
17 minute read
Maintain Plant Production
The redesigned EX 120 HMA plant from ADM takes up less real-estate on the job site.
RRefinitiv hosted a webinar Dec. 1, 2020, titled “Caribbean Energy Outlook” in which Senior Energy Analyst Corey Stewart and Proposition Sales Specialist Michael Sahrman presented impactful issues for the Caribbean region as a whole. The information offered education to North American asphalt mix producers in a number of ways, including potential pricing of liquid asphalt cement (AC) products in the near future. The presenters looked at the relationships between prices and the many factors that affect them—demographics, group preferences (such as owning/ driving a car) and population growth rates.
What I found most intriguing from the presentation was Stewart’s discussion of corruption’s effect on environmental stagnation. The presenters shared that the Annual Corruption Perceptions Report ranked Venezuela at 173 out of 180 countries, and Stewart shared that Venezuela’s problems are affecting refineries and storage facilities in Aruba, Bonaire, and Curacao, to name a few. When environmental disrepair is allowed to reach a critical point—as Bonaire’s BOPEC experienced—shut-down is the only responsible course of action. Shut-down in one area, of course, influences price elsewhere.
Also consider the effect COVID-19 had on the region. Stewart and Sahrman shared that COVID’s impact on the Caribbean had been less than 1 percent as of Dec. 1, yet still wreaked havoc on infrastructure.
“From a direct-impact perspective, the Caribbean has fared better than other areas of the world,” Stewart shared. “The story of Caribbean refining is one of hardship. First, Caribbean refining was affected by Coronavirus.” Workers did get sick, which affected maintenance schedules. “Schedules were largely put off. If you don’t maintain a refinery, it breaks down.” This same scenario is taking place around the globe.
Apply this concept to the hot-mix asphalt plant. Consider the maintenance schedule(s) at your asphalt plant or quarry. Have you allowed routine maintenance to slide as worker rotation has changed in the COVID-19 climate? It may be difficult to schedule workers for their optimum safety with distancing and still get all the components of the plant double-checked this winter, but you can bet the extra effort in scheduling and maintenance now will pay dividends in uptime this spring and summer.
Safe, smart scheduling of winter maintenance is paramount to optimum summer production. Let the manufacturers and service providers listed on the next few pages help you make the most of each worker’s time and expertise.
ADM
Producers in dozens of countries have experienced firsthand the high-quality asphalt plants manufactured by ADM, headquartered in Huntington, Indiana, including the EX 120 asphalt plant, part of the ADM EX Series of plants.
Recently redesigned with a reverse air baghouse (in lieu of a pulsejet), the single-drum EX 120 with counterflow technology is more compact and portable than ever. With its shorter length, the plant’s new design makes it easier than before to transport. Plus, the redesigned EX 120

BROCK Industries now supplies most non-proprietary parts and components for all makes and models of HMA plants.
takes up less real-estate on the job site, making the plant ideal for remote and demanding locations worldwide, according to the manufacturer.
For customers with smaller production requirements who need to meet all federal and state environmental specifications, the EX 120 asphalt plant gets up to 99.99 percent efficiency with the baghouse when normal clean aggregate materials are used, according to the manufacturer.
The counterflow technology also enables the EX 120 to achieve the highest level of heat transfer and fuel efficiency, using separate drying and mixing zones for highest quality asphalt production. Affordable and ruggedly built, the EX 120 offers producers a fast return on investment at a low cost per ton.
With up to 50 percent RAP usage, ADM customers who currently use ADM’s SPL Series of asphalt plants, and who require more RAP usage and environmental soundness, will want to explore the EX 120. A wide range of components is available to customize the plant to meet customers’ specific production needs.
For more information, contact Carlos Cardenas or Jeff Dunne at (260) 637-5729 or visit www.admasphaltplants.com/ex-series/. work environment with total focus on providing quality products and outstanding service along with building great relationships. We would not have the start we have had without our customers—and we thank each one for their business and support. Stay tuned for more announcements as we move ahead.”
For more information, contact Travis Sneed at (423) 476-9900 or visit www.brock.industries.
CARDINAL SCALE
Cardinal Scale, Webb City, Missouri, announced the acquisition of BeltWay Scales, one of the industry’s leading conveyor belt scale manufacturers, based in Rock Falls, Illinois. Belt-Way Scales has a partner network that spans multiple continents and 34 countries and has been manufacturing conveyor belt scales since 1992. The acquisition adds an additional product line to Cardinal Scale’s wide variety of scales and weighing equipment that the company manufactures. Belt-Way Scales’ employees, operations and manufacturing will remain in Rock Falls to continue with their own dedicated engineering, technical service and manufacturing departments.
BROCK
BROCK, headquartered in Georgetown, Tennessee, and established July 1, 2020, after the acquisition of 30-year-old JBK Enterprises, is pleased to announce it now supplies most non-proprietary parts and components for all makes and models of hot-mix asphalt (HMA) plants. BROCK also provides in field construction services for HMA plants including repairs, maintenance and plant relocation services.
Commenting on the announcement, Ben Brock, president and CEO, said, “In addition to our expanded product line we couldn’t be happier with our results so far. Our team, which together now carries a combined 238 years of hot-mix asphalt plant experience, is having fun in a great
COLORBIOTICS
Colorbiotics, Ames, Iowa, has launched Invigorate™ rejuvenator to increase the use of recycled asphalt and extend asphalt service life. The company has long served landscaping and sports/recreation industries, and was part of the former BASF Construction Chemicals business. Now, Colorbiotics and other former BASF brands make up MBCC Group, a supplier of construction chemicals and solutions worldwide.
Invigorate rejuvenator is a new soybean oil-derived additive that triggers chemical reactions inside recycled asphalt pavement (RAP) and stiff binders to break down asphaltene aggregation and reverse the effects of oxidation in the final mix. The Invigorate additive is designed

The Eagle Crusher 1200-CC with pre-screen feeder comes with a lifetime rotor warranty in North America on its solid-steel, three-bar, sculptured rotor.
to improve the chemical properties of lower-quality binders, addressing aged elements within RAP. This new technology, developed at Iowa State University, is designed to improve recyclability of asphalt while still meeting PG and performance-testing specifications.
“With Invigorate rejuvenator, we have been able to meet specifications and increase usable RAP material to as much as 50 percent, well beyond the standard 20 to 25 percent used today,” said Dan Staebell, Colorbiotics asphalt business development manager. “That obviously has environmental and economic benefits.”
For more information, contact (888) 663-6980.
CWMF
CWMF, Waite Park, Minnesota, announced in August 2020, the expansion of their facility. They are currently in the process of adding on an additional 6,300 square feet. The new area will house two more overhead cranes and a brand new 10-foot by 50-foot HD cutting table. The new table will double the size of the previous table, which will greatly increase cutting capacities. In addition to the expansion, CWMF also announced the purchase of 11 acres, which will be utilized in conjunction with their future growth plans.
For more information, contact Travis Mick at (320) 267-3805.
E5 ENGINEERS
To focus on improving plant operations, Malcolm Swanson has begun e5 Engineers, headquartered in Chickamauga, Georgia. The company builds upon Swanson’s decades of experience in engineering, innovating and environmental sustainability to assist clients with both sustainability efficiency concerns and quality control issues at the asphalt plant. Swanson explained that he intends to visit and inspect sites to offer clients a written set of recommendations, including potential value statements and actionable designs, to improve the asphalt plant operation with an eye toward environmental as well as quality control aspects. As a consultant, Swanson is not selling equipment, but is assisting asphalt production professionals in improving operations to meet all manner of environmental standards as well as production goals at asphalt plants, sand drying systems, environmental control systems, combustion systems and more.
For more information, visit the e5 website or reach out to Swanson at (423) 667-6781.
EAGLE
Introduced at CONEXPO-CON/AGG 2020, the UltraMax® 1200-CC with pre-screen feeder from Eagle Crusher Co., Galion, Ohio, is one of the company’s newest plant innovations, designed to increase asphalt producers’ overall production while reducing equipment wear.
This closed-circuit plant is equipped with all the features of the Eagle Crusher 1200-CC, the company’s best-selling plant, with the added benefit of an integrated pre-screen feeder that allows material at- or near-spec to be discharged before crushing. The plant was specifically designed for larger-sized jobs with high volumes of at- or nearspec material.
The plant features a two-deck inclined screen for producing two cubical spec products, and is also available with a twin-shaft screen option with third reliever deck. Top-deck retained material is returned to the crusher for further processing.
The 1200-CC with pre-screen feeder is available in tri-axle, tri-axle with tag axle, or quad-axle version, making the plant highly portable. The hydraulic lift and leveling system enables quick set up and tear down at the job site, using the hydraulic run-on legs. An available in-line magnet removes for transport. The 1200-CC does double duty, with crushing and screening on one chassis, and because most of the product may be removed for crushing when processing at- or near-spec product, equipment wear and tear is reduced, and overall production, greatly increased.
For more information, contact (800) 253-2453 or visit: https:// eaglecrusher.com/products/1200-25-cc-pre-screen-feeder.
EVOQUIP
Whether you are a fleet or service manager, staying connected and keeping track of your equipment helps to optimize machine performance and contribute to a positive impact on the bottom line. In recent years, telematics has enabled crushing and screening equipment owners to monitor work progress, manage logistics, access critical machine information, analyze and optimize machine performance, and perform remote operator support.
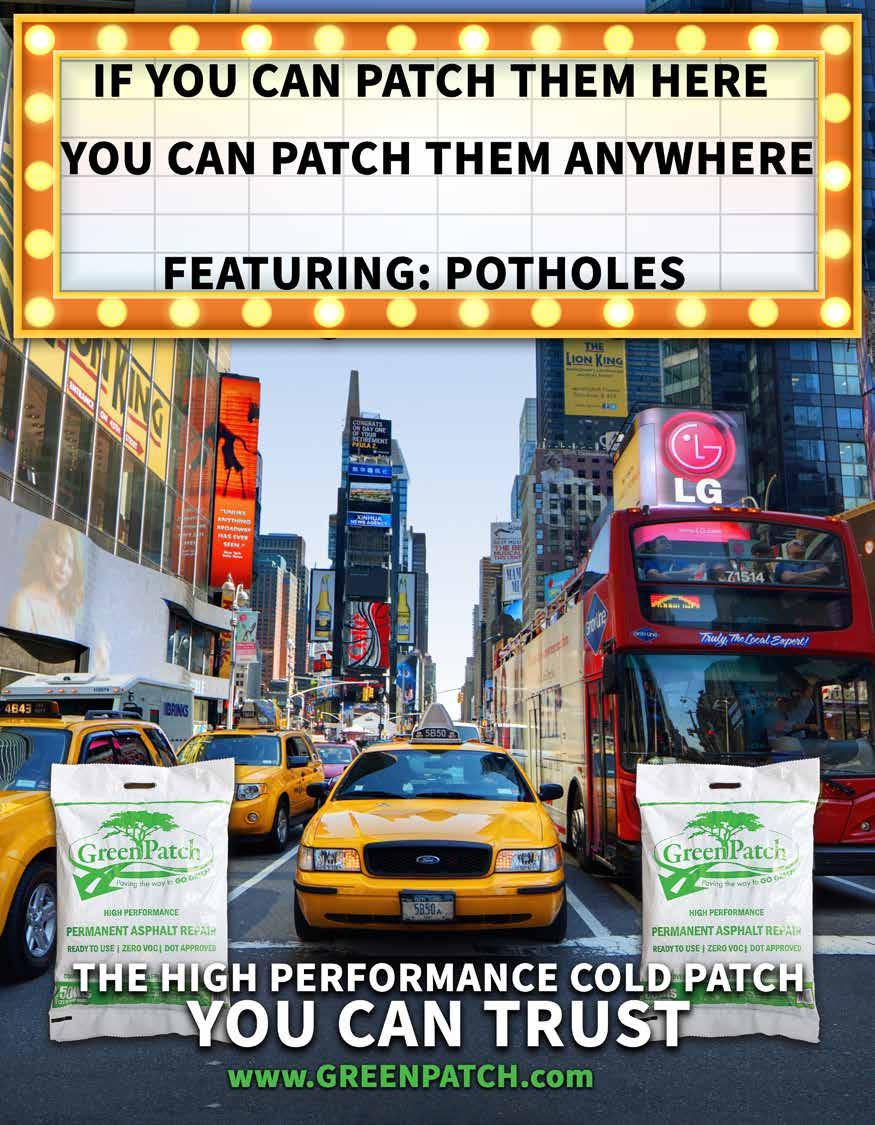
Mobile Screening & Crushing (MSC), an EvoQuip distributor in New Zealand, is no stranger to this concept, with telematics proving to be an essential tool in efficiently managing their hire fleet. Dan Meikle, MSC operations manager said, “We have had telematics fitted to make it easy to evaluate machine usage, billing and scheduled maintenance. This also enables us to show the customer their downtime and billing hours at the end of the month. In the past, this would have been a manual, time-consuming process.”
Paul Morris, Terex materials processing telematics manager, said, “Crushing and screening equipment operates in busy, challenging work environments. Telematics enables equipment owners to stay connected and keep track of their equipment, the information available can show you precisely what areas you can improve in to remotely optimize profitability, for both the equipment owner, but in the MSC case, the profitability of their customers too.”
Data is great, but value is created when data is transformed into information. “The goal of telematics is to make life easier for equipment owners, to reduce the total cost of ownership and not inundate them with meaningless data. It is about useful information that can be used to mitigate downtime,” Morris added.
MSC is well versed in this, Meikle explained. “If we are keeping up with planned maintenance, downtime is no more than one to two days per month on a long-term job. Telematics helps us monitor the machines remotely, which allows us to schedule maintenance and service intervals. Accordingly, we also give the machines a full inspection and clean after every hire. This enables us to pick up on problems before failure.”
Many of the EvoQuip crushers and screens are fitted with telematics, with new crusher customers benefiting from a 7-Year Free Subscription and 3-years on new screens from EvoQuip. The subscription includes the ability to consume the data through weekly customer report emails. The reports display information at a glance on metrics and diagnostics, allowing the operator to act before damage occurs; predetermined maintenance intervals are signaled, and error messages are displayed in plain text messages.
For more information, contact the EvoQuip team via Terex.
PAVE-AID™
FIBER FOR 100% RAP A SUSTAINABLE SOLUTION
Adding Pave-Aid to the mix helps achieve sustainability objectives.
• EASY TO USE • PROVEN LIFE EXTENSION • REDUCED MAINTENANCE COSTS

Ask us for a copy of our tech reports! WWW.FORTA-FI.COM
H&B
Haver & Boecker Niagara, St. Catharines, Ontario, introduced its TyDeck Ultra modular screen media. The polyurethane screen media offers accelerated screening action without the use of water.
Ty-Deck Ultra screens feature H-shaped openings made up of individual strips of polyurethane. Each opening is separated by two independent extensions parallel to each other. The strips vibrate independently to increase material acceleration, improving material separation and cleanliness, and often eliminating the need for a rinse screen. The rapid movement of the strips also virtually eliminates pegging and blinding. The screen is designed for handling abrasives with a top size of 50 millimeters on the second deck in non-impact areas. The polyurethane is poured open cast, allowing it to permanently harden when cured to maintain its chemical properties, and resulting in a 1.5-2 times longer wear life than injection molded screen media.
For more information, contact Kristen Randall at (905) 688-2644.
KESPRY
Kespry, headquartered in Menlo Park, California, announced Dec. 3 its Winter 2020 Aerial Intelligence platform updates aimed at helping businesses across the mining, aggregates, energy and other industries launch successful enterprise visual intelligence programs. The enhancements strengthen the platform's field-to-finish usability and ensure automation is a part of the entire stack—from capturing data to identifying critical business insights from it. Kespry’s Winter 2020 Aerial Intelligence platform updates include: enhanced inspection reporting; and image navigation and WingtraOne RX1 PPK support.
MAGNA TYRES
Magna Tyres Group has launched the 18.00-25 Magna M-Stacker (IND4) tire for use on reach stackers, empty container handlers and heavy-duty forklifts. The Magna M-Stacker has been developed starting from the already proven MB01 tread design.The 18.00-25 M-Stacker and 18.00-25 M-Stacker+ are now in production and with immediate effect, being offered to the market.
MAJOR
MAJOR, Candiac, Quebec, appointed Premier Equipment, based in Bellingham, Massachusetts, as its new aggregate and mining screen media authorized dealer.
For more information, contact Bill Boland at (508) 902-7752.
MCCLOSKEY
McCloskey® International, Keene, Ontario, has introduced the new RF80 and RF80R feeder stackers.
The RF80 feeder stacker is designed to facilitate the handling and stockpiling of materials including aggregates and sand. Materials can be fed into the feed hopper with large loaders or excavators, while variable speed prevents material from building up. Both the RF80 and radial RF80R are designed for low-level rear feeding, making them more accessible for various loader sizes.
The track mobility of the RF80 ensures the machine is versatile on-site. It’s available in dual power and diesel/hydraulic.
For more information, visit the McCloskey site.
PLANTDEMAND
A small company out of the United States and Germany, PlantDemand, has released a new feature with API integration that allows plant operators to integrate documentation to create custom dashboards with the company data. Custom reports with a data visualization tool can be created through a workflow using Microsoft Power BI and other tools.
Most businesses keeping up with digitization are using expert agencies in User Interface, which help foster software to make technology easy and useful to their specific needs. PlantDemand conducted User Interface tests and interviews and was iteratively built, tested and optimized for construction material planning. Because of this, it’s designed to be easy and efficient to enter, edit and move orders.
Daniel Mekis, who has more than 12 years of experience in asphalt industry materials operation, was an early adopter, and helped partner with PlantDemand, said, “For the first time, people could check what was on the schedule for the next days, know what aggregates and oils they needed to bring in, or who to contact on the job, all while viewing their smartphone and sitting on the couch in the evening. For the first time, our sales manager could pull to the side of the road, view the plants’ calendar and schedule (or move) a customer’s order on his iPad, while on the phone with the customer. Plant operators and supervisors had the important information at their fingertips. And for the first time, I could give my suppliers a detailed forecast with the click of a button.”
Organizations are working hard to reduce manual methods of completing repetitive tasks and are turning to technology to help. This will give time for the team to work on more important issues. Powerful, quick and simple tools that address these specific problems are perfect to add momentum to this journey.
PlantDemand is an online plant scheduling and forecasting software for the asphalt and aggregate industry. It’s available for desktop computer and on your iOS or Android phones.
For more information, contact Paulina Schaaf at PlantDemand.
RELIABLE
Reliable Asphalt Products, Shelbyville, Kentucky, is proud to introduce a revolutionary new era in burners, the Vulcan burner. Vulcan burners are a true combination fuel gas and oil burner, capable of running on multiple fuels, simultaneously if required, according to the manufacturer. Other game-changing features include a total air burner with a single motor and a coaxial blower to provide a near-linear fan curve, allowing for more accurate control over air delivery to the burner and less excess air required. The Vulcan burners are available in surface mount and long-nose configurations and in 80 MMBTU, 120MMBTU and 150MMBTU variants making it available for retrofit applications. There are also optional blower mount configurations allowing for the burner to fit into unconventional spaces.
The surface mounted combustion box is double walled and stainless steel, with an air venting system to help cool the unit. Vulcan burners are designed to be low maintenance—the direct driven fan has no belts or pulleys, meaning no misaligned drive belts or adjusting of those components. When maintenance is needed, the Vulcan burner opens completely to allow for easy access.
Vulcan burners come equipped with an over-temperature safety switch for automatic shut down in case of overheating. A second safety switch protects the unit in case the burner and fan/motor sections were to separate while in operation.
The VFD driven motor moves the same amount of air as other burners with larger motors, according to the manufacturer, meaning energy efficiency and cost savings. The fan intake is sound insulated for quieter operation. The adjustable and automated flame shaper can be adjusted while the burner is in operation and is completely profile-able. The burners are competitively priced, energy-efficient and simply designed with minimum moving parts.
For more information, contact (866) 647-1782, j.ferguson@ reliableasphalt.com or visit www.reliableasphalt.com.
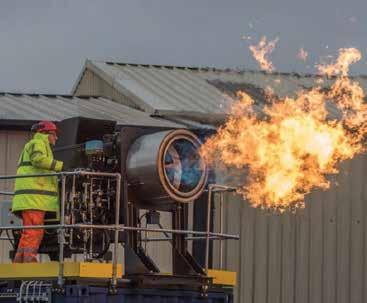
Reliable Asphalt Products is the official distributor of the new Vulcan burners, which are a true combination fuel gas and oil burner, capable of running on multiple fuels, simultaneously if required.
RUCKIT
Command Alkon, Birmingham, Alabama, has acquired Ruckit Inc. This transaction combines Command Alkon’s comprehensive
construction materials toolset and CONNEX platform for heavy work with Ruckit’s innovative solutions for digital ticketing, invoice reconciliation, and third-party management for aggregate, asphalt, paving, and trucking companies. Financial terms were not disclosed.
For more information, contact Command Alkon at (800) 624-1872.
STANSTEEL
Clogging and sticking of recycled asphalt products (RAP) on the screen deck can be a thing of the past. With the Turbo RAP Gator® from Stansteel, Louisville, Kentucky, RAP millings are shattered to one inch or less. The Turbo RAP Gator is designed to shatter clumps of material to help meet gradation specs and allow for processing 250 TPH of millings without plugging or clogging. It maintains specified milling sizes by breaking materials that have stuck together.
The Turbo RAP Gator has hardened steel teeth with chrome carbide plated tips that break up settled RAP piles. The two rolls are designed to also reject scrap metal and other unwanted items, keeping production going. The RAP Gator is placed inline on a recycle system and can be retrofitted to any manufacturer’s system on any drum or batch plant, portable or stationary, according to the manufacturer.
For more information, please call Jeff Mitchell at 502-631-0162 or 800-826-0223 or at jmitchell@stansteel.com. The small RAP millings produced by the Stansteel Turbo RAP Gator allow for improved heat transfer from virgin aggregate during production. This saves energy by using less heat and reduces the temperature of exhaust gas that feeds into the air system.

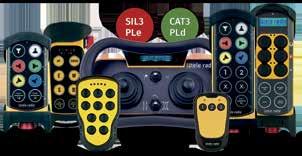
