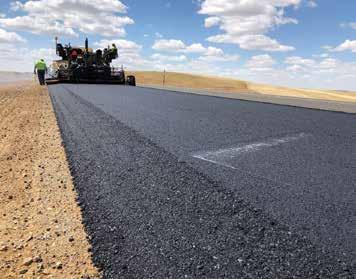
6 minute read
How to Pave RAP Mixes
Produce consistently in the field for successful paving with reclaimed asphalt pavement mixes
TBY BRYCE WUORI The asphalt industry is seeing more state departments of transportation (DOTs) incorporating higher percentages of reclaimed asphalt pavement (RAP) in mix designs. Whether your project specifies 5% or 50% RAP, there are practices you can perform in the field to produce consistency and complete a successful RAP project.
When working with RAP, the key from start to finish is consistency. Plant production, stockpile management, paver speed, roller patterns and even the milling operations from which the RAP is sourced, are just a few of the main variables that will need to be managed with great consideration. There are many more variables that must be managed correctly for success with RAP. The few listed above can be identified as more common and can take the least amount of effort to improve quality and produce consistency on your next RAP project.
CONSISTENCY FROM
START TO FINISH
It all begins with the RAP source that will be used in the mix design. The condition of the RAP source can affect the consistency of the mix leaving the plant. RAP mix that leaves the plant with inconsistencies will produce problems in the field for the paving and rolling operations. The foundation to producing consistency while paving with
RAP starts with the RAP source itself. Without this foundation in place the potential for all other procedures to be successful can decrease considerably.
If the RAP source is not from the existing project, further research and investigation of the material should be made prior to producing and paving. A few of the common variables that should be investigated with the
RAP sources include: • depth of the milling to produce the RAP material; • age and condition of the road or RAP source being used; • existing section of roadway where RAP material was extracted from; and • types of binder used in extracted road pavement.
These are just a few questions that can better determine what kind of consistency may be expected from the RAP source provided for the specific project.
If the RAP is coming from the existing road on the project, there will be a better chance at managing some of the variables that may cause future issues with the RAP material.
MANAGE MOISTURE
If the RAP source is extracted by milling operations, there are some management techniques that will assist with producing a more consistent RAP mix through the plant. Managing water during milling operations and RAP stockpile management techniques are two ways moisture can be managed when paving with RAP mixes. It is a well-known fact that moisture in the RAP source will cause issues at the plant with production and developing a consistent asphalt field mix.
Increases in RAP moisture being placed through the asphalt plant can cause volumetric issues that may include air void variability, asphalt binder variability (chasing AC) and plant production issues. When moisture is present in the RAP source, it will naturally take more thermal energy to remove this variable which causes strain on an asphalt plant producing the asphalt mix. If the moisture is not fully removed during plant production, we can see issues in the field or develop moisture in the asphalt field mix.
When there is a high amount of moisture in the asphalt field mix, often sweat dripping from the mix trucks can be detected. This is moisture leaving the mix through a thermodynamic process and is a very good indication that there is a moisture issue at the plant or with our RAP source.
Paving with RAP in Eastern Montana
LEFT: This tender zone appeared from moisture in the asphalt field mix. CENTER: Thermal image of 24% RAP project. RIGHT: Intelligent Compaction roller on a mill-and-fill project using RAP
Another common indication that there are significant amounts of moisture in the field mix include large amounts of steam leaving the newly laid asphalt mat behind the paver screed.
The final indication that we may be dealing with moisture in the asphalt field mix is when a tender zone develops during the rolling operations.
This tender zone typically develops within the intermediate rolling position and often requires the use of a rubber tire roller in place of steel drum roller to manipulate the mat.
Managing RAP source moisture is a very important step in producing a consistent RAP material for the asphalt plant and field operations. During milling operations, managing extraction speeds and water control can prevent the addition of excess water in the RAP source.
If hauling and stockpiling the RAP source is within your project scope, there are management procedures that can be put into place to reduce moisture as well. One effective stockpile management technique that can assist in controlling moisture within the RAP source is performing separate daily RAP stockpile locations. This stockpile technique is designed to separate daily RAP piles in an order that allows the oldest RAP stockpiles brought from extraction to be put through the asphalt plant first. This specific method allows the RAP source to dry for longer periods and with the additional surface area exposed to natural environments, individual stockpiles will dry more efficiently. Individual RAP stockpiles also allow for better management and an increased understanding of what the actual moisture of the RAP source is on the project.
Although this technique works well for drying and managing RAP sources, it does have some drawbacks that may include additional space in your asphalt plant yard and the possibility of requiring another payloader in the plant operations.
PAVE WITH CARE
With a good RAP source and properly managed moisture, the next step to produce consistency in the field is to concentrate on the paving and rolling operations. Setting up the paver and rollers for a RAP mix will vary from project to project depending on the scope and requirements of that specific project. There are a few techniques that seem to trend on RAP projects when setting up field operations.
Mixes containing RAP can naturally have a larger thermal gap than mixes of all virgin asphalt due to the way the material is introduced into the asphalt plant. With technologies such as paver mounted thermal profilers and thermal cameras, we can identify these areas on RAP mixes during paving operations. This thermal gap increase can cause the asphalt mat to cool down unevenly in specific areas which can potentially cause segregation or low density.
To manage this issue, field operations must keep consistent paver speeds and reduce paver stops. Finding a comfortable paver speed that allows the rolling operations to stay as close as possible to the paver will reduce these areas of potential low quality. Matching the plant production to the paver speed will increase quality, improve ride, and produce a more consistent density.
Rolling operations and patterns for RAP mix designs do not change that much from a virgin asphalt mixes. The biggest factors to remember are keeping consistent rolling patterns and allowing the rollers to be in a temperature zone that allows optimum density achievement. Technologies such as Intelligent Compaction assist roller operators tremendously with obtaining consistent patterns in designated temperature zones. Roller operators must continuously maintain patterns on the project to produce a consistent asphalt mat. If rolling operations happen to fall out of patterns or temperature zones, the margin for producing a high-quality asphalt mat will decrease. This rolling technique is especially important for consistency on a RAP project.
In conclusion, RAP is a great sustainable addition to many mix designs when constructing long lasting smooth roads. These asphalt mix designs may be more challenging to manage and place at times, but this does not imply the material is less durable or will not be as smooth when compared to conventional asphalt mixes. When working with RAP, paying attention to detail and precise operation management techniques will develop consistency in the field. Developing consistency in the field starts from the beginning and must be followed through to the end to be effective when paving with RAP.
Bryce Wuori is the owner of Wuori Consulting and the developer of PaveWise™ and Dynamic Density Design. He studied construction engineering at North Dakota State University and holds a Master of Project Management. For more information, contact him at bryce.w.wuori@gmail.com.