
16 minute read
Summer Production
Summer Production Products, Services
FFor the summer of 2020, the asphalt industry has remained active while socially distancing on the job site. For those producers busily bringing in materials, and then designing and making mixes for placement, original equipment manufacturers and service providers have continued to shape the steel and form the iron you need. If you’re looking for tools to enhance your bottom line during a time when every penny counts, here’s a group of OEMs with products to help.
ASTEC
The Voyager™ 140 portable, compact asphalt plant from Astec Inc., Chattanooga, is built around a Double Barrel® drum featuring Astec v-fights for densifying the veil of material across the dryer. Astec’s Mike Varner explained this allows the lowest practical stack temperature, which results in optimal heat transfer and reduced fuel use. The drum and baghouse of this portable plant are on the same load, giving the mix producer an agile system that produces 140 metric tonnes per hour, or 154 short tons at 3 percent moisture. It’s designed to allow up to 50 percent reclaimed asphalt pavement (RAP) content and to accept the new, compact Versa Jet™ burner as one of its burner options. While available before CONEXPO-CON/ AGG 2020, the Voyager 140 was rolled out during the show.
For more information, contact Astec at (423) 867-4210 or visit www. astecinc.com.
Web Extra: See a model of the new plant at https://youtu.be/
JY3_TpiqHTk.
CEDARAPIDS®
Designed around the high-performance JW55 jaw crusher, the Cedarapids® MJ55 modular jaw crusher from Cedarapids—a Terex brand—is designed for large quarries or contractors that want a stationary type design. The module combines the JW55 jaw crusher, sloped hopper, Cedarapids 52x20 feeder, and straight line conveyor on a galvanized steel structure. The standard structure can be transported in standard shipping containers plus a flat rack for the crusher and can be bolted together quickly on site with basic tools, according to the manufacturer. Three configurations offered
The Astec Voyager 140 portable asphalt plant offers a production capacity up to 140 tonnes/hour and RAP mixing capability of 50 percent.
The mobile MOBIREX MR 130 Zi EVO2 from Kleemann includes an impact crusher for both recycling and natural rock processing.
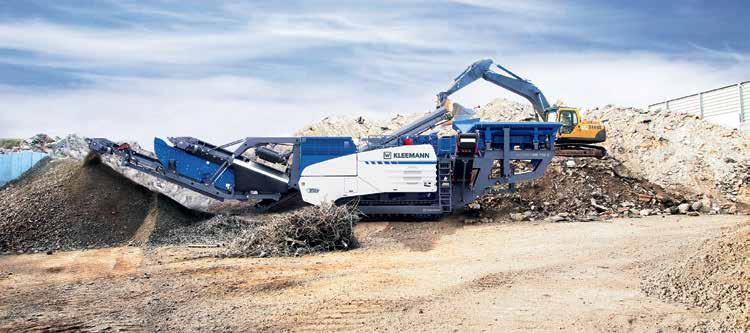
for the feed hopper allow for the optimum size to match up to the equipment being used to load the machine.
The structure includes oversize walkways, repositionable stairs and guard rails. Three plant emergency stops are placed convenient ly around the platform for easy access during operation. Optional mounting feet allow for the basic unit to be installed on compacted gravel base.
The MJ55 comes with hydraulic CCS jaw adjustment controls but can be optioned up with the addition of the CCM switchgear panel. Additional options include a cross plant magnet and off plant conveyor starter kit.
For more information, visit the TerexMPS website.
H&B
Haver & Boecker Niagara, H&B’s new mineral processing brand, introduced at CONEXPO-CON/AGG the PROcheck service program, which is dedicated to keeping customers’ operations running at peak performance. Each analysis comes with a thorough vibrating screen and screen media inspection report—known as a PROcheck—and focuses on recommendations for optimized screening. The program is complemented by Haver & Boecker Niagara’s pulse vibration analysis to help customers maximize productivity, proficiency and profits.
“By partnering with our customers through the PROcheck service program, we are monitoring the efficiency of their screening process to identify potential problems early on,” said Karen Thompson, president of Haver & Boecker Niagara’s North American and Australian operations. “The program can significantly extend service intervals, improve vibrating screen and periphery equipment performance and, most importantly, save our customers time and money.”
For more information, contact Kristen Randall at (905) 688-2644.
KLEEMANN
The MOBIREX MR 130 Zi EVO2 impact crusher from Kleemann GmbH, a company of the Wirtgen Group, was one of four innovations from Kl eemann on display during CONEXPO-CON/AGG 2020. It offers an output of up to 496 U.S. tons per hour. The mobile impact crushers of the EVO2 series are designed so they can be transported easily and made ready for operation in a short space of time. The direct diesel drive concept offers a high output while keeping consumption low. The sys tem widths of the impact crusher plant open in the direction of material flow. The plant is also operated using the SPECTIVE control concept.
As the other crusher options on display, the MR 130 Zi EVO2’s ideal support unit is the new MOBISCREEN MS 952i EVO classifying screen from Kleemann. The double-decker screen offers good transport di mensions and short setup times, according to the manufacturer. It has a screening surface of 5 foot 1 inch by 20 feet and boasts an output of up to 550 U.S. tons per hour. Either a wheel loader or upstream crushing plant loads into the generous feed hopper. Material is then transported on the extra wide feeding conveyor of 3 foot 11 inches to the screen casing.
For more information, contact Matt Graves at matt.graves@ wirtgen-group.com or visit www.wirtgen-group.com/america/en-us.
LIBRA
Libra Systems Inc., Harleysville, Pennsylvania, also offers the Automatic AC Tank Switching Module, available for the Plant Wise Drum Mix Control System. The enhanced module controls all fill, return and supply valves, as well as the AC pump and truck unloading. Tank levels are also monitored, includ ing critical limits. Dynamic, color-coded graphics provide at-aglance status pertaining to valve changes, material flow, tank levels, temperatures, interlocks and any alarm conditions that require the operator’s attention. Manual control of heaters, ag itators, etc. can be turned on and off through the software. The
The Automatic AC Tank Switching Module from Libra Systems is fully integrated with the PlantWise automatic blending process.
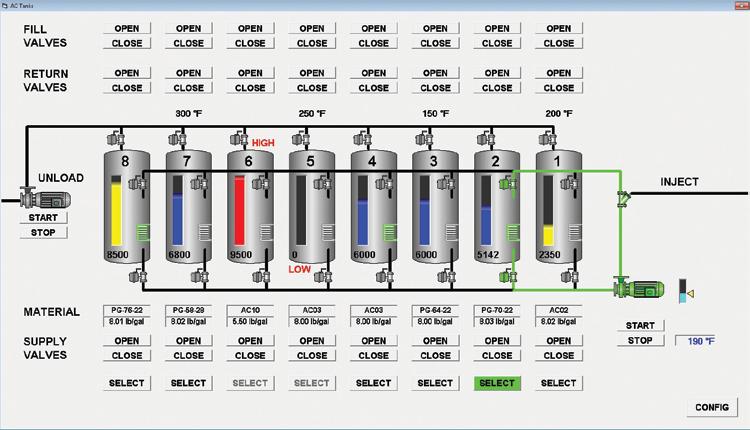

Automatic AC Tank Switching Module is fully integrated with the PlantWise automatic blending process, including material usage totals and the capability to control the entire plant with out manual buttons.
For more information, contact Libra at (215) 256-1700 or visit www. LibraSystems.com.
MAJOR
MAJOR, a Haver & Boecker company, Candiac, Quebec, displayed its FLEX-MAT Sensor at CONEXPO-CON/AGG 2020. The sensor, as demonstrated in the January Here’s How it Works feature, is a vibration data measurement tool that lets users review results and fine tune their screen machine without shutting down equipment. The app-controlled vibration analysis sensor enables users to measure and view vibration data.
The operator connects the sensor to the MAJOR app on their phone before placing the sensor on one corner of the machine. The user will continue to move the sensor to each corner of the machine until finished. Once the measurement process is completed, the information will be delivered to the phone in the time it takes to climb down from the machine.
Machine information is stored locally for ease of use and viewing in areas with cellular limitations. Once signal is available, the information uploads to MAJOR’s cloud service where it is viewable from a web browser. Historical equipment performance data is also viewable through the cloud.
The sensor measures g-force, stroke, rpm and orbit, including lateral movement. Producers can use the data to monitor and fine tune screen box performance as well as make parameter decisions with minimal guesswork.
The sensor kit arrives in professional casing and includes one sensor, instructions, a USB charging cable and instructions on how to download the MAJOR app. The app is available for iOS and Android phones.
For more information, contact your local MAJOR dealer.
MCCLOSKEY
McCloskey International, Peterborough, Ontario, displayed its newest products in the silver lot during CONEXPO-CON/AGG 2020, including the I44RV3HD from the re-designed impact crusher line. This plant combines a 45-inch impactor with a full screening and recirculat ing system. New features include an open chassis for ease-of-access, a larger double deck prescreen for fines removal, a swing-out radial re turn conveyor that can complete 90 degrees while the machine is running, and a direct drive crusher to boost power and lower fuel costs.
Afterward, this summer, McCloskey unveiled a new product line. The company expanded its mobile solutions with a new product range of shredders, which a spokesperson for the company said include the ability to shred roofing shingles. The new McCloskey VTS95 is the first product to make its debut for the new recycling division. The VTS95 tracked primary shredder is designed to effectively shred virtually any type of material from solid waste,
industrial and commercial waste, to bulk waste. It’s designed to meet the requirements for plants in which the incoming materials vary greatly in terms of size, composition and difficulty to shred.
The interaction between the rotating knives on the dual shafts runs asynchronously in both directions, ensuring the input material is constantly moving to prevent bridging.
The VTS95 track shredder features include: • 8-knife Samurai, heavy duty cutting table; • Multiple shredding programs; • Shredding in both directions with full torque; • CT C15 540-horsepower Stage V/Tier IV Final engine; • Anti-jam system; • Double hydrostatic drive transmission; and • Access ladder mounted at the front of the cutting table.
Fergal Mallon, McCloskey recycling product line manager, said: “We have a busy year of new product development ahead of us to compile a range of equipment in order to meet our customers’ needs. This first addition follows a stringent and strenuous development cycle, which has seen the shredder tested and prove itself in diverse product applications across the globe. We have teamed up with Metso Waste in Denmark, who are experts in static shredding applications, and have a range of tried and tested cutting table solutions, and we intend on using these cutting tables in our new equipment.”
For more information, contact Julie Andras at (705) 295-4925.
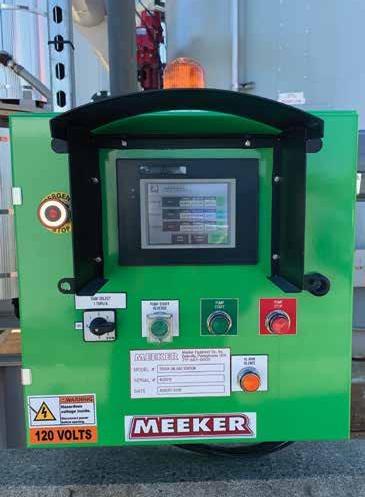
Connect With Us! Stay in touch with AsphaltPro between issues where you can find how-to content, trends and technology, and industry insight.
The Production Issue E.T. Simonds Shares Plant Moves PRODUCTION – PROFESSIONALS – PRODUCTS IR-Dry RAP asphalt PRO asph al t The Recycling Issue Experts Share Their Secrets For Equipment Staging Success PRODUCTION – PROFESSIONALS – PRODUCTS asphalt PRO Seal the Southeast
• How to Protect Feed Sensors • Overlay Ultimate Maintenance • Here’s Your Next Best Investment • How to Incorporate Asphalt in Freight
JANUARY 2017 WWW.THEASPHALTPRO.COM • How to Build an ADA Ramp • How to Rejuvenate Your Recycling • C.W. Matthews Crushes Pavement Maintenance
FEBRUARY 2017 WWW.THEASPHALTPRO.COM
facebook.com/ AsphaltPro
bit.ly/AsphaltPro LinkedIn
theasphaltpro.com
The Liquid Vision digital tank monitoring and valve control system from Meeker Equipment allows plant operators to give or take filling responsibility to or from truck drivers.
MEEKER
The Liquid Vision digital tank monitoring and valve control system from Meeker Equipment, Belleville, Pennsylvania, is designed to ensure safety and reliability when filling your tanks. Liquid Vision provides four distinct advantages to plants and plant operators: 1. It provides tank farm level (AC, fuel, etc.) to plant operators in the control room and out by the tank unloading station; 2. It provides automatic tank valve control to allow plant operators to choose a tank and valves will open/close automatically; 3. It has tank level detection so that it warns operators when tank levels are getting too high with multiple alarms; and 4. It has phone app application so managers and operators can see tank levels remotely from their phones.
The product can be purchased in building blocks so that you can add level monitoring at first, then valve control later. If you don’t want to have the unloading station control now, you can always add that later.
For more information, call (888) 333-0323 or visit https://www. meekerequipment.com/productDetails-44.
MIDWESTERN
Midwestern Industries Inc., Massillon, Ohio, introduces its new KLEAR-SCREEN series panels. The series design features spaced wire cloth urethane strips that essentially operate as live moving wires to create more through-put to dislodge materials. The re sulting “near size” particles should then not blind the screens. The non-blinding, wire cloth clean screen’s urethane strip de signs are spaced across the panels and the wire flexes. Made to fit most applications and rectangular vibrating machines, each series’ panel is available in openings ranging from 1/16 inch to 1 inch and in a variety of wire sizes.
For more information, contact (877) 474-9464.
PHCO
Lo-Density® drop-in tank heaters from Process Heating Company (PHCo), Seattle, Washington, are designed for 100 percent efficient heating of asphalt and emulsions in both underground tanks and distributor trucks. The drop-in heater is installed by simply dropping it through the tank’s manway and attaching it horizontally to the tank bottom. If needed, multiple heaters can be laid end-to-end using flexible, high-temperature power leads. Lo-Density, electric, drywell-style heat requires no permits or stacks.

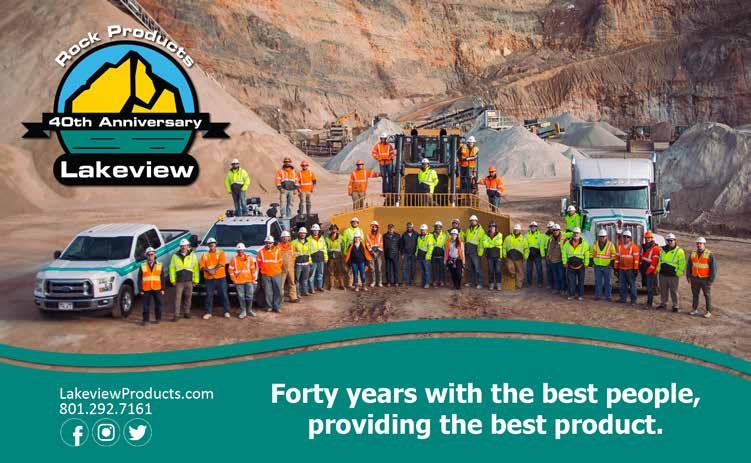
To see the Hotmix Parts/Stansteel Road Show, call on Stansteel to check availability of the team.
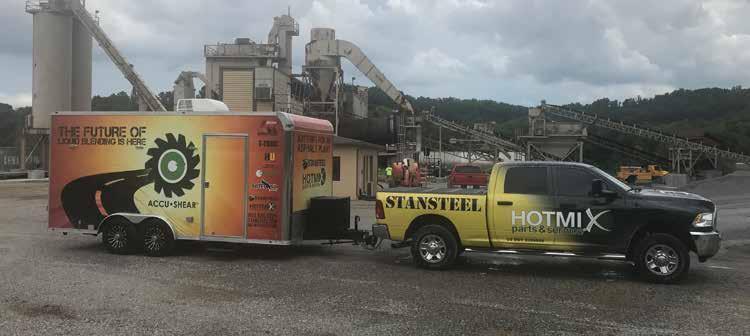
Lo-Density drop-in heaters are also appropriate for aboveground applications, including static installations up to 50,000 gallons, as well as distributor trucks. The heaters install the same way as in underground tanks. Above-ground tanks must have a minimum of 3 inches of fiberglass (or similar) insulation and weatherproofing.
Drop-in heaters from PHCo are available for tank capacities ranging from 1,000 gallons to 50,000 gallons, and are designed to maintain temperatures from 125 degrees F to 325 degrees F. The heaters’ recommended capacities include sufficient heat to maintain the temperature shown, plus a resere capacity for heat-up requirements. The drop-in tank heater kit includes a UL-listed control panel with digital thermostats for tank content temperature control. The complete kit includes heaters, controls, temperature sensors, wiring boxes and transition fittings for the tank top.
For more information, call (866) 682-1582 or visit www. processheating.com.
POWERSCREEN®
Powerscreen, a Terex Corporation brand, displayed its CT75R tracked radial conveyor along with other Powerscreen crushing and conveying solutions during CONEXPO-CON/AGG 2020. The radial conveyor offers a stockpiling solution for any crushing and screening operation. The mobility and flexibility of Powerscreen tracked radial conveyors are designed to reduce or eliminates the use of a wheel loader on site while reducing fuel, labor and maintenance costs.
Options on the CT75R include: overband magnet, dust suppression solutions and radio remote to start/stop the feeder and raise/ lower the discharge conveyor. The CT75R can be transported using a low loader or packed into a container for shipping.
For more information, contact your local distributor.
RM® GROUP
The RM GO! SMART service package from RUBBLE MASTER offers human-machine interaction. The infrastructure RM developed for this system promotes intelligent operation of the crushing machine and en ables remote processing and display of real-time trends and historical machine data. A GSM/UMTS connection is not essential, according to the manufacturer, because the data can be saved temporarily on the de vice. Any cellular device, like a smartphone or tablet, can be used to visualize and process the information. RM GO! SMART is an add-on to the RM GO! principle, which is known for its simplicity and intuitiveness.
RM crushers and screens have been a part of the American con struction and demolition machinery fleets for 20 years. With exports accounting for over 95 percent of business, RM is currently represent ed by 80 sales partners in around 110 countries with core markets of Central Europe and North America.
For more information, visit the RUBBLE MASTER website.
STANSTEEL
Given the travel and social distancing constraints due to Novel Coronavirus, you may need to have original equipment manufacturers bring products and demonstrations to you. The purpose of the Hot mix Parts/Stansteel Road Show is to do just that. Initiated in 2019, the Road Show helps inform and educate industry professionals of the products that Hotmix Parts and Stansteel have available to make run ning plants easier. The region the Road Show team travels to will determine the products displayed, or you can make a special request. For instance, would you like to see the Accu-shear™ model that is used for warm mix or liquid blending in batch plant applications or the model used in continuous mix applications?
The Road Show can easily carry the Precision Pin Pusher™ to show producers. It is designed to break press fit chain connections and push
pins out on 4-inch and 6-inch pitch chain, which means one tool for multiple chain sizes.
The Safe-T Station™ is another device that the Road Show carries. It can be used in multiple areas of the plant to sample asphalt cement (AC) in a safe, enclosed environment to prevent burn injuries. This de vice will fit up to 3-inch or 4-inch thermal jacketed asphalt lines. It allows operators to sample and test AC being off loaded from the truck to veri fy you are receiving the grade of AC that you ordered from the terminal. The Safe-T Station also enables you to ensure sure you have the correct foaming/grade coming through the Accu-shear liquid blending device.
One of the newer technologies being shown is the Tank Management Series that includes the Accu-level™ for checking the level of tanks or si los without having to leave the control house or climb equipment. The Tank Tracker™ gives you the ability to see levels and temperatures of tanks, from remote locations right over your cell phone.
The Tank Manager Total Inventory Management System™ is the to tal inventory management system storage solution for your plant. The Tank Manager gives you the control to run your business while it runs your tanks, and you can read more about that in “Granite Manages Mul tiple Tanks” in the May edition.
These are just a few of the items that are displayed in the Hotmix Parts/Stansteel Road Show that the team would be happy to come by and discuss with you at your asphalt plant.
For more information, call (800) 826-0223 or visit www.stansteel.com.
SUPERIOR BOILER
Superior Boiler, headquartered in Hutchinson, Kansas, offers the Mohawk model. Superior representative Mike Moore of MG Sales in Indiana has found the Mohawk to be an excellent candidate for asphalt processing. Available in pressures from 15-350 psi steam and 30-160 psi hot water with sizes from 30- 1,000 BoHP, Superior can tailor this model to meet specific re quirements for every terminal application.
The Mohawk’s 3-Pass dryback design offers increased effi ciency as hot combustion flue gas is turned to make additional “passes” through the boiler before being vented. This allows for maximized heat transfer, resulting in energy and cost savings. Superior Boiler exceeds industry requirements for tubesheet thickness, according to the manufacturer, protecting against warping that can occur from extreme environments. Vice Pres ident Nick LeJeune stated, “Customers appreciate that their boilers are made in the USA, from 100 percent American steel. They have a lot riding on this equipment.”
Superior’s boilers are also burner and control “neutral” so that burner (and fuel) of choice can be paired with the boiler, and there is no need for proprietary replacement parts.
For more information, contact your local Superior Boiler dealer.
– BY ASPHALTPRO STAFF
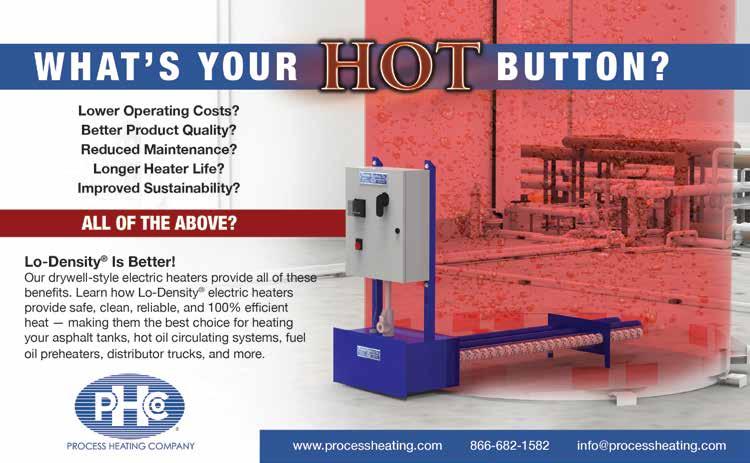