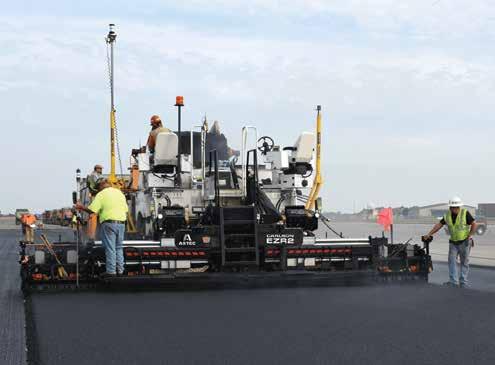
10 minute read
Autonomous Tech Gets Assist from NODAR
BY ASPHALTPRO STAFF
NODAR, Somerville, Massachusetts, a provider of advanced stereo vision technology for autonomous vehicles, announced in January that it is moving to accelerate the growth of the autonomous vehicle market and ensure the development of safer autonomous solutions by expanding to new markets, including (but not limited to) commercial and agricultural vehicles. NODAR’s Hammerhead Development Kit (DevKit) enables new partners to assess and integrate its 3D vision technology, which already supports the ADAS and automotive markets with ultra-precise, long-range camera-based sensing, according to the manufacturer.
The NODAR DevKit includes the software, hardware and tools for autonomous systems developers to leverage the benefits of NODAR’s patented Hammerhead™ technology. Hammerhead is an untethered stereo vision software platform that uses images from multiple cameras to produce high-fidelity 3D point clouds in real time. The system detects objects as small as 10 cm at 150 meters away.
Autonomous systems such as construction cranes and farming equipment should benefit from Hammerhead to perceive their environment in real time. Hammerhead’s proprietary online calibration system delivers resilience to extreme vibration, making the system ideal for off-road, commercial and in-air autonomous system applications, according to the manufacturer.
“Every autonomous system must have the ability to ‘see’ and sense its environment in order to avoid obstacles and do path planning,” NODAR CEO Leaf Jiang said. “In the automotive industry, 3D vision is the cornerstone of developing safer autonomous vehicles. Recently, we’ve been hearing increasingly about the automation of robotic systems beyond the automotive market, and that’s very exciting for us. The DevKit we are releasing makes NODAR technology accessible across a wide variety of markets and applications of autonomy, offering the reliability of active sensing systems at the price-point of cameras.”
Demand for autonomous systems across markets is being driven by the promise of improved efficiency, safety and economics. For instance, the $270 billion U.S. commercial trucking market was suffering from an 80,000-driver shortage at press time, due in part to the pandemic and substantially to the growth of ecommerce in general. Yet the cost of the driver constitutes approximately 60% of the overall cost to run a vehicle. While human drivers cannot legally drive more than 8 hours a day, autonomous trucks are tireless and can run nearly 24 hours a day, improving delivery times and capacity. Further, trucking accidents are reported to account for nearly 5,000 fatalities a year in the United States—a number that is expected to decline as autonomous functionality comes online.
“Autonomous heavy equipment is making inroads in the construction industry— for instance, autonomous track loaders and skid steers are in use on construction sites today,” NODAR COO Brad Rosen said. “With lower fuel consumption and reduced emission, self-driving equipment can help meet increasingly strict environmental standards. It can also eliminate human issues like fatigue and distracted driving, and help compensate for the ongoing shortage of skilled labor.”
“Self-driving compaction equipment is likely to join the paving train next,” Rosen continued. “Rollers for asphalt and soil compaction use highly repetitive processes, which can lead to rolling pattern variations as an operator’s attention waivers. By performing repetitive tasks more consistently and precisely, automated equipment can ensure greater layer durability, improving quality while freeing skilled workers for more demanding work and reducing costs. Further, autonomous equipment can have a significant impact on one of the industry’s most important objectives: making asphalt paving sites safer for workers.
“In this context, NODAR’s Hammerhead technology makes it possible to operate more safely and reliably in a challenging environment where the terrain and surroundings are different every day, the temperatures can reach high levels, and where the vehicles and road cause significant vibration. The system’s camera-based advanced stereo vision helps heavy equipment identify potential hazards, accurately detect where objects and hazards are located, and navigate safely with resiliency to dust and vibrations as the equipment moves across bumpy sites. The use of high-performance 3D vision in autonomous heavy equipment helps improve productivity and reduce overall operational costs as well.”
As with autonomous vehicles and trucks, NODAR’s platform benefits all these new markets with its support for independently mounted cameras and wide baseline configurations, offering camera-based resolution, a small footprint, and the sensing reliability of LiDAR. NODAR’s new Hammerhead DevKit contains everything customers need to set up and begin using the system in a matter of minutes, according to the manufacturer.
For more information, contact sales@nodarsensor.com or www.nodarsensor.com/dev-kit.
Astec
The EZR2 highway class, rear-mount screed, now from Astec Industries, Chattanooga, comes in the 8 and 10 models. The EZR2 10 extends from a standard paving width of 10 feet to 19.5 feet to a maximum paving width of 30 feet and features vibration from four motors from zero to 3,000 vpm. The screed weighs 8,275 pounds. Its maximum extension slope is 12% positive and 5% negative. Depending on the tractor, it includes four outlets for power. Power output is 120 volts.
The EZR2 is designed so it can be mounted to all current 8-foot and 10-foot North American paver models offered by the major paver manufacturers, as well as able to retrofit to nearly any previous 8-foot or 10foot North American highway-class paver.
One of the screed’s features is the power tunnel kit from Astec, which features hydraulically extendable tunnel extensions made with durable steel parts that are easy to replace if damaged, according to the manufacturer’s website. The tunnel is designed to be compatible with most make and model pavers.
For more information, visit https://www. astecindustries.com/products/details/ezr2highway-class-screed?
Bomag
The BW 174 AP-5 AM Hybrid from BOMAG Americas, Ridgeway, South Carolina, is designed for tandem roller efficiency. The roller’s innovative hydraulic hybrid drive stores braking energy, which is released flexibly during peak loads. This allows the engine to cover the base load and operate with maximum efficiency. The system lowers fuel consumption and CO2 emissions by up to 20% without sacrificing performance, according to the manufacturer.
ECOMODE and ECOSTOP are standard on this roller. ECOMODE is an intelligent control system designed to optimize engine speed to save up to 30% on fuel and reduce noise from the machine. ECOSTOP will automatically shut down the engine if left to idle, reducing fuel use, cutting down on noise and helping to avoid wear.
The roller’s menu navigation is displayed on a high-resolution, 10-inch (254-mm) customizable touchscreen. User friendliness is paramount with this roller, as it offers the choice of three operating modes: touch, rotary pushbutton or classic switch operation. The Asphalt Manager operation system assists operators of all skill levels from there. The operator sets the layer thickness, and
Product Gallery
Asphalt Manager does the rest. The vectoring drum changes vibration from true vertical to true horizontal as asphalt stiffness increases.
The pivot-steer roller features five steering modes. Its generous crabwalk is activated in one of two ways—via travel lever or by preselection with a rotary switch. BOMAG’s patented steering system is engineered to automatically reduce crabwalk when turning to ensure the roller travels safely and precisely along the edge.
For more information, contact 803-337-0782 or visit www.bomag.com/us-en.
Cnh Industrial
If a mini excavator engine fails in the middle of a job, it can mean significant cost, both in time and dollars, to make those repairs. CNH Industrial Reman offers remanufactured engines for Case and New Holland mini excavators as an alternative.
“When an engine fails on a mini excavator, you have several options—buy new, buy reman or repair the failures,” Kent Whitaker, product manager for CNH Industrial Reman, said. “When repairing an engine like this, the number of parts that would have to be replaced almost out values the value of the engine itself.”
According to Whitaker, the decision to launch reman mini excavator engines in 2018 was based on a feasibility study. The study identified a gap in the reman market, especially in the landscaping and construction industry, which CNH Reman sought to fill with their remanufactured engines.
As industry demand shifted from traditional equipment to new mini excavators, it created a lot of competition in the marketplace. By offering reman engines on the service side, CNH
Industrial Reman added value to Case and New Holland’s product offering and created a competitive advantage.
Because of the increase in demand for mini excavators, Whitaker says there is a number of machines in use that could potentially need remanufactured engines, which creates a steady stream of demand for this product offering and service.
Whitaker said with CNH Reman’s remanufactured mini excavator engines, customers are receiving a like new product. During the process, engines are completely disassembled and failed parts are replaced. Every CNH Reman engine is tested for quality assurance and backed by a 24-month warranty.
CNH Reman engines are qualified for use in Case and New Holland machines. The team goes through OEM engine training and original OEM designs are used to remanufacture engines, increasing the overall quality of the remanufactured product.
For more information on remanufactured equipment, read the AsphaltPro article, “Rebuild & Reman for Savings, Sustainability, Supply Chain,” in the November 2022 issue.
Dynapac
Dynapac’s foray into oscillation on a tandem drum roller came about four years ago with the 11-ton CO4200 VI. Since then, Dynapac has introduced the oscillation technology on its CO5200VI (77-inch, 13-ton), CO2200 (59-inch, 8.5-ton), and the largest roller in the family, the CO6200VI (84-inch, 13.5-ton). The CO6200VI features vibration on the front drum and oscillation on the rear. The large roller also addresses two pain points contractors have shared:
One: Dynapac addressed the premature wear some contractors have experienced on the drum shell from the rubbing action against asphalt material by constructing the drums out of Hardox® 450 steel, which is the hardest steel that can be shaped into a drum shell.
Two: Dynapac addressed the inconvenience of changing the timing belts of an oscillating drum’s off-center eccentric weights. While the job often requires dismantling a drum in a shop, Dynapac has designed the drum so the timing belts can be replaced in two hours, and can be done in the field if necessary. They’ve prepared a one-minute video showing the process at https://youtu.be/yMvPNuJY_EM.
Dynapac will focus on technology and new products in its booth 30931 in the central hall at CONEXPO-CON/AGG.
For more information, contact Vijay Palanisamy at (210) 818-9602.
Rma Companies
RMA Companies (RMA), RANCHO CUCAMONGA, California, announced in January the acquisition of C Below Inc., dba C Below Subsurface Imaging (“C Below”), a provider of technology-enabled underground utility locating services. As part of the transaction, C Below’s operations will be merged with RMA’s SiteScan Subsurface Imaging business (“SiteScan”) under the leadership of Chris Loera, C Below’s CEO. Since December 2021, RMA has completed four acquisitions, as it executes an aggressive growth strategy to build a national platform for testing and inspection services.
This matters to paving and pavement maintenance contractors performing milland-fill work because C Below’s engineers and technicians use specialized equipment to offer advanced geophysical capabilities, including electromagnetic location, ground penetrating radar, BIM mapping, and CCTV pipeline inspection. Through these services, C Below helps its clients prevent construction delays during excavation of existing subsurface infrastructure by confirming the location, depth and type of buried utility assets.
Topcon
Topcon Positioning Systems, Las Vegas, announced in January its 2D-MC automatic grade control solution for compact track loaders. Now available in North America, 2D-MC is a two-dimension machine control system that is designed to be installed directly onto select grading attachments. Connecting directly to the machine’s controls and a wireless display, the solution works along with familiar rotary laser technology to provide simplified operational visibility, with all the information needed to hit target grade with greater precision and in less time, according to the manufacturer.
The manufacturer stated: Ideal for slope work, sidewalk grading, road base and drain rock replacement, parking lots, sports fields, landscaping, flat pads, indoor work, site prep and more, 2D-MC is an automatic grade control solution designed to adapt to different grading attachments for compact equipment, leveraging the performance of machine control technology with the accuracy of laser positioning.
Volvo
Volvo Construction Equipment (Volvo CE), announced in January its investment into the production of electric wheel loaders from its plant in Arvika, Sweden, which specializes in the production of medium and large wheel loaders. The SEK 65 million (around $6.3 million) investment from Volvo Group will allow the Arvika site to expand its facilities with a new building and allow for the phased introduction of new electric wheel loaders.
It is not only a milestone in the plant’s almost 140-year history, but a significant moment for Volvo CE and its determination to be completely fossil-free by 2040, which is in line with the aims of the Paris Agreement. It is also a pioneering step forward in the company’s ambition for 35% of its machines sold to be electric by 2030. Volvo CE has already introduced compact electric wheel loaders to the global market with the L20 Electric and L25 Electric wheel loaders.
Thanks to the investment, Arvika will erect a new building, approximately 1,500 sq m, which will allow the facility to free up areas inside its assembly factory to be able to build electric wheel loaders. While it has not yet been announced which models will begin their electric transformation and exactly when, production of both electric wheel loaders and more traditional wheel loaders fitted with combustion engines will continue for now on the same production line.
Yanmar
Yanmar Compact Equipment North America (YCENA), encompassing the Yanmar Compact Equipment and ASV brands, finalized its status as a single legal entity. The major milestone came three years after the Yanmar Group acquired ASV Holdings Inc. Now, the Yanmar Compact Equipment division in North America and ASV officially join to become YCENA.
The entity, headquartered in Grand Rapids, Minnesota, also announced, back in January, plans for a 32,000-square-foot expansion to its Grand Rapids facility. The new expansion and a subsequent paint system will increase paint capacity by up to three times with maximum automation and allow a parts manufacturing capacity increase of up to two times in the previously occupied space. This project sets the stage for future capacity increases with company officials projecting the addition of hundreds of full-time positions over the next five years.
Ad Index
AsphaltPro’s advertiser index is designed for you to have quick access to the manufacturers that can get you the information you need to run your business efficiently. Please support the advertisers that support this magazine and tell them you saw them in AsphaltPro magazine.
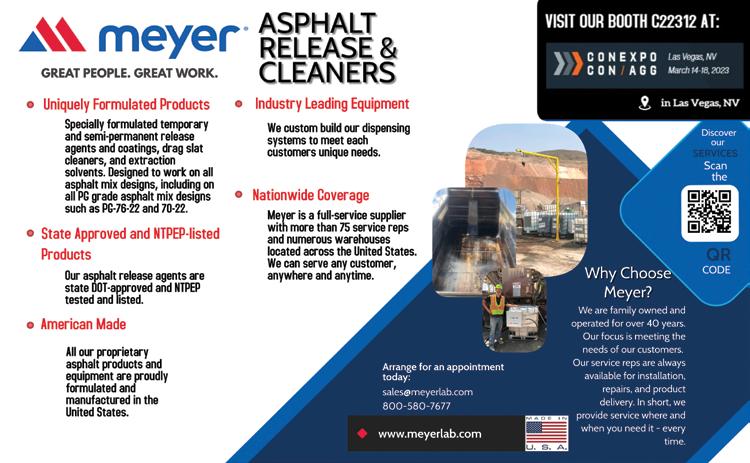

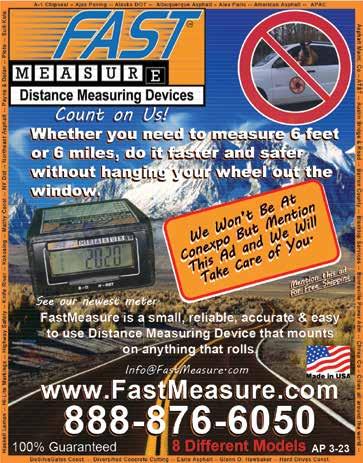
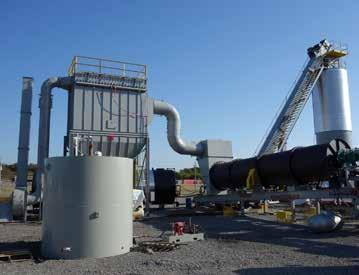