PORTFOLIO
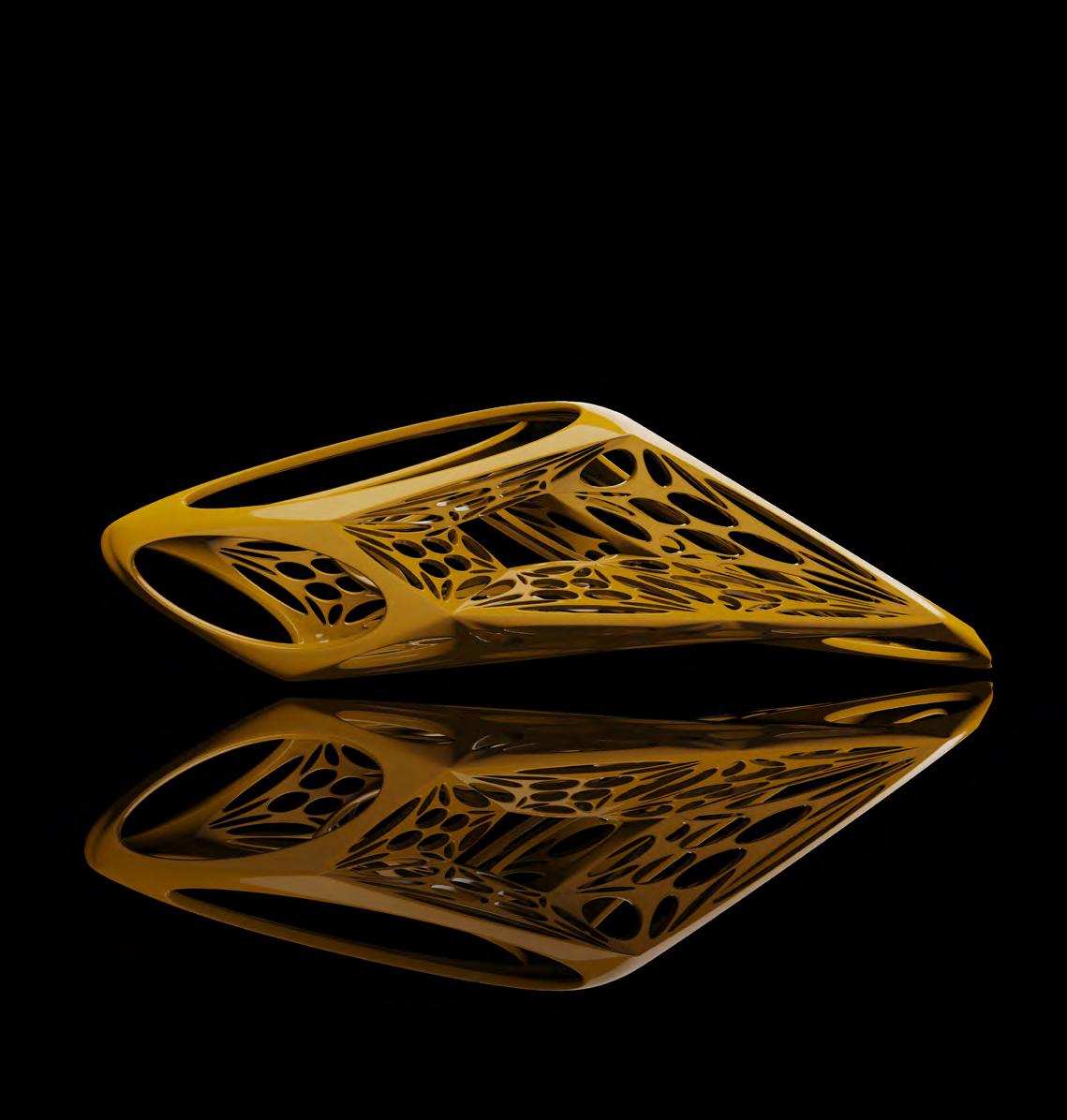
Project : Interior Design Project.
Location: Trivandrum,Kerala,India
wood used: Jack fruit tree wood.
Drill bit used: 3mm
A Pooja Door that was created parametrically for an interior design project in Trivandrum, India.
A CNC router was used to perform 3D carving and routing on this one-of-a-kind pooja door.
• A one-of-a-kind design.
• Hard to replicate with a hand or a carpenter.
• The only way to bring this to life is through digital fabrication.
To produce iterations for the door design, an attractor curve concept is applied.
Two curves are used here as attractor geo. One controls the aperture openings, and the other controls the height of the extrusions of the frustum.
The door is being built on-site. This project was an incredible learning experience, with numerous technical skills learnt along
Project : Interior Design Project. Location: Kakkanad,Kochi,Kerala,India wood used: 12 mm HDF board. Drill bit used: 6 mm
A parametric ceiling and wall paneling inspired by natural organic waves and bumps. This stunning work of art is displayed in front of the apartment’s front door. Nobody leaves the corridor without taking a second look and admiring this one-of-a-kind work of art.
• Smooth
• A one-of-a-kind design.
• Hard to replicate with a hand or a carpenter.
• The only way to bring this to life is through digital fabrication.
This fluid design was made by lofting two sets of curves.
One is a collection of straight lines, while the other is a collection of wavy curves.
The control points are used to precisely manage the wavy curves to achieve a suitable form and texture.
The two curve sets are then grafted and lofted to create the desired surfaces.
They are ultimately contoured for depth.
12 mm HDF boards are router cut and assembled.
Here are a few of the numerous iterations that were developed to attain the final form.
Sheet set A
Sheet set B
Sheet set C
The artwork is divided into three halves in order to fit in the router machine.
Page No : 13
Project : Interior Design Project.
Location: Trivandrum, Kerala, India
Material used: 3 mm ACP panels
This parametric jali was designed for a lightwell to regulate the lighting during the day and was digitally fabricated using CNCcut ACP panels.
• Intrinsic but simple.
• A one-of-a-kind design.
• Capable of controlling lights.
• Bold Shadow art.
A wonderful work of shadow art that shows interesting patterns as the light moves around it! Both daylight and moonlight produce patterns of shadows that never repeat.
As the sun rotates around the earth, the poetic interaction of light and shadow creates patterns that never repeat themselves, enhancing the interior experience.
Project : Experimenting 3d printing on a medical application.
Location: Pune, India
Material used: PLA
Printer :FDM printer
This brace was created in partnership with MetaFix Ortho LTD, an ortho medical firm situated in Pune, India.
This is a Thumb Immobilizer, and it is used to treat thumb fractures. This brace can be used instead of plaster of Paris hand braces. They are both lighter and more aesthetically appealing.
Quad remesh is used to optimize the patient’s handscan mesh. Then Voronoi patterns are projected onto the mesh based on a few attractor points. The attractor points are used to influence the density of the cells .
Cells will be denser in the fractured area and lighter elsewhere. The mesh is finally divided, optimized for slicing, and printed in two pieces.
Project : 3D printing for children with Club Foot illness.
Location: Pune, India
Material used: Nylon
Printer :SLS printer
This brace was created in partnership with MetaFix Ortho LTD, an ortho medical firm situated in Pune, India.
This is a leg brace for children with clubfoot. This brace can be used instead of plaster of Paris hand braces.
They are both lighter and more aesthetically appealing.
Quad remesh is used to optimize the patient’s leg scan mesh. Then some patterns are projected onto the mesh
The Animal shapes are used to make the children happy. The mesh is finally divided, optimized for slicing, and printed in two pieces.
Clubfoot describes a range of foot abnormalities usually present at birth (congenital) in which your baby’s foot is twisted out of shape or position
Doctor will move baby’s foot into a correct position and then place it in a cast to hold it there.
The Venus pavilion is an output of conceptual abstraction of a Venus fly trap and the local textures of Emirati flavour leading to a perfect amalgamation of nature and art!
This pavilion will act as a catalyst which amplifies the exchange of art and culture ! Just like the Venus plant, the pavilion attracts creative minds from all over the world, captures their imagination and dreams, and acts as a catalyst for many more creative mutations of ideas.
I believe that 3D printing technology offers a lot of potential for creating unique and innovative fashion designs for several reasons:
Customization: 3D printing technology allows for mass customization,ie individual products can be customized to fit the needs and preferences of individual customers.
Design Flexibility: 3D printing technology offers designers more flexibility and freedom when it comes to creating designs.
Sustainability: 3D printing technology is more sustainable than traditional manufacturing methods because it produces less waste and requires fewer resources.
Innovation: 3D printing technology is still relatively new, which means that there is a lot of room for innovation and experimentation.
Material Variety: 3D printing technology allows for a wide range of materials to be used, including plastics, metals, and even fabrics. This means that designers can experiment with a wide range of materials to create unique and innovative fashion designs.
Overall, I believe that 3D printing technology offers a lot of potential for creating unique and innovative fashion designs that would be difficult or impossible to create with traditional manufacturing methods. The technology allows for customization, design flexibility, material variety, sustainability, and innovation, all of which are essential for creating successful and memorable fashion designs.
Snippets from my class rooms. As part of my startup, I’ve been teaching designers visual coding with Grasshopperfor the past 1 year.
‘Environmental Analysis’ workshop for semester 5 architecture students conducted at SEED Kochi College of Architecture.
About the workshop:
The goal of the workshop was to introduce the scope and potential of computational design in architecture.
Implementing simple energy calculations for designing sustainable architecture.
Using parametric design techniques to create the optimum output for the design.
The participants get and overview of the different technologies for design development.
The workshop was cnducted during december last week