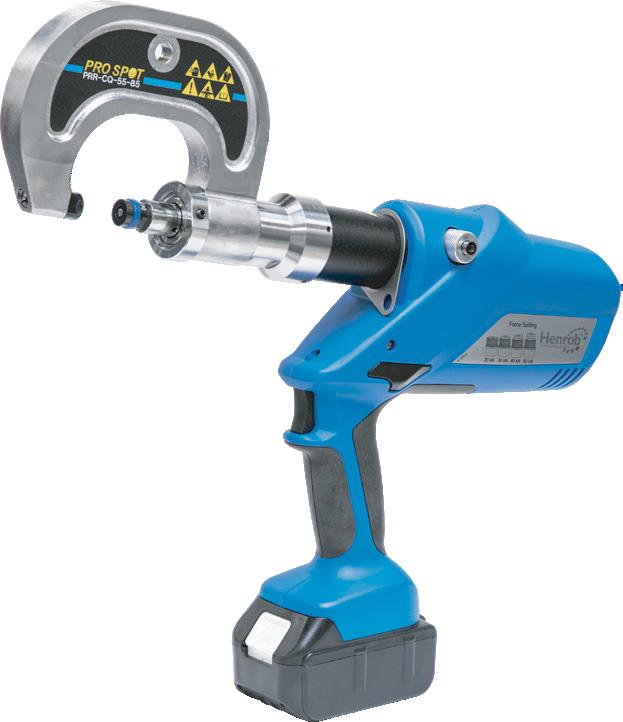
SATA®air vision TM 5000 System
Supplied air respirator is independent from booth atmosphere – for ultimate safety, comfort and perfection.
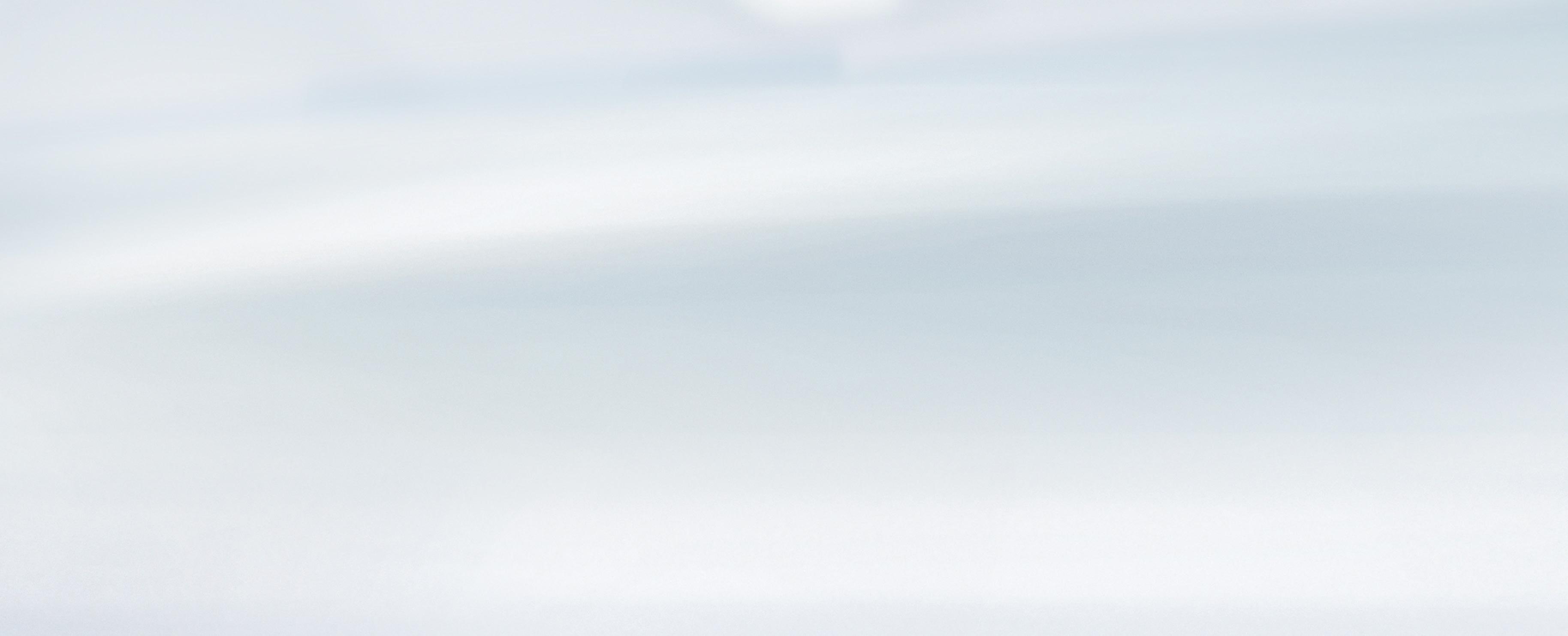
Whatever environment you are working in: Whether you want cooled, heated or re-humidified breathing air or simply looking for absolute safety from particle contamination – with the new add-on modules complementing the SATA air vision 5000 breathing protection system, you can be sure that your health and comfort are both efficiently catered to.
www.sata.com/SATAairvision5000

The NIOSH approval number is TC-19C-0533

Stay healthy
The exclusive independent distributor of SATA products in the US and Puerto Rico Phone: 800-533-8016 www.satausa.com E-mail: satajet@satausa.com