
13 minute read
Tracking electrical system failures

from Auto Service Professional - October 2018
by EndeavorBusinessMedia-VehicleRepairGroup
It takes skill to traverse the correct diagnostic path
By Edwin Hazzard
The need to track down electrical system failures in today’s vehicles are more preva
Tlent now than they were many years ago. With the addition of system add-ons such as increased safety items, more entertainment and creature comfort options and overall improved vehicle operating capabilities, the technician is faced with the added complexity of performing proper diagnostics.
Today’s vehicles have more control modules, more wiring, more harness connections and with all of that less room in the vehicle to access these changes. A major issue is the way the vehicle manufacturers route their wiring harnesses. They are routed in such a way that they try to make it all fit in a very small, confined space. Sometimes the harness routing isn’t always optimum, and due to the cramped space and confined areas, the harnesses themselves become stressed. A harness can be so tightly routed that the wire inside of the plastic insulation can break and you won’t even see that with a good visual Figure 1: Over time, improper harness routing inspection. The opposite scenario is a harness can easily result in a direct short. that is routed so loosely that with vehicle vibra
Figure 2: This harness rubbed on a transmission case. Over time, it chafed through.
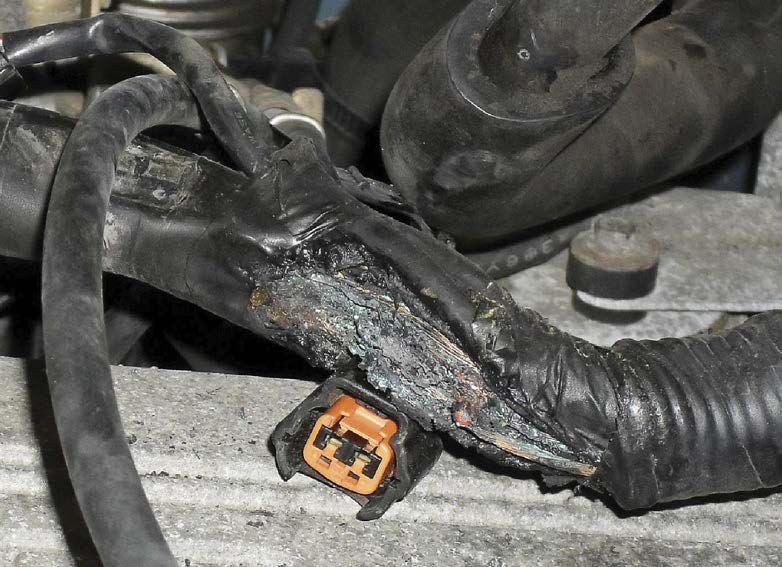
tion the harness has too much movement and can rub up against a sharp object like a bracket, a high heat source or any other object that will compromise the wiring insulation or protective conduit covering.
A perfect example in Figure 1 shows what happened to a harness over time when it is routed incorrectly. This issue was a direct short to ground. Figure 2 shows a harness that has rubbed on a transmission case flashing. It, too, was routed incorrectly.
The vehicle electrical system is like the human body. The wiring in a vehicle is similar to a complex network of veins. Both act like a highway where they provide a path for movement. If a vein leaks then the pressure isn’t as high as it should be.
The same thing occurs with a wire. Voltage will be lost if the wire is compromised. In an electrical system, the two biggest factors which cause electrical failures are moisture and heat. Both create havoc and both can feed off one another.
If an electrical circuit has high resistance, then naturally it will be overheated. Overheating over time will damage the circuit and cause it to fail. Tracking down the cause of the excessive
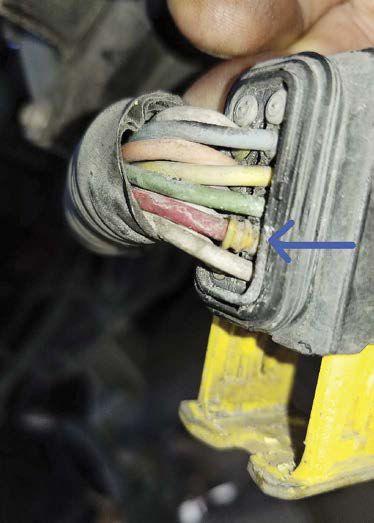
resistance before it damages the circuit is key to saving the circuit from failing completely.
Many times I’ve seen technicians find the cause of the failure but not repair the circuit correctly. In Figure 3, you will see how excessive moisture got into this connector and caused a complete circuit failure.
The cause of this was due to a misplaced seal around the terminal where it enters the connector body. That little seal actually keeps moisture out of the connector body (see Figure 4). As I mentioned before, excessive resistance in a circuit creates excessive heat.
The key to tracking down electrical failures before they crop up is to perform preventive maintenance.
As I stated in one of my previous articles, it all starts with the battery. Making sure the battery is fully charged and the connections are clean and tight is a step in the right direction. A battery terminal that is corroded or even loose is a point of high resistance.
It’s essential that those are taken care of before you start your circuit troubleshooting. Once you have established a good base you can continue on your diagnostic path for the circuit in question. So let’s look at an electrical circuit and see how and where the trouble started.
Our first vehicle in question is a 2005 Kia Sorento that was having an intermittent no-start condition. After retrieving the diagnostic trouble code P0336 for intermittent crank shaft position signal, it was apparent that the circuit that controls the crankshaft position sensor wasn’t working correctly.
I performed a test on the circuit in question and found that the reading from the sensor wasn’t always there.
On this vehicle the crankshaft sensor is located inside the front timing cover and access wasn’t going to be easy.
When testing of a sensor shows an intermittent signal, you want to be absolutely certain that you know it’s either a circuit problem or a component problem. I tested this circuit from the electronic control module (ECM) as that was the easiest access point.
Sure enough, I was getting a reading on my scope and then it showed a flat line while cranking. When I did get a signal the engine would start then stall, but in the majority of attempts it would not start.
Unfortunately I had to remove the front timing cover to actually get a visual of this sensor. When the covers were removed I found an excessive amount of oil on the timing belt due to a leaking front crankshaft seal.
To remove the crankshaft sensor I first had to remove the timing belt. Once the sensor was removed I immediately saw the problem. With the oil saturating the crankshaft sensor over a prolonged period of time it had eroded the plastic covering that protects the three wires going into the sensor assembly (see Figure 5).
With the wires being exposed, moisture along with the debris from the belt created corrosion on the signal wire coming out of the sensor, which was giving me that intermittent no-start. This vehicle needed a new timing belt and crankshaft seal, along with the seals that keep moisture out of the timing covers, as well as a new sensor.
Besides water intrusion entering a circuit, another electrical circuit failure is that of excessive resistance.
When a circuit has higher than normal resistance in a circuit it creates heat. If the heat is too high it will cause wires to melt, along with terminal ends inside of connectors to melt the
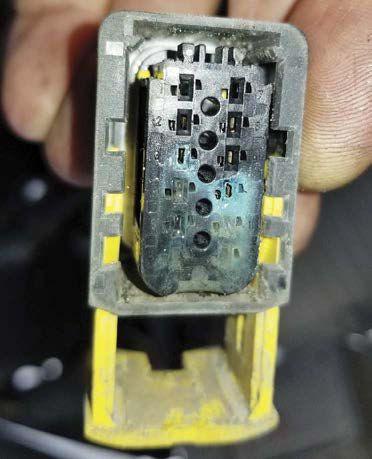
Figure 5: Oil saturation caused by a faulty crankshaft seal killed the plastic protective coating. This in turn killed the vehicle’s crank position sensor and its wires.
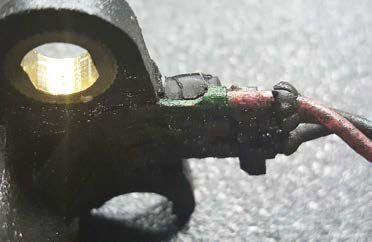
AUTOMOTIVE INTELLIGENCE
WORK SMARTER NOT HARDER
Figure 6: This terminal connector was backprobed with a test light, but left unsealed. Corrosion began quickly. cavities inside the connectors, thus allowing the terminals to move around, creating a potential for an unsecured connection and poor terminal retention. When a circuit becomes overheated, the circuit is designed with a fuse to alleviate the high resistance. e fuse which is placed in the circuit as a safety precaution is supposed to trip its connection and stop the circuit from operating and possibly saving the wiring and components from damage.
Somewhere in this circuit the resistance was so high it actually melted this fuse but didn’t blow the fuse. e high resistance will always nd the weakest point in a circuit and will rear its ugly head.
It is especially important that a good quality fuse be used in a vehicle. A fuse with a poor design will not operate as it should and it could create problems and cause a risk for damage.
Many things can cause high resistance in a circuit. For example, a ground circuit that is loose or corroded will cause excessive heat. A ground circuit that is not supposed to have voltage on it but does will create a circuit failure.

MS908S

MS908SP DIAGNOSTIC INTELLIGENCE
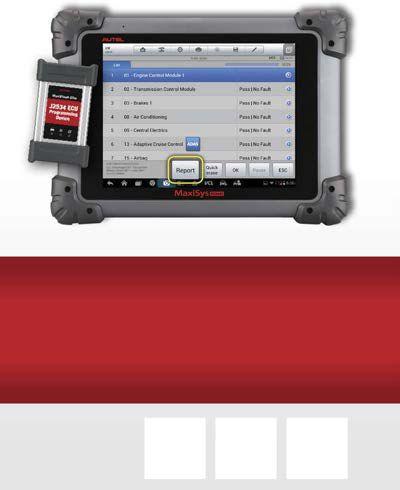
POWERFUL HARDWARE SMARTER SOFTWARE
64G Memory
( 855 ) 288-3587 autel.com / maxitpms.com
Register and update tools for latest coverage © 2018 Autel Intelligent Technology Inc.
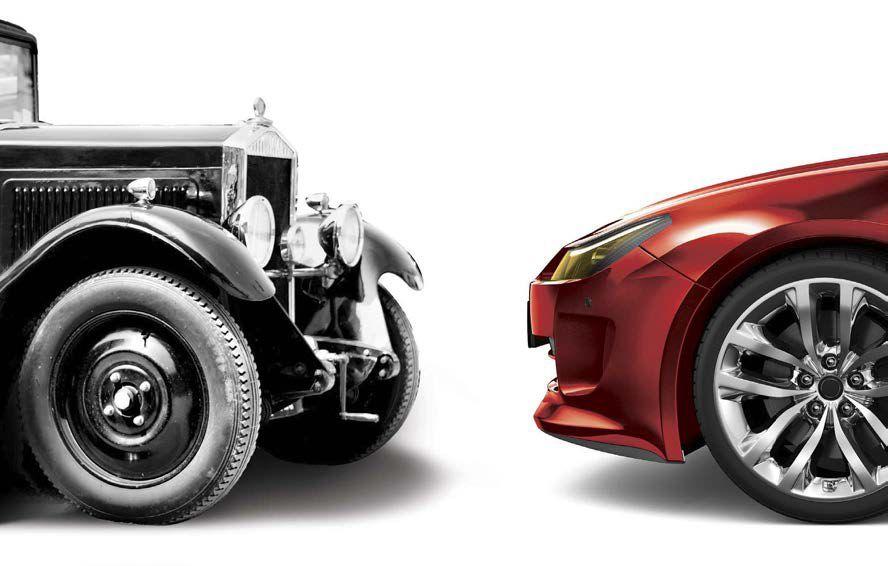
Installing condence. Yesterday. And today.
Since the earliest days of the automobile, SKF has been supplying the world with the highest quality drivetrain, engine and wheel end components available. Today, SKF continues to provide high quality products and premium services to car and truck manufacturers, technicians and distributors across North America and around the globe.
Install confidence. Install SKF.
www.skfpartsinfo.tv @skfpartsinfo
Figure 7: It’s best to have a terminal test kit with probes that feature both male and female connections. They fit the terminals properly and work great when performing a terminal retention test.
Performing a voltage drop test on a circuit is a surefire way of checking that circuit for high resistance.
Performing a voltage drop test is quick and effective when testing the integrity of that circuit. For example, let’s check a negative ground circuit such as a battery cable. Simply take your DVOM (digital volt ohm meter), place one lead on the negative battery post and the other lead on the end of the battery cable where it attaches to the ground connection on the engine block.
Set your DVOM to the millivolts scale and operate the circuit. Crank the engine and watch your reading. This is best viewed on a graphing meter, if possible.
The voltage reading should be very close to zero volts. If you are obtaining a voltage reading that’s too high, then adjust your voltage scale on your meter so you can see what the actual voltage is. If it’s excessive, then your ground circuit has too much resistance, either due to a bad connection, loose connection or possibly a faulty battery cable.
Remember, a circuit only has 12 volts. If you have two volts on your ground side then that only leaves you 10 volts to operate that circuit. You will probably start to see problems arise if that’s the case.
As a mobile tech, some of the issues I come across out in the field are created by unapproved testing methods. Anytime you are testing a circuit it is imperative not to disturb the circuit. I prefer back probing a connector or disconnecting the connector if possible, but it is important to take great care of that circuit while testing. If you disturb that circuit too much you just might have temporarily repaired the circuit and you don’t even know it!
If you have to pierce a wire to check it or back probe a connector which has a moisture protecting seal on it, make sure you seal that test point with a sealer that doesn’t allow moisture into the wire or terminal. If you have to apply shrink wrap to the area that will work as well. Sometimes you might even have to solder your test point with a new connection.
Here is an example of a terminal connector that was probed with a test light and then left un

Visit us at AAPEX Booth #2626
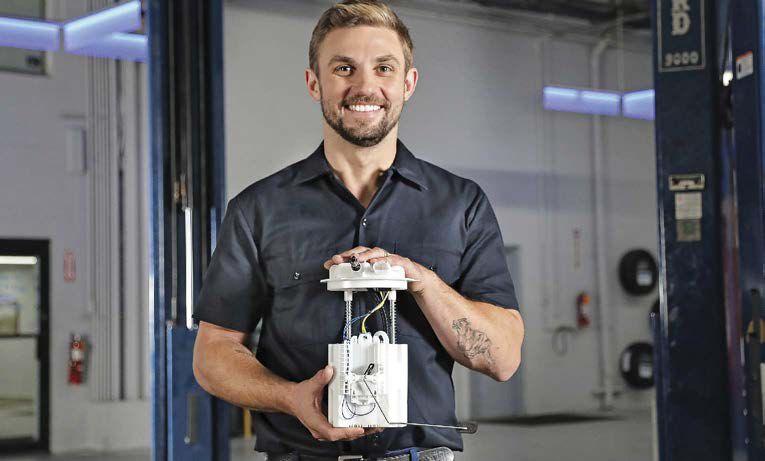
www.vdo.com/usa
You can trust they’re OE quality - these are genuine OEM parts.
VDO OEM Direct Parts are genuine OEM parts direct from the manufacturer – that’s us! They’re the same high quality original equipment parts manufactured by Continental, affordably priced to keep you competitive.
Why settle for parts that claim to be OE quality when you can have the genuine OEM parts?
salessupport-us@vdo.com 800-564-5066

Air control valves, electronic throttle valves, flex fuel sensors, fuel modules, fuel injectors, temperature controlling water pumps, door lock actuators, MAF/MAP sensors, wheel speed sensors, and washer pumps.
Circle 113 on Reader Service Card
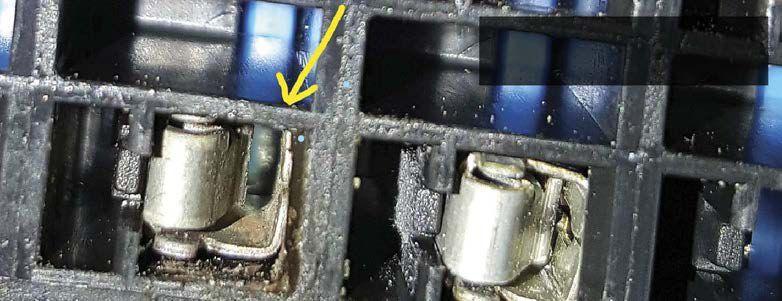
Figure 8: If spread out and not making good contact, this creates a source of resistance and heat.
sealed (see Figure 6). Notice how the green corrosion death entered the connector? I also recommend that you don’t just wrap your test points up in electrical tape. Electrical tape alone will not keep out the moisture.
There are some essential tools that’s needed for tracking down electrical failures in today’s vehicles.
Having a high quality DVOM is important, but adding some good testing probes and wire terminal leads is just as important. A terminal test kit as shown in Figure 7 is a great tool to have, as it includes both male and female terminal connections.
Not only do they fit the terminals properly, but they work great when performing a terminal retention test. Remember, if the terminal is spread out and not making good contact, then that is a potential source of resistance and a place for heat build up to form (see Figure 8).
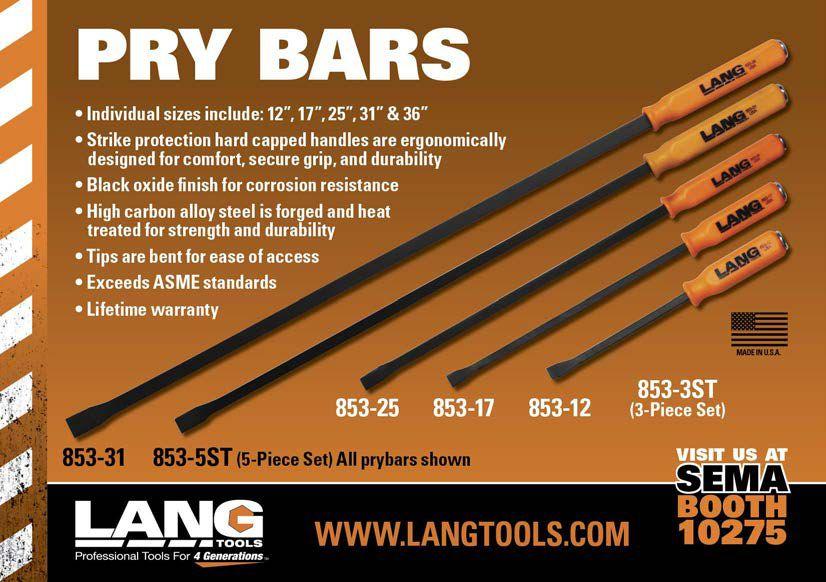
Figure 9: Water entered this module, caused by a leaking through an exterior source. Initially the blame was placed on the module.

So we know that resistance and heat are big contributors for electrical problems. Another well-known source for problems to crop up is water. Water and electricity don’t get along very well.
I was called to a shop for a 2006 Chevrolet Trailblazer that had an issue with the door chime going off randomly. After checking the circuit completely and reviewing the scan data in the truck’s body control module (BCM), I didn’t see anything out of the ordinary. I did however see the BCM register that the module was active when it did go off, but nothing else.
I instructed the shop to replace the warning chime module and to save the old one for me. They replaced the warning chime module assembly and the problem was cured… for now.
I opened up the chime module and I immediately saw the cause of this component’s failure. Water intrusion entered inside this module and caused corrosion on some of the circuits (see Figure 9). I called the shop and told them to get the customer back in and check for a water leak around the windshield, door and cowl assembly.
They did, in fact, find the water leak and repaired the root cause of the module failure. 40
Remember, it’s very important to find the cause of any failure to avoid a repetition of the problem. When tracking down electrical circuit problems there are many things to take into consideration.
The most important thing to consider is that you have to know how the circuit that you are troubleshooting works. You need to have access to a wiring diagram and you need to understand how that circuit runs and what that wiring diagram is telling you. The diagram is your road map.
I don’t for the life of me understand how some technicians can trace a circuit and get away without one.
Another vital piece of the electrical troubleshooting puzzle is to have a good working DVOM and a complete understanding on how the meter works.
Some meters are very sophisticated and have a lot of bells and whistles. That’s fine as long as you’re familiar with them.
Also, a good set of test leads is equally important. If you are using a bargain-priced test lead set, it’s likely that the leads will already have some built-in resistance. This extra resistance will skew your readings and quite possibly give you a false direction on your test procedures.
And finally, you have to have a good understanding on how voltage, amperage and ohms work. Learning this may seem boring to some, but it is really important that you do understand it.
With your knowledge in place and your tools in hand, becoming a skilled electrical troubleshooter will help you in tracking down electrical system failures in today’s modern vehicles.
Edwin Hazzard owns South East Mobile Tech in Charleston, S.C., which is a mobile diagnostic and programming service providing technical service to many automotive and body repair shops. He has 35 years experience in the automotive industry. He currently is an automotive trainer, a board member of TST (Technician Service Training), a member of the MDG (Mobile Diagnostic Group), a member of the Professional Tool and Equipment advisory board for Pten magazine, a committee member of Nastaf, and is a beta tester for multiple tool makers.
