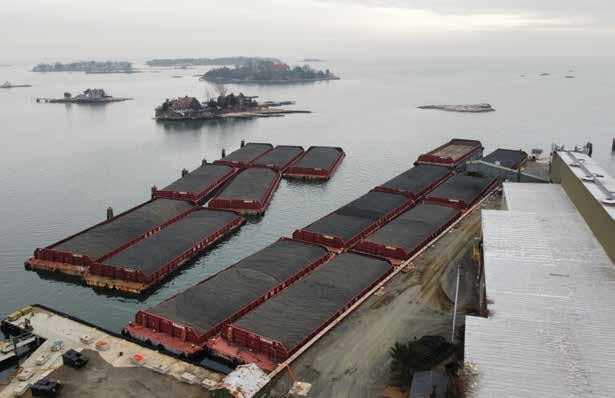
4 minute read
Tilcon Connecticut Barges Aggregate
BY ASPHALTPRO STAFF
Tilcon's Pine Orchard Dock has been in continuous operation since 1914 and accommodates large quantity deliveries to customers along the Connecticut coast, Rhode Island, New York and New Jersey, and occasionally elsewhere.
TTucked on-shore near the Thimble Islands, a group of small islands southeast of Branford, Connecticut, is a crushed stone aggregate transshipping facility. Known as Pine Orchard Marine Terminal or Pine Orchard Dock, the railroad and marine barge facility is owned by Tilcon Connecticut, New Britain, Connecticut, a CRH Company. Tilcon's Pine Orchard Dock has been in continuous operation since 1914 and accommodates large quantity deliveries to customers along the Connecticut coast, Rhode
Island, New York and New Jersey, and occasionally elsewhere. Although the company operates a large fleet of specialized trucks for delivering its products, their transport by marine barge offers many benefits to Tilcon and its customers.
According to the National Waterways Foundation, transport by marine barge has the smallest carbon footprint among transport modes. For an equal tonnage of cargo, a tugboat with barge(s) emits 30 percent fewer emissions than rail and 10 times fewer emissions than truck transport. Barging also offers reduced rates of spillage, fewer injuries and fatalities and the ability to move large volumes of materials.
One of the benefits of using transport by marine barge is that this type of transportation can load 1,800 to 2,000 tons of crushed stone aggregate on a single marine barge. That is equivalent to roughly 78-tri-axle truck loads or 20 railroad carloads. Additionally, tugboats aren’t impacted by traffic patterns and don’t face the same problems truck drivers often encounter on roadways.
Large tugboat availability, wind, weather, tidal timing and occasional bridge opening schedules can be challenging when delivering aggregate to the barge customer’s
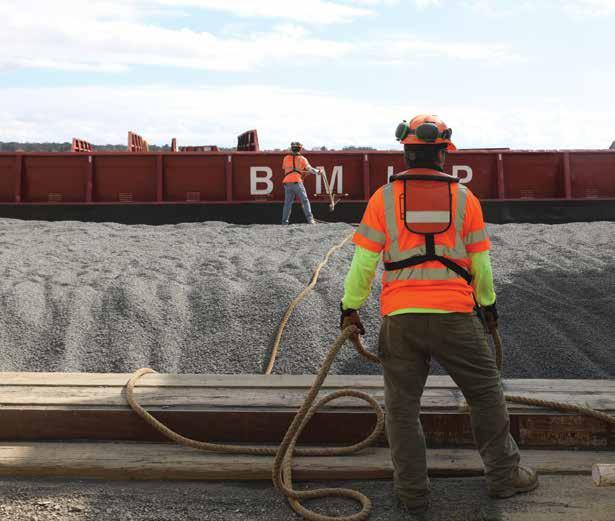
receiving dock facility. Tilcon’s affiliate company, Buchanan Marine LP, New Haven, Connecticut, operates the tugboats.
Ultimately, it’s up to the tugboat captains to decide what’s moving and when. Tilcon’s scheduling and Buchanan Marine’s tugboat captains have to occasionally contend with bridge openings and/or customers located in shallow canals and rivers. In those cases, they must schedule deliveries near high-tide or ensure a restrictive low bridge is open for passage.
Fortunately, many of their customers have deep-water docks where they can deliver at any time and without bridge openings.
Tilcon’s long-serving Superintendent of Marine and Rail Transportation James “Jim” Laske coordinates the deliveries with customers, tugboat and rail service dispatchers. According to Laske, the crushed and screened aggregate shipped by barge is sourced from Tilcon’s North Branford trap rock (igneous basalt) quarry. The material is transported to the Pine Orchard Dock by Tilcon’s Branford Steam Railroad. The railroad is approximately six miles long, and operates with several diesel-electric locomotives sized for their tasks.
Those tasks consist of moving dedicated Branford Steam Railroad 100-ton hopper
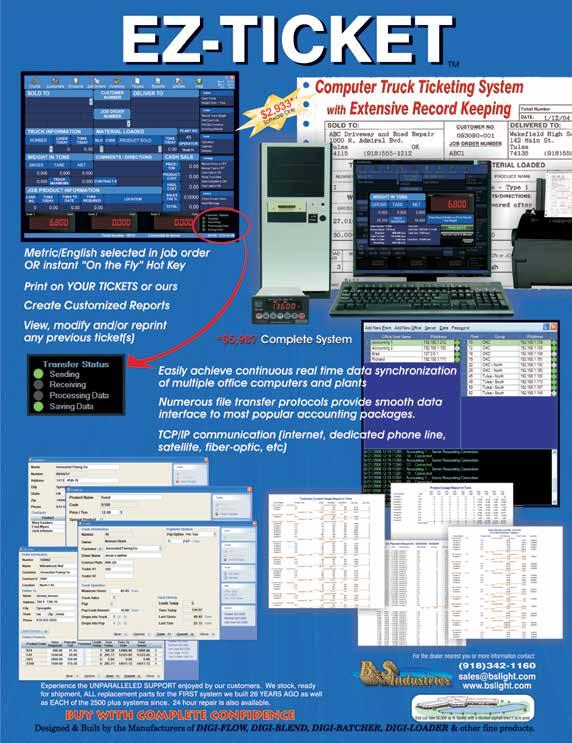
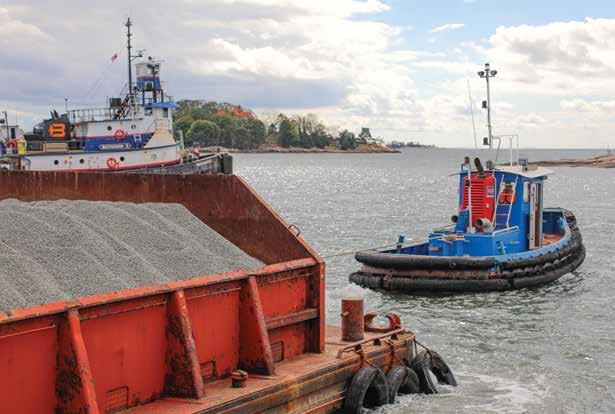

Barges offer several benefits, including the ability to carry greater quantities of material and they aren’t impacted by traffic patterns.
cars for loading at the quarry and transporting the fully loaded train approximately six miles to a marshalling yard at Pleasant Point Road in Branford, Connecticut. The BSRR hopper cars are finally pushed up a steep grade onto Pine Orchard Dock’s enclosed unloading trestle. The cars are spotted over pockets or bins below the trestle specific to the aggregate size to be unloaded. The cars are pneumatically operated bottom-dump hoppers and can discharge a full 100-ton load in less than a minute.
These types of operations can potentially cause noise and dust that could impact the surrounding areas. According to Laske, Tilcon enclosed the entire unloading and conveying operation in a 600-foot-long concrete and metal building equipped with sound-proofing, roof-mounted exhaust fans and LED lighting.
Beneath the building is a tunnel. Every pocket or bin for each aggregate size has a discharge opening in its floor controlled by a gate that feeds onto a large, long conveyor. The conveyor runs the entire length of the enclosed building and then up to an enclosed transfer conveyor, which feeds the movable barge loading conveyor. The final loading conveyor is equipped with HPLV (high pressure, low-volume) water sprays to eliminate any dust generated during the loading process. Additionally, the final loading conveyor swivels to allow the barges to be fully loaded side to side while being moved laterally along the dock by a cable and winch system.
Since much of the barges’ delivery and empty return movements are affected by wind, weather and tide height or bridge openings, Tilcon and Buchanan Marine also maintain some U.S. Coast Guard-approved heavy moorings at the most active and/ or challenging harbors. This allows some pre-staging of high-demand aggregate-size loaded barges or empty barges awaiting return to improve the efficiency of the available tugboat movements.
Tilcon’s barge transportation division delivers more than 6 million tons of stone by water each year to asphalt and concrete customers in the northeast region. Laske added, “These flat-bottomed water vehicles relieve traffic congestion, help the environment, and are considered a safe method to efficiently deliver large quantities of crushed stone aggregate material.”