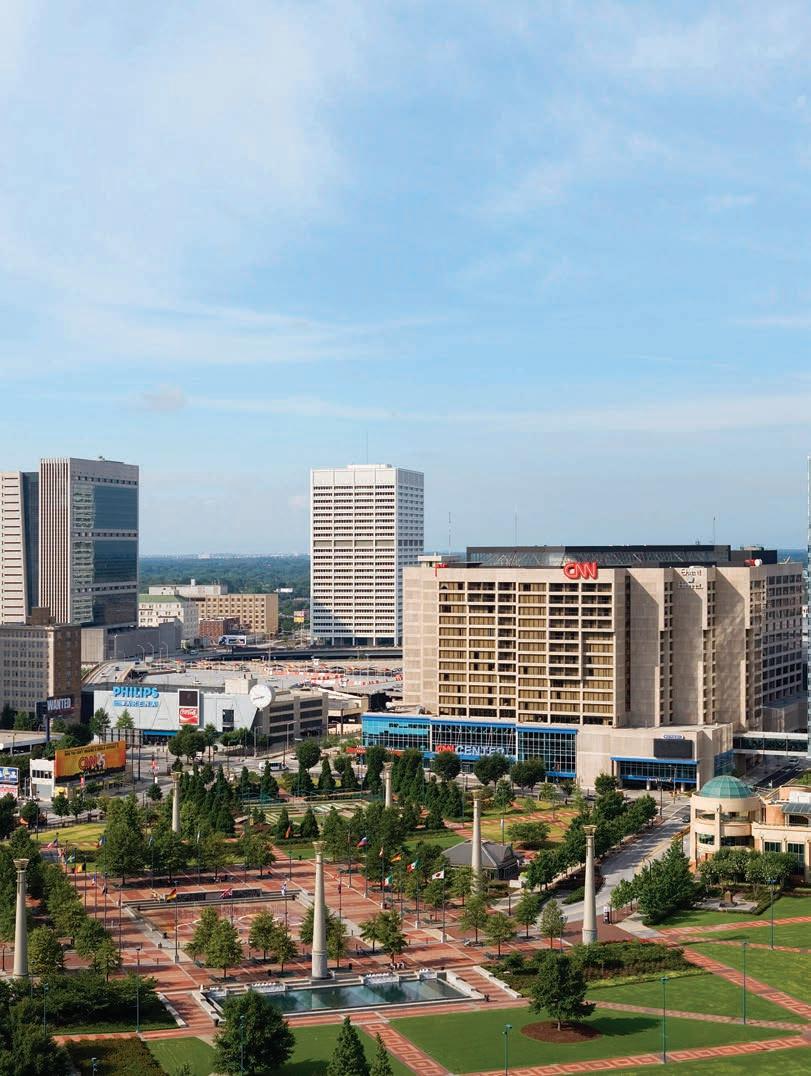
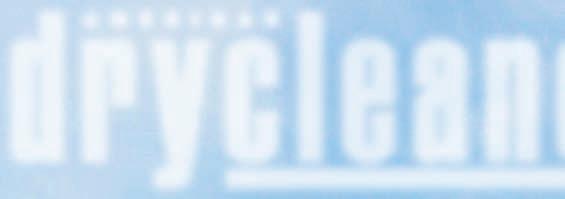
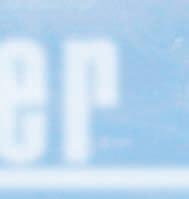
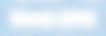
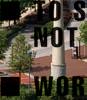
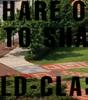
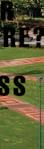
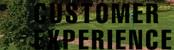
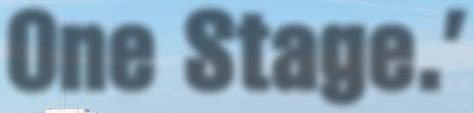

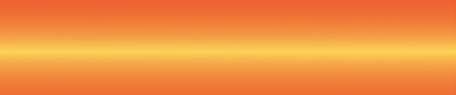

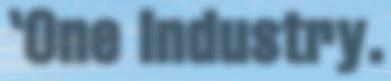


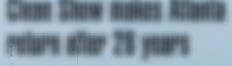
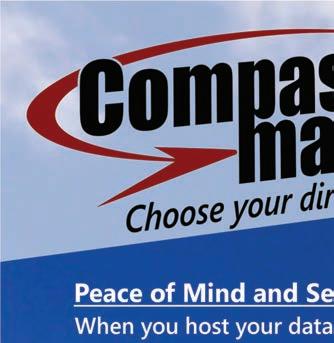
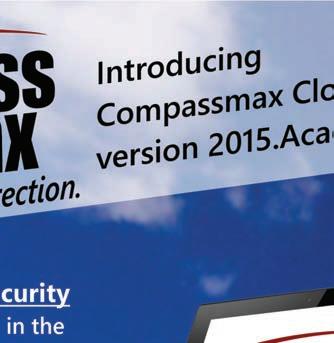

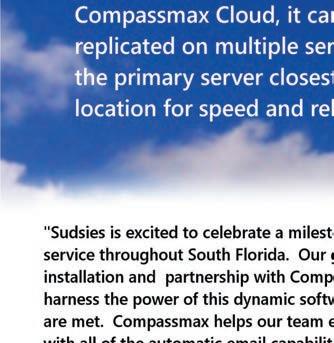
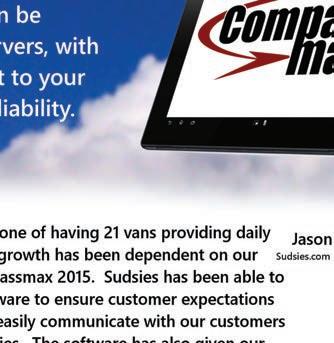
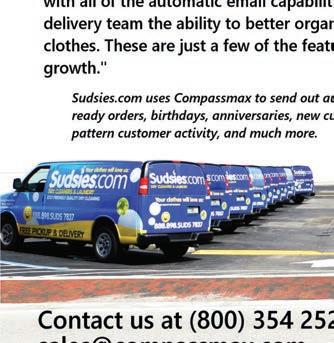

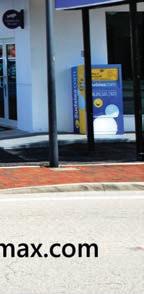

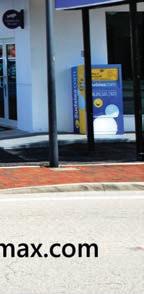
InkGo has been reformulated to remove its odor… and to improve its performance.
InkGo is still the environmentally friendly,* safe way to remove ink stains from all types of fabric. It’s still great at removing autoclave tape and adhesives. And since it’s odor free, InkGo is more pleasant to work with. Does odor really matter? As more drycleaners position themselves as good environmental stewards, keeping chemical odors in the plant to a minimum can help them differentiate from their competition. And odor-free is a real plus if you’re working on ink for an extended period of time.
Now that’s worth noticing!
*InkGo is Biodegradable and is California Prop 65 and California VOC Compliant.
Become a STAIN WIZARD at ALWilson.com
To learn more, visit ALWilson.com or call 800-526-1188 A. L. WILSON CHEMICAL CO.
“The support from CBS was great. Even before we signed up, they were responsive and flexible in their approach. They have helped our team become more efficient.”
Since 2003, CBS has given me consistent updates and easy to understand tech support, all at a price that our industry can afford. I would recommend CBS, and I have, to anyone who is still wasting their time and money on those over priced POS systems.
Next month’s Clean Show will mark my eighth writing about the textile care industry, and my first ever in Atlanta.
Just like every other edition before it, Clean 2015 promises owners and operators of drycleaning businesses a rare opportunity: the chance to see and inspect the newest high-tech equipment and systems all under the same roof.
year’s attendees (we’ll have much more to report about the host city’s hospitality and tourism in April’s Atlas of Atlanta feature).
The official Clean Show hotels are within walking distance of the convention center, but there will be free shuttles available to transport the weary at the end of a day spent on the show floor covering approximately 195,000 net square feet.
Unlike Las Vegas and New Orleans, which have become frequent Clean Show stops, it’s possible only a small share of the industry recalls the last time the event convened in Atlanta (it was 1987).
A steam system in the Georgia World Congress Center and a vibrant downtown full of attractions await this
Publisher
Charles Thompson 312-361-1680 cthompson@ATMags.com
Editorial Director
Bruce Beggs 312-361-1683 bbeggs@ATMags.com
Production Manager
Roger Napiwocki
National Sales Director
Donald Feinstein 312-361-1682 dfeinstein@ATMags.com
Digital Media Director
Nathan Frerichs 312-361-1681 nfrerichs@ATMags.com
Main: 312-361-1700 Fax: 312-361-1685
Whether you’ll be visiting for business, for pleasure, or both, this Clean 2015 Guide has all the information you’ll need to navigate the April 16-19 event.
Exhibitor descriptions, a show floor map, the schedule of 40-plus hours of educational sessions, and more await you in these pages.
Armed with this special issue, and a pair of comfortable walking shoes, you’ll have everything necessary to make your Atlanta visit a Clean getaway to remember. ADC
American Drycleaner (ISSN 0002-8258) is published monthly except Nov/Dec combined. Subscription prices, payment in advance: U.S., 1 year $39.00; 2 years $73.00. Foreign, 1 year $89.00; 2 years $166.00. Single copies $7.00 for U.S., $14.00 for all other countries. Published by American Trade Magazines LLC, 566 West Lake Street, Suite 420, Chicago, IL 60661. Periodicals postage paid at Chicago, IL and at additional mailing offices.
POSTMASTER, Send changes of address and form 3579 to American Drycleaner, Subscription Dept., 440 Quadrangle Drive, Suite E, Bolingbrook, IL 60440. Volume 81, number 11. Editorial, executive and advertising offices are at 566 West Lake Street, Suite 420, Chicago, IL 60661. Charles Thompson, President and Publisher. American Drycleaner is distributed selectively to: qualified dry cleaning plants and distributors in the United States. The publisher reserves the right to reject any advertising for any reason.
© Copyright AMERICAN TRADE MAGAZINES LLC, 2015. Printed in U.S.A. No part of this publication may be transmitted or reproduced in any form, electronic or mechanical, without written permission from the publisher or his representative. American Drycleaner does not endorse, recommend or guarantee any article, product, service or information found within. Opinions expressed are those of the writers and do not necessarily reflect the views of American Drycleaner or its staff. While precautions have been taken to ensure the accuracy of the magazine’s contents at time of publication, neither the editors, publishers nor its agents can accept responsibility for damages or injury which may arise therefrom.
American Drycleaner, March 2015
More than 41% of dry cleaners responding to February’s American Drycleaner Your Views survey say they are planning to attend Clean 2015 in Atlanta, while another 24.7% are unsure at this point.
Approximately 34% of those responding to the unscientific survey say they will not be attending the biennial event slated for April 16-19 at the Georgia World Congress Center.
Asked about the biggest factor in favor of attending (whether they were personally planning to attend or not), 45.2% of respondents named “exhibits of equipment and supplies.” Roughly 8% listed “networking and socializing” as the chief factor, 6% look to Clean for its “educational sessions,” and 4.8% are most drawn to “combining business and pleasure.” For a sizable portion (35.7%), “It’s all of the above.”
Clean returns to a four-day format after trying out a three-day schedule in 2013. More than half of respondents (52.4%) are “indifferent” about this change, and 38.1% are “OK” with it. Just 9.5% “don’t care for this change.”
Among dry cleaners who do not plan to attend this year’s event, 40.8% “can’t spare the time,” 30.6% “can’t afford the cost,” and 10.2% have “made other plans.” The remaining 18.4% have “other” reasons, some of which include earlier-than-usual show dates, or a belief the event is “geared mostly to industrial” laundering.
Among the six educational sessions being sponsored by the Drycleaning and Laundry Institute (DLI), How to Sell to the #SELFIE Generation is garnering the most pre-show interest among respondents, at 36.6%. Other popular topics based on our survey results are Success = More Than Just Drycleaning (26.8%), Is Great Customer Service Worth It? (11.0%) and Policing Employee Policies (11.0%).
While American Drycleaner’s Your Views survey presents a snapshot of trade audience viewpoints, it should not be considered scientific; percentages may not add up to 100% due to rounding.
Subscribers to American Drycleaner e-mails are invited each month to participate in a brief industry survey they can complete anonymously. The entire trade audience is encouraged to participate. ADC
Professionals from all facets of the textile care industry will convene once again April 16-19 for the biennial World Educational Congress for Laundering and Drycleaning—better known as the Clean Show.
“I’m anxious to see what this time slot in April will do,” says John Riddle, president of Riddle & Associates, the show’s management company.
“Atlanta is a good city, [and] I think people are going to find out a lot of positive things are going on around here.”
In its 38th year, the convention makes a return trip to Atlanta, some 28 years since the city last hosted the show in 1987.
This year’s theme is “One Industry. One Stage.” The Georgia World Congress Center (GWCC) provides the platform.
This will be the third time the GWCC plays host to Clean (it also hosted in 1981), particularly as recent renovations to the center can accommodate the show’s size and unique utility demands.
A new steam system has been installed at the center, covering approximately 125,000 square feet of exhibit
space, according to Riddle & Associates.
“The Clean Show features working equipment and uses more steam than any other trade show in the world,” the company explains, as an equivalent of about 100 neighborhood drycleaning establishments are built on the sprawling exhibit floor.
“[The show takes] the entire textile care industry, from the coin-operated stores to your huge commercial laundries, and everything in between in textile care, [and] we put them all together all on one stage. We’re all here,” says Riddle of the show’s theme.
“I can’t tell you that I see any trends different than what we’ve seen in the past [but] we’ve got some new companies coming and I think we’re going to have a great show,” he adds.
Clean 2015 is set to take place in Building B of the convention center, in halls B2 to B5, with an anticipated total exhibit space encompassing approximately 195,000 net square feet, according to Riddle & Associates.
This year’s show sees another return, as the exhibition reverts to its traditional four-day format, after Clean 2013’s shortened three-day schedule.
Distributors will have exclusive early access to the show floor beginning 8 a.m. on Thursday, April 16, with the show opening to all attendees at 10 a.m. and running until 5 p.m.
Show hours for Friday and Saturday are 9 a.m. to 5 p.m., while Sunday has a shorter schedule: 9 a.m. to 3 p.m.
The 2013 show, hosted by the Morial Convention Center in New Orleans, attracted 10,300 industry professionals, including 1,663 people from 83 countries outside of the United States, according to Riddle & Associates.
Named 112th among 2013 Trade Show News Network’s Top 250 Trade Shows, the Clean Show is the largest textile care exposition in the world that features working equipment, says Riddle & Associates.
The show traces its roots back to the mid-1970s, when industry manufacturers and suppliers found exhibiting shows annually was costly. Interest in consolidating into one biennial industry-wide show was expressed, and as a result, three associations collaborated for a 1975 show they called the Clean Show.
Three additional sponsors joined, eventually forming the World Educational Congress for Laundering and Drycleaning in 1977, giving birth to the Clean Show with which the industry is familiar today.
Current show sponsors include the Association for Linen Management (ALM), Coin Laundry Association (CLA), Drycleaning & Laundry Institute (DLI), Textile Care Allied Trades Association (TCATA), and the Textile Rental Services Association of America (TRSA).
In 1992, the show (which was being managed by the CLA) had grown in size and stature, leading sponsors to seek counsel with professional show management, according to Riddle & Associates, who was then hired to produce Clean ’93.
The move was a “natural fit,” the company says, as John Riddle had worked with the Clean Show’s operations since 1981.
Riddle & Associates explains that, according to Clean Show surveys, 94% of attendees are business owners, executives or managers.
Riddle & Associates anticipates more than 400 exhibitors at this year’s show. At press time, 387 companies were listed on the show’s site. (For a complete listing of exhibitors, turn to page 12.)
The biennial show not only provides an arena for networking and business opportunities, it also presents pro-
American Drycleaner, March 2015
fessionals in the industry this year with more than 40 hours of educational sessions. (See article on page 32 for full details.)
For Riddle, the show’s various educational opportunities is one of the highlights of attending the Clean Show.
“Education is key to the success of anything,” he says. “If you’re in this business, there’s a need for you to be here if you want to be in this business and want to grow.”
Educational opportunities occur not only in the show’s classroom sessions, but on the show floor, as well.
“The largest classroom in this industry is the exhibit floor. You can see things work. You don’t just come up and look at pictures … You can compare [equipment],” says Riddle.
Faced with plenty of exhibits and activities, managing one’s time at the Clean Show can be quite challenging.
To help with this, Riddle & Associates is again offering a Clean Show app for use on all smartphones, “allowing attendees to virtually connect with exhibitors, organize their day and navigate the show floor.”
Those without smartphones can also create an account on the “My Briefcase” feature on the show’s website. Attendees can view and print the show’s floor plan, as well as browse the show’s list of exhibitors and select which companies they’d like to include in their itinerary.
Riddle & Associates has once again established a “Cyber Café” at this year’s show where attendees can check their e-mail.
Attendees can pre-register for the show online and take advantage of the $99 per person fee until March 31. After that date, it will be necessary to register on-site at a cost of $149 per person.
On-site registration hours will be 1-5 p.m. Wednesday, April 15; 7 a.m. to 4:30 p.m. Thursday, April 16; 7:30 a.m. to 4:30 p.m. Friday, April 17; 7:30 a.m. to 4 p.m. Saturday, April 18; and 7:30 a.m. to 2 p.m. Sunday, April 19.
The show is offering special discounted rates at a variety of hotels in downtown Atlanta, but time is short. Reservations for official Clean 2015 hotels can be made on the show’s site through March 13.
For full registration and show information, visit www. cleanshow.com. ADC
Carlo Calma is editor of sister publication American Coin-Op.
“The largest classroom in this industry is the exhibit floor. You can see things work.”
–– John Riddle, Riddle & Associates
Our new generation of Point Of Sale system is designed for both small and larger cleaner stores. DryClean PRO Enterprise (DCPe) is even simpler to use than before. With user friendly screens and menus, DCPe will make your life easy. We offer, promise, and guarantee the best after sales support to our end users. Save time and money and add to your profits by contacting existing clients and reaching out to new clients through DryClean PRO Enterprise’s built in MARKETING and EMAILING functionality. You’ll be able to send Thank You emails to new or Top 100 customers, Customers with overdue inventory, Customers that have not visited you for awhile, Route customers & e-mail coupons to all your customers.
Call us about our new version of Uniform Tracker.
ATLANTA —The following companies and organizations have reserved exhibit space in the Georgia World Congress Center for Clean 2015 as of Feb. 14, according to show manager Riddle & Associates.
The list totals approximately 390 exhibitors at press time; it’s possible that more exhibi tors will be added in the final weeks leading up to the April 16-19 event.
Where available, the descrip tions of products and/or ser vices provided here are general in nature and should not be considered all-inclusive.
Listings are subject to change without notice. Check www.cleanshow.com for any updates.
o
AABS Laundry 2856 Business Solutions
Route accounting, garment tracking and linen management software and systems.
o Absorbcore 3368 Urinal and commode mats.
o ADI American Dawn 820
Textile products for food and beverage, lodging, healthcare and industrial markets.
o Air World Inc. 2506
Pads, covers, mesh net bags and other supplies for dry cleaners and laundries.
o Albatross USA Inc. 3045
Dr ycleaning chemicals and detergents; compressed air equipment; spotting boards and kits; steam generators.
o Alcoa Wheel 418 Products
Aluminum wheels and accessories for the commercial vehicle market.
o Alliance Laundry 1810
Commercial laundry equipment and services under the Huebsch®, IPSO®, Primus®, Speed Queen® and UniMac® brand names.
o Alliant Systems 412
Route accounting software for the textile service industry.
o A.L. Wilson 2606 Chemical Co.
Stain removers and other chemicals for professional dry cleaning and laundry use.
o American Changer 3706
Bill changers, bill breakers, token dispensers, ticket dispensers and card dispensers.
o American Coin-Op 2857
Trade magazine and website for self-service laundry owners.
Consulting and engineering company specializing in commercial laundry consulting, plant layout/design, process mechanical systems, equipment installations, and more.
o American Reusable 534 Textile Association (ARTA)
Trade association promoting awareness of and appreciation for reusable textiles.
o American Textile 521 Systems
Point-of-sale computer software for dry cleaners and coin laundry operators.
o ARCO/Murray 2061 Natl. Construction Co. Design/build contractor focused on the laundry industry.
o ArtiClean Ozone 3143 Laundry Systems Ozone laundry systems.
o ASCO Numatics 1806 Fluid-control and fluid-power products.
2857
Trade magazine and website for drycleaning businesses and suppliers.
o American Dryer 2048 Corp.
Dryers for coin-operated, on-premise and industrial laundry facilities.
o American Laundry 2857
Trade magazine and website for managers and administrators of institutional/on-premise laundries and textile rental companies (commercial, industrial and linen supply).
Bed linen and pillows; terry towels and bath products; sheeting; and miscellaneous textiles and toilet paper.
o American Trade 2857 Magazines
Publisher of American Coin-Op, American Drycleaner, and American Laundry News
o Amethyst 3915 Health mats.
o AMS Products/ 3570 Object Design
Nylon, cotton, mesh, polyester, biohazard and barrier laundry bags.
o Angeline Group 3261 Ltd.
o Association for 533 Linen Management
SPONSOR: Nonprofit educational association for laundry/linen managers from hospitals, hotels, nursing homes, correctional facilities, government institutions, management companies, and commercial laundries.
o Association of 941 Wedding Gown Specialists
Nonprofit trade association for members specializing in wedding gown cleaning, preservation and restoration.
3357
Pads, covers, belts, belting and accessories for feeders, folders and flatwork ironers.
3853
Healthcare and hospitality textiles and other products.
o AquaRecycle 3433 Laundr y-wastewater recycling systems and dryer heat-recycling system.
o ArbelSoft 425
o Automation 3519 Dynamics
Automated sorting, counting and weighing equipment for various laundry applications.
o Autovalet Systems 3676 LLC
Automated uniform and scrubwear dispense and return systems.
o AWOIS 3723
Ozone laundr y systems.
o B&C Technologies 1011
Commercial and industrial washer-extractors, dryers, ironers and finishers, and OEM parts.
o B&G Lieberman 4022 Co. Inc.
Sewing supplies, replacement buttons, sewing machines, boilers, irons and vacuum pressing boards.
o Beck’s Classic 3460
Reusable incontinence care products, including bibs, clothing protectors, underpads, briefs and diapers.
o BeCreative 360 853 Marketing and promotions for dry cleaners.
o Big Bill 606 Flame-Resistant Protective Apparel Workwear apparel for the uniform market.
o bizzie 3777
Dr ycleaning franchise focused on locker delivery service.
o BLC Textiles 3159 Wide variety of imported textiles for the textile rental industry.
o Bobco Systems Inc. 3952
Material-handling systems for laundry operations.
o BOWE Textile 3576 Cleaning GmbH Drycleaning equipment.
o Braun 2232
Batch tunnel washing, conventional washing, material-handling, drying, and finishing equipment.
o Brim Laundry 2548 Machinery Co. Inc.
Washer-extractors, large-capacity dryers, and touchscreen control systems; OEM replacement parts and supplies.
o Brooks-Waterburn 1507 Insurance ser vices for coin laundries.
Bo CACO 3344 Manufacturing Corp.
Coin laundry furnishings, including folding tables, seating, clothes-hanging racks, and custom bulkheads.
o Calderon Textiles 3464 LLC
Commercial linens for the healthcare, hospitality, textile rental and retail markets.
o Caled Chemical 3276
Specialty cleaning products for professional dry cleaners and laundries.
o Card Concepts Inc. 1210
Automated systems for Laundromats to handle cash collections, employee management, equipment service, and store marketing.
o Cart & Supply Inc. 410
o Centurion Medical 855 Products
Soiled-linen collection system and liner recycling program.
o Century Place 4056 Apparel Rental-friendly and direct-sale knit shirts.
o Chandler Machine 4010 USA LLC
Industrial sewing machines for dry cleaners and laundries.
o ChemFree Corp. 1040
Parts washing systems and solvents.
Co Chem-Tainer Ind./ 1032 Maxi-Movers
Laundr y and linen carts, trucks, tables and hampers, and chemical storage tanks.
o Chicago Dryer Co. 1632 Flatwork linen separating, feeding, ironing and folding systems.
o Chief Clean 3360
Commercial janitorial dust mops and wet mops, handles and frames.
o Christeyns Laundry 3665 Technology LLC
Laundry detergents, sanitizers, dosing systems, and water and energy management equipment.
o Church & Dwight 3257 Co. Inc.
Laundry detergents and chemicals.
o Clayton Industries 1256
Steam boilers, feedwater treatment systems, boiler chemicals, and hydro steam cleaners.
o Clean Cycle 3925 Systems Filters, a div. of TQI LLC Lint filtration systems.
o Cleaner Business 525 Systems Point-of-sale software systems for dry cleaners.
o Cleaner’s Supply® 3865 Wide range of dr ycleaning products.
o Clenacorp 3144 Waxes, lubricants, belting, ribbons, guide tapes, pads, covers and aprons for flatwork ironer and folder systems.
o CMV Sharper 2611 Finish Inc.
Commercial cylinder ironers and combination ironer/folder/stackers.
o Coin Laundry 740 Association
SPONSOR: Not-for-profit trade organization representing member coin laundry owners, equipment manufacturers and distributors.
o Colmac Industries 2649 Tunnel finishers; shirt and pant presses; hangering systems; and other products related to the commercial laundry, drycleaning and apparel industries.
o Columbia/ILSA 2532 Machines Corp. Drycleaning machines, metal degreasing machines, and conveyors.
o Commercial Coils 420 Inc. Replacement coils for laundry and drycleaning equipment.
o Compassmax/ 515 Maineline Computer Systems Software and computer systems for dry cleaners.
o Computer 3160 Connections Inc. Point-of-sale/management
computer systems for dry cleaners.
o Computer Software 949 Architects
Software systems for managing route, healthcare, hospitality, garment, and dust control laundries, as well as linen tracking tools for hospitals, hotels and casinos.
o Computer Systems 1207
Software systems for dry cleaning, garment tracking and uniform rental.
o Computype 3945
Heat-seal labels and related equipment.
o Conni 4036
Reusable incontinence management, linen and mattress protection products for hospitals, long-term care and hotels.
o Consolidated 2769 International Corp. Industrial laundr y machines, parts, textiles and supplies.
o Consolidated 2560 Laundry Machinery Industrial dryers, shuttle conveyors, and mat rollers.
o Continental 3111, 3119 Girbau Inc./ Girbau Group
Laundry equipment for vended, onpremise and industrial laundries.
o Cost-Less Parts! 3719 Replacement parts for commercial laundry and drycleaning equipment, focusing on coin laundries.
o Covers Etc. Inc. 3176 Pads and covers for garment-finishing equipment.
o CRDN 3776
Dr ycleaning franchise focused on garment and textile restoration services.
o Dajisoft Inc. 2757
Point-of-sale dr ycleaning software systems.
o Dante Bertoni 2968 S.R.L.
Material-handling products.
o Darman 4051
Manufacturing Co. Inc.
Cloth-roll towel cabinets, paper dispensers, towel-processing equipment, and microfiber products.
o Datamars Inc. 933
Radio-frequency identification (RFID) products for laundry and textile rental applications.
o Davis Packaging 3960
Laundr y packaging equipment and wrapping film.
o DCCS (Dry Cleaning 3941 Computer Systems) Point-of-sale software systems for dry cleaners.
o Dexter Laundry Inc. 1316 Washers, drying tumblers, card systems, and equipment financing.
o Diamond Chemical 1041 Co. Inc.
Laundry detergents, chemicals, dyes, and chemical injection systems.
o Dickies 1055
Occupational Wear Workwear designed for industrial laundries, uniform dealers and ASI distributor industries.
Diversified Plastics 2676
Custom and standard materialhandling carts and plastic storage containers.
o Dow Chemical 2868
Perchloroethylene dr ycleaning solvent and specialty chemicals.
o Doxon Mfg. Co. 1155
Commercial laundr y equipment parts.
Drycleaning & 832 Laundry Institute
SPONSOR: Trade association representing member dry cleaners, launderers and wet cleaners.
Do Duncan Fabricating 506 Co. Inc.
Coin laundry bulkheads and commercial appliance outlet centers.
o
Durable Superior 415 Casters
Casters and wheels.
o
Dynaric Inc. 3168
Non-metallic strapping
and strapping equipment.
o EAM-Mosca Corp. 2860
Polypropylene strapping and strapping systems.
1049
Water heaters, water softeners, and storage tanks.
Small-business financing for Laundromats and drycleaning businesses.
1407
Services
Consulting and engineering services focused on textile rental, institutional and resort laundering.
Eo Ekostar Textiles 3070
o Ellis Corp. 1018
Washer-extractors, tunnel washing system, dryers, ironers, feeders, folders, rail systems, conveyors, system controls, heat exchangers, stack economizers, water heaters and wastewater treatment.
o Ecolab 2732
Laundr y detergents and chemicals, consulting services, dispensing systems, and wastewater treatment.
o EcoTex 1149 Ozone laundr y systems.
o EDRO 1033
Industrial washer-extractors, tumbler dryers, and ozone laundry systems.
o EKM Management 4072
2965
Sheeting, blankets and terry flat goods; incontinence pads and briefs; operating room and surgical linens; and patient and staff apparel, uniforms and lab coats.
o Energenics Corp. 911 Wet- and dry-type lint filters for dryer exhaust, and vacuum systems for lint collectors.
o Ensign Emblem 4040 Emblems, screen-print transfers and direct embroidery for industrial laundries.
o EnviroForensics 3371 Environmental engineering services for the drycleaning industry.
o ERC Wiping 3668 Products Inc.
Cotton wiping cloths, disinfecting wipes, rags, terry towels, paper wipers and spill control products.
o Ergocon Solutions 1355 Towel inspection and packaging system.
o ESD 1432 Payment systems for laundry, vending and amusement industries.
o E-TECH 1542
Monorail and belt conveyor systems; material-handling control systems; and cart dumpers.
o European 2542 Finishing Equipment Tensioning finishers.
o Evercare/Butler 3468 Home Products Lint rollers.
o Everstrong 3957 Commercial Products Flame-retardant fabrics and linens.
o EzProducts 3953 International Inc. Systems for garment labeling, heatsealing, decorating and mending.
spotting, restoration and shirt laundry products.
o Fanafel (Valmet) 1307 Textiles for flatwork feeders, ironers and folders, including feed ribbons, padding and belts.
o Fashion Seal 1042 Healthcare Uniforms and image apparel for the healthcare industry.
o Faultless Starch 3859 Co.
Laundry chemicals, starches, sizings and specialty items.
o Fawn Vendors 2771 Vending machines.
o Felins USA Inc. 3511 Tying, banding and bundling machines and systems.
o Felrap World Inc. 2673 Laundr y wrapping equipment and supplies.
o FH Bonn 3140 Laundr y and drycleaning press pads and covers.
o Fibertech Inc. 3476 Laundr y trucks and carts.
Fo Fike and Fike Inc. 3973 Linen management and route accounting software.
o Firestone Financial 2060 Group
Equipment financing and leasing.
o First Film 2659 Extruding Drycleaning garment bags and film.
o First Preference 3818 Products
Commercial laundry products and single-use laundry products.
o Flexco 1761 Conveyor belt equipment and supplies.
o FLM — Fairfield 2576
Laundry Machinery
Monorail systems, soil-sort systems, lint collection systems, pneumatic conveying systems, automatic loading hoppers, chutes and folding tables.
o F-MATIC Inc. 3966 Odor-control and restroom hygiene products.
o Foltex 3765
o Forenta L.P. 2932 Dr ycleaning and laundry finishing and pressing equipment.
o Foster-Stephens Inc. 943 Wedding gown and garment preservation systems.
equipment/systems.
Go Garment Company 2973 LLC
o Garnier-Thiebaut 2669 Inc.
Table, bed and bath linens for hotels, restaurants and retail stores.
o Gemu Valves 4054 Valves, and measurement and control systems.
o Golden Star Inc. 3742 Dust/wet mops and microfiber cleaning products.
o GreenEarth 3165 Cleaning
Patented liquid silicone-based drycleaning solvents.
o Greenwald 3010 Industries
Coin/card acceptors, metering and security products for self-service laundries.
o G.S. Manufacturing 3807 Material-handling systems, including baskets, bins, carts and racks.
o Fabricare 3849 Management Systems Computer software systems for dry cleaners.
o Fabritec 3465 International Drycleaning, wetcleaning,
o Fimas SRL 3065 Steam cabinets; vacuum, blowing and steam ironing tables; spotting tables; and pressing machines.
o Firbimatic 2940 Dr ycleaning equipment.
o Fujitsu Frontech 3914 North America Radio-frequency identification (RFID) products for laundry/linen applications.
o Fulton Boiler Works 3365 Boilers and related
o Gurtler Industries 3748 Inc. Advanced detergents and specialty chemicals for the commercial laundry industry.
Ho Hamilton 3522 Engineering Inc. Commercial and light industrial
water-heating systems and boilers.
o Hangzhou A-tek 3172 Medical & Textiles Co. Ltd. Reusable healthcare textiles.
o Hans-Joachim 3965 Schneider GmbH Industrial ironing and finishing equipment and supplies.
o Harbor Linen - 2768 A Division of Bed, Bath & Beyond Institutional linens, case goods and apparel for the hospitality, healthcare, cruise line and foodservice industries.
o Harris Pillow 1208 Supply Inc. Pillows and pillowcleaning systems.
o Healthcare Laundry 552 Accreditation Council
Non-profit organization formed to inspect and accredit laundries processing healthcare textiles for hospitals, nursing homes and other healthcare facilities.
o High Mark 3518 Manufacturing Inc. Coin-laundry bulkheads, drain troughs and furniture.
o H-M Company 1148 Drain troughs, lint interceptors and related products.
o HMC Solutions 710
Automated order-assembly system and 24/7 kiosk system
for garment care.
o Hoffman Mint 3607 Laundr y tokens.
o Hoffman/New 2848 Yorker
Drycleaning presses, shirtfinishing equipment, laundry presses, industrial laundry machines and specialty presses.
o Hong Kong 3359 Wells Ltd.
Wire hangers for dry cleaners and uniform rental services.
o HPI Emblem 3958 Patches.
o Hunt Textiles 3556
Bar mops, kitchen/terry/shop towels, napkins, tablecloths, aprons, wet mops, dust mops, paper products, laundry bags and microfiber products.
o Hurst Boiler 3456 Boilers and related systems.
Textile Rental Association (ITRA) Network of independent textile rental companies.
o Indy Hanger 3820 Galvanized hangers.
o Infinite 446, 3977 Creative Enterprises Inc. Electronic message centers and signage.
o Ink Strokes Inc. 2760 Dr ycleaning-resistant heat seal and nylon labels.
o Innovative 411 Management Designs
IT consulting, project management, technical support, data warehousing, and other services.
o Irving Weber 433 Associates (IWA) Insurance services for dry cleaners and Laundromats.
o Italclean Srl 3156 Perchloroethylene and hydrocarbon dr ycleaning machines.
o JP Equipment Inc. 1561 Industrial laundr y equipment sales.
o JS Fiber Co. Inc. 2873 Hospitality and institutional healthcare textiles.
o Kannegiesser USA 2210
KContinuous-batch washers, extraction presses, material-handling systems, shuttles, conveyors, dryers, washer-extractors, linen separators, feeders, ironers, folders and garment finishers.
o Kemco Systems Inc. 1255 Water heaters, heat reclaimers, water recovery/reuse systems and water treatment systems.
o Keycolour Inc. 2477 Industrial laundr y dye products.
o Kibler Chemical 1056 Corp. Industrial water treatment equipment.
Io Ideal Chemical 3815 & Supply Co.
Laundry and industrial chemicals, and textile care supplies.
o Imonex Services 3913 Inc.
Coin acceptors.
o Impreglon Surface 661 Technologies Inc.
o Independent 3169
o ITD Trailers 3857 Custom linen-transport trailers.
o Itsumi USA Inc. 2742 Shirt finishers, laundry presses and rotary dryers.
o Kleen-Tex 3473 Industries Inc. Washable track-control mats.
o Kreussler Inc. 2977 Laundr y, drycleaning and wetcleaning chemicals and detergents.
o James Gutheim 3068 & Associates Management consulting services.
o J.B. Industries Inc. 560
o Jensen USA Inc. 1832 Washing equipment, finishing systems, material-handling systems, and system software and process technology.
o JiangSu Sea-lion 1342 Machinery Group (Corp.)
Washer-extractors, dryers, ironers, and drycleaning, folding and finishing equipment.
o John Ritzenthaler 417 Co.
Chef apparel and other foodservice textiles.
LJo Lac-Mac Limited 3911 Reusable surgical gowns and drapes, and other healthcare apparel.
o Landen Strapping 2776 Corp.
Plastic strapping machines, glue machines and stretch film wrappers, plus related supplies, parts and service.
o Lapauw USA 3756 Flatwork finishing equipment, washer-extractors, garment finishing tunnels, cart washers, and more.
o Laundroworks 2872 Card Systems Card-based payment, control, and monitoring systems for multihousing and vended laundries.
o Laundry Logic LLC 752
Computer software and systems for textile rental.
o LaundryDealer.com 449 Online sales and marketing platform.
o Lavatec Laundry 1513 Technology
Continuous-batch washers, washer-extractors, dryers, flatwork feeders, ironers, folders, stackers, material-handling equipment and mat-processing equipment.
o Leebaw 514 Manufacturing
Material-handling carts, garment carts, shelving units, lift tables and laundry/sling bags.
o Leonard 2248 Automatics
Tunnel finishing equipment, pressing equipment, conveyor products and production management systems.
o LG Electronics 649 Washers and dryers.
o Lochinvar LLC 4011
Energy-efficient boilers, water heaters, and storage tanks.
o Low Cost Mfg. Co. 548 Washer and dryer parts.
o Lyon 657
Lockers, shelving, storage racking and modular drawer cabinets.
o Mainetti Group 4052 Garment hangers.
o Maruso USA Inc. 2869
Plastic hangers, shoulder guards, skirt hangers/clips, and tie holders.
3771
Material-handling systems, including rail systems, conveyors and trolleys.
o Material Imports 2972
Textile products for hospitality, industrial, laundry and institutional customers.
o Maxi Companies 2806
Export management company specializing in commercial and industrial laundry and drycleaning equipment.
o Maximizer 1442
Water heaters, boiler stack economizers, wastewater heat recovery and water reuse systems.
o Maxtex Inc. 3961
Linen products for industrial laundries, and hospitality, resort and healthcare industries.
o Mayfield Group 3245 Advertising Bureau Advertising and marketing services for retail fabricare.
o McClure 532 Industries Inc. Laundry, linen and trash carts; motorized tuggers; cart dumpers; and cart washers.
and plastic film for launderers and dry cleaners.
o Micross 3608 Automation Systems Hardware, control systems and counting systems for commercial laundries.
o Midwest 4057 Specialty Products Disposable towel and wiper products.
o Midwestern 2657 Industries Inc. Wastewater-screening equipment and replacement screens and parts.
o Milliken & Co. 810 Fabrics for tablecloths, napkins, placemats, aprons and tableskirts; dust control products.
o MIP Inc. 2959
Reusable healthcare products, including bed linens, underpads, carts, bags, etc.
o Miura America 510 Boilers and related systems.
o Mobile Computing 754 Corp. Inc. (MCC) Route-delivery software and systems for the linen and textile rental industry.
o MOD (Meese 3548 Orbitron Dunne Co.) Bulk linen and laundry carts.
No National Cleaners 3376 Association Trade association for professional garment/fabric cleaners and suppliers.
o National 1560 Combustion Co. (NATCO) Water-heating systems.
o Navien Inc. 3470
o Newhouse 2877 Specialty Co. Specialty products for the laundry, dry cleaning, hospitality and garment manufacturing industries.
o NIE Insurance 2706 Insurance services for dry cleaners.
o Nilodor Inc. 4013 Air care and odor control products.
o Norchem 3823, 3833 Corp.
Laundry chemicals; chemical dispensing systems; wastewater treatment and recycling systems; and system controllers and software.
o Novozymes A/S 455 Industrial enzymes.
o NuMat Systems 3270 LLC
o M&B Hangers 2623
Wire hangers for dry cleaners and textile rental companies.
o MA Industries Inc. 461 Paper strapping.
o Maestrelli Srl 3356
Dr ycleaning and laundry equipment.
o Magid Glove 4014 & Safety
Work gloves, protective clothing, industrial hygiene, and safety equipment.
o Magline Inc. 4015
Aluminum material-handling equipment.
Mo Medline 2711 Industries Inc. Healthcare textiles.
o Memories Gown 755 Preservation
Wedding dress cleaning, preservation, packaging and shipping services.
o Messe Frankfurt 2772 Inc.
Trade-fair organizer responsible for Texcare exhibitions.
o Metalprogetti 1232 Garment handling and distribution systems.
o Mevo Metzler 3671 GmbH
Wire hangers, paper products,
o Monarch Coin 407 & Security Coin/token chutes, money boxes, locks and keys for coin laundry machines.
o Moonsoft 915 International Microfiber products, cleaning towels, and mop pads and materials.
o Morgan Olson 3733 Aluminum walk-in vans for the textile rental industry.
o Mountville 3811 Mills Inc. Floor mats for uniform and textile rental companies.
o Multimatic 3033 Dr ycleaning machinery, specializing in conventional and alternative solvents.
Rubber-backed floor mats, and mat-processing equipment for the textile services industry.
Oo Omni Apparel 3964 Launderable butcher coats, lab coats, smocks and aprons for the food industry.
o Onnera Group 1448
o Othis USA 2665 Dr ycleaning finishing equipment.
Po P&E Products 3277 Mat-rolling and -storage equipment.
o Parker Boiler Co. 2759 (continued on page
ABS Laundry Business Solutions 2856
Absorbcore 3368
ADI American Dawn 820
Air World 2506
Albatross USA 3045
Alcoa Wheel Products 418
Alliance Laundry Systems 1810
Alliant Systems 412
A.L. Wilson Chemical Co. 2606
American Changer 3706
American Coin-Op 2857
American Drycleaner 2857
American Dryer Corp. 2048
American Laundry News 2857
American Laundry Products 3357
American Laundry Systems 3853
American Reusable Textile 534
Association (ARTA)
American Textile Systems 521
American Trade Magazines 2857
Amethyst 3915
AMS Products/Object Design 3570
Angeline Group 3261
AquaRecycle 3433
ArbelSoft 425
ARCO/Murray National 2061
Construction Co.
ArtiClean Ozone Laundry Systems 3143
ASCO Numatics 1806
Association for Linen Management 533
Association of Wedding Gown 941
Specialists
Automation Dynamics 3519
Autovalet Systems 3676
AWOIS 3723
B&C Technologies 1011
B&G Lieberman Co. 4022
Beck’s Classic 3460
BeCreative 360 853
Big Bill Flame-Resistant 606
Protective Apparel
bizzie 3777
BLC Textiles 3159
Bobco Systems 3952
BOWE Textile Cleaning 3576 Braun 2232
Brim Laundry Machinery Co. 2548
Brooks-Waterburn 1507
CACO Manufacturing Corp. 3344
Calderon Textiles 3464
Caled Chemical 3276
Card Concepts 1210
Cart & Supply 410
Centurion Medical Products 855
Century Place Apparel 4056
Chandler Machine USA 4010
ChemFree Corp. 1040
Chem-Tainer Ind./Maxi-Movers 1032
Chicago Dryer Co. 1632
Chief Clean 3360
Christeyns Laundry Technology 3665
Church & Dwight Co. 3257
Clayton Industries 1256
Clean Cycle Systems Filters 3925
Cleaner Business Systems 525
Cleaner’s Supply® 3865
Clenacorp 3144
CMV Sharper Finish 2611
Coin Laundry Association 740
Colmac Industries 2649
Columbia/ILSA Machines Corp. 2532
Commercial Coils 420
Compassmax/Maineline 515
Computer Systems
Computer Connections 3160
Computer Software Architects 949
Computer Systems 1207
Computype 3945
Conni 4036
Consolidated International Corp. 2769
Consolidated Laundry Machinery 2560 Continental Girbau/ 3111, 3119
Girbau Group
Cost-Less Parts! 3719
Covers Etc. 3176
CRDN 3776
Dajisoft 2757
Dante Bertoni 2968
Darman Manufacturing Co. 4051
Datamars 933
Davis Packaging 3960
DCCS (Dry Cleaning Computer Systems) 3941
Dexter Laundry 1316
Diamond Chemical Co. 1041
Dickies Occupational Wear 1055
Diversified Plastics 2676
Dow Chemical 2868
Doxon Mfg. Co. 1155
Drycleaning & Laundry Institute 832
Duncan Fabricating Co. 506
Durable Superior Casters 415
Dynaric 3168
EAM-Mosca Corp. 2860
East Coast Water Systems 1049
Eastern Funding 1407
Ecolab 2732
EcoTex 1149
EDRO 1033
EKM Management Services 4072
Ekostar Textiles 3070
Ellis Corp. 1018
Encompass Group 2965
Energenics Corp. 911
Ensign Emblem 4040
EnviroForensics 3371
ERC Wiping Products 3668
Ergocon Solutions 1355
ESD 1432
E-TECH 1542
European Finishing Equipment 2542
Evercare/Butler Home Products 3468
Everstrong Commercial Products 3957
EzProducts International 3953
Fabricare Management Systems 3849
Fabritec International 3465
Fanafel (Valmet) 1307
Fashion Seal Healthcare 1042
Faultless Starch Co. 3859
Fawn Vendors 2771
Felins USA 3511
Felrap World 2673
FH Bonn 3140
Fibertech 3476
Fike and Fike 3973
Fimas 3065
Firbimatic 2940
Firestone Financial Corp. 2060
First Film Extruding 2659
First Preference Products 3818
Flexco 1761
FLM — Fairfield Laundry 2576
Machinery
F-MATIC 3966
Foltex 3765
Forenta 2932
Foster-Stephens 943
Fujitsu Frontech North America 3914
Fulton Boiler Works 3365
Garment Company 2973
Garnier-Thiebaut 2669
Gemu Valves 4054
Golden Star 3742
GreenEarth Cleaning 3165
Greenwald Industries 3010
G.S. Manufacturing 3807
Gurtler Industries 3748
Hamilton Engineering 3522
Hangzhou A-tek Medical & 3172 Textiles Co.
Hans-Joachim Schneider 3965
Harbor Linen 2768
Harris Pillow Supply 1208
Healthcare Laundry Accreditation 552 Council
High Mark Manufacturing 3518
H-M Company 1148
HMC Solutions 710
Hoffman Mint 3607
Hoffman/New Yorker 2848
Hong Kong Wells 3359
HPI Emblem 3958
Hunt Textiles 3556
Hurst Boiler 3456
Ideal Chemical & Supply Co. 3815
Imonex Services 3913
Impreglon Surface Technologies 661
Independent Textile Rental 3169
Association (ITRA)
Indy Hanger 3820
Infinite Creative Enterprises 446, 3977
Ink Strokes 2760
Innovative Management Designs 411
Irving Weber Associates (IWA) 433
Italclean 3156
ITD Trailers 3857
Itsumi USA 2742
James Gutheim & Associates 3068
J.B. Industries 560
Jensen USA 1832
JiangSu Sea-lion Machinery Group 1342
John Ritzenthaler Co. 417
JP Equipment 1561
JS Fiber Co. 2873
Kannegiesser USA 2210
Kemco Systems 1255
Keycolour 2477
Kibler Chemical Corp. 1056
Kleen-Tex Industries 3473
Kreussler 2977
laundry operations.
control industries.
Steam boilers and indirectfired water heaters.
o Pellerin 1749, 2058 Milnor
Washer-extractors, automated tunnel washing systems, apparel processing machinery, dryers, material-handling systems, and laundry computer networks.
o Penco Products 3564 Inc.
Garment lockers, hygiene products and storage products for textile and linen rental.
o Penn Emblem Co. 3558 Emblems, and ID labeling and mending equipment.
o Pepin Mfg. Inc. 860 Lint removers.
o Performance 706 Matters
Consulting services for textile rental service companies.
o Phoenix Scale Co. 1014 Linen-processing and -tracking computer software.
o Phoenix Textile 2956 Corp.
Textile products and services for nursing homes and hospitals.
o Pinnacle Textile 1249 Industries LLC Uniforms, aprons, table linens and related products.
o Plexus Industries 3645
Commercial laundr y bags, slings and cart covers.
o Point-of-Rental 2871
o Pony S.p.A. 2765
Garment finishing and pressing systems.
o Positek RFID L.P. 3525
RFID-enabled sorting and tracking software and systems for the textile rental industry.
o Powerhouse 1461 Equipment Boilers.
o PSP Industrial 2678 Laundry Equipment Turnkey solutions for
o PurClean/PurWater 3243 Water treatment equipment and systems.
o QuickSort 3817
QAutomated assembly systems for dry cleaners.
o Quietaire Cooling 1360 Inc.
Portable evaporative coolers.
o R&B Wire 3418 Products Inc.
RLaundry and utility carts and trucks, wire shelving, hampers, garment racks and other materialhandling products.
o RealStar USA 2865
Dr ycleaning machines using perchloroethylene, hydrocarbon, SolvonK4, GreenEarth, Rynex and other alternative solvents.
o Reed Mfg. Co. 2307 Workwear and uniforms.
o ReflectiveStripe. 952 com/Block Bindings & Interlinings
Custom reflective striping for workwear.
o Rema Dri-Vac Corp. 3041
Air vacuum units, boiler feed systems, blow-off separators, boiler feed pumps, storage tanks and condensate systems.
o Rennco LLC 3457
Laundr y bagging and packaging equipment.
o Renzacci SPA 3549
Dr ycleaning machines, washerextractors, dryers and wetcleaning machines.
o Riegel Div. Mount 3271
Vernon Mills Inc.
Table linens, infant bedding products, hospitality sheeting and towels.
o R.L. Williams Co. 4060 Restroom products for the uniform, linen rental and dust
Drycleaner,
o Rotational 3469 Molding Inc.
Bulk linen trucks, exchange trucks, poly bushel trucks, extractor trucks and low-boy washroom trucks.
o Rowe Bill Changers 852
Money-changing equipment.
Vinyl and canvas carts in various styles.
Laundr y packaging.
o Service Textiles 3369 LLC
Wholesale textiles for distributors, healthcare laundries, hospitals and nursing homes.
o Setomatic Systems 1143 - SpyderWash
Electronic payment acceptance technology, and coin meters.
3571
o Royal Blue Textiles 2960
Importer of institutional linens for the textile rental, commercial, healthcare and hospitality laundries.
o R.R. Street & Co. 3265 Inc.
Drycleaning process additives, stain-removal agents and filtration products.
o R.W. Martin 1052 & Sons Inc.
Buyer and seller of single pieces of laundry equipment, complete processing lines, and entire processing plants.
o Ryco Conveyors Inc. 1858 Design, sales and installation of material-handling systems.
o SewingMachine. 3970 com Sewing and embroidery equipment and supplies.
o Shanghai Sailstar 3876 Machinery Group
o Sharp Packaging 555 Systems Bagging systems.
o Sierra Hygiene 2969 Products
Turnkey paper programs for textile rental industry.
o Sigma Garment 954 Films Garment film and flexible packaging.
o Sigmatex-Lanier 714 Textiles Wide range of textile products for the linen supply, healthcare and hospitality industries.
o S. Thomas & 553 Associates Inc.
o San-Ai Industries 1458 Inc.
Laundry/drycleaning supplies and equipment.
o Sankosha USA Inc. 2919 Garment-pressing equipment.
o SanMar 3411
Industrial workwear and wholesale imprintable apparel.
o Sealed Air Corp. 3565 Laundr y/linen wrapping systems.
o SEITZ Inc. 3949 Chemical additives for dry cleaners and laundries; powder and liquid detergents; and cleaning products.
o Sejong DNS 556
So Simple Route 953 Accounting
o SNA 3373 Manufacturing LLC Foam hanger covers and shoulder guards.
o Softrol Systems 3711 Inc.
System controls and management information solutions for the automation of industrial uniform and textile laundry facilities.
o Sonicaire 1808 Cleaning and cooling fans for laundries and drycleaning plants.
o Southwest 2756 Laundry Equipment Commercial laundry equipment and parts.
o Spartan Chemical 3841 Co.
While other solvents have come and gone, our innovative cleaning process has been scientifically proven to deliver better cleaning results, year after year. 1,700 dry cleaners in over 40 countries have already experienced the GreenEarth difference, which translates to millions of customers who see, smell and feel the GreenEarth difference.
Better Cleaning: GreenEarth Cleaning uses sustainable silicone (liquid sand) to keep clothes looking newer, longer, with no harsh chemicals, no odor and no hazardous waste.
Expert operational guidance produces truly sustainable results through the lowest utility costs in fabric care.
Seamless Transition: Reinvigorate Your Brand:
Our marketing tools are designed and proven to leverage the GreenEarth difference and separate your business from the competition. Science proves it, customers love it!
Learn more at greenearthcleaning.com
Laundry detergents and chemicals.
o Spindle 3249
Software solutions for tracking laundry productivity and utility usage.
o SPOT Business 749 Systems
Computer software and systems for drycleaning operations management.
o Springpress 1306
Spring padding, waxes and cleaners for ironers.
o SRS Conveyors 1206
Material-handling equipment for the uniform and laundry industry.
o Standard Change- 3917 Makers Inc./BCC Payments LLC
Currency change machines and electronic payment acceptance.
o Standard Textile 2349 Healthcare, hospitality and institutional textiles and apparel, and linen management services.
o Storms Industries 3171 Inc.
Flatwork ironer textiles and supplies, cleaners and belting; sling bags; cart covers; filtration and dust-control products.
o Strapack Inc. 3643 Plastic-strapping machines.
o Streamline Solutions 849
Soiled-linen bags, cart covers, cart liners, hamper stands, laundry wrap, and other types of bags.
o Stry-Lenkoff Co. 956
Stock tags, labels and business forms for the laundry/drycleaning industry.
o Superior Boiler 3572 Works Inc.
Boilers and boiler room equipment.
o Superior Sewing 1154 Machine & Supply LLC
Wide variety of sewing and garment care supplies.
Corp. Parts, equipment and rebuild services for commercial laundries.
o TBR Associates 3552 Business consulting firm focused on textile services, commercial laundry and manufacturing industries.
o TCF Equipment 4012 Finance Inc. Drycleaning equipment financing.
o Tecni-Quip 3925 Material-handling carts for healthcare facilities.
o Texas Automation 1349 Products Inc.
Heat-sealing machines and accessories.
o Textile Care Allied 541 Trades Association
SPONSOR: Trade association representing manufacturers and distributors of laundry and drycleaning equipment and supplies.
o Textile Rental 840 Services Association of America
SPONSOR: Trade association representing the textile services industry.
o Textile 1261 Technologies Computer software systems for the textile rental industry.
o The DECC Co. 1107 Abrasion-resistant release coating for dryer panels.
o The Green 2907 Garmento
Reusable garment and laundry bags.
o The Route Pros 753 Route development/ management consultants.
o The LaundryList. 1706 com Inc.
New and used laundry equipment, machines and parts; plant installation services; energy and wastewater consultation.
o Thermal 1960 Engineering of Arizona
water heaters, storage tanks, pumping systems, ceramic filtration systems and other products.
o Thermopatch 4019 Textile and garment identification products and systems.
o 3M Body 1156 Protection Solutions Reflective materials for uniforms, transfers, etc.
o Tiffany Outdoor 3268 Advertising specialties and marketing services.
o Time in a Box 607 Preservation Co. Bridal, military and christening gown preservation enclosures.
o Tingue, Brown 3448 & Co.
Finishing equipment products and dedicated services for commercial laundries.
o Tolkar - Smartex 1549 Makina A.S. Textile processing and commercial laundry machines.
o Trevil America Inc. 2568 Tensioning equipment, wet cleaning systems, shirt-finishing equipment and laundry washers, dryers and flatwork ironers.
o Tri-State Technical 1361 Services/TLC Equipment
Commercial laundry equipment and parts.
o Turn-Key Industrial 4025 Engineering Services
Facility planning/design, project management, process improvement and building construction services for resort, medical, hospitality and industrial laundry providers.
o Union Drycleaning 2949 Products
Dr ycleaning equipment for use with perchloroethylene, hydrocarbon and alternative solvents.
o UniSec Div. of 2355 New York Machinery Drycleaning machines.
o United Brass 3069 Works Inc. Pressing machine replacement parts, and steam valves, traps and regulators.
o United Textile 4044 Distribution Inc.
Dust control products, table linen, bed linen, towels, hangers, aprons and other products.
o United Wire 2609 Hanger Corp.
Wire and plastic hangers and related paper products for the uniform rental, drycleaning, laundry and apparel industries.
o Unitex 3442 International Inc. Microfiber products, towels, table linen, napery, fender/seat covers, sheets, patient wear and other textile products.
o U.N.X. 3333 Incorporated Commercial laundry chemical products and dispensing systems for domestic and international markets.
o Utilimaster 720 Walk-in vans, parcel delivery vans and truck bodies.
Vo Vega Systems 1119 Washer-extractors; flatwork feeders, ironers, folders and stackers; continuous batch washing systems; and more.
Uo Vend-Rite 3424 Mfg. Co. Inc. Soap venders, bag venders, snack/drink venders, coin laundry signs, plastic laundry bags and drop-off bags.
o Venus Group 3533 Tablecloths, napkins, aprons, sheets, towels, hospital linens and chef apparel.
o Talley Machinery 3452
Wastewater heat reclaimers, heatrecovery systems, shaker screens,
o Unipress Corp. 2719 Shirt-pressing and finishing equipment for drycleaning, commercial and industrial applications.
o Veolia Water 756 Technologies
o VF Imagewear Inc. 511
Industrial workwear, hospitality garments, corporate apparel and protective apparel; managed uniform programs.
o Vintex Inc. 2876
Launderable barrier fabrics.
o Voltea 549
Water/wastewater treatment.
o Wasatch Co. 3071
Textile products for institutional, hospitality, food service and healthcare industries.
o Wash Club NYC LLC 760
o Wash Tech 4059
Heavy-duty washers and dryers for industrial laundries and dry cleaners.
o WaterSoluble 856 Bags.com
Water-soluble bags for
laundry applications.
o Webb & Son 3543 Sewing Machine Sales Inc.
Industrial sewing equipment, parts, workroom supplies and custom clamping for automated machines.
Wo Wedding Gown 3873 Preservation Co. Gown preservation services.
o WeiserMazars LLP 3269
Accounting and consulting services for textile rental companies.
o Weishi Machinery/ 3148 Fuji Star Dryers, washer-extractors, steam equipment, drycleaning equipment and pressing equipment and supplies.
o Welspun 3976 Hospitality
o Wesvic Systems 1508
Automated system for tracking productivity of drycleaning and laundry equipment operators.
o WGS World’s 442 Global Source Hospital textiles.
o White Conveyors 3933 Inc.
Automated garment-sorting, storage and retrieval systems.
o Wholesale Textiles 3972 Inc.
o Winona Paper 416
o Woodbine Products 3343 Co. Hand-care products.
o Workrite Uniform 1161 Flame-resistant work apparel.
o World Emblem 3545 International Custom embroidered, sublimated and screen-printed emblems.
o WSI 1311
Chemicals and detergents; dispensing systems; wastewater treatment.
Xo Xeros Inc. 421 Commercial laundr y system that utilizes polymer beads.
Yo YAC Japan 2615 Laundr y and drycleaning equipment.
o Yamamoto 2811 Japan Inc.
Washer-extractors, combination washer/extractor/dryers, and small-piece folders.
Between visits to the Clean Show’s extensive exhibit floor, those attending the April 16-19 event will have the opportunity to attend educational sessions targeting the unique issues of their industry segments, as well as some broader general sessions that offer strategies on improving operations, engaging workers and increasing business, among others.
Access to the educational sessions is included in conference registration, and is not dependent on association affiliation. All morning sessions will be staged on level three of the
THURSDAY, APRIL 16
8-9 a.m. — Communicating in a Crisis: A Practical Guide to Protecting Your Reputation, sponsored by the Textile Rental Services Association (TRSA)
Protect the reputation of your business. Learn to communicate and plan properly during crises, such as accidents, natural disasters and public health scares. Gain practical advice on building an effective crisis response plan, as well as communicating with the media and customers, and managing social media.
8-9:45 a.m. — Going Hi-Tech: Emerging Textile Technologies, sponsored by the Association for Linen Management (ALM).
Join this discussion on processing, validating performance and the environmental impact of antimicrobial textiles, such as MJS spun-poly sheeting and microfibers. The advantages and disadvantages of the new products, as well as an analysis of their cost benefit, will be discussed.
8:30-9:45 a.m. — Is Great Customer Service Worth It? sponsored by the Drycleaning & Laundry Institute (DLI).
How can great customer service affect your bottom line? A secret-shopping CEO shares insight and data from our industry
Georgia World Congress Center. Afternoon educational sessions will be located at the end of the main aisle of the exhibit floor in the Sponsor Education Theater, just beyond the sponsor pavilion.
Educational sessions will take place between 8 a.m. and 10 a.m., and between 1 p.m. and 3:30 p.m., daily Thursday through Saturday. On Sunday, the show’s final day, sessions will take place only in the morning.
Here are brief session descriptions from Clean Show organizer Riddle & Associates:
about identifying weaknesses and rewarding excellence.
8:30-10 a.m. — Flip My Laundry: Best Practices for Remodeling Laundries, sponsored by the Coin Laundry Association (CLA).
Identify ways to design a store to maximize revenue per square foot in this session about remodeling a self-service laundry. Remodeling success stories will be shared and will include a discussion of how these projects overcame design issues.
9-10 a.m. — Industry Analysis: Domestic Trends and Emerging Markets, sponsored by TRSA.
A discussion of the textile services industry and its potential growth in light of economic trends and employment in key customer markets.
1-2 p.m. — TRSA Clean Green and Hygienically Clean Certification Programs: Quantifying Your Commitment to Cleanliness and Sustainability, sponsored by TRSA.
Nearly 50 companies have earned TRSA’s Clean Green certification, and more than 45 facilities have earned TRSA’s Hygienically Clean designations. These certifications are independent, quantitative, and conducted by a third party, and are growing quickly to become the most recognized
international certification programs for textile service operators, TRSA says. Learn how your company can meet these rigorous standards and quantifiable measurements, including inspections and testing.
2:30-3:30 p.m. — The HighTech Laundromat: Streamlining Store Operations Through Technology, sponsored by CLA.
Through the use of technology designed to streamline store operations and improve efficiencies, owners can now monitor stores from afar, lock doors remotely, and track revenue through a mobile device. In this session, store owners share their high-tech experiences.
8-9 a.m. — All Things Google: Tips and Secrets to Your Best Marketing Resource, sponsored by CLA.
Learn how to avoid an advertising agency and reach potential customers through a cheap and easy medium—Google. This session will include a discussion of some of Google’s best tools for laundries, and will identify ways to leverage those resources to reach your customers.
8-9:45 a.m. — The 4-1-1 on Equipment Acquisition, sponsored by ALM. (continued)
Goals play an important role in planning for capital investment in equipment. Once the goals are in place, acquiring the equip ment is the next step. The RFP (Request for Pricing) process will assure that you are purchasing the right piece of equipment to meet your productivity and financial goals. Industry veteran Charles Berge will pres ent a discussion on ways to approach this important decision.
u 8:30-9:45 a.m. — How to Sell to the #SELFIE Generation, sponsored by DLI.
Behavioral psychology can lend some insight into why customers switch compa nies and make purchases. Learn how to apply this science to selling dry cleaning to an Internet-connected generation.
u 9-10 a.m. — Healthcare Textiles in 2015 and Beyond: Strategies to Maximize Sales of Reusables, spon sored by the American Reusable Textile Association (ARTA).
In order to maximize the sales of reus ables in the rapidly changing healthcare environment, operators will have to market smarter and more aggressively. This ses sion offers strategies to secure profitability in this segment.
u 9-10 a.m. — Maximum Performance: Getting the Most from Your Laundry Attendants, sponsored by CLA.
Clear goals and processes will help your laundry attendants and your business reach their full potential and be competi tive. Join this discussion of methods of training attendants on store cleaning, equipment maintenance, customer service, money handling, sales and more.
u 1-2 p.m. — Boiler Alert: Save Money on this Massive Expense, sponsored by DLI.
Make sure your boiler is working with you and not against you. In this session, find out how to get more work out of less energy and lower your insurance costs.
u 2:30-3:30 p.m. — Starting a Laundry on a Shoestring, sponsored by ALM.
This session will cover the issues you need to consider before starting a com mercial laundry business or expanding an existing one. ALM’s panel of experts will discuss rental textiles vs. processing customers’ goods, selecting equipment, regulatory requirements and more.
SATURDAY, APRIL 18
u 8-9 a.m. — Tips for Entering the Commercial Laundry Industry, spon sored by TRSA.
Industry experts present on what it takes to enter the commercial linen and uniform rental market, as well as the pros and cons
that come along with tackling an unfamiliar market. The discussion will cover the best place to start this type of transition, how the industry works and what competition already exists, to help you determine if it’s the right move for you.
u 8-9 a.m. — Your Guide to Wash, Dry, Fold: Folding, Packaging and Presentation Techniques, sponsored by CLA.
This session will demonstrate how to generate additional income and capture a different slice of the customer base by practicing good methods to fold, package and present laundry so that it is not only clean, but looks great, too.
u 8-9:45 a.m. — Industry Chat, sponsored by ALM.
ALM’s popular panel chat will feature a discussion by decision-makers responsible for selecting textiles and textile care ser vices for various markets.
u 8:30-9:45 a.m. — Success = More Than Just Drycleaning, sponsored by DLI.
Succeeding in today’s market means cleaning more than suits and formalwear. Hear from fellow industry professionals on how to expand services to accommodate customers’ changing needs.
u 9-10 a.m. — Commercial Accounts Marketing Toolkit, sponsored by CLA.
Drycleaner,
For those considering adding com mercial accounts to their wash/dry/fold operations, and those wanting to grow that segment, this session tackles what’s needed to pursue those accounts, and identifies strategies for growing a commer cial account base.
u 9-10 a.m. — Fostering Communication, Ensuring Engagement, sponsored by TRSA.
Learn more about a top-down and bot tom-up communication approach, where employees voice their concerns and ideas and report incidents and near-misses.
u 9-10 a.m. — How to Convert O.R. Clients from Disposables to Reusable Surgical Textiles—Deliver Value to Keep Them, sponsored by ARTA.
Learn specific steps required to convert healthcare clients from disposable to reus able surgical textiles, and how to retain these clients. The discussion will be led by an operator and supplier.
u 1-2 p.m. — OSHA Compliance: Identifying Laundry’s Most Cited Violations, sponsored by TRSA.
A top OSHA administrator from 20062008 has helped TRSA develop consensus proposals for overcoming the most difficult obstacles the industry faces in eliminating injuries and illnesses. In this session, hear OSHA’s top 20 most frequently cited stan
dards and the top 25 “low-hanging fruit” violations.
u 2:30-3:30 p.m. — Problem Garment Parade, sponsored by DLI.
Preventing claims not only stops pay outs, it increases customer confidence in your business. DLI’s educators will help attendees learn how to identify and prevent common claim-causing garment problems.
SUNDAY, APRIL 19
u 8-9 a.m. — Acquisition Financing: Today’s Options for Your Next Store Purchase, sponsored by CLA.
Purchasing a self-service laundry requires a large initial capital investment, and financing a laundry often differs from more traditional financing models. This session will discuss information needed to obtain financing and how to avoid potential financing pitfalls.
u 8-9:45 a.m. — Textile Effectiveness from a Clinician Point of View, spon sored by ALM.
With changes in reimbursement empha sizing patient satisfaction and outcomes, understanding the nursing perspective regarding patient care linen is key to the delivery of quality textiles. Listen to a dis cussion on new technology and its impact on HACs and HAIs.
u 8:30-9:45 a.m. — Getting the Most
Out of Your Association Membership, sponsored by TRSA.
Learn how to maximize the resources available to you through your association membership. Get tips on how to be more engaged, and to use your membership to grow your network, increase your brand recognition and build business opportuni ties to get a higher return on your invest ment.
u 8:30-9:45 a.m. — Policing Employee Policies, sponsored by DLI.
The way employees look and behave is changing—are your company policies current with today’s employment issues? Learn how to protect your business from a lawsuit filed by a disgruntled employee.
u 9-10 a.m. — Top 10 Secrets
Potential Laundry Owners Should Know, sponsored by CLA.
Learn from others’ experiences and avoid potential pitfalls that could cost you hundreds of thousands of dollars. Michael Sokolowski, former multi-store owner and current CLA executive, counts down the top 10 secrets that you need to know before purchasing or building a self-service laundry. ADC
Many dry cleaners keep their operational details private and don’t readily share with others. This may lead to a cozy comfort zone or to a feeling of isolation and loneliness.
Let’s examine the benefits and risks of an owner of a dry cleaner being willing to open up to other cleaners in an effort to improve their own operation.
Comparisons of industrywide results contrasted with the results of companies that network consistently show that networkers have better results, especially in profit performance, where it really counts for the enterprise.
First, let’s examine the rewards of sharing information with a network and then we’ll follow with the risks.
In the spirit of full disclosure, Methods for Management is fully engaged in the business of consulting and particularly in facilitating noncompeting owner peer management groups. However, there are multiple consultants of this type available inside and outside of the industry, and your associations all offer valuable networking opportunities as well.
The comfort of knowing that others are facing the same challenges and opportunities that you encounter provides the encouragement to move forward. A network of peers relieves the stress of facing every decision and obstacle alone in the isolation of a small-business, entrepreneurial environment.
Reviewing actual results and comparing them against the group averages and benchmarks opens the discussion on how the benchmark companies achieved their better results and higher profits. Sharing the various approaches to a process or procedure can help fine-tune implementation to improve efficiencies and profits.
This insider information can lead to success in less time and to a lower expenditure of resources invested in a slow and costly process of reinventing the wheel through trial and error.
When the question is cutting-edge innovation, group members can each test different innovations and share
the results so they don’t all have to invest in trying all the options. They individually may choose to reinvent the wheel on a unique opportunity as a test for the benefit of their own company and also for the group, and then mutually capitalize on each other’s successes by copying the lucrative test results.
In summary, this process of sharing can provide:
• Exchange of new ideas and methods (both what has worked and what has not)
• Management tools for improved effectiveness and profitability
• Detailed operational knowledge
• Group operating average, benchmarks, and best practices
• Analysis of variances in results
• Motivation and encouragement to improve
• A framework for development
• Peer support and advice
• Accountability
• Management development and coaching for both owners and their teams
• Identification of trends early in the life cycle
• Objective identification of strengths and weaknesses
• Recommendations for your implementation from supportive peers
• Peer camaraderie and interaction
• A disciplined framework in which to address your interests, concerns and results
Degrees of sharing can range from simple socializing at industry meetings with little or no detailed operational information discussed to intermediate involvement that comes from brainstorming at conferences, either local, national or international. Moving further along the continuum, there are ongoing management groups that meet regularly to share and analyze operational results in a non-competing group environment.
Whatever the level of networking, participants are positive in their feedback about the benefits gained.
You probably believe that your business is exceptionally unique. Whatever your distinction, you may be hesitant to share your “secrets” to success with other owners
for fear of strengthening a current or potential competitor who might copy you and infringe on your success.
Take a moment and realistically ponder the question: “What trade secrets can a cleaner conceal that are not easily visible or ascertainable to a curious competitor?”
If you still believe that your individual competitive advantages are top-secret, that concern can be addressed by networking with broader, more geographically diverse groups of non-competing owners. They are likely to hold your information in confidence, as a reciprocal sharing of information is critical to both of you.
Another question to ponder: “What aspects of your superior operation are highly visible to anyone in the market?” Perhaps your vans are distinctive, you have the best parking, you offer the customer convenience of a drive-through, pick-up and delivery or 24/7 access. So why have competitors not already copied you?
The risk of most cleaners in your market copying your innovations are relatively low because it takes planning, hard work, follow-through and/or a required investment in time, capital, people or other crucial resources. Most business owners are happy with the status quo or are too burned out to make the effort.
One of the highest hurdles to networking is that, initially, owners are reluctant to share because they don’t want to disclose their financial or operating results. This can be avoided completely, depending upon the event chosen for participation. It can also be delayed until a comfort level is reached within the chosen group.
Whatever level of networking is chosen, shared knowl edge is an efficient path forward, and for this reason there will always be market leaders who take a proactive ap proach, network, interact, improve and innovate.
There will also always be another larger group of cleaners that will continue operating as they always have, hoping for better results and complaining about the death of the industry, the negative effects of the current economy or some other factor that is “not their fault.”
The poorest-run of these competitors are likely to be forced out of business through attrition or acquisition. The rest will trudge along hoping for the best and that outside factors and influences will improve their results.
Being one of these disappearing cleaners is a risk of not networking.
ADC
Diana Vollmer is managing director at Methods for Man agement (MfM) Inc., which has served the drycleaning and laundry industry with affordable management expertise for improved profitability since 1953. For assistance in deter mining beneficial networking opportunities with other owners or for your management team with its peers, contact Vollmer at dvollmer@mfmi.com or 415-577-6544.
Dry cleaners will face new problems avoiding unions because the National Labor Relations Board (NLRB) recently issued “quickie election” rules for representation elections to take effect April 14.
These rules will cut the time between the filing of an election petition and the election to 10 to 15 days from today’s median of 38 days. This means cleaning establishments will have little time to campaign to persuade their employees to vote against unionization.
Here are the most important new rules, their practical results, and what astute dry cleaners are doing to avoid union elections entirely:
Management must give the NLRB the names, job titles, shifts, phone numbers, and home and e-mail addresses of workers within two days of notification of a union organizing petition.
Since most elections occur in small companies—the median size of voting units in elections is now about 25 employees—the business owner faces an almost impossible set of tasks.
The first requires a small cleaner’s “human resources department”—sometimes just a clerk who does the weekly payroll—to scramble to put together the required information. Personnel files sometimes do not
contain accurate home addresses because workers often move and don’t report their new ones. Failure to give the NLRB an accurate list of addresses could prompt an “Unfair Labor Charge.”
This early list gives organizers more time to phone more employees, make home visits or e-mail them to further their unionizing efforts. Today, it is unclear whether the NLRB wants workers’ home or work e-mail addresses. If the latter, that raises new issues due to the NLRB’s new efforts to restrict companies from policing what workers say on their internal e-mail systems.
Management must file with the local NLRB office a complete “statement of position”—the company’s take covering all potential election issues: who is or isn’t a supervisor under NLRB rules, who should vote, the date and time of the election, etc.—within seven days of the filing of a petition.
Since the business owner often wears multiple hats, has no ‘labor lawyer’ on speed dial, and doesn’t know what a statement of position is, he often phones his own personal attorney for help.
This attorney may have little experience in labor matters. Some call back, telling the bewildered owner to find a labor lawyer. Others buy a do-it-yourself book with a “cookbook” plan for running elections. Finding an
experienced labor lawyer can take another day or two.
Then, they meet to discuss the cleaner’s situation, asking themselves why workers might want a union, brainstorming what to do, and then composing a statement of position. This does not happen instantaneously. Meanwhile, the NLRB’s clock is ticking.
Most knowledgeable labor lawyers are conservative and want to protect their bewildered clients. So they no doubt will file a lengthy statement raising every possible question imaginable. They know that under the NLRB’s new rules, if a question or issue is not raised in the initial statement, it cannot be raised in any later proceedings.
Rather than speeding elections, this delays them, as hearing officers sort through all the “boilerplate” the attorneys have raised.
While all this is going on, the worried owner must meet same-day deliveries, handle customer complaints, and handle his/her normal busy work schedule … and the NLRB’s clock is still ticking.
All questions about the voting unit—who is in it and is eligible to vote—will be deferred until after the election. Ballots will be counted before those questions are answered. Only if they affect more than 20% of the employees voting will they be considered.
Quite often, owners ask their floor supervisors to help in their election campaigns, making handouts and asking workers in the central plant to back their company by voting “No Union.” The cleaner risks an unfair labor practice charge if it asks a person to make anti-union handouts and the NLRB then rules that person is not a supervisor. Nervous employers often tend to avoid using supervisors to campaign, hobbling their efforts to win their election.
Second, workers often ask who will be in the union. Will it be just their co-workers in the central plant, or does it include delivery drivers and counter clerks in the branches? And what about front-office staffers? To many workers, knowing who their fellow union members might be is a key issue. Not knowing is like buying a pig in a poke.
The hearing officer will be required to rule immediately on pertinent questions and set a rapid date for an election, often within 10 days to two weeks, which gives a company little time to campaign and give its side of the story.
Since only about 7% of privatesector employees are union members, few know unions have a downside as well as an upside. There are strikes, union dues and assessments, and even union fines for disobeying the union bosses. Wages and benefits can go up, down, or stay the same in negotiations.
Just as unions call strikes to pressure companies to meet their
demands, companies lock out employees to pressure them to agree to company demands. Strikers can be permanently replaced in economic strikes.
Employees have the right to know the full story when they are voting. It takes more than a week or so to tell the full story of the pluses and minuses of unions and answer the questions workers invariably have. But with the compressed election
timetable of the NLRB, companies will have little time to inform their workers before they vote.
A dry cleaner cannot lose an election that is not held. Union organizers rarely cold call, going from door to door seeking likely companies to unionize. Almost invariably, it is the employees who call union organizers because they feel the need for somebody to speak for them to management, and for protection against management abuses.
The best way for a dry cleaner to avoid the expense and disruption of an election, the potential cost of a union with higher wages, and restrictive work rules and costly grievances is to treat his/her central plant employees fairly, openly and honestly so they don’t believe they need a union in the first place. But how?
Testing Employee Attitudes — Many business executives remain in the dark about employees’ sentiments until a union petition is filed. Perceptions of fair treatment must be monitored accurately by cleaners wishing to remain union-free.
Supervisory Behavior and Employee Union Sentiment — The key issues causing workers to seek unions revolve around perceptions of favoritism and unfair treatment, often by first-line supervisors. Since most employees see their immediate bosses as the company, disrespect, unfair treatment and supervisory favoritism are seen by workers as being the attitude of the entire dry cleaner, from owner on down.
Owners of most dry cleaners rely upon central plant superintendents and supervisors to report on morale. Not surprisingly, few of these subordinates would report petty abuses or favoritism they themselves practice. Standing alone, one or two abusive incidents may not be important. But as they accumulate, they impact
employee attitudes severely.
Obviously, training supervisors how to listen and respond to employee concerns is important. Many cleaners use “canned” training programs taken from the Internet. Most deal with generalities, not an individual company’s specifics. Asking a knowledgeable trainer to develop training tailored to the specific problems in a specific central plant takes a little time, but the results are worth it, especially when dealing with diverse workforces. Then, evaluating supervisors not only on their production but also on their “people” skills reinforces the training.
Uncovering Employee Attitudes
— Executives sometimes use fast, computerized attitude surveys, hoping they will uncover workers’ concerns. This doesn’t work, especially when the surveys are in English and many of the central plant’s foreignborn workers can only read their native language. Workers are often asked to score various factors on a 1-to-10 scale. But numeric scores do little to tell the front office why employees believe as they did, nor what remedial efforts to take.
I believe that only a handful of executives in the drycleaning industry take the time to obtain unfiltered views of their employees’ attitudes by having audits conducted by skilled outsiders conducting faceto-face interviews in carefully structured groups. Outsiders are highly effective, because workers are reluctant to speak openly to management for fear of retribution.
Marrying Labor and Management Interests — Dealing with the employee concerns quickly is important. Interestingly enough, many of them revolve around their inability to do their jobs as well as they would like. Poorly maintained equipment or poor working conditions all slow productivity and frustrate workers.
Since employees have many practical ideas about improving productivity, it pays to train supervisors to listen to them in a systematic way and respond. When employees see management caring about productivity and quality, they will, too. Finally, providing incentives like Gainsharing plans to reward workers for their better overall performance is a powerful tool to reinforce labor management bonds.
When these efforts are done effectively, dry cleaners won’t have to worry about unions. When are you going to start?
Dr. Woodruff Imberman is president of Imberman & DeForest Inc. and an authority on labor issues. Readers wishing further information on union avoidance strategies may contact Imberman at 847-733-0071 or info@ imbdef.com.
As if Cancun’s sun, sand and surf in January weren’t enough, a highlight of the Five Star & Brainstorming Conference was John R. DiJulius III’s presentation, How to Make Your Customer Experience World Class.
DiJulius, author of The Customer Service Revolution, offered special insights into a customer’s life and how dry cleaners can translate that into a superb experience.
“How can we be the brand that our customers literally can’t live without?” he asked the audience attending the joint National Cleaners Association/Drycleaning & Laundry Institute event, pacing around and among the scattered round tables where attendees sat.
It starts with service aptitude, which DiJulius defined as a person’s ability to recognize opportunities to exceed customers’ expectations, regardless of the circumstances. And where does this come from? It comes from previous life experiences, previous work experiences and current work experience.
(Image licensed by Ingram Publishing)“Just as you would never allow someone to handle someone’s clothing without the proper training, you can’t let them interact (with customers) without the proper hospitality training,” he says.
The concept of “world class” starts at the top, with “executive sponsorship.”
“You don’t (just) have annual customer service training once a year with your staff,” DiJulius says. “That’s like deodorant: with time, it wears off and the odor comes back. It’s every time you speak—about anything. Sales, marketing, promotions, new point of sale, new equipment. You bring in how that affects the customer experience.”
He played video clips of iconic CEOs—Walt Disney, Amazon’s Jeff Bezos, Starbucks’ Howard Schultz, Apple’s Steve Jobs—that illustrated how each routinely framed their comments with the customer in mind.
Often, it is the most recently hired, least trained, lowest paid employees who deal with customers the most, he says. Do you think that’s an ideal situation?
“Unless you’re hiring directly from the Ritz-Carlton, the Four Seasons Hotel, Nordstrom, they worked for someone who wasn’t world class,” he says. “They worked for a leader who wasn’t world class, and they’re ‘brainwashed’ in a different way than you want them to be.”
Thus, it is not your employee’s responsibility to have high service aptitude, it is your company’s responsibility to “give it to them.”
In a survey of 300 company CEOs from various industries, 80% said they believe they deliver world-class service, DiJulius says. What they didn’t know is that 3,000 of their customers were being surveyed at the same time. And what did they say? Just 8% of customers believe they received world-class service from these same companies.
“You’re in the customer perception business,” DiJulius says. “You can tell me how great you are, but your average ticket, your repeat customers, whatever your key metric is doesn’t lie.”
Employee apathy creates customer apathy, and customer apathy is the enemy of a successful business, he says.
The best way to improve a customer’s perception of your service is to put yourself in their shoes. By better understanding the demands on their time, the pressures they’re under, the personal issues they may have, their likes and dislikes, etc., you improve your chances of fulfilling their needs and pleasing them while you’re doing so.
DiJulius calls Chick-fil-A the “Ritz-Carlton of fast food,” because its service vision is to make every guest feel cared for unlike anywhere else.
The restaurant chain trains its employees to learn to see the world through their customers’ eyes. One tool it uses is an emotionally charged training video that pictures a variety of customers and their untold stories. There’s the father who just lost his job. And the young immigrant who just received U.S. citizenship. Over there sits the widow whose husband died recently; today would’ve been their 50th anniversary. And there are more. The video is available on YouTube; search for “Chick-fil-A every life has a story.”
World-class service organizations do two things better than everyone else: they dictate the best service aptitude, and they consistently put their employees in the shoes of the customers, DiJulius says.
“Every moment is an interaction to tell me whether this is going to be a positive or negative experience.”
Now, every business has “policies” that it stands by, but
DiJulius—owner of a chain of upscale spas in the Cleveland area—prefers to use “guidelines” that permit his employees to act in the best interests of the customer while retaining their business.
He shared a story about Spirit Airlines, which infamously refused to refund a terminal cancer patient’s $197 ticket when doctors would no longer allow him to fly. The incident gained worldwide media coverage, “grounding” the brand’s reputation.
“Build your company’s customer service experience as if no customer had bad intentions,” he says. “Everyone builds it the opposite way, to catch that 2%, then you punish the other 98%.”
DiJulius is a believer than if the service is good enough, a customer truly won’t care if they’re paying more here than they would across town. He favors competing in “experience wars” instead of “price wars,” because “the problem with discounting is there is always someone more willing to give it away than you.”
There has to be a paradigm shift: from a commodity a customer can get anywhere to an experience he/she can only enjoy with you. ADC
Check back next month for more from DiJulius and his concept of “Secret Service.”
Features: Atlas of Atlanta Here’s what to see and do while in ‘Hotlanta’ for Clean ’15. Coin-Op Laundry A self-service laundry could make a plant a comprehensive fabricare center. Showcase: Point-of-Sale Systems
Editorial Submission Deadline — February 15
MAY
Features: Routes to Success The pros and cons of taking drycleaning services directly to customers. Clean Show: First from the Floor The big news from the just-completed event.
Editorial Submission Deadline — March 15
Want to send a press release or submit a story or story idea? Contact Bruce Beggs, Editorial Director, today! Phone: 312-361-1683 E-mail: bbeggs@ATMags.com
www.americandrycleaner.com
...and much more!
Let’s make a commitment to get away from bad habits in 2015. Many of you have decided that what is good enough for you is good enough for the customer. This is what your competitors want you to think, while they quietly raise the bar on their quality and service. You can do/not do a lot of things in the name of minimizing the effort you give to cleaning and spotting, but there is no substitute for great attitude and service.
A common bad habit I’ve noticed is placing the spotting gun too close to the fabric surface. I commonly see “experienced” spotters get the nose against the fabric, especially when drying the area that has been spotted.
Normally, you should place the spotting gun’s nose no closer than the width of your hand, about 4 inches, when using for either steam or air. Increase this distance to 6 to 8 inches when dealing with knits and decorative trim.
Also, when working with a satin weave, spot it on the reverse side to minimize the potential for fabric distortion.
as possible” into the drycleaning machine or laundry washer. Overloading restricts the distribution of solvent, detergent, additives and water. In a dry-to-dry machine, this practice will result in unequal drying, which will rear its ugly head as streaks and swales. Additionally, overloading will reduce the level of mechanical action on the entire load, resulting in less efficient cleaning.
If you are using a cationic process (injection of detergent on each run), your solvent should be clear. If you are using an anionic process (solvent charged to 1% or greater), your solvent should be no darker than the amber color of a pilsner beer. The idea that solvent loaded with contaminants can be used for darks is simply not correct.
Non-volatile residue (NVR) is made up of all the things too small to be filtered out of the solvent. Dark solvent is evidence that filtration is not working properly, or distillation is past due. This is the result of a mechanical failure, misinformation about solvent, or simply poor solvent maintenance.
If you are not delivering one change of good solvent to the wheel at least every 90 seconds, you are doing your customers a disservice and handing your competitor an advantage. When you allow your base tank to drop below 60% of capacity, you are forcing the NVR to become concentrated, which makes filtration more difficult.
When drying the area, resist the temptation to get closer. Keep the spotting gun at a distance of no less than 4 inches. Work in a slow circle by aiming the gun just outside the moist area, and follow the drying in a spiral until you reach the center. Another bad habit has its roots in the best of intentions. The concept of high productivity is a worthy goal. However, processing garments that are still damp with water is the cause of a large problem.
A damp area on fabric can act as a dirt “magnet” in a solvent system. During a cleaning run, the foreign material removed from the items will be redeposited in and on the spot. This leaves an obvious dark area that is difficult to remove. Take the time to dry any garment that comes in damp or that you have spotted wet-side. Also, take advantage of a leveling agent to emulsify any unseen residual moisture. It is easier and faster to take precautions than to spend hours trying to remove the damage you caused in haste.
I cringe each time I visit a plant where the cleaner/ spotter is using any means necessary to “cram as much
Your cleaning equipment must be maintained to work properly and to protect your investment. Lint is generated from cleaning and drying items every day. Clean the button trap and the strainer on the solvent pump daily to maintain the adequate flow of solvent. The filter on the air inlet to the steam coil, which supplies warm air for drying, should be cleaned daily. You must keep solvent and air flowing to ensure proper cleaning and drying.
Every plant has an area or two where protocols need to be “polished.” Look around your plant with an open mind. Now is the time to polish your policies and make 2015 flow more smoothly. ADC
Martin L. Young Jr. has been an industry consultant and trainer for 20 years, and a member of various stakeholder groups on environmental issues. He grew up in his parents’ plant in Concord, N.C., Young Cleaners, which he operates to this day. Contact him by phone at 704-786-3011, e-mail mayoung@vnet.net.
It’s coming together sooner than you think. Register now at www.cleanshow.com
April 16-19, 2015 Georgia World Congress Center Atlanta, Georgia USA
The Certified Restoration Drycleaning Network (CRDN), headquartered in Berkley, Mich., leads the dry cleaning businesses named in Entrepreneur magazine’s 36th annual “Franchise 500” list.
This is the eighth straight year CRDN has made the list, receiving an overall ranking of No. 253 for 2015. The list recognizes growth-oriented franchises based on objective, quantifiable measurements, including financial strength and stability, growth rate and size of the system, according to the company.
Other drycleaning franchises that made the 2015 Fran chise 500 list were Martinizing Dry Cleaning (No. 399), Tide Dry Cleaners (No. 402) and Comet Cleaners (No. 464).
Lapels Dry Cleaning has named Jeff Kline as its Fran chise Owner of the Year for 2014. Kline, who resides in Gilbert, Ariz., owns Lapels franchise locations in Gilbert and nearby Chandler, Ariz.
“Since Jeff opened his doors for business in 2011, his Lapels Dry Cleaning stores have exemplified the excel lence we strive for with all our locations,” says Kevin Dubois, CEO of Lapels Dry Cleaning, who presented Kline with a trophy and a $2,000 award.
Dubois cited several reasons for choosing Kline from among more than 60 franchise owners, including growth of Kline’s plant in Gilbert by nearly 50% and his Chandler satellite store by 20%; training new Lapels franchisees at his facility; working with the Lapels cor porate team to create a “Construction Document” that has helped new franchise owners in the build of their new stores; helping, with his staff, to develop a customer review platform; and more.
America’s Best Cleaners™ and SPOT Business Systems have teamed to create a Users’ Group that will weigh in on future SPOT processes and developments.
More than 95% of America’s Best Cleaners’ Affiliates use SPOT software to manage not only back-end opera tions but also front-end revenue streams, marketing data, client data and client retention.
“What we find ... is that a lot of Affiliates aren’t using the SPOT system to its full capacity,” says Chris White, executive director of America’s Best Cleaners, “This Users’ Group will allow operators to capitalize on every thing the software has to offer.”
The new group will offer input and feedback to SPOT, potentially beta-testing new processes and developments.
It will meet frequently via online conferencing, and through participation in October’s SPOT Users Confer ence (the America’s Best Cleaners National Affiliate meeting will take place immediately after this gathering).
These Affiliates are ideal to assist a business like SPOT in determining future developments, says White, because the non-competing dry cleaners are protected under a nondisclosure agreement and are accustomed to sharing intimate business details.
SIMPLE, RELIABLE, EFFICIENT
SIMPLE, RELIABLE, EFFICIENT
NO BLOWER OR ELECTRICAL COST FOR FAN
Reduces electrical costs on parasitic energy losses of fan, saves $, plus this eliminates more things that can go wrong such as air prover switch, blower motor starter or overloads, upgraded flame safeguard system for air change requirements and interlocking
NO BLOWER OR ELECTRICAL COST FOR FAN Reduces electrical costs on parasitic energy losses of fan, saves $, plus this eliminates more things that can go wrong such as air prover switch, blower motor starter or overloads, upgraded flame safeguard system for air change requirements and interlocking
NO POST PURGE OR PRE-PURGE
Most sealed combustion boilers with fan require four air changes after burner shuts off and before it can turn back on(typically 60 seconds total).
Parker Boiler is on from call for heat in less than 10 seconds
Most sealed combustion boilers with fan require four air changes after burner shuts off and before it can turn back on(typically 60 seconds total). Parker Boiler is on from call for heat in less than 10 seconds
QUIET
You won’t even know it is on.
QUIET You won’t even know it is on.
NON PROPRIETARY CONTROLS
Buy our controls from any supply house or wholesaler on the planet.
NON PROPRIETARY CONTROLS
Buy our controls from any supply house or wholesaler on the planet.
REPAIRABLE
Technically, it can be the last boiler you ever have to buy, as every single component is replaceable at a fraction of the cost of a new boiler.
REPAIRABLE
Technically, it can be the last boiler you ever have to buy, as every single component is replaceable at a fraction of the cost of a new boiler.
FLUE CLEANING
No Annual requirements to clean boiler flue passages.
FLUE CLEANING
No Annual requirements to clean boiler flue passages.
HEAVY DUTY INDUSTRIAL GRADE
HEAVY DUTY INDUSTRIAL GRADE
Call us today and ask us how you can save money by using our boilers. 323-727-9800
Call us today and ask us how you can save money by using our boilers. 323-727-9800 See us at Clean 2015 • Booth # 2759
Angeles CA 90040
(323) 722-2848
5930 Bandini Boulevard ● Los Angeles CA 90040
Phone (323) 727-9800 ● Fax (323) 722-2848
www.parkerboiler.com
www.parkerboiler.com
Compact Systems have always been a popular style and now with new larger capacity and availability in two foot prints, there is no need to squeeze a large foot print machine into a limited spaced shop.
Loaded with standard features, three working tanks and dual filter system operating in accordance to your needs has never been easier.
Limited space? High volume? No Problem – the Performance Series is available in Tandem configuration. Tandem systems can be configured in any capacity you require.
“ there is always ingenuity, passion and determination behind every great machine”