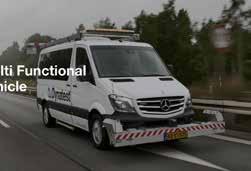
33 minute read
Dynatest’s PCI Calculation Tool
Step 1
The user takes a pavement survey with an MFV, RSP, and LCMS. Step 2
DDC software collects the survey data from the survey and exports it into the DE pavement analysis program.
Step 3 Dynatest Explorer evaluates the functional pavement condition, giving the user access to all information, including PCI values.
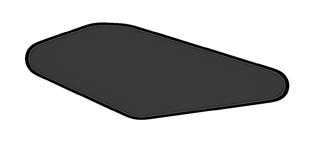
Step 4
The system can display PCI values or export them to a spreadsheet or Google Earth map.
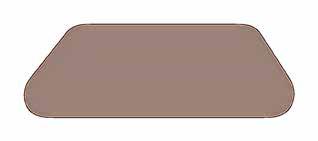
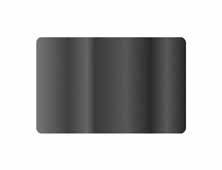
TThe U.S. Army Corps of Engineers Research Lab developed in 1976 an empirical metric for rating a pavement’s condition taking all types and severities of distresses into consideration. The international standard ASTM D643320 (and ASTM D-5340-20 for airports) uses the resulting pavement condition index (PCI) to determine the current condition of a pavement network, but the calculations of the PCI value can be time consuming and difficult to perform.
To do all the PCI calculations based on ASTM D6433-20 and with the functional pavement condition data within the sample unit that a user defines, Dynatest A/S, headquartered in Denmark, has launched its automated PCI calculation function as a licensed module within the Dynatest pavement analysis program, Dynatest Explorer (DE). Here’s how it works:
Because the PCI calculation tool is a module of DE, the user first takes readings of the pavement in question with the Dynatest Multi Functional Vehicle (MFV) equipped with the Road Surface Profiler (RSP) system and Laser Crack Measuring System (LCMS®), which collect pavement data.
Dynatest Data Collection (DDC) software stores and controls the data from the MFV’s survey. The data is displayed while testing or stored for export into the DE program.
The DE program analyzes the data, evaluating the functional pavement condition. DE then gives the user access to all the data, images and distresses acquired during the survey, allowing for visualization, verification, calculation and reviewing of results, which now include the PCI values.
The system can display the PCI values on a table or a graph, export them to Excel, or show them on a map exported to Google Earth.
For more information, contact Dynatest through Oline Westerdahl at owl@dynatest.com.
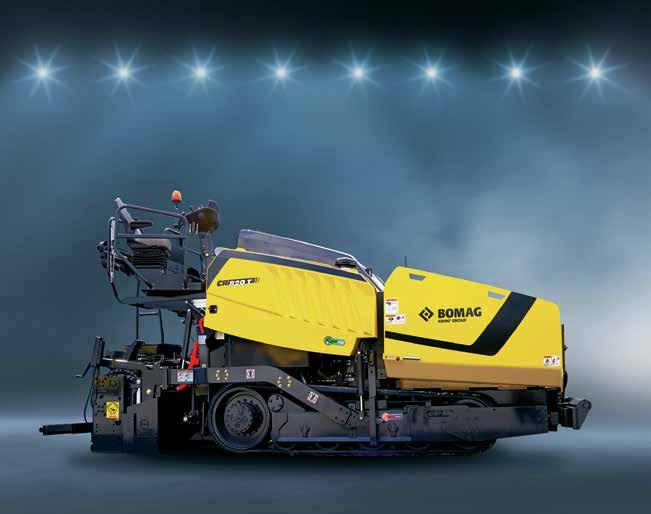
Don’t Let Shortages Get You Down
BY ASPHALTPRO STAFF
As discussed in the January 2022 article “Alternatives Exist to Source Parts,” some producers and contractors in North America may have found themselves in a pickle when it came to winter equipment repair if they hadn’t planned months in advance. For the 2022 season, the possibility of postponing repairs, upgrades, and maintenance until parts and components could be made available had become reality. Luckily, as the article detailed, there are ways around bottlenecks and blockages.
The team at Albarrie, a vertically integrated filter bag supplier in North America, detailed another option for asphalt producers and baghouse manufacturers who are enduring a global Nomex/meta-aramid fiber shortage. Their staff writer explained two of the global issues factoring into the supply shortage that’s affecting the availability of high-heat fabrics for particulate dust filtration.
“Factories belonging to two of the four major suppliers in Zheng Zhou, China, have been part of the city-wide lockdown since 2021,” they wrote. “The city-wide lockdown...[added] to the strain on supply in September/October 2021. The shutdowns are responsible for the raw material shortage of polymers and finishing agents for coating fibers.”
The Albarrie team also cited the Dow and Dupont merger and subsequent expansion of America’s 5G wireless network as contributing to the shortage of fibers. “Dow and Dupont; one of the largest manufacturers of plastics, and finishing agents are unable to meet their usual demand for raw materials needed to manufacture fibers,” they wrote.
An alternative solution for 2022, according to Richard Watson, a purchasing manager at Albarrie Canada, is to replace your meta-aramid filter bags with “Polyphenylene Sulfide (PPS) or Polyimide (P84) fabrics, depending on the plant’s environmental conditions and materials processing.”
Albarrie also offers a cleaning service designed to prolong existing baghouse filter bag life while the bags remain in place. The company offers virtual consultations. For more information, visit the Albarrie website.
Not all aramid fiber types have been affected by the shortages discussed above. Mike Scardina of Surface Tech explained the aramid fibers required for the company’s ACE XP Polymer Fiber® and other asphalt mix-strengthening aramids are a different grade than the one in short supply. “From a raw materials standpoint, we’re in very good shape,” he said. “We don’t expect any problems in 2022.”
Industry professionals seeking alternatives for binder modification in areas where polymers have become difficult to attain are seeing fibers—for binder modification—as an alternative. “We are a viable tool as we address supply for the asphalt industry,” Scardina said. For more information, visit surface-tech.com/ asphalt-ace-xp.
While discussions of alternatives to what a producer or mix designer is accustomed may not be comfortable, it’s good to know suppliers are thinking ahead to provide options and solutions to help producers and contractors through supply chain issues. For this month’s product gallery, take a look at some products and services lined up to help you with your day-to-day goals.
ASPHALT UNLIMITED
Liquid Asphalt must compete with other products that are refined from crude oil and energy prices are currently soaring due to inflation. Imagine bidding today’s cash price plus the cost of the hedge instead of guessing at some future price. A new app that forecasts future liquid asphalt prices is designed to assist with that. Created by Brian Lawrence, president of Asphalt Unlimited LLC, Kennesaw, Georgia, a 30+ industry expert, the app is designed to help asphalt producers and highway contractors bid future work.
The app is based on Asphalt Unlimited’s proprietary algorithm that pulls the daily closing prices of a variety of energy products from the NYMEX and provides an asphalt projection that mirrors the coker values of asphalt. It has been back-tested against 13 years of published coker values and it produced a correlation (r-value) of 0.988041. Almost a perfect, positive correlation. This gives the projection an actual basis in reality because it is based on today’s closing futures prices.
“The algorithm never predicted a value below the published value,” stated Lawrence, creator of the algorithm. “To me, that fact along with the high degree of correlation (0.988041), provides a lot of confidence when either producing a financial outcome or predicting a future price, whether up or down. I think in the near future, coker values will probably provide the floor for wholesale asphalt pricing anyway.”
The values produced by the app are a retail (rack) projection and are also tailored to specific geographic areas in the 48 contiguous United States. The prices are given in ranges and are suggestive of what is a reasonable value to possibly include in a bid. The app is subscription based and all annual subscribers receive private asphalt pricing consultation with Lawrence, if desired.
For more information, contact Sherry Butler at (602) 703-3659.
CITY-WIDE LOCKDOWNS IN CHINA ARE RESPONSIBLE FOR THE RAW MATERIAL SHORTAGE OF POLYMERS AND FINISHING AGENTS FOR COATING FIBERS.
ASTEC
During the World of Asphalt 2022 tradeshow, Astec displayed a host of new or updated equipment, including a model of its new Astec SESS, which is a self-erect storage silo, designed to work hand in hand with portable plants. The silo is certified by the National Institute of Standards and Technology’s National Type Evaluation Program (NTEP) and designed for easier ticketing and loadout. Check with Astec for available tonnages.
For more information, visit astecindustries.com.
BLUE SMOKE CONTROL
Blue Smoke Control, a division of Butler-Justice Inc., Anaheim, California, has introduced the X-VOCS™ system for eradicating odor-causing emissions that can be produced as a byproduct during hot-mix asphalt (HMA) production. The X-VOCS system features proprietary carbon absorption technology designed to filter and remove up to 99% of odors and VOCs, such as Hydrogen Sulfide (H2S), from tanks. X-VOCS incorporates a five-stage filtration system. In the first three stages, a series of filters remove more than 95% of targeted particulates down to 0.3 microns. In the final two stages, carbon filtration beds remove remaining odors and volatiles. While designed for new plants, the X-VOCS system can also be retrofittable into existing operations, with minimal modifications to the plant.
When the X-VOCS technology is coupled with the company’s Blue Smoke Control system, emissions from HMA plants can be
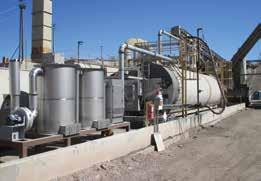
The patent-pending technology of X-VOCS combines with the Blue Smoke Control system to reduce both odor and blue smoke.
reduced to nearly zero, providing owners with the means to achieve the highest level of environmental stewardship. Implementation of this technology has been proven to virtually end calls from nearby neighbors regarding odor and visual emissions. Similar to X-VOCS, the Blue Smoke Control system is retrofittable with few plant modifications.
For more information, contact Butler-Justice at (714) 696-7599 or mikeb@butlerjustice.com.
Rejuvenate Reclaimed Asphalt with ReLIXER® Rejuvenator
An Elixir of Bio-Based Oils
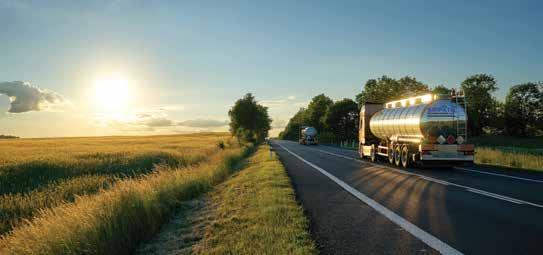
Tested.
Proven.
Trusted by users woldwide.
ReLIXER® • PGXpand® • NuMIXER®• ReNUBIT® • SriCote®
1-800-562-6276 1-201-721-7562
Learn More At Sripath.com/pro
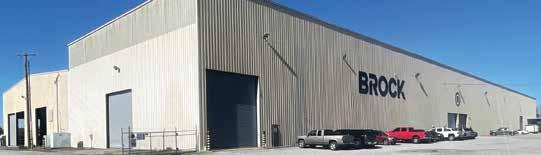
The Brock Chattanooga location has 108,000 square feet under roof on 23 acres of land and now allows a second shift for manufacturing operations.
BROCK
BROCK, a manufacturer and supplier of equipment, parts and onsite services to the hot-mix asphalt (HMA) plant industry, is pleased to announce the addition of a second shift team to its manufacturing operations in Chattanooga. The second shift team started operating Monday, March 21, 2022.
Commenting on the announcement Ben Brock, president and CEO, said, “We couldn’t be happier with the people we have added for our new second shift. While the shift is new to our company, the new team itself averages nearly nine years’ experience per person in building hot-mix asphalt equipment. As a result, we have great confidence in our ability to have the quality we want and need in our new shift team. We thank our customers for putting us in the position to add the second shift team at our Chattanooga facility.”
For more information, visit www.brock.llc
CLARENCE RICHARD
Clarence Richard Co., Minnetonka, Minnesota, offers the Ez-Flo continuous weigh feeder bin. The manufacturer states you “set it and forget it.” Step 1. Pull up, position the load cells on the solid ground and jack the wheels up off the ground. Step 2. Batch or blend your material most accurately at rates as low as pounds per minute (lbs/min) or as high as tons per hour (TPH).
The bins can discharge into a feeder belt or auger or vane feeder. Ez-Weigh Loss finds its setpoint from the blending control tach signal. No hardware software changes to your existing control system are required.
For more information, visit https://ezfloweighing.com/.
COLAS USA
Colas USA, Morristown, New Jersey, a leader in road construction, materials, and innovation appointed John Harrington as president and chief executive officer, assuming responsibilities as of March 1, 2022. Harrington succeeds Thierry Le Roch’. Harrington began his career at Colas USA in 2015 as executive vice president of Western Operations, overseeing the subsidiaries of Colaska Inc., Simon Contractors and Sully-Miller Contracting Co. His strong experience, not only in the construction and engineering fields, but in leadership operations, has helped grow this area of the U.S. business for Colas.
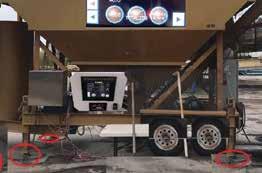
The EZ-Flo continuous weigh feeder bin is designed so the Ez-Weigh Loss finds its setpoint from the blending control tach signal with no hardware or software changes needed from your existing control system.
CONTROLS
CONTROLS Inc., Tucker, Georgia, has released its AUTOTRIAXQube, which is an all-in-one, automatic, triaxial testing system for the lab at your production facility. It is designed to make triaxial testing easier on lab personnel while fitting neatly in any lab and complimenting existing testing capabilities. The manufacturer states all existing accessories already in use with the 70-mm banded triaxial cell (28-WF4070) are compatible with the AUTOTRIAXQube. The manufacturer states there’s no need for external panels, tank or hydraulic connection; connect the AUTOTRIAXQube to water and power supply and start testing. The built-in vacuum pump, tank, control valves and cavitation system are designed to de-air the water quickly and efficiently down to levels of dissolved air acceptable for triaxial test methods.
A secure triaxial cell lifting system incorporates a new lifting mechanism that allows the operator to raise the cell to its highest position and rotate it through 90 degrees, until it’s safely held in place with a magnetic latch. A built-in hydraulic system speeds up the time required to set up the system correctly (water circuit saturation, pressure system and triaxial cell), thus avoiding possible damage to a sample already positioned in the triaxial cell.
For more information, visit the CONTROLS group website.
CWMF
CWMF Corp., Waite Park, Minnesota, is pleased to announce its recent acquisition of Eagle Electric Service of St. Cloud, a UL listed panel build company and full-service provider of HMA plant equipment controls, automation, installation, service, and maintenance.
Management stated: “Our corporate mission has been to go the extra mile to provide exceptional asphalt equipment solutions and service. The acquisition of Eagle Electric Service brings us closer to accomplishing this goal. For the past 10 years, CWMF and Eagle Electric Service have been industry partners, working toward turnkey solutions for our customers. These solutions will now be offered under one company, making that commitment even stronger.”
For more information, visit https://cwmfcorp.com/
ERIEZ
Eriez, Erie, Pennsylvania, has invested millions into spare parts inventory within its recently expanded service and repair center, according to John Klinge, Eriez director of strategic sales-aftermarket. Klinge explained that Eriez stocks parts that integrate with Eriez equipment as well as competitors’ products.
He said, “We maintain a balance of stock components—such as motors, reducers, bearings and plastic chain belts—which are applicable to most standard equipment, as well as custom parts for Eriez state-of-art products specially designed to meet a customer’s specific application requirements.”
While Eriez can ship parts quickly, sometimes next-day, the company’s service team encourages customers to be proactive to ensure they maintain optimum productivity. “We always suggest that customers keep a supply of wear parts and highly customized components on-hand,” said Klinge.
The Eriez Service and Repair Center is located at the company’s Wager Road plant near its corporate headquarters in Erie. In addition to spare parts, Eriez’ Service and Repair Center offers a 24/7 service hotline, on-site field service equipment remanufacturing and full “as new” warranties.
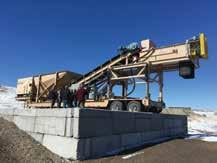
HAVER & BOECKER
Haver & Boecker Niagara, St. Catharines, Ontario, named Jon Cheladyn the certified sales manager for Northeastern United States. He brings more than 13 years of industry experience with Haver & Boecker Niagara to his role. In his new position, Cheladyn will serve producers in Ohio, Pennsylvania, New York, Michigan, New Jersey, Maryland and Delaware.
KENCO
Kenco Engineering Inc., Roseville, California, offers the UniMix System to provide long wear life and quick installation of Uni-Mix parts for your pugmill operations. The recessed bolt heads minimize wear on mounting hardware, and notched shanks allow tips to fit either left or right-hand throw positions, which means no separate inventories for left and right hands. The streamlined shank design reduces drag and wear; tips are held in place by a single roll pin with no bolt heads.
The shanks are made of high-strength, heat-treated alloy steel for maximum durability. Tips are made of Kenco Alloy-K
PUGMILL SYSTEMS
We’ve been designing and manufacturing custom mixing solutions in Tennessee for nearly 40 years.
RCC • CTB • Pugmix • Stabilized Sand
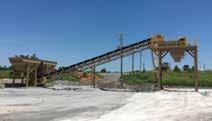
Coldmix • Fly Ash • Salt Treatment
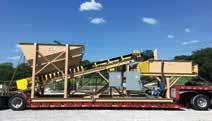
Rental Plants Available
Check out additional projects at: PUGMILLSYSTEMS.COM or give us a call at: 931-388-0626
Uni-Mix shanks from Kenco Engineering are mounted with bolts rotated 90 degrees from OEM designs. Uni-Shrouds, which cover the front of the shank, reduce wear in the highest abrasion zone.
for maximum wear life. The manufacturer explained: “The UniMix shank, shroud and tip are specially contoured to slice through the asphalt, aiding the mixing operation while minimizing wear. The tip is free of bolt holes, which can initiate wear and disturb material flow. The streamlined design reduces drag and the amperage required for efficient mixing.”
For more information, contact Kenco at (800) 363-9859 or visit www.kencoengineering.com.
MCCLOSKEY
McCloskey International, Keene, Ontario, launched in February its 365SiteConnex connectivity solution for monitoring of McCloskey products. Monitoring a fleet is key to reducing downtime and maintaining efficiency and profitability. With 365SiteConnex, key information for machines can be obtained in just a few clicks, allowing users to review faults or status issues from a single notification feed, monitor fuel use across all machines, and monitor service schedules and requirements.
Additionally, with GeoData, a machine’s current and previous locations can be tracked, from maneuvers on a work site to being transported halfway across a continent. Geofences can be programmed to be notified if a machine goes outside its designated area. 365SiteConnex will be available in the first quarter of 2022 through McCloskey dealerships as a subscribed service. The software will offer remote software updates to deliver the latest program upgrades, as well as remote support from the 365SiteConnex service team.
For more information, contact your local McCloskey dealer.
MDS
MDS is undergoing changes following the acquisition by Terex in 2021. Along with significant investment in its facilities and expanding its distribution footprint, the company has added to its team to help deliver aggressive production growth goals to meet ever growing demand for its products.
With the positive changes to MDS ongoing, the company launched its rebranding with new livery offering a consistent look across all its models. As part of this rebrand, the company launched a new website and changed all its social handles to @mds.terex across all social media channels.
For more information, visit the terex.com/mds website.
MESA
Mesa Systems Co., town, state, introduced its HD2-Kit to provide aggregates suppliers and plant managers with a stockpile moisture measurement system. To measure the moisture content of construction aggregates—including sand, gravel and crushed stone up to 1.25 inches—the user inserts the SONO-M1 probe into the pile. The HD2 meter then reads and displays the level of moisture within two seconds, according to the manufacturer.
For more information, visit the Mesa Systems website.
MINDS
Astec Industries, Chattanooga, announced March 23 and finalized April 1, the acquisition of MINDS Automation Group Inc. (MINDS), headquartered in British Columbia, Canada, with locations in the United States, United Kingdom, France and Belgium. The company develops customizable plant automation control systems for drum, batch, combo/hybrid hot-mix plants, emulsion plants, liquid terminals, silo load-out, ticketing and data management for the asphalt industry.
MINDS Inc. CEO Pierre Vidaillac and the leadership team will stay with Astec to support the advancement of its automation and controls technology and the overall Rock to Road™ digital platform. A spokesperson for Astec stated current MINDS customers will continue to communicate through any established channels without change as there is no plan to change the communication structure at press time.
ROTOCHOPPER
Rotochopper equipment owners and operators gathered at Rotochopper’s manufacturing facility in St. Martin, Minnesota, for training the third week of February. The customer service department hosts Rotochopper University annually for companies that have purchased Rotochopper equipment during the past year. The two-day class includes a manufacturing facility tour, equipment operation best practice training, a hands-on demonstration and networking opportunities allowing machine owners to learn from each other as well. This year the education focused on how to properly feed your grinder, how to perform preventive maintenance and how to troubleshoot. The hands-on demonstrations showed attendees how to install the main rotor bearings and how to adjust the sheave and tension the drive belt on a Rotochopper grinder. Rotochopper was able to host over 20 students during the two-day event from various companies across the United States.
RUBBLE MASTER
Rubble Master, Ennis, Texas, has launched the RM XSMART telemetry and fleet management app to help contractors get more clarity
about their operation, to identify blind spots and improve processes. It also assists operators with more information about the condition of their machines to become more proactive and accelerate service processes. RM XSMART is available as an app on your phone or your desktop computer to access machine data anywhere, at any time. Operators can monitor fuel levels, reset belt scales, and track their tonnages with an optional belt scale conveniently from their cab.
For more information, visit the Rubble Master website.
SURFACE TECH
Surface Tech has completed the verification process to achieve an environmental product declaration (EPD) for ACE XP Polymer Fiber®, its advanced aramid polymer fiber additive.
An EPD is a transparent, objective report that details what a product is made of and how it impacts the environment across its entire lifecycle. The EPD is an independently verified and registered document that can help construction projects earn credits for green building rating systems. EPDs satisfy the requirements of product category rules (PCR) and follow international standards, including ISO 14044, ISO 14025, and ISO 21930.
EPD-listed products are gaining in importance as producers seek new ways to validate the assertions made by companies about the environmentally beneficial qualities of their products. Architects and designers also increasingly specify products with transparent lifecycle-assessment-based environmental impact reports.

The ACE XP Polymer Fiber® from Surface Tech has completed the third-party verification process to achieve its EPD.
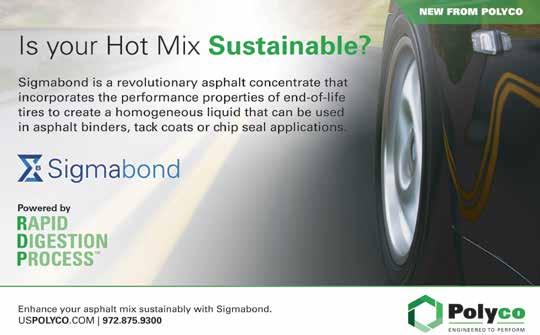
“We are pleased to be EPD-certifying our flagship product/technology and joining the ranks of other proven, sustainable solutions,” said Steve Santa Cruz, president of Surface Tech.
ACE XP uses the tensile strength of aramid to address the performance distresses of cracking and rutting. It disperses over 19 million para-aramid fibers throughout each ton of mix, providing a three-dimensional reinforcement that increases the asphalt’s resistance to reflective cracking, rutting and fatigue. ACE XP is designed to make asphalt pavement stronger and last longer, thus increasing the pavement’s life expectancy, reducing maintenance costs, and providing enhanced sustainability to asphalt pavements. ACE XP can be added to any mix design with no needed changes at both batch and drum plants, according to the manufacturer.
For more information, visit surface-tech.com/asphalt-ace-xp.
TARMAC
Tarmac International Inc., Lee’s Summit, Missouri, launched its new 30NOx burner with PLC controller at WOA 2022. The burner features two fuel valves—a primary in the back and a secondary in the center. “We pre-mix the fuel and air early,” President Ron Heap said. The burner uses early mixing of fuel and air along with internal gas recirculation to reduce NOx from over 100 PPM down to 30 PPM. This 30 PPM NOx is a level that Tarmac’s customers are experiencing in the USA.
The new burner controller allows for improved fuel and air valve positioning (parallel positioning) with both manual and auto control. An Allen Bradley PLC with 10-inch touch screen controls the burner and interlocks. Manual operators are seen for backup control should the PLC fail. There is a “dashboard” where management can see burner production, fuel per ton, position of the fuel and air valves, position of the ID fan, negative pressure of the burner faceplate. Over-the-phone service is available with the technician seeing the parameters of the burner controller.
For more information, contact any member of the Tarmac team at (816) 220-0700 or info@tarmacinc.com.
ZONAR
Zonar, Seattle, announced the availability of Zonar SightIQ™, which is a real-time analytics solution for construction aggregate operations. The asset productivity and health solution is designed to increase the efficiency and cycle times in pits and quarries by delivering a real-time, consolidated view of—and insights into—an operation’s equipment, machines and vehicles regardless of make, model, year, manufacturer or asset location.
With SightIQ, construction aggregate site operators could eliminate the need to manually collect and analyze data from disparate sources and production impact studies. In return, operators can focus on unearthing enhanced profits by leveraging SightIQ insights to avoid breakdowns and fine-tune site processes. For example, SightIQ-driven insights can identify unnecessary idle time, inefficient use of fuel, or non-optimal timing of maintenance across assets. Even a 58-second longer cycle time can cost quarry fleets over $180,000 in lost productivity per day. Additionally, SightIQ meets the Association of Equipment Manufacturers (AEMP) 2.0 telematics standard, pulling asset data from all major yellow-iron OEMs into a singular, unified view accessible through Zonar Ground Traffic Control®.
For more information, visit the Zonar Systems website.
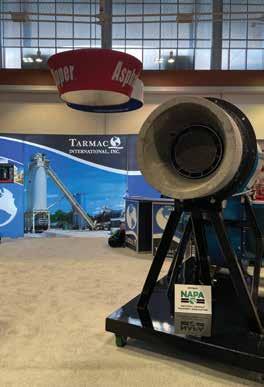
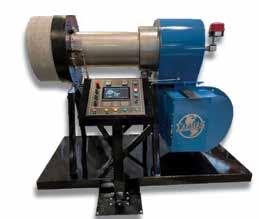
The new 30-NOx burner from Tarmac features two fuel valves and tight PLC control.
SNAPSHOTS FROM WORLD OF ASPHALT/AGG 1 2022
World of Asphalt/Agg1 2022 brought together a record-breaking 11,400 asphalt paving and aggregates professionals to its 20th anniversary event. More than 440 companies filled a sold-out Music City Center exhibition floor in Nashville from March 29-31, 2022. Here are a few highlights!
Photo courtesy of AEM
B2W’s ONE Platform, Many Applications
The ONE Platform from B2W Software, Portsmouth, New Hampshire, aims to enable contractors to win more bids and operate more profitably.
BY ASPHALTPRO STAFF
B2W Software’s ONE Platform connects the office, field and shop through a single operational database and its suite of applications for managing estimating, scheduling and dispatching, field tracking, equipment maintenance, e-forms and business insight workflows.
B2W Software’s ONE Platform contains five applications: • B2W Estimate allows contractors to bid with centralized resource databases, templates and cost structures that can be used simultaneously by multiple estimators. • B2W Schedule is a single online system for resource scheduling and dispatching that is also unified with job site and equipment maintenance workflows. • B2W Track is a field tracking solution that enables contractors to record labor, productivity and equipment utilization via electronic field logs and analyze actual versus planned performance on a daily basis. • B2W Maintain can be used to drive automated preventive maintenance, generate and process work orders, track warranties, manage parts and inventory, manage mechanic timecards/payroll, and consolidate historical data and equipment reporting. • B2W Inform can be used to create electronic forms, enabling employees to access and fill out forms on any device, submit them immediately and generate reports.
HOW IT WORKS
The ONE Platform’s latest update, announced in the fall of 2021, introduced new capabilities that enable contractors to identify equipment defects and make repairs quickly. It can now generate repair requests automatically based on data from electronic forms used for completing equipment inspections. The new process relays detailed information from equipment inspections to the maintenance team immediately.
B2W Marketing Communications Director Greg Norris reminded us, in years past, companies would note equipment in need of maintenance on paper forms.
“Because it was on paper, there was usually some lag time between when the problem arises and when it can be resolved,” Norris said. “With electronic forms, you can connect
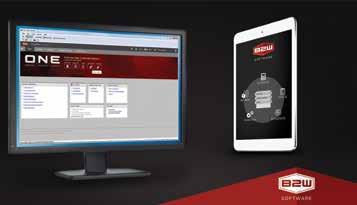
The ONE Platform can be accessed via the Cloud or deployed on-premise with a user’s own servers.
“BECAUSE YOU AREN’T WAITING ON THAT PAPER PROCESS, YOU CAN SCHEDULE MAINTENANCE QUICKER, WHICH TRANSLATES TO LOWER MAINTENANCE COST, MORE UPTIME, BETTER MAINTENANCE SCHEDULING, AND THE ABILITY TO FIX PROBLEMS BEFORE THEY BECOME A BIGGER ISSUE.”—GREG NORRIS
the inspection in the field with mechanics in the shop in real time. Because you aren’t waiting on that paper process, you can schedule maintenance quicker.”
The API connection for automating the creation and logging of repair requests relies on the ONE Platform’s B2W Inform and B2W Maintain applications. B2W Inform is designed to enable contractors to customize and manage electronic forms for any requirement, including equipment inspections. Form fields can be mapped to the format of equipment repair requests, which are managed in the B2W Maintain application. This connection allows inspection forms to trigger repair requests automatically in the maintenance software and for information from forms—including descriptions and photos— to flow directly to the requests.
“Asphalt paving is an equipment-intensive operation where it’s not uncommon for contractors to spend 10% of their revenue maintaining their fleet,” Norris said. “Using equipment maintenance software to shift to a preventive maintenance approach can cut that down to 5%.”
GW-EX Inc., an excavating company based in Ontario, Canada, is among the initial companies benefiting from this new workflow. The company has close to 100 pieces of equipment and generates more than 100 requests monthly for emergency and preventive maintenance. Jon Ewart, owner of GW-EX, said they faced efficiency, accountability and visibility challenges when repair requests were generated based on phone calls, text messages or paper forms submitted to the shop supervisor. Drivers or operators frequently claimed to have reported defects, while mechanics claimed they did not receive the information.
“Now, there is a record and history of the request being submitted and also investigated by our mechanics,” Ewart said. “We have also been able to prioritize work more effectively, so issues impacting safety and production take priority over less significant, cosmetic requests.”
UPDATE & INTEGRATE
Norris said what sets the ONE Platform apart from other software approaches is the integration of its various applications under one platform. “The key concept behind our platform approach is the integration between different workflows,” Norris said. “All the elements are designed to work together, versus bits and pieces from different companies being bolted together.” Examples of other integrations include automatically pushing data from B2W Estimate into B2W Track, “so the crew can build the project like it was bid without discrepancies between the way the estimator assumed it would be done and the way the supervisor does it,” Norris said.
Another is electronic communication from B2W Track automatically going into B2W Maintain, allowing foremen in the field who notice defects outside of the inspection process to automatically make a repair request from the field. Or, integration between B2W Schedule and B2W Maintain so the maintenance crew can schedule repairs for periods when machinery is not in use, and the dispatcher is aware of when machinery will be out for repair.
The next big addition to the ONE Platform is the launch of a new application, the B2W Employee App, which offers individual time and performance tracking. “We have B2W Track, which is geared more toward tracking crews,” Norris said. “But, our customers often find it challenging to track the hours of individual employees working independently, like a grader operator or a truck driver. That’s why we decided to develop an app that individual employees can use to log their hours and performance that integrates with the company’s field logs.”
GREAT PEOPLE. GREAT WORK.
Specially formulated temporary and semi-permanent release agents and coatings, drag slat cleaners, and extraction solvents. Designed to work on all asphalt mix designs, including on all PG grade asphalt mix designs such as PG-76-22 and 70-22.
Our asphalt release agents are state DOT-approved and NTPEP tested and listed.
All our proprietary asphalt products and equipment are proudly formulated and manufactured in the United States.

"Since making the switch to Meyer Laboratory’s asphalt release agents and drag slat cleaners at all the All States Materials Group plants throughout New England more than 2 plus years ago, we are extremely pleased with the performance of the products and customer service provided. I have also received positive feedback from our paving superintendent that Meyer’s products have performed much better than our previous products used on the tools, transfer machines, rubber tire rollers and pavers in the field. Thank you again for everything - Todd Jarvis, Plant Operations Manager - Trew Stone, LLC a division of All States Material Group
We custom build our dispensing systems to meet each customers unique needs.
Meyer is a full-service supplier with more than 75 service reps and numerous warehouses located across the United States. We can serve any customer, anywhere and anytime.
Arrange for an appointment today:
sales@meyerlab.com
800-580-7677
www.meyerlab.com
Discover our SERVICES Scan the
We are family owned and operated for over 40 years. Our focus is meeting the needs of our customers. Our service reps are always available for installation, repairs, and product delivery. In short, we provide service where and when you need it - every time.
QR
CODE
800 Pavement Network. . . . . . . . 9 ALmix . . . . . . . . . . . . . . . . . . 7 Asphalt Drum Mixers, Inc . . . . 30, 31 Astec Industries Inside Front Cover, Inside Back Cover, 11 B&S Light . . . . . . . . . . . . . . . .13 Blaw-Knox . . . . . . . . . . . . . . . 9 Bomag. . . . . . . . . . . . . . . . . 59 BROCK . . . . . . . . . . . . . . . . . .71 Cargill . . . . . . . . . . . . . . . .27, 47 CWMF . . . . . . . . . . . . . . . . 3, 44 Dynapac. . . . . . . . . . . . . . . . .51 Fast Measure . . . . . . . . . . . . . 73 Forta . . . . . . . . . . . . . . . . . . .57 Gencor Industries, Inc. . . . . . . . . 4 Greenpatch. . . . . . . . . . . . 23, 53 KM International . . . . . . . . . . . 49 Meeker . . . . . . . . . . . . . . . . .17 Meyer Lab. . . . . . . . . . . . . . . 70 Minds, Inc. . . . . . . . . . . . . . . 25 NCCP. . . . . . . . . . . . . . . . . . 72 Olson-Homestead Valve . . . . . . 39 Polyco . . . . . . . . . . . . . . . . 65 Pugmill Systems . . . . . . . . . . . 63 Quik Pave Products . . . . . . . . . 54 Reliable Asphalt Products . . . . . . . . . . Back Cover Sripath . . . . . . . . . . . . . . . . .61 Stansteel . . . . . . . . . . . . . .13, 41 Systems Equipment . . . . . . . . . .12 Tarmac Inc. . . . . . . . . . . . . . . .21 Top Quality Paving. . . . . . . . . . 73 Unique Paving Materials . . . . . . 50 Weiler . . . . . . . . . . . . . . . . . 43 Willow Designs . . . . . . . . . . . . 73 Wirtgen . . . . . . . . . . . . . . . . 37
AsphaltPro’s advertiser index is designed for you to have quick access to the manufacturers that can get you the information you need to run your business efficiently. Please support the advertisers that support this magazine and tell them you saw them in AsphaltPro magazine.
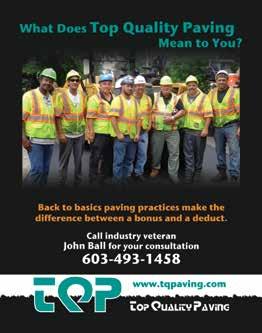
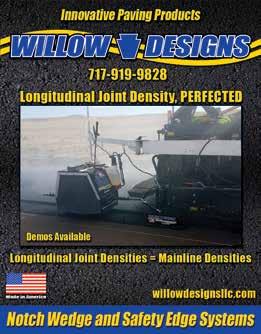
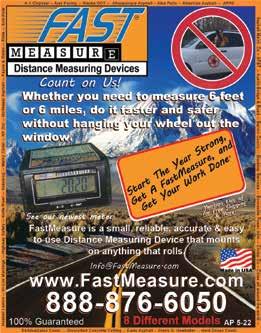
Step 2
Polymer pellets from the weighbridge are augered to the mixing chamber.
Step 3
The D&H horizontal mixing chamber disperses the polymer into the asphalt.
Step 4
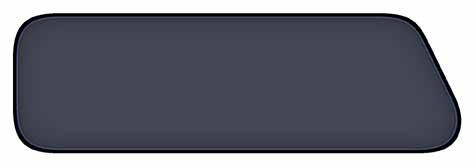
The discharge pump moves the mixed material through a high shear mill. Step 1
Heated virgin asphalt enters the system and flows toward the mixing chamber.
If product needs to be remilled, the discharge pump, or extra piping and valving, can recirculate the product back through the mill.
Step 2
Step 4 Mill Step 6
From the mill, the material is sent to a concentration tank, where heat and aggressive agitation promote the dilution and even the dispersion of polymer within the asphalt.
Step 5
The mill shears the polymer to increase surface area and reduce dilution time.
D&H Equipment’s PMA Blending Plant
BY ASPHALTPRO STAFF
Polymer-modified asphalt (PMA) is a premium product consisting of liquid asphalt binder combined with polymers to improve overall durability and in-service pavement performance. D&H Equipment, Blanco, Texas, offers production equipment for inline blending, milling and processing of PMA. Here’s how it works:
The modified asphalt production process starts by heating the asphalt to dissolve the polymer and to compensate for addition of ambient temperature dry material during the process.
Next, polymer pellets are loaded using a bulk bag unloading system into a feed hopper. A weighbridge at the bottom of the polymer feed hopper controls the discharge of dry material into another lift auger for transportation to the mixing chamber.
Neat asphalt is metered through a mass flowmeter by a variable speed pump. The automated controls manage the flow rate of the incoming liquid asphalt and adjust the feed of desired dry material to meet input ratio specs. As asphalt flows through the system, the polymer feed is managed by the automated controls based on the asphalt flow rate and the desired polymer percentage.
Materials then enter the D&H horizontal mixing chamber where polymer is dispersed into asphalt. A discharge pump transfers the mixed material through a high shear mill, which shears the polymer to increase surface area and reduce dilution time.
From there, the product is sent to a concentrate tank for processing. Heat and aggressive agitation inside the processing tank promote the dilution and even dispersion of polymer within the asphalt until the polymer has fully dissolved into the asphalt.
If a polymer concentrate was produced (typically using around 9-15% SBS by weight), then it is generally diluted to 6% or less so that it can be safely crosslinked. Crosslinking the final product creates a molecular net that keeps the polymer molecules in suspension and prevents separation of the polymer and asphalt during storage. Typical finished products are further diluted to around 2-4% polymer by weight, based on the desired mix design/specs.
For more information, visit https://www. dhequip.com/.
SHOW US HOW IT WORKS
If you’re an original equipment manufacturer with a complex product, let us help you explain its inner workings to asphalt professionals. There’s no charge for this news department, but our editorial staff reserves the right to decide what equipment fits the parameters of a HHIW feature. Contact our editor at sandy@theasphaltpro.com.
