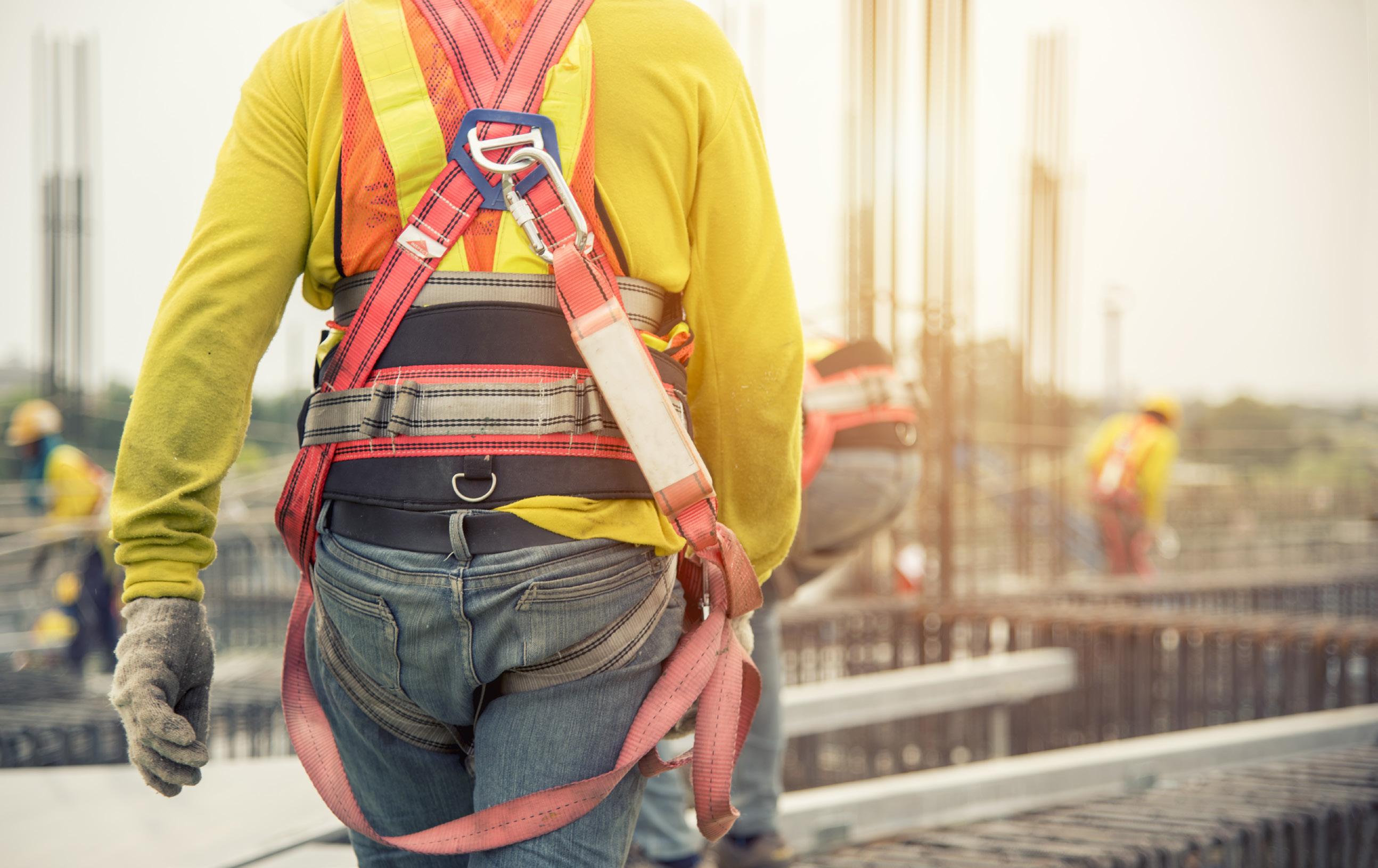
4 minute read
SAFETY REPORT: Preventing Falls on the Job
from the edge. Anchor points can be designed into the roofing system.
“It’s a lot easier to put it in during the design phase instead of trying to retrofit it down the road after the facility’s already been built. Cheaper, too,” Albright said.
Some project owners may not want to spend the extra money or may have concerns about aesthetics.
“The key is education and trying to get them to realize the long-term benefits,” Albright said. Gannett Fleming studies the workflows of each business group to assess specific hazards team members face. Then it gears safety training to those tasks.
The importance of training for good strength and balance is an overlooked aspect of fall prevention safety, said Johnson, who serves on the safety committee for the Associated Builders and Contractors Keystone Chapter and is a member of the Keystone Contractors Association.
“There are certain things that have to be strengthened to be able to play a sport. There are certain things that have to be strengthened to be able to do your job in the construction industry,” he said. “Their profession is their sport now. It’s what provides for their family.”
Many in the industry don’t think about strength training until they lose strength after an injury and have to regain it, he said.
National Safety Stand-Down week is an opportunity to reinforce other safety practices, too, such as wearing a hard hat.
Sallows has put on a demonstration where a heavy object is dropped from 30 feet onto a watermelon. The watermelon explodes when it’s not covered with a helmet and is hit with a falling sledgehammer. When protected with a helmet and hit with a falling brick, the melon stays intact.
“There’s a lot you can do and make it look really interesting, so the workers are interested.”
Something as simple as hard hats — how complacent we are when we put them on every day. We don’t think about how important they are until you actually see how they can protect our heads.
— Mayone Sallows Safety Manager, Alexander
Safety equipment can’t be taken for granted. New technology is making some equipment obsolete. And gear must be well maintained.
“Workers throw it in the back of the truck. It’s wet. It gets moldy, and then it starts to get destroyed. Some people don’t check it before they use it, and that can result in injury or death,” Johnson said.
During Safety Stand-Down Week. Alexander designs hi-vis T-shirts for team members, hands out stickers for hard hats, and provides lunch.
“It really shows our subcontractors and our people on our job sites that we appreciate what they’re doing every day by taking safety seriously and creating a good culture on our sites,” Sallows said.
Events also have included a Jeopardy-style trivia contest about fall prevention and other safety topics.
“The contactors like it and get to arguing about who got what answer right, and it’s a lot of fun,” she said.
Alexander holds an in-house safety trivia competition, too. Sallows sends out a question every morning during the week, and prizes are awarded to those who answer the most questions correctly.
The National Safety Stand-Down should be a company-wide undertaking, she said.
Fall Prevention Week also pertains to management personnel — even if you’re an estimator on a project, you have to account for what items are required to do the project safely. If you’re a project manager and making scopes for a project, you’re still going to have to look at these items and put them in the scope, so the contractors are bidding it accordingly. It involves more than just safety in the field. You really want to hit it from the start in the preplanning, in the preconstruction stage, before it ever gets to the site. At that point, it’s a last resort, and you’re trying to figure out what to do.”
Gannett Fleming reinforces fall prevention with videos, messages on social media, and tailgate talks at job sites during the National Safety Stand-Down Week. Despite all of the training the industry does, falls still happen too often, Albright said.
“It still amazes me in this day and age that you’ll go out and see people working in conditions where they should know better.”
Finding a proper anchor point when working at elevation is critical, Sallows said.
“What are you tying off to? Is it sprinkler piping? Because that certainly isn’t going to hold you.”
Some locations may not have proper anchor points, so portable safety systems are needed such as a Raptor Cart or a Garlock railing system.
“The key is to get your safety person involved because there are lots of resources, and we can find a system that works best for any situation,” Sallows said.
Contractors have gotten more sophisticated about ensuring there are adequate anchor points on job sites. Albright said the OSHA standard requires an anchor point to withstand 5,000 pounds of impact force per person who’s attached to it.

Workers now are attaching anchor points to steel beams on the ground, before they are flown into place, so there is an anchor point to tie off to immediately. Points can be temporary such as a wire lifeline or permanent such as a cut-out or an eye bolt on the beam.
Safety can affect a company’s bottom line, Albright said.
“They always say, ‘Safety sells.’ And from our standpoint in the engineering and construction management business, it really does. Our clients are getting a lot more sophisticated when they put out RFPs. They are really looking at our safety metrics very strictly to see how sophisticated our safety management systems are. And they’re looking at them now and asking, are we a competent firm to deal with? As that gets more and more to be a focus from owners and clients, I think contractors are going to be forced to make sure their programs are in good shape.” KC