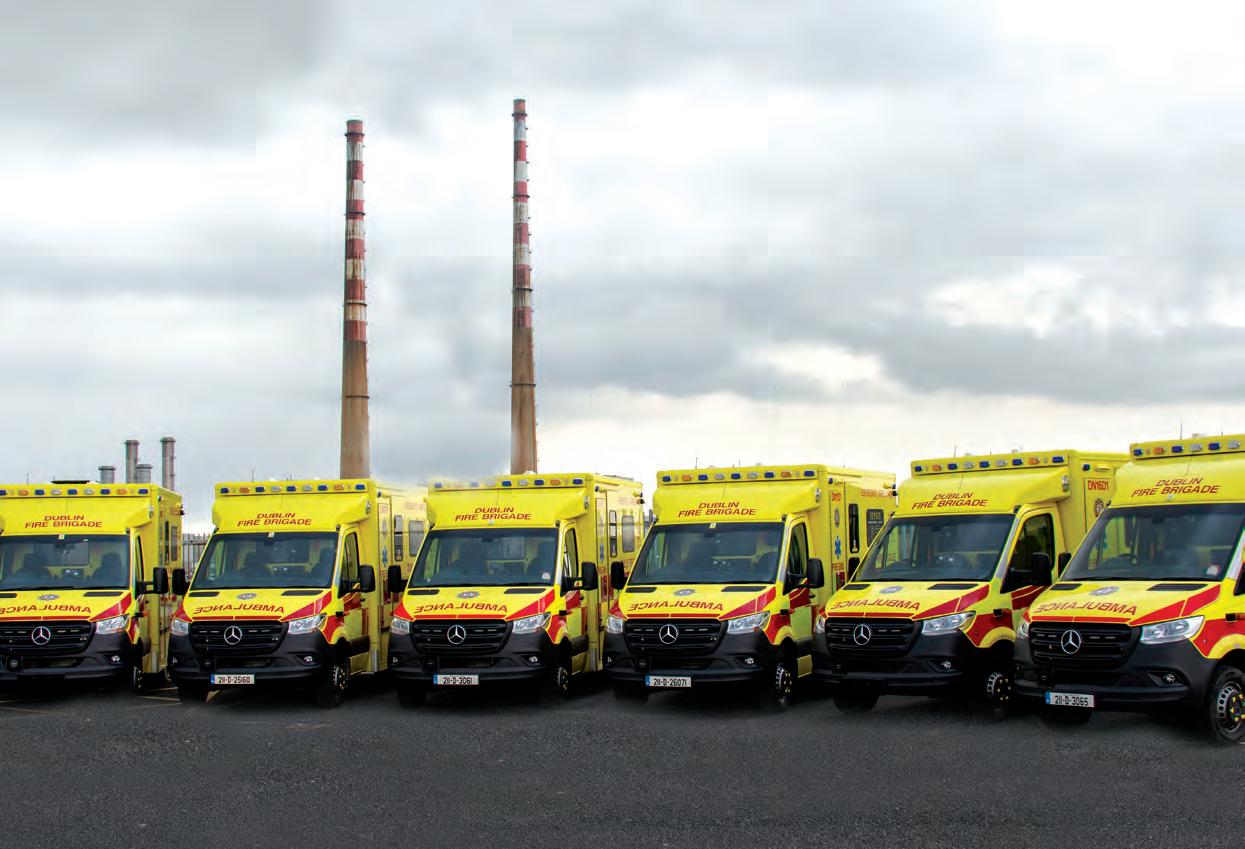
11 minute read
ADDITIONS TO THE FLEET
The DFB Service Support Unit has done excellent work to oversee the seamless integration of seven new ambulances into the fleet.
Dublin Fire Brigade took delivery of seven new Mercedes Benz Sprinter ambulances this year as part of its Fleet Replacement Programme, significantly reducing the average age of its 14 frontline ambulances. Each new vehicle has already been designated to stations across the city and county, and is the result of months of planning, preparation and production by the
Service Support Centre in Stanley
Street, otherwise known as Logistics.
The Department headed by A/C/O
Richard Hedderman with Third Officer
John Guilfoyle, and D/O Martin Cooke overseeing day to day management, plays an essential 24/7 role in keeping a full complement of frontline vehicles on the road at all times, and the introduction of several new vehicles and subsequent cascading of older vehicles to other areas has required an enormous amount of work.
“With 14 EMS vehicles on the frontline, it would be very unusual to be able to get seven new ones in a particular year, so this has been a big event for us,” T/O Guilfoyle tells me. “There is a huge amount of work involved in procuring these new vehicles, from working with the National Ambulance Service to try to secure funding and allocation, to strategic planning with management, before we can even go and order them.
“Every year myself and A/C/O Hedderman sit down and have an annual review of the fleet,” he tells me. “We see what our allocation is, we begin the planning, some of which is around the build and schedule, making sure each vehicle arrives the way we ordered it so it is specific to our emergency service requirements.
BESPOKE
“Every vehicle has to be bespoke, and needs to be planned in great detail. We don’t have off the shelf vehicles, so before they arrive with us, we have project build meetings with the coach builder. There is a six-month process with a detailed specification that could include up to 600 features
that have to be agreed, before going into production. All of this happens throughout that six-month process, until we reach the final production of the vehicle bespoke to our particular needs.
“This goes right down to the shade of red paint used, the reflective markings that have to reach standards, the lettering - everything. You have to make sure that absolutely every single spec is right, starting from the very obvious one – that it has to be righthand drive. That’s all the background work that nobody sees. It starts off on a desk and there is an enormous amount of planning involved, but it is great when the ambulances do arrive, are made ready, and then head out to the stations.”
That process of preparing the vehicles to join the fleet in the workshop is also a detailed endeavour, as D/O Martin Cooke explains.
“We liaise with Wilker, the builders of the vehicle body, and with Mercedes as manufacturer, and work in tandem with them so when they are putting the body onto the back of the chassis, they have to make sure it is seamless, to make sure the new technology goes into the vehicle.”
The stations who were allocated the new vehicles were Swords, Finglas, Tallaght, Donnybrook, Rathfarnham, Kilbarrack and Blanchardstown.
“We generally decide based on mileage where each new vehicle is going to go,” D/O Cooke says, “but we still have a lot of work to do with them after that, and look at where other equipment is going, as well as the vehicles that are being replaced with the new ones, so there is a natural cascading of vehicles and equipment.”
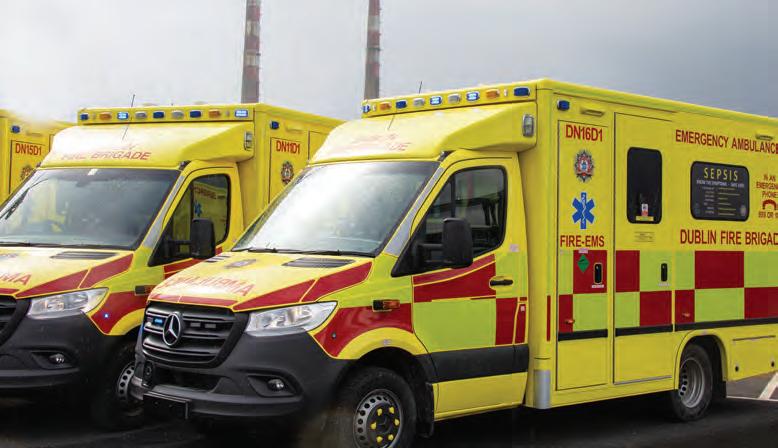
FEATURES
T/O Guilfoyle adds: “There is always some tweaking that needs to be done. Defibrillator brackets have to be fitted, vehicle recording and tracking systems, and finally the digital radio system. So, there is quite a bit of work, and then they have to be badged up with the relevant call signs, depending on where they are going into service.”
D/O Cooke says: “Yes, we have seven 2021s, but we also got in three of the new ambulances last year, so we now have ten of the new Mercedes ambulances with the latest technology, and then four others make up the frontline fleet, with more in reserve.”
T/O Guilfoyle also adds: “They all have a lot of other important features too. If you take environmental factors in, they are all Euro 6 standard for emissions, which is a big plus we want to promote, so they meet all stringent regulations for emissions. We want to have the lowest possible environmental impact, and that is always in mind when we bring in new vehicles.
“Also, we have the latest communications features to be added, which is another story entirely (and is covered elsewhere in this issue) – digital radio systems, webbased camera recording systems in the saloon for security reasons, mobile communications between crews, defibs, live patient data being sent to STEMI labs and emergency depts. The ambulances are essentially a central communications hub with live information. They are just some of the advancements we have now, as well as vehicle stability systems, driver aids, automatic braking, speed detection, all the best technology and specs.”
D/O Cooke adds: “There are also other features that improve the health and safety of our paramedics as well as patients. For example, there can be a lot of strain in lifting a stretcher on to the vehicle, but now we have a tail lift that makes it much easier and smoother. A lot of research has been done into ambulance ergonomics and there are many improvements such as having a clinical waste area, and air-con in the cab for crew comfort. The Mercedes vehicles give us very little trouble. They are lovely to drive, I can say from experience.”
The new vehicles are state-of-the-art.
D/O Cooke with S/O Richard McDonnell .
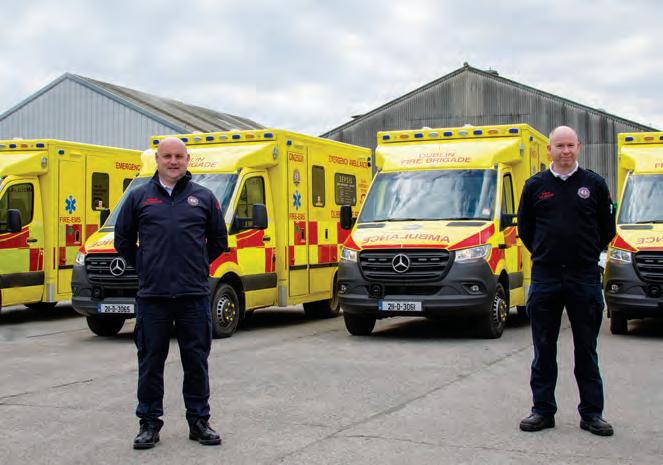
ADVANCEMENTS
This makes for a much more comfortable vehicle that meets the needs of a modern emergency service, and A/C/O Hedderman points out just how far DFB ambulances have advanced over the years.
“When I first joined in 1982, all you had was a normal vehicle with a box on the back of it, and all you had was triangle bandages, presses and wooden splints,” he says. “We have moved from that now – the defibrillator is probably one of the biggest advancements we have had, but there is a whole range of equipment on board now – cannulas, intubation, and the training for our personnel has also really advanced over the years. Probably the biggest development we have seen recently is in the use of STEMI labs. Our guys go out and get defibs on to the patient and get cardiac readings on the cardiograph and communicate this information directly to the Hospital.
“There is a place for everything on the ambulance now, from the clinical waste to the lockers to PPE for dealing with the likes of COVID-19. There have been huge changes to the role of the paramedic, and with that there have been many changes to the ambulances they work in. With that comes an improved service to the public, but it also means that the average age of our ambulances is now three years.”
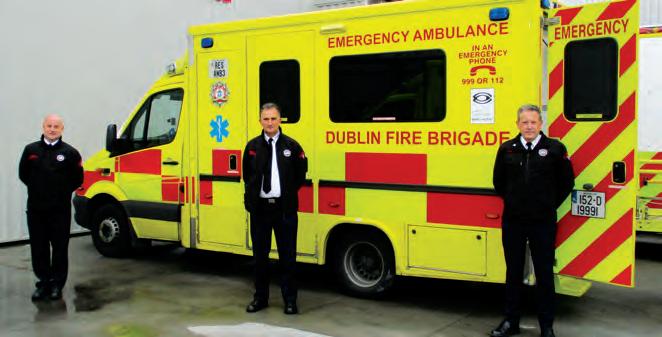
D/O Martin Cooke, A/C/O Richard Hedderman and T/O John Guilfoyle oversee fleet maintenance and replacement as part of the Services Support Centre’s multi-functional role.
FLEET MANAGEMENT
That’s where the Fleet Replacement Programme comes in. The 14 vehicles cover around 90,000 call outs annually, covering a million kilometres, so when they come out of frontline service, they will have had a short but busy life. However, their service doesn’t end there, with the cascade plan forming an important part of the programme.
“When we start looking at our cascade plan, we can see decide that some units may move from a lessbusy station or one that covers less mileage, and we allocate a new vehicle to those that cover a lot of ground,” T/O Guilfoyle says. “For example, one went out to Swords recently and in three weeks had already covered 8,000km. That’s due its first inspection from Mercedes already, whereas on a normal vehicle it wouldn’t be due for six months, and this is all monitored as part of our fleet planning and maintenance systems.
“Any maintenance or inspection due is flagged on the system, but sometimes we try to precede the manufacturer’s servicing notice because it is an emergency vehicle with an arduous work schedule.”
FURTHER ADDITIONS
DFB has also procured other new vehicles to add to the fleet, with a 42-metre turn-table ladder due to be introduced later this year. “That is ten metres higher than our current highest ladder, in order to enhance our high-rise response,” T/O Guilfoyle tell me. “We have also been allocated four Class B Fire Tenders, we have an electric van on order, a new rescue boat due in October, and interestingly,
An ambulance is readied to be taken out of frontline service as part of the Fleet Replacement Programme.
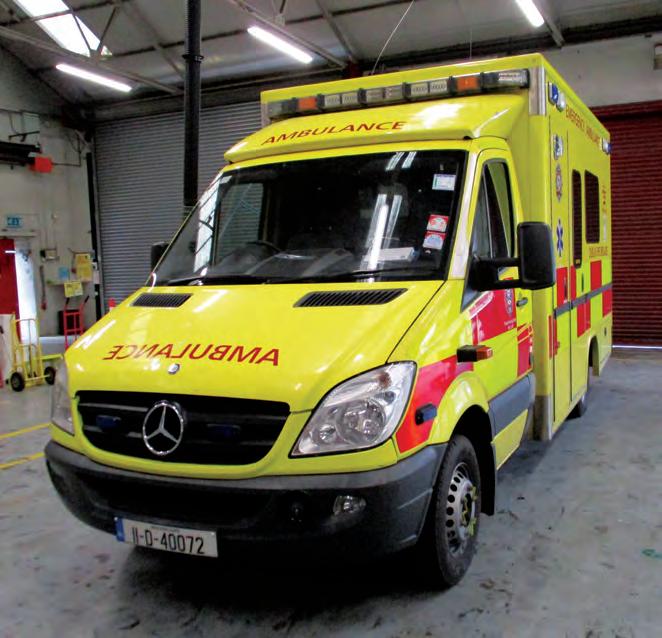
two electric bikes on trial that will be used to make journeys across the city to DCC buildings.
“The turn-table ladder is scheduled for late December. DFB procured this vehicle via a public tender process and when the contract was awarded, myself and Martin started liaising with the supplier on project plans because you can’t just walk into the showroom and order this type of vehicle off the shelf.”
Of course, the fleet replacement programme must tie in with the training plan as part of strategic management. “It is important that our training centre know these vehicles are coming into service, because it has to marry up with the Brigade’s Training Plan,” T/O Guilfoyle explains. “The last thing we want is for a vehicle or piece of equipment to be delayed entering into service because the specialist training hasn’t been scheduled.”
With the new ambulances already on the road, feedback has been positive.
A/C/O Hedderman says: “The thing about feedback is that if you hear nothing, everything is good. If there is anything wrong with the vehicles, or anything they are not happy with, our personnel are very quickly on to you about it. We are very happy that our staff regularly engage and are willing to provide feedback. It is a continuous loop of improvement.”
“Manufacturers have told us that they know we test everything to the maximum,” D/O Cooke tells me. “If they put something into Dublin Fire Brigade first, they know it will get a punishing time, and the product must be good. They have said that if we have a problem after the first year, they tend to see it in other areas of the country later.”
T/O Guilfoyle agrees. “You will definitely see any issues surfacing a year in advance of seeing them in other services using the same product because our requirement is so intensive. You have a year’s testing done within a couple of months.
“The feedback we do get always feeds into our next set of specifications. Each time we are allocated vehicles they vary slightly, and that is because of advancements in technology or crew input, but mostly both, and how we want to use the vehicle more practically.
“There are examples of that in the vehicles coming in. We have recommendations that will be incorporated into the specs, such as with helmet storage, shelving, air conditioning – we listen and take ideas and suggestions on board, and where we can accommodate them, we do. We want our people to be happy in these vehicles because they are a place of work for our personnel.”
The vehicles being replaced on the frontline will still be of use, of course. “Some will be cascaded into our reserve fleet, and some of the reserve fleet will be dismantled for parts here,” T/O Guilfoyle tells me. “We can take parts of the vehicle, such as the patient compartment of the ambulance, which can be used for simulated live training. They still have a role to play. They are well finished by the time we dispose of them!”
As for the new vehicles, T/O Guilfoyle says they will have a huge impact. “They will bring about a reduction in fleet maintenance costs, reducing downtime,” he says. “When you put new vehicles into operation, and in this instance seven new vehicles, the maintenance and purchase of parts will all change because of this major investment. We really hope our crews are happy with these vehicles and all the journeys they take in them will be safe ones.”
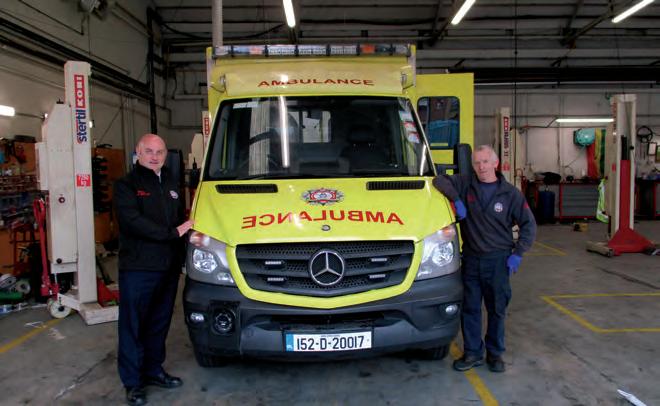
D/O Martin Cooke and Garage Foreman Fran Lynam with an ambulance being readied to be taken out of frontline service.