
22 minute read
Design a Sustainable World Built on Strong Connections

from Architectural Products - March/April 2023
by Buildings & Construction Group
At Amerlux, we started by lighting your world. Now, we’re connecting it.
With tunable lighting in commercial and retail spaces, Bluetooth in healthcare and institutional design, and automation throughout corporate campuses and along streetscapes
We make disparate interior and exterior building systems come together under the most beautiful, comfortable illumination to create buildings that work for you.
And you can too—with one call to us.
Amerlux’s suite of intelligent lighting solutions easily integrates with best-in-class products from Delta Electronics and its brands, including Delta Controls, LOYTEC, March Networks and VIVOTEK, to provide automated comfort and quality in any space.
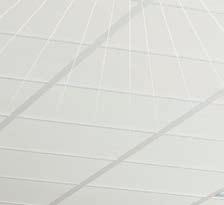
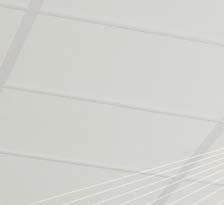
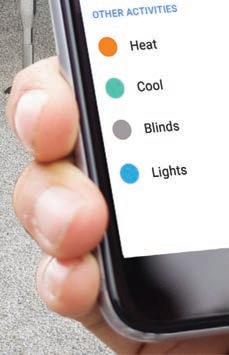
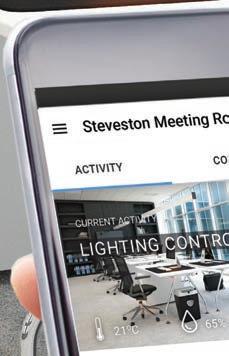
Architectural lighting. Adaptive climate control. Enhanced security. A reduced environmental footprint. A more robust bottom line.
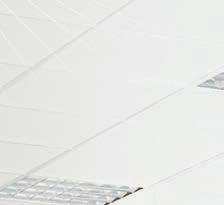


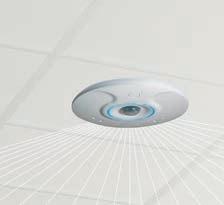
Intelligent. Sustainable. Connecting.
Delta is committed to leading building automation into a sustainable, energy-efficient future. The Delta Partnership ensures you have everything you need to design and operate sustainable building solutions under one roof, one network and one family of companies.
Healthy Building
Healthy Lighting
WELL Consulting
Smart Care Solution
Smart Building
Access Control Management
Parking Management
Smart Building Integration Service
Architectural Lighting Design
Connected Lighting
Low-Carbon Building
Smart Energy Integration Service
Smart Energy Solution
Green Building Consulting
LED Lighting Service
Book our free AIA/CES webinar, “Designing a Greener Future: An Introduction to Building Automation for Net Zero Carbon,” for your office. Email Gary Harvey, Director of Business Development and Operations, at gary.harvey@deltaww.com for details.
Visit bestlight.amerlux.com/deltaww-building-automation or scan code to learn more.
Smart Community
Video Surveillance
Landscape Lighting Design
Smart Pole Solution
Building automation essentially takes the many disparate systems in a building that are interrelated— the lighting system, the HVAC system, the electrical system, the shading system, the security system, indoor environmental quality systems and others— and connects them so that the systems can coordinate with each other to improve the overall performance of the building. The results have been impressive with projects realizing benefits that include improved energy conservation, security, and indoor air quality (IAQ) in buildings.
I nterior space is expensive. Building automation can help to ensure it’s being used better in buildings big and small. Let’s begin this discussion by taking a closer look at all the ways that building automation could benefit the built environment.
Commercial Spaces
Bas Benefits For Commercial Spaces
The potential advantages that building automation systems can bring into a commercial space reach far and wide. By enabling the various building systems to communicate and respond to each other, the building can become an active participant in its own energy consciousness. It also reduces the reliance on human intervention and the opportunity for human error to derail the intent of the design. As an interesting aside, building automation makes it possible for energy savvy to be achieved while still prioritizing occupant comfort.
Building automation systems offer more than reliable action, they offer unprecedented access to information about how the various building systems are performing, the environmental conditions of the interior, and even the way the space is being used. These details equip building owners and facilities personnel to identify areas for improvement and make the necessary adjustments.
INCREASE ENERGY SAVINGS + REDUCE UTILITY COSTS
It turns out that, when properly equipped, buildings are very good at turning out their own lights. Instead of relying on people to turn lights off when they leave a room, the building can recognize when a room is empty and turn the lights and the HVAC down or off. This can have an incredible impact on the overall energy use of a building. Simply monitoring building occupancy and allowing the building automation system to adjust HVAC use accordingly can result in savings of 10% to 30%.
Increase Comfort Of The Interior Environment
Smarter buildings can eliminate energy waste in ways that go completely unnoticed by people in the building. For example, when rooms are empty, a smart building can ensure that the lights and HVAC are turned off or down.
T hese systems can also ensure that people are more comfortable. Buildings are often afflicted with areas that are too hot or too cold throughout the day. Lighting levels are often mismatched with the visual tasks being performed in the space. Creating more comfortable employees has been shown to create happier, more satisfied employees, who show up more often.
W hile there is no recipe for comfort. A good tip is to get a head start. With building automation systems, the HVAC system can be programmed to bring the interior to a comfortable temperature before occupants arrive and then turned down after everyone leaves. This prevents employees from arriving to frigid morning temperatures in the winter and stifling temperatures during the summer. Lighting can be programmed to better meet the needs of the certain tasks and times of day.
Improve Indoor Air Quality
According to the U.S. Environmental Protection Agency (EPA), “Indoor air quality is a major concern to businesses, building managers, tenants, and employees because it can impact the health, comfort, well being and productivity of building occupants. While most buildings do not have severe indoor air quality problems, even well-run buildings can sometimes experience episodes of poor indoor air quality.”
One of the difficulties is that indoor air quality is an ever-changing, atmospheric element that describes the complex interaction of various factors. The EPA identifies the factors that influence indoor air quality as: sources of pollutants or odors; design, maintenance, and operation of building ventilation systems; moisture and humidity; and occupant perceptions and susceptibilities.
With building automation systems, indoor air quality can be constantly and consistently monitored so that if and when a problem arises, it can be immediately identified and remedied.
Improve Space Utilization
It’s often stated that after employees, square footage is the most expensive item on a company’s balance sheet, which places a premium on ensuring that space is being used well. Building automation systems can offer important insights into how employees are using the interior space throughout the day.
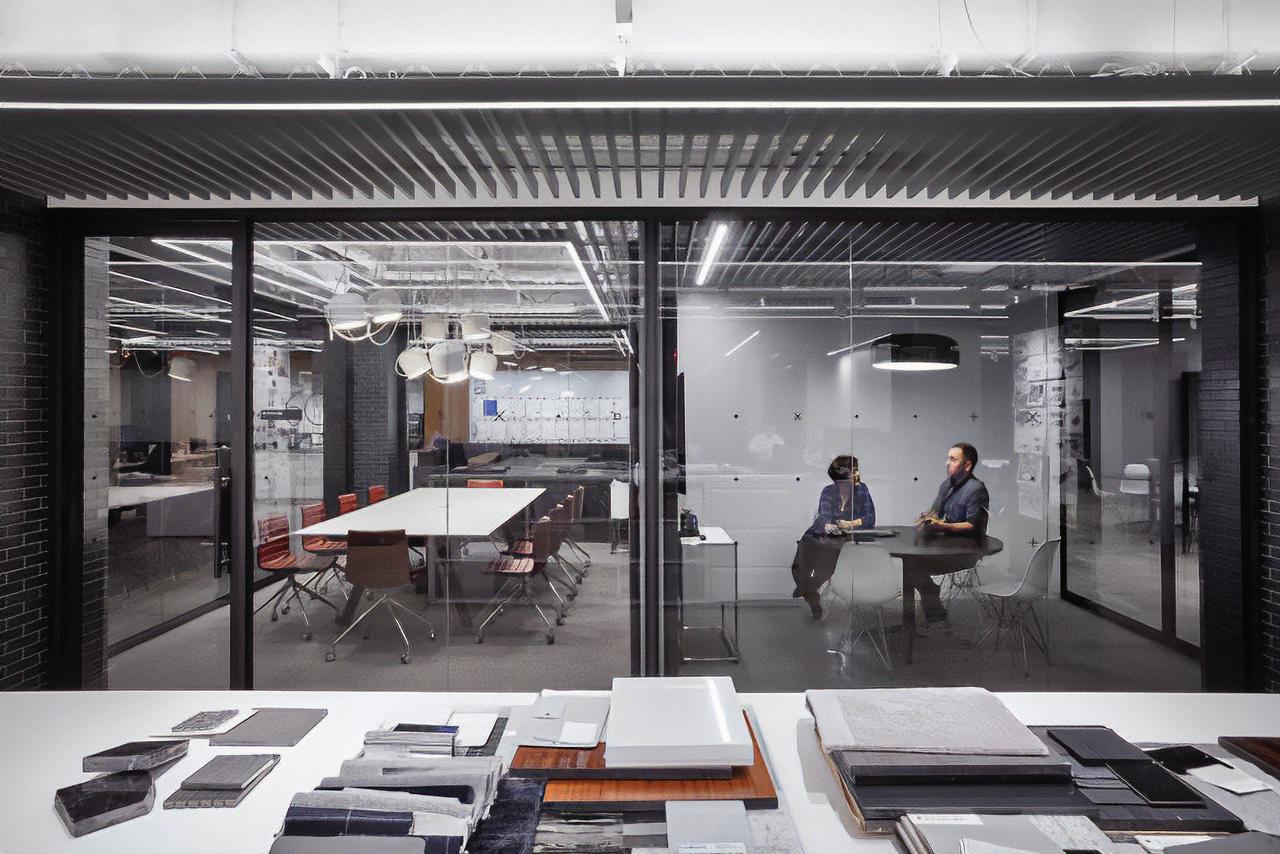
S ensors installed in lighting fixtures or in the ceiling detect and chart the movement of people. This information reveals if certain spaces are being under-utilized or are over-crowded. It will also illustrate if there are opportunities to make the daily journeys employees take more efficient. If, for instance, a popular kitchenette or copier is located on the far side of the building. Then owners or facility operators can decide how the situation can be improved and visualize the results of any actions they take.
K-12 EDUCATION BAS BENEFITS FOR K-12 SCHOOLS
According to the Department of Energy, K-12 schools spend roughly $6 billion a year on utility costs. This bill could be cut dramatically if these buildings were able to be smarter about the way they used energy. In addition to saving energy, smart technology can streamline building maintenance, enhance school safety, and improve the quality of the learning environment.
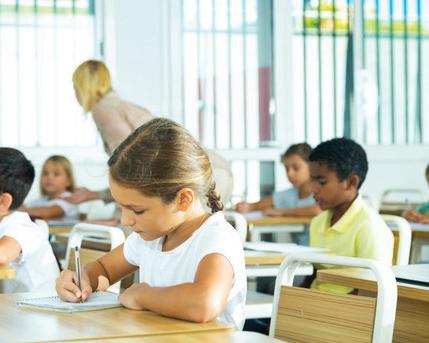
STOP WASTING ENERGY IN VARIABLE-OCCUPANCY SPACES
There are many rooms in the K-12 building that are identified as variable occupancy, which means that their occupancy changes throughout the day. An art room, the library, or the gym may be filled with a full class for one period and then be empty the next. From an energy use perspective, these types of space don’t require the same amount of conditioned air all day long. Nor do they require the lighting to be left at full on from the first bell to dismissal. Building automation can help to match the lighting and HVAC needs of these spaces to the lighting and HVAC provided. Room-based smart devices learn user schedules and class patterns to offer more finely tuned energy savings and systems operations.
I nsights into energy use are important for the whole building, in addition to the variable-occupancy spaces. Building monitoring systems give maintenance and facilities teams better information about the school’s use of electricity, gas, and water so they can understand how the systems respond to changing conditions throughout the day and seasons and identify opportunities for improvement and cost savings.
Receive Better Overall Maintenance
Remote, real-time diagnostics offer better information on the upcoming maintenance needs of the various building systems and enable facilities personnel to schedule maintenance activities so that class disruptions are minimized. The improved visibility enables the staff to provide better overall maintenance to the building which results in systems that run more efficiently and are less likely to break down.
Use The School Performance To Teach Students About Energy Efficiency
Real-time building monitoring data is being shared with students at the school to provide insights into the way buildings use energy and emphasize the importance of energy efficiency and efficiency-enhancing technology.
Create Optimal Learning Environments
Lighting, HVAC, ventilation, and other systems can be coordinated and customized to create optimal learning environments based on trends, task, or student and teacher preferences. Demand-controlled ventilation paired with CO 2 monitoring, for example, can more closely match space occupancy with the influx of outside air to keep students alert and engaged, instead of yawning and groggy.
Improve Security
Improving school security is very top-of-mind today and building automation offers a solution that is both effective and ready-to-implement. These systems offer security personnel better views of the interior and exterior spaces and can alert teams when certain troubling details are detected.
Video management systems can maximize the ways that cameras detect possible unwanted activity, while AI can help reduce the security workload by scanning for specific anomalies. Cameras and AI analytics-based software can identify detrimental behaviors such as loitering around perimeters, intruding on entrances, and crossing barriers, and even detect specific problematic elements—fire/smoke, guns, and even fighting between students. These systems can also notify security about an open window or door that didn’t shut entirely.
B eyond issue detection, features like keyless doors and access systems with facial recognition technology offer additional safety measures to help prevent issues and can be crucial if the facility faces a lockdown scenario.
Retail Spaces
Bas Benefits For Retail Spaces

Retail stores operate on razor thin profit margins and require the use of brick-and-mortar buildings, which gobble increasingly expensive energy for lighting, heating, and cooling. Building automation systems can offer store owners a solution that will reduce their energy use, without compromising the comfort or quality of their retail environment.
I n the article, “Smaller Buildings Can Benefit from Building Automation Systems,” by Joanna Turpin, she writes, “Small- to medium-sized buildings—usually considered to be under 50,000 square feet—make up about 94% of all commercial buildings in the U.S, according to the U.S. Energy Information Administration, yet only 13% of those buildings have a building automation system.” Despite the potential benefits being substantial.
I n the whitepaper, The Untapped 87%: Simplifying Controls Technology for Small Buildings, author James Dice, PE, CEM, CMVP and founder of Nexus Labs explains, “Small structures can cut energy use from 27% to 59%, depending upon building type, using economically viable and commercially available technologies.”
B eyond improvements in energy consumption, building automation systems can offer powerful surveillance solutions to prevent asset and property loss, improve transaction security, and provide intelligent analytics.
ENHANCE SECURITY AND LOSS PREVENTION
Protecting an investment in inventory and maintaining low shrinkage rates are two critical objectives for achieving long-term business success in the retail sector. Shrinkage describes the difference between the amount of merchandise that a retail company owns on its books and the actual physical count of the merchandise in the store. Common reasons for shrinkage include breakages, spillages, misplacements, perished goods, and internal and external theft. There are a number of surveillance technologies that can be applied through a building automation system to monitor in-store activity.
Capture Business Intelligence
In any business, knowledge is power. In retail, knowing what’s going on in the store in terms of in-store data, customer flow patterns, and traffic data enables companies to optimize a store’s layout and influence customer behavior. Point-of-Sale (POS) integration provides real-time monitoring at the checkout counter capturing transaction details that help security teams and store owners prevent asset and property loss and decrease shrinkage.
SAVE MONEY WITH SMARTER SYSTEMS
Smart systems can also offer more cost-effective solutions than traditional systems. In a retail setting, specifiers could replace the thermostats installed throughout the space with a sensor that monitors the temperature of the interior. With building automation, the temperature setting can be adjusted through the software, instead of at a thermostat on a wall. This thermostat/sensor swap creates real savings in a few ways. Thermostats no longer need to be purchased, creating savings on the physical parts and pieces necessary for the system, and its much easier to pull low-voltage wire to install a sensor than pulling line-voltage to the different thermostat locations, creating savings on system installation too.
Components
Components Of A Building Automation System
With such an exhaustive list of potential benefits, its easy to see why there’s such interest in building automation, but there is still much confusion on what these systems consist of, how they are assembled, and specified. For the purpose of this discussion, let’s take a look at the various components and some of the features and functionalities that deliver a building automation system at its best.
The Role Of Luminaires
The lighting system offers an excellent platform for building automation systems because it is a powered and omnipresent entity that is located throughout the entire building. Beyond offering a reliable power grid that the various components can tap into, the cameras and sensors can be integrated into the physical housings of the lighting fixtures, which streamlines the design, specification, and installation of the building automation system.
W hen the Internet of Things (IoT) and building automation systems first broke into the market, the luminaires with integrated sensors available were almost exclusively troffer style, which forced architects and lighting designers to choose a form that may not have been their first choice in order to get the functionality they desired. Today, sensors can be integrated into linear and circular luminaires, high bays, pendants, and exterior lighting solutions as well, allowing design teams to achieve both the aesthetic and level of building automation that will best benefit the project.
Multisensors
A multisensor combines multiple environmental sensors into one piece of equipment offering building automation systems an accurate view of an interior space, without requiring all of the different, individual sensors that would clutter up the ceiling. There are multisensors available that combine temperature, humidity, motion, sound, and light sensing, enabling this one solution to offer HVAC, occupancy, and daylight control from one device.
Indoor Air Quality Monitoring System
An indoor air quality (IAQ) monitoring system continuously monitors real-time data for several types of harmful indoor air factors that include carbon monoxide (CO), carbon dioxide (CO2), fine suspended particulates (PM2.5), suspended particulates (PM10), formaldehyde (HCHO), Ozone (O3), and Total Volatile Organic Compounds (TVOC). The quantity of ventilation air at outside air intakes can also be measured to validate the quality of the air being drawn into the interior.
Some IAQ monitors offer more than just the detection of poor conditions. They can also be linked to the HVAC or ventilation system and trigger a response that will introduce fresh air into the building.
Here’s how it works. When the sensor detects environmental factors that are outside the acceptable range, the monitor will set off an alarm, alerting facilities personnel to the issue, and cue the ventilation system to bring more fresh air into the building, improving the quality of the indoor air.
T he design of some sensors can also contribute toward earning points in the LEED green building standards and the WELL healthy building standards. This is important to consider if either of those certifications is a goal of a project.
Network Cameras
When selecting cameras that will provide the security and surveillance for the building automation system, its important to consider the quality of the images, the ability to communicate with law enforcement, and any available AI.
I n order for video surveillance to be helpful, the images need to be clear. The clearer, the better. Unfortunately, surveillance solutions placed near windows or by entrances often have moments during the day where they operate in bright sunlight. These bright conditions can obscure or decrease video quality.
Wide Dynamic Range (WDR) technology improves image visibility in high contrast lighting scenarios, which makes it easier to see objects and people any time of day. In order to ensure the clarity of nighttime images, look for cameras with advanced infrared (IR) technology that can deliver crystal-clear quality even when the light levels are extremely low.
CASE STUDY
DORM ROOM ENERGY SAVINGS
A major university wanted to ensure the comfort and wellbeing of students while reducing energy consumption and protecting room equipment. With an existing Building Management System monitoring and controlling the facilities across the campus, they wanted to integrate emerging technology to improve student experience and meet their objectives.
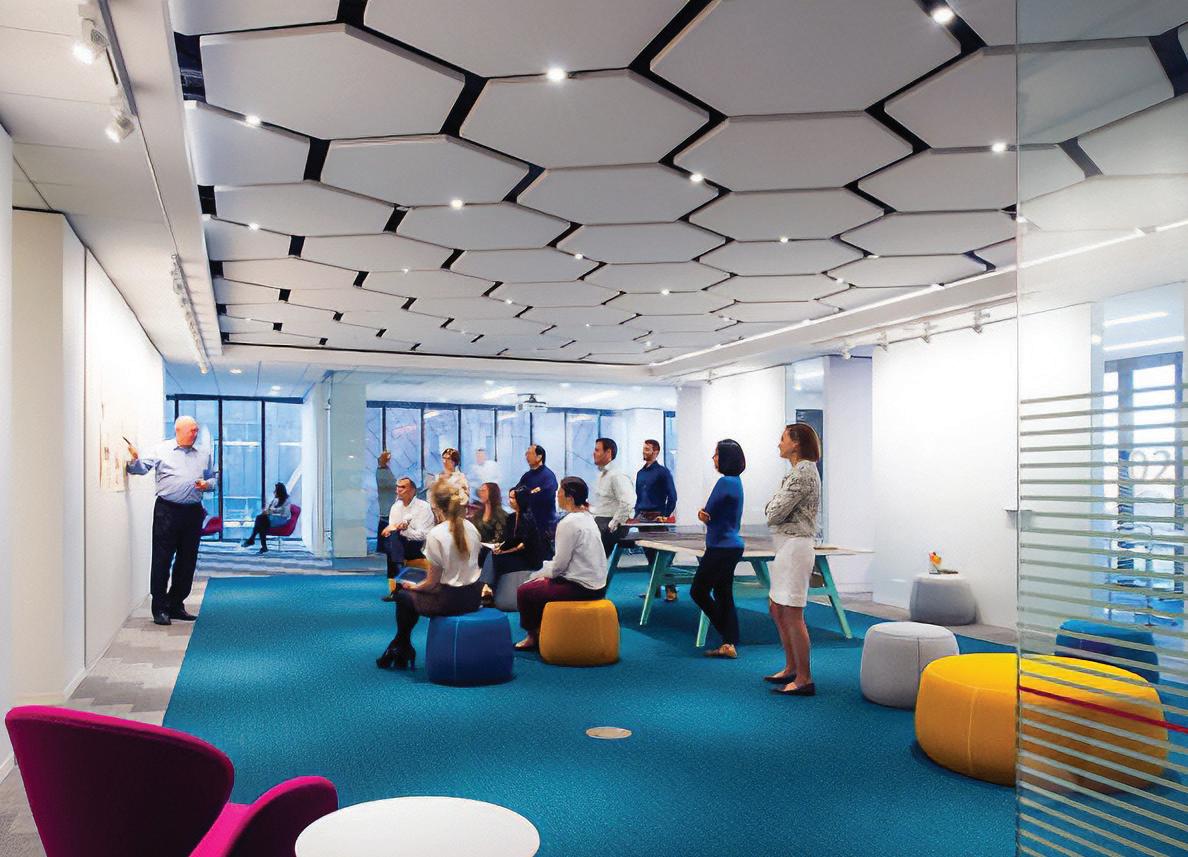
I n student housing dorm rooms, the objectives were to improve sanitation, reduce vandalism on thermometer wall stats, and conserve energy when either the occupant was not in the space or when the window was opened. With the limitations of the existing system, facility operations were unable to shut down the air when the occupant was not in the area or when the occupant opened a window in the dorm room.
T he proposed solution called for removing the existing thermometer wall stats and replacing them with ceiling-mounted multisensors. The removal of the wall stats eliminated the need to sanitize them and reduced the occurrence of vandalism and overrides. The multisensor provides occupancy sensing and thermal load monitoring, so it can identify when an area is unoccupied and when a window is opened. When these conditions are detected, the multisensor sends a signal to shut the air conditioning down.
B efore the strategy was implemented, a pilot program was set up to compare the performance of the multisensor with the existing smart thermostat. The results made the choice clear. The temperature readings from the multisensor were far more linear and consistent. In addition, the vantage point of the ceiling-mounted multisensor, when compared with the wall-mounted thermostat, provided better, more accurate temperature sensing. The improved temperature detection enabled the multisensor to identify environmental changes more quickly, such as a person leaving a room or a window being opened, and, in turn, respond to those changes faster, saving energy. The trial showcased just how effective this sensor swap would be in creating energy savings in unoccupied dorm rooms or when the windows were opened.
DESIGN TREND NO. 2 INCREDIBLE LOOK OF WOOD CEILING AND WALLS
While building automation is a trend defining the way that more buildings in 2023 may be designed to function, the use of wood ceiling and wall systems is a trend shaping the way a growing number of interior spaces will look and feel.
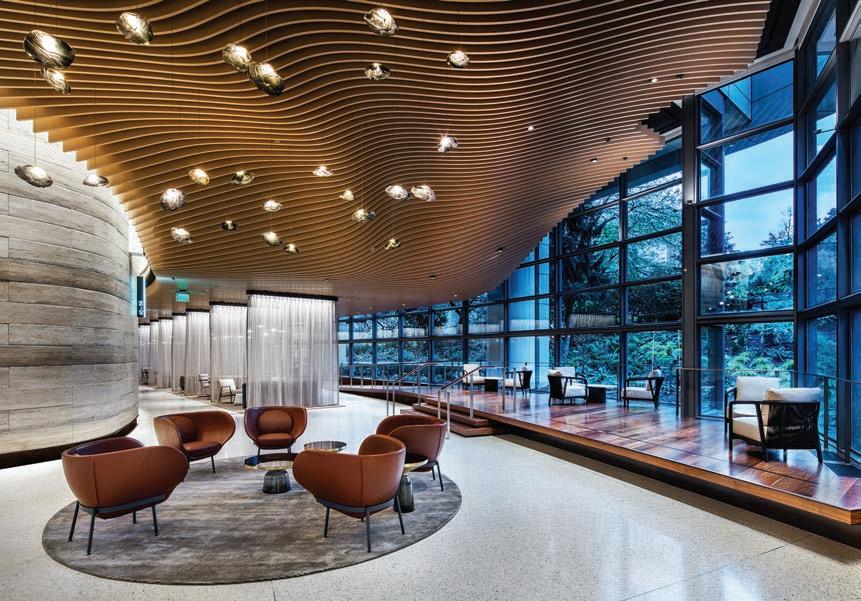
T he use of wood on ceilings and walls is gaining momentum for several reasons. The material has been shown to create a positive response in people and supports the nature-inspired biophilic design movement that seeks to bring elements of the outdoors in. Wood also has a low embodied carbon footprint, making it a people-first and environmentally friendly design solution.
Advances in technology and manufacturing are now making it possible to create wood systems in an incredible array of forms and styles—planks, slats, cubes, and curves. The versatility of these systems enables architects to design solutions that truly push the boundary of creativity and transform a surface into a stunning architectural element.
With the growing interest in these systems, manufacturers are constantly fielding three questions from the architectural audience. One common question focuses on the presence of formaldehyde in these wood products and whether they may negatively impact indoor air quality. Architects also often ask which species of wood is the best for a project and which type of attachment can be used to help achieve their creative vision.
Thi s article will address the presence of formaldehyde in wood and explain what designers should look for to specify beautiful wood products that will not create harmful interior environments. It will also share tips for identifying the species of wood best suited to a certain application and explore the various options for attaching these systems to the wall and ceiling.
Emissions Formaldehyde Emissions Certificate Of Compliance
Some architects may be surprised to learn that composite wood products can contain formaldehyde. While the word may immediately conjure the vision of embalming fluids, formaldehyde is quite common in building products. In fact, the construction industry consumes 60% to 70% of all the formaldehyde produced in the U.S. Formaldehyde occurs naturally, in living cells, and is exhaled by human breath. This colorless, highly toxic, and flammable gas is also man-made and used in the production of fertilizer, paper, plywood, and resins (a.k.a. glue) added during the manufacture of composite wood products.
It’s important to note that not all resins are created equal. While some products may contain a high level of formaldehyde, resins can be designated as No Added Urea Formaldehyde (NAF or NAUF) and UltraLow Emitting Formaldehyde (ULEF). NAF-based resins are resins formulated with no added formaldehyde as part of the resin cross linking structure, and include resins made from soy, polyvinyl acetate, or methylene diisocyanate. ULEF resins are formaldehyde-containing resins formulated such that the formaldehyde emissions from composite wood products are consistently below applicable emission standards.
T here are standards that explore and guide the industry on the level of formaldehyde emissions deemed safe for interior environments. The Formaldehyde Standards for Composite Wood Products Act was signed into law in 2010. This new act established a framework for regulating emissions from composite wood products at the national level and is based on the California Air Resources Board (CARB) Airborne Toxic Control Measure (ATCM)—the most stringent regulation in the world.
T he CARB provided special provisions in the ATCM for manufacturers of hardwood plywood, particleboard, and medium density fiberboard who plan to use no-added formaldehyde (NAF) based resins or ultra-low-emitting formaldehyde (ULEF) resins.
Manufacturers who plan to use NAF or ULEF based resins may apply to the Executive Officer of the CARB for an exemption from the third-party certification requirements. If the products are deemed appropriate, they will earn a Formaldehyde Emissions Certificate of Compliance.
T his means that even projects seeking to earn certification from the WELL Building Standard version 2 (WELLv2) to be recognized as a certified safe and healthy interior can include wood composite components that contain a certain amount of formaldehyde.
T he WELL v2 VOC Restrictions feature within the Materials concept is focused on minimizing the impact of slow-emitting VOCs on indoor air quality. It requires testing and adherence to emission thresholds for newly purchased furniture and furnishings, flooring, and insulation.
Part 2 of the VOC Restrictions feature titled Restrict VOC Emissions from Furniture, Architectural, and Interior Products requires that newly installed furniture and furnishings meet VOC emission thresholds set by the California Department of Public Health (CDPH) Standard Method v.1.1-2010 or any more recent version. One point is earned for a 50% restriction. 2 points are earned for a 90% restriction.
L ook for wood composite products with NAF and ULEF cores that have earned their Formaldehyde Emissions Certificate of Compliance to specify wood products that will not have a harmful effect on the interior environment.
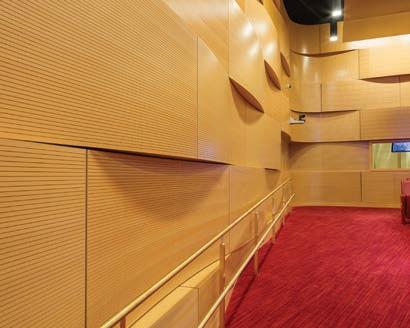
Species Selection The Secrets To Species Selection
When looking to incorporate wood into a project, an architect will invariably wonder which type of wood is best for that specific application. There are so many species available—spruce, poplar, maple, ash, red oak, lodgepole pine, western red cedar, and white oak. The first step is deciding whether or not the wood needs to be sustainably sourced.

CONSIDER FSC-CERTIFIED WOOD PRODUCT
The Forest Stewardship Council (FSC) is an international non-profit organization that verifies sustainable sourcing from forest to consumer. The group has certified more than 210 million hectares of forest worldwide, finding that they meet the highest environmental and social standards. When architects specify a product that has earned an FSC label, they know that the world’s forests are not harmed in the production of that material.
Consider Decay Resistance And Durability
When we talk about durability in wood, it most often references the wood’s natural resistance to rot and decay. There is tremendous variability in the decay resistance offered from species to species.
T he durability of wood, and comparing the durability of different species, is the focus of a report titled, “Natural Durability of Wood: A Worldwide Checklist of Species,” authored by the Forest Research Laboratory, Oregon State University. In it, the researchers assign a numerical resistance rating to 1500 species.
According to the paper, “Durability of a wood product subjected to a decay hazard is determined by both the inherent decay resistance of the wood and the magnitude of the hazard. The risk of decay in wood can vary widely with moisture availability, soil condition, and climate.”
T he report rates the durability of different species on a scale of 1-4.
1=very resistant.
2=resistant.
3=moderately resistant.
4=nonresistant.
T he list of species that were found to be very resistant to decay in the temperate American climate include, but are not limited to: White cypress pine, Coffeewood, Western juniper, Virginia pencil cedar, Longleaf pine, and White oak.
Consider Resistance To Termite Infestation
Termites are another worrisome threat to the longevity of wood products. Termite-resistant wood species promote both termite mortality and reduce mass loss from termite damage. Species such as Yellow Cedar, Juniper, and Ipe all show low mean mass loss and high termite mortality when subjected to termites. The use of Alaskan Yellow Cedar is recommended on projects where termites may be more severe or threaten to damage supplied wood products more thoroughly.
I f wood species are selected that are not naturally resistant to termite damage, some wood products manufacturers can provide a termite-resistant additive to the topcoat that will provide similar benefits. While there are many options for termite treatments such as TimBor and BoraCare, the simplest application method is as a finish additive as it does not incur extra steps or cost during the manufacturing process. Another solution is the use of Copper Naphthenate, a common ingredient used in industrial and commercial wood preservation, in a very low concentrated
A s a general rule, architects may want to consider using wood species that are susceptible to photodegradation selectively in locations where non-uniform photodegradation cannot naturally occur. This references locations where natural or created shadow lines or selective UV blockages are not present.
An Attachment Discussion Installation
form. Copper Naphthenate has significant insecticidal activity in termites and has antifeedant properties, both limiting the number of termites feeding on the treated material and increasing the mortality rate of those that did.
CONSIDER RESISTANCE TO PHOTODEGRADATION
Light sources can negatively impact the look of exposed wood surfaces. According to the 2014 Architectural Woodwork Standards 2nd Edition, “Photodegradation is the effect on the appearance of exposed wood faces caused by exposure to both sun and artificial light sources. If an entire face is exposed to a light source, it will photodegrade somewhat uniformly and hardly be noticeable, whereas partially exposed surfaces or surfaces with shadow lines might show non-uniform photodegradation. Some woods, such as American Cherry, Fir, and Walnut are more susceptible than others, and extra care should be taken to protect against the effects of non-uniform photodegradation.”
An important element of every wood wall and ceiling system installation is identifying the best way to attach the wood ceiling and wall system to the project. This issue can also cause some confusion in the architectural audience. Sometimes designers and architects will sketch something that doesn’t have any visible method of attaching to the underlying building components.
T here are so many different types of wall and ceiling system products and solutions that exist. From linear planks, to cubes, to flat or curved veneer panels, acoustic panels, and beams, it makes sense that there are also a number of available attachment methods. Simple, non-proprietary solutions include z-clips, 15/16-in. grid, torsion springs, c-hangers, and hanger wire. These common and industry standard attachment solutions offer straightforward methods for affixing decorative surfaces that are often used throughout a building.
On the other hand, there are attachment methods that are best described as complex and proprietary. What this means is that whatever the creative vision is that needs to be achieved, there is either a simple solution or a custom solution, but there is a solution.
CASE STUDY
2+U QUALTRICS TOWER

Encircling the historic Diller Building at the corner of 2nd and University in downtown Seattle rises a classically clean, yet elegantly unique skyscraper. The structure houses 1,000,000 sq. ft. of office space and peers directly over the Puget Sound. The windows reflect Seattle’s skyline while the occasional splash of wood connects the buildings to the heavily forested pacific northwest. The skyscraper—now renamed Qualtrics Tower—stands completed, ready to welcome occupants as the city’s downtown continues to evolve.
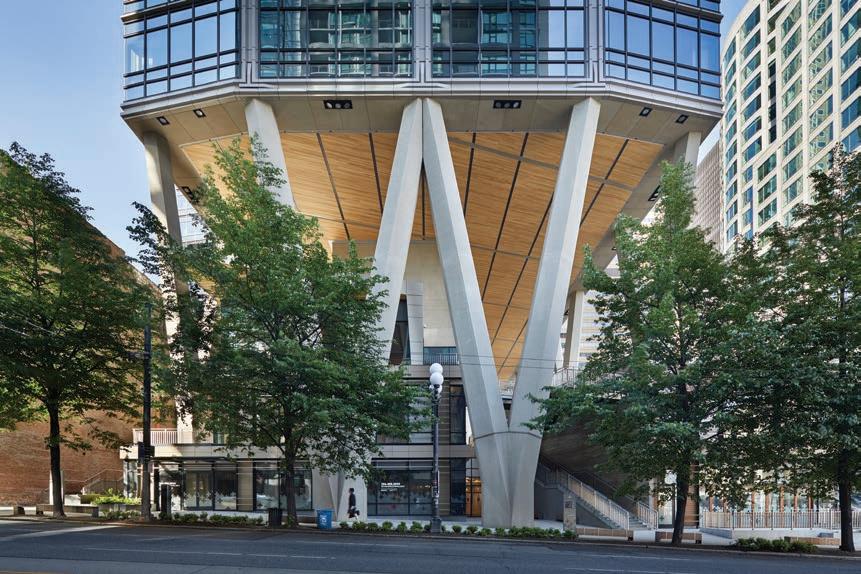
One of the most inviting spaces, the dynamic, open-air, urban village beneath the tower, creates the illusion of a tree canopy over a set of concrete terraces. The 24,000 sq. ft. public space includes local retail, art, culture, and green spaces and is capped by a protective covering of wood. The original plan was for this element to be a 4-in. wide tongue-and-groove Ash lumber that would be finished with a fire-rated coating on-site. This approach posed some concerns, because applying finish to an already-installed system does not fully coat individual boards (front, back, and sides) and often does not provide for a fully enveloped fire coating or a balanced finish to prevent warping or cupping due to expansion and contraction. Attaching loose tongue and groove boards to a completely sheathed substructure without a proper layout would have been incredibly time-consuming and detrimental to the visual aesthetic of the design concept. Instead, the decision was made to use a pre-finished Linear Closed system that was modified to match the style of the original ceiling design, provided a Class A, factory-applied finish, and developed an invisible attachment method that would retain the natural look and feel of the Ash ceiling system.
Unique to this ceiling design, multiple intersecting planes required that the wood ceiling system change orientation to either match or run perpendicular to the direction of the slope. A loose-board tongue and groove approach to this layout would have resulted in multiple complex cuts and no guarantee of alignment accuracy, which was another issue with the original plan.
Case Study
CHILDREN’S HEALTHCARE OF ATLANTA
Children’s Healthcare of Atlanta’s North Druid Hills campus is the astonishing vision of pediatric care that aims to directly connect medical research with children in need all while maintaining an environment that is healthy in design and transformative in spirit.

T he first on-campus building to open was the Center for Advanced Pediatrics, an impressive eight-story, 260,000 sq. ft. outpatient care center that provides 40+ services to medically complex patients with chronic illnesses. The calming lobby space is the centerpiece of this building where a combination of curved and flat veneer panels climb the walls and spread out across the ceiling, mirroring the outdoor tree canopies and paying homage to Atlanta’s affectionate tag of being the “city in a forest.”
T he design of the ceiling was conceptually difficult. In this half-circle entry space, flat veneer panels line the ceiling and the walls in 2-ft. wide strips while complex curved panels create the arcs that allow the wood to wind from floor to ceiling. The wall panels at the center of the room arc mirror the size, orientation, and reveal spacing of the ceiling panels, but as you move away from the center, this symmetry moves further and further apart. The transition panels are curved and need to be cut to be parallel to connecting floor and ceiling panels and kerfed (i.e. machined to allow for panel flex) at the correct angle to maintain an exact radius and proper alignment as required by the room design.
The key manufacturing hurdle was unfolding the surface curvature of panels to the far right and left of the center radial line as this resulted in panels that were too large for nominally-sized MDF sheets. The curved panels that fell within the first 20 degrees left and right of the center radial line could be cut from 4-ft. × 8-ft. sheets. Panels outside this range exceeded nominal substrate dimensions. In order to solve this problem, extra reveals were added to limit overall panel size and provide better panel optimization.
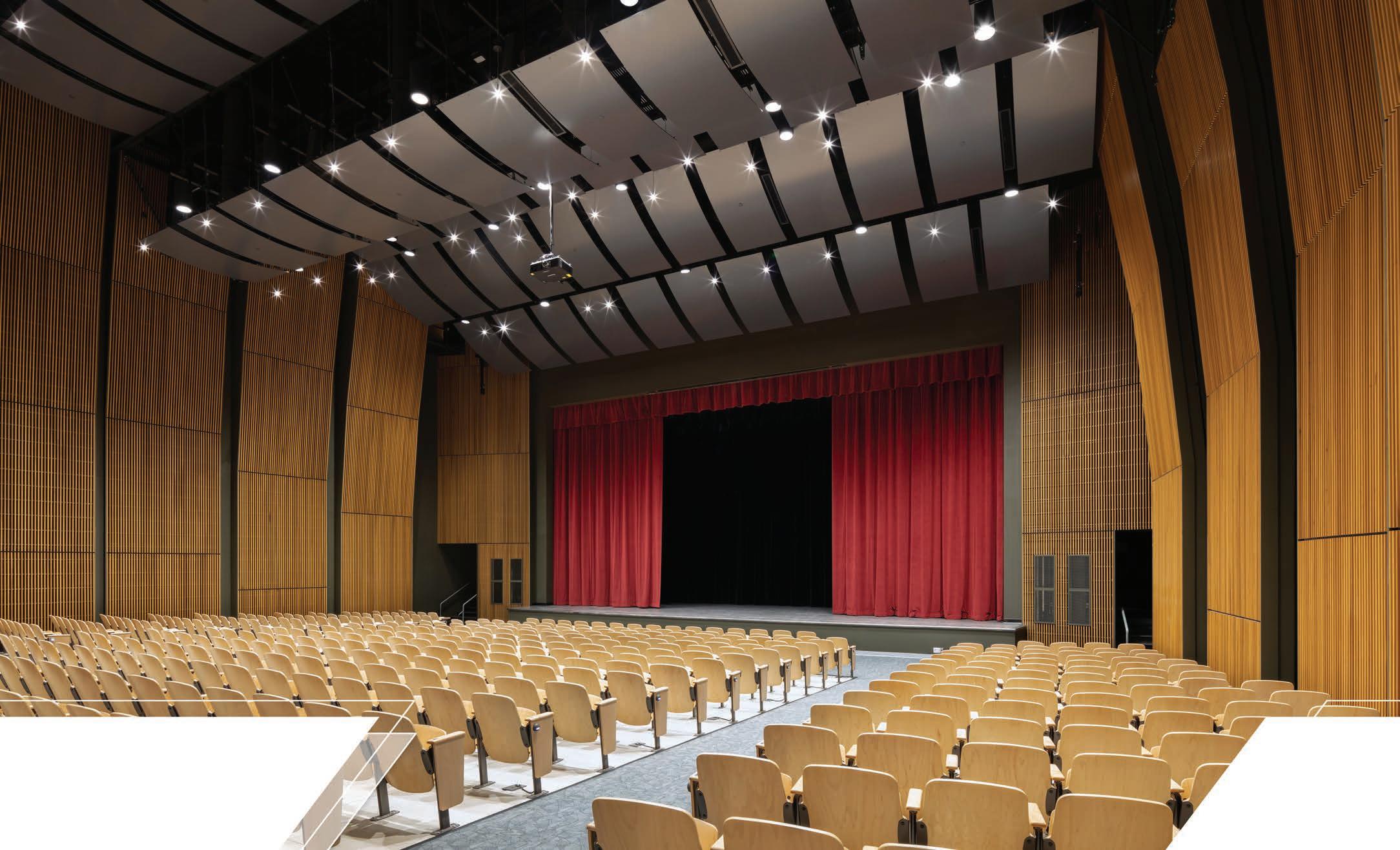
PROJECT SPECS
INSULATION