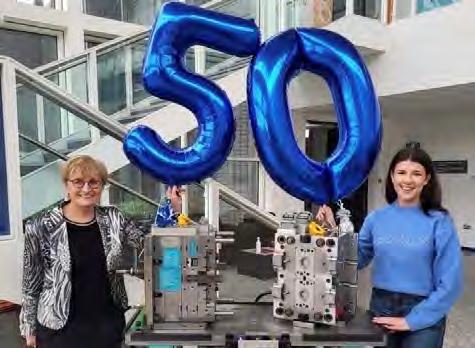
5 minute read
Women in ApprenticeshipsToolmaking at ATU
Úna Parsons, Head of College and Head of Faculty of Engineering and Design at ATU Sligo, talks to Julie Coleman, an apprentice student in Toolmaking at ATU
Úna: Thanks Julie for agreeing to talk to me about your experience on the apprenticeship programme in Toolmaking. How did you end up on the programme?
Julie: I didn’t have an idea of what toolmaking was before I started the programme though my father is a toolmaker in Cork. I wanted to do a programme that would be handson. There’s not many students pursuing an apprenticeship which is unfortunate as there are a lot of career paths that you can go down after you qualify.
Úna: That’s very true and a lot of people don’t know what toolmaking is. Toolmaking is not the production of hammers and spanners, but the manufacture and maintenance of “industrial tools” used in the mass production of everyday components. These include moulded plastic components (moulds), formed metal components (press tools) and also jigs and fixtures used in the automation and inspection of the manufacturing process.
Toolmaking is “high precision” engineering, working to tight tolerances of less than .01mm, 8-10 times less than the average human hair. It requires an attention to detail, and knowledge and skill of a variety of machining techniques, including manual and computer controlled machines to produce the many components that make up these “industrial tools”. These tools are used to produce components from the panels of cars (press tools), medical devices, mobile phones, and ‘keep cups’. We’ve just introduced plastic ‘2GoCups’ here in ATU Sligo. Could you explain to the reader how a toolmaker might be involved in the production of a ‘2Gocup’?
Julie: Basically, a toolmaker designs the metal mould, that the liquid plastic used to make the cup is injected into.
Úna: Yes, and the moulds can be quite complicated. Precision is very important when making the metal mould so that we have a smooth finish and, on this cup, we have a lot of ribs so it would need a complicated mould to this.
Julie: That’s right and we also need to maintain the mould as it can change over time, so that’s a large part of the toolmaking work we do. We need to make sure they stay accurate and precise.
Úna: There’s other jobs that a toolmaker does apart from making metal moulds for cups. The pharmaceutical, and medical device industries also require plastic parts.
Julie: Yes, especially in the pharmaceutical industry, for example there’s an Irish company who make asthma inhalers. Precision is important for making metal moulds for jobs like this. The more technology develops the more critical it is to have the moulds accurate. So essentially toolmaking is precision engineering because it’s the mould rather than the liquid plastic that is the critical part of the manufacturing process.
Úna: Making moulds are just one aspect of toolmaking. One of my first jobs, in 1978 in Braun, was to create the gripper needed to lift a hair dryer out of its metal mould. I liked sewing and that’s what attracted me to toolmaking. Sewing is very precise and toolmaking appealed to me because it’s so precise too. At that time there were very few females working in toolmaking and it seems to be the same today. What’s it’s like for you to work in a male dominated environment?
Julie: I was surprised when I started that there were so few women in the industry. Working in a male dominated industry has its challenges but times are changing. It’s so important for women to be involved in toolmaking. They have a lot to contribute particularly as it requires people who are precise in their work. Toolmaking is a fantastic apprenticeship to do particularly for women.
Úna: When I started in the toolmaking industry there was a lot of manual work involved like polishing the surface of the metal mould, so it was smooth, so the finished plastic product didn’t end up with lumps and bumps.
Since then, technology has changed and we now have Computer Numerical Control (CNC) machines which have transformed the way toolmaking is conducted. Our tool room in ATU Sligo now has state-of-the-art computer-controlled equipment. Could you describe what some of that computercontrolled equipment does?
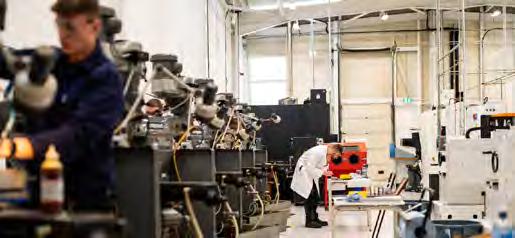
Julie: Yes, I work with CNC machines, and I use design software to create precise tools for pharma companies. Computer programming means that there’s less chance of errors when making the tools. I love seeing something I’ve designed coming to life. It’s very rewarding.
Úna: Could you describe some of the work you’re doing for the pharma industry, like what kind of tools are you making?
Julie: We make a lot of dies for pharma companies. Dies are fixtures they use on their production lines.
Úna: So, you make tools that cut metal for the pharma companies and they use these tools to make items like surgical instruments?
Julie: Yes, and we also make backup tools for them in case something happens on the production line and a tool is comprised. Back-ups help them stay efficient.
Úna: You started in college and then went into an apprenticeship. What would you say to anyone in school who is interested in either going to college or doing an apprenticeship?
Julie: Apprenticeship is an ideal way to learn, you are paid as you learn on the job, and you also get the experience of going to college and sitting in lectures. The lecturers are industry experts, so you are taught by an actual toolmaker.
Apprenticeship has changed. It’s important, particularly for women to know that there’s so many different routes you can take. You just have to look, and you will find something you’re interested in and allows you to use your talents.
But it’s important to know that it’s not easier than college. You must show up every day at work, you can’t just take a day off. However, there’s a lot of career opportunities when you qualify.
Úna: That’s very true. We have many employers coming to us asking if we know of any qualified toolmakers. Many industries rely on toolmakers so it’s a great apprenticeship to do.
Julie: Yes, and it’s a small apprenticeship for the size of the industry and I’d like to say to any woman reading this article that women can do the job as good as any man.
About Úna Parsons
Úna did her apprenticeship block release in Sligo forty-five years ago studying the trade of toolmaking at what was then called Sligo Regional Technical College.
She later did her Masters Degree in Advanced Manufacturing Systems with Brunel University in the UK. Since then, Úna has travelled the world in various global management positions working in the manufacturing industry across Europe, the USA, Mexico, Hong Kong and China.
An award-winning Chartered Engineer, Úna has worked as Industry Director for Engineers Ireland and was CEO of the Crafts Council of Ireland before taking up an academic management position in ATU Sligo in 2012. She is a Fellow of Engineers Ireland and in the last year was conferred with the distinction of Fellowship of the Irish Academy of Engineering.
About Julie Coleman
Julie is a 24-year-old apprentice toolmaker living in Cork City. She works for Automation & Tooling Specialists based in Carrigaline, Cork. She plans on completing her apprenticeship in toolmaking in 2024 and completing her qualification in mechanical analysis and automation in 2025. Julie is currently working on projects primarily for the pharma industry.