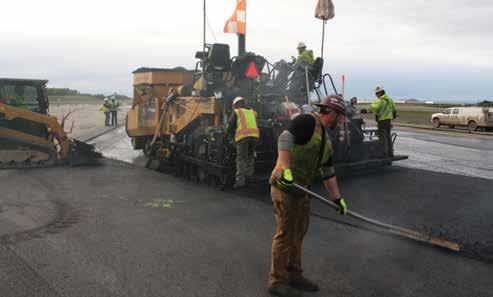
16 minute read
Quality Asphalt Paving
Quality Asphalt Paving Upgrades Anchorage Airport
AAlaska’s largest city is currently witnessing a case of new technology clearing the way for…new technol ogy. At Ted Stevens Anchorage International Airport (TSAIA), Quality Asphalt Paving (QAP), based in Anchorage and a subsidiary of the Colaska Group, recently performed a ma jor overhaul of the primary north/south runway to accommodate today’s bigger, heavier cargo aircraft. To help make that happen, the company assembled a fleet of heavy equip ment, most of it employing GNSS-based technology. Facing only a six-month window to finish work on the nearly two-mile-long run way, shoulders and adjacent taxiways, QAP achieved outstanding results in earthmoving, milling and paving.
CARGO IS KEY
While TSAIA handles its share of passenger traffic—more than five million people annu ally—the airport’s real strength is as a key hub for cargo traffic. Strategically located between the world’s two largest e-commerce markets, China and the United States, TSAIA ranks fifth in the world in air cargo, growing by 2.52 per cent to 2.79 million metric tons in 2018 alone. According to Martin Meenaghan, QAP’s proj ect engineer, the stream of cargo-laden jumbo jets into and out of the facility on any given day is virtually non-stop.
“This airport sees some of the largest air craft flying today, including ‘The Dreamlifter,’ which Boeing uses to transport entire wings of commercial aircraft,” he said. “We were tasked with bringing the runway up to new FAA specs designed to better handle these—and larg er—aircraft as the airport moves forward…. We were contracted to widen the structural section of the runway. So, while the footprint of the runway will remain essentially the same, the weight-bearing section of it was widened by some 65 feet.”
Upgrade work at TSAIA started with a 1,500-foot section of runway so QAP could gain familiarity with the technique they would use for milling the entire structure: Topcon Millimeter GPS. However, work began later The team from QAP, a Colaska subsidiary, completed the asphalt work on TSAIA ahead of schedule in September 2019. While the company had no financial bonus waiting on an early completion date, Martin Meenaghan, QAP’s project engineer, said the incentive to finish early was three-fold. “We’re done, we’re under budget, we did a good job and the customer is satisfied.”
with the shutdown of runway 15/33, and the di version of all traffic to the east/west runway (07/25) at the southern end of the airport.
FLIGHTS TO LIGHTS
QAP’s work at TSAIA ran the gamut from preliminary earthmoving to milling to paving to prep for landing light installation. To help them handle each facet in the most efficient way possible, the company called upon Mike Williams, co-owner of GPS Alaska, based in Anchorage, to discuss equipment and con trol solution options available to them. Doing so was not just the proverbial “shot in the dark.” For several years now, their parent company, Colaska, has been one of Topcon’s strategic partners.
“We enjoy a great relationship with Colas ka and worked hard to win them over,” Williams said. “…we knew they could benefit from what Topcon had to offer. We sat down with Joe Webb, Robb Dunn and Mike Fizette and showed them all that was available, finally do ing a ‘Fly and Try’ into Topcon’s Livermore, California, test center. There, each potential Scott Hightower, QAP project manager, saw everyone on his team working off the same model with the Topcon machine control.
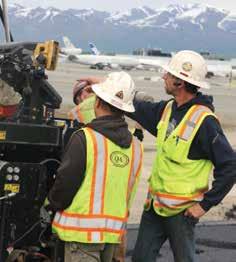
user got a chance to see and test the technol ogy that could improve their effort….Today, thanks to their commitment, they are one of our best proponents of GNSS solutions, and it showed out at the airport.”
ABOVE: The QAP team placed and compacted roughly 150,000 tons of asphalt. BELOW: Robert Hoadley tracked his passes with Topcon’s intelligent compaction on the Anchorage airport project.

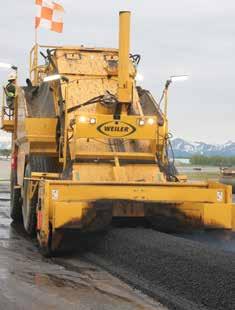

The lineup QAP brought to bear at TSAIA included: a John Deere 850 dozer, a Cat D6N dozer with 3D-MC MAX, and a Cat D6T doz er with 3D-MC2 machine control; a Cat 16M motor grader running twin 3D-MC; a Komatsu 1200 excavator with X-53i indicate-only GPS; a Wirtgen W250i milling machine with dual Mil limeter GPS; two CAT F Series pavers; a pair of Cat CB-68B rollers and a Dynapac 700 roller with Topcon C-53 IC Intelligent Compaction; and four Topcon FC-5000 data collectors.
The runway began as 11,470 feet long and 200 feet wide. Excavation work included dig ging a full-length trench on either side of the runway and filling each trench with gravel to provide the additional structural stabili ty. Work in this area also included new piping systems for drainage. Runway Safety Areas (RSAs), which extend off the pavement, were excavated at 2 feet deep, 110 feet wide the en tire length of the runway. According to Meenaghan, having machine control at work made a significant impact.
“With everyone working off the same a model, things are roughed in quickly—it’s all very efficient,” Meenaghan said. “We were out here for seven weeks and had the bulk of the earthwork knocked out. It turned into a paving show much sooner than we ever anticipated. Granted, there are always weather days that we always have to anticipate up here, but it’s nice to get a bit of breathing room so early on.”
Having that level of efficiency in all phases of the project was not just a luxury. While there’s no incentive built into QAP’s contract for finishing the TSAIA project ear ly, there was a penalty of $18,000 per day between two phases for delays beyond the contracted end date.
“For us, the incentive to finish early is this: we’re done, we’re under budget, we did a good job and the customer is satisfied,” Meenaghan said.
MILLIMETER MILLING
While QAP has done its fair share of airport work in the past, the tight milling specs— within 0.02 foot—still made the Anchorage job something of a challenge. For that rea son and others, they opted for the Millimeter GPS solution and found it to be the answer they needed, according to Thomas Davis, QAP’s grinding and reclaiming foreman.
“From my perspective, the biggest benefit the Millimeter GPS provided was an amazing ly accurate way to deal with the grade breaks,” Davis said. “Out here, the grade off centerline was consistent: for 25 feet on either side it was 1.5 percent. But in the areas where the runway crossed the taxiways, not only did it vary, it was also vague in the plans and needed to be cal culated. But when we built the model, all that data was in there. That was huge—without it, we would have been chasing cross slopes throughout each taxiway.” He added that, despite the time it took to ready the system each day (calibrations, set ting up transmitters, etc.), they were still far ahead of the game in milling.
“Once we were off and running it was great to see the GPS take over,” he said. “In a sense, it took my job from me. However, it did free me up to do other things and to follow behind with a data collector for periodic grade checks. I think it was a great setup for what needed to be accomplished out here and the results speak for themselves.”
INTELLIGENT COMPACTION DURING PAVING
In anticipation of things to come, QAP also opted to employ intelligent compaction (IC)
during the paving facet of the job. Already close to being a prerequisite to bid DOT proj ects in a number of states, IC can provide real-time feedback for the number of passes performed, temperature and stiffness. Doing so helps the operator compact when, where and only as much as needed. One of the compa ny’s roller operators, Robert Hoadley, said that, while IC can help management remotely monitor the machines and identify issues be fore they become a concern, he also finds the technology helpful.
“I think this is a really good system,” Hoad ley said. “It shows me on-screen how many passes I’ve made as well as my densities—it even has a sensor that tells me what the tem perature of the asphalt is. Without IC, none of that is available and operators have to count the number of passes made. Here, I can pro gram each pass to be a different color and quickly identify an area that is at risk of over or under-compaction.”
QAP’s completion date for asphalt work at TSAIA, while technically Sept. 30, 2019, in cluded two weeks during which the FAA had scheduled flight testing to begin mid-month.
A STORY IN VOLUMES
To get a better handle on the size of the project at TSAIA, one need look no further than the volumes of material involved in the various phases. By project’s end, QAP placed and compacted roughly 150,000 tons of asphalt, laid down a half million tons of gravel, and moved a half-million cubic yards of earth during excavation.
According to Martin Meenaghan, though they’ve become much more GNSS-savvy the last couple years, the help provided by GPS Alaska on the airport job was invaluable.
“Mike Williams and his team have been great—they’re our go-to guys out there for sure,” he said. “They are very knowledgeable of the solutions they provide and always make themselves available—a company like ours can’t ask for better than that. There’s a lot out here that simply couldn’t have happened without them.”
“So, we were dealing with substantial completion mid-September, final completion at the end of the month,” Meenaghan said. “But this was a great job and we are very satisfied with the way things have gone. All the GPS equipment we had on site saved us either time or manpow
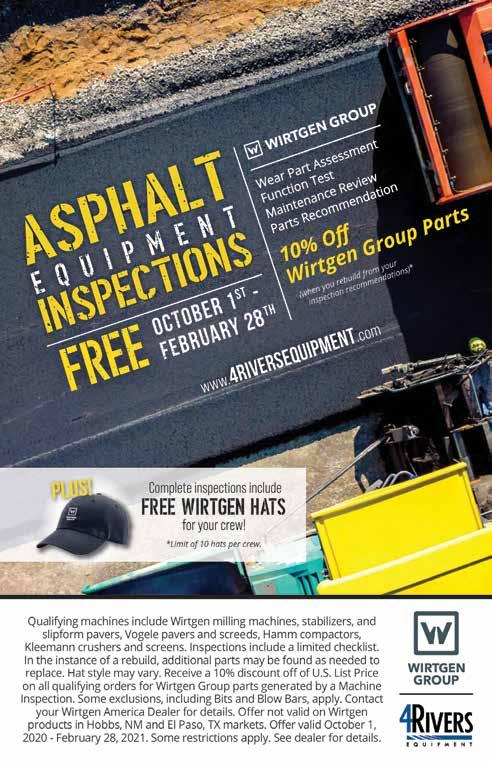
er. And milling with the Topcon Millimeter GPS system proved to be a good move; production exceeded what we had built in for the job. We’re definitely pleased with where we’re at and what we have moving forward.”
– BY LARRY TROJAK
In the fall of 2019, Palmetto celebrated the first year of operation for its new plant in Lugoff, South Carolina, with a team cookout.

Palmetto Puts up Plant #4
WWhen Palmetto Corp., Conway, South Carolina, was awarded a large project on Hard Scrabble Road in 2016, the company began investigating the need for another asphalt producer in the central South Carolina market.
Hard Scrabble Road is a main thoroughfare 15 miles northeast of Columbia, with an average annual daily traffic count of 45,000. Surrounded by a mix of schools, commer cial properties and residential properties, the road is a major commuter route in ad dition to supporting a high volume of business-related heavy trucking.
“Congestion, coupled with growth and expansion, created a need for improved access and traffic flow,” said Palmetto COO Eric Faulk. Palmetto began working on the project July of 2018 and is expected to com plete the project June of 2022.
During that time, the 8-mile span of road way will be expanded from two lanes to four. The scope of work includes two new bridges, newly installed overhead and underground utilities, newly installed concrete curb and gutter and sidewalk, subgrade prep, and 130,000 tons of paver-placed 10-inch cement stabilized base course (CSABC) topped with 182,000 tons of hot mix asphalt (HMA).
“Our asphalt plants are the core of what drives our business,” said Palmetto CEO Shawn Godwin. “Even though we provide trucking, milling, concrete, reclamation, sur veying, dirt moving, pipe laying and crushing, our core business is asphalt. That is driven by having the ability to control all variables from quality to production and the asphalt plant allows us to do that.”
Palmetto already had three plants located in the central and eastern parts of the state, in Conway, Florence and Bishopville, but a fourth plant located closer to the state’s capital of Columbia would expand its reach.
According to U.S. Census data, Colum bia’s population has grown by 15 percent since 2000. As the state’s capital and its most populous city, Columbia is also a junc tion of numerous major highways.
“Columbia is a growing market, especial ly the suburbs,” said Palmetto’s Plant Division Manager Charles “Ray” Mothershead. Palmetto’s new plant in Lugoff, 30 miles from central Columbia and 12 miles from its Hard Scrabble Road p roject, is well-situated for future growth.
“It would be difficult to be competitive in the Columbia market without the new plant in Lugoff,” Mothershead said. Trucking mix from its second-nearest plant, in Bishopville, would add 25 miles to the journey. “Now, we
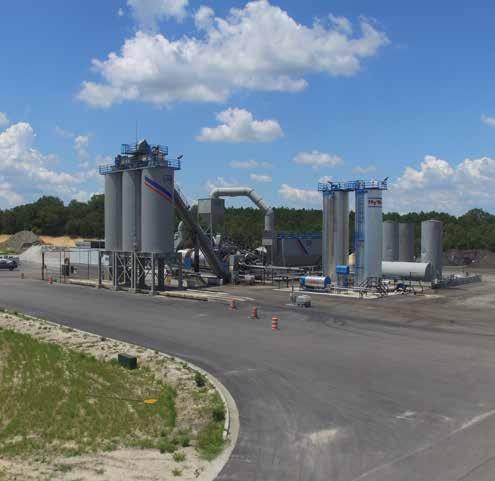
can reach into the Columbia market, as well as into Lexington County to the west and Kershaw County to the north.”
“Expansion was part of the plan to grow in a new region to not only actively pursue more SCDOT and municipal work but to also tap into a flourishing commercial mar ket,” Faulk said. The majority of Palmetto’s work is a mix of South Carolina Department of Transportation (SCDOT) contracts, FAA airfield work, municipal contracts and com mercial contracts. “The Lugoff plant, along with the Hard Scrabble Road project, acted as the catalyst that helped facilitate some very intentional progression where that growth strategy was concerned.”
The Hard Scrabble Road project will require 52,000 tons of HMA Base Type A, 4,000 tons of HMA Surface Type C and 126,000 tons of HMA Surface Type B.
The Lugoff plant is a Gencor Ultradrum rated up to 300 tons per hour. It’s equipped with three 200-ton silos, six cold feed bins, one RAP bin and its own lab.
When the plant was first built, Palmetto had only installed two silos. However, after one year of operation, they realized they needed more storage space.
“We didn’t think the demand would pick up as fast as it did, or that we’d need to have as many mixes as we did on any given day,” Mothershead said. At times, they still had to send mix from Palmet to’s Bishopville plant to jobs closer to the Lugoff plant for that reason. In May 2020, Palmetto added a third silo to the Lugoff plant. “This year, we will begin the paving portion of the Hard Scrabble Road job, so we will definitely need that third silo so we can continue outside sales of asphalt while balancing the intercompa ny demand.”
Palmetto also invested in Gencor’s Ultra-II multi-fuel aggregate combustion system for clean and efficient burning.
“When the company bought the plant, we knew we wouldn’t be able to get natural gas to the site initially because the site was brand new,” Mothershead said. “We knew we’d have to run waste oil for at least the first year.”
The Ultra-II burner was the ideal choice, Mothershead continued, because “it not only works well with waste oil, but it will also do a good job when that plant gets switched over to natural gas.”
Mothershead said the ability to mount the flights within the Ultradrum into mul tiple positions is also a helpful feature. “By positioning the flights in a certain way, you can control the veil of stone in the drum and create some holes in the veil as the stone comes down to allow for the heat to make its way to the back of the drum and into the bag house,” he said.
SCDOT requires 1 percent lime in two standard mix designs, so the Lugoff plant also has a lime silo integrated into the plant’s controls. Although each of Palmet to’s plants has this capability, Mothershead said the Lugoff plant was built from the ground up with this capability.
SCDOT’s RAP spec is based on percentage of aged binder rather than overall RAP percentage. “We average about 25 percent RAP to stay within the aged binder limits,” Faulk said. However, Mothershead added, the amount of RAP allowed will likely increase in the future and said the Lugoff plant will accommodate higher RAP content.
The plant also incorporates Gencor’s Ultralogic plant controls.
“We’ve trained a couple fellows to run the plant who hadn’t run an asphalt plant before
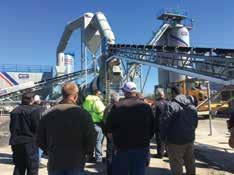
In May 2020, Palmetto added a third silo to the Lugoff plant to keep up with demand.
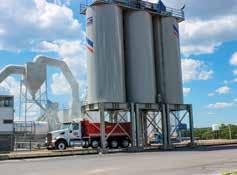
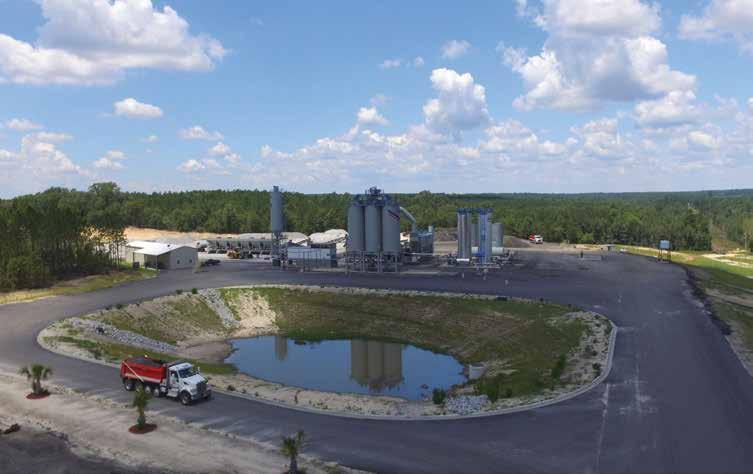
and they took to it very easily because of the Ultralogic controls,” Mothershead said. One of those new employees was Mothershead’s son, Charles Mothershead III, age 22. When Mothershead was promoted to division man ager of all of Palmetto’s plants, his son was promoted from plant operator to plant fore man at the Lugoff facility.
“I think the modern controls are more us er-friendly for the next generation of plant operators,” Mothershead said. Mothers head, who has been in the asphalt industry for 30 years, recalls the days of levers and batch plants. By comparison, the new system is a breeze, he said. “You can start the whole plant up with the push of a button.”
The Lugoff facility is also home to three asphalt paving crews, one concrete crew, four grading crews, 20 haul trucks and driv ers, a truck foreman and a dispatcher. It is also home to a fully equipped equipment and truck shop, as well as an office that houses Palmetto’s Midlands survey division, direc tor of business development, Midlands estimators and the Midlands area management.
In total, Mothershead estimates the plant has created 100 jobs in the area.
“We have assembled a great team and the Midlands market is going to be a great market for the years to come,” Godwin said. “It has far exceeded our expectations.”
In its first year, the Lugoff plant produced around 140,000 tons, with 120,000 tons for Palmetto projects.
“The leadership at Palmetto isn’t just growing the company for themselves, but to create more jobs in the state and to open up doors for so many people,” Mothershead said. “With leadership like that, I wouldn’t be surprised if Palmetto covered the whole state one day.”
– BY SARAH REDOHL
IMAGINE YOUR DREAM

YOUR BUSINESS STARTED AS A DREAM, TO GROW AND PROFIT. To get the personalized attention you want to help you on your way. The customization you need to meet your business’s specific production goals. Consult with one of our specialists today to help configure just the right asphalt plant for you. Start your custom plant design today.