
30 minute read
Should OBD-II be your first step in

from Auto Service Professional - February 2017
by EndeavorBusinessMedia-VehicleRepairGroup
Engine diagnostics
Should OBD-II be your first step in diagnosing an engine management issue? Yes, and here’s why...
When a check engine light comes on, having a game plan for understanding the cause and fixing it quickly is critical for your customer’s satisfaction and profitability for you. Having the correct scan tools at your disposal and running through the 10 diagnostic modes to OBD-II are keys to your success.
By Jeff Taylor
We can’t possibly have all the tools that we need to repair every vehicle that comes into our shop, even if we concentrate on only a couple of makes or manufacturers. There are simply too many dedicated tools required today to perform all of the required tasks on today’s engine, transmission and drivetrain systems. Even a simple water pump service can now require highly specialized tools, but dealing with a check engine light doesn’t always require the factory scan tool, even if you have one available.
It’s important to remember that the OBD-II system’s responsibility is to turn on the check engine light and alert the driver if there is a failure in the vehicle’s emission control systems, and it’s this fact that made me change my diagnostic approach.
I typically start to diagnose a check engine light (malfunction indicator light/MIL), by grabbing one of my generic scanners first. I check the OBD-II system to see what information is available to properly diagnose the issue, allowing me to base my decision on this data.
Will I need a factory scanner (that I may or may not have access to) or tell the customer that I don’t have the factory scan tool needed and possibly send them back to the dealer?
There are times that you are going to need a factory tool to complete a diagnostic or need some form of bidirectional control, but research has shown that almost 85% of the emissions-related MIL complaints can be dealt with using nothing more than an OBD-II diagnostic capable scanner.
For example, intake air temperature and coolant temperature should have similar readings after a cold soak. The OBD-II system also has to keep track of these test results, the operating conditions when it ran the tests and other information that can potentially be used to diagnose a MIL light issue. There are 10 diagnostic modes to OBD-II that we can use and these modes are typically available on that generic scanner that you already have, but it’s important to understand what information each of these modes provides us and how to interpret that information so we can use it in our diagnostic process.
Mode $01... Request the current powertrain diagnostic data. (The $ sign in the
mode number indicates it’s a hexadecimal number used by the computers involved.)
Before any scan tool can communicate it needs to know what language the vehicle speaks. CAN, ISO 9141-2 and J1850 PWM are examples of communication protocols used. Once the scanner understands the vehicle’s protocol, the PCM will allow the scanner access to current live powertrain data values or PIDs (parameter identification). This data must be actual sensor reading, not default, substituted or enhanced data that some manufacturers’ factory data streams may provide.
Many manufacturers’ factory data streams (Fiat/Chrysler and Honda come to mind) may show false information that the PCM is supplying because it is aware of a failed sensor or skewed data and still wants the vehicle to run properly for the customer. It just bases the false information from another input or sensor but it doesn’t tell you that when you are looking at the factory data.
The vehicle’s system readiness test status and the MIL status are also displayed in this mode. The fewer PIDs that are selected the faster the data refresh rate will be, and having genuine sensor data is a real help.
Mode $02... Request the freeze frame information. Mode $02 provides the data stored at the time the fault was detected by the OBD-II and when the OBD-II system turned on the MIL. Mode $02 output only shows the data from when the code set or matured and caused the MIL. This is important to note, because it may not provide information on when the actual problem started, but it provides clues and these clues can still be useful in replicating the failure conditions.
I frequently use the freeze frame data in Mode $02 to diagnose a Toyota Matrix P0171 lean code in the winter. These vehicles typically aren’t running lean when I see them, but the Mode $02 freeze frame data shows the outside temperature when the code set was -20 degrees Fahrenheit and the intake manifold gaskets are as hard as rock and unable to seal properly (that’s why it always runs fine by the time I see it).
Be aware that the freeze frame data can be overwritten by higher priority DTCs, (a misfire code, for example, will overwrite a lean code) and all of the Mode $02 data be cleared when the codes are cleared.
Mode $03... Request the emissions-related diagnostic trouble codes. Mode $03 allows our scanner access to the stored DTCs in the PCM. These emissions related codes will be
“P0, P2 or P34-P39” generic codes or “P1 or

Among the numerous tools in my shop’s arsenal, these are my three favorite generic OBD-II scanners that I use, even though one is a specialized VW/Audi tool (its OBD-II capabilities are fabulous).

This Mahle scanner provides quick access to the OBD-II system and will even provide a printout to give to the customer before and after a repair. P30-P33” manufacturer specific OBD-II codes that have turned on the MIL. tors status, distance travelled while the MIL was on, number of engine warm-ups, engine run time, oxygen sensor data, on-board monitoring test results and pending codes.
I try to record as much of this information as possible for future reference after the repair (I use screen capture or take a picture with my phone). Performing a values and adaptive memories that may cause some driveability issues unless properly road-tested. Certain vehicles will not allow a clear/reset if the proper conditions aren’t met (Chryslers and Hondas both need the key on but engine off).
Mode $05...Request the oxygen sensor monitoring test results. This mode was intended to allow access to the PCM’s oxygen sensor monitoring values and test results. Different manufactures used many different and unique methods to calculate the O2 effectiveness and operation (one mode may convert that data to the same standard units of measurement).
This mode is only used if the vehicle is not using CAN (controller area network) electrical architecture. If it is a CAN vehicle this

Mode $04... Clear/reset the emissionsMode $06...Request the on-board monirelated diagnostic information. When toring test results for specific monitored you want to clear a stored code or codes, systems. Mode $06 provides access to the you enter into this mode to do it, but be OBD-II test results of the specific components certain of exactly what you want to do before and systems that it has tested. proceeding. It will show the results of both continuously
Clearing/resetting the memory will not monitored (misfire monitoring for example) just turn off the MIL but also erase the freeze and non-continuously monitored systems frame data and much more. (EGR or evaporative systems for example) in
Clearing/resetting will reset the monithis data.
data is now stored in Mode $06. clear/reset may erase This is the opening screen of the Mahle OBD-II diagnostic panel showing some learned engine the 10 different modes that can be accessed.

Circle 108 on Reader Service Card

Sometimes this data may need to be
I like to look at Mode $06 data to see just how bad a particular component has failed; this is very helpful in P0420/430 catalytic failure codes. Mode $06 is not only useful for finding Ford misfires; it’s also really handy at identifying other issues that may appear after clearing a code. I like to take a look at Mode $06 and see From this screen capture you can see that there are no permanent codes (this example is a 2006 Saturn), but you see Mode $03 codes and the Mode if any other tests are $07 freeze frame data and the code that set that data. close to failing even
Mode $06 shows actual test results and related to the code or issue that I’m diagnosinformation but only if the readiness monitors ing or have just repaired. status from Mode $01 shows that the monitor Many times, a misfire code will shut off the is complete. enabling criteria for many other tests, and it’s
This is important to remember because good to have the information that the evapothere may be data there before the monitor rative, or EGR system, was close to failing has run to completion and this may just be or that the catalytic converter was already garbage data until the monitor has to run to borderline to warn a customer of another completion. impending repair.
though they are not converted to usable values if your scan tool Mode $07... Request the emission-related doesn’t do it automatically. diagnostic trouble codes detected during
Many manufacturers’ websites provide current or last completed driving cycle. This information on how to do this and what the mode shows the codes that are pending or values mean. For example, Ford’s OBD-II waiting to mature. Mode $07 was designed to information is free and a valuable resource aid in diagnostics after a repair by showing a that explains how systems are tested as well test fail after one drive cycle. If the test fails (www.motorcraftservice.com/FreeResources/ again a related DTC will be stored. But if the OBD). fault is not seen again for 40 to 80 warm-up

Mode $06 isn’t just for Ford misfires. This view shows that the EGR system barely failed and after testing the operation of the EGR valve it was found that the EGR passages were plugging up.
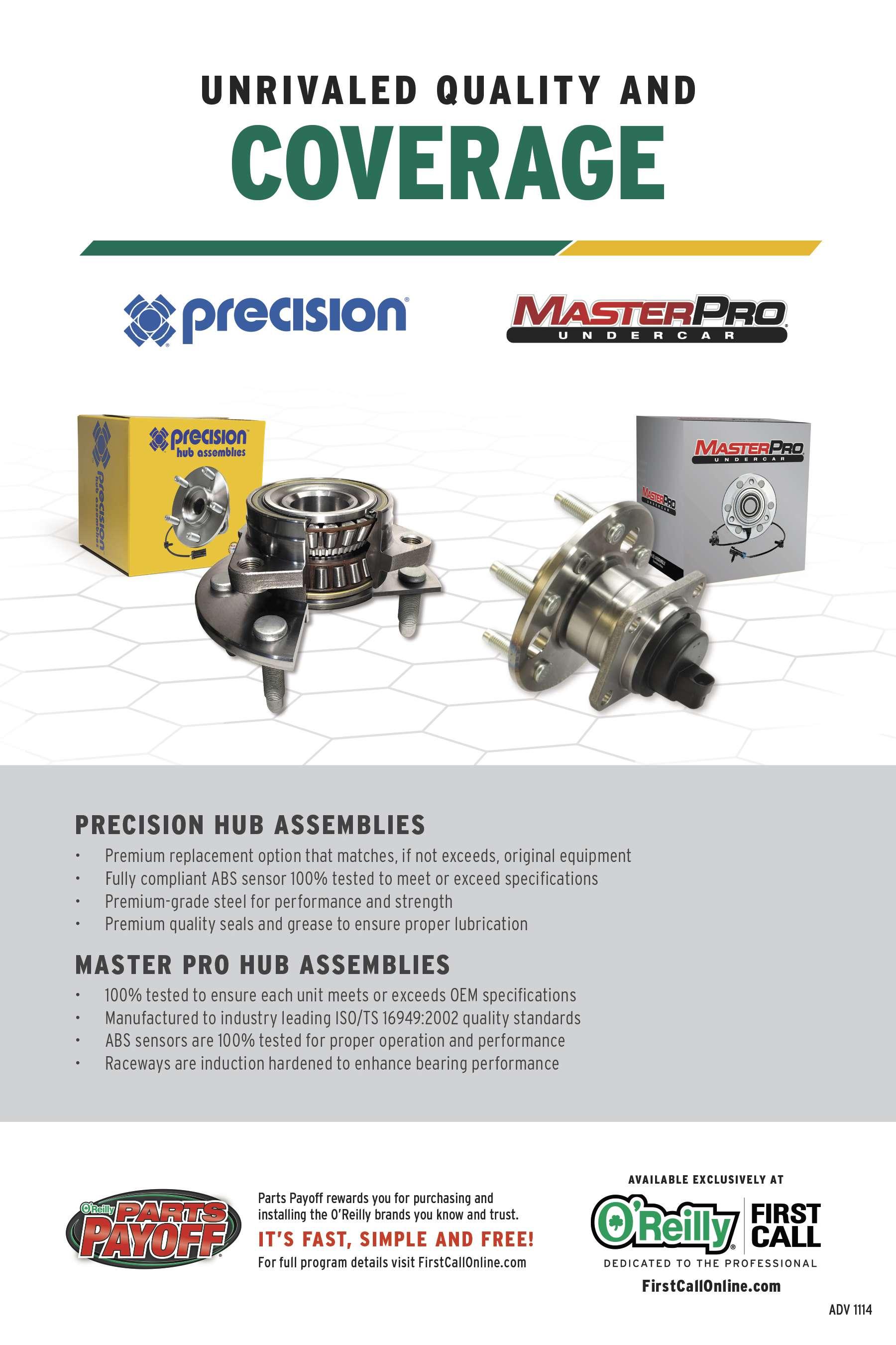
cycles the code will clear automatically. But if the test fails again during those cycles then the DTC will set and the MIL will be illuminated.
This mode should always be looked at before the codes are cleared as this information is cleared when a Mode $04 reset is performed. Pending codes that are unrelated to the hard code that turned on the MIL should be noted and mentioned to the customer before any repairs are performed.
Mode $08... Request control of on-board system, test or component. Mode $08 is intended to allow the scan tool to perform some bidirectional control of an onboard test or component. Typically it will allow you to seal the evaporative system to check for leak testing. This mode is really hit or miss and doesn’t usually do anything.
Mode $09... Request vehicle information. Mode $09 provides the vehicle’s VIN, calibration IDs, calibration verification numbers, and other useful data that includes in-use performance tracking. In-use performance tracking logs the number of times that specific component monitors (catalysts, primary 02’s, EGR, AIR, and evaporative system) ran to completion, and it also shows how many times the conditions to run that monitor were enabled and the total number of engine starts.
This information is useful in verifying a repair and knowing if something was inhibiting the enabling conditions (failing thermostats are very common at stopping monitors without trouble codes being generated). I like to look at this area to make sure that the monitor counters are increasing. If they seem to be fixed or display a very low number relative to the vehicle age or mileage, I am often suspicious of a car that has some form of tune or non-factory PCM software and this can help in your diagnostics.
Mode $0A (10)... Emission-related DTC with permanent status. We know that the MIL light can be turned off either by passing the prescribed number of tests without a fault reoccurring or having the fault repaired and using Mode $04 to clear the MIL. But just
Mahle provides an OBD diagnostic report that provides not only all the Mode $06 data, but codes as well. This is very helpful in explaining to customers that other systems may be close to failing or shut off by certain codes that already exist.

because you or someone else has turned off the MIL, that doesn’t mean that the PCM has forgotten that any codes were set. Starting on some 2009s and all 2010 and up vehicles, Mode $0A remembers that there was a fault serious enough to request the illumination of the MIL and keeps this information in a nonvolatile random access memory (NVRAM).
This NVRAM can’t be erased by using Mode $03 or a battery disconnect and it can hold up to four codes for over a year until the diagnostic executive part of the PCM erases it after it performs a test verifying that it’s been repaired (typically passing three consecutive trips without fault).
Finishing up and putting this all in practical terms, and using it in the shop. Here is a scenario that I have encountered more than once. It’s a 2011 Ford Escape with a 3.0 V6. The customer’s issue is that it drives fine but the MIL is on.
The first thing I do is hook up an OBD-II capable scanner and look for codes. At this point I have used Mode $01 and Mode $03. It displays the code P0420, a catalytic efficiency code for bank 1. I then look at the freeze frame data (making sure that freeze frame data is for the P0420 code) and check the operating conditions when the MIL was turned on.
The Data in Mode $02 ( freeze frame) shows me that the vehicle was at operating temperature, in closed loop, on the highway and the fuel trims on both banks were at about +/-5% (which is OK). From this point I will go to
Mode $01 again to make sure the catalytic monitor is ready and run to completion, then off to Mode $06 to look at the catalytic test data. In this case I am able to compare bank 1 with bank 2. Mode $06 data tells me that bank 1 failed badly, while bank 2 is well within specs.
Before I leave the Mode $06 area, I look over all the other test data to make sure nothing is close to failing (O2 values) just in case something is just on the borderline. At this stage I have pretty much decided that I am going to be looking at a converter, but I go to Mode $07 first and see if any other codes are pending.
From here I will check and see if there is any Mode $0A codes other than the P0420 that may have been cleared recently. If misfire, thermostat or O2 codes are still stored, they could be clues as to why the P0420 is setting. In an example case, there were no issues and only the P0420 is set.
The last step is to look at Mode $09 and see if the vehicle has had any issues running this test, and it hadn’t, in fact the test had run over 1,500 times. I have made my decision: It needs a new converter. Most techs are already using several OBD-II modes, but in many cases techs are quite unaware of all the information that is available. Using as many of the 10 OBD-II modes as possible can help in diagnostics, verifying a repair successfully and accomplishing that repair without the use of a factory scan tool.
Jeff Taylor boasts a 31-year career in the automotive industry with Eccles Auto Service in Dundas, Ontario, as a fully licensed professional lead technician. While continuing to be “on the bench” every day, Jeff is also heavily involved in government focus groups, serves as an accomplished technical writer and has competed in international diagnostic competitions as well as providing his expertise as an automotive technical instructor for a major aftermarket parts retailer.
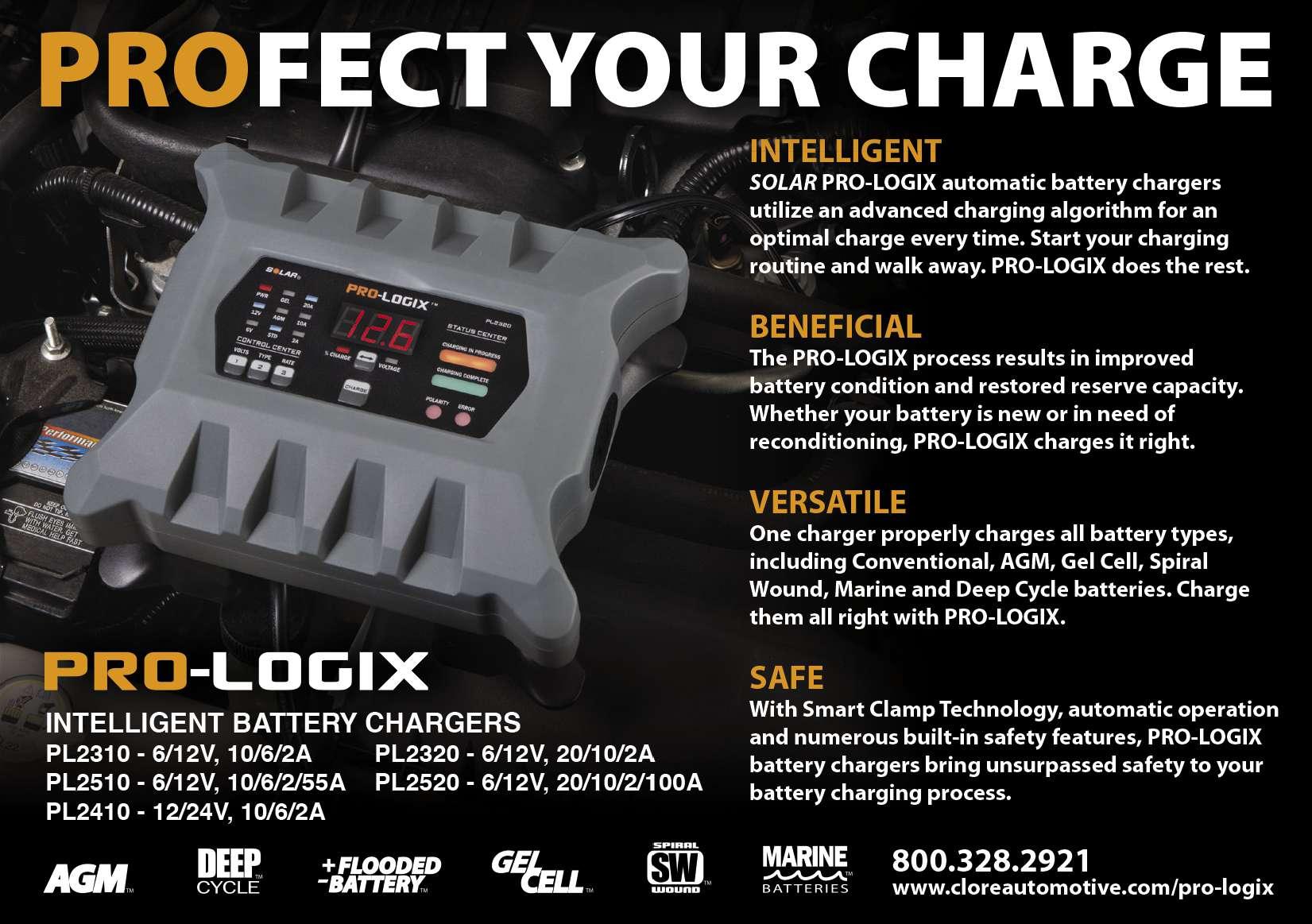
Luxury car and high performance brakes
Premium vehicles = premium brakes and premium dollars for your shop
Owners of luxury and high performance vehicles expect topnotch braking performance. In addition, these customers likely have an appreciation for high-quality parts, workmanship and attention to detail. As a result, they are willing to spend what is necessary to have their vehicle’s brake job done properly. This customer base represents a solid profit opportunity by giving them what they want.

By Mike Mavrigian
Premium-priced high-performance luxury cars tend to push the envelope in terms of braking system performance. While a disc/drum or disc/disc system found on any production vehicle is designed to provide safe and reliable braking, luxury performance cars tend to be outfitted with “spirited” driving in mind. As engine power increases, accompanied by the potential for higher speed operation, there’s more demand on the brake system, requiring the system to meet these challenges.
As a result, expensive luxury/high performance vehicles tend to take advantage of braking components that provide a higher level of performance. Rotors tend to be larger in diameter, and sometimes made of more exotic materials than are found on less expensive cars.
Many OE high-end luxury/high performance braking systems feature larger diameter rotors and multi-piston calipers for superior stopping power under higher speed situations, providing a larger pad contact area and often utilizing fixed caliper designs that feature multiple opposing pistons. In addition, innovations such as brake pad wear sensors and electronic parking brakes are more common.
After all, when the customer is paying big bucks for his or her new ride, they expect all of the latest bells and whistles.
Brake pad materials are routinely selected by OEMs to maximize braking performance. With regard to high-dollar luxury and high performance vehicles, customers expect superior braking capabilities, and the vehicle makers tend to utilize the best materials available, regardless of cost, in order to maintain maximum braking performance and to avoid issues of squeals, premature wear and/or brake dust accumulation on incredibly expensive alloy wheels.
When dealing with this demanding market, you simply cannot arbitrarily replace pads with whatever is readily available from a local supplier or at the lowest cost.
Pads intended for high performance European and some domestic vehicles likely use a semi-metallic or low-met material in order to
generate a higher coefficient of friction. Some ultra-exotic applications employ carbon/ carbon rotors and pads or other unique application-specific pad compounding.
The evolution of semi-met materials has come a long way over the past few years to accommodate the higher energy generated during braking.
Depending on the application, high performance fitments may feature ceramics, Aramids or some application-specific semimetallic formulation.
Stopping power is of obvious importance on any vehicle application, but for “spirited driving,” the customer will expect and demand consistent braking with a high degree of fade resistance, so don’t compromise.
Bear in mind that these customers are not going to be as budget minded as others, so regardless of cost, always select the highestperforming pads for these discriminating customers.
The point we’re making is that high-end/high performance applications require pads that are designed for specific makes and models.
Rotors
High performance vehicles (this may include both late-model OEM vehicles that push the legal limits in terms of horsepower, torque, handling and braking, as well as custom vehicles built with these attributes) require high performance brakes. As part of the system, brake rotors must be able to withstand the rigors of performance use. In addition to potential rotor wear, issues of concern involve cooling channel rust. As these heat-evacuation channels become clogged, the rotor tends to absorb more heat. As heat increases, the chances of disc cracking, wear and warping increase.
If you discover rotor warp, it’s best to replace the rotor(s) rather than resurfacing. Machining the disc reduces its thickness, making it even more susceptible to warping and cracking due to overheating. When you’re dealing with a mega-dollar vehicle, don’t cut corners. Buy the best rotors available that meet the same material and design criteria as the original equipment rotors.
Premium performance rotors may feature a high carbon content. Citing Centric Parts’ offerings as an example, a proprietary blend of molybdenum and chromium is used in the casting process, which boosts braking power, reduces potential squeal, resists stress cracking under extreme braking use and aids in heat dissipation.
From an appearance standpoint, this formula also resists oxidation/rust, making

Some high performance rotors employed by OEMs feature an exotic disc construction formula such as carbon fiber-infused material. The point is that not all rotors are simply made of “cast iron.”
the rotors looking good for a longer period of time, as the increased chromium and carbon content is also more resistant to oxidation.
Raybestos R-300 high performance rotors represent another example of high-carbon metallurgy that improves cooling and vibration-cancelling. High performance aftermarket rotors are offered by a number of manufacturers including Centric Parts, Brake Parts Inc. LLC (Raybestos) and others.
Whether replacing with new OEM or aftermarket components, these vehicles require the highest quality rotors, pads and calipers that provide a direct-fit.
Today’s quality aftermarket suppliers

Aftermarket performance rotors are offered in a variety of designs. Examples shown here (from left to right) include slots, slots and cross-drilled holes and cross-drilled holes only. Note that non-friction surfaces are e-coated to prevent rust and to maintain a like-new appearance.
offer quality and performance that meets or exceeds original equipment.
Rotor coatings
Preventing rust buildup on a brake rotor offers two benefits: to improve visual appeal when the rotor is visible behind an alloy wheel, and to minimize corrosion that can lead to clogging the vents and overheating. While non-frictional surfaces such as rotor hats and vents can be treated with a variety of methods including electro-coating (often referred to as e-coating and is usually black in color), frictional surfaces may be zinc coated.

These cutaway views illustrate curved vanes. Rotors with curved vanes should always be mounted so that the outboard end of the vanes aim toward the rear of the vehicle. This provides a superior pad bed-in and bite, while maintaining a rust-free appearance for a much longer period of time and use.
According to Centric, e-coating is an advanced electro-statically applied finish that has been engineered to withstand 400 hours of salt spray testing without corroding. That means much longer service life, especially on icy, salt-encrusted winter roads.
The coatings used on the Raybestos R-300 rotors involves a “black fusion” coating on the hat and a “grey fusion” coating on the disc and vane surfaces rated as withstanding 300 hours of saltwater exposure. Many performance rotors available today feature similar coatings that greatly extend the appearance factor.
If the disc area is coated, it is not recommended to remove this during installation. During installation, it’s advisable not to clean the disc area with a strong solvent such as brake cleaner. Instead, wash the rotors with hot water and Dawn dish washing liquid, followed by a rinsing. This will remove any residual oils and contaminants without disturbing the coating.
Vented and solid rotors
Vaned/vented rotors are designed to release heat from the rotor. As the rotor rotates, the vanes pump cooler air from the center

of the wheel, which carries this air through
the vanes, picking up heat along the way
and removing a percentage of that heat from
the rotor. A rotor featuring straight vanes is
bidirectional and may be installed on either
the right or left side of the vehicle.
If the rotor features curved vanes, it is directional and must be positioned properly to achieve full heat-dissipation performance, mounted so that the vanes curve towards the rear of the vehicle. This causes hot air to be pumped from the center area outwards (pumping air from the inner diameter toward the outer diameter).
Rotor drilling/ slotting
An increasing number of high performance brake rotors feature disc slots, cross-drilled holes or a combination of both. While many enthusiasts are attracted to this feature from a visual perspective, these design elements serve a purpose.
Both help to keep the pads clean by providing an escape path for pad residue as the pads wear, and to reduce the gas-ramping buildup between the pad and rotor emitted by pad material resins, reducing the potential “hydroplaning” effect as the pad pushes against the disc and aiding in keeping wheels clean by reducing pad dust buildup and improving brake pad “bite” for superior braking.
Slots or holes essentially serve the same purpose in terms of a self-cleaning attribute, with cross-drilled holes also aiding in heat release. If holes are featured, they should include a slight chamfer to reduce the chance of stress cracking.
Rotor disc slots are often machined at an angle relative to the hub centerline, making the rotors directional (dedicated left or right). While some OE rotor

manufacturers may specify that slots should sweep away from rotational direction, in most cases, a slotted rotor (whether the slots are straight or curved) should be
Photo courtesy Raybestos
Raybestos’ R-300 performance rotors feature an “S-Groove” slot design that simultaneously allows for out-gassing on both leading and trailing ends of the pad’s swept area while maintaining maximum surface contact. The slot design is also non-directional, allowing the same rotor part number to be installed on both sides of the same axle. The high carbon rotor features a “black fusion” corrosion-preventative coating on the hat and a “grey fusion” corrosion-resistant coating on the disc, making them able to withstand 300 hours of saltwater exposure, the company says. mounted so that the grooves sweep forward at the outer perimeter of the rotor, allowing the end of the slots closest to the outer disc edge to contact the pads first.
In addition, some performance rotors feature a mixture of slot angles (forward angle, rearward angle and straight) as a design element.
Unique slotting configurations are
also offered, such as Raybestos’ R-300 S-Groove slot designs that are non-directional (non-axle-specific).
Multi-piston calipers
Many high performance brake calipers will feature multiple pistons. As opposed to a single-piston caliper, this provides greater
and more even distribution of pad application force along the length of the pad, reducing or eliminating the potential for tapered pad wear. Some performance calipers will feature equal-diameter pistons, while others will feature pistons of progressively small-to-large piston diameters.
When dealing with a caliper that features a staggered variation of piston diameter, the
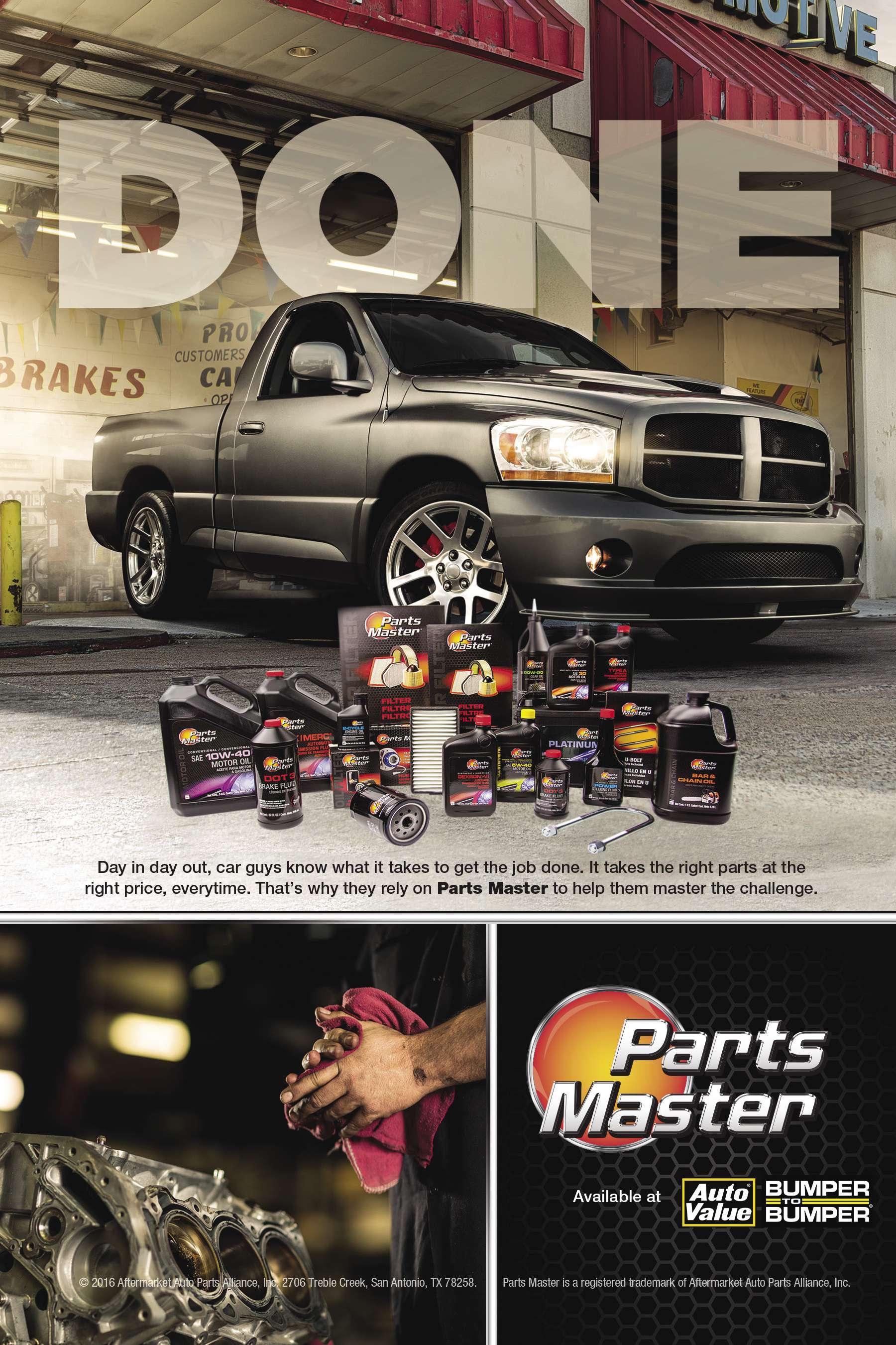
caliper must be mounted so that the smaller piston end is closer to the entrance or “attack” of the rotor, with the larger piston end toward the exit path of the rotor. The smaller piston end creates the beginning of the clamping force and the larger piston end provides slightly greater clamping force, the combination of which helps to compensate for pad taper wear.
A multi-piston caliper that features different-diameter pistons must be mounted so that, as noted earlier, the rotor travel path hits the smaller pistons end first. This means that the calipers must be dedicated for the right or left side of the axle.
This staggered piston diameter design also helps to alleviate any potential for pad resin gas “pressure ramping” effect.
Photo courtesy of Raybestos

In an effort to eliminate pad squeal, vibrationdamping shim layers are featured on pad backing plates. Shown here is an example of Raybestos’ Element3 pad that utilizes multiple shims of steel with vulcanized rubber in-between and a thermo-set adhesive, the combination of which serves to dampen vibrational harmonics.
This pressure begins just after the point of attack as the pad meets the rotor, and continues to progressively build along the pad until it can escape at the exit end of the pad. Depending on the brake pad compound, as the pads compress onto the rotor, heat builds and resins in the pads react and gases are released to the pad surface, building a sudden “pressure ramp,” which forces the pads away from the rotor, which pushes the pistons back into their bores. A staggered piston setup uses the larger diameter piston(s) at the exit portion of the pad to counteract this gas-push by applying greater force behind the pad. If the rotor disc design includes a series of slots or holes, this provides a faster escape path for these gas buildups, which function in unison with staggered piston calipers.
Performance brake fluid
It’s time to pay attention to brake fluid, especially from a performance standpoint.
All too often, a brake system is filled, bled and then forgotten. Age, humidity, operating temperature and potential air ingestion can begin to take its toll.
There are two basic types of brake fluid: poly glycol and silicone. Glycol fluid (DOT 3, DOT 4 and DOT 5.1) is “hygroscopic.” That means that the fluid is capable of attracting and holding airborne moisture.
NOTE: Do not confuse DOT 5.1 with DOT 5 fluid. DOT 5 fluid is silicone, while DOT 5.1 is simply a high performance DOT 4 type fluid with a slightly lighter viscosity and generally a higher wet boiling point.
As water begins to be absorbed into the fluid, this has two effects: it begins to lower the wet boiling point, which diminishes the fluid’s ability to obtain solid and dependable braking performance. Water absorption also creates the potential for holding water inside the system, which can contribute to corrosion of steel brake lines and can lead to wheel cylinder and caliper piston sticking, especially for vehicles that are stored for extended periods.
Because of the propensity for glycol fluid to absorb moisture, it’s important to change the fluid on a regular basis. Brake fluid does not last forever... it needs to be changed to maintain proper braking performance.
Silicone brake fluid (DOT 5) is not hygroscopic, so it does not absorb moisture from the air. Silicone fluid is also not harmful to painted surfaces, as compared to glycol fluid. That’s why some owners prefer silicone (to prevent paint damage in the case of a leak or spill) and because many people assume that, since silicone does not attract and absorb
water, that it will protect the braking system from corrosion.
While silicone does not “hold” water, any airborne moisture (humidity in the air) can still enter the system and be carried on the surface of the silicone fluid.
While the use of silicone fluid definitely helps to prevent internal system damage, it’s not a cure-all to prevent moisture contamination.
The real downside of silicone is that it may aerate/foam under rapid braking situations, such as might be experienced in repeated and rapid modulation of the brake pedal at high speed. Foaming results in air globules, which leads to an unexpected soft/lower brake pedal. For this reason, silicone fluid should also never be used in an ABSequipped brake system.
Silicone brake fluid can have a very undesirable effect on ethylene propylene rubber found in most brake systems, as silicone fluid may tend to cause seal swelling. In addition, silicone may tend to be somewhat compressible when heated or in high altitudes, resulting in changes to the pedal travel.
Primarily due to silicone’s benign characteristic in terms of preventing damage to a painted surface, it remains popular for many show cars that are not intended to be driven routinely at higher speeds and potential hard braking.
If the vehicle is stored for periods and rarely driven, and never exposed to performance
For high performance applications where the potential for extreme braking heat is likely, a variety of brands and specification level brake fluids are available that offer higher dry and wet boiling temperature performance.
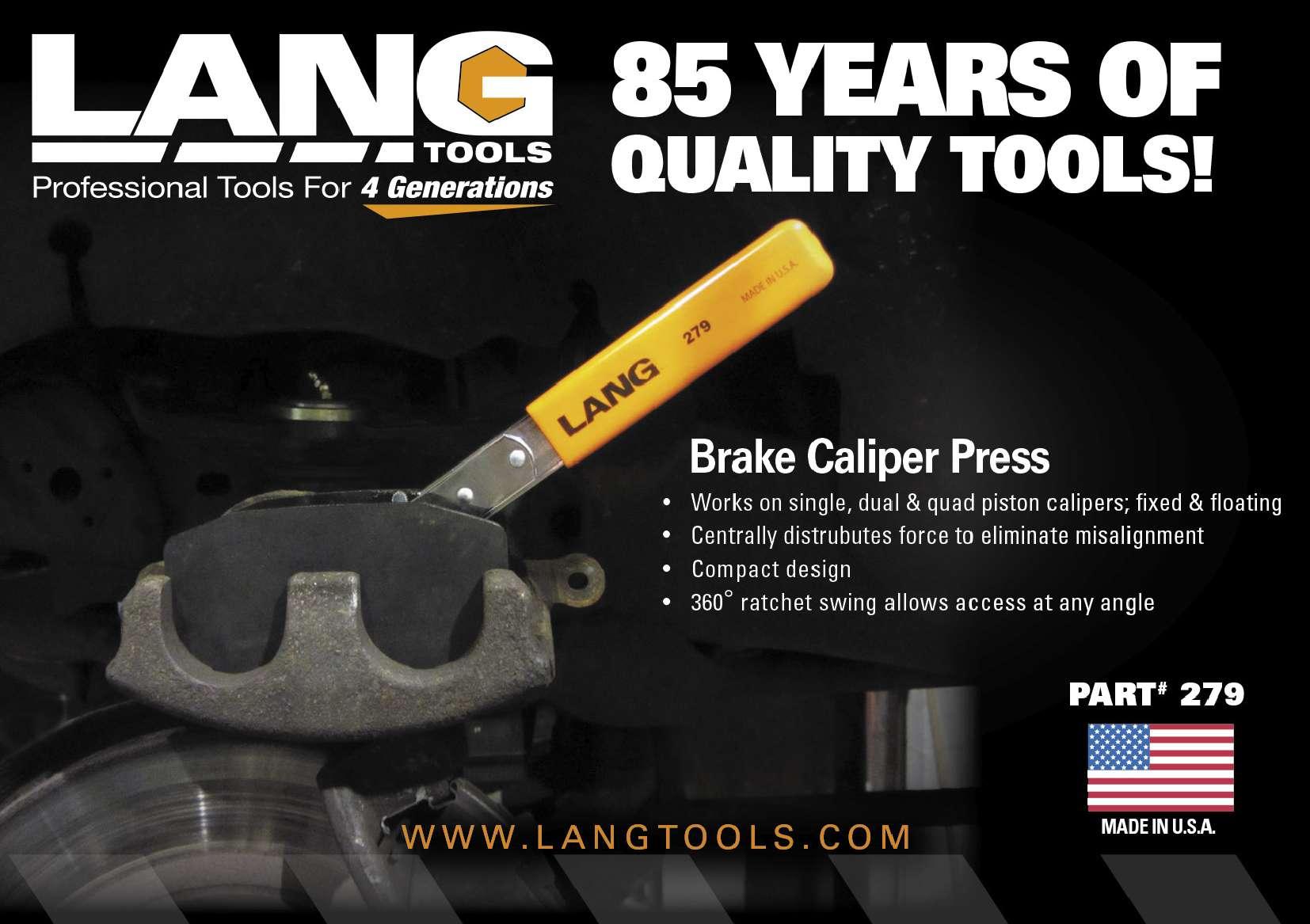
driving, silicone fluid is certainly an option to consider.
But for your customers’ daily driving and especially for performance driving, stick with DOT 3, DOT 4 or DOT 5.1 glycol fluid that offers a high wet boiling point.
Brake fluid boiling points
As the brake system absorbs airborne moisture, this will lower the boiling point of the fluid. The rated dry boiling point represents the point at which fluid will boil when fresh, with no absorbed moisture.
The lower or “wet” boiling point represents the expected performance of the brake fluid after it has been in the car for approximately one year.
For a routinely driven street vehicle, the wet boiling point is more important than the dry, because the brake fluid is going to be in use for much longer periods. In addition to lowering the boiling point, water in the system will eventually corrode the metal surfaces within the system.
While all brake fluids feature corrosion inhibitors, these inhibitors eventually break down and become less effective over time. Glycol brake fluids should be completely drained and replaced, on average, every two years or 24,000 miles in order to maintain optimum fluid performance, regardless of how much the vehicle is driven or stored.
Silicone brake fluid offers very high dry and wet boiling points. However, silicone tends to be more compressible because it will absorb more air than a glycol based fluid, and will infuse itself with air. The dissolved air results in a slightly spongy pedal feel.
Especially from a performance standpoint, it’s recommended to always select a brake fluid that’s rated with a dry boiling point of at least 450 degrees Fahrenheit.
The two most important aspects of a performance brake fluid are compressibility and its rate of moisture assimilation.
Compressibility refers to pedal feel... how firm the pedal feels when the brake pedal is depressed (also assuming the system is properly bled of air).
Different brake fluids can dramatically alter pedal feel, with no other system changes.
Obviously, a braking system generates frictional heat, as the friction material is forced against the surfaces of a rotor disc. This heat is quickly absorbed into the fluid, elevating its temperature.
The published “typical” dry and wet boiling points indicate at what temperature the fluid will begin to boil.
The dry boiling point represents the point at which fluid will boil when it’s fresh and contains no water. The wet boiling point indicates the temperature at which the fluid can begin to boil when it contains as little as 1% to 2% moisture.
The older the fluid, the more moisture
Brand/model
Centric STR 600 Centric STR 660 Ultra Brake Man Hi Temp 577 fluid Castrol SRF Castrol LMA DOT 3/4 ATE Type 200 DOT 4 (same with amber tint) Ford Heavy Duty DOT 3 (inexpensive, but must be changed frequently) TBM DOT 5.1 Xtreme 6 (high rejection to moisture absorption)
Dry boil point
594 degrees F 622 degrees F 577 degrees F 590 degrees F 446 degrees F 536 degrees F
550 degrees F
612 degrees F
Wet boil point
404 degrees F 404 degrees F 300 degrees F 518 degrees F 311 degrees F 388 degrees F
90 degrees F
400 degrees F

High-dollar luxury performance cars often feature premium-performance brake components such as multiple-piston calipers and large diameter rotors. This example is featured in 2009-2012 Mercedes-Benz AMG vehicles, featuring 6-piston calipers and ceramic-compound discs. You’re not going to find these at your local parts store.
it potentially holds, and the boiling point diminishes accordingly.
For maximum braking performance, choose a brake fluid that offers high dry and wet boiling points, and consider replacing brake fluid on a regular basis.
As a glycol brake fluid gradually and inevitably absorbs airborne moisture, its boiling point begins to decrease.
A moisture factor of as little as 3% or so can allow the brake fluid to boil at under 300 degrees F, which will lead to reduced braking effectiveness.
Regardless of the vehicle type or performance level, maintaining the brake system’s fluid purity is important both to maintain system performance and to reduce internal contamination.
If the customer expects maximum braking performance, the brake fluid should be changed according to the vehicle manufacturer’s recommendation (or if no recommendation is listed, changing fluid every one to two years would be a rough guideline).