Ensuring sanitary healthcare linen


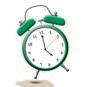
Aramark named a top 50 company for diversity
PHILADELPHIA — Aramark, a provider of food, facilities management and uniforms, was once again named one of the top 50 companies for diversity by BLACK ENTERPRISE for its professional inclusion of people from all races and demographics.
“We strive to create a workplace culture of diversity and inclusion, and we are honored to once again be recognized by BLACK ENTERPRISE,” says Lynn B. McKee, executive vice president of Human Resources for Aramark. “Our 270,000 team members, who represent many different backgrounds, perspectives, talents, beliefs and values, are the backbone of our vibrant workforce, and essential to our success. We share this year’s recognition with them.”
BLACK ENTERPRISE is a business, investing and wealth-building resource for African Americans. The magazine surveys the top 1,000 publicly traded companies, as well as the 100 leading global companies with strong U.S. operations. ALN
COMPILED BY MATT POE, EDITORCHICAGO — Theodore N. Halkias, director of Contracts Administration and Corporate Compliance for Hospital Central Services Inc. (HCSC), a provider of textile programs and services to the healthcare industry based in Allentown, Pa., says his company is seeing more and more requests for proof that its procedures are producing sanitary linens.
This isn’t an isolated case.
It seems more healthcare facilities want verifiable proof that processed linens are clean. These requests are coming from both existing customers and in request for proposals (RFP) from potential customers.
American Laundry News asked experts to share their insights into rising requests for proof of sanitary linens, effective methods to ensure cleanliness, and how laundries
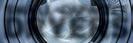
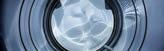

and healthcare facilities can work together to keep healthcare linens sanitary, from processing to patient.
First up is Halkias, who is also a member of the American Reusable Textile Association (ARTA). He has been with HCSC for more than 31 years in the service and marketing aspects of the linen rental business. He is also responsible for formalizing HCSC’s infection control and prevention policies, as well as procedures and renewals.
Halkias’s viewpoints are followed by perspectives from leaders of two organizations that validate clean healthcare linen and facilities. Linda McCurdy is president-elect of the Healthcare Laundry
See SANITARY on Page 6
Evolution of patient gowns
rates the healthcare facility receives.
BY MATT POE, EDITORCHICAGO — The patient gown.
It seems simple enough—a garment someone being treated or cared for in a healthcare facility wears to offer covering, yet allow medical personnel access for tests and treatments.
It is what it is, isn’t it? Well, no.
“The introduction of the HCAHPS patient satisfaction survey has put a focus on the patient experience in the healthcare setting,” says Steve Berg, vice president of National Healthcare Accounts for ADI American Dawn in Los Angeles. “Patients and their families will now place a grade on their stay and their entire experience. These surveys will influence the reimbursement
“This relationship between patient experience and hospital earnings will allow an increase in quality for all goods associated with the patient, especially what she/he is wearing.”
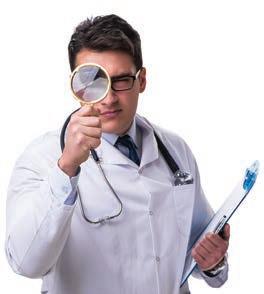
Teri Burke, senior product manager of patient apparel for Medline Industries Inc., says that studies show that upgraded linens greatly improve patient satisfaction during their stay at the hospital—and that includes the patient gown.
“Whether it’s a simple X-ray or major surgery, one of a patient’s first contact with a facility is the gown they wear,” she says.
Burke goes on to say that healthcare customers not only want better material, but they are also looking to create gowns
that show customization and branding as well. Custom designs and quality fabrics are powerful touch points. They can help
Utilizing Employees Effectively

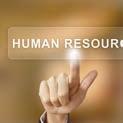
In a tight labor market, laundry managers need to know operating costs, get creative in the plant.
Panel of Experts
In this issue, the experts talk about how to have better communication with vendor partners.
With more healthcare facilities requiring proof of clean linen, what’s a laundry to do?
Design, material, comfort—many factors have changed when it comes to what patients wear in a healthcare facility(Image licensed by Ingram Publishing)
Linen rental company satisfies food and beverage customers

GLENDALE, Calif. — Blue Bird Uniform, located here, is a family-owned linen rental business providing food and beverage clients with perfectly cleaned, fully ironed table linens, towels and custom-designed chef coats and aprons.
In 11 years, Blue Bird has grown to handle more than 150 banquet and restaurant accounts. Its on-premises laundry, equipped with Continental Girbau laundry equipment, has grown proportionately, as well.
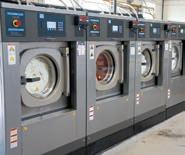
“We are unlike other linen rental companies because we manufacture all of our table linens and chef coats,” says Lucine Igraryan from Blue Bird. “We purchase the fabric and cut and sew it to meet each customer’s unique table linen and uniform specifications.”
Each day, Blue Bird cleans 5,000 pounds of
laundry using large-capacity Continental E-Series Washer-Extractors. The washers are engineered to properly clean a wide variety of items. This is because every variable of a wash cycle is programmable, from water temperatures and levels, to number of baths, extract speed and mechanical action. This ensures that even the most greasy, stained kitchen towels come out of the wash looking hospital white.
Once washed, laundry is loaded into a corresponding dryer. Blue Bird’s Continental ProSeries II Dryer features a moisture-sensing system to prevent damaged due to over drying. Additionally, a programmable control makes for simple operation.
While towels are fully dried and subsequently folded, table linens are loaded into the dryer for just two minutes for untangling. Then they are fed through one of two Continental flatwork
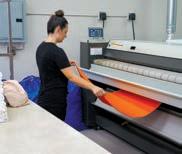
ironers, where they are automatically straightened, dried and ironed in a single pass.
The ironers are significantly more efficient than hand folding, according to Igraryan.
“We cut that time by nearly half with the installation of our first ironer,” she says. “Before we had our first ironer, we were doing everything by hand. It was a lot of labor and work.”
Now, it takes just 22 minutes to iron a 60-pound laundry load consisting of 17 108-inch tablecloths.


“We were able to bring in more clients and purchased a second ironer a year later,” adds Igraryan. “We just moved into a new, larger location. We are constantly growing.” ALN
Publisher
Charles Thompson
Phone: 312-361-1680
E-Mail: cthompson@ ATMags.com
Associate Publisher/ National Sales Director

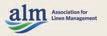
Donald Feinstein
Phone: 312-361-1682
E-Mail: dfeinstein@ ATMags.com
Editorial Director
Bruce Beggs
Phone: 312-361-1683
E-Mail: bbeggs@ ATMags.com
Editor Matt Poe
Phone: 866-942-5694
E-Mail: mpoe@ ATMags.com
Production Manager Roger Napiwocki
Digital Media Director
Nathan Frerichs
Phone: 312-361-1681
E-Mail: nfrerichs@ ATMags.com
Advisory Board
David Barbe • Jim Buik
Tony Jackson • Janice Larson Tom Marks
Main Phone: 312-361-1700 Fax: 312-361-1685
Subscriptions
630-739-0900 x100 www.americanlaundrynews.com
Charles Thompson, President and Publisher. American Laundry News is distributed selectively to qualified laundry and linen management and distributors in the United States.
© Copyright AMERICAN TRADE MAGAZINES LLC, 2019. Printed in U.S.A. No part of this publication may be transmitted or reproduced in any form, electronic or mechanical, without written permission from the publisher or his representative. American Laundry News does not endorse, recommend or guarantee any article, product, service or information found within.
Opinions expressed are those of the writers and do not necessarily reflect the views of American Laundry News or its staff. While precautions have been taken to ensure the accuracy of the magazine’s contents at time of publication, neither the editors, publishers nor its agents can accept responsibility for damages or injury which may arise therefrom.
MEMBERSHIPS
Equipment mix key to quality processing, helps business account growth, company says
Our M-Series Washer-Extractors are built for optimum performance and easy service access. The simple design with single pivot two-way tilt and large door provide safe, fast and efficient loading and unloading. The open access allows for easy and simplified maintenance. Milnor’s unique and innovative SmoothCoil™ Suspension System means maintenance-free, superior vibration dampening with less wear and tear. Our intelligent bearing design provides three water seals and an excluder seal mounted on an easy-to-replace seal sleeve, along with a leak-off cavity to keep water and chemistry away from bearings. All of this and more, built to Milnor’s legendary ruggedness and durability.
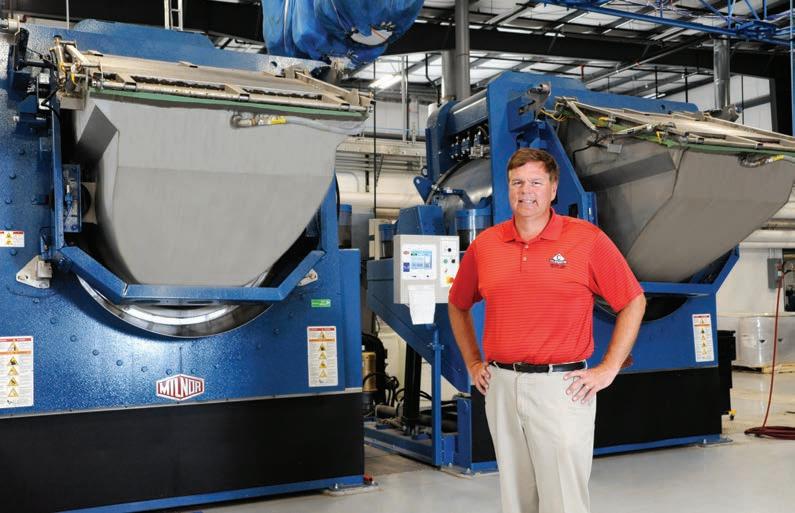
Contact an authorized Milnor distributor or call 504-712-7656 to find out more.
www.milnor.com
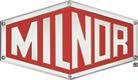
“When I saw an overhead sling automatically loading walk-off mats directly into a Milnor 450 lb open-pocket washer-extractor, I was sold!”
– Randy Clemens, General Manager of Clemens Uniform
Proof in the processing
Looking at the front page of this issue of American Laundry News, you probably noticed that both cover stories relate to healthcare.
Healthcare laundry and linen is a big part of the industry. It’s also a very challenging segment because of the guidelines laundry processors must follow and meet. Then there’s satisfying patients, facility staff … my hat’s off to those who service this industry.
One way to try to ensure that a laundry is providing sanitary healthcare linens is to provide proof to its customers. That’s why the top cover story looks at what’s going on in accreditation and certification.
Those in the know say that more healthcare providers are asking for proof, even including it in requests for proposal before working with a laundry. I
The Editor’s Desk MATT POEworked with a healthcare laundry representative and leaders of two accreditation/certification organizations to find out what laundry’s need to know in this market.
While sanitary linens are topof-mind, patient satisfaction isn’t too far behind, and in the past, patient gowns have left things a little too “behind.”
You’ll see in the bottom cover story that patient gowns have evolved in recent years for patient comfort, and modesty. There have also been improvements made to help facility staff in their jobs.
And, of course, we look at how these alterations impact processing of patient gowns.
However, this issue isn’t all about healthcare laundry. Our Panel of Experts (page 14) talk about how laundry/linen services can improve communications with vendors.
Also, this issue’s Product Showcase (page 18) provides a glimpse at what manufacturers have to offer in small-capacity dryers (under 100 pounds).
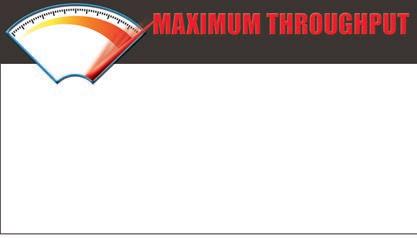
With those pieces, two columns on staffing, and news, I think you’ll find something to help you keep it clean! ALN
Final testing underway on healthcare laundry monitoring toolkit
HLAC says resource will measure microorganisms to validate processes
PLAINFIELD, Ill. — Final-phase testing has commenced on a new resource, called the HLAC Laundry Process Monitoring Toolkit™, available from the Healthcare Laundry Accreditation Council (HLAC).
The organization says the toolkit validates the effectiveness of a laundry’s processes by measuring the number of microorganisms found in a laundry on hard surfaces, in the air, on linen, in the water and on employee hands.
The organization says that a cross-section of healthcare laundries—HLAC-accredited and nonaccredited—are part of a control group to substantiate the new toolkit’s performance through a testing process.
“HLAC has developed the Laundry Process Monitoring Toolkit to respond to the challenge for operators to continually know how well their processes are performing and whether their standards are on target as originally intended,” says Gregory
Gicewicz, who heads the committee developing the toolkit on behalf of HLAC.
HLAC is a nonprofit organization that inspects and accredits laundries processing textiles for hospitals, nursing homes and other healthcare facilities.
“Responsible healthcare laundries go to great lengths to maintain the highest standards in the name of hygiene and infection prevention,” says HLAC President-elect Linda McCurdy.
“Moreover, laundries that are accredited by HLAC have set in place numerous in-plant processes to provide their healthcare customers hygienically clean linen. Our toolkit goes a long way to safeguarding all of these endeavors.”
Final-phase testing is expected to be completed by the first quarter of next year, with a formal international launch of the new toolkit shortly thereafter. ALN
One solution to staffing in a tight labor market
W e are once again in an employment cycle where there are more jobs than candidates looking for jobs. This is commonly referred to as a tight labor market.
There are “help wanted” signs in the windows of a number of businesses that regularly compete in the same labor pool as I would as a laundry manager.
So, how do I make my entry-level job more attractive than entry-level jobs in other businesses in my area?
The most common answer is to pay more than the competition, but the truth is salary adjustments made by one employer are quickly matched by others.
A good benefits package can help to keep employees but does little to attract entry-level workers. They are focused more on the hourly rate than the fringe benefits. Fringe benefits do not make the car payment or pay for food and housing.
How does a business stand out in this tight labor market and become the preferred place for people to want to work? The first thing is to understand the history of your industry.
In the vast history of doing laundry in a commercial setting, it has often been staffed by the recent immigrant who needed a job so they could start their American dream. The laundry business is an entry-level job that can be handled effectively by someone who has limited or no English skills.
This type of employee is used to hard work and poor working conditions. Where an American high school graduate might turn his or her nose up at the physically demanding production and business, a recent immigrant finds it very much to their liking. Their expectations are based on their life experiences, and those have been harder than most of us can imagine.
Unfortunately, more and more smart business owners are learning about this source of labor, so there is competition for this group as well.
So, how do you attract this natural source of labor to your business? There are several key groups you need to establish a working relationship with.
The first would be whatever agency assists legal refugees with relocation and placement in your community. There are agencies in every area that help legal refugees to settle in and find jobs. Establishing a good working relationship with these people can be a key to getting the best new arrivals as they become available. Of course, it goes without saying that you must treat these recent immigrants fairly and establish a workplace environment that is accepting and tolerant of people with different cultures and languages.
The second key relationship to develop is with places of worship that provide assistance to recent immigrants. Often these religious communities help by providing English as a second language classes. Another good source of referrals is to develop a relationship with the adult instructor for the local educational system that teaches English as a second language.
All these groups are trying to improve the life of this targeted group of employees. Part of their mission is to help them find stable, secure employment. That is the very definition of the laundry business: stable, secure and predictable.
Your hardest hire will be the first non-English speaking employee. Once you have successfully employed one and you have established a training program and a business environment to meet their needs, word-of-mouth will begin to spread and you will get more opportunities.
•
•
•
•
•
•
When I went to work in Roanoke, Va., for the Carilion Health System, my goal was to become the preferred employer for recent immigrants. I am proud to say that upon my retirement 14 years later I had achieved that goal. Next month’s article will deal with the training of limited or non-English-speaking employees.
Eric Frederick served 44 years in laundry management before retiring and remains active in the industry as a laundry operations consultant. You can contact him by e-mail at elfrederick@cox.net, or by phone at 540-520-6288.


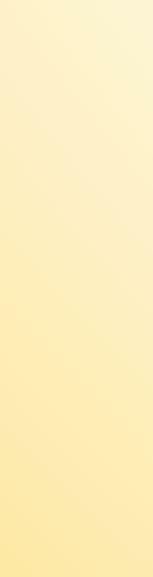


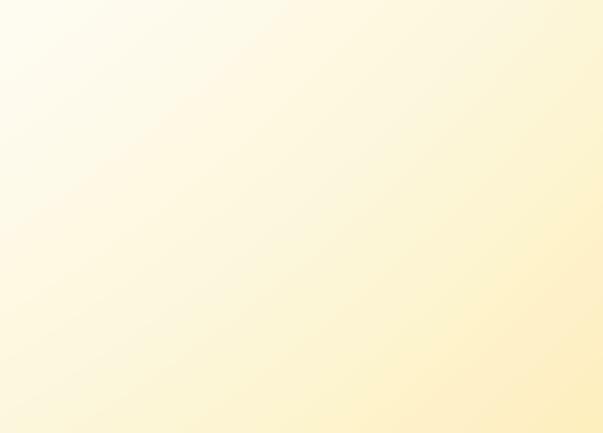
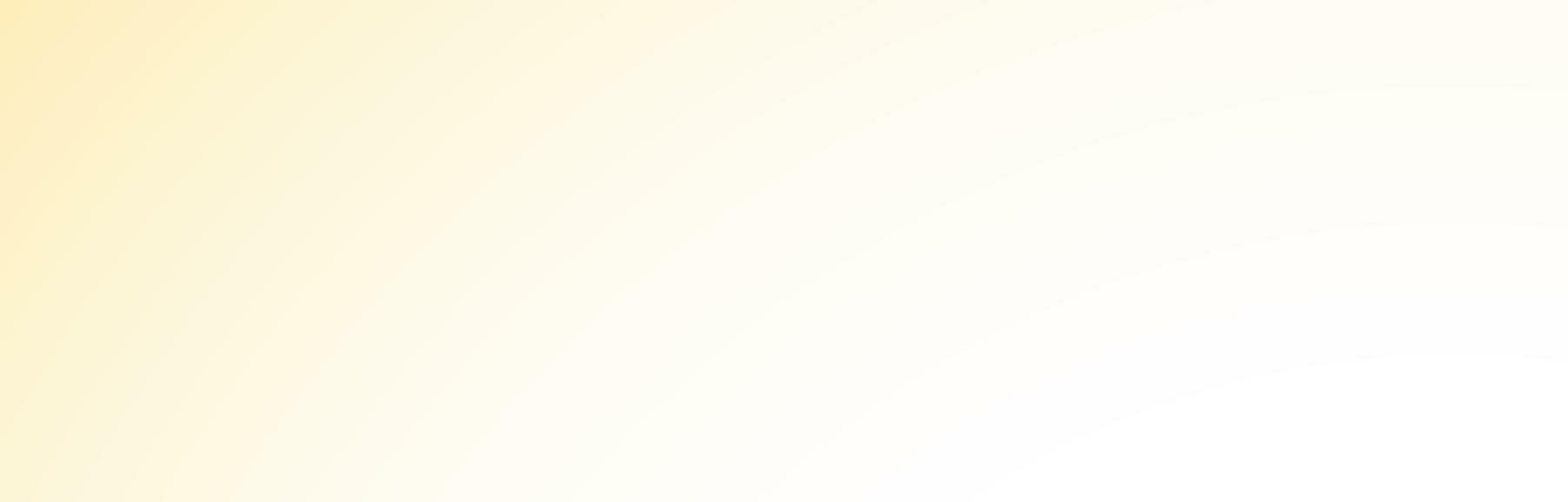

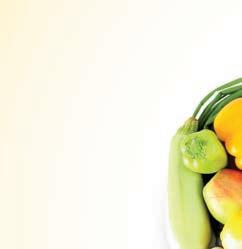
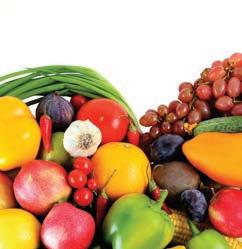
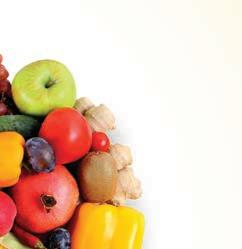

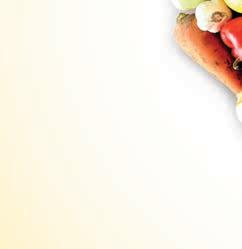

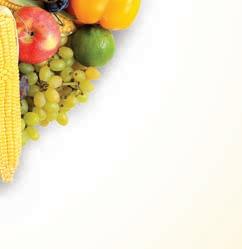


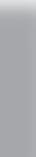
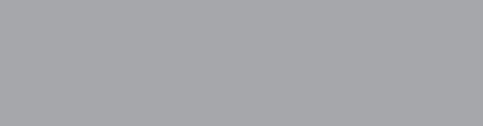


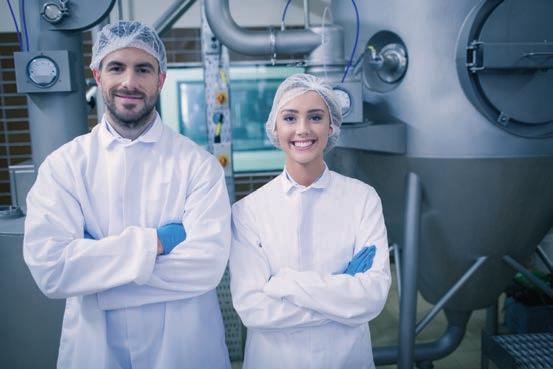
Sanitary
Accreditation Council (HLAC), and Joseph Ricci, CAE, is president and CEO of TRSA, the association for linen, uniform and facility services, which offers Hygienically Clean certification.

THEODORE N. HALKIAS, HCSC
HCSC has experienced an increasing number of requests from healthcare facilities for verification of laundering procedures to produce hygienically clean linen, whether from existing or prospective customers performing their due diligence. We are also seeing the requirement for certification of plants on linen and laundry service RFPs from perspective customers.
I think this is driven by two key factors: 1) the rise of medicineresistant superbugs and HAI (healthcareassociated infections) and 2) patient outcomes and satisfaction intricately tied to reimbursements. The healthcare industry’s focus has narrowed for each of these aspects as it strives to meet patient needs at lower costs. As a result, the role of textiles in infection prevention is an area under increased examination.
Our plant is inspected annually by our customers’ infection preventionists. As a laundry, we adhere to internal standards and also those required by HLAC accreditation and the TRSA Hygienically Clean certification. This combination of client inspections and sharing our third-party accreditation and certification has been acceptable proof of linen quality by our customers to date.
Probably the best ways to offer proof that the linens are sanitary are via the monitoring groups I mentioned and by performing independent lab testing of the processed textiles.
Years ago, I was not necessarily a proponent of periodic lab testing of processed linens because no one ever defined what reduction in pathogen level must be achieved to prevent human illness, but I thought it was still good PR. However, in today’s environment, a quantified biological test of the microbial load level on a laundered item is more exacting evidence of the efficacy of your processes and logically carries more weight with a hospital.
We must put cases of news reports of infected healthcare laundry into perspective. According to the public record of recent incidents, only one had any validity—the mold issue linked to the deaths of five patients at the children’s hospital in New Orleans. In that case, what could go wrong did seem to go wrong. There was poor compliance to industry guidelines by both the laundry and the hospital, and when combined with vulnerable patients, the consequences were tragic.
The mold issue that occurred at a western Pennsylvania health system in late 2015 and early 2016 was never definitively linked to the laundry provider. In fact, both the CDC and Pennsylvania Department of Health issued statements saying the facts of the investigation did not support the conclusion that infections resulted from exposure to the linens.
And lastly, the C.diff U.K. study has
been thoroughly criticized as flawed.
This causes me to recall a conversation I once had with an epidemiologist contact of mine from a major health system in the Midwest. He told me about a term used by some behavioral scientists called the “availability heuristic.” Basically, it implies that a person’s perception of risk is based on how much attention is paid to the problem and, if not careful, can easily lead to faulty decision making and judgments.
When the media latch on to issues such as these and they are re-printed/re-transmitted in many other publications and platforms, the information can be perceived as alarmist in nature and lead to incorrect conclusions. I’ve seen this all too often in our industry.
We know that contaminated healthcare textiles can contain a large number of microorganisms, but you must place things in proper context. It will interest readers to know that commercial healthcare laundering has an admirable track record on producing consistently hygienically clean product.
Decades of experience with laundered, reusable textiles strongly supports the notion that current laundry processes are effective in interrupting potential patient-to-patient transmission of infectious diseases. Indeed, outbreaks of infectious diseases associated with laundered textiles are extremely rare.
A recent literature search identified only 13 incidents that have been reported worldwide in the past 46 years. Of these 13 outbreaks, only three have occurred in the United States. The significance of this statistic increases all the more when one notes that the volume of laundered linen produced for U.S. healthcare facilities is at least 6 billion pounds annually, with some sources estimating it closer to 10 billion pounds. Follow-up analysis of the outbreaks has revealed that in each case there was a breakdown in aseptic technique.

To maintain the sanitary condition of the processed linens you must understand the principle that whatever surface the clean linen touches must be as hygienically clean as the linen. In preparation to transport clean linen, goods must be packed into a sanitized plastic-lined delivery cart and when completely packed, sealed up with the plastic to protect the linen while in transport from the laundry to the healthcare facility’s receiving dock.
The interior of the truck used to deliver clean linens had transported soil earlier, so it should always be cleaned before loading clean linen carts using an EPA-registered, broad-spectrum germicide. This is usually accomplished via a fogging device. Once delivered to the hospital, the clean carts should be moved inside the facility in a timely manner to avoid contamination from the environment or unauthorized tampering with the clean linen.
Good policies and practices that enable a laundry provider to become certified or accredited ensures that all linen is hygienically clean when it leaves the laundry facility. From there it is up to every employee who handles, stores and distributes that linen to follow proper procedures and make sure it remains hygienic. The best way to do that is to assume that any contact throughout the transportation, storage and distribution process can contaminate linen.
Maintaining both the quality and cleanliness of processed linens prior to use is a shared responsibility. It calls for collaborative efforts between the laundry operator and the healthcare professionals who receive clean linen at healthcare facilities. This maintenance phase is the last part of the overall process of preparing linen for patient care. One methodology to enhance patient safety is for the laundry operator to add a bacteriostatic agent to the wash formula that provides a residual, self-sanitizing effect which inhibits bacteria growth on the linen while in storage and use.
For the healthcare facility, it’s up to management to develop a policies-and-procedures manual that outlines best practices for the various aspects of clean linen handling. Such a manual serves as a guide for training new staff members and should be used for monitoring and evaluating the linenhandling process within their facility.
I think that our industry should continue to monitor the efficacy of new antimicrobial technologies such as silver ion and copper, but at the same time it is important to proceed with extreme caution and rigorous analysis. Besides being efficient against microorganisms, these antimicrobials need to satisfy the requirements of:
• Suitability for textile processing.
• Ease of application.
• Durable for laundering and hot-pressing/drying.
• Safe for use on skin.
• Retention of fabric quality.
• Conducive to the biology of the environment.
Laundry operators are also running a business, so these needs must always be counterbalanced by the need for cost effectiveness. For instance, say the new technology meets all of the criteria listed above and is projected to cost an additional 15 cents a pound. Say you have a 4 million annual pound system on rental. Who’s going to pay for the added $600,000 a year price tag? What assurance can there be that the new technology will save more than that amount each year from reductions in HAIs in that system?
Although emerging technologies using silver ion or copper offer the potential to lower HAIs, there is still no definitive truth on the matter.
I think it is important to note that although various studies have shown that linen can harbor pathogens, just because pathogenic microorganisms are found on textiles doesn’t automatically mean transmission of infection will occur. Recall the chain of infection concept. If any of the four links (portal of entry, susceptible patient,
mode of transmission, sufficient dose) is missing, transmission will not occur.
The perceived health benefit of antimicrobials on textiles is not supported by data and further research and verifiable studies are needed.
LINDA MCCURDY, HLAC

We haven’t put it into actual numbers, but lately we’ve been hearing that among a growing number of healthcare facilities, having HLAC accreditation is becoming a requirement in order to be considered a healthcare laundry vendor.
However, many of our laundries don’t wait to be asked but instead aggressively promote their HLAC accreditation and its benefits to infection prevention strategy. It’s a significant competitive advantage.
What healthcare facilities most regard about HLAC accreditation is the fact that our standards cover the complete textile processing cycles, from handling and transporting soiled healthcare textiles (HCTs) to inplant processing and back to the delivery to the customer. These standards also include strict adherence to federal government regulations and guidelines.
All of this gives the healthcare customer peace of mind that their laundry is operating to the highest standards for infection prevention and patient safety.
Requests for proof runs the gamut, from asking for something as simple and convenient as providing proof that the laundry facility is accredited to seeing healthcare facilities/ organizations dig a bit deeper, like asking for proof that healthcare laundry standards are being followed.
For example, there are healthcare laundry standards that address processes in areas such as environmental hygiene, laundry wash formulas, employee hand hygiene and linen transport. Certain healthcare facilities/organizations with an additional level of rigor will ask for actual data proving that the standards are being followed. The data being asked for is often in the form of checklists, training records or even actual microbial counts on surfaces, air, employee hands, water and even linen.
It is all about proving the processes used to produce clean linen and proving the processes used to keep that linen clean. For example, show proof of your wash formulas and temperatures in the form of regular chemical titration reports, and show proof of your environmental cleaning processes in the form of cleaning checklists and microbial contamination counts of clean laundry surfaces.
Also, show proof of your cart-cleaning processes in the form of cart-cleaning checklists, cart washer titration records and microbial contamination counts of clean carts, and show proof of your hand hygiene processes by showing employee hand hygiene training records as well as records of employee hand cleanliness analyses. Finally, show proof of clean linens by showing, at the point of entry to the hospital, visibly clean linens, as well as microbial contamination count records of clean linen samples.
Recently, HLAC announced the finalphase testing of the HLAC Laundry Process Monitoring Toolkit. Our toolkit identifies and measures the number of microorganisms found in a laundry on hard surfaces,


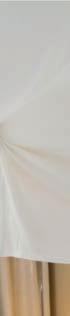
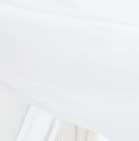
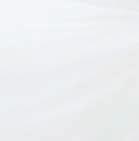
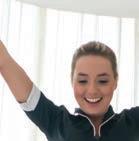
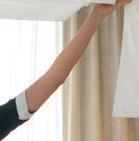

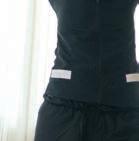
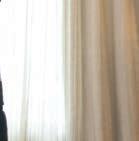
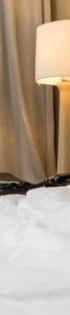

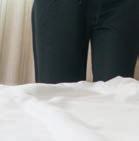

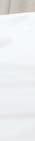

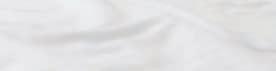



















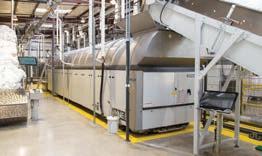

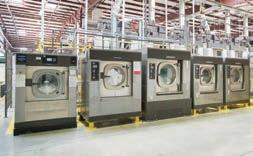
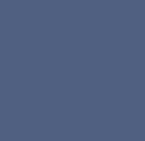
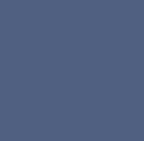
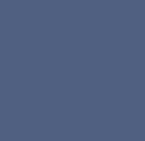
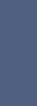
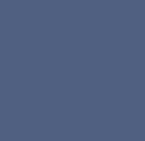
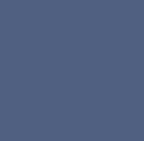
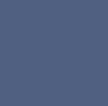


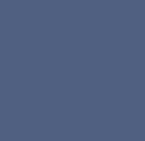
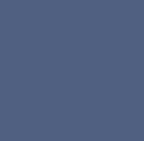

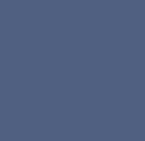
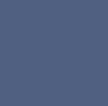


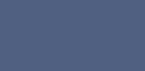

attract and keep consumers by making their experience more comfortable, personal and caring.
“As the years have passed, we have listened to our consumers and have made changes for design and style, patient comfort, and patient privacy,” says Sami Kahen of Royal Blue International, an importer and domestic manufacturer of institutional linen items in Los Angeles.
“Although there are a lot of gowns still around with the standard string closure, there have been advancements in patient privacy with new snap designs and larger sweep sized gowns to protect patient privacy with larger coverage.”
CHANGES IN DESIGN, MATERIALS USED
Berg believes patient gowns have made significant improvements in areas such as design, style, comfort and privacy.
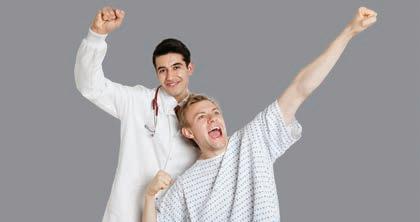
“Overlap backs, creative closure methods and front-opening gowns offer new style options for caregivers,” he says. “Most new gowns being introduced in the market today have an acceptable fabric weight that allows patient comfort as well as privacy due to increased opacity.”
In addition, Berg says new synthetic and synthetic blend fabrics have allowed manufacturers to incorporate color schemes and designs that resist fading in the laundering process, allowing a move away from the institutional look of traditional patient gown prints.
Synthetic blends, softer fabrics, brighter and more stainand fade-resistant prints and designs, and better coverage (while still allowing for fast and easy clinical access) will be the new normal in patient apparel, adds Joe Przepiorka, vice president of Marketing for Encompass Group LLC, a manufacturer of healthcare textiles and products. Synthetic knit gown usage is on the rise, too.
Richard Stewart, corporate vice president of Platform Development at Standard Textile Co. Inc., adds that upscale fabrics (similar to those found in the retail market) and features that allow easier and faster gowning have become available. Other areas that have received attention in recent years include expanded options for bariatric, mental health and risk of elopement identity.
“Countless new designs have been presented to the marketplace over the past couple of years that provide improved modesty and patient coverage,” says Dan Schwartz, vice president of Fashion Seal Healthcare, part of the Superior Group of
Companies.
Schwartz says Fashion Seal regularly takes measures to improve fabric hand, creating softer, more comfortable fabrics, increase opacity, increase coverage, and provide gowns that allow patients to feel comfortable in any healthcare setting.
“Modesty has always been top of mind at Medline when it comes to our patient apparel,” shares Burke. “Our gowns have full tie-side closures to make it easy to reach for the patient and ensures complete coverage. Our gowns also feature stylish patterns with IV sleeves and plastic snaps. Medline’s plastic snaps are MRI compliant and ensures the patient will not have to switch to a different gown for imaging.”
There has been a gradual effort to streamline the patient gown offering, notes Berg.
“Rather than purchase, inventory, launder and distribute a different gown style to each user area, it makes sense to combine gown styles into a gown that can service multiple areas within the healthcare setting,” he points out.
Historically, Stewart says most patient gowns have been made using a woven fabric with a blend of cotton and polyester that was constructed and finished to perform well during the institutional laundry process.
“In recent years, many manufacturers have introduced an allpolyester fabric option, which has the look and feel of a traditional, familiar woven cloth and the added benefit of superior performance,” he says. “These fabrics will typically have minimal shrinkage and excellent durability and color retention, which translate into an extended service life for the products, reduced waste generation and lower merchandise replacement expense.”
PROCESSING TODAY’S GOWNS PROPERLY
New synthetic and syntheticrich blend fabrics process differently than traditional cottonblend fabrics, points out Berg.
“These new gown fabrics dry faster, wrinkle less and retain color better than their cotton-blend counterparts, but they aren’t bullet-proof,” he says.
Attention to proper sorting as well as adherence to manufacturer suggested care instructions (particularly drying) must be addressed to achieve peak performance, Berg shares.
“The move to synthetic and synthetic-rich fabrics should add up to easier processing, quicker drying and less energy use for laundries,” Przepiorka says. “The greater stain resistance of the new fabrics should lessen rewash and ragout amounts, as well.”
Today’s synthetic fabrics are also much more durable than a cotton-blended fabric, more stain resistant and more colorfast, he shares. This all adds up to less rewash, less ragout, less retirement
due to color fades and higher use cycles.
“Today’s gowns definitely last longer with the advent of microfiber patient gowns and 100% polyester gowns as opposed to the standard cotton-poly blend,” Kahen says. “Of course, the fibers that compose these items are more expensive than standard cotton, so there needs to be a cost benefit analysis, but microfiber has been tested to last sometimes five to 10 times longer than the standard cotton/poly gown.
“The way they are made is the secret to the longevity of these items.”
Chuck Rossmiller, director of Laundry Programs for Medline Industries Inc., says that gowns are heavier than they were previously, which means slightly longer processing times and some adjustment to how they’re folded.
“The newest gown innovations are in the material being all-synthetic fibers, which are longer lasting and faster drying,” he says. “Some facilities are treating gowns like uniforms—the gowns are hangered, steam tunnel finished and automatically folded. The quality and consistency of the finished product is substantially enhanced, and the automation reduces labor cost.”
Rossmiller adds that as gowns have gotten larger, and heavier, they take up more space on carts and shelves.
“So, where a stack used to contain 18-20 gowns, it may now be 15,” he points out. “Conversely, though, the larger, heavier gowns, with consistent prints, are leading to the use of fewer gowns as patients don’t need to be double gowned to achieve an acceptable level of modesty.”
Schwartz agrees that fabric technology has come a long way over the last decade, allowing patient gowns to have more endurance than they have in the past.
“Such advancements have allowed patient apparel suppliers to produce polyester-rich garments that have more durability, but are still able to maintain a soft fabric hand,” he says. “Patients are comfortable in these garments, and due to the higher polyester
content and printing techniques, gowns tend to last longer than cotton-rich sheeting gowns.
“From a visual standpoint, the synthetic fabrics will be more stain resistant than before, so the gowns will look cleaner longer. The colorfastness of the synthetic printing process will also allow for a brighter, newer look for longer.”
This combination will offer a “new-looking” gown deeper into its life cycle, and a better presentation to the patient and staff, according to Przepiorka.
In addition to style, comfort and processing changes, he adds that the emergence of knit gowns and no-fold linen systems allow for unfolded gowns to be delivered in bags instead of stacked and folded on shelves.
“However, knit gowns are still a fraction of the overall market use, so this is more of an emerging trend to watch than a market shift,” he cautions.
When it comes to the concern about achieving sanitary healthcare linens, manufacturers indicate that healthcare laundries do a good job no matter what fabric type or blend it used.
“There has been some controversy in the literature about which fabric blends (cotton vs. synthetic) ‘hold’ more microbes after processing,” says Przepiorka. “Our position is that if either blend is properly processed to a hygienic state, this discussion is moot.”
“Like synthetic uniforms, cotton and cotton blended materials have shown to harbor more bacteria, particularly from skin shed from the users,” adds Rossmiller. “All synthetic products improve the wash process time, withstand the commercial process better, maintain the color, size and shape, making them more consistently clean.
“Certified healthcare laundry providers will consistently achieve hygienically clean products regardless of the type of material.”
FUTURE OF PATIENT GOWN DESIGN, FUNCTION
“I don’t have enough fingers and hands to count all the recent instances of fashion designers, design students, and individual
doctors and nurses, among others, who have claimed they have come up with a new patient gown design that will make the ‘ole open-butt gown’ a thing of the past,” says Przepiorka. “They have all failed.”
He says the problem is that the “inventors” don’t really understand the full use cycle of a garment, how it is used and cared for along its travels, and what facilities and laundries would be willing to pay.
“The requirements of inpatient and outpatient use, institutional laundering, and donning and doffing by anyone (without instruction) make the overly-simple current design enduring if not endearing,” Przepiorka adds.
That said, he believes there will be continued tweaks to the traditional gown design that include the fabric changes already shared and minor design changes, such as better coverage and closure options, and more clinical features, such as access slits and pocket redesign.
The other promising trend he says to watch is smart-fabric technologies, which are still years from mass market.
“This might allow for vital signs and other diagnostic measure features to be built into the gown, or act as accessories to gowns,” says Przepiorka. “The trend is starting now with wearables such as wrist bands and watches.”
“With sensors embedded directly into the gown fabrics, monitoring would be much less visible or obtrusive to the patient, creating a better environment for treatment and healing,” Stewart says. “Vitals such as blood pressure, heart rate, pulse rate, and fetal vitals could potentially be monitored wirelessly. Other areas of current research include smart textile technology for wound care and drug-based released systems.”
Przepiorka says another trend to watch is the change in patient apparel similar to the changes in athletic apparel to performanceoriented features, such as cooling, wicking, odor control and compression therapy.
Schwartz agrees that there will
Notice Anything?



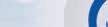

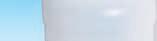








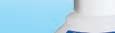
InkGo® Is Now Odor Free!
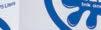
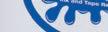



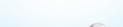
InkGo has been reformulated to remove its odor… and to improve its performance.




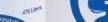




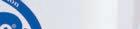
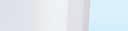
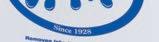

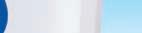




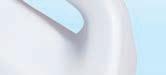
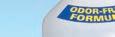
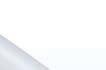
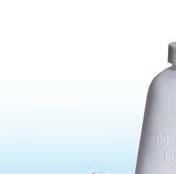
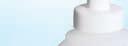
InkGo is still the environmentally friendly,* safe way to remove ink stains from all types of fabric. It’s still great at removing autoclave tape and adhesives. And since it’s odor-free, InkGo is more pleasant to work with.

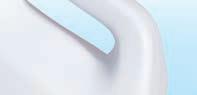


Does odor really matter? As more drycleaners position themselves as good environmental stewards, keeping chemical odors in the plant to a minimum can help them differentiate from their competition. And odor-free is a real plus if you’re working on ink for an extended period of time.
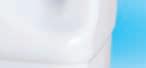
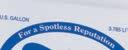
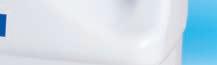
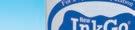
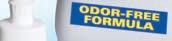
Now that’s worth noticing!
*InkGo is Biodegradable and is California Prop-65 and California VOC Compliant.

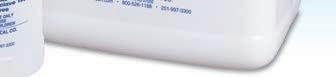
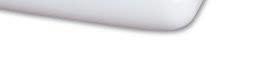
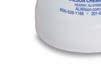


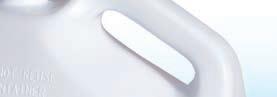
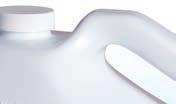
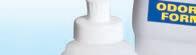

Become a STAIN WIZARD at ALWilson.com
To learn more, visit ALWilson.com or call 800-526-1188 A. L. WILSON CHEMICAL CO.

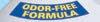
Sanitary AVIOD THE HIGH COST OF ALKALINE HYDROLYSIS
in the air, on linen, in the water and on employee hands. The toolkit employs a proprietary extraction technique that is designed to recover a more accurate representation of bioburden load on laundry media; it is vastly different in scale from anything else currently available in the industry.
With regular monitoring, the toolkit lets operators know how well their laundry processes are performing and whether their standards are on target as originally intended.
There’s a saying in laundry that it’s easy to get healthcare textiles clean, but the real challenge is keeping them clean. There are countless possibilities for HCT contamination on the journey from the washer exit to the patient’s skin. HCTs must be protected from potential contaminants every step of the way along this dangerous journey.
During transport within the laundry, they must be protected from contaminated employee hands, contaminated surfaces, contaminated conveyers and contaminated air, to name a few. During transport from the laundry to the hospital, they must be protected from contaminated carts, contaminated trucks, contaminated hands, as well as contaminated air. Covered and protected HCTs every step of the way is imperative.
Maintaining the quality and cleanliness of processed HCTs prior to use is a shared responsibility. This maintenance phase is the last part of the overall laundry process of preparing reusable fabric items for use in the next clinical setting, and infection prevention is central to its success. It calls for a collaborative effort between laundry operators and the healthcare professionals in the recipient healthcare facilities: nurses, environmental services technicians and infection preventionists.
Effective control of inadvertent environmental contamination of HCTs requires commitment and diligence from all laundry operators and healthcare professionals who manage the production and use of hygienically clean HCTs. Staying on top of these responsibilities can be made easier through the use of checklists such as those provided by HLAC.
A healthcare facility looking for a reliable partner to develop or enhance their linen strategy need look no further than to their healthcare laundry professional. This is especially true if the laundry is HLAC-accredited.
A good practice is for the hospital-based infection prevention team members to treat their healthcare laundry professionals as part of their extended team, where there’s an ongoing sharing of updates in infection control and prevention efforts and in the regulatory and licensing arenas.
Important to this team-style relationship is for facility professionals to visit the healthcare laundry to become acquainted with the personnel responsible for administering the laundry. In fact, the laundry should be open to at least yearly visits from their healthcare customer. These visits are more productive when they’re treated collaboratively. Critical here is open communication, cooperation and collaboration between the healthcare facility and the laundry profession.
On-going education is key. This is where trade media, like American Laundry News, play an important role by providing opportunities to present discussion of relevant issues, challenges and solutions.
JOSEPH RICCI, TRSA

Requests for proof that laundries are producing clean, sanitary linens are more common when academic, professional, business or consumer media call attention to linen. This includes the research connecting linen to C. diff and Mucorales published since October, which generated attention not only with readers of the journals where it appeared, but also with other publications that reported on it.
Such widespread publicity often triggers hospital administrators to seek assurance from their infection prevention and/or environmental services teams that their laundries are producing clean linen. Those teams then turn to our members for proof; often it’s proof of certification.
TRSA’s Hygienically Clean certification requires launderers to test samples for microbial content. Some certified operators provide reports of these tests to customers, but they’re rarely requested. Although routine microbiological testing is relatively new to North America, introduced here by Hygienically Clean in 2012, healthcare professionals are recognizing its importance.
The authors of the Mucorales study urged these professionals, their laundry counterparts and public health officials to collaborate in developing reasonable standards for testing. This research deployed the same protocol Hygienically Clean uses to detect total microbial content: a replicate organism detection and counting (RODAC) plate test.
Test results from linen samples are the most definitive way for a laundry to show its linens are hygienically clean. If a Hygienically Clean-certified laundry is asked to provide proof of testing, we suggest presenting the results of the USP 62 procedure that confirms the absence of specified microorganisms including Clostridium (the C. in C. difficile).
Other tactics include sending a copy of the Hygienically Clean certificate or results of more linen sample tests. Without this routine screening, laundries typically don’t portray their product quality, they present evidence of the effectiveness of their processes. This is an important step in building customer confidence that certification also provides.
Further indications of process effectiveness include documents such as a narrative that describes each step in processing, identifying equipment from soil sorting to delivery, or a description of wash processes covering formula time, temperature and chemistry.
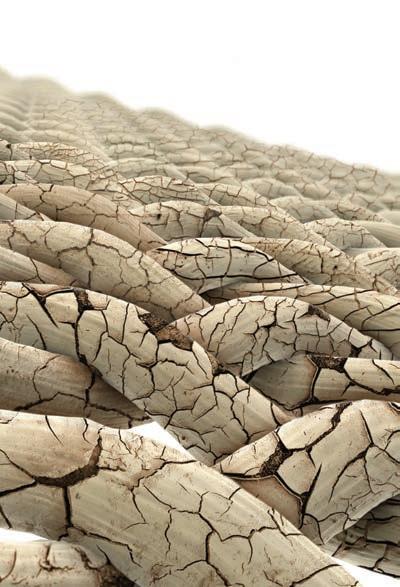
Cleaning schedules for the laundry and trucks can be shared, too.
At the Executive Roundtable at TRSA’s Healthcare Conference in November in Charlotte, participants described an influx of new products and processes to prevent infection and minimize the risk of hospitalbased infections (HAIs) through the use of silver, copper and chlorine in textiles; newly formulated wash chemicals; ozone injection; and other initiatives.
When such products emerge, many laundries view them with a healthy dose of skepticism, noting the specific processing requirements needed to handle them, especially from washing to finishing. Those less disruptive to existing processes and less costly are more likely to become the subject of experimentation and perhaps adopted into a laundry’s mainstream production and service.
When it comes to transport of goods, the Hygienically Clean standard identifies critical
best practices for this function. Trucks need to be either steam-cleaned or cleaned with an EPA-approved cleansing agent/disinfectant and water solution, accurately mixed as directed by the manufacturer’s instructions.
Trucks should be swept daily and decontaminated at least twice a month.
Clean textiles must be well protected during transit. Laundries must package and transport them by methods that ensure their cleanliness and protect them from dust and soil during inter-facility loading, transport, and unloading, as stipulated by the Centers for Disease Control and Prevention (CDC) and its Healthcare Infection Control Practices Advisory Committee (HICPAC). Carts need to be covered, with reusable cart covers cleaned after every use.
Containers and carts used to transport soiled linen must be properly cleaned before they are used to transport clean linen. Separation must be maintained on trucks between soiled and clean.
Drivers must be trained on proper hand hygiene, with hand sanitizer and gloves available on the truck. They need to wear personal protective equipment (PPE) when handling soiled textiles and remove it when they handle clean ones.
Healthcare facility management needs to develop and maintain a written policies-andprocedures manual outlining their own best practices for the various aspects of healthcare textile handling. Input should be welcomed from the facility’s professionals in infection prevention, risk management, environmental services and quality management. Such a manual serves as a guide for training new staff
members and should be used for monitoring and evaluating the linen-handling process. Maximizing professionalism in this function is critical.
Lynn Sehulster, formerly CDC’s top expert on linen and laundry, now a consultant, said that transport and storage of clean linen “is the part of the overall process that is most vulnerable to outside contamination.” Recognizing that the cleanest textiles delivered to healthcare facilities are vulnerable in this respect, Hygienically Clean certified laundries collaborated to produce Handling Clean Linen in a Healthcare Environment, an eight-page guide to assist healthcare professionals in developing a manual.
The guide suggests procedures for transportation, storage and distribution. For example, storage closets need to be properly disinfected and staff must practice good hand hygiene when carrying clean linens, which shouldn’t be taken into patients’ rooms until soiled linens are removed.
Laundries and healthcare facilities should continue to communicate on the subject of hygienically clean linens as much as practical, where appropriate.

At the TRSA Healthcare Conference, presenters from Crothall Healthcare (Liz Remillong and Diana Smith) discussed the importance of managing customer relation ships and expectations. Typically, laundry personnel are prominent contributors to linen committees. Motivated by merchandise inventory concerns, they provide expertise on utilization, linen awareness, PAR levels and linen loss. But they can also help customers perform linen quality audits, take surveys and develop action plans.
If a customer isn’t properly handling clean linen, these tactics bring the situation to light. It’s not really a laundry’s responsibility to perform these, but it’s possible that the cus tomer’s poor transportation, storage and dis tribution practices will contaminate linen and the laundry will be incorrectly blamed for it.
Healthcare facility linen rooms are a flash point. Individuals responsible for handling textiles every day can be trained and compli ant with transportation, storage and distribu tion rules, but if linen room doors are left open, visitors and patients may take linen, posing a contamination risk. They can make a mess of storage shelves by rummaging through them as they look for the type of textile they want.
Carts in the linen room and left elsewhere unattended are vulnerable, too. Anyone can dig through the bottom of a cart and get what they want. It’s best that linen rooms are always locked, permitting only staff to enter, and shelves are organized and labeled, enabling nurses to easily find what they need.
address the needs of our laundry partners from a processing standpoint as well.”
Rossmiller adds that material for all healthcare textiles continue to evolve to make products that improve patient com fort and facility value.

continue to be rapid advancements in fabric technology which will subsequently affect patient apparel offerings in the future.
“We anticipate ourselves, as well as other patient apparel suppliers, expanding offerings to cover all acute and non-acute healthcare settings,” he shares. “We are frequently looking at new designs that not only help to address the healthcare system’s needs and new monitoring technology but
“The industry has wanted better patient gowns for years,” Berg says. “Every year it seems some major news outlet runs an op-ed piece complaining about patient gowns and wondering why they can’t be constructed differently, better, nicer, more dignified, etc.
“My answer is because the cost-benefit analysis hadn’t progressed to the point of making a change. But if it hasn’t so far, it shortly will. In fact, it already has.”
Make best use of employees, then plan for finding new talent
BY BILL BROOKSRIPON, Wis. — Conversations with on-premises laundry managers are a little different today than they were in the past. Time was that managers were solely focused on just keeping machines turning, discussing ways to increase efficiency, improve quality and keep employees from bypassing processes or from engaging the rapid advance to get out of work earlier.
While keeping the machines turning will always rank high in conversation, today, labor is top of mind. However, it’s not just top of mind for laundry managers. Getting and keeping employees is a challenge facing most business—no matter if it’s manufacturing or service-focused.
BY THE NUMBERS
Attracting and keeping employees right now is a tall order, and the reason is because it’s a seller’s market.
Unemployment is low … really low. With the current rate at 3.7%, you’d have to go back roughly 50 years to see a better figure.
Again, laundry managers aren’t just competing against one another for employees, they are competing with a host of other industries. The bottom line is that workers are in short supply, and laundry managers—in whatever industry they are supporting—need to do all they can to attract and retain quality employees.
START WITH A PLAN
Attacking this issue can and should start from within. During tight times, the popular saying is “do more with less.” That’s the statement that really should drive a laundry’s first steps through a focus on getting a handle on the operation as a whole. Is our operation as efficient as possible? Could we manage the daily throughput requirements with fewer hours or less people?
Before banging your head against the wall trying to fill staff positions, you first must understand your operation and if you need to fill all the positions. That means having a grasp of costs, cycle times and staff hours. Without a true understanding of what your operating costs are, managers aren’t equipped with the data to improve the situation.
Laundry management systems are becoming the norm in providing this information. Data goes far beyond just what cycles are being selected.
One example I can offer relates to a hotel property that had recently opened in Oregon. Despite new, high-performance equipment, the laundry was not keeping up and was outsourcing once a week. It seemed an additional shift might be necessary.
However, digging into machine operations data showed that there were significant process breakdowns that were not
only costing the laundry time, but also money. With this information, they were able to correct problems and meet the daily throughput volumes without outsourcing. In addition, the laundry could actually meet those numbers with less staffing.
Moral of the story is, before filling or increasing staff, look at your operation objectively to determine if it’s truly necessary. If you don’t have data to help in this review, you are, quite frankly, flying blind.
THE BASICS
As you continue to set a baseline on the overall efficiency of the operation and where improvements can be made, one seemingly small area can have a major impact is in loading equipment. Loading to full capacity is low-hanging fruit when it comes to staffing. The simple act of under loading machines can add additional loads onto the day, which again impact staffing.
Again, technology in the form of a laundry management system can offer warning signs that your laundry is suffering with this condition. Frequent out-of-balance errors are likely caused by staff under loading the washer-extractor.
This issue impacts efficiency and staff time a number of ways. First, the machine is wasting water and chemicals—formulas are created for full loads. Regular under loading also necessitates that more loads need to be run daily. In addition, the under loaded washer-extractor likely is not hitting its full extract speed because of the out of balance condition. That contributes to more water left in loads, which requires more drying time and wastes additional staff time.
Make no mistake, while under loading
seems like a minor issue, it has a real impact and these are real staff hours (and money) being wasted.
Just training staff on what full loads should look like can help reduce the number of loads being run and trim staff hours.
Similarly, over drying of loads also wastes utilities and staff time. Technology, in the form of accurate over-dry prevention systems, can again help overcome this problem and further trim staff time.
NEXT-LEVEL THINKING
If laundries are running at peak efficiency and still struggling with staffing up, it may be time to think outside the box. Is cross training other employees outside the laundry an option and vice versa? Sharing employees between departments can not only take pressure off hiring, but could offer greater job satisfaction as employees get variety.
Build in some flexibility in scheduling. Can you leverage the delayed start feature on some equipment to stagger staff scheduling? Flexibility is almost always a desired perk for employees.
Is raising wages a possibility? If you are leveraging technology to bring greater efficiency in utilities and staffing, those savings could be tapped to raise hourly wages to reduce turnover. It’s also incumbent upon managers to do more than manage the throughput workload, they also must engage with employees. Part of that comes with laying out opportunities to advance in the laundry or even outside (see the cross training). Career progression can go a long way in eliminating turnover and getting new hires in.
When it comes to recruiting during a
labor shortage, you have to identify the things that you absolutely need in the person and what you are willing to train on. Make it exciting for a candidate to come to a new opportunity, where they get to learn and be challenged. People don’t leave for the same job they are already doing. Invest in your people and their development and recruiting will go much smoother.
In approaching advertising for open positions, don’t just post the job and hope you get applications; tell a story and sell them on why they should want to work with your team. Also, make the interview process special—think conversation versus interrogation.
FINAL THOUGHTS
Our current labor shortage is only going to get tighter, evidenced by December 2018 job growth of 312,000 positions, which surpassed expectations. And during tight times, managers must figure out first how to achieve maximum efficiency by getting a firm grasp on what their true costs and productivity levels are.
From there, it’s about dialing in processes, hiring quality staff and keeping them happy through flexibility, incentives and other activities that build satisfaction and engagement. ALN
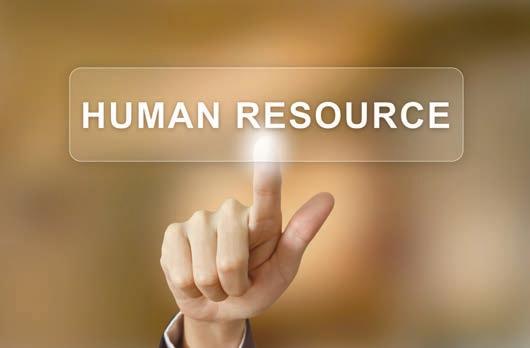
Bill Brooks is the national sales manager for UniMac, a provider of on-premises laundry equipment. He can be reached at bill.brooks@ alliancels.com or 920748-4437. Brooks

A tight labor market means managers must understand laundry operating costs, get creative(Image licensed by Ingram Publishing)
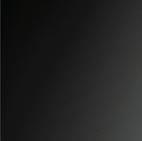

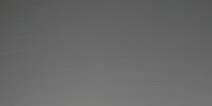
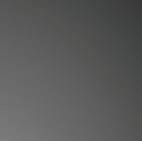
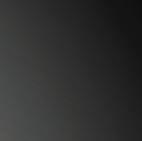
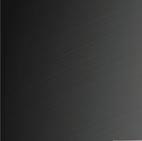

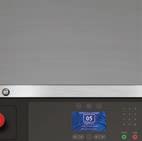
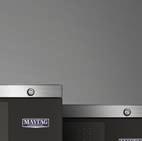
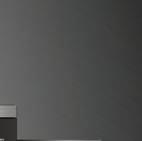
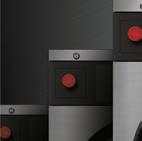

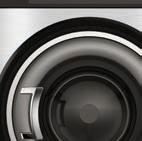
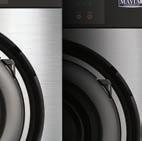
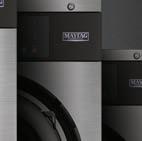
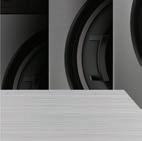
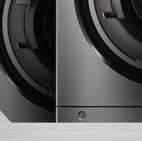
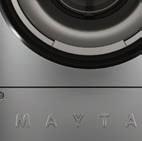
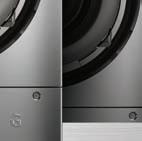
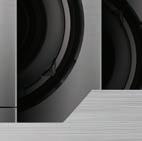
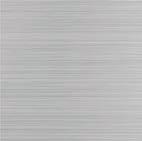
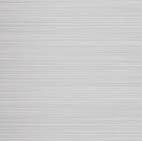
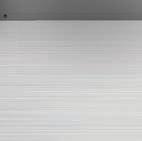
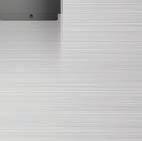
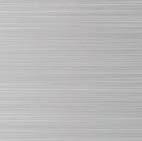
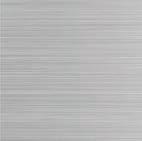
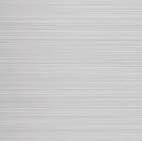
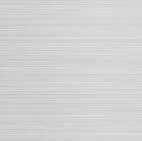
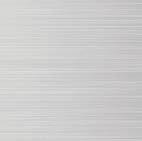
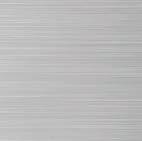


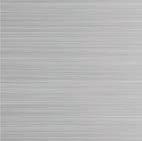

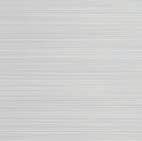



































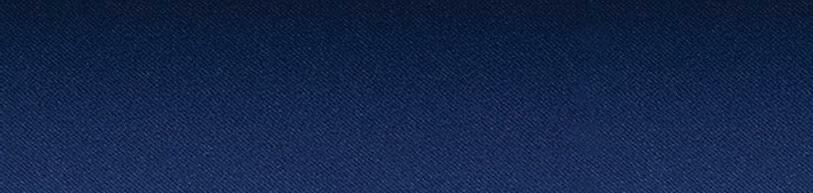
PANEL OF EXPERTS
Making positive steps with vendor relationships




Communication is still key even after the vendor has applied a fix to the problem. If you are dissatisfied with how the vendor fixed the situation, how is the vendor to know if you do not tell them? The vendor will assume the situation has been corrected unless they receive feedback to the contrary.
“The effectiveness of communication is not defined by the communication but the response.”
— Milton Erickson
Because of our industry’s unique business environment, there are occasional difficulties with between end-users and vendors. Lack of transportation options, price increases, resource availability and supply chain issues are causing disruptions globally. However, most of these issues can be remediated with better communication, and if you make a simple action plan, you can avoid headaches for you and your business.
First, and most importantly, you need to address the issue with the vendor. It is important to state your concerns in a matter-of-fact tone, clearly and concisely. It is your decision how you choose to address the issue with the vendor, whether it be a face-to-face meeting, a phone call or an e-mail.

Second, ask your vendor how they intend to address your concerns. Third, set up a timeline to make sure your concerns are rectified within a reasonable timeframe for you. Fourth, follow up with the vendor to make sure they are fixing the problem. Fifth, start making a backup plan if things cannot be worked out with the problematic vendor.
It is much easier to be in contact with a vendor than to wait for a problem to come up before re-engaging contact.
Most vendors appreciate feedback from customers because when there is a problem they want to be proactive to the problem rather than reactive. This is because many times problems arrive in batches and not in one-off instances. Therefore, you might feel as though your problem is unique but perhaps your vendor has seen the issue before and can apply a fix more quickly.
If you use a key performance indicator (KPI) to judge the vendor’s work, maybe it is a good idea to start sharing that data with the vendor. Sharing the KPI keeps the line of communication open but does it in an objective way to avoid people’s feelings being hurt.
If you feel as though, after exhausting all efforts with your vendor, that you still need to find another source for the product or service, do not hesitate to start looking.
If possible, it might be a good idea to find multiple sources going forward to replace the single sourced vendor. Applying a multiple-source method for the vendor might help you avoid any disruptions in your future business by giving you the freedom of being able to change sources more quickly than a single source.
should preferably be a part of the RFP (request for proposal) that is used when you are looking for any type of service. If an RFP was not issued, then it will be up to you to spell out your expectations when a vendor begins calling on you.
is unable or unwilling to resolve the issue.
W e all strive to have good relations with our vendors. No one wants to do business with a company that is hard to do business with or is not meeting our expectations. But there are steps that need to be taken to build and keep good relations with any vendor.
You should always remember that no matter how much you like a vendor, they are a vendor and you are not their only customer. They have a list of customers to take care of and will make time for the ones that demand the most attention.
Vendors need to know, upfront, exactly what you are expecting from them. This
If at any time you are not satisfied with a vendor, you should make it known to them. This does not have to be a confrontational meeting, but they need to know they are not meeting your standards. If you expect twice-amonth service but they are only coming once a month, then you need to make it clear to them they are not meeting your expectations. The moment you accept once-a-month service you have changed what they believe your expectations are.
When purchasing new equipment, it is always good to check references. Almost all manufacturers build good equipment, but what separates them is how good their post-sales service is.
There have been many equipment manufacturers that have come out with a new machine that laundries jump out and purchase only to be woefully disappointed when the machine has a problem and the manufacturer
Service is a cost that any good vendor has figured into their initial bid. Always be careful jumping on the lowest bid that is presented to you. It is usually the post-sales service that is being removed to allow them to give the lowest price.
Poorly engineered, ugly, cheap and a great punch line for comedians. But their customer service is impeccable. Humans answer the phone on the first ring and the service representatives are considerate, responsive, and professional. Which company’s products would you choose around which to bet your airline company? I was right! You chose Company “A”!
Laundry equipment is a lot like airplanes in this regard. Quality products usually win out over quality service. Great service can’t suddenly make a poorly engineered product great. But why can’t we have both?
L et’s say you are the CEO of an airline company. You have two airplane manufacturers to choose from. Company “A” produces the top-of-the-line, safest, most durable, efficient and speedy airplanes. They have a 100% safety record. But their customer service is terrible. It’s impossible to get a human to speak to you and when you do, the person on the other end is rude and unhelpful.
Company “B” produces the “Yugo” of the airplane world.
In our industry, some of the greatest and most innovative products were engineered and manufactured by laundry industry engineers. Service and support, while critical, may have come as an afterthought.
Also, realize that highly performing service and support organizations require resources and time. Often a fantastically engineered revolutionary product may have been recently created by a small team of professionals without the benefit of an existing huge support infrastructure.
“I’m working with a vendor, and I really like the product, but I find their responsiveness to be lacking. What suggestions do you have for steps I can take to improve the relationship to help ensure success for both of us?”Commercial Laundry
Typically, when a company is lacking in responsiveness, it means that they have a breakdown in their support infrastructure. This could be as simple as one bad hire that happens to be facing you, the customer. Or it could be a more systemic problem, such as an inadequate customer call management process/ system, not enough qualified support staff/resources, or multiple bad hires. Either way, you get what you tolerate.
Therefore, it is best for you to notify the ownership of your subpar experiences with their support organization. Any ownership team worth their salt will want to know this information and will take action to remedy it.
Where possible, build a partnership with senior management, and be part of their solution to fix their support. Help them understand how their poor responsiveness impacts your company. Consider drafting and signing a formal agreement with them, where they guarantee a certain service level, with consequences if they fail to perform. If they are a reputable company, they should agree to this.
If support is so bad that it outweighs any benefit of the great product, then move on to a different product from a different vendor. The greatest piece of wash equipment in the world is worth nothing if you can’t get parts in a timely manner. The most innovative textile product is worth nothing if the company will not respond and deliver timely orders.
certain is that each individual has a burden that we know nothing about. They may have recently experienced a birth, a death, a sick child, assisting an aging parent, trying to mend a broken marriage or working hard just to make ends meet. Their internal challenges often manifest in the manner the customers are treated.
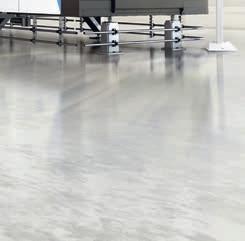
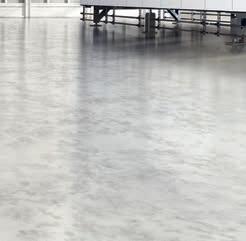
Unfortunately, many times we are the customer and can be a casualty of their current circumstances.
Recognizing there may be an extenuating circumstance and having a short discussion will

often break down barriers and lead to an excellent outcome for all.
When seeking a vendor for the first time, research the company via their website and social media. Ask your team and industry associates if they have experienced working with the vendor; if so, inquire about their experience.
Then, when you contact the vendor:
• Provide the product or services you need and be as specific as possible.
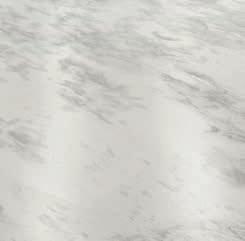
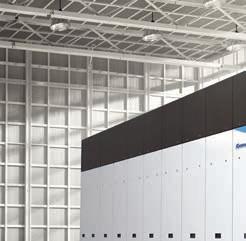
• Explain the timeframe you need the product or service.
• Discuss payment terms, warranty and after-sales support.

• Ask the vendor if communication will be via telephone, e-mail or text.
• If more than one department is involved, request contact information.
• Request and provide the information in writing when possible.
If the vendor is someone you have dealt with for years, and suddenly his or her response time has gone south, be professional and frank.
Examples:
• “Hey Lu, I have noticed a
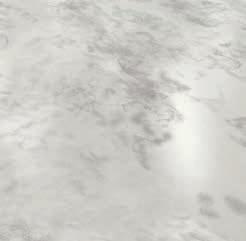
breakdown in our communication lately, is everything okay?”
• “Should I be reaching out in a different manner … maybe through text versus voicemail? Perhaps I am directing my questions to you, when they should be to a different department within your company?”
If a problem persists, or the experience does not meet your level of expectation, contact someone in leadership and ask for a different representative.
H ave you ever experienced a scenario such as the ones listed below?
“That’s it, I’m finished,” Al stated. “It appears we want to work with Mark more than he wants to work with us. I provided the demographics, square footage and the budget for our home search, and he either e-mails us incorrect material, is unable to review the site with us, or his voicemail is full!”
“I would love to be your customer, providing you will allow me”—these were the soft words spoken by a decision maker that could easily afford to shop elsewhere. Her comment was made to the vendor, after first being ignored and then treated with arrogance and disrespect.
Sound familiar? Have you ever attempted to purchase a product or service, or even place a fast food order, and the person was rude, unresponsive or distracted? The only thing we know for
There is someone for everyone, and professionals recognize and respect personality conflicts.

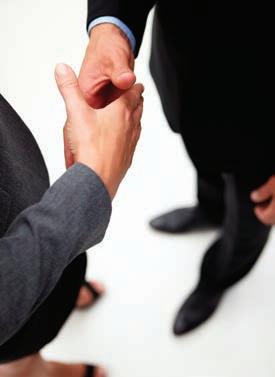
Communication is the key— with the right attitude, aptitude, and willingness to “do the right thing,” honest and respectful discussions will provide an experience that is meaningful for both the vendor and for the customer.
suggest contacting the manufacturer directly to see if they have another distributor. It’s also important to let the manufacturer know how their distributor is managing your account and how dissatisfied you are with their poor customer management.
If you are buying the product directly from the manufacturer, I would recommend following the same steps for contacting and requesting to meet with a local sales manager, as mentioned above.
operators now approach their market segments, but also how we as vendors continue to work with and develop our approach to our laundry partners and customers on a daily basis.
The landscape for all of us has gotten smaller and more competitive. We all need to present our “A” game consistently if we want to grow and succeed in today’s market environment.
A s a vendor myself, I can certainly say customer service is the key to any successful, longterm relationship. If a vendor does not address the needs of their customers in a timely and regular manner, especially after attempts by the customer to reach out, then the vendor does not value the business and has made a critical error.
One of the important characteristics to look for in a vendor is “proactiveness,” especially if the product may require technical service and support. However, if you find that the vendor is falling short and want to continue using the product, here are a few suggestions worth trying.
The first thing is distinguishing whether you are purchasing with a distributor of the product or purchasing directly from the manufacturer. The process of working with each has its differences.
If you are purchasing through a distributor, I would recommend contacting your assigned sales manager at the distributor company, or, if you do not have one, try to contact a general sales representative from the company. Request that they meet with you in person and inform the representative of your dissatisfaction with their responsiveness.
If the sales manager fails to address your concern, attempt to reach out to their superiors or the owner(s) of the distribution company. Sending your message to the top will get your point across, and, while unfortunate that it may take that action, you should be able to get a much better response and improve your relationship with the distributor. I suggest letting them know how happy you are with the product and that you would like to see a better and timely response from them.
If that fails, then I would
If the manufacturer sells the product online or via catalog and does not have local representation, then I would ask them to connect you with a technical manager or sales manager who you can either request to meet with you or establish rapport with to address your needs and concerns. Again, let them know that you are very satisfied with their product but would like to see more visibility and activity from them.
I highly recommend arranging an in-person meeting if it is available so that you can begin to build a face-to-face relationship with the vendor, should that be of value to your operation. If there is no response or if it is an unsatisfactory attempt for their representative(s) to address your needs, learn whether they can offer any other type of customer or technical support.
If after all attempts the vendor fails to meet your expectations, I would suggest beginning to look for either a distributor of the product, if it is available, but if not, search for another vendor that has a similar product that can meet your expectations of customer service and product quality.
During the last week of 2018, while sitting in my office gazing out my office window, I was reflecting on how the year ended. I thought about the many laundry operators I have been fortunate enough to work with over the years and the relationships developed, both strong and, unfortunately, weak. I thought about the opportunities I was able to check off as closed won, but also those I had to mark as closed lost.
Fortunately for me, I have a superior product line and support staff that helps me daily as I work with my laundry partners in helping them not only meet their expectations but exceed them as well.
During my self-evaluation of the past year, I realized that all my customers and partners in this crazy, fun business had choices. They had choices on the products they rent and/or sell and from which vendors they so desire to purchase these items.
In looking at the wins and losses, I thought about not only what I did right, but also, more importantly, what I did wrong. Where and why did I fail to win some opportunities? Several phone calls and in-person calls were made to customers soliciting feedback whether it be positive and/or negative on my performance and what I could do better to help them grow their business. What could I have done to turn some of the losses into wins? As I performed my self-interrogation, I asked myself the following questions:
• Did I not have the right product line to present to my customers?
of-the-box ideas?
• Did I go that extra mile?
• Was I honest?
• Was I an order taker or an order maker?
After this process, I realized that as a salesperson and as a person, I do have my faults. Although I am fortunate to represent a strong company with a superior product line, it is important for me to know my customers, understand their needs and offer suggestions that will take them to the next level. Confidence and enthusiasm breeds success.
relationships already in place and establish new ones going forward. Your feedback is important to me. I cannot correct something if I am not aware of how I am failing or letting you down.
As Peter Drucker once said, and I quote, “The most important thing in communication is hearing what isn’t said.” If you have an issue with a supplier/ vendor, tell them. Share it with them no matter if positive or negative.
This past year was a year of change for many of us in the laundry industry. Together we experienced and witnessed, firsthand, how the landscape of the healthcare market changed drastically with the merger of multiple healthcare systems.
We have also seen and felt the tremors of the commercial laundry market with multiple major acquisitions on both the national level and on the regional level. Additionally, we have witnessed the impact the private equity groups have made with their financial input in our industry with multiple laundries coast to coast.
Not only have these changes had an impact on how laundry
• Was my responsiveness to my laundry partners lacking? Did I not answer e-mails, phone messages or objections properly and on a timely basis?
• Was I friendly in my approach? Did I not smile when meeting with customers?


• Did I ask the proper questions and then offer suggestions to solve situation or needs at hand?
• Did I challenge my partners’ perceptions of what our product line represents and can bring to the table for them to offer to their customers?
• Did I listen to my customers and offer suggestions to help them grow their business? Offer new, refreshing, out-
If you are to succeed in today’s competitive market, you need to protect your business and deal with those who bring value and ideas as well as superior products, service and enthusiasm to the table. We need your feedback and we need to learn from it whether it be positive or negative.
Personally, I want to know if and where I let you down and what I can do for you to make our relationship stronger and help you as you look to grow your business in 2019.
When you meet with your vendors and review your past year or even recent transactions, if you are not happy with our performance, tell us why. It is important for us to know not only why we were successful, but also why we failed or let you down. We cannot correct a wrong or a situation if we do not know one exists.
My goal for 2019 is to revisit my losses and my wins, take your feedback, learn from it, and win those lost opportunities back. I want to solidify the
I t appears that your vendor has forgotten the old sales adage that states, “Make a sale and make a living; sell a relationship and make a fortune.”
With relevant deciding factors such as price and product being equal or merely close and competitive, most purchasing decisions are ultimately based upon relationships. Given this fact, simply researching a new vendor that offers a comparable product could be a realistic solution.
If, however, you see unique value in this particular product, I suggest that you meet with your rep and work together to determine the root cause of these service concerns. Work your way up the chain of command,
Your table linens touch every Customer at every event. Your linen needs to speak their language… fresh, clean, safe, consistent, reliable, and yes elegant. They count on it.
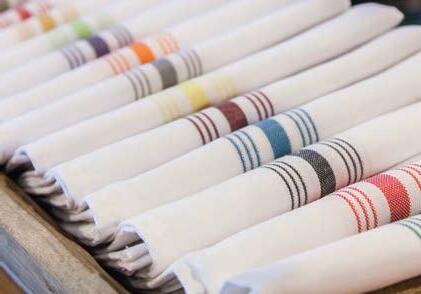
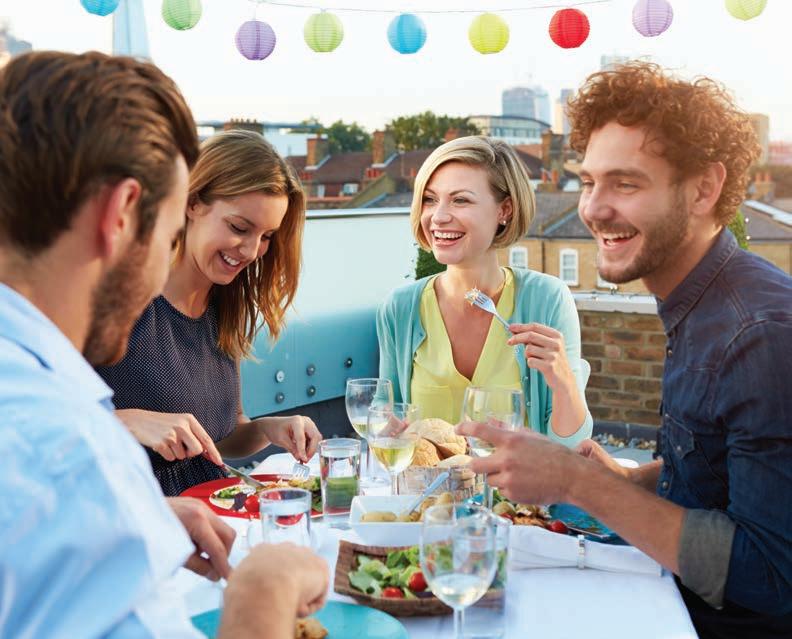
Together, ADI and Milliken have set the standard of linen excellence for decades. USA made Signature Plus fabric. Soft luxurious hand, consistent long-lasting color. Whites that stay white, and colors that stay bright.
ADI American Dawn. The world’s leading supplier of Milliken Signature table linen products. Count on us. Signature Plus is a registered trademark for Milliken & Company for fabrics.
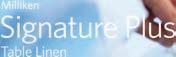
PRODUCT SHOWCASE
SMALL-CAPACITY DRYERS
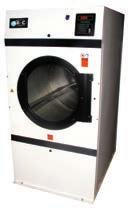
CONTINENTAL GIRBAU INC.
Continental Girbau says its ProSeries II single-pocket commercial dryers are designed with quality internal components, flexible controls, moisture-sensing technology and other features that increase laundry production, end results and energy-efficiency.
Small-capacity models (20- and 95-pound capacities) blend properly balanced airflow, heat input and basket volume for maximum production.
Continental adds that its Linen Life Extension moisture-sensing system offers 12 programmable dryness levels from zero to 40%. When the load reaches its preset target level of dryness, the system shuts the dryer off to prevent over drying and potential linen loss.
Moreover, Continental ProSeries II Dryers bring complete load-management control with multiple programmable cycle types, time-dry, auto-dry and moisture sensing, the company says. Additionally, the control offers “no heat” and four temperature options, including High, Medium, Low and Delicates. Each one is programmable from 100190 F.
Finally, to ensure dryer fires don’t go unchecked, the company says Pro-Series II Dryers feature an optional Integrated Sprinkler System (ISS), which automatically
senses and extinguishes dryer fires in the rare event they occur.
www.cgilaundry.com 800-256-1073
the demands of continuous use and stands up to the rigors of the most challenging laundry, the company says.
B&C says all of its dryers come standard with a stainless-steel drying cylinder, fully enclosed fancooled motors, cast iron pulleys and a heavy-duty steel base. The DE line has the option of either a standard manual timer controller or an easy-to-use microprocessor.

The large door allows for fast and easy loading and unloading, while the welded steel, fully enclosed cabinet offers energysaving insulation and quiet operation, according to the company.
RAMCO

RAMCO says its 60-pound DE/ DS/DG dryers come with a userfriendly microprocessor control with onscreen display, which has automatic and manual programs to choose from.
The stainless drum has overload protection built in. It has the ability to run in one-way or two-way direction, which can help reduce tangling, according to the company. Also, the heavy-duty drive and door system allows for low noise while running. The drum is designed to resist wrinkle and twining of the fabric.
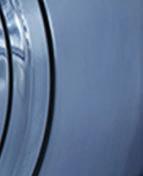
RAMCO adds that the machines have a wool fiber clean system with cool- and hot-air choice programs, which it says is ideal for delicate or high-end materials. Lastly, the large door makes it easier to load and unload materials, and the large window is for ease of viewing the loads.
www.ramcolaundry.com 800-878-5578
B&C TECHNOLOGY
The B&C DE Series dryer line, available in 30-, 50-, 75-pound capacities, and higher, is designed to exceed

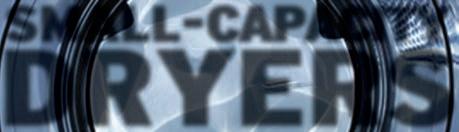
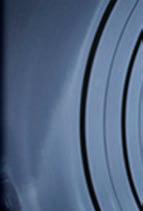
The exclusive humidity sensing system directly measures the remaining moisture, preventing over drying, saving time, money and wear on the goods. B&C reports that when paired with a high-speed washer, the DE line of dryers can dry as fast as 20 minutes.
www.bandctech.com 850-249-2222
standard with variable drum speed, trans-axial airflow and a fully insulated cabinet with double-pane door glass. The sturdy steel-welded cabinet withstands tough laundry environments, and the components contribute to machine longevity and consistent performance, the company says.
Equipped with customizable, easy-to-use Intuitive Micro Controls (IMC), ADC says the machine provides an intelligent, one-touch program selection to enhance productivity. By creating a fully integrated drying system, users can utilize IMC to control all aspects of the drying process to minimize user error and optimize drying time and efficiency.
According to the company, operators can feel confident knowing the Sensor Activated Fire Extinguishing (S.A.F.E.®) System comes standard on OPL models, which helps to detect potential dryer fires—further protecting product investments.
motor uses precise current measurements to accurately detect airflow drops that result from exhaust path restrictions.
www.adclaundry.com 269-923-3000
ADC

Through innovation and engineer-driven design, ADC says that its i-Series Dryer Lineup offers versatility and customized solutions to help maximize facility efficiency. The AD80i is an efficient, single-unit, dryer tumbler designed with operators in mind.

The 80-pound dryer comes
The single-phase reversing basket helps prevent linens from tangling, creating effective dry cycles.

Finally, ADC says the optional Automatic Airflow Compensator (AAFC) helps neutralize high static pressure caused by airflow restrictions to increase drying performance and efficiency.

With AAFC, the dryer’s Variable Frequency Drive-equipped blower
HUEBSCH
Medium- and large-scale laundries require tumble dryers with significant capacity, fast drying power and low maintenance. Huebsch says its 75-pound dryer can provide results in all three areas.

A high-performance heater box, sealed cylinder rims and a concentrated airflow pattern combine to keep utility costs down and the laundry operation yielding maximum throughput volumes, according to the company.
Meanwhile, a self-cleaning lint screen means fast, efficient lint removal from the tumble dryer’s large storage area, which keeps staff focused on moving loads through the laundry.
Huebsch says that by adding in a reversing option to keep tangles to a minimum and the Galaxy™ control, with 30 programmable cycles, the company’s 75-pound tumble dryer will give on-premises laundries years of solid performance.
www.huebsch.com 800-553-5120

involving your representative’s manager if possible.

First, clearly state your concerns, as well as your requirements. Confirm that your expectations are reasonable and realistic, and give the vendor an opportunity to respond and offer solutions. Make it clear to the vendor that these issues may jeopardize future purchases.
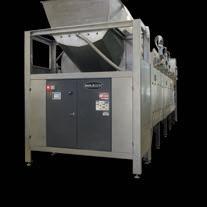

One very effective method for determining root cause concerns and eliminating waste is to perform a “process mapping” exercise with the vendor representatives. This exercise involves mapping out every step of the purchasing process from placing the order to product delivery. Look for unnecessary or redundant steps and any decisions that are involved. Then work to streamline the process by eliminating or reducing these extra steps.
On a few occasions, I have applied process mapping to administrative functions with different teams to great results. Even when evaluating the simplest processes, redundancy and unnecessary decisions are uncovered. The team is then able to streamline the process by eliminating these steps.
Strong vendor relationships are important to any organization’s success. Clearly defining expectations and working together to resolve concerns will assure positive results for all.
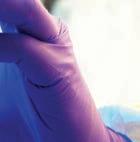
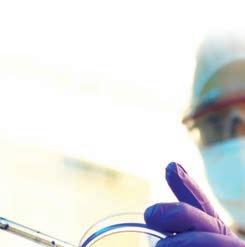
If that didn’t happen then, do it now. Pick up the phone (follow up with a meeting or put it in writing and send them a copy). Don’t talk in circles. Don’t try to be crafty or sneaky or hide your disappointment and or desperation in innuendo or double-meaning. Nobody is going to take you seriously if you can’t say what you need and when. Say it plain and clear.
Don’t be scared to apply a little bit of pressure, but you don’t have to be a jerk either.
Nowadays, I think everyone’s complaint department is social media. The most recent stats I’ve

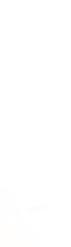
seen are that 55% of customers use social media to complain about customer service. I personally don’t find it that effective in our industry, but more and more laundries and laundry vendors are getting social media accounts so that is changing. If you decide on that direction, remember your own ethics and forewarn them, then copy/ tag them in the post or tweet and don’t be rude. Customer service reps are not as likely to spend time working with a “hater” who’s more interested in being angry on social media than actually receiving help.
Going forward, keep ongoing notes about your vendor’s responsiveness, communication, processes and ethics. Together, be proactive and decide how solutions to unforeseen problems can be efficiently resolved. Be eager to maintain a good working relationship. Keep in mind, this may mean some periodic compromise (again, be sure to note it so your efforts can be used in the future).
My experience is that there are only a few in the company that are truly able to help you during a crisis. So, network, network, network—attend their customer
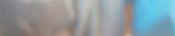
appreciation events, plan a plant event with a short tour and some simple refreshments and invite them, then, build a relationship with the one or two people in the company that you feel you can count on. Call them periodically to say things are good, offer a cleaning discount just for them—they’ll be more inclined to stop by and “check on you.” Yes, schmoozing is effective. Most importantly, make it clear that your main goal is to keep your company’s reputation intact, and that if they negatively affect that, your relationship will change.
I think we have all been there. We chose a product mainly based on the company’s reputation. The majority of the time, the product functions just as you envisioned it would.
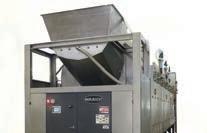

But then, there’s an issue. The severity of the issue determines the type of response you need. Despite your best efforts, you feel stuck with an inferior product or service affecting your business.
Take a breath—think about your current efforts to communicate the problem. Have you talked to your contact? Do you have a contact? The question of serviceability really started when you made the initial agreement with the vendor. Some things are non-negotiable and need to be made clear at the conception of a working relationship. The most important being that service or information requests must be met in 24 hours or less.
JENSEN USA
JENSEN says its JTD series tumbler/dryers are designed for strength and durability, with decades of proven experience. The JTD series is available in 45- and 90-pound capacities, and higher.
Standard design features for the JENSEN JTD series include stand-alone design, touchscreen PLC controls with easy setup and copying of programs through a USB port, reversing cylinder, vertical sliding doors for ease of loading and unloading, built-in
system provides one-touch program selection to minimize user error.
Milnor’s Premier Series dryers range from 50 to 120 pounds of capacity and provide high productivity and efficiency with its trans-axial airflow, variable drum speed and direct spark ignition features.
The company says its design results in shorter dry times while saving money in utilities. The series is offered in gas, steam and electric heat options. Additionally, an optional Automatic Airflow Compensator (AAFC) adjusts exhaust fan speed to improve exhaust flow with increased backpressure due to installation issues.
www.milnor.com 504-467-9591
UNIMAC
UniMac says its 75-pound tumble dryer, equipped with the UniLinc control, not only offers speed and efficiency, but also a high level of control for laundry managers.

lint filter, fire suppression standard on gas models, stainless-steel cylinder, smart indicator light to keep the operator informed of the machine status, and much more.
Gas, steam or electric heating sources are available, the company says.
www.jensenusa.com 850-271-5959
PELLERIN MILNOR CORP.
Milnor says it offers a variety of dryers capable of meeting the production requirements of various laundries.
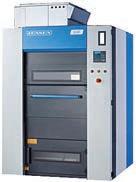
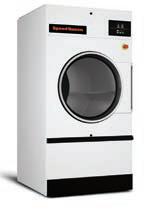
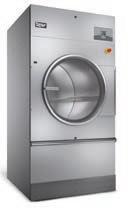
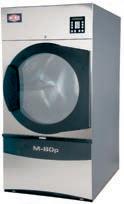
The company says its line of Premier Series small-capacity dryers offers high performance with important features such as double pane glass door and fully insulated cabinet for thermal efficiency, stainless steel baskets and fronts for durability, front serviceability for easy maintenance, self-cleaning lint screen and Sensor Activated Fire Extinguishing System (S.A.F.E. ®)—raising washroom safety to a high standard.
The company adds its intelligent and simple-to-use control
The efficiency story starts with the dryer’s balance between temperature, airflow pattern and usable cylinder space. UniMac, however, says it takes that efficiency to the next level with its Over-dry Prevention Technology (OPTidry).
OPTidry eliminates costly over drying of loads, which wastes utilities and labor, as well as degrades linens. UniMac says its system stops the drying process once the load reaches the ideal moisture level. The end results are lower utility costs, longer life for linens
healthcare facility. Getting the most out of those linens and keeping them clean and scentfree is therefore important to a property. At the same time, laundry operations are considered a cost-center, and finding ways to increase productivity and efficiency can have a direct impact on the bottom line.
Maytag Commercial Laundry says its MDG75PNJVW provides operators reliable performance and features. Easy-to-use microprocessor controls offer countdown display and multilingual readouts to accommodate different language needs—empowering operators to program options based on facility needs. Sealed bearings are designed to provide an extra layer of protection. The sealed bearings are permanently lubricated to help minimize friction.
Maytag shares that singlephase reversing is offered on the MDG75PNJVW. This can save on installation costs as an upgrade isn’t required. The reverse tumble feature helps prevent balling and long dry times.
Dual, powder-coated lint drawers with stainless-steel mesh help dry linens evenly by allowing more airflow to pass through, and are easy to clean. The Maytag® Sensor-Activated Fire Extinguishing (S.A.F.E.®) System comes standard on the MDG75PN. Should a fire be detected, the machine uses a controlled extinguisher to disperse water and alerts that the system has been activated.
longer than a quarter century.
Lavatec says it provides a full range of equipment with a high ROI rate, including small-capacity dryers such as the FL613 and FL623.
These front-loading machines are ideal, small-capacity dryers that offer flexibility and durability for laundry operations, according to the company. The FL line of forced air dryers has a long track record of success, especially with efficiency in comparison to atmo-
and better allocation of staff time.
With the UniLinc Control, UniMac says it gives laundry managers the pinnacle of laundry management, enabling them to see start/stop times and idle time between cycles to track labor efficiency. The control also reminds staff of maintenance schedules and records any machine errors for quicker troubleshooting and repair.
www.unimac.com 800-587-5458
MAYTAG COMMERCIAL LAUNDRY
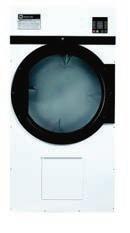
Quality, clean linens and towels are key to any guest experience, whether the setting is a hotel or
Finally, the company says the dryer optimizes energy use with the machine’s solid basket design and dual-pane glass door, which helps keep warm air in the dryer pocket, forcing more heated air through the load.
www.maytagcommerciallaundry.com 800-662-3587
LAVATEC
Lavatec Laundry Technology Inc. says it has delivered dependable commercial laundry equipment for nearly three decades. The company has more than 6,000 pieces of equipment in United States laundry operations alone, some of these manufactured machines have been on the job for
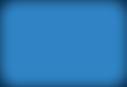
spheric machines.
In fact, Lavatec says some customers have replaced two similar sized atmospheric dryers to reduce their capital costs and saving on their laundry’s footprint space at the same time. This is in addition to energy cost savings.
Ergonomically designed for safe operation with features such as sensor controls, the 55-pound capacity FL613 offers a hinged or sliding door option. The FL623, like the entire FL line, is CSA approved and can be programmed for custom settings to save time and manpower, the company says.
www.lltusa.com 203-632-8777
DEXTER LAUNDRY
Dexter Laundry says its new line of O-Series dryers is designed to give laundry managers “Total Control” over their laundries.
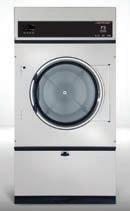
The company says its controls are easy to use, with multi-lingual capabilities and state-of-the-art reporting. Plus, every dryer is designed with innovative technology, such as Dexter’s Moisture Detection System and Fire Response System that operates without the need for water.
The O-Series dryers are available in multiple sizes, including 80-pound capacity. The T-80 is an extra-large dryer with a reversing tumbler option to decrease linen roping and reduce dry times, the company says. The T-80 is designed for versatile installations. It’s available with multiple electrical configurations and features a reversing door.
Dexter says that like all its dryers, the T-80 is built with highquality materials, balanced radial airflow and the right amount of air recirculation to maximize effi-
ciency.
With heavy-duty bearings in a cast-iron housing, the company says there is no doubt that its dryers are built to withstand even the harshest laundry environments. www.dexter.com 800-524-2954
SPEED QUEEN
The union of high-performance technology and user-friendly control options make the Speed Queen 75-pound tumble dryer a great addition for on-premises laundries of all sizes and types, according to the company.
Speed Queen’s Quantum Gold control gives laundry staff control of the drying process and even offers audit data reports on machine operations and advanced diagnostics. As a lower-cost option, the dual digital control offers one-touch cycle repeat and simple selection of drying time, cool-down time and temperature.
A reversing option helps prevent tangling when drying larger items such as sheets. The company adds that the unit’s speed and drying efficiency will assist operations in reining in operating costs, while maximizing throughput.
www.speedqueencommercial.com 800-590-8872
Kansas City hotel moves to soft-mount
OSHKOSH, Wis.— Frequent outbursts by an aging hard-mount washer forced the Hampton Inn in Kansas City to seek help. After years of stress, the washer’s violent vibrations ripped it from its anchor point on the floor.
General Manager Glenn Koch contacted Bruce Kusgen of All Pro Laundry Equipment in Lees Summit, Mo. The solution? A new soft-mount Continental E-Series Washer-Extractor.
Initially, Kusgen tried to fix the existing washer.
“We drilled through the concrete pad and into the floor to install new anchor bolts to tie it all back together,” he says. “Soon after, however, the washer’s inverter blew up, and Glenn decided enough was enough.”
Kusgen recommended a replacement. The old hardmount washer was pulled and a new soft-mount E-Series Washer took its place. Because of its softmount design, the Hampton Inn saved on installation costs.
“Unlike the old machine, the new washer does not bolt to the floor or a concrete pad,” Kusgen says. Rather, it is freestanding and features a spring system that absorbs 99% of all vibrations. It was installed without bolt-down or grout and produces much higher extract speeds for maximized performance.”
The result is greatly improved laundry production and efficiency, according to Koch. This is because the new washer reaches extract speeds up to 400 G-force. In doing so, it removes more water during extract, which cuts dry time. Because dryers operate less frequently, the laundry consumes less natural gas, as well.
With the new washer installation, the Hampton Inn’s onpremises laundry completes more laundry loads per day— without distracting vibrations and noise.
ALN
KEARNY, N.J. — ARCO/Murray recently completed a 57,000-square-foot laundry build-out for Cooperative Laundry here, the design-build contractor reports.
The new facility will serve the New York City metro area hospitality market.
Cooperative’s new facility is one of the most technologically advanced laundries in the United States, ARCO/Murray says. The automated laundry equipment and rail package supplied by Kannegiesser ETECH is fully integrated to maximize productivity and minimize operating costs.
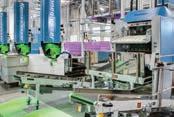
The facility also includes spot cooling
to increase employee comfort, lint fans to improve plant cleanliness, Miura boilers and Kemco process water systems to minimize water and gas consumption, LED lighting to reduce electrical usage, and a centralized control center to track and manage the laundry production.
ARCO/Murray provided a custom designbuild solution including architectural and engineering design, construction drawings, permitting, main utility upgrades, building construction, mechanical/electrical/plumbing installation, and final equipment connections.
ALN
All Pro Laundry’s Bruce Kusgen (left) installed this Continental E-Series softmount washer, and Hampton Inn General Manager Glenn Koch is pleased with its quiet operation and efficiency. (Photo: Continental Girbau)
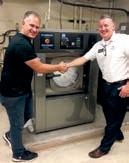
SHRINK
EXPENSIVE DOWNTIME.
You know that when your washers and dryers aren’t running, they’re not making your company money.
Now we’ve introduced a breakthrough that shrinks downtime and makes your washer and dryer production line easier to operate. It’s the UptimeTM intelligent machine manager.
Offered on our side-loading and open pocket washers, WHISPERDRYer dryers, water recycling and process water systems, the Uptime machine management system is a simple but smart control and reporting system. Operated from a touchscreen panel mounted on our machines, this user-friendly solution allows you to:
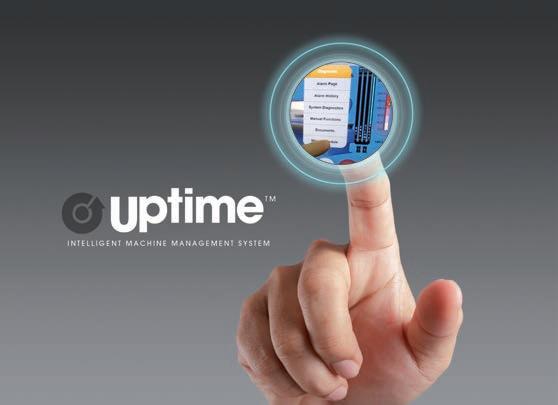
work smar ter. www.ellisuptime.com | 800-611-6806 | 630-250-9222
Receive alerts when it’s time to perform preventative maintenance to maintain your assets, and document that the work was performed
Cut troubleshooting time to just minutes, because the system diagnoses the machine, pinpoints problems, and tells you what to do
Tap into our experts who can remotely access your system and quickly tell you what’s going on with your machines — and what actions to take
Identify and order any needed parts in less time
These are just a few of the ways this Ellis innovation can make your life easier and your business more profitable.
CHICAGO — In laundry and linen services, benchmarking, the process of checking against a standard, helps in the effective usage and processing of textiles.
But what standards should be used for such measurements, and how can improvements be made?
Two experts discussed these topics during the webinar Benchmarking Basics, presented by the Association for Linen Management (ALM).
UTILIZATION
Janice Larson, vice president of Clinical Resources and Consulting for Encompass Group LLC, a manufacturer of healthcare textiles and products, began the webinar discussing benchmarks in linen utilization, specifically hospital linen utilization.
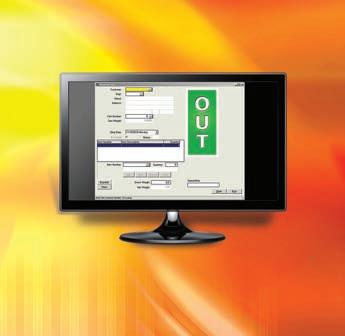
“The most top level is something known as pounds per adjusted patient day (PPAPD),” she says. “Basically, the calculation is to get total processed, clean pounds divided by adjusted patient day.”

An adjusted patient day is the inpatient, room-night census, adjusted for outpatient activity. Larson says it’s a financial calculation that is the same calculation throughout all hospitals because it has to be reported to the American Hospital Association.
“Every hospital calculates an adjusted patient day on a monthly basis,” she says.





Another common top-level
benchmark for linen utilization is pounds per patient day. Larson says this mark uses the same total processed, clean pounds divided by the in-patient census only.
The last benchmark she says has been used is cost per adjusted patient day.
“This is a pretty complicated benchmark,” Larson remarks. “There are so many variables contributing to cost per piece, one being cost per pound. Another is the replacement price per item. Is there tax included in your replacement? Is there freight included? Then there’s product life, the quality of the products that you’re buying. National contracts. It can be extremely complicated to arrive at.”
Larson points out that PPAPD benchmark in hospitals has been going down consistently over the past 20 years.
“While I’m proud to say that some of this is due to better linen utilization practices and more awareness around how to drive linen down while being able to maintain patient care both on the part of the hospital and on the part of the commercial laundry as they partner,” she says, “there’s also that dynamic where outpatient activity is increasing.
“The dynamic of outpatient in the adjusted patient day means that you have less pounds contributing because outpatient activity uses less pounds, that also contributes to the adjusted patient day number trending down, that number being diluted by more outpatient activity
in laundry/linen
and less outpatient pounds.”
Larson then moved beyond toplevel measurements to the “next level down of benchmarking,” which is items by adjusted patient day.
“In other words, taking your adjusted patient days and looking at individual usage by item,” she says.
After that, the measurement looks at pounds by activity per department.
“Honestly, benchmarking usage by individual item and by pounds per activity in a department is the level of detail that kind of tells you where the bodies are buried,” Larson quips. “This really tells you what items and what departments you should be focusing on, that have the most opportunity to improve. Nurses are scientists. They really rely on data to make decisions. You need data to convince them that, A) there’s a problem, and B) there is an opportunity to change. This data is key to get their buy-in that they to change utilization processes.
“The value you get from that data is so much greater than dealing with just the top-level benchmarks.”
Larson cautions that people often get “national average” and “best practice” confused. They are not the same thing.
“If anyone says the best practice linen use for a 500-bed hospital is 12.2 per adjusted patient day, they’re really not referring to best practice,” she points out. “They’re saying that 12.2 might be the desired result, something you want to build toward. Best practice is not the number. It’s products and pro-
cesses and how they’re being used and in what quantities that make up best practice.”

The problem with the calculating by cost is the variables associated with the products and the quality of the products, both of which can affect the cost, Larson shares. The variables can also influence weight.
“If you are benchmarking yourself against a hospital who’s using a lesser-quality product, they are naturally going to have a much lower usage than you do in pounds,” she says. “Also, when you’re looking at pounds per adjusted patient day, you have to say is this hospital a big user of reusable underpads. In some cases, a hospital may be using more disposable products.
“You have to also think about what percentage of poundage is scrubs. More hospitals are providing scrubs compared to the previous decade.”
Larson cautions that when it comes to hospital utilization benchmarking, real data must be gathered and collected, and it has to use the same factors and calculations in order to represent a benchmark that is reliable.
“To me, it’s important that benchmarking be derived by data that you can you can go back and fact check,” she says.
Another caution: Benchmarking against different kinds of hospitals and different kinds of units. For example, comparing an acutecare hospital against a long-term care hospital, each of which has very different practices and level of nursing care.
“You also have to make sure you’ve established a baseline in the

same way the benchmark is calculated,” she adds.
Larson also sees hospitals that don’t research best practices thoroughly.
“When you do find a best practice that is delivering an outcome that is a lower pounds per adjusted patient day and you want to adopt it, if you don’t really research how that’s being done and what products are being used and what kind of patient outcomes they’re getting, a change can really backfire,” she points out.
Also, hospitals have to think about customer and staff satisfaction. “If staff isn’t happy with the changes you’re making and the benchmarking you’re doing, they’re going to sabotage this,” she shares.
Finally, Larson cautions against thinking that there are benchmarks for every department and every item.
“It might be a level of complexity that is impossible to track,” she says.
LAUNDRY PRODUCTION
Michael Dodge, a production consultant for Gotli Labs (GLOBE), a company based in Switzerland with an objective to create a new system that can manage all resources in a laundry, then shared about benchmarking in laundry production.
“What we kind of say is that data is the new gold,” he says. “We have to kind of go into the vault a little bit and pull the data that we need. We have to get the numbers we need to do our benchmarking.”
Dodge says there are many resources as far as production data.
“We can go ahead and pull data
from our laundries, our washroom, our soil area, our finishing equipment,” he points out. “There are a lot of areas where we can pull data into a report that we can look at and benchmark ourselves.”
There are four main areas in a laundry for managers to benchmark, according to Dodge: soil, washroom, finishing and pack out.

“Be aware of where you were in the past and what you need to do to improve,” he shares. “You have to know what the limitations are of your system; there’s always a limiting factor in a laundry. When we need to push product through, how can we do that?”
Dodge says the first elements normally examined in a plant are direct production hours and the dollars related to that, including overtime. Also, look at supervisors and their labor hours. Then look at standard performance, whether those are indicated by pieces per hour going through a piece of equipment or pounds per operator hour (PPOH) going through the entire system.
“I normally see some type of spreadsheet out there that most laundries use, broken down by department, showing number of hours along with what the cost is and other factors,” he says. “Cost of hours and overtime, and pounds being processed.”


Dodge stresses that a laundry should compare itself to itself when
it comes to improvement, and not against other plants. This is because there are numerous variables that impact laundry operations.
“There are different factors that make them get their PPOH,” he shares. “One is automation. What type of automation levels do you have as far as your equipment?
Your textile mix, that’s a huge one. COG or rental? Materials handling is the biggest one I’m seeing for industrial, hospitality, healthcare. Look at the input measurement. Sometimes it’s not an apples-toapples comparison.”

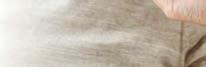
Another type of comparison Dodge sees laundries making, that they shouldn’t, is price per pound. There are even more variables when it comes to price, because
the revenues might be different. Costs can be different by area of the country, labor costs and the type of customers the laundry has.
Finally, laundries might be comparing quality, when the question really is, “What do our customers expect going back to them?”
So, what benchmarks can a laundry get started with? First, Dodge looks at production processing costs.
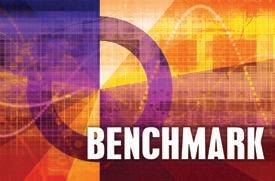
“You could look at a lot of factors, like therms per pound or kilowatts per pound or gallons per pound, but here I just want to get some type of range for you to be thinking of, just benchmarking,” he says. “Between 2 and 5 cents per pound for gas and electric, but know where you’re at. Five might
not be bad for your location. Water and sewer, between 1 and 2 cents per pound, and chemicals between .5 to 1.5 cents.”

Dodge then says to increase PPOH, there are three things a production manager should be doing, and being aware of, in the laundry. First, does the laundry have product for all of its equipment and different areas and work stations? No station should ever be idle, he says. Second, make sure the equipment is working properly, and third, make sure operators are doing what is expected at each of the positions.
“These three things, if you make them work, your PPOH is going to be where it should be,” he says.
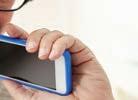
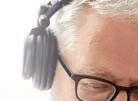
In terms of PPOH achieved in laundries, Dodge says he has heard of a range from 100 PPOH to plants being designed to push 225 PPOH.
“However, you have to be aware of factors mentioned earlier,” he cautions. “Just because you’re at 100 PPOH doesn’t mean you’re bad. That may be the highest you can get with the plant as it is right now. Realize where you’re at and what you can do.
“Still, you can almost always improve 10 to 15% by paying attention to the operations in your plant.”
Dodge says the key to really understanding what’s going on in a laundry system is to have accu-



rate standards.
“I am a firm believer that the foundation of production is having standards for all your different areas: soil, washroom, finishing, pack out,” he stresses.
However, production standards have to be fair to the operator and the supervisor, Dodge points out.
“A trained and skilled operator over the period of eight hours, with a fair and reasonable effort, should be able to get 100%,” he says. “That’s just average. You’re going to have people who can do over 100%. The reason for these numbers is not to say he or she isn’t doing the job the way they should, but to understand why. That’s the important part.”
Every standard should have some documentation, a written description of the job so the operator knows what’s expected, according to Dodge. On top of the documentation, he says there should be some type of time element that shows how the standard was arrived at—know what a plant can do, and each department.
“You have to have the number and be confident in the number—don’t just have numbers out there,” he says. “The best thing you can do is have constant feedback with the operators, coach them, show them what they need to do, let them know how they’re doing. What you’re trying to do is reduce any idle time.” ALN

CHECK OUT WHAT YOU’VE MISSED:
Sheets,
and More: A Look into Hospitality Laundry/Linen Services



In this episode, Phil Jones, director of laundry for Sheraton Vistana Resort in Orlando, offers his view of hospitality laundry, from its challenges to its future.

Behind Bars: Correctional Facility Laundry Operations



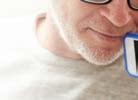
Todd B. Jenson, formerly the laundry supervisor at the Ramsey County Correctional Facility in Minnesota, talks about the challenges and rewards of jail laundry operations.
Jon
Revealed
today and in the future.
Track Career
SYRACUSE, N.Y. — Frederick G. (Rick) Rudmann has been appointed president of laundry equipment manufacturer G. A. Braun Inc., says J. B. Werner, CEO and chairman of the board for the company.

Rudmann will be based out of Braun’s corporate headquarters here.
“Rick’s vast knowledge and experience includes 30-plus years of strategic planning and business analysis in various manufacturing arenas,” Werner says. “Our foundation of unrivaled product quality and customer support will continue and advance. Under Rick’s direction, we look forward to adding new technological innovations and enhancements to our product portfolio.”
Werner believes Rudmann will further strengthen Braun’s capabilities and its ability to continue to develop solutions for its customer base, both domestically and internationally.
HLA expands business development team
SAN DIEGO — Rick Gaffney has joined the Healthcare Linen Alliance (HLA) to head business development and partnerships, HLA reports.
HLA is one of the largest commercial healthcare linen service providers in the nation, serving more than 120,000 hospital beds daily and more than 1,800 customers.
Gaffney has spent much of his career in the commercial healthcare laundry industry. With experience that extends from operations management to service to sales, HAL says he brings his extensive background in the industry to the team.
“The Healthcare Linen Alliance is the better alternative for national healthcare laundry, and I’m happy to be part of the team and share that message,” Gaffney says.
Gaffney has years of experience working in commercial laundry operations, on turnarounds and increasing revenue by focusing on quality and hiring talent. Throughout his career, HLA says he has a demonstrated track record of helping businesses improve their operations, increase their reach and ensure the right team is in place.
“We are very pleased to welcome Rick to our team, and I am confident that through his efforts we will continue to expand the reach of the group across the country,” says Randy Bartsch, founding member and chairman of the Alliance. “As a group, with our combined size, scale and coverage, the Alliance is helping hospitals and health systems drive down overall laundry and linen costs.”
The HLA group includes Century Linen & Uniform, Ecotex Healthcare Linen Service, Emerald Textiles, Logan’s Healthcare Linen Systems, Paris Healthcare Linen Services, Superior Health Linens, Textile Care Services and Up to Date Laundry.
CG West adds parts, warehouse assistant
SANTA FE SPRINGS, Calif. — Sergio Lomeli of Los Angeles recently joined Continental Girbau West as parts and warehouse assistant, the company reports.

Lomeli brings 22 years of experience to the distributorship.
In his new role at CG West, Lomeli juggles multiple duties, including parts order processing, daily communication with customers, inventory stocking and organization, warehouse staging, and maintaining accurate inventory records, among others.
“I’ve known Sergio for about 22 years from the laundry parts department business,” says Patty Torres, CG West manager of Product Support. “He brings ample parts and customer service knowledge to CG West and great value to our company. Sergio is a wonderful communicator and person who provides top-level customer service.”
“My knowledge in parts allows me to provide excellent customer service,” Lomeli adds. “My goals in this position are to make our customers feel great about CG West and to grow within the Continental family by contributing my experience, knowledge and hard work.”
Kannegiesser ETECH bolsters regional sales management roster
MINNEAPOLIS — Kannegiesser ETECH, which provides washing, finishing, and uniform processing systems, along with monorail, conveyor solutions, and software, has promoted Kelly Outram to regional sales manager for the Western United States.
In addition, the company has hired Mel Davis as its regional sales manager for the Southeast.

The company says Outram has spent the last 32 years supporting sales efforts in the laundry industry, the previous eight years with Kannegiesser ETECH in the Southeast region.
He brings his experience of innovative linen processing
systems design to the Western region, according to the company, and will be serving the healthcare, hospitality, linen rental and industrial uniform processing laundry segments.
Davis brings approximately 15 years of laundry operations experience to the team having worked previously as SVP operations for Angelica and VP operations for Crothall Laundry.
Kannegiesser ETECH says he has an extensive understanding of equipment, engineering and efficiency and will bring a “user” perspective to the team. In addition, Davis is passionate about people, process and customer satisfaction.
He earned an MBA from the University of St. Thomas and resides in the Atlanta area with his wife of 25 years and three children.
The company says Corrigan’s dedication to the industry, vast knowledge of plant operations and strategic planning will enhance its customer support in the U.S. and Canadian markets.
Fashion Seal Healthcare promotes Schwartz to VP


SEMINOLE, Fla. — Dan Schwartz, senior director of operations for Fashion Seal Healthcare®, a uniform designer, manufacturer and distributor, has been promoted to the position of vice president of Fashion Seal, reports parent organization Superior Group of Companies.
According to Superior, Schwartz will lead the Fashion Seal sales organization and will continue to manage the operations of the brand.
Braun
promotes two in sales, marketing
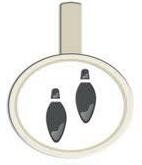
SYRACUSE, N.Y. — Laundry equipment manufacturer G.A. Braun Inc. has promoted Gary Ostrum to executive vice president of Global Sales and Marketing and Jim Corrigan to vice president of Sales, U.S. and Canada, says Rick Rudmann, president.
“Both Gary and Jim are respected industry veterans and have strong backgrounds in laundry facility management, strategic sales planning and business analysis,” says Rudmann. “The restructuring of our sales team will further strengthen our commitment to our domestic and international client base. Our foundation of unrivaled product quality and customer support will continue and advance.”
Ostrum’s experience includes 38 years within the laundry industry in both plant management and equipment sales. Currently, he is on TRSA’s healthcare committee and is also a PMI (Production Management Institute) instructor.

Additionally, Ostrum has written several articles and is actively involved in other industry associations. He recently held the position of East Coast Regional Vice President of Sales.
Corrigan has been in the laundry industry for 37 years and is also actively involved in several laundry industry associations. He recently held the position of West Coast Regional Vice President of Sales.


“With Dan’s background in sourcing, operations and customer engagement, he is uniquely qualified for his new role,” says Peter Benstock, president of Fashion Seal Healthcare. “We look forward to Dan’s positive impact on revenue growth.”
Corp.
KENNER, La. — Mike Diedling, applications engineering manager, has retired from Pellerin Milnor Corp., the company reports. Diedling began his career in the laundry industry as an industrial engineer for Morgan Services, where he worked on increasing the efficiency and productivity of their plants. He then joined the Milnor family in 1978 as an industrial engineer in the Laundry Engineering Department.
Just three years later, Diedling took on the role of Laundry Engineering Department manager. The company says he quickly became a valued expert on turning challenging projects with demanding requirements into efficient laundry solutions for customers all over the world.
“It can’t get any better than that,” he notes, reflecting on his personal satisfaction helping customers achieve their laundry dreams.
Diedling also notes that the people— from fellow workers to customers—have all left a lasting impact on him that he will treasure for years to come.
He leaves Milnor will a strong sense of family, a strong work ethic, and a strong sense of satisfaction that the department he managed for nearly 37 years will continue to support customers’ needs for future generations.

G.A. Braun Inc. appoints Rudmann president
Diedling retires from Pellerin Milnor

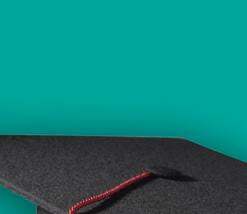



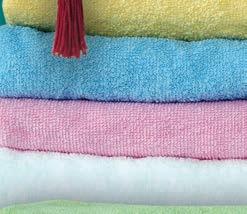

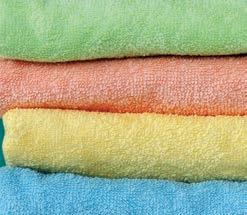
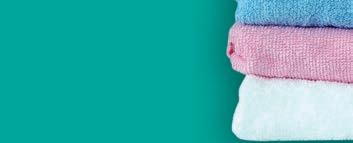
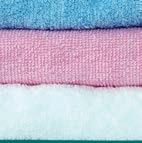
Classified Advertising






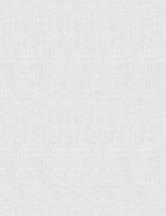
PARTS FOR SALE
PARTS, PARTS, PARTS
Huge stock of parts for most laundry equipment & boilers. Also traps, valves and lubricants. Overnight delivery.
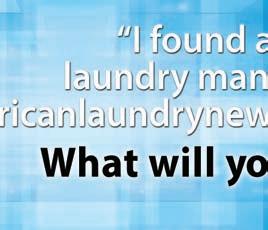
Steiner-Atlantic, 800-333-8883 Fax: 305-751-8390 parts@steineratlantic.com www.steineratlantic.com
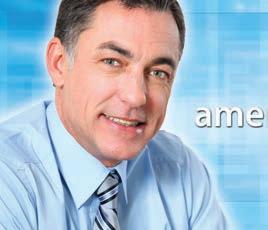
PARTS & SERVICE
®
The Griffin Group, Inc. “Recruitment Specialist” Need to FILL a position?
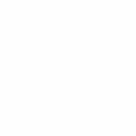
Call Deana Griffin 888-235-2365 www.thegriffingroup.cc deana@thegriffingroup.cc

In need of service and or parts for all your finishing equipment manufactured by BB&D, Lavatec, Washex, and Voss? Contact Michael @ 203-232-4004 or E-Mail me: mtenhave66@yahoo.com Chief


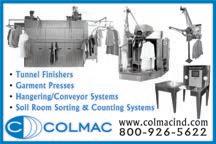
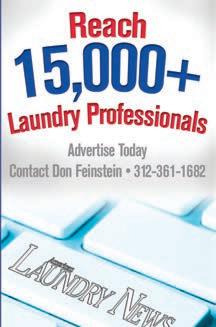











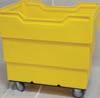
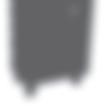













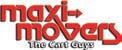















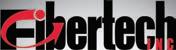










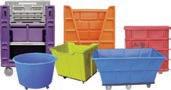
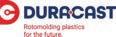
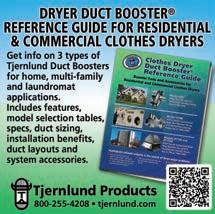




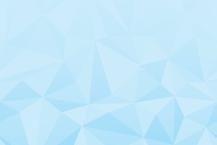









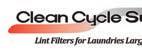

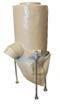
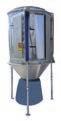

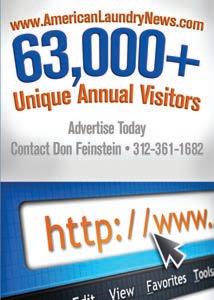
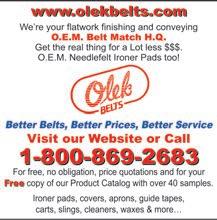


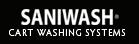
SMALL-PIECE FOLDERS

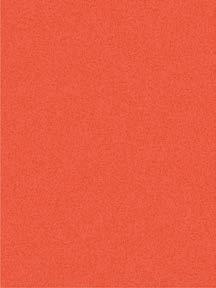
Pellerin Milnor Corp. P.O. Box 400, Kenner, LA 70063 504-467-9591, Fax: 504-468-3094 www.milnor.com
Pellerin Milnor Corp. P.O. Box 400, Kenner, LA 70063 504-467-9591, Fax: 504-468-3094 www.milnor.com
Pellerin Milnor Corp.














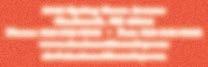

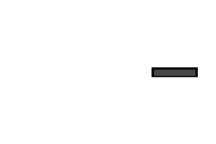
P.O. Box 400, Kenner, LA 70063 504-467-9591, Fax: 504-468-3094 www.milnor.com

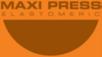
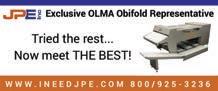
Pellerin Milnor Corp. P.O. Box 400, Kenner, LA 70063 504-467-9591, Fax: 504-468-3094 www.milnor.com









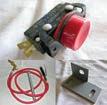
Encompass Group awarded group purchasing agreements with Premier
MCDONOUGH, Ga. — Encompass Group LLC, a manufacturer and marketer of reusable textiles, professional apparel, and disposable and single-use medical products, has been awarded new group purchasing agreements with Premier Inc., a healthcare improvement company.
“Encompass Group is excited about these four new agreements, and we will continue to bring innovative, cost-effective solutions to the Premier membership in all markets served,” says Tom Sweatt, executive vice president, Health Systems, for Encompass Group.
The company says the group purchasing agreements include Disposable Non-Sterile Protective Apparel; VCT Anti-Embolism Stockings; Cubicle Curtains, Tracks and Privacy Screens; and Reusable Textiles and Textile Services.
The new agreements allow Premier members, at their discretion, to take advantage of special pricing and terms pre-negotiated by Premier for these four different product categories.
Emerald Textiles continues California expansion as healthcare linen provider
LOS ANGELES — Emerald Textiles has acquired the assets of MediClean Linen and Laundry, a Los Angelesbased healthcare linen service provider, the company reports. Terms of the deal were not disclosed.
The acquisition expands the footprint of the healthcare linen provider, increasing the total number of locations on the West Coast to seven.
Additionally, Emerald Textiles has commenced construction on a new, “state-of-the-art” 60 million-pound facility in Livingston, Calif. The new Livingston facility will allow Emerald to serve its expanding customer base in Northern California along with its existing facility in Turlock.
Emerald says the new facility is scheduled to be complete by Q3 2019.
“We are excited to add the Los Angeles location to our network of facilities. The Los Angeles location provides Emerald Textiles with a strong foothold in Southern California, and further enhances Emerald’s existing network of linen processing facilities,” says Greg Anderson, CEO of the company.
Under the ownership of two private equity firms, Pacific Avenue and Highland Avenue Capital Partners, Emerald Textiles says it has grown through significant new customer wins, emphasis on building a world-class team, a universal commitment to providing high levels of service to the customer, the acquisitions of two Southern California linen processing facilities, a de-novo build of a Northern California facility and material investments to upgrade existing facilities and equipment.
As part of the asset acquisition in Los Angeles, Emerald will immediately undertake a “re-tooling” of the facility to upgrade equipment. The capital plan includes more than $6 million of investment to ensure that the Los Angeles facility upholds the same level of quality and efficiency found across the entire Emerald network.
“This acquisition represents a continuation of our effort to build a world-class healthcare linen provider that can serve the needs of the entire state of California and West Coast markets,” says Chris Sznewajs, founder and managing partner at Pacific Avenue. “We are excited about our expansion into the Los Angeles market.
“The de-novo facility will further enhance our position in Northern California and provides much needed capacity in that market. We are committed to investing in our people and facilities to ensure that we are best positioned to serve the needs of our customers in an environmentally
responsible way.”
UniFirst opens high-tech industrial laundry facility, creates 100 jobs
LOS ANGELES — UniFirst Corp., which provides customized work uniform programs, corporate attire and facility service products, recently celebrated the opening of its new 73,000-square-foot, state-of-the-art industrial laundry plant in Santa Fe Springs, Calif.
The company says the new facility has created more than 100 jobs to service businesses in the Greater Los Angeles area.
The new plant, which features the latest innovations in textile services technology and automation, was developed to accommodate the rapidly growing customer base in Greater Los Angeles, Long Beach, Newport Beach, Anaheim and surrounding areas, according to UniFirst. It provides local businesses with managed service programs for uniforms and workwear, as well as facility service products, including floor mats and mops, wipers and towels, and restroom and ancillary products.
UniFirst had previously serviced area customers from its smaller-sized branch facility in Norwalk, Calif., which employed 55 people, most of whom relocated to the new facility.

“Our L.A. plant is an engineering showpiece,” says UniFirst President and CEO Steven Sintros. “The new facility features latest technologies and high-tech processing
systems that are among the most advanced in the textile service industry. This will allow us to continually improve our managed uniform programs for our customers’ benefit, so they consistently receive the very best services possible.”
Spanning 3.57 acres, UniFirst says the new facility supports greater energy efficiency through investments that include heat-reclaiming equipment, latest-generation warehouse lighting and contemporary rooftop HVAC units. The company adds that all cleaning formulas and detergents are 100% environmentally friendly, and natural light throughout the plant offers a positive employee boost to the workday.
“We’re extremely excited to bring this world-class operation to the Greater Los Angeles market,” says the new plant’s general manager, Anthony Ortega. “Our L.A. operation is the culmination of all the technological advancements we’ve made over the years, serving as a model for new UniFirst servicing operations to come.”
Continental Girbau partners with distributor Washington Automated
OSHKOSH, WIS — Continental Girbau Inc. recently partnered with Washington Automated Inc., a full-service laundry equipment distributor in Everett, Wash., the company reports.
Washington Automated, a 50-year-old distributor, now provides Continental’s comprehensive offering of onpremises and industrial laundry equipment throughout Washington, Oregon and northern Idaho.
“Washington Automated is not only committed to customer satisfaction and success, it is a leading laundry equipment distributor serving the Pacific Northwest,” says Joel Jorgensen, Continental vice president of Sales. “We are excited to work with the company’s talented team for many years to come.”
“We believe we stand out from our competitors because of our high-level customer service,” adds Ryan Lucken, Washington Automated president. “Taking care of the customer is the most important thing we do. It’s been the key to our success for a half century. We aligned with Continental because it mirrors our dedication to the customer and stands behind its quality products.” ALN
Calendar
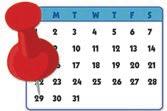
February
7 MTSA
Annual Blackhawks Suite Event
Chicago, Ill. Info: 888-672-6872
20-21 TRSA
Hospitality Conference Lake Buena Vista, Fla.
Info: 703-519-0029
March
25-29 Association for Linen Management Laundry & Linen College: Textile Care Services Richmond, Ky. Info: 859-624-0177
27-28
TRSA
9th Annual Legislative Conference Washington, D.C.
Info: 703-519-0029
April
2 JENSEN
Spring Service Seminar –
L-Tron DTX Tumbler/Dryers Panama City, Fla.
Info: 850-248-4129
3-4 JENSEN
Spring Service Seminar –
L-Tron Washer/Extractors Panama City, Fla.
Info: 850-248-4129
8-10 JENSEN
Spring Service Seminar –Flatwork Finishing Systems Panama City, Fla. Info: 850-248-4129
9-12 MILNOR
Spring Service Seminar: Washer-Extractor Kenner, La. Info: 504-712-7716
These bar mops are perfect for wipe-and-toss in heavily soiled environments. Minor weaving defects such as over-stitching or imperfect cuts reject perfectly good wiping tools from circulation. We buy these at a deep discount and pass the savings on to you. Packed: 100 doz/bale.
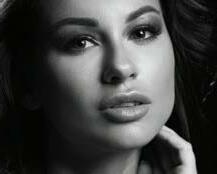
When bar mop production runs are over and inspections have been completed, mills may still have excess yarn, and a running loom. Run Of Mill (ROM) bar mops contain every bar mop that comes o the loom after the first quality run has been finalized, so are more economical than Grade A1 bar mops.
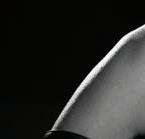
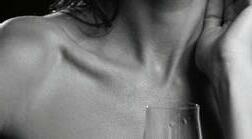


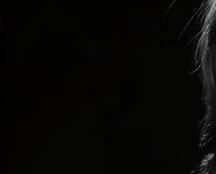
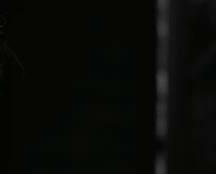
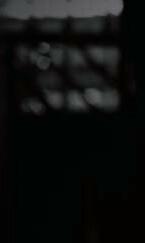
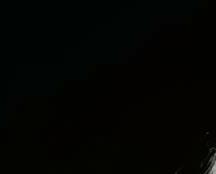


Route Ready bar mops are optically white and packed in bags of 25 so you never have to pre-wash or recount them prior to use. Typically, laundries save 70¢/doz by freeing washroom and finishing floor operators from a whole wash cycle, you gain production time to focus on other laundry room bottlenecks.

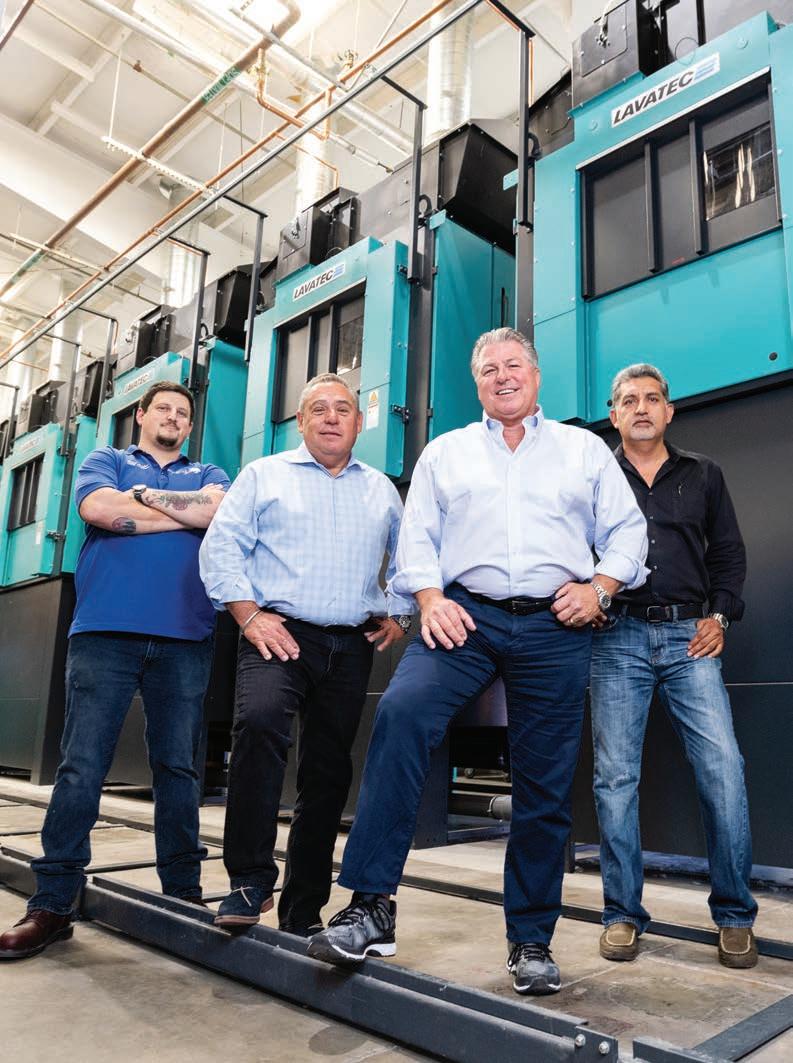
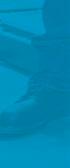
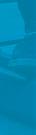
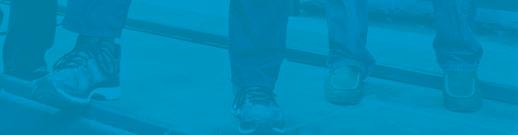
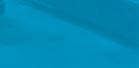

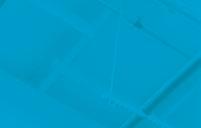
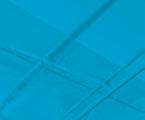
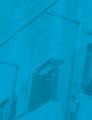


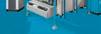


