Alsco helps provide food for hungry students
CHARLOTTE, N.C. — Linen and workwear rental services provider Alsco’s branch here is teaming up with Temple Israel to sponsor an annual food drive to ensure students at Huntingtowne Farms Elementary School in the Charlotte-Mecklenburg School District don’t go hungry.
The Alsco Charlotte branch applied for and received a nonprofit gift/grant through the Steiner Foundation, which Alsco created in 1969 to allow Alsco branches to help and support community nonprofit charities and projects.
Food collected from the annual drive will be distributed to the school through the Blessings in a Backpack program, which provides children with food for weekends and school breaks. Also, some of the food collected will be allocated to the local food pantry.
“We are very happy to be able to help sponsor the Blessings in a Backpack program,” says Alan Sowers, general manager for the Charlotte branch. “No child should have to go hungry, and this program helps ensure they don’t.” ALN
Textile care industry ready for Clean ’19
BY MATT POE, EDITORNEW ORLEANS — When the Clean Show takes to the floor of the Ernest N. Morial Convention Center here June 20-23, it will be an event of firsts and lasts.
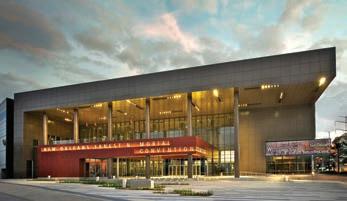
For some attendees, it will be their first experience of the biennial event formally known as the World Educational Congress for Laundering and Drycleaning.
It will also be the first Clean Show under new ownership in its 42nd year.
In December, Germany-based Messe Frankfurt, an international trade fair, congress and event organizer—the largest in the textile care industry—purchased the Clean Show from the five sponsoring associations: Association for Linen Management (ALM), Coin Laundry Association (CLA), Drycleaning and Laundry Institute (DLI), Textile Care Allied Trades Association (TCATA) and TRSA, the association for
linen, uniform and facility services.

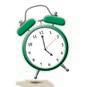
As part of the acquisition, the sponsor associations will maintain their close involvement with the show, and Messe Frankfurt aims to continue the Clean Show success story.
“We look forward to this first Clean Show
under the ownership of Messe Frankfurt, whose portfolio of laundry trade shows includes Texcare International in Frankfurt, Germany, and its expansion into China with Texcare Asia and the United Arab Emirates
The man behind the Clean Show
Decades-long connection coming to end for event manager Riddle
BY BRUCE BEGGSATLANTA — President John Riddle and his staff at longtime Clean Show management firm Riddle & Associates are experiencing many “lasts” in the days leading up to Clean 2019 in New Orleans.
You see, Germany-based trade fair organizer Messe Frankfurt recently purchased Clean from the five associations that have sponsored the show for decades. The New Orleans show in June will be the last managed by Riddle & Associates, which has overseen the every-other-year event under contract since 1992.


John Riddle’s personal involvement in assisting with Clean dates back to 1981.

We visited Riddle, 78, in his Atlanta offices
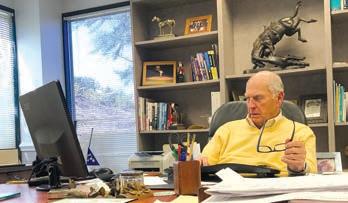
in late March to talk about the upcoming show, but also took the opportunity to quiz him on his storied past and to find out what
he’s planning in semi-retirement.
Columnist at Large
In
Panel of Experts
In this issue, the experts share their advice on how to get the most out of Clean 2019.
Effective Plant Tours
No matter the purpose of a plant tour, there are ways to make them as successful as possible.
The Clean Show to build on past in New Orleans, step into the future
this issue, Eric Frederick writes about the benefits of solid employee onboarding.
In addition to legislative efforts, honors presented at Leadership Awards Dinner
WASHINGTON, D.C. — TRSA, the association for linen, uniform and facility services, held its 9th Annual Legislative Conference here March 27-29, coinciding with the very first blooms of cherry blossoms.
The event began with a keynote speech by Chris Stirewalt, the politics editor for Fox News Channel and host of the Fox News Halftime Report. Stirewalt discussed the recent release of the Mueller Report and the impact its findings will have on strategy for both the Democratic and Republican parties moving forward.
He also took several questions from the crowd. In closing, Stirewalt shared his opinion that partisan politics is here to stay.
The same afternoon, attendees were also briefed by Kevin Schwalb, TRSA’s vice president of government relations, on key issues to discuss with legislators in the following day’s Hill meetings, such as TRSA’s support for infrastructure improvement and adoption of the U.S. Department of Labor’s (DOL) update of overtime rules.
The day wrapped up with prime networking opportunities: the TRSAPAC Reception and a celebration of TRSA members’ exemplary business practices as a total of 25 awards were present-
ed during the Annual Leadership Awards Dinner at the Dupont Circle Hotel.
The second day of the conference provided TRSA members with an insider’s view of Washington politics and policy during three speaking engagements with Capitol Hill lawmakers.
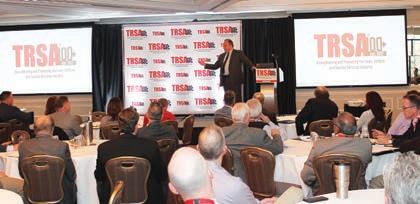
Sen. Ron Johnson (R-WI), chair of the Homeland Security Committee, and Todd Young (R-IN), a 10-year Marine veteran and U.S. Naval Academy graduate elected to the Senate in 2016, spoke on Capitol Hill before the TRSA members set off for congressional offices to discuss issues, including the abovementioned need for infrastructure improvements and approval of the Department of Labor’s proposed changes in overtime eligibility.
U.S. Rep. Ben Ray Luján (D-NM), was the third speaker of the day, and he addressed the TRSA attendees at a luncheon meeting following their Hill visits. As chair of the Democratic Congressional Campaign Committee (DCCC), Rep. Luján helped engineer last year’s Democratic takeover of majority status in the U.S. House of Representatives.
More than 50 TRSA members visited a grand total of 77 offices of both Democratic and Republican lawmakers on Capitol Hill to discuss issues impacting the linen, uniform and facility services industry. Each attendee was armed with several folders to leave behind with TRSA’s stance on DOL’s Overtime Regulation

MEMBERS HONORED WITH LEADERSHIP AWARDS
Five linen, uniform and facility services company members (operators) and three supplier company members (associates) took home the highest honors from the presentation of annual TRSA awards on March 27 at the Legislative Conference.
A total of 25 award winners were acknowledged during the Annual Leadership Awards Dinner at the Dupont Circle Hotel. There were multiple winners in each of the eight competitions with an overall winner topping each.
Interest in the TRSA competition was higher than ever as dozens of entries were received and judged by TRSA committees and subject-matter experts.
Most accolades acknowledged team efforts of company staff but some heralded individuals’ outstanding performances on behalf of their companies. Among the overall winners, those individuals were in the Above and Beyond Service competition:
Publisher
Charles Thompson
Phone: 312-361-1680
E-Mail: cthompson@ ATMags.com
Associate Publisher/ National Sales Director

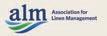
Donald Feinstein
Phone: 312-361-1682
E-Mail: dfeinstein@ ATMags.com
Editorial Director
Bruce Beggs
Phone: 312-361-1683
E-Mail: bbeggs@ ATMags.com
Editor
Matt Poe
Phone: 866-942-5694
E-Mail: mpoe@ ATMags.com
Production Manager
Roger Napiwocki
Digital Media Director
Nathan Frerichs
Phone: 312-361-1681
E-Mail: nfrerichs@ ATMags.com
Advisory Board
David Barbe • Jim Buik
Tony Jackson • Janice Larson Tom Marks
Main Phone: 312-361-1700 Fax: 312-361-1685
Subscriptions
630-739-0900 x100 www.americanlaundrynews.com
American Laundry News (ISSN 1091-9201) is published monthly. Subscription prices, payment in advance: U.S. 1 year $46.00; 2 years $92.00. Foreign, 1 year $109.00; 2 years $218.00. Single copies: U.S. $9.00; Foreign $18.00. Published by American Trade Magazines LLC, 650 West Lake Street, Suite 320, Chicago, IL 60661. Periodicals postage paid at Chicago, IL, and at additional mailing offices.
POSTMASTER, Send changes of address and form 3579 to American Laundry News Subscription Dept., 440 Quadrangle Drive, Suite E, Bolingbrook, IL 60440. Volume 45, number 5. Editorial, executive and advertising offices are at 650 West Lake Street, Suite 320, Chicago, IL 60661.
Charles Thompson, President and Publisher. American Laundry News is distributed selectively to qualified laundry and linen management and distributors in the United States.
© Copyright AMERICAN TRADE MAGAZINES LLC, 2019. Printed in U.S.A. No part of this publication may be transmitted or reproduced in any form, electronic or mechanical, without written permission from the publisher or his representative. American Laundry News does not endorse, recommend or guarantee any article, product, service or information found within. Opinions expressed are those of the writers and do not necessarily reflect the views of American Laundry News or its staff. While precautions have been taken to ensure the accuracy of the magazine’s contents at time of publication, neither the editors, publishers nor its agents can accept responsibility for damages or injury which may arise therefrom.
MEMBERSHIPS
Milnor has a better solution through dilution.
When Milnor introduced PulseFlow® technology, CBW® washing was thrust into the future. The idea of balancing time, temperature, mechanical action and chemistry was missing one critical piece of the pie – DILUTION through the efficient use of water.
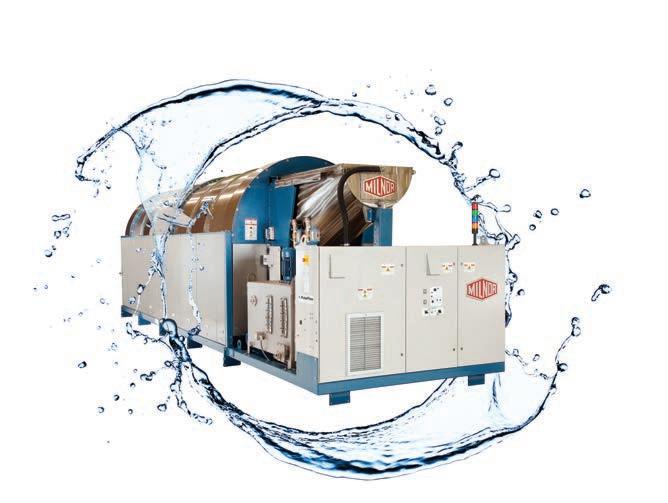
PulseFlow combines the innovative RecircONE® fast wet down and chemical immersion in the first module with standing bath washing in every spacious process module. Thorough and efficient dilution occurs by way of intermittent high velocity counterflow rinsing and traditional True Top Transfer.
The result is hygienically clean linen using less water (as low as 0.3 gallons per pound/2.5 liters per kilogram) and less energy as proven time and again by hundreds of PulseFlow tunnels in a variety of laundry applications worldwide.
Contact an authorized Milnor distributor or call 504-712-7656 to find out more.
www.milnor.com
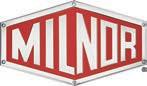
Plan for a ‘Clean’ sweep
Y ou probably noticed that many articles in this issue of American Laundry News are very Clean Show-related. That’s because this edition is your tool to help plan to make the most of your Clean Show experience.
Starting on page 1, you’ll find an in-depth preview of the show, along with hints and tips to make the most of your time in New Orleans.
Our Panel of Experts (page 12) also share their advice, there’s an in-depth look at the educational sessions on page 38, and there’s a listing of exhibitors with booth numbers (page 20-37) signed up at press time.
And of course we have the handy-dandy show floor map (2829) so you can start planning your days in New Orleans (and you can use the map to find your way
The Editor’s Desk MATT POEaround during the show).
You probably also noticed the story on John Riddle on page 1. Clean 2019 will be the last show organized by John and his company, Riddle & Associates, since Clean’s purchase by Messe Frankfurt. We figured that after all these years behind the scenes,
it was time to shine the spotlight on “The Man Behind the Clean Show.”
You can hear a lot more from John in the latest American Laundry News Podcast as well.
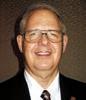

As much as we’d all like to be able to get to everything at Clean, it’s just not physically (or mentally) possible. Since American Laundry News will feature online and print follow-up articles, and plan future articles on topics gleaned from the show, let’s work together to cover as much of it as possible.
How, you ask? E-mail me at mpoe@atmags.com and let me know what you’re hoping to discover or investigate in New Orleans.
FYI: We’ll be in booth 4645. Stop by and we can talk about keeping it clean, everybody. ALN
TCATA holds meeting to chart future
Reducing turnover through proper on boarding
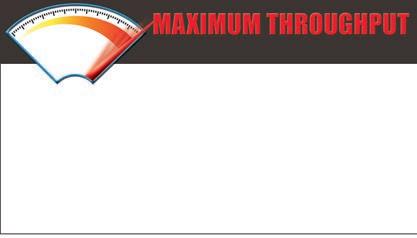
I recently decided to interrupt my endless days of retirement by taking on a local part-time job near my home.
I wanted something easy to do that did not require me to make management decisions. I decided 44 years in laundry management was enough, and I would just relax and let someone else deal with management issues.
I went to work at the local airport, which is only a few miles from my house, driving rental cars from the airport drop-off location to the service center, and then driving the clean ones back to the appropriate pick-up location.
The company I am working for has seen tremendous growth over the past several years—and has also experienced a lot of employee turnover. I suspect that their turnover has a lot to do with a poor quality new employee training program.
Now you may be thinking what does the car rental business and the laundry business have in common? At first glance they are totally different industries, but upon closer examination they have a lot in common.
Both pull from basically the same pool of potential employees for their entry-level jobs. The pay scale between the two industries are very similar. Both would greatly benefit from reduced turnover and a stable staff. Both industries perform well when they are well organized and have happy employees.
TAMPA, Fla.
— Fourteen members of the Textile Care Allied Trades Association (TCATA) gathered here in late February for a strategy meeting to discuss plans for the association’s future direction.
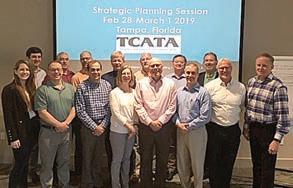
Continued consolidation and other factors have changed the textile care industry in significant
ways, and the association’s leadership recognizes that now is the time to examine TCATA’s role and how it can best serve the industry.
The members attending this meeting represented a cross section of the industry—manufacturers and distributors from both the laundry and drycleaning sides.
“Those who attended expressed an enthusiasm for TCATA’s important role as the exclusive representative of manufacturers and distributors in the textile care industry,” says TCATA president Leslie Schaeffer. “Many interesting ideas were put forth on ways that TCATA can offer value in a changed, consolidated industry.”
The results of this meeting, after further discussion with the TCATA board of directors, will be announced later.
ALN
On my first day at work, I was told to report to the airport, and then they had an employee from the service center come pick me up. They had trouble setting me up on their computer system for entering my time, and even now, three weeks after starting, I cannot sign in on their system on my own.
Each employee has their own way of getting things done, and there is the right way, the preferred way, and the fast (but not entirely legal) way of getting things done. The company lacks a formal training program, and each employee passes on tips to the other employees they like.
As a new employee, it would be very easy for me to walk away from the job and go back to retirement. It is extremely frustrating not to be able to do the essential things, like clock in and out on my own, that should be done every day. There are critical pieces of equipment that I need to have to do my job effectively that I have not been given.
I have no idea if they think I am doing a good job or not. These feelings are a directly result of a poor on boarding process. To reduce turnover and improve the chances of keeping a new employee, I have always recommended that a trainer be assigned to a new employee from the moment they arrive on their first day. This person is responsible for introducing them to their fellow employees, making sure they get an assigned locker, know where the bathrooms are, where the breakroom is and teaching them the best techniques in how to process linen.
Work is a social part of our lives, and feeling comfortable and that you belong in a situation is more important than the pay.
Having a consistent point of contact to guide you through this process is critical during the first week of employment. Both the car rental and the laundry industry assume that the job is easy and requires very little training—that almost anyone can do the job, that employees are interchangeable parts.
Quality service and quality product are produced by a team of employees who thoroughly understand the nature of the business they are involved in and are committed to delivering the best they can.
OUR SISTER WEBSITES
From
•
•
•
•
•
From AmericanCoinOp.com:
• Laundrylux Acquires Automated Laundry
This sense of commitment comes from proper on boarding where the philosophy and nature of the business is thoroughly explained, the importance of a good market reputation is explained, and proper training is conducted.
When I worked daily in the laundry industry, I used to call it a love-it or leave-it industry. Either people enjoyed the type of work they were doing and the team environment or they left in about a week.
Many mangers I have known over the years have pointed to lower salaries in the laundry industry for our high turnover,
•
From COLUMNIST AT LARGE Eric L. Frederick, RLLD“Casual Dress” Redefined.
Milliken Chambray Signature Stripe Napkins are an excellent way to bring people together. With a variety of colors, our Chambray works for any occasion or location - from formal to casual.
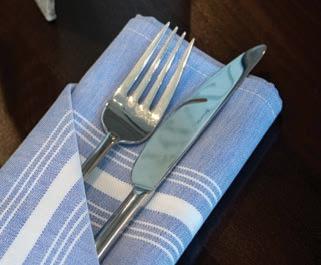
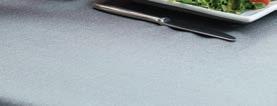
With a new twist on an old tradition, your linen will speak their language... fresh, clean, consistent and stylish.
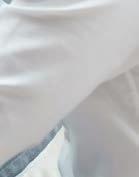
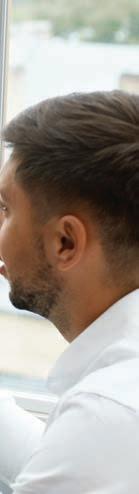
Together, ADI and Milliken have set the standard of linen excellence for decades.
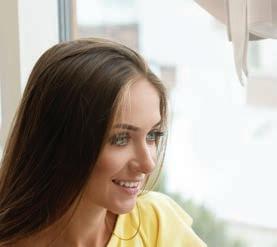
ADI American Dawn. The world’s leading supplier of Milliken Signature table linen products. Count on us!
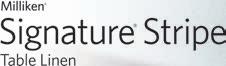
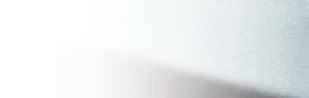






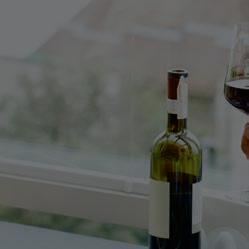
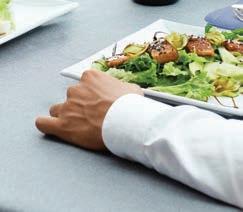
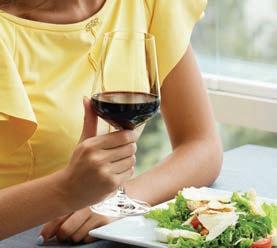
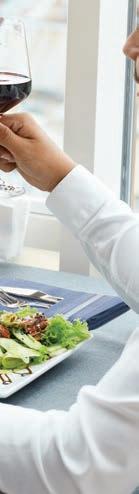
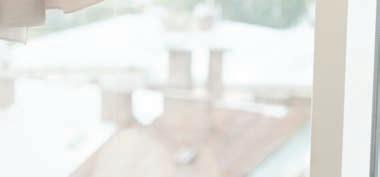
with Middle East Cleaning Technology Week, as well as global Texcare Forums,” says Joseph Ricci, president and CEO of TRSA, and executive committee chairman of Clean ’19.
Because this marks the first Clean Show under Messe Frankfurt, Clean ’19 will be the last organized and managed by Atlanta-based Riddle & Associates.
The collaboration and management between the sponsoring associations and Riddle & Associates helped put the Clean Show on Trade Show Executive magazine’s 50 FastestGrowing Shows and the Trade Show News Network Top 100 shows, as well as being the largest textile services and care show in the world, Riddle shares.
“It has been a pleasure to work with John Riddle of Riddle & Associates, which has managed the show since 1993,” says Ricci. “John had indicated several years ago that he would be retiring from full-time event management following the 2019 Clean Show. We salute John and his staff for their excellent service to the show sponsors and our attendees.”
Riddle & Associates says Clean 2019 will provide a platform for all industry professionals and companies to come together on the show floor to share ideas, technologies, education and networking.
LEARN, WORK, SUCCEED
According to Riddle & Associates, Clean Show attendees include store owners, plant operators, technicians, institutional laundry managers, distributors, consultants and buyers.
The largest share (94%) of attendees are business owners, executives, or managers, according to a past Clean Show survey by Riddle & Associates. Clean brings those business owners and executives face-to-face with hundreds of industry exhibitors.
The show organizer says for companies looking to expand, reeducate or upgrade current technology, the exhibit floor is where they should be.
“I think everyone who is in some form of the textile care industry, whether it be laundry, dry cleaning, textile rental, coinop, etc., I think you’re going to be very happy,” says John Riddle. “We had a great show in ’17 in Las Vegas, and New Orleans is right there with it, right now.”
The June 2017 Las Vegas Clean Show was named one of Trade Show Executive’s 50 FastestGrowing shows of 2017. The show was honored in all three categories of the awards competition: net square feet of exhibit space, number of exhibiting companies and total attendance. Riddle & Associates says Clean attracted 12,563 visitors (including 2,282
people from 101 foreign countries and overseas territories) and 481 exhibitors in 227,006 square feet of space to Las Vegas in 2017.
At press time, the management company says around 417 exhibitors are signed up to be in New Orleans, with more than 211,000 square feet of exhibit space sold (a full list of exhibitors at Clean ’19, as of April 4, begins on page 20).
“You’re going to see an awful lot of exhibitors,” Riddle shares. “New things are coming that you will be pleased to see. Our attendance is holding up. Based on what I know in the years I’ve done this is that we can look for a good show, and as always you can come and actually see equipment work.”
Exhibits featuring equipment, products and services will be on display in halls B-F in the Ernest N. Morial Convention Center.
“Exhibit sales and hotel room blocks are ahead of previous Clean Shows in New Orleans, demonstrating the strength of the event and the industry as a must-attend opportunity for researching solutions and information-sharing,” adds Ricci.
“I am thrilled with the support of our exhibitors, including their commitment to innovation and introduction of new products and services that increase productivity and safety.”
Riddle says he’s proud of the fact that when industry professionals come to the Clean Show, they get a chance to see the equipment they’re contemplating buying actually work.
“It becomes very expensive for an exhibitor to bring a tunnel washer or a big washer or extractor to the show,” he points out. “Just the cost alone of getting it there [is great], then you have the time and materials and the money, if you will, to fire them up, and then run them and show the attendee what it will do.
of
tors
Besides interacting with exhibi-
10 W A YS TO M AKE C LEAN ’19 WORK FOR YOU
At the world’s largest exhibition and education platform for the textile care industry, it is difficult to see and do everything, but most people who attend Clean ’19 will have specific things they want to accomplish. The show is only held every two years, so you want to get as much as possible from the experience.
Advance planning can give you a solid return on your investment of time and money and help keep your business running smoothly. Here are 10 ideas from Riddle & Associates for maximizing your Clean 2019 visit.
1. Set specific goals. What do you want to accomplish? Is it purchasing or upgrading equipment, learning about new technologies, finding a solution to a business problem, or interacting with colleagues and friends? Prioritize what is important to you.
2. Develop an action plan. Search the Clean Show website, www.cleanshow.com, for the exhibitors and education that interest you most. Add these to your itinerary. Check the floor plan to locate the booths you want to visit. It will keep you on track and ensure that you meet your primary goals.
3. Learn in the classroom. Take advantage of the many educational sessions that are pertinent in today’s market. The morning classroom sessions and afternoon exhibitfloor sessions cover a multitude of industryrelated topics for all segments of the industry. You would pay hundreds of dollars for these sessions in another setting, but they are included in your low Clean Show registration fee. Sessions are listed on www. cleanshow.com. Add those of interest to your itinerary.
4. Make advance appointments. For a product you are particularly interested in seeing, make advance appointments with the exhibitors of that product. This ensures that you will get one-on-one time.
5. Don’t miss the new stuff. Leave enough time in your plan to the visit as many booths as possible beyond your original plan. See what is new and exciting, and don’t miss the small booths. You might find a something that is just right for your operation.
6. Join the discussion. If you participate in Facebook or Twitter, connect with the Clean Show so you can be up to date on anything from Clean 2019 news to interesting facts about New Orleans.
7. Write it down. When the show is over, it can all seem like a jumble of information. Listening carefully and documenting important points in education sessions or exhibitor conversations can be invaluable in reviewing and analyzing your show experience. Use your phone or iPad, a notebook or write on the back of business cards for later reference.
8. Dress for comfort. New Orleans can get very hot and humid in June. Wear light, comfortable clothes and comfortable walking shoes. You will walk miles on the exhibit floor. Travel light. Carry only what you absolutely need. Several exhibitors offer bags for carrying items you pick up along the way. If you gather too much literature, you can mail it home from the building’s business center.
9. Have some fun. New Orleans has a lot to see and do. Take a stroll around the worldfamous French Quarter or take a ride on a streetcar to visit the renowned Garden District. See what’s new in the Warehouse District. In the evenings, enjoy the region’s outstanding cuisine and enjoy the jazz music that plays on every corner.
10. Educate your coworkers. When you return home, share your new knowledge with coworkers who did not attend Clean 2019. They will feel like they had a part in it and can apply the information to make your entire operation go smoothly.

“Our package plan for exhibitors is such that it has enabled the exhibitor to actually come and operate the equipment in a cost-effective manner so that the attendee gets the advantage of that. You don’t just see one sidea presentation; you can look at multiple pieces of equipment operate under one roof, generally within a couple hundred feet of each other. That demonstration alone is worth the trip.” on the show floor, attendees also have the opportunity to take advantage of 30 hours of educational sessions. Riddle & Associates says sessions include
GROWTH COMES FROM SOLID ROOTS

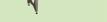
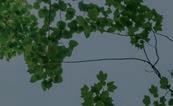

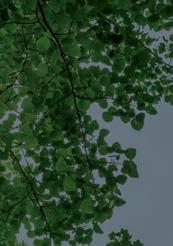
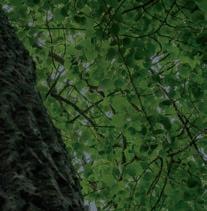
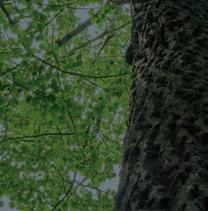
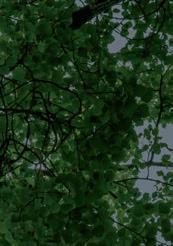

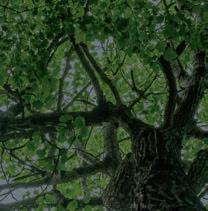
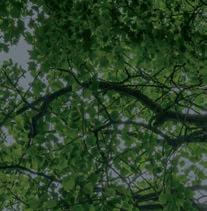
The Girbau family has been providing laundry solutions globally since 1960, and whether you produce 20lbs of laundry per hour or enough to justify a tunnel washer, Girbau Industrial has a solution to wash, dry, iron, fold & stack. We are your single source for everything laundry.


Growth takes time. Small changes today impact gains in production and efficiency tomorrow. Replace aging equipment, add feeding & folding automation or update your wash floor. Grow one piece at a time with Girbau Industrial.

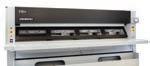
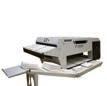
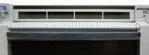
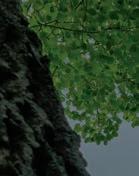

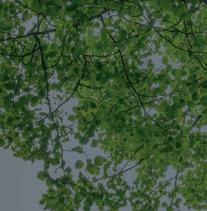
topics such as training, business management and environmental issues.
Morning sessions, which run from 8 to 10 a.m., will take place in on-site meeting rooms. Afternoon sessions will be held in the exhibit hall (a full schedule, along with brief descriptions of each session, is on pages 38-39).
“This combination has already strengthened the Clean Show as a platform for industry professionals and suppliers to work, learn and succeed together,” Ricci says. “Make the most of your time here and you will find no better place to share ideas and grasp trends and technologies, show after show.”
The Clean Show has also developed with the times and has a strong social media presence. Attendees and exhibitors can get updates on the upcoming show, registration and Clean Show facts on its Facebook and Twitter pages, says Riddle & Associates.
As social media takes a larger role in communication, Riddle & Associates says the Clean Show interacts with attendees and can answer questions on social media platforms to better engage with its followers.
Attendees sharing their Clean Show experience in New Orleans are encouraged to use the handles #Clean2019 at @thecleanshow so others can easily find messages and photos and information related to the show.
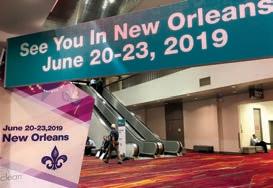
In addition, Riddle & Associates says attendees can use the Clean Show 2019 My Planner (available through the show website and mobile app) to organize show floor visits. Through the Planner, attendees can see what companies are exhibiting and sort them by name, keyword, booth number and more. From there, a personalized list can be created to visit on the show floor.
STILL TIME TO GET PREREGISTRATION DISCOUNT
Industry professionals still interested in attending Clean ’19 can take advantage of pre-registration discounts on the show’s website (www.cleanshow.com) through June 10. The pre-registration fee is $119 per person for any member of one of the sponsoring associations, and $149 for nonmembers. After June 10, attendees must register onsite at Clean 2019 for a fee of $169 per person.
Registration hours at the convention center will be 1 to 4:30 p.m. on Wednesday, June 19; 7 a.m. to 4:30 p.m., Thursday through Saturday, June 20-22; and 7:30 a.m. to 2:30 p.m., Sunday, June 23.

The show starts June 20, when attendees will be able to explore the exhibits 10 a.m. through 5 p.m. Distributors have exclusive access from 8-10 that morning.
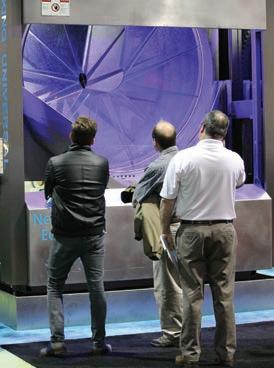
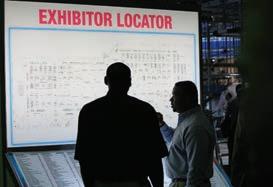
The show floor opens at 9 a.m. Friday through Sunday (June 21-23) and closes at 5 p.m. Friday and Saturday (June 21-22) and at 3 p.m. on Sunday, June 23.
On show days, the Clean Show will provide a complimentary shuttle between most official hotels and the convention center, according to Riddle & Associates.
Several U.S. cities have hosted the Clean Show over the years. The first two shows were in Chicago, where it has been held four times. New Orleans is hosting Clean 2019 for the sixth time, tied with Las Vegas. Atlanta follows closely behind Chicago with three shows. Orlando has hosted twice and Dallas once.
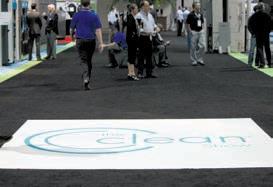
Future events are planned for Atlanta and Orlando in 2021 and 2023, respectively.
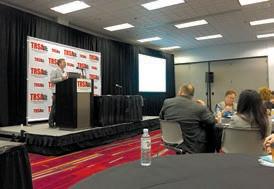
“The Clean Show is the culmination of nearly 24 months of collaboration and hard work between the sponsoring associations that represent nearly every market and demographic of the textile care
and textile services industries, from small local, single facility or store operations to regional, national and even international companies and show management,” says Ricci.
“Our common objective is to create an international marketplace for innovative products, services and solutions, as well as a forum for exchanging information regarding trends and best practices, all focused on helping our respective laundry, dry cleaning and vended laundry members improve productivity, operations and profitability.”
The sponsoring associations and Riddle & Associates have worked hard to ensure Clean ’19 will touch on all aspects of the industry in New Orleans, creating a solid foundation for the future.
“The Clean Show absolutely addresses every sector of the textile care industry,” says Riddle, “whether you’re operating in the coin laundry environment, if you’re operating in laundry, dry
cleaning, commercial/industrial laundry, or if you’re in textile rental, whether it be uniforms or linens, etc., software, hangers, computers, everything that one needs to be in this business for all sectors is
there.
“This is not just a laundry show, or a rental show, or a ‘this’ show or a ‘that’ show. This show really covers the entire industry called textile care.”
Notice Anything?



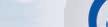

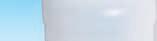








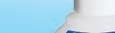
InkGo® Is Now Odor Free!

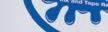



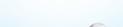
InkGo has been reformulated to remove its odor… and to improve its performance.


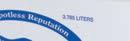

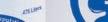

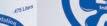


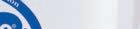
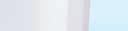
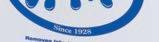

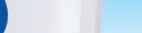

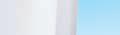

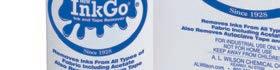
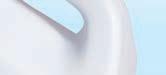
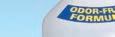
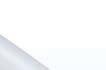
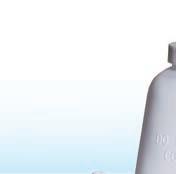
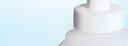
InkGo is still the environmentally friendly,* safe way to remove ink stains from all types of fabric. It’s still great at removing autoclave tape and adhesives. And since it’s odor-free, InkGo is more pleasant to work with.

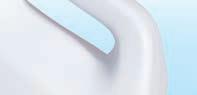
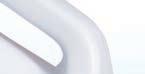
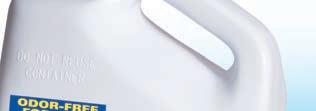
Does odor really matter? As more drycleaners position themselves as good environmental stewards, keeping chemical odors in the plant to a minimum can help them differentiate from their competition. And odor-free is a real plus if you’re working on ink for an extended period of time.
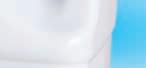

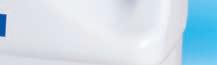
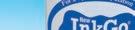
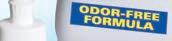
Now that’s worth noticing!
*InkGo is Biodegradable and is California Prop-65 and California VOC Compliant.

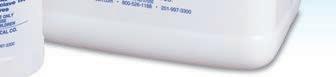
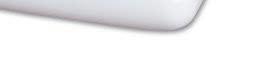
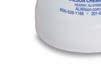


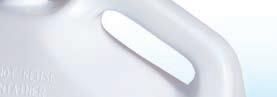
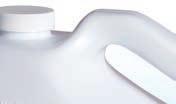
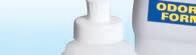

Become a STAIN WIZARD at ALWilson.com
To learn more, visit ALWilson.com or call 800-526-1188 A. L. WILSON CHEMICAL CO.


Riddle
“We had a great show in ’17 in Las Vegas, and New Orleans is right there with it right now,” he says. “Based on what I know and the years I’ve done this, I’m going to say that we can look for a good show, and, as always, you can come and actually see equipment work.”
Riddle says that aspect of the show is unique, due to the costs of shipping, setting up, and operating laundry and drycleaning equipment in a convention setting.
“We have … our package plan for exhibitor services (and) is such that it has enabled the exhibitor to actually come and operate his equipment in a cost-effective manner so that the attendee gets the advantage of that,” he adds.
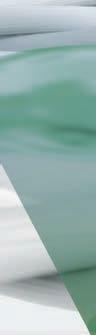
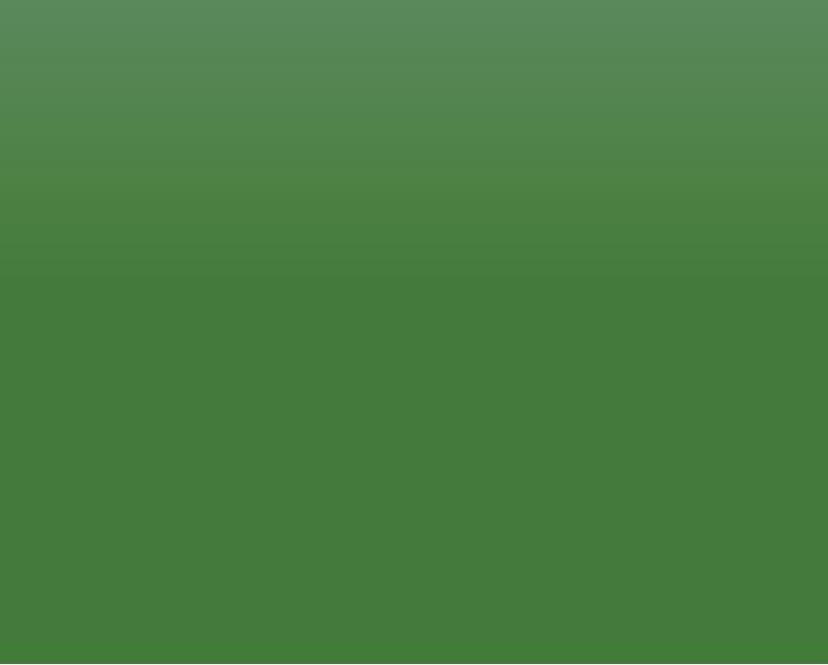
Among the trade media that publicize and cover the Clean Show, Riddle is well-known for shedding a tear or two in appreciation during the press reception that is a fixture as soon as the exhibit floor closes on the opening day.

So, if he’s already prone to becoming emotional in that setting, how will he react knowing that it will be the last time he’ll greet the media at Clean 2019?
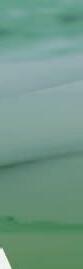
“It is an emotional thing for me to acknowledge the fact that this will be the last show that I do,” Riddle says. “I hope it won’t be the last I attend but this will be the last one in which I am in charge of it. I’ve been blessed to have been involved in this great industry since 1981.”
Riddle’s age and his desire to spend more time with family played significant factors in deciding that it was time to step aside and enjoy his golden years in a trout stream or on a golf course instead of on a show floor at 5:30 in the morning.
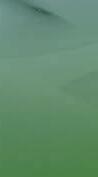
“We all have to say, ‘It’s time,’” he shares. “I think it’s time for me particularly to do that. It’s been an honor for me and for everybody in our organization to be associated with such great people.”
CIRCLING THE BASES
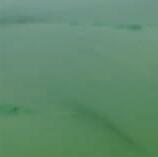
Organizing a trade show requires relationship-building and teamwork, both of which have been at the heart of Riddle’s personal and professional growth.
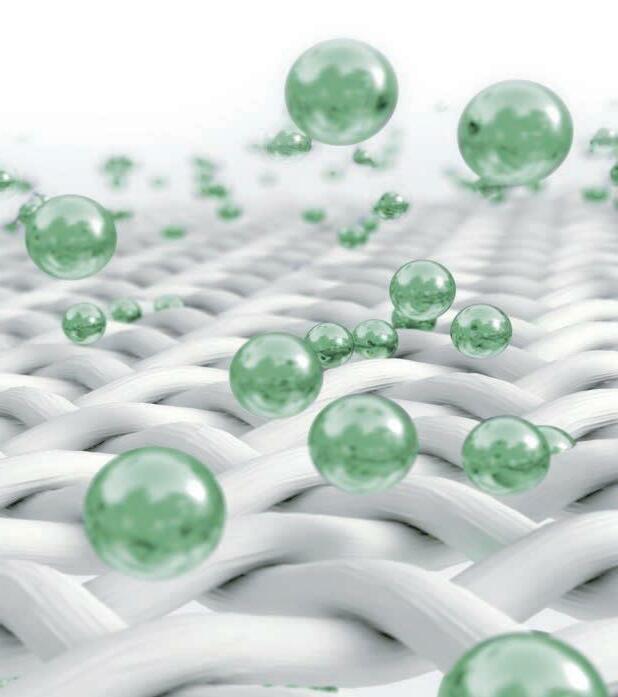
He grew up in the cotton mill town of Kannapolis, N.C., the youngest son of a
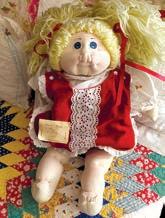
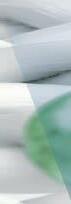
police officer and a 1st grade school teacher. You “made your own fun” in those days, he recalls, and he was drawn to team sports, especially baseball. In fact, he dreamed of playing professionally someday.
After graduating high school, he left home to attend Mars Hill Junior College and later Campbell College. At Mars Hill, he was an All-Conference and All-American first baseman in 1956 and 1957 (he was named to the College’s Hall of Fame in 1988).
At a time when there were only 16 teams in Major League Baseball, Riddle was signed by the Baltimore Orioles as a center fielder in 1962. After four years, he was traded to the Chicago White Sox organization.
“I had the chance to play for (managers) Earl Weaver, Billy Hunter, Cal Ripken Sr.,” Riddle recalls. “I played with Lou Pinella, Jim Palmer, Mark Belanger, Davey Johnson, a number of people that some will know and some won’t know.”
As a 21-year-old rookie playing for Bluefield, he slugged 16 home runs and drove in 61 runs in just 66 games, earning him Appalachian League All-Star honors. Working his way up, he also earned All-Star nods in the Class A California and Class AA Eastern leagues.
“If you ever saw (the movie) Bull Durham, you saw what minor league baseball was like,” he says. “Even when I got into Triple-A ball, we got out of yellowback school buses and old Greyhound buses, riding all over the Dakotas, Midwest, the Upper Midwest in white Edsel station wagons.
“There’s no time you can imagine, being with a group of guys at 2 o’clock in the morning, riding in a bus on a highway somewhere, dark, not a care in the world, and you’re going to go play a baseball game. That’s strong.”
But with so few MLB roster spots available, an Achilles injury that occurred on the base paths, and other circumstances, he never made it to the “Show” … as a player.
FRONT OFFICE FOUNDATION

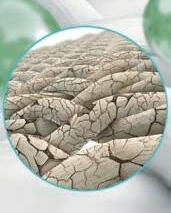
Riddle had done some offseason work for the Atlanta Braves, which had relocated there from Milwaukee in 1966.
“I was part of a team of ballplayers that were in the area who helped sell season tickets, did some PR for them,” he shares.
With a wife and a young son at home, he decided to leave his playing days behind and pursue a career of some sort. One day, he
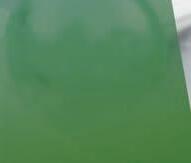

visited some friends at the stadium and left there as the Braves director of operations.
“I told the gentleman who hired me, a good friend of mine, ‘I don’t know anything at all about operations of a stadium,’” Riddle says. “We laughed, we cut up, and he said, ‘Don’t worry, we’ll teach you.’”
From there, he was promoted to director of advertising sales, plus he was promotions director for the newly formed Atlanta Chiefs soccer club owned by the Braves. He left there in 1975 to become the general manager of the Atlanta Convention & Visitors Bureau.
“I had the No. 2 position there,” Riddle says. “My job was to run the Convention Bureau on a daily basis. It’s a big promotion, in multiple ways, of a municipality.”
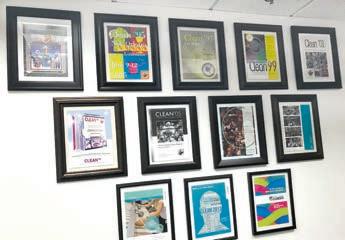
He left the CVB after about two years to enter into business for himself, owning several retail stores, including one that became famous for its link to a line of special dolls.
“I had a retail store in downtown Atlanta in Peachtree Center. It was called Terminus Gift Shop,” Riddle recalls. “It was the first store in Atlanta in which the local Georgia artisans had an outlet.”
At a regional art festival, Riddle met Xavier Roberts, who was creating soft sculpture dolls he called “The Little People,” dressing them in used children’s clothing and offering them up for “adoption.” Riddle asked if his gift shop could become an “adoption center.”
“I was No. 1,” he points out. “People went absolutely nuts over this. … That put Terminus Gift Shop, really, on the map.”
Soon thereafter, Coleco licensed the doll line as the Cabbage Patch Kids that caused shopper riots in the early ’80s and have delighted children and collectors for years.
Another unique endeavor for Riddle was rodeo promotion. With a friend he’d met through Terminus, he became interested in roping cattle.
“I was 42, got on my first horse in a long time, and the bug bit me,” he says.
Riddle was at an Atlanta restaurant one day when a friend, Spurgeon Richardson, then the president of Six Flags Over Texas, spotted him in his Western garb. The two got to talking and Richardson asked Riddle if he could produce a rodeo for the amusement park. Despite having no such experience, he said yes.
“Then, the journey began to find a stock contractor,” Riddle says. “And we did, Preston Folks. We produced rodeos for Six Flags for nine years. Sometime, if you really want to have some fun, we’ll talk about the
says he’ll miss the people and the relationships most when his decades-long association with Clean ends.
day we were putting bulls in the arena to feed them for the performance the next day and they got out.”
In the years since, Riddle has learned that it’s much easier to rope attendees than steers.
THE EXHIBITION GAME
When he worked at the Atlanta CVB in the mid-1970s, he booked a National Association of Music Merchants show for the new Georgia World Congress Center.

Right before the event, and after Riddle had left his CVB post, a tourist robbery turned fatal had the city on edge and visitors leery of coming to Atlanta.
“A number of my friends that I had met when I was at the Bureau called and asked if I could do some things to help them,” he says.
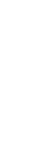
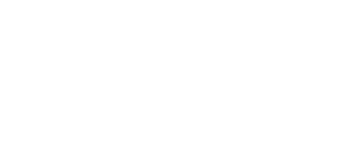

“They wanted me to have meet-and-greets at the airport, be on the show floor and help the exhibitors know that the associations were really after their best interests. I did.”
Impressed by his performance, the Music Merchants asked if he’d come to California and offer the same services for a show there.
Riddle agreed, and soon he was helping manage shows for several associations and groups around the country.
“All of a sudden, all of the things I’ve got at home, I’m on the road, trying to make people happy on a trade show floor,” he says.
One day, Riddle received a call from Ward Gill, who was executive director of the

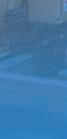



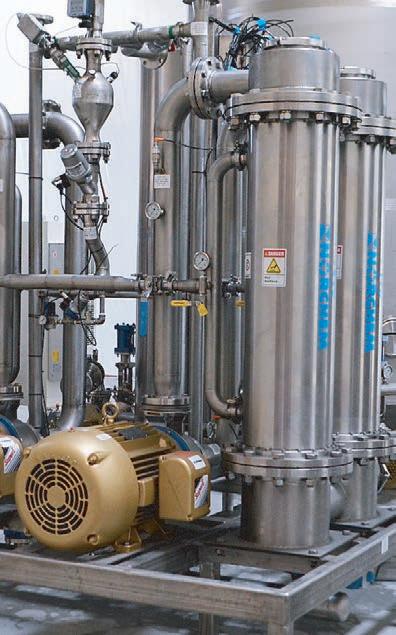
PANEL OF EXPERTS
Cleaning up at the industry trade show
especially on larger items. Manufacturers would much rather ship the machine from the show to you versus shipping them back to their plants. But these deals usually go fast, so get there early.
experience.
I recommend trying to get plenty of rest. This show is a marathon and not a sprint. You will spend much time standing on your feet during the day and late nights with colleagues and customers
associates who may help guide on the best practices to process that product would be very beneficial and help you avoid costly mistakes.
A
ttending the Clean Show can be a great way to learn what is new in the market, especially for persons new to the laundry industry. There are also several good classes that a person can gain great information from.
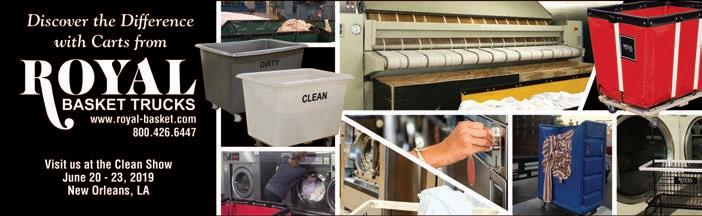

Over the years I have made one-day trips to the show when I was specifically wanting to see one item. Other years I have spent four days at the show. I have found that a two-day trip works best for me.
I think all veteran show goers have their own philosophy that helps them get the most out of the show. Here are a few that I try to use:
1. Download the show layout before you arrive in New Orleans. This will help you know where the company booths are located that you are specifically wanting to touch base with.
2. Know what your purchasing mindset will be. If you are going to purchase a piece of machinery, you should get to the show early on the first day. Many manufacturers will have machinery that can be purchased at the show. At times these deals can give you significant savings,
3. If you are going to the show to gain information on various equipment, then you would be much better served going on the last two days of the show. The show usually thins out after the first two days. Vendors have a lot more time to give you more specific details on their equipment.
Our company usually sends four of us. On our first day we usually spread out and all go our separate ways, doing a flyby of what the manufacturers have brought. Later in the day or evening we will compare notes on what we have seen. Then the following day we have a set plan on where we want to go and what we want to see.
I wish everyone safe travels, and hopefully I will see you at the show.
Before the show starts, make sure you are comfortable with the layout of the show room floor. Having knowledge of the layout helps you to prioritize the booths you want to visit.
Hopefully walking the whole show once is already on your agenda. Keeping abreast of new products and trends in the industry is paramount in being a successful operator. Attending the Clean Show is one of the best ways to stay on top of new trends and products. You might notice something you missed the first time around, which is why I choose to walk the show at least twice.
Networking is an underrated aspect of the Clean Show. Try to meet other operators that process similar goods as your plant. You might not be knowledgeable on an operation that a companion laundry uses to launder the same goods. Attending the Clean Show is a good way to brush up on learning about laundering best practices. Sharing ideas only leads to better operators, and you might make friends in the end.
Time management is very important, too. Try to stay on a strict schedule with a customer or vendor’s time as much as possible. You also might want to attend a seminar or a lecture, so make sure you did not over book time in a booth with a seminar you want to attend.
Take breaks, stay hydrated and consider wearing comfortable shoes. The Clean Show is going to be in New Orleans and in the month of June. As a local, I can tell you it gets hot and humid in New Orleans during the summer months. If you need to sit down or take a break, do not hesitate for the respite, especially if you are coming from a less humid climate.
Enjoy New Orleans and have fun. The Convention Center is located in the Warehouse District, which is walking distance to downtown and the French Quarter, plus there are ample amounts of ride-sharing vehicles and taxis available in the event you do not want to walk.
long show hours over four days) can become very trying.
AS A VISITOR
Before attending the show, plan your booth visits. Who are the exhibitors you must meet with? Identify their locations and plan the rest of your visit accordingly. We try to book appointments with the suppliers we wish to meet with. You never know what traffic at booths will be like, and you want to make the most of your presence during show hours. You ensure that the individual you wish to meet will be available and won’t need to stand waiting for long periods of time.
With the Clean Show coming up in June, I have a couple of tips to get the most out of your
Meeting other operators is especially important if you are considering adding another linen item to your business. If you were thinking about taking on a new linen item, having a network of



M
IP approaches the Clean Show from two angles: As an exhibitor and as a visitor. From these very different points of view, our strategies differ except in one very important aspect: Make sure to wear comfortable shoes. All that walking (it is a very big show) or standing up time (these are
Take advantage of the associations’ or suppliers’ social events. This ensures you will connect with colleagues that share similar interests as well as with vendors in a very relaxed atmosphere. You never know the type of connections you might make. And then of course, there is the free food and cocktails. One must know his priorities!
AS AN EXHIBITOR
Clean has so many exhibitors and attendees. We try to differentiate ourselves either by the look of the booth or the theme we focus on.
“With the Clean Show coming up next month, I’m brushing up on my trade show skills. What strategies can you recommend to get the most out of a show?”Commercial Laundry David Griggs
At your facility, your production is strategic. It’s scheduled. It happens on every shift, every day. And you don’t like surprises. It’s why we bring you purposeful engineering in powerful machines built to help your facility perform at its peak — because we don’t like surprises, either. Maximize your productivity with the help of Maytag® Commercial Laundry by your side.
GO WITH THE NAME YOU KNOW






Visit us at MaytagCommercial.com
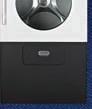

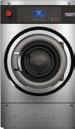







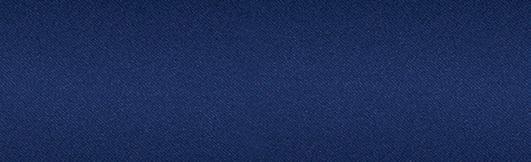





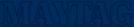
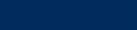















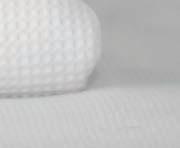



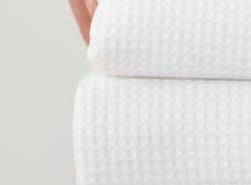

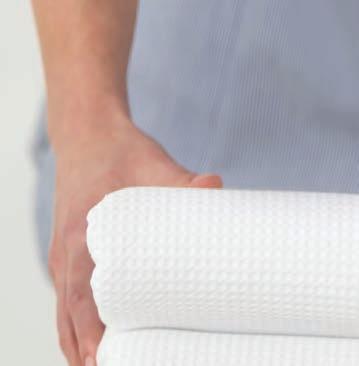



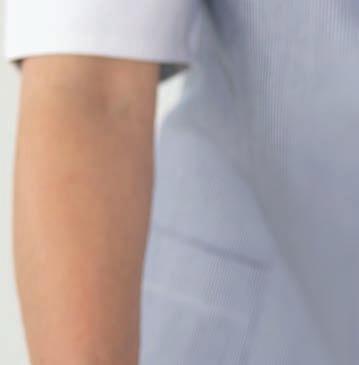
We also try to select key products/services to present instead of having a booth that overflows with everything we have in our catalog. That often leads to a feeling of confusion for potential customers and takes too much space in what is often very limited space.
When you are in the booth, make yourself available and smile. When our staff needs to rest or make a phone call, we try to make it outside the booth. In that fashion, no show attendee ever feels like they are interrupting you or being a bother when you are representing your company at the booth.
Set appointments with your key customers and ensure that you allow enough time for constructive discussions. Make sure you have an area where you can meet with them comfortable, whether it is in your booth or in the various open areas offered by the Clean organization. It allows for an even-paced discussion instead of a rushed one.
Get interested in anyone that drops by your booth. Before starting your pitch, make sure you know the person you are talking to. That way you can tailor your presentation to their needs and make them feel important.
As a supplier, you also need to attend as many associations’ events as possible, especially the ones you are a member of. You show support and meet individuals that may give you interesting pointers for the rest of the show.
IN BOTH CASES
We always found Clean to be THE show to be at for our industry. All important players are there. There are so many social events to be at, and this is where you make the connections that will last until the next Clean Show two years later.
so many compelling exhibits and sessions, it can be overwhelming. With just four days, one can’t possibly do justice to every booth, meeting or activity.
In order to get maximum benefit from Clean 2019, it is best that we, well in advance of the show, carefully plan our “Before Clean” activities, our “At Clean” activities and our “After Clean” activities. I recommend the following.
BEFORE CLEAN
Interview your plant personnel—Speak with people in your plant to understand their needs and interests. What does maintenance need? What does production need? Customer service?
Interview your customers— Speak with your customers and explain the show. What piques their interest? New linen materials possibly? New styles? Antimicrobial textiles? Educational sessions? Other innovations?
Research show exhibits & sessions—Find out which companies are exhibiting where. Identify educational and other sessions of interest.
Make a plan—Make an hourly plan of exhibits, sessions and social engagements. Don’t forget to let your team/customers know you will be out.
AT CLEAN
Attire—Be sure to wear comfortable walking shoes and attire. New Orleans can be sweltering in June. Expect to cover lots of ground.
Items to carry—Carry a notebook and a camera at all times (maybe even a step tracker). Bring a bag to hold all the handouts received. Snap pictures/videos of compelling exhibits. Share with your team at home where appropriate.
Observe and engage—You will see unbelievable displays of shiny new technical innovations demonstrated by skilled salespeople. They will work perfectly. Assess what may help your plant but beware and be hyper critical. It is one thing to make a piece of equipment work in an exhibit hall with a team of engineers babysitting. It is quite another to make it work long-term, hour after hour in the harsh environment of a commercial laundry.
Research—Research key technologies and products of interest. Ideally, gather feedback from customers using these in production.
Plan—Put together a plan to implement appropriate discoveries from Clean 2019.
So, lace up those walking shoes and prepare to prepare to grab this Crescent City extravaganza by the lapels (fully launderable and reusable of course). Happy Clean Showing!
Equipment/ Supply Distribution
cards.
• Follow up with your contacts within two (2) business days after the show.
Regarding show attendees “kicking the tires” and attendees “looking to purchase,” regardless if you are interested in purchasing new products or getting further educated on industry technology:
• Travel light to the show, wear comfortable shoes and take a large backpack or bag (tons of trinkets are given away).
• Download the Clean Show App and work your way around the event in an efficient and effective manner.
especially include asking for references of existing customers of that company so that you may have the opportunity to reach out and learn the experience of the user of those products/services you are more seriously considering. It’s key to ask what kind of common issues arise and what kind of support is provided in those instances.
If you are seriously considering purchasing equipment from an exhibitor at the show, it is worth noting that you may be able to get a discounted deal on the items if you agree to place your order at the booth.
TLC
“H enry, great to see you, how was the flight?” The Englishman had a bright smile and lovely accent to match his yellow sports coat and colorful tie, as he inquired about his guest’s wellbeing at the showroom entrance door.
This is the story I recall hearing from Chris Duffett’s team regarding his diligence to make the most of the Clean Show. More importantly, there are actions I personally witnessed as he escorted his guests around, with his assistant walking alongside detailing pertinent information.
Now happily retired, Chris, former V.P. of TLC TriState Laundry Companies, recognized the importance of being present, figuratively and literally speaking. Chris was also aware that you get one chance to make a good first impression.


“Failing to plan is planning to fail.” Benjamin Franklin’s quote is the sum total of how to maximize various situations, including the Clean Show. Let’s start with vendor tips:
• Make telephone calls ahead to share Clean Show information with your current or wouldbe clients and invite them to attend.
• Share your contact information on social media, including the location of your booth. Invite people to visit you.
• Schedule a time to meet with vendors that you are in discussion with in order to preview products of interest.
• Record information that is important to you. The faintest ink is better than the fondest memory.
• Take a small notepad and pencil, or make notes on your cell phone.
• Schedule coffee, lunch or dinner with vendors of interest.
• Have your contact information printed and ready to distribute.
• Request follow-up documentation regarding the services or products offered.
The experience will be as meaningful as you wish to make it, with your investment of time potentially rendering remarkable results. Enjoy!
Ultimately, it is in any operators’ best interest to identify a list of top exhibitors they would like to meet and set appointments in advance to optimize your time. That way you will be given the time by the exhibitor that is required to reach an informed decision.
Other Institution Laundry
Robin Kramer

St.
Ican say I always have a clear plan of action, but then sometimes I develop this secret objective I didn’t even know I had until I got there and saw something that surprised me and changed my direction a bit.
Ah, the “The Big Easy” in late June. Succulent Creole cuisine, the birthplace of jazz, the historic French Quarter with vibrant and raucous Bourbon Street, over 400 exhibits of laundry products … Wait laundry products?
As any member of the laundry brotherhood/sisterhood worth their weight in 1.75-pound bath blankets knows, June is the time for our industry’s bi-annual trek to the Clean Show, which is hosted in New Orleans this year. With

Network—Get out there and network. Meet vendors, other laundry operators and industry experts. Your network is among your most important assets. Clean 2019 is the best opportunity in our industry to build this network.
Identify follow-ups—Identify a manageable number of follow-up products, associates and ideas.
Enjoy—Explore and experience all that New Orleans has to offer.
AFTER CLEAN
Reach out—Reach out to new acquaintances, thanking them for their time.
Share—Share your experiences and lessons with your team and with your customers
• Preschedule a meeting with clients who are interested. Plan a time, place and space to meet and be on time. If you are not 10 minutes early, you are late.
• Download the mobile Clean Show App to make it easier to navigate the floor.
• Escort the folks you are meeting to the specific booths that display the products of interest to them.
• Don’t overwhelm them with data, just a few facts. They will ask questions that are relevant to their operation and to their needs.
• Provide and request contact information and take an ample supply of business
The Clean Show is one of the biggest events of the year for exhibitors and attendees alike in the Clean industry, and with that in mind, it is critical to develop a strategy to make the most out of your time at the show. The following are my recommendations for any operator of a laundry attending the Clean Show.
Simply put, the most important step toward having a productive show experience is by taking an assessment of your operations with your production managers and chief engineers to see where you’d like to bolster efficiencies in labor, utilities and material.
Ask the question, “What do I need to make me more competitive in the long term?” and then begin researching what is new out there that can support your objectives. The best way is to use the trade show website to find the exhibitors that are specifically listed for the solutions you are evaluating.
Pick the vendors that you determine would be beneficial to meet with during the Clean Show and set up appointments. Prepare a list of questions you have,
I am like most people and I love my own technology, but I always use the show’s app (as well as signage and the show staff) as my arsenal to get what I came for. Keeping up with industry trends is definitely my driving force. I watch the working demonstrations because I know it will be a long time before I get another opportunity to see all of that in action in one place—after all it is THE biennial textile care event!
But, I always let exhibitors know that I am on a tight schedule and that I am protective of my dollar. When making appointments, I try to get the first or the last for the day, leaving plenty of room in the middle for some unorganized networking activities. Your chances are high that you’ll meet some wonderful professional contacts (even sitting at the lunch table).
I venture to be wise and make time to attend as many educational sessions as possible that serve my niche. I opt in to all of the classes that genuinely pique my interest. I was especially pleased to see that some educational sessions are being offered a little later in the morning this year. This shows me that the promoters are listening to feedback because I know this has been a request. It feels like they have shined a light on perceptions, behaviors and the needs


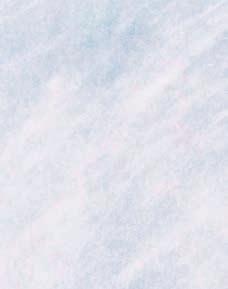
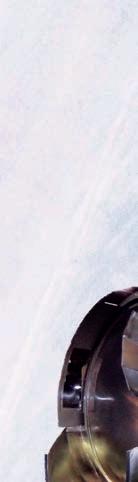
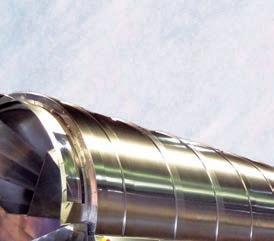

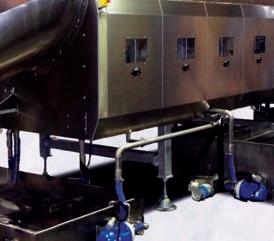
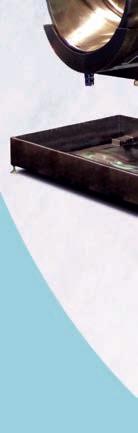
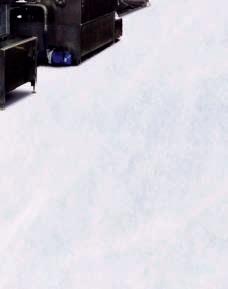
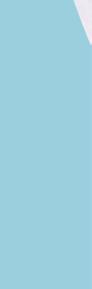
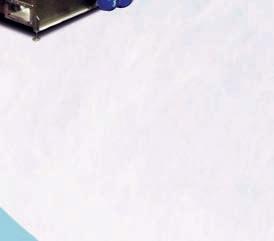
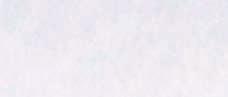



of attendees.
My follow-up strategy is pretty simple: I sort info I’ve collected for coworkers who did not get to come into envelopes with their names and use sticky notes to jog my memory of why I saved it for them. And finally, I sort through those business cards I received and send connection invitations on LinkedIn.
Oh, and this one has been etched into my mind, I don’t forget to remove my name badge as soon as I leave the convention center. I don’t want to be advertising that I am from out of town and a name badge screams “this person is a tourist, likely on expense account, with a phone and maybe even a laptop” to pickpockets and the like.
That is nothing against New Orleans, which never ceases to amaze me. I love attending the show there, and the event is always amazing. And when it’s over, I plan to embrace the culture at the NOLA Caribbean Festival (at Central City BBQ) on Saturday, June 22. It looks like a blast, and it’s only $20. See you at the show!
ary quotes that can be used for comparison.
It is also helpful to speak with other operators who have recently made similar purchases. Learn the pros and cons of their experiences and prepare a list of questions to allow more thorough follow-up at the show.
Schedule appointments for private booth time with your prospective vendors before going to the show. Some years back I worked for one of the major equipment manufacturers in our industry and I saw the value of scheduling appointments, firsthand. By blocking out specific times, you will have your vendor reps’ undivided attention.
Be sure your sales rep includes his/her boss and even the president of the company if possible. Having the highest possible authority present at your meeting will increase your chances of negotiating the best deal.
Additionally, be open to purchasing show floor demo equipment if applicable. Equipment manufacturers would rather sell equipment off the floor and ship it directly to you as opposed to shipping it back to their factories, and they are often willing to provide discounted pricing to do so. Purchasing a floor model also allows you the opportunity to see your specific machine in operation before you buy.
Finally, remember to take advantage of the seminar and educational opportunities that the show has to offer. From sales and service to plant operations, there is always something to learn. This is especially valuable for those managers new to our industry.
I t’s Clean Show time again.
Vendors and equipment manufacturers are working diligently to prepare for the show to make the best impressions and assure success. As an operator, to assure a successful show and accomplish your goals, you should prepare as well.
There are many reasons to attend a trade show. Some have specific equipment needs and want to explore their options (often with the intention of closing a deal), while others simply enjoy the opportunity to look around, catch up with industry friends and get away from the plant for a few days. For the purpose of this article, I will focus my comments primarily on those operators with specific equipment or product needs.

Be sure to research potential purchases in advance. Have conversations with vendor reps to learn the benefits of their equipment, products or services. For major capital purchases, I do recommend getting price quotes from all prospective manufacturers prior to the show. Even if you have not settled in on the specific options for your purchase, vendor reps will usually provide budget-

Enjoy Clean 2019 and be sure to prepare to guarantee a successful experience.
car dealer, both my wife and I could not believe how the technology and interiors of cars have advanced since she purchased her current vehicle back in 2009. I think the new technology if nothing thing else intimidated her and raised concerns as she did not understand how it all affected the efficiency of the automobile.
Being a smart shopper, and getting excited about the possibility of purchasing a new vehicle to replace her current mode of transportation, we created list of concerns and created a want list for her new vehicle: How many miles per gallon does the car get? How long does it take to get from zero to 60 when pulling onto a highway? How much storage space does the vehicle offer? What is the safety rating of the car? Does it come with a navigation system? Does it have heated seats? Does it have a rear camera? What about floor mats, are they included? What other colors options for exterior and interior are available?
However, wait for it … then came the best part of the buying experience—she walked around the car and kicked the tires.
There is so much to on display that two to three days might not be enough time.
Machinery companies will be highlighting the latest technology their equipment has to offer. Attendees will marvel in awe at the massive pieces of machinery designed to produce and process faster while using less energy to operate, in some cases less chemicals, and more importantly reducing our rising labor costs while increasing production.
Other companies will be displaying equipment capable of scanning bar codes or reading RFID tags, thus offering solutions for quicker more efficient garment sorting and route makeup.
Apparel and textile manufacturers will be introducing new fabric technology that addresses the issue of reducing both processing and labor costs. They will also be highlighting new, innovative styles desired by the daily changing healthcare and hospitality market end-user.
new soil sort or conveyor system? Will I be able to reduce labor?
c) Maybe you are looking new ironers and dryers. Gas, electric or steam?
d) How about steam tunnels? What is the speed of the tunnels and how many garments per hour will it process?
e) RFID technology or bar code? What is best for your operation? What savings and benefits will this offer to my laundry and customer base?
f) Uniforms and apparel. What about new fabrics, styles and colors in healthcare apparel and uniforms? Are they industrial laundry friendly and energy efficient?
Being a seasoned veteran of attending these shows as both an operator and now as a supplier, when I first enter the massive convention center with my to-do and want lists in hand, I look and study the map and layout of the convention hall and highlight the specific vendors or areas I need to visit. Without a game plan in hand, one can typically waste too much time walking up and down the aisles in search of that one item on your want list.
Make a game plan of how you wish to attack the show. If you are with a group of co-workers, divide and conquer. Maybe split up, look at different vendors and ideas, and then regroup at lunch or at the end of the day to discuss your findings and decide how and who to revisit either later that day or the next day. This will allow you to maximize your time and efforts while attending this show.
Recently I had the wonderful experience of looking for a new car for my wife (note: before the process started I had dark hair and by the time it ended, I was gray and balding).

A little background history: My wife was driving a Volvo XC90 that had 245,000 miles on it and unfortunately since her Volvo was running like a champ, and having the genes of her father, she was hell bent on driving this car till it stopped dead in its tracks.
After long deliberations back and forth between us, and given the high mileage on her car, we thought it might be a good idea to consider replacing her vehicle with a newer, more efficient one. With that said, off to visit car dealers we went.
During our first visit to a local
This adventure made me think about the upcoming Clean Show and how exciting it must be for those attending the world’s largest trade show geared for laundry operators, whether you are a firsttime attendee or a repeat visitor. This is a show unlike any other trade show in the world.
This massive, one-of-a-kind trade show displays laundry equipment for processing, machinery for finishing, technology for garment sorting and identification, uniforms and apparel for the employees and end-user. At this show, one can find everything and anything that has to do with our industry, whether we are on the processing side or the manufacturing side. One might ask, “What should I expect when I get there?”
The Clean Show is so big, you need to plan at least two to three days to see, visit and walk this show. For the one who is attending this show for the first time, be prepared to be overwhelmed.
Chemical companies will be displaying their new chemicals geared to reduce wear and tear on the textiles processed in our plants while again influencing linen life and overall quality of products in our plants
There is so much to see at this show that for the first time or repeat attendee, this show is going to be a mind-blowing experience. So here are a few suggestions, I would like to offer in order for you to get the best experience out of this show:
1. Make a list of what you want to accomplish while attending the show so you do not waste time walking the show.
2. What is your goal and purpose for the show? What are your wants and needs for your current operation and what is needed to improve your productivity?
3. What are looking to purchase or try to learn more about?
a) If it is machinery, what type of equipment are you interested in and looking for it to accomplish for you in your plant.
b) Are you looking for a
I can assure you that this is going to be a grueling, tiring process for you and suggest you wear comfortable shoes or sneakers, as you will be doing a lot of walking and talking while attending Clean 2019 and will definitely achieve your daily steps.
This is a great show and I for one having over 38 years’ experience in the industry look forward to attending this show every two years. Even as a vendor, I always walk away from it learning something new and finding better ways to do my job and offer more ideas to my customers that will help them exceed their customers’ expectations.
My last piece of advice I have is have a good time. Yes, the new technology can and will be overwhelming. Take it all in and be open to the new technology and ideas you are about to witness. Be sure to ask many questions and most important of all, do not forget to kick those tires on the new machinery as well.
Have a great Clean Show! Make sure to come visit the team from Fashion Seal Healthcare and Wonder Wink. We are looking forward to meeting with you very much.
BECAUSE THERE’S NOTHING UNIFORM ABOUT FLEET REQUIREMENTS.
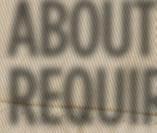
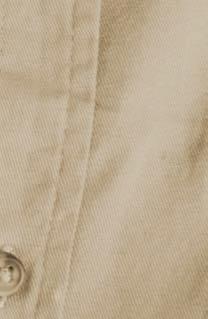
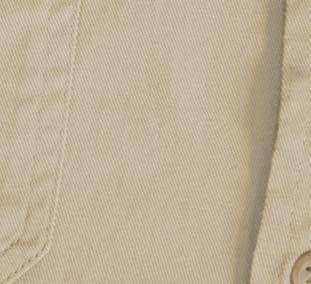

With Freightliner Custom Chassis, it’s all about delivering greater profits through increased productivity and proven fuel economy. Our commercial chassis feature heavy-duty components that are designed to surpass automotive-class vans for maximum uptime and unbeatable driver safety. FCCC chassis also provide the ultimate flexibility for box configurations to meet your needs. Most importantly, as an FCCC owner, you have access to 24/7 factory support and the largest nationwide service network.

FUEL EFFICIENCY
No matter which power you choose, you can count on the MT to lead the way in fuel efficiency that translates into enhanced profitability.
SAFETY
From heavy-duty braking to maneuverability, ergonomics and curbside access – driver safety is our top priority.
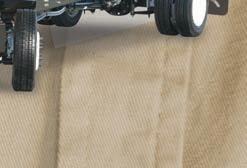

QUALITY
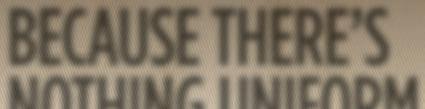
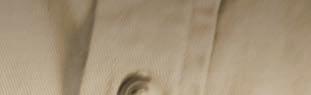
As part of the Daimler family, FCCC chassis are developed with legendary resources for design, engineering and manufacturing processes.
UPTIME

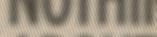
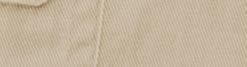

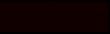


With 24/7 factory support and the largest nationwide service network, issues are quickly resolved to keep you on the road.
FUEL OPTIONS Choose from gas or diesel to best meet the needs of your delivery fleet.
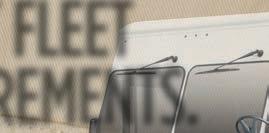
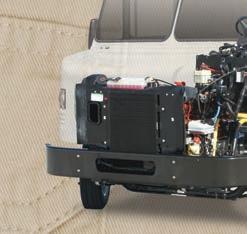
Never stop learning about your industry
Networking with peers, attending conferences, training, webinars constantly provide new ideas
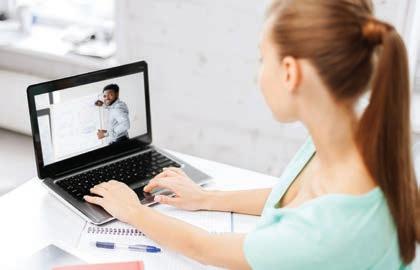
RIPON, Wis. — No business stays the same forever. Progress is not just inevitable, it’s required. This includes our industry.
While it might be easy to lean on the old phrase, “Don’t mess with success,” the truth is that just because an operation has processed loads one way for years, maybe decades, it doesn’t mean there can’t be improvement.
Staying up to date and educated on new advancements in equipment and processes helps ensure the laundry is measuring up in terms of both quality and efficiency.
JOIN AN ASSOCIATION/ ATTEND EVENTS
There’s no debate that joining organizations such as TCATA, the Association for Linen Management (ALM), the American Reusable Textile Association (ARTA), TRSA or other national/regional organizations specific to you brings tremendous upside. Some associations focus on distribution and manufacturers, but they are great sources to learn best practices.
However, greater value can be leveraged through various educational opportunities and webinars.
Membership in these organizations is as simple as you get out what you put in.
We are all busy and often don’t carve out time for such learning opportunities. We join an organization, read the newsletters, but sometimes don’t make more time to take our involvement any deeper.
Trust me, making time for conferences and webinars truly is time well spent. Not every session is going to elicit an epiphany and a deluge of changes you’ll make to your operation, but if you walk away with one solid idea, it’s worth it. The nature of education and continuing it is to, at its base, elicit additional thought—that resonance that happens afterward. This is where you begin looking at the operation with new eyes.
Networking with peers at these events also is well-spent time. We can all agree that chatting with others in our profession offers casual access to new ideas and new ways of thinking. But again, you must put forth the effort and engage with those folks.
ATTEND THE CLEAN SHOW
Let’s face it, we could generate a list that will fill this entire space with reasons to leverage the educational value of our largest trade show.
For starters, the educational sessions, which are well attended, always do a fabulous job of getting professionals in our industry updated on timely topics. Best of all, they often include a good mix of general and specific topics.
For instance, if you are attending this year’s event in New Orleans in June, you’ll see themes such as, “Preventing Microbial Growth and Infection in Laundry Facilities” and “Labor Law and Compliance: Current Issues and Trends.” Those are just two of the many educational session topics at the show, but they illustrate the broad range of learning available over the four-day run. It’s definitely worth your time to go out and visit the site and see what’s scheduled.
Learning at The Clean Show is not confined to just the breakout sessions. The show floor offers a wealth of opportunities. Having all the key equipment manufacturers and providers of
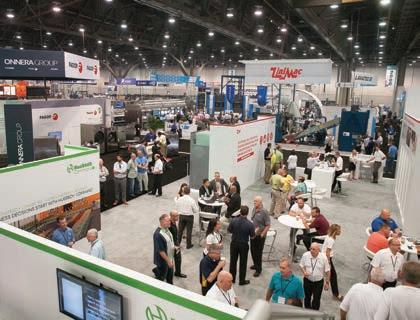
additional services and products in one spot is a fantastic chance to see what’s new and get your own new ideas on how you might leverage advancements in all those arenas.
I would stress that you come with a plan in hand. Decide before leaving what areas you want to explore. Get a grasp on your pain points or areas that might need improvement.
Are utility costs going up? Maybe you want to look for new washer-extractors and drying tumblers. Is labor management a question? Maybe you want to draft a list of the different technologies you want to better understand and how they might work to help manage your operation. Laundry chemicals? No better place to see the options.
Again, have a plan of specific areas you want to improve and the booths you think may offer solutions.
MANUFACTURER, DISTRIBUTOR TRAINING
Many equipment manufacturers and even local distributors offer training to help owners get better acquainted with their machines. This can be another great way to increase your educational base. Often, such training is focused on service and maintenance tasks.
Certainly, I always recommend managers take advantage of such opportunities. When we have a better understanding of how our machines operate and how small process variations can
negatively impact overall laundry performance, we are better off.
I think it’s particularly important in terms of technology. Work with your distributor to understand the features and functionalities of what you paid for. Today’s equipment can track large amounts of data. Working with the manufacturer and distributor to learn how to efficiently collect and leverage the information will help your operation.
Take the time to learn these details and then continue to expand your knowledge base through networking with peers to see how they are using it.
FINAL THOUGHTS
If we aren’t growing, we are stagnating. And in this so-called “information age,” there’s no excuse for not taking advantage of opportunities to expand our knowledge base. We just need to set aside time to grow.
If the perfect laundry was established decades ago, we’d never have a need to upgrade equipment. That’s clearly not the case.
By networking with peers, attending conferences, training and webinars, we give ourselves a variety of options to glean new ideas to implement in our own operation. Never stop learning. ALN
Bill Brooks is the national sales manager for UniMac, a provider of onpremises laundry equipment. He can be reached at bill.brooks@alliancels. com or 920-748-4437. Brooks

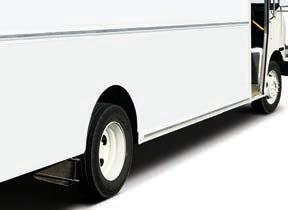
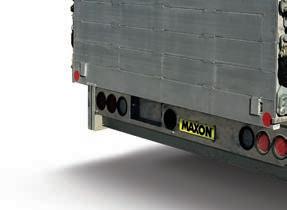
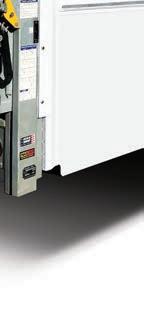
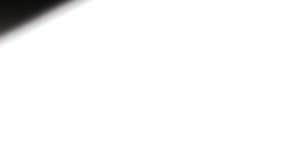
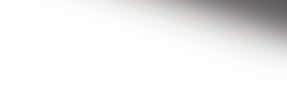
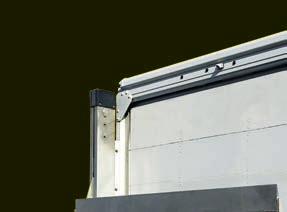
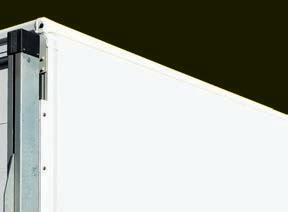
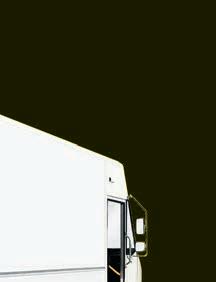

Clean ’19 exhibitors near 420
The following companies and organizations have reserved exhibit space in the Ernest N. Morial Convention Center for Clean ’19 as of April 4, according to show manager Riddle & Associates.
123
❏
21st Century Dry Cleaners 1304
Route Pros
Training services: route sales/marketing; management/customer service.
❏
AABG Systems 1855 Healthcare textile traceability and identification systems.
❏ Abrasive Technologies 4472
❏
ABS Laundry Business 4752 Solutions Route accounting, garment tracking and linen management software and systems.
❏
Ace Heaters LLC 4257 Water heaters and related equipment.
❏
ADI American Dawn 3164
Reusable textiles for rental and institutional laundries, including toweling, table linen, bed linen, patient gowns, scrubs, chef apparel, lab coats, butcher frocks, wraparounds and specialty apparel.
❏
Advanced Poly Packaging 4357
Customized equipment solutions designed to bag bar towels, mop heads, microfiber towels, gloves or other small textiles, as well as folded or bulky products.
❏
Air & Water Systems 4816 Specializes in industrial humidification and evaporative cooling equipment.
❏
Air World Inc. 4427
Manufacturer of pads, covers and drycleaning supplies.
❏
Albatross USA Inc. 4742 Cleaning chemicals,
The list totals approximately 417 exhibitors at press time; it’s possible that more exhibitors will be added in the final weeks leading up to the June 20-23 event. Where available, the descriptions of products and/
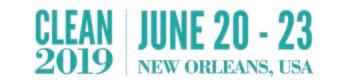
adhesives and lubricants for textile production and care.
❏ Alliance Laundry Systems 3543
Commercial laundry equipment and services under the Huebsch®, IPSO®, Primus®, Speed Queen® and UniMac® brand names.
❏ Alliant Systems 1730
Route accounting softwarefor the textile rental industry.
❏
A.L. Wilson 1136, 1637 Chemical Co. Stain removers and other chemicals for professional drycleaning and laundry use.
❏
or services provided here are general in nature and should not be considered all-inclusive. Listings are subject to change without notice. Check www.cleanshow.com for any updates.
American Associated 1203 Sources and distributes linens to healthcare, hospitality and commercial laundry markets.
❏
American Changer 1562 Manufactures banknote changers, redemption devices, custom solutions, and tokens.
Educational Sessions Schedule at a Glance
THURSDAY, JUNE 20
8-8:55 a.m. Customer Migration ALM 8:30-9:30 a.m. Laundries Connecting Communities CLA 8:30-9:30 a.m. No Bad Days: Positive Attitude is Everything DLI 8:30-9:30 a.m. Protecting Your Customer, Employee and TRSA Business Assets Through New and Improved Contracts 9-10 a.m. Preventing Microbial Growth and Infection ALM in Laundry Facilities
2-3 p.m. Social Media Marketing and Measurement General 3:30-4:30 p.m. Workplace Risks of Legalized Marijuana? General
FRIDAY, JUNE 21
8-8:55 a.m. Are You a Trusted Advisor? New Role of Sales ALM 8-9 a.m. Laundromat Lifecycles: Planning for the Future CLA 8-9 a.m. Venture Capital and Private Equity TRSA 8-9 a.m. What First Impression Does Your Website Make? DLI 9-10 a.m. New Textile Technologies for Infection Prevention ALM 9-10 a.m. ARTA Study Shows Peracetic Acid Kills C.diff Spores ARTA 9-10 a.m. CLA Connect LIVE: Interactive Idea Exchange CLA 9-10 a.m. Are Your Marketing Methods Changing with DLI Your Clientele?
9-10 a.m. Labor Law and Compliance: Current Issues TRSA and Trends
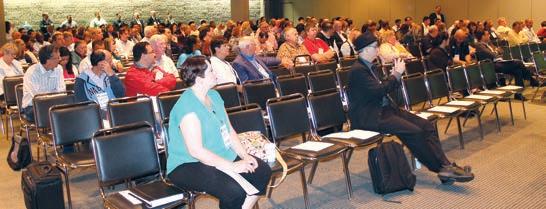
2-3 p.m. Helpful Business AppsBeth Z - Your Nerdy Best Friend
❏ American Coin-Op 4645 Trade magazine, website, podcast and social media for self-service laundry owners.
❏ American Drycleaner 4645 Trade magazine, website, podcast and social media
3:30-4:30 p.m. Secrets to Chick-fil-A Hiring & Training General for Exceptional Customer Service
SATURDAY, JUNE 22
8-9 a.m. Wash-Dry-Fold 2.0: What’s Next for CLA Full-Service Laundry?
8-9 a.m. Customer Service: Being Good is Not Enough DLI 8-9 a.m. TRSA Certification: Hygienically Clean, TRSA Clean Green, Certified Professional Laundry Manager (CPLM)
8:30-9:30 a.m. Consistent Benchmarks for Competitive Analysis ALM 9-10 a.m. New LCA Data and How to Use LCAs ARTA to Help Convert Clients to Reusables 9-10 a.m. Due Diligence: Preparing to Buy (or Sell) CLA Your Next Laundromat
9-10 a.m. Tips for Entering the Wash-Dry-Fold Market DLI 9-10 a.m. Top OSHA Violations and New TRSA TRSA Safety Certification Program
1-2 p.m. Tips for Entering the Commercial Laundry Industry General 3:30-4:30 p.m. #NotHere: Sexual Harassment Prevention General
SUNDAY, JUNE 23
8-9 a.m. Introduction to Laundromats for Investors CLA 9-10 a.m. Top 10 Secrets First-Time Laundromat CLA Owners Must Know
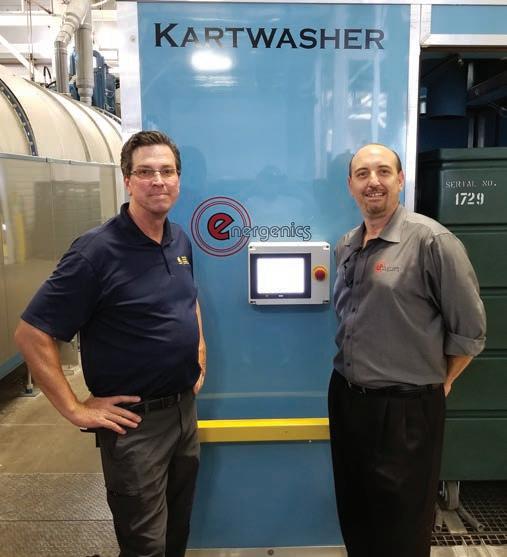







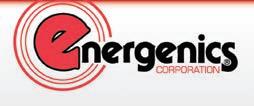


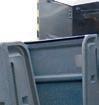
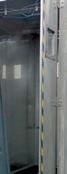
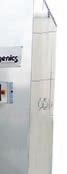
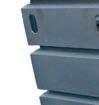

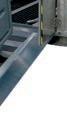
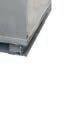
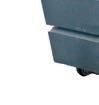





❏
Exhibitors
❏
for drycleaning businesses and suppliers.
American Laundry News 4645
Trade magazine, website, podcast and social media for managers and administrators of institutional/on-premise laundries and textile rental companies.
❏
❏
❏
American Laundry 1865 Products
Laundry textiles and associated items for flatwork ironers.
American Locker 4702 Lockers.
American Pride Linen Co. 1167
American Reusable 1364 Textile Association (ARTA)
Member association whose mission is to create greater awareness and appreciation for reusable textiles.
❏
American Trade 4645 Magazines
Publisher of American Coin-Op, American Drycleaner, and American Laundry News.
❏
AMS Products/ 4659 Object Design
Custom-printed laundry and route bags; mesh laundry bags; barrier and impervious bags; cart covers; and other bags.
❏
Angeline Group Ltd. 3906
Operating room textile and
❏
surgical apparel, including uniforms, incontinent pads, specialized garments, surgical drapes and other technical fabrics.
ANKO 1028
OEM drain valves and chemicaldispensing pumps.
❏
AquaRecycle 1101
Water recycling and dryer heat recovery systems.

❏
Aquawing Ozone Laundry 1643 Systems - AWOIS Ozone laundry systems.
❏ ArbelSoft Inc. 4227
Specializes in creation, distribution and installation of POS systems and software created for dry cleaners, Laundromats, shoe repair and tailoring services.
❏ ARCO/Murray National 1754 Construction Co.
Design/build construction firm focused on the laundry industry.
❏
ArtiClean Ozone 2664 Laundry
Systems
Ozone laundry systems.
❏ Association for 1233 Linen
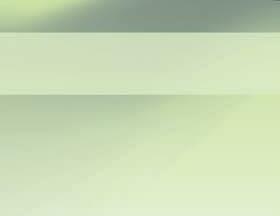
Management
Nonprofit trade association dedicated to the professional development of personnel involved in the textile care industry.
❏ Association of Wedding 4215 Gown Specialists
Nonprofit trade association for members specializing in wedding gown cleaning, preservation and restoration.
❏ A13 Srl 3573
Padding, covers, insulation, parts and accessories for ironing and drycleaning machines.
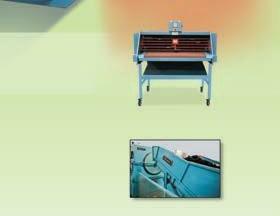
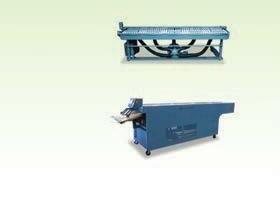
❏
Automated Packaging 1209 Systems
Flexible-bag packaging systems for industrial laundries and textile rental services.
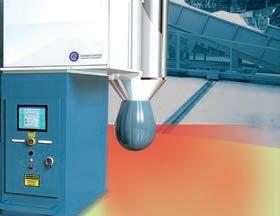
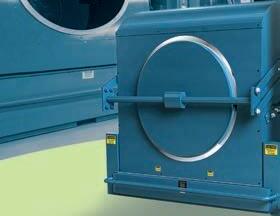
❏
Automation Dynamics 2154
Automated sorting, counting and weighing equipment for various laundry applications.
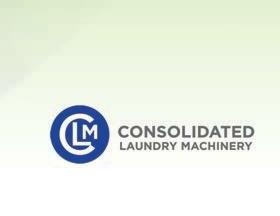
❏ Autovalet Systems LLC 4273
Automated tracking and distribution for uniforms, scrubs and linen.
❏
BB&C Technologies 1710, 1811 Commercial washers, dryers, ironers, feeders and folders.
❏ Bahnson Mechanical 4802 Systems
Industrial construction services.
❏ BC Textile Innovations Inc. 4868
❏ BCC Payments LLC 1820 Vending payments and creditcard processing systems.
❏ Beck’s Classic 1405 Reusable incontinence products,
underpads, clothing protectors, diapers and briefs.
❏
BeCreative 360 1404
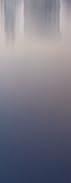
Marketing and promotions for dry cleaners.
❏
Beneficial Equipment 4926 Finance Corp. Equipment financing/leasing.
❏
Biosan PAA 4424
Peracetic acid formulations for sanitization and disinfection of laundry in commercial, institutional and industrial operations.
❏
Bissell Commercial 4643
Vacuums, power sweepers, extractors, flooring machines and other equipment.
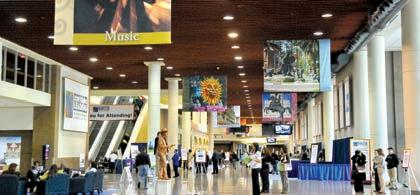
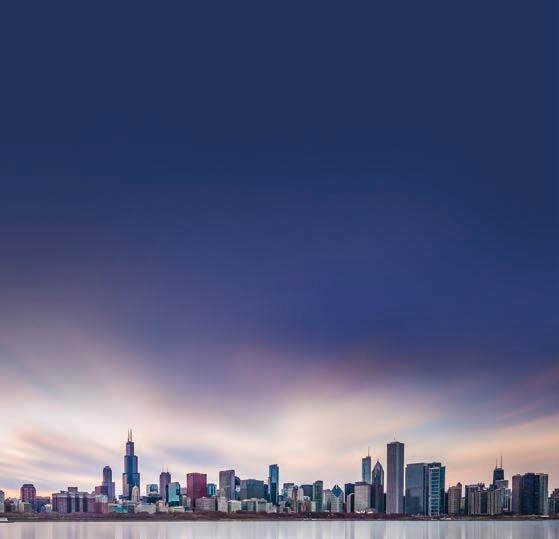
❏
BLC Textiles 4625
Wide variety of imported textiles for the textile rental industry.
❏
Bobco Systems Inc. 1463 Material-handling and garment-handling equipment and systems.
❏
Boca Terry 1262
Manufacturer/supplier of bathrobes, towels, spa wraps, lounge chair covers and slippers to hospitality, healthcare, textile/linen rental and corporate gift industries.
❏
❏
Bootie Butler 1866
BOWE Textile 4252
Cleaning GmbH Perc and multi-solvent drycleaning machines.
❏
Braun 3521
Batch tunnel washing, conventional washing, material-handling, drying, and finishing equipment.
❏
Brim Laundry 1831
Machinery Co. Inc.
Large-capacity washerextractors and dryers; touchscreen control systems; OEM replacement parts and supplies.
❏
Brooks-Waterburn Corp. 1309 Insurance services for Laundromats.
❏
❏
❏
control, automation and filtration.
❏ CACO Manufacturing Corp.2564
CCoin laundry furnishings, including folding tables, seating, clothes-hanging racks, and custom bulkheads.
❏ Calderon Textiles 1021 Distributes commercial linens to the textile rental, hospitality, cruise line CLEAN ’19 EXHIBITORS continue on Page 24
❏
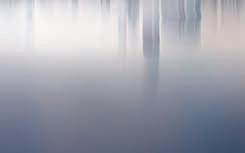
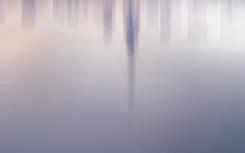
Brown-Eyed Girl Textiles 4172
Buckeye Pads and Covers 3873
Bundle Australia Pty. Ltd. 4225 Productivity software for laundry operations.
Burkert Fluid Control 3907
Systems
Water treatment process
Exhibitors
❏
❏
and retail industries.
Capital One 4205
Credit card for businesses.
Card Concepts Inc. 1955
Automated card systems for Laundromats to handle cash collections, employee management, equipment service, and store marketing.
❏
❏
Cart & Supply Inc. 1106
CBA Machines 4611
Purchases and sells second-hand industrial laundry machinery.
❏
❏
CDF Systems 4657 Mat processing systems.
CeraMem LLC 4758
Ceramic membrane modules for water treatment applications.
❏
Chem-Tainer Ind./ 1631 Maxi-Movers
Bulk delivery trucks,
❏
❏
shelved exchange carts, tilt trucks, utility carts and bushel carts.
Chevron Phillips 1166 Chemical Co.
Chicago Dryer Co. 3003
Flatwork finishing equipment, including separators, feeders, ironers and folders; data tracking technology.
❏
Chief Clean 4511
Commercial janitorial dust mops and wet mops, handles and frames.
❏
Church & Dwight Co. Inc. 4447 Laundry detergents and chemicals.
❏
Clayton Industries 3265
Equipment for industrial process steam generation.
❏
Clean Cycle Systems 2603 Lint Filters
Lint collection and exhaust air systems.
❏
CleanCloud 4543
Point-of-sale software systems for dry cleaners and laundry services.
❏
Cleaner Business 4243 Systems
Point-of-sale software systems for dry cleaners.
❏
Cleaner’s Supply® 4542
Wide range of drycleaning and laundry supplies and products.
❏
ClearToken 1467
Vended payment systemsfor Laundromats.
❏
CLM/Texfinity 729
Industrial laundry equipment, including feeders, ironers and batch washing systems.
❏
❏
CM2W JSC 4405
CMV Sharper Finish Inc. 2665
Commercial laundry flatwork ironing equipment.
❏
Coin Laundry Association 1243
Not-for-profit trade organization representing member laundry owners, prospective laundry owners, and equipment manufacturers and distributors.
❏
Colmac Industries 4130
Garment finishers, automated soil sorting and counting systems, and garment presses.
❏
Columbia/ILSA 3943 Machines Corp. Drycleaning machines.
❏
Commercial Coils Inc. 1734
Replacement coils for laundry and drycleaning equipment.
❏
Computer Software 1213 Architects
Linen management and distribution software.
❏
conveyors, and mat rollers.
❏ Continental 2021, 2027 Girbau Inc.
Vended, on-premises and industrial laundry equipment and solutions (booth 2021 focuses on vended laundry solutions, booth 2027 focuses on industrial and commercial laundry solutions).
❏ Covers Etc. Inc. 4349
Laundry and drycleaning pads and covers.
❏ Creaset® Permanent 4655
Crease Systems
Garment creasing system.
❏ CryptoPay/WorldPay 4700 Card payment system for Laundromats. ❏ Cupron 4411
❏
Curbsidelaundries.com 1863 Wash and fold POS software for Laundromat owners.
D❏ Dajisoft Inc. 4311 Point-of-sale drycleaning software systems. ❏ Dark POS 4258 ❏ Darman Manufacturing 1114 Co. Inc.

Cloth roll towel cabinets, paper roll cabinets, and towel winders and unwinders. ❏ Datamars Inc. 2255 Radio frequency identification (RFID) products for textile identification markets.
❏ Davis Packaging 4415 Laundry wrapping equipment and wrapping film.
❏ deister electronic GmbH 1162 Electronic, RFID and mechatronic systems for security, logistics and supply chain markets.
❏
Computer Systems 4510
Point of sale software for dry cleaning, Laundromats, alteration, and shoe repair.
Consolidated Laundry 2365 Machinery
Industrial dryers, shuttle
❏
Dexter Laundry Inc. 2227, 2536 Commercial washers, dryers, and laundry management systems for vended and on-premises laundries. ❏ Diamond Chemical Co. Inc.4431 ❏
Dimmid Inc. 4272 ❏ D.J. Giancola Exports Inc. 4612 ❏
Doxon Mfg. Co. 1313 Commercial laundry equipment parts. ❏ DropLocker 4324
❏
Drycleaning & Laundry 1442 Institute
Trade association representing member dry cleaners and launderers.
❏ Duncan Fabricating 1766 Co. Inc.
Coin laundry bulkheads andcommercial appliance outlet centers.
❏
❏
Dunnewolt B.V. 730
Dura-Cast Products Inc. 921 Rotomolded laundry and linen trucks, and storage tanks.
❏
Dynaric Inc. 1037
Plastic strapping and strapping equipment.
❏
systems; and vacuum systems for lint collectors.
Ensign Emblem 1047
Emblems, screen-print transfers and direct embroidery for industrial uniform and rental uniform companies.
❏ Envirochem Inc. 3807 Chemicals and detergents, specializing in powder, liquid and solid laundry, housekeeping and warewash products.
❏ EnviroForensics 4664
Environmental consulting services.
❏ ESD 1743
Mechanical and electronic payment systems for the multi-housing, vended laundry, and arcade/ gaming markets.
❏ Euro Systems Corp. 3874
❏ European Finishing 4143 Equipment
Tensioning equipment.
❏ Eurotape BV 1659 Self-adhesive products for surgical
❏
covering materials.
Evercare/Butler 4671 Home Products Lint rollers.
❏ Evoqua Water 4866 Technologies LLC Water and wastewater treatment products and services.
❏ EzProducts 4312 International Inc. Permanent tagless systems for textile labeling, heatsealing clothing text and barcode labels to fabric;
rope ties; hanger stands; and hanger equipment.
F❏ F-MATIC Inc. 4746 Odor-control and restroom hygiene products.
❏ Fabricare Management 4635 Systems

Computer software systemsfor dry cleaners and laundries.
❏ Fashion Seal Healthcare 1502
CLEAN ’19
❏
EEAM-Mosca Corp. 4006
Automatic strapping machines.
❏
Eastern Funding 2305
Offers loans to commercial laundry, professional garment care and other industries.
❏
ECC Horizon 4858
Environmental consulting and remediation company.
❏
Ecolab 2520
Laundry detergents and chemicals; dispensing equipment; water and energy management; and real-time data management for large-scale, commercial laundry operations.
❏
Ecotex Ozone Laundry 4247 Technology
Laundry disinfection systems.
❏
EDRO 2843
Industrial washer-extractors, tumbler dryers, and ozone laundry systems.
❏
❏
Ekostar Textiles 1057
Ellis Corp. 3343
Open pocket and sideloading washerextractors, industrial dryers, conveyors for automation, water heating and heat recovery systems, and wastewater and ceramic filtration systems for recycling laundry water.
❏
Encompass Group LLC 1366
Manufacturer and marketer of reusable textiles, professional apparel, and disposable and single-use medical products.
❏
Energenics Corp. 3911
Lint filters for dryer exhaust; cart-washing
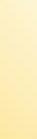


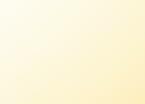
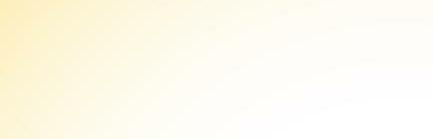

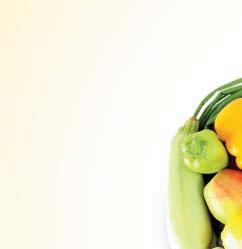
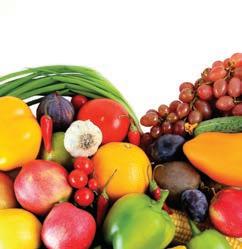
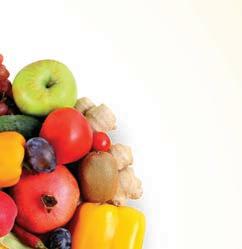



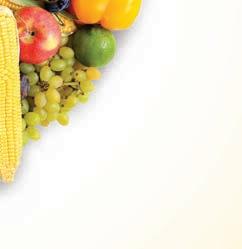


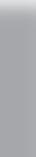
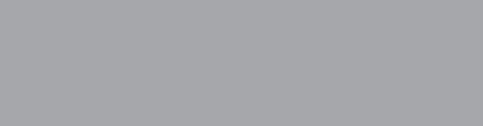



925 921
1366 1365 1364 1363 1362 1354 1353 1352 1321 1313 1311 1309 1305 1304 1301 1300 732
1467 1466 1463 1462 1453 1442 1410 1409 1408 1405 1404 1402 1401 1400 738 736 730 729 721 720
1567 1566 1565 1563 1562 1553 1543 1533 1520 1509 1504 1502 1501 1500 935 929
21st Century Dry Cleaners Route Pros 1304
A. L. Wilson Chemical Co. 1136, 1637
A13 Srl 3573
ABG Systems 1855
Abrasive Technologies 4472
ABS Laundry Business Solutions 4752
Ace Heaters LLC 4257
ADI American Dawn 3164
Advanced Poly Packaging 4357
Air & Water Systems 4816
Air World Inc. 4427
Albatross USA Inc. 4742
Alliance Laundry Systems 3543
Alliant Systems 1730
American Associated 1203
American Changer 1562
American Laundry Products 1865
American Locker 4702
American Pride Linen Co. 1167
American Reusable Textile Association (ARTA) 1364
American Trade Magazines 4645
AMS Products/Object Design 4659
Angeline Group Ltd. 3906
ANKO 1028
AquaRecycle 1101
Aquawing Ozone Laundry Systems - AWOIS 1643
Arbelsoft Inc. 4227
ARCO/Murray National Construction Company 1754
ArtiClean Ozone Laundry Systems 2664
Association for Linen Management (ALM) 1233
Association of Wedding Gown Specialists 4215
Automated Packaging Systems 1209
Automation Dynamics 2154
Autovalet Systems LLC 4273
B&C Technologies 1710, 1811
Bahnson Mechanical Systems 4802
BC Textile Innovations Inc 4868
BCC Payments LLC 1820
Beck’s Classic 1405
1031
1025 1024 1021 1020
1766 1765 1763 1762 1758 1755 1754 1743 1736 1734 1731 1730 1710 1702 1032
1667 1666 1663 1662 1659 1657 1655 1643 1637 1631 1621 1030 1028
1432
BeCreative 360 1404
Beneficial Equipment Finance Corp. 4926
Biosan PAA 4424
Bissell Commercial 4643
BLC Textiles 4625
Bobco Systems Inc 1463
Boca Terry 1262
Bootie Butler 1866
BOWE Textile Cleaning GmbH 4252
Braun 3521
Brim Laundry Machinery Co. Inc. 1831
Brooks Waterburn Corp 1309
Brown-Eyed Girl Textiles 4172
Buckeye Pads and Covers 3873
Bundle Australia Pty Ltd 4225
Burkert Fluid Control Systems 3907
CACO Manufacturing Corp. 2564
Calderon Textiles 1021
Capital One 4205
Card Concepts Inc. 1955
Cart & Supply 1106
CBA Machines 4611
CDF Systems 4657
CeraMem LLC 4758
Chemtainer Ind/Maxi-Movers 1631
Chevron Phillips Chemical Co. LP 1166
Chicago Dryer Co. 3003
Chief Clean 4511
Church & Dwight Co. Inc. 4447
Clayton Industries 3265
Clean Cycle Systems Lint Filters 2603
CleanCloud 4543
Cleaner and Launderer 2267
Cleaner Business Systems 4243
Cleaner’s Supply 4542
ClearToken 1467
CLM/Texfinity 729
CM2W JSC 4405
CMV Sharper Finish Inc. 2665
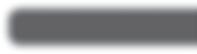
Coin Laundry Association 1243
Colmac Industries 4130
Columbia / ILSA Machines Corp. 3943
1866 1865 1863 1862 1855 1831 1824 1820 1811 1803
1267 1266 1265 1264 1263 1262 1243 1233 1225 1221 1213 1209 1203 1201 20' 30'
1964 1962 1955 1943 1921
information supplied by: Riddle & Associates
Commercial Coils Inc. 1734
Computer Software Architects 1213
Computer Systems 4510
Consolidated Laundry Machinery 2365
Continental Girbau Inc. 2021, 2027 Covers Etc. Inc. 4349
CREASET Permanent Crease Systems 4655
CryptoPay/WorldPay 4700
Cupron 4411
Curbsidelaundries.com 1863
D.J. Giancola Exports Inc. 4612
Dajisoft Inc. 4311
Dark POS 4258
Darman Manufacturing Co. Inc. 1114
Datamars Inc. 2255
Davis Packaging 4415
deister electronic GmbH 1162
Dexter Laundry Inc. 2227, 2536
Diamond Chemical Co. Inc. 4431
Dimmid Inc. 4272
Doxon Mfg. Co. 1313
DropLocker 4324
Drycleaning & Laundry Institute (DLI) 1442
Duncan Fabricating Co. Inc. 1766
Dunnewolt B.V. 730
Dura-Cast Products Inc. 921
Dynaric Inc. 1037
EAM-Mosca Corp. 4006
Eastern Funding 2305
ECC Horizon 4858
Ecolab 2520
EcoTex Ozone Laundry Technology 4247
EDRO 2843
Ekostar Textiles 1057
Ellis Corporation 3343
Encompass Group LLC 1366
Energenics Corp. 3911
Ensign Emblem 1047
Envirochem Inc. 3807
EnviroForensics 4664
ESD 1743
Euro Systems Corp. 3874
1963
2063 2027 2021 2008 2002
2165 2161 2154 2142 2109 2103
1167 1166 1165 1163 1162 700 1000 1400 1900 2200 2500
1158 1156 1154 1153 1146 1143 1136 1132 1131 1130 1125 1121 1114 1113 1112 1110 1109 1106 1104 1101 1067 1065 1063 1057 1055 1049 1047 1043 1037 Ernest N. Morial Convention Clean Show 2019 Booth
2267 2265 2264 2261 2255 2227 2221
European Finishing Equipment 4143
Eurotape BV 1659
Evercare/Butler Home Products 4671
Evoqua Water Technologies LLC 4866
EzProducts International Inc. 4312
Fabricare Canada Magazine 4310
Fabricare Management Systems 4635
Fashion Seal Healthcare 1502
Felins USA Inc. 2109
Felrap World Inc. 4665
Fibertech Inc. 4621
Firbimatic 2657
First Film Extruding 935
F-MATIC Inc. 4746
Foltex 1409
Forenta L.P. 3821
Foster-Stephens Inc. 4211
FRSTeam Inc. 4607
Fujitsu Frontech North America 4106
Fulton Boiler Works 2765
G.S. Manufacturing 1301
Garment Management Systems 4521
Gemu Valves 1154
George Courey Inc. 1362
GKC Corp. 3872
Golden Star 4656
Gotli Labs AG 4854
GreenEarth Cleaning 4455
Greenwald Industries 4201
Gurtler Industries Inc. 1702
Gusher Pump 4105
Hamilton Engineering Inc. 2221
HamperApp 4369
Hanel Storage Systems 4425
Hans-Joachim Schneider GmbH 4531
Harris Pillow Supply Inc. 4473
Hartdean Ltd 4744
Hayikama 4567
Healthcare Laundry Accreditation Council (HLAC) 4610
Heat Seal LLC 4173
High Mark Manufacturing Inc. 1824
Booth assignments and/or their configuration are subject to change without notice. Listings are current as of April 4, 2019
HJ Weir Engineering 4925
HJLite 4421
HK Textiles Inc. 4571
H-M Co. 1962 Hoffman Mint 1563
Hoffman New Yorker 2864
Hot Water Products 3803
Hunt Textiles 4465
Hurst Boiler 4102
Hutchinson Belt Drive Systems 4528
Hydro Systems Co. 4321
Hydrofinity 1964
Imonex Services Inc. 1566, 1567
Independent Textile Rental Association (ITRA) 4564
Industrial Gold Air Compressors 1266
Indy Hanger & Supply 4613
Infinite Creative Enterprises Inc. 4003, 4808
InnoClean Corp. 4666
Innovative Management Designs 2265
Inox Milton 736
Irving Weber Associates (IWA) 4451
Isuzu Commercial Truck of America 1453
Italclean Srl 4443
Itsumi USA, Inc. 4165
J.P. Equipment Inc. 1803
JENSEN USA Inc. 2621
Jiangsu Sea-lion Machinery Co. Ltd. 2103
JLT Co. Ltd. 4372
JS Fiber Co. Inc. 1265
Kaeser Compressors Inc. 1401
Kannegiesser ETECH 3021
Kemco Systems Co. LLC 2965
Keycolour Inc. 4325
KioSoft Technologies LLC 4374
Kleen-Rite Inc. 4673
Kleen-Tex Industries Inc. 4850
Klopp Coin Counters 4924
Korean Cleaners Monthly 4210
Kreussler Inc. 2357
Lac-Mac Limited 1365
Lapauw USA LLC 1621
American Trade Magazines Publisher of American Laundry News Booth 4645
2864
2965 2943
3265 3165 3164 3155 3143 3021 3003
3364 3355 3343
3573 3565 3543 3521
3673 3665 3602
4365 38733872 3865 3855 3829 3821 3811 3807 3805 3803
Convention Center, New Orleans 2019 Floor Plan Floor plan prepared by: a2z Inc.
44734472 4468 4467 4465 4464 4459 4455 4451 4448 4447 4065 4021 4011 4006 4004 4003 4002
4325 4324 4321 4313 4312 4311 4310 4307 4305 4301 3765 3755 3743
4443 4431 4427 4425 4424 4421 4415 4414 4411 4410 4406 4405 4404 4402 4401 4400 3965 3943 3911 3907 3906 3903 3902
457345724571 4567 4566 4565 4564 4557 4553 4550 4543 4542 4535 4531 4528 4525 4524 4521 4514 4513 4512 4511 4510 4505 4501 41734172 4165 4143 4130 4121 4113 4111 4106 4105 4102 4101
3874 3672 20' 20'
4673 4671 4666 4665 4664 4661 4659 4657 4656 4655 4653 4652 4645 4643 4635 4631 4625 4621 4613 4612 4611 4610 4607 4601 42734272 4265 4258 42574256 4252 4247 4243 4233 4227 4225 4221 4215 4212 4211 4210 4205 4201
Lattner Boiler Co. 1300
Laundroworks Card Systems 3673
Laundry Logic LLC 1267
Laundrylux 2642
LaundryPass 2063
Laundry-Trak 4414
Lavatec Laundry Technology Inc. 2343
Lavo Solutions 3672
LCT 4572
Leebaw Manufacturing 3902
Leonard Automatics 2943
LG Electronics 720, 721
Linen Tech 1146
Low Cost Mfg. Co. 2360
M&B Hangers 3811
M+A Matting LLC 4459
Maestrelli Srl 2537
Magid 4402
Main Street Hub 4111
Mainetti 4768
Mamute Laundry 4464
Marina Textiles Inc. 4468
Maruso USA Inc. 4864
Material Flow Systems 1113
Maxi Companies 4513
MaxiMizer Systems 3805
Maxi-Press Elastomeric Inc 4601
Maxon Lift Corp. 1025
Medline Industries Inc. 1731
Meese 1352
Memories Gown Preservation 1305
Messe Frankfurt Inc. 1432
Metalprogetti 2008
MEVO METZLER GMBH 3165
Micross Automation Systems 1055
Midwest Specialty Products 1112
Miele Inc. 4121
Milliken & Co. 1520
Million Dollar Collar 1402
MIP Inc. 2503
Miura America Co. Ltd. 4301
Mobile Computing Corp. Inc. (MCC) 4766
Monarch Brands 1762
Monarch Coin & Security 1158
Moonsoft International 1165
Morgan & Morgan Olson 1153
Movexx 4002
Multimatic 4343
Naomoto Corp. / Apparel Machinery & Supply Co. 4824
National Cleaners Association 4764

National Clothesline 4307
National Combustion Co., Inc (NATCO) 1862
Navien Inc. 3903
Nayax 4710
NIE Insurance 4514
Norchem Corp. 1321
Noritz 4814
NuMat Systems LLC 1504
Olin Corporation 4448
OMNI Solutions 4501
Onnera Group 1943, 2309
Otto Trading Inc. 1264
PAC Strapping Products 1400
Parker Boiler Co. 1031
Paypont 4820
PayRange 929
paystri 1565
Pellerin Milnor 2703
Penco Products Inc. 4524
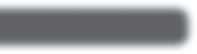
Penn Emblem Company 4410
Pepin Mfg. Inc. 4305
Phoenix Textile Corp. 1049
Pivot 1156
Planet Laundry Magazine 1163
Planiform Conveyors Inc. 1131
Plexus Industries 1063
Polypack GmbH & Co. KG 3965
Pony Spa 3665
Poseidon Textile Care Systems LLC 4557
Positek RFID 2511
Prime Capital Inc. 1758
Pristine Collars 4774
Quietaire Cooling Inc. 1065
R&B Wire Products Inc. 2420
R. L. Williams Co. 1024
R.R. Street & Co. Inc. 4221
R.W. Martin & Sons Inc. 1125
Railexcorp 4373
RAMCO Laundry Machinery Inc. 4401
Rampi S.r.l. 4467
RealStar USA 3755
Reed Mfg. Co. 2405
ReflectiveStripe.com / Block Bindings & Interlinings 1104
Rema Dri-Vac Corp. 4113
Rennco LLC 1032
Renzacci SPA 4233
Revista Multiservicios 4512
Revitec 4712
Riegel Linen Co. 1121
Rochester Midland Corp 1311
Rome Conveyors 1663
Rotational Molding Inc. 4566
Royal Basket Trucks 1963
Royal Blue Textiles 1201
Ryco Conveyors Inc. 1662
San-Ai Industries Inc. 4810
Sanitone by Fabritec 4860
Sankosha USA Inc. 3829
SanMar 2303
SEITZ, The Fresher Company Inc. 4535
SEKO Dosing Systems Corp. 4631
Select Risk Insurance Services Inc.
dba Select Programs 1110
Sensotechnics USA 4760
Setomatic Systems - SpyderWash 2409
Shanghai Lijing Washing Machinery Manufacturing Co., Ltd 738
Shanghai Sailstar/Everstrong Commercial Products 3155
Shanghai Weishi Machinery 3855
ShinePay 4800
Sigma Garment Films 4404
Sigmatex-Lanier Textiles 1225 Sintex 1030
4775 47744773 4768 4766 4764 4760 4758 4752 4746 4744 4742 4714 4712 4710 4704 4702 4700 4357 4349 4343 4327
4667
4374 4916
Restaurant 2700 3100 3300 3700 4100 4500 4900
SmartBuy TK 4573
SMC Corporation of America 4704
SNA Manufacturing LLC 4565
Softrol Systems 2855
SonicAire Inc. 4313
Spartan Chemical Co. 4011
Spector Textile Products 1765
Spindle 2611
Spot Business Systems 2002
Springboard 2264
Springpress 1408
SRS Conveyors 1667
Stahls Hotronix 4400
Standard Change-Makers Inc. 1221
Standard Textile 3364
Starchup Inc 4804
Storms Industries Inc. 2261
Streamline Solutions 1462
Striem 4367
STRY-Lenkoff Co 4406
SUDSY Vending Supplies 1763
Sumal 4505
System Laundry Management Co. 1666
Tagitron 925
Tap Laundry 1363
TBR Associates 1353
Texas Automation Products Inc. 4327
Texas Microfiber Inc. 1466
Textile Care Allied Trades
Association (TCATA) 1543
Textile Services Magazine 4653
Textile Technologies 4714
The DECC Company 1020
The Huntington Company 4553
TheLaundryList.com Inc. 1043
Thermal Engineering of Arizona 2161
Thermopatch 2403
Thomaston Mills 1263
Thornell Corp. 4004
Tide Cleaners 4265
Tingue 1354
Tolon Global Makina San. ve. Tic. A.S. 3355
Booth assignments and/or their configuration are subject to change without notice. Listings are current as of April 4, 2019
Trevil America Inc. 4021
TRSA, the Association for Linen, Uniform and Facility Services 1533
U.N.X. Inc. 1143
U.S. Jaclean Inc. 1655
Union Drycleaning Products 3143
Unipress Corp. 3743
UniSec Div. of New York Machinery 3565
United Soybean Board 4365
United Textile Distribution 4652
United Wire Hanger/UWH Industries 1736
Unitex International Inc 4101
Utilimaster 1755
Valmet 1410
VEGA Systems USA 2142
VEIT 3865
Vending.com 4212
Vend-Rite Mfg. Co. Inc. 1921
Venus Group 1509
VF Workwear 4525
Vintex Inc. 1130
Vita Microfiber International LLC 732
Voltea 1109
Wasatch Co. 4661
Wash-Dry-Fold POS 2165
Washin Jax 4256
Webb & Son Sewing Machine Sales Inc. 2364
Wedding Gown Preservation Co. 4550
Wesvic Systems 4667
wh Münzprüfer Dietmar Trenner GmbH 1657
Whirlpool Corp. 3602
White Conveyors Inc. 1501
Williamson-Dickie 4916
Winona Services 4922
WonderWink 1500
Woodbine Products Co. 1067
World Trading Company Inc. 4773
WSI 1553
YAC Japan 4065
Yamada 1132
Yamamoto Japan Inc. 2556, 3765
Your table linens touch every Customer at every event. Your linen needs to speak their language… fresh, clean, safe, consistent, reliable, and yes elegant. They count on it.
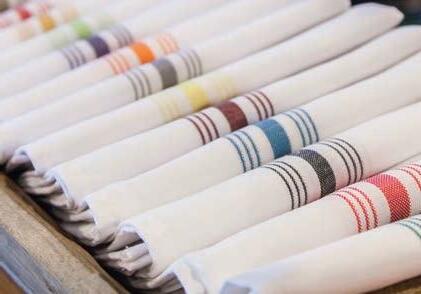
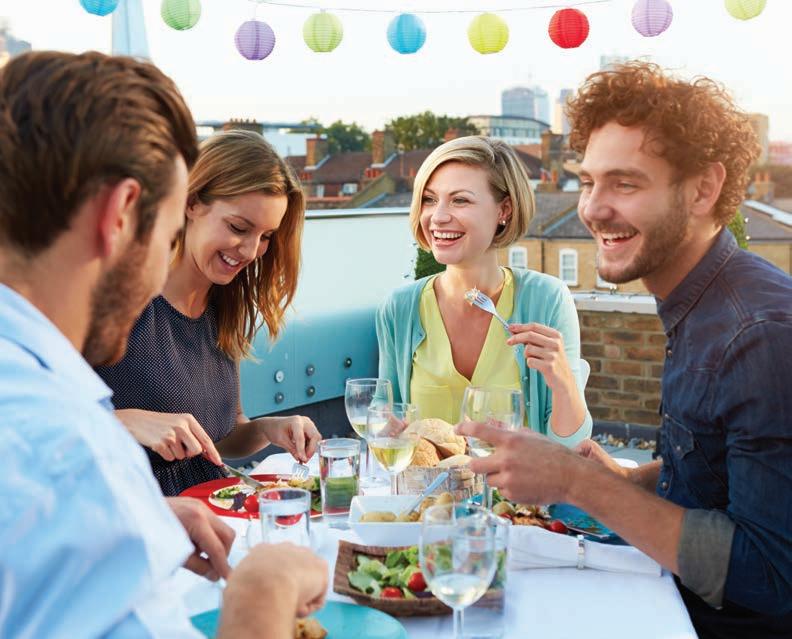
Together, ADI and Milliken have set the standard of linen excellence for decades. USA made Signature Plus fabric. Soft luxurious hand, consistent long-lasting color. Whites that stay white, and colors that stay bright.
ADI American Dawn. The world’s leading supplier of Milliken Signature table linen products. Count on us. Signature Plus is a registered trademark for Milliken & Company for fabrics.

Exhibitors
❏
❏
Washing, finishing and uniform processing systems; conveyor systems; production management software.
❏
Imonex Services Inc. 1566, 1567
Coin acceptors and pay-by-phone systems.
Independent Textile 4564 Rental Association (ITRA) Network of independent textile rental companies that promote informational exchange and education.
❏
❏
❏
Industrial Gold Air 1266 Compressors
Indy Hanger & Supply 4613 Galvanized wire hangers.
Infinite Creative 4003, 4808 Enterprises Inc. Massage chairs.
❏
❏
InnoClean Corp. 4666
Innovative Management 2265 Designs
RFID tracking systems.
❏
Inox Milton 736
❏
Irving Weber Associates 4451 (IWA)
Insurance services for dry cleaners,coin-ops, linen suppliers, commercial launderers and uniform rental.
❏
Isuzu Commercial Truck 1453 of America Trucks.
❏
Italclean Srl 4443 Drycleaning and laundry equipment.
❏
Itsumi USA Inc. 4165 Shirt finishing equipment.
Kemco Systems Co. LLC 2965
Water heaters, heat reclaimers, water recovery/reuse systems and water treatment systems.
❏ Keycolour Inc. 4325 Textile dyeing products.
❏ KioSoft Technologies LLC 4374
❏
Kleen-Rite Inc. 4673 Solvent filter/purifier system.
❏ Kleen-Tex Industries Inc. 4850 Commercial and industrial mats.
❏ Klopp Coin Counters 4924 Coin counters, sorters and wrapper crimpers.
❏ Kreussler Inc. 2357 Laundry, drycleaning and wet-cleaning chemicals and detergents.
❏
finishing tunnels, cart washers, and more.
Lattner Boiler Co. 1300
Fuel-fired and electric boilers for dry cleaning and other industrial applications.
❏
Laundroworks 3673 Card
Systems
Card-based payment, control, and monitoring systems for multi-housing and vended laundries.
❏ Laundry Logic LLC 1267 Computer software and systems for textile rental.
❏ Laundrylux 2642 North American supplier of Electrolux and Wascomat commercial laundry equipment.
❏
LaundryPass 2063 Card payment/ management system for Laundromats.
❏ Laundry-Trak 4414 Linen processing and tracking software.
L❏
Lavatec Laundry 2343 Technology Inc.
❏
Leebaw Manufacturing 3902
Material-handling carts, garment carts, shelving units, lift tables and other products.
❏ Leonard Automatics 2943 Garment finishing, small-piece stacking, cart washing, and pressing equipment.
❏ LG Electronics 720, 721 Commercial washers and dryers.
❏ Linen Tech 1146 Laundry management software for industrial laundry facilities.
❏
Low Cost Mfg. Co. 2360 Parts for commercial washers and dryers.
❏ Mainetti 4768 Garment hangers and garment packaging products.
❏
❏
Mamute Laundry 4464
Marina Textiles Inc. 4468 Institutional linens for hospitality, healthcare, commercial laundries, linen rental, prisons, and other markets.
❏
❏
Maruso USA Inc. 4864 Plastic garment hangers.
Material Flow Systems 1113
Material-handling systems, including rail systems, conveyors and trolleys.
❏ Maxi Companies 4513
❏ M&B Hangers 3811
MWire garment hangers and paper products for drycleaning and textile rental industries.
❏ M+A Matting LLC 4459 Mats.
Export management company specializing in commercial and industrial laundry and drycleaning equipment.
❏ MaxiMizer Systems 3805 Direct fired water heaters, boiler stack economizers, and waste water heat recovery.
❏ Lac-Mac Limited 1365 Reusable surgical gowns and drapes, and other healthcare apparel.
❏
Lapauw USA LLC 1621 Flatwork finishing equipment,washerextractors, garment
Continuous-batch washers, washer-extractors, dryers, flatwork feeders, ironers, folders, stackers, materialhandling equipment, and other equipment.
❏ Lavo Solutions 3672
❏ LCT 4572
❏ Maestrelli Srl 2537 Drycleaning and laundry equipment.
❏ Magid 4402
Personal protective equipment and safety solutions.
❏ Main Street Hub 4111 Social media management services.
❏ Maxi-Press 4601 Elastomeric Inc. Membranes for water extraction presses; additional spare and special parts for other laundry equipment.
❏
Maxon Lift Corp. 1025 Truck and trailer liftgates.
❏ Medline Industries Inc. 1731
CLEAN ’19 EXHIBITORS continue on Page 32
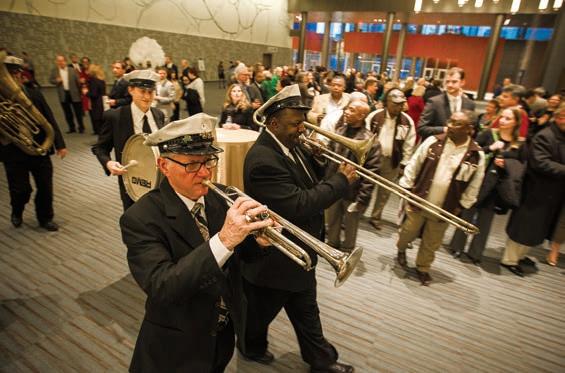
❏
JJENSEN USA Inc. 2621
Washing equipment, finishing systems, material-handling systems, and system software and process technology.
❏
❏
JiangSu Sea-lion 2103 Machinery Group (Corp.)
JLT Co. Ltd. 4372
❏
J.P. Equipment Inc. 1803
Industrial laundry equipment sales.
❏
JS Fiber Co. Inc. 1265 Hospitality and healthcare bedding.
❏
KKaeser Compressors Inc. 1401 Compressed-air equipment.
Exhibitors
Broad spectrum of healthcare textiles and other healthcare products.
❏
Meese 1352
Bulk linen and laundry carts.
❏
Memories Gown 1305
❏
Preservation
Environmentally friendly wholesale gown cleaning, preservation, and pre-paid shipping.
Messe Frankfurt Inc. 1432
Trade fair, congress and event organizer.
❏
Metalprogetti 2008
Automated systems for moving, handling, sorting and dispensing hanging and folded garments.
❏
Mevo Metzler GmbH 3165
Wire hangers, and drycleaning and laundry products.
❏
Micross Automation 1055 Systems
Laundry tracking software and systems.
❏
Midwest Specialty 1112 Products
Disposable towel and wiper products.
❏ Miele Inc. 4121

❏
Laundry care equipment and products.
Milliken & Co. 1520
Fabrics for tablecloths, napkins, placemats, aprons and tableskirts; dust control products; industrial and specialty textiles.
❏
Million Dollar Collar 1402 Placket stays for collared shirts.
❏
MIP Inc. 2503
Reusable healthcare products, including bed linens, underpads, carts, bags, etc.
❏
Miura America Co. Ltd. 4301 Steam, hot water and modular boiler systems.
❏
Mobile Computing 4766 Corp. Inc. (MCC)
Software for linen and textile delivery optimization.
❏
Monarch Brands 1762
Wholesalers and manufacturers of microfiber, commercial linen, institutional towels and wiper rags. ❏
Monarch Coin & Security 1158 Coin/token chutes, money boxes, locks and keys for coin laundry machines; bathroom locks.
❏ Nayax 4710 Cashless payment systems.
NIE Insurance 4514 Insurance services for dry cleaners and coin laundries.
Norchem Corp. 1321 Laundry chemicals; chemical dispensing systems; wastewater treatment and recycling systems; and system controllers and software.
Noritz 4814 Tankless water heaters.
NuMat Systems LLC 1504 Rubber-backed floor mats, and mat repair and remanufacturing service.
Olin Corp. 4448 Chlorinated organics drycleaning solvent.
OMNI Solutions 4501 Laundry chemicals.
Onnera Group 1943, 2309
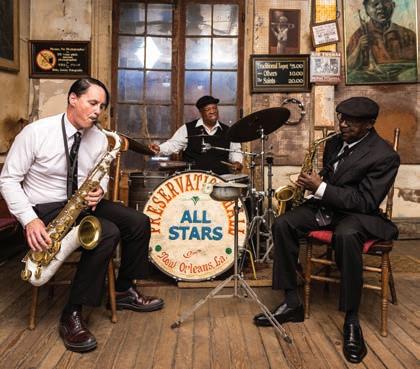
❏ Otto Trading Inc. 1264
❏
Moonsoft International 1165 Microfiber products, cleaning towels, and mop pads and materials. ❏
Morgan & Morgan Olson 1153 Walk-in step vans. ❏
Movexx 4002 Compact push/pull assist to move carts. ❏
Multimatic 4343 Drycleaning machinery.
P❏ PAC Strapping Products 1400 Plastic strapping, steel strapping, strapping machines, strapping tools, and accessories.
❏ Parker Boiler Co. 1031 Steam boilers, indirect-fired water heaters and related equipment.
❏ Paypont 4820
Cashless laundry payment system.
❏ PayRange 929 Mobile payment systems.
Naomoto Corp./Apparel 4824
Machinery & Supply Co. Distributor for Naomoto irons, self-contained vacuum tables, and other finishing equipment; Hoffman pressing equipment; Koenig irons, mini boilers and automatic garment finishers; and Reliant fusing and laminating machines.
National Cleaners 4764 Association Trade association for professional garment/ fabric cleaners and suppliers.
National Combustion 1862 Co. Inc. (NATCO) Water-heating systems.
Navien Inc. 3903 Tankless water heaters and boilers.
❏ paystri 1565 Customized payment solutions.
❏ Pellerin Milnor 2703
Washer-extractors, automated tunnel washing systems, dryers, materialhandling systems, and laundry computer networks.
❏
Penco Products Inc. 4524 Garment lockers, hygiene products and storage products for textile and linen rental.
❏ Penn Emblem Co. 4410
Image and identification products for uniform, garment and apparel industries.
❏
Pepin Mfg. Inc. 4305 Lint rollers.
Workwear and uniforms.
❏
Phoenix Textile Corp. 1049
Terry products, blankets, bedding, uniforms, microfiber, window coverings, cubicle curtains, furnitures, and design services.
❏
Pivot 1156
Point of sale software for dry cleaners and laundries.
❏
Planiform Conveyors Inc. 1131
Garments on hanger automatic sorters and monorail systems for commercial laundries.

❏
❏
Plexus Industries 1063
Commercial laundry bags.
Polypack GmbH & Co. KG 3965
Full automatic bagging machines for hanging garments; single and set packing; bundling systems; labeling systems; conveyor systems.
❏
Pony SpA 3665
Garment finishing and pressing equipment.
❏
Poseidon Textile Care 4557 Systems
Wetcleaning equipment, parts and service.
❏
Positek RFID 2511
RFID-enabled sorting and tracking software and systems for the textile maintenance industry.
❏
Prime Capital Inc. 1758 Independent equipment and specialty finance company.
❏
Pristine Collars 4774
❏
Railex Corp. 4373
Garment and clothing conveyors, handling, and storage systems.
❏
RAMCO Laundry 4401 Machinery Inc.
Commercial and industrial laundry systems.
❏
Rampi S.r.l. 4467 Laundry chemicals and detergents.
❏
RealStar USA 3755
Drycleaning machines.
❏ Reed Mfg. Co. 2405
❏ ReflectiveStripe.com/ 1104 Block Bindings & Interlinings
Custom reflective striping for workwear.
❏
Rema Dri-Vac Corp. 4113
Air vacuum units, boiler feed systems, blow-off separators, boiler feed pumps, storage tanks and condensate systems.
❏
Rennco LLC 1032
Laundry bagging and packaging equipment.
❏
Renzacci SPA 4233
Drycleaning machines, washer-extractors, dryers and wetcleaning machines.
❏
Riegel Linen Co. 1121
Broad range of hospitality, healthcare and institutional linens.
❏
Rochester Midland Corp. 1311 Water management programs.
❏
Rome Conveyors 1663
Conveyors and other material-handling systems.
❏
Rotational Molding Inc. 4566
Linen and laundry trucks; material-handling products; liquid tanks.
❏
Royal Basket Trucks 1963 Basket trucks and specialty laundry carts.
❏
Royal Blue Textiles 1201 Bedding, terry products and patient apparel.
❏
Ryco Conveyors Inc. 1662 Design, sales and installation of materialhandling systems.
CLEAN ’19 EXHIBITORS continue on Page 34
❏
QQuietaire Cooling Inc. 1065
Industrial fans and commercial ventilation equipment.
❏
RR&B Wire Products Inc. 2420
Industrial laundry and linen transportation equipment and products, including carts and trucks.
❏
R.L. Williams Co. 1024
Restroom products for the uniform, linen rental and dust control industries.
❏
R.R. Street & Co. Inc. 4221
Solvents, additives, stain removal agents and filtration products for laundry, wet cleaning and dry cleaning.
❏
R.W. Martin & Sons Inc. 1125
Laundry equipment sales, expertise, parts, and equipment remanufacturing.
❏
❏
SSan-Ai Industries Inc. 4810
Sanitone by Fabritec 4860
Professional drycleaning detergents, wetcleaning soaps and spotting chemicals as well as restoration and shirt laundry products.
❏ Sankosha USA Inc. 3829
Garment-pressing equipment and bagging machines.
❏ SanMar 2303 Apparel and accessories.
❏ SEITZ, The Fresher 4535 Company Inc. Complete line of laundry and drycleaning chemicals.
❏
SEKO Dosing Systems Corp. 4631 Dosing pumps and metering systems.
❏
Select Risk Insurance Inc. 1110 dba Select Programs Insurance, risk management and business consulting services for the textile care industry.
❏ Senso Technics USA 4760 Software for laundry production optimization.
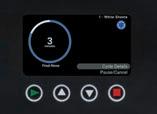
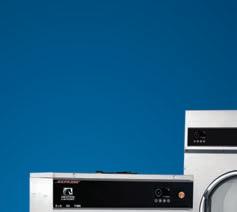
❏ Setomatic Systems - 2409 SpyderWash
Electronic payment acceptance technology, drop coin meters, and other accessories.
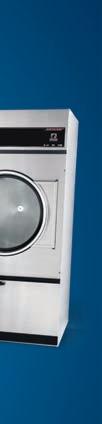
❏
Shanghai Lijing Washing 738
Machinery Mfg. Co. Industrial laundry equipment.
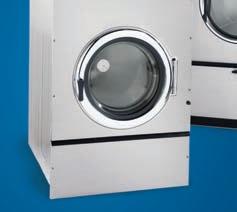
❏
Shanghai Sailstar/ 3155
Everstrong Commercial Sailstar: Washers, dryers, wetcleaning equipment, drycleaning machines, ironers, folders and feeders; Everstrong: Bags, bag stands, carts, trolleys, cart liners/covers and casters.
❏ Shanghai Weishi 3855
Machinery
❏ ShinePay 4800 Digital payment system.
❏ Sigma Garment Films 4404 Garment film and flexible packaging.
❏ Sigmatex-Lanier Textiles 1225 Wide range of textile products for the textile rental, healthcare and hospitality industries.
❏ Sintex 1030 Textile manufacturer for hospitality, commercial laundry, healthcare, and airline industries.
❏
SmartBuy TK 4573 Uniform sales for employee apparel programs.
❏ SMC Corp. of America 4704
❏ SNA Manufacturing LLC 4565
Foam hanger covers and shoulder guards.
❏ Softrol Systems 2855 System controls and management information solutions for the automation of industrial uniform and textile laundry facilities. ❏ SonicAire Inc. 4313 Cleaning and cooling fans for laundries and drycleaning plants. ❏ Spartan Chemical Co. 4011 Laundry detergents and chemicals. ❏
Spector Textile Products 1765 Laundry bags and other textiles. ❏ Spindle 2611 Operations management software for commercial laundries. ❏ SPOT Business Systems 2002 Computer software and systems for drycleaning operations management. ❏
Springboard 2264 Suite of cloud-based tools for laundry pickup/ delivery services. ❏ Springpress 1408 Spring padding, waxes and cleaners for ironers.
SRS Conveyors 1667 Turn-key garment material-handling solutions.
Stahls Hotronix 4400 Heat presses.
Standard 1221 Change-Makers Inc. Currency change machines.
Standard Textile 3364 Healthcare, hospitality and institutional textiles and apparel, and linen management services.
❏
Starchup Inc. 4804
Digital ordering and route management software for dry cleaners and launderers.
❏
Storms Industries Inc. 2261
Flatwork ironer textiles and supplies, cleaners and belting; sling bags; cart covers; filtration and dust-control products.
❏
Streamline Solutions 1462 Recyclable soiled-linen bags, laundry hamper stands, laundry supplies, medical supplies, medical cart covers, disposable cart liners and other products.
❏ Striem 4367
Solids interceptors, oil separators and chemical waste tanks.
❏
Stry-Lenkoff Co. 4406
Stock tags, labels and business forms for the laundry/drycleaning industry.
❏
SUDSY Vending Supplies 1763 Broad range of coin laundry products and supplies.
❏
❏
Sumal 4505
System Laundry 1666 Management Co. Laundry/linen service.
❏
Textile Technologies 4714
Computer software systems for the textile rental industry.
❏
The DECC Co. 1020
Abrasion-resistant release coating for dryer panels.
❏
The Huntington Co. 4553
Franchisor of Martinizing Dry Cleaning and Certified Restoration Drycleaning Network.
❏
TheLaundryList.com Inc. 1043
CLEAN ’19 EXHIBITORS continue on Page 36
❏
TTagitron 925
RFID tracking for the textile industry.
❏
Tap Laundry 1363
Computer software to automate laundry operations.
❏
TBR Associates 1353
Custom-tailored consulting and management coaching services.
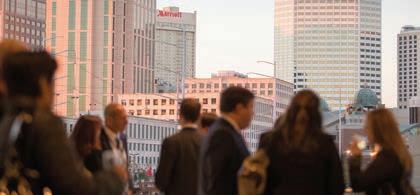
❏
Tecni-Quip Carts 2603 Aluminum, stainless and fiberglass laundry carts.
❏
Texas Automation 4327
Products
Heat-sealing machines and accessories.
❏
Texas Microfiber Inc. 1466
Microfiber and cotton finished textiles, including cloths, mops, linens, cotton terry towels, woven cotton and polyester roll goods, and finished goods.
❏
Textile Care Allied 1543 Trades Association Trade association representing manufacturers and distributors of laundry and drycleaning equipment and supplies.
❏
Used industrial laundry machinery; plant design and installation services; energy efficiency studies.
Thermal Engineering 2161 of Arizona Inc.
Wastewater heat reclaimers, heat-recovery systems, shaker screens, water heaters, storage tanks, pumping systems, ceramic
❏
filtration systems and other products.
Thermopatch 2403
Textile and garment identification products and systems.
❏ Thomaston Mills 1263 Bed and bath linens for the hospitality, healthcare and institutional markets.
❏ Thornell Corp. 4004 Odor elimination products.
❏ Tide Dry Cleaners 4265 Drycleaning business
❏
franchise.
Tingue 1354 Laundry textiles, parts, supplies, remanufactured equipment, and rigging services for industrial laundries.
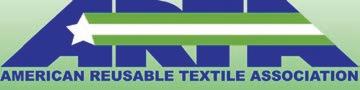
❏
Tolon Global Makina 3355 San. ve. Tic. A.S. Apparel/garments.
❏
Trevil America Inc. 4021 Professional ironing equipment and electric steam generators.
❏ TRSA, the Association for 1533 Linen, Uniform & Facility Services Trade association representing the textile services industry.
and massage chairs.
❏ Union Drycleaning 3143 Products Drycleaning machines.
❏
U.N.X. Incorporated 1143
Commercial laundry chemical products and dispensing systems for domestic and international markets.
❏ U.S. Jaclean Inc. 1655 Personal massagers
U❏ Unipress Corp. 3743 Shirt-finishing machines, and laundry and drycleaning equipment.
❏ UniSec Div. of 3565 New York Machinery Drycleaning machines.
❏
❏
United Soybean Board 4365
United Textile Distribution 4652
Dust control products, table linen, bed linen, towels, hangers, aprons and other products.
❏
United Wire Hanger Corp./1736 UWH Industries
Wire and plastic hangers and related paper products for the uniform rental, drycleaning and apparel industries.
❏
Unitex International Inc. 4101 Distributor of cotton, microfiber and spun table linen textiles.
❏
Utilimaster 1755 Walk-in vans, parcel delivery vans and truck bodies.
❏ Valmet 1410
❏
❏
Vega Systems USA 2142
VEIT 3865
Garment finishing equipment and related systems.
❏
Vend-Rite Mfg. Co. Inc. 1921 Soap venders, bag venders, snack/drink venders, coin laundry signs, plastic laundry bags and drop-off bags.
❏ Vending.com 4212 Snack, beverage, cold food, frozen food and non-food merchandisers. ❏
Venus Group 1509 Tablecloths, napkins, aprons, sheets, towels, hospital linens and chef apparel.
VF Workwear 4525 Workwear.
Vintex Inc. 1130 Launderable barrier fabrics.
Vita Microfiber 732 International LLC Microfiber mops and cloths, wet mops, dry mops, and related products.
Voltea 1109 Water/wastewater
treatment.
❏
Wasatch Co. 4661
Textile products for hospitality, food service and healthcare industries.
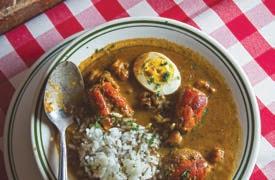
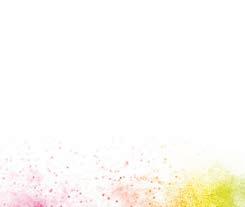

❏
Wash-Dry-Fold POS 2165 Point-of-sale system for Laundromats.
❏
Washin Jax 4256 Agitation system designed to reduce laundry detergent usage while boosting cleaning.
❏
Webb & Son Sewing 2364 Machine Sales Inc. Sewing machines and after-market products and services for the sewing industry.
❏ Wedding Gown 4550 Preservation Co. Gown preservation services.
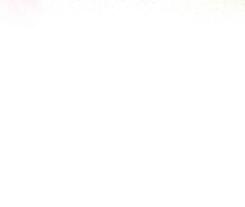
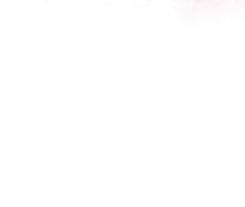
❏ Wesvic Systems 4667

Automated counting and real-time performance feedback system.
❏
wh Münzprüfer Dietmar 1657 Trenner GmbH Cashless payment systems.
❏
Whirlpool Corp. 3602 Commercial washers, dryers and specialty products under the ADC, Maytag® Commercial Laundry and Whirlpool® Commercial Laundry brands.
❏
White Conveyors Inc. 1501 Automated garmentsorting, storage and distribution systems.
❏
❏
Williamson-Dickie Mfg. 4916 Workwear.
Winona Services 4922 Towel and tissue products for textile rental companies, plus related training and marketing services.
❏
❏
❏
WonderWink 1500 Healthcare apparel.
Woodbine Products Co. 1067 Hand-care products.
World Trading Co. Inc. 4773 Textiles for the hospitality, institutional, healthcare and home markets.
❏
WSI 1553 Wash-aisle chemistry, wastewater treatment, specialty chemicals, dispensing technology, and information systems.
W❏ YAC Japan 4065
YLaundry and drycleaning equipment.
❏ Yamada 1132 Air-operated diaphragm pumps.
❏ Yamamoto 2556, 3765 Japan Inc. Washer-extractors, combination washer/ extractor/dryers, and small-piece folders.
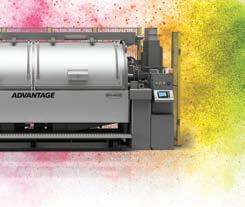
Textiles

Beyond the floor—Educational sessions in New Orleans
Thirty class sessions offered across four days at busy Clean 2019 in Ernest N. Morial Convention Center
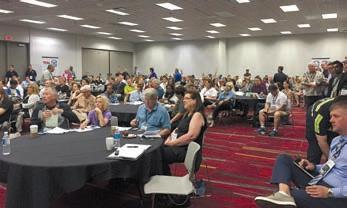
NEW ORLEANS — Thirty hours of educational sessions—all included as part of Clean Show registration—will be spread across the fabricare event’s four days at the Ernest N. Morial Convention Center, June 20-23, in New Orleans.
Joe Ricci, Clean ’19 executive committee chairman and president of TRSA, the association for linen, uniform and facility services, says this about class sessions over the four days of the Clean Show: “While the Clean Show is definitely about the products and services on the floor, the sponsoring associations, both collectively and individually, create educational content and networking opportunities that enhance the value of the event.”
The 30 educational sessions run across four days of Clean ’19. They offer industry perspectives, idea-sharing, and a chance to hear new voices, as Ricci explains: “Dry cleaning, vended laundry and linen and uniform services professionals that attend the Clean Show benefit from time away from operational and customer demands to focus on strategic investments and innovations.”
Note that these educational opportunities begin Thursday morning, on the first day of the show, and there are also general sessions Thursday through Saturday afternoons at Clean ’19, with the sessions wrapping up Sunday morning, the last day of the show.
Mary Scalco, CEO of Drycleaning and Laundry Institute (DLI), adds, “This year there are more educational opportunities and events on the show floor than ever before. And for the first time, Clean Show sponsors have joined forces to bring top notch speakers to provide more businessfocused education.”
THURSDAY, JUNE 20
• 8 a.m. to 8:55 a.m. Room: 238-239 — Customer Migration, sponsored by Association for Linen Management (ALM).
Transparent usage data and a solid plan is critical to a smooth transition from one textile services provider to another. What happens when the exiting textile services provider is not forthcoming with data? How do you handle surprises that have a significant impact on the terms of the agreement?
• 8:30 a.m. to 9:30 a.m. Room: 255-257 —
Protecting Your Customer, Employee and Business Assets Through New and Improved Contracts, sponsored by Textile Rental Services Association of America (TRSA).
Join attorney Scott Kamins to get a review of the most updated law, contract terms, developments and strategies when it comes to drafting, enforcing and defending contracts with customers, employees, vendors and others.
• 8:30 a.m. to 9:30 a.m. Room: 243-245
— No Bad Days: Positive Attitude Is Everything, sponsored by Drycleaning & Laundry Institute (DLI).
If you allow yourself to have a bad day, you LOSE! NO BAD DAYS is a philosophy and mindset. Learn how to set your attitude up for success by rolling with the punches and finding opportunities where others see obstacles.
• 8:30 a.m. to 9:30 a.m. Room: R6-R9 —
Laundries Connecting Communities, sponsored by Coin Laundry Association (CLA).
This important opening session will feature the initiatives of the LaundryCares Foundation which aim to provide early childhood development and literacy support to the families who support our businesses.
Learn how to connect with your community to benefit those families—and the profitability of your laundromat.
• 9 a.m. to 10 a.m. Room: 238-239 —
Preventing Microbial Growth and Infection in Laundry Facilities, sponsored by ALM.
Improve the overall cleanliness of your laundry by identifying and blocking key avenues of microbial contamination using applied microbiology techniques and an HACCP assessment of the environment.
Learn about the proper management of airflow, pressure differentials between spaces, temperature control, surface cleanliness, and lint and dust control.
• 2 p.m. to 3 p.m. Exhibit Hall — Social Media Marketing and Measurement. General Session.
• 3:30 p.m. to 4:30 p.m. Exhibit Hall
— Workplace Risks of Legalized Marijuana? General Session.
Whether for medicinal or recreational purposes, legalized marijuana use creates new concerns for employers. Questions are plentiful when it comes to assessing impairment, the ADA, workers’ compensation, and drug testing. Find out what rights you retain as well as where your responsibilities lie with keeping your operation safe and your performance high.
FRIDAY, JUNE 21
• 8 a.m. to 8:55 a.m. Room: 238-239 —
Are You a Trusted Advisor? New Role of Sales, sponsored by ALM.
Customers are becoming more savvy, which means sales professionals must “up their game” to build credibility and relationships. Listen first and discover textile care customer needs and weaknesses, then show them how you will deliver solutions and improve their operations for years to come.
• 8 a.m. to 9 a.m. Room: R6-R9 — Laundromat Lifecycles: Planning for the Future, sponsored by CLA.
Like every small business, laundromats must navigate the lifecycle of the business successfully to ensure long-term success. Understanding the key considerations of that cycle will be the focus of this session which will explore equipment replacement, lease negotiation and planning—as well as tracking the present-value of the business. Make sure that you are maximizing your success throughout the lifespan of your laundromat investment.
• 8 a.m. to 9 a.m. Room: 255-257 — Venture Capital and Private Equity, sponsored by TRSA.
Discuss pros and cons of debt versus equity financing and evaluate the various financing vehicles. Decide if potential growth is substantial enough to merit an effort to seek sufficient capital.
• 8 a.m. to 9 a.m. Room: 243-245 — What First Impression Does Your Website Make? Sponsored by DLI.
Does your website provide the same amazing experience people get when they walk in to your store? Can they find answers to their questions? Can they request or receive services after hours? Hear how to improve your website’s performance and impress your customers even when you are not around.
• 9 a.m. to 10 a.m. Room: 243-245 — Are Your Marketing Methods Changing with Your Clientele? Sponsored by DLI.
Hear how a successful cleaner has evolved his marketing techniques to attract the growing new wave of consumers. The reality is your customers are changing whether you are or not. So now is the time to future-proof your customer base.
• 9 a.m. to 10 a.m. Room: 342 — ARTA Study Shows Peracetic Acid Kills C.diff Spores, sponsored by the American Reusable Textile Association (ARTA).
The American Reusable Textile Association (ARTA) will present the results of a study designed to determine whether the laundry process using a tunnel washer will adequately kill C.diff spores. One of ARTA’s researchers will share results from the study using Peracetic Acid and answer questions from the audience.
9 a.m. to 10 a.m. Room: R6-R9 —
CLA Connect LIVE: Interactive Idea Exchange, sponsored by CLA.
Building on the popularity of the association’s online forum, this session will bring
those valuable interactions to life in this interactive session. Come meet some of your favorite online contributors in a live setting while gathering the tips and tricks of the trade to propel your laundromat business forward. Make sure your visit to New Orleans pays off by networking with your most successful peers.
• 9 a.m. to 10 a.m. Room: 255-257 — Labor Law and Compliance: Current Issues and Trends, sponsored by TRSA. Hear about the newest trends in employment law to watch for in 2019 and how you can help ensure your organization adheres to current and future changes. Get solutions to the latest HR and OSHA regulatory and compliance issues.
• 9 a.m. to 10 a.m. Room: 238-239 — New Textile Technologies for Infection Prevention, sponsored by ALM.
An increasing number of studies show that healthcare-associated infection rates may be improved by adding antimicrobial textiles to hospital infection prevention efforts. We’ll review and discuss the range of available antimicrobial products and technologies, discuss evaluation criteria, and the impact of any process changes on hospitals and laundries.
• 2 p.m. to 3 p.m. Exhibit Hall — Helpful Business Apps – Beth Z – Your Nerdy Best Friend. General Session.
• 3:30 p.m. to 4:30 p.m. Exhibit Hall — Secrets to Chick-fil-A Hiring & Training for Exceptional Customer Service. General Session.
SATURDAY, JUNE 22
• 8 a.m. to 9 a.m. Room: 243-245 — Customer Service: Being Good is Not Enough, sponsored by DLI.
Customers expect the finest service and today’s market offers them plenty of choices for their clothing service needs. Wow them with service above and beyond their expectations to keep customers coming back for years to come.
• 8 a.m. to 9 a.m. Room: 255-257 — TRSA
Certification: Hygienically Clean, Clean Green, Certified Professional Laundry Manager (CPLM), sponsored by TRSA. Build customer confidence and offer your company a competitive advantage with TRSA’s Clean Green and Hygienically Clean Certification programs. Learn how your company can meet these rigorous standards and quantifiable measurements including inspections and testing. Speakers will also share info on earning TRSA’s Certified Professional Laundry Manager (CPLM) designation.
• 8 a.m. to 9 a.m. Room: R6-R9 — WashDry-Fold 2.0: What’s Next for FullService Laundry? sponsored by CLA.
The incredible consumer interest in “outsourcing” the weekly laundry chore is changing the way our business works—and will continue to disrupt the model into the foreseeable future. This session will feature the leading innovators in the space talking about what we should expect next with washdry-fold and commercial accounts with an emphasis on the processes and technologies to which you must adapt in the immediate future.
• 8:30 a.m. to 9:30 a.m. Room: 238239 — Consistent Benchmarks for Competitive Analysis, sponsored by ALM.
If you don’t keep track of where you’ve been, where you are, and how you stack up, how will you get to where you want to be? Participation in sound benchmarking initiatives provides a roadmap to operational success. Learn how solid, compatible data can lead to improved efficiencies and superior quality.
• 9 a.m. to 10 a.m. Room: R6-R9 — Due Diligence: Preparing to Buy (or Sell) Your Next Laundromat, sponsored by CLA.
Buying (or selling) a small business is a complex and challenging endeavor that nearly every laundromat owner will encounter at some point in their laundry career. Begin the important preparation process for your next acquisition (or opportunity to sell) with this session focused on both what you can do to make your business more valuable to an educated buyer—and how to get the best price when you’re ready to add your next location.
• 9 a.m. to 10 a.m. Room: 342 — LCA Data and How to Use LCAs to Help Convert Client to Reusables, sponsored by ARTA.
A panel of operators and a researcher from Environmental Clarity will share the newest LCA data on incontinence pads and tangible examples of how to use LCA data to convert clients to reusable textile items.
ARTA has completed and published three peer-reviewed LCAs to date on: surgical
gowns (AORN), isolation gowns (APIC), and cleanroom coveralls (IEST).
• 9 a.m. to 10 a.m. Room: 243-245 —
Tips for Entering the Wash Dry Fold Market, sponsored by DLI.
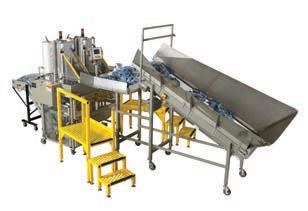
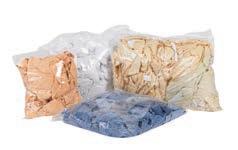
In today’s economy, drycleaning isn’t enough. Customers expect you to offer a full spectrum of services. Diversification into wash-dry-fold is a natural fit for dry cleaners. Hear how one expert is running a booming business in this expanding service. Wash, Dry, Fold and Succeed!
• 9 a.m. to 10 a.m. Room: 255-257 — Top OSHA Violations and New TRSA Safety Certification Program, sponsored by TRSA.
Learn about the most common OSHA
workplace safety violations and how to avoid them. Get details on TRSA’s newest certification to gain recognition for your company’s Safety and Health programs and enhance your company as an employer and as a service provider.
• 1 p.m. to 2 p.m. Exhibit Hall — Tips for Entering the Commercial Laundry Industry. General Session.
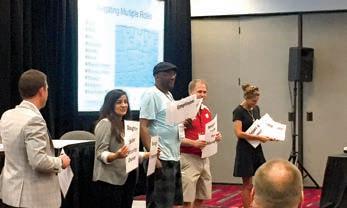
There are pros, but also cons that come along with tackling a market you’re unfamiliar with. Hear from industry experts on the best place to start if you’re interested in entering the linen, uniform and facility services industry to determine if it’s the right move for you.
• 3:30 p.m. to 4:30 p.m. Exhibit Hall
— #NotHere: Sexual Harassment
Prevention. General Session.
Given the heightened awareness of unwelcome sexual conduct, give your policies a check-up and ensure current concerns are addressed such as fear of reporting by migrant workers, cultural differences in acceptable behavior, how to respond to claims, and more.
SUNDAY, JUNE 23
• 8 a.m. to 9 a.m. Room: R6-R9 — Introduction to Laundromats for Investors, sponsored by CLA.
For those interested in becoming firsttime laundromat owners, don’t miss this session that will walk you through the basics of owning a laundry. Tap into the association’s decades of experience to learn whether laundromat ownership is a good opportunity for you.
• 9 a.m. to 10 a.m. Room: R6-R9 —
Top 10 Secrets First-Time Laundromat Owners Must Know, sponsored by CLA.

Why reinvent the wheel? Start your journey into laundromat ownership armed with the keys to success. Learn from those who’ve gone before you and are willing to share their mistakes and lessons learned. Knowing these secrets will cut your learning curve down to size and help you get started on the right path to profitability. ALN
Tim Burke is editor of American Laundry News’ sister publication American Drycleaner
Laundromat owner develops commercial laundry from scratch
BY HALEY JORGENSENSAN DIEGO — Vended laundry owner gone commercial, Brian Voytovich recently completed the first phase of his newest endeavor—the development of 36,000-square-foot Revolve, a new commercial laundry in San Diego.
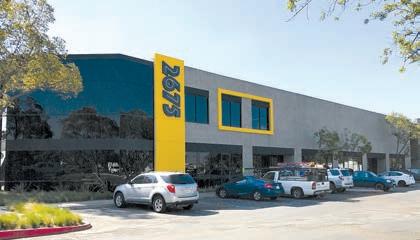
Featuring Girbau Industrial equipment and catering to the hospitality industry, the builtfrom-scratch operation churns out 35-45,000 pounds of customer owned goods (COG) per day. And, it’s just a year in.
During phases two and three, a tunnel system and third ironing line will be added in order to reach a potential throughput of 100,000 laundry pounds per day. All of this is to serve a need.
IT STARTED WITH AN INKLING ABOUT HOTELS
Voytovich morphed from vended laundry owner to commercial laundry owner as a result of an inkling, which spurred him to action, which unveiled a market need. Previously, his laundromats frequently processed overflow hotel laundry. It seemed there was ample hospitality laundry to go around.
Voytovich explored his idea.
“I walked into 20 hotels and did a sample study on who outsourced and if they liked the companies they used,” he says. “I discovered 13 of the 20 outsourced and all were dissatisfied with the service and/or quality received.”
PLANNING & DEVELOPMENT
All in, he sold his Laundromats and secured a facility 100 yards from the U.S.-Mexico border. During the 14-month development process, Voytovich worked closely with Girbau Industrial National Sales Manager Seth Willer, who he credits with designing the laundry’s layout and equipment mix.
“Seth developed profit-andloss and forecasting spread sheets, the laundry layout and flow, and determined our expectations for laundry poundage,” says Voytovich. “He was a huge contributor.”
“Brian basically started the laundry from scratch, which doesn’t happen too often,” Willer shares. “He came to us asking what he needed for equipment. He gave us a space and we designed the laundry to be flexible in order to handle a variety of items and customer types. The idea was to start small and bring in additional automation in later phases.”
“At the time, I didn’t even know
what ironers or tunnels were,” admits Voytovich. “I was familiar with GI through experience with Continental laundry equipment on the vended side. The machines are well built with high-extract speeds for more production and longer linen life.”
ECO-FRIENDLY, FLEXIBLE EQUIPMENT MIX
Revolve, which became operational in January 2018, is equipped with a combination of equipment and systems that make it highly efficient, flexible and eco-friendly. The wash line is comprised of six 255-pound and six 130-pound, high-speed GI washers and matching moisturesensing and reversing dryers.
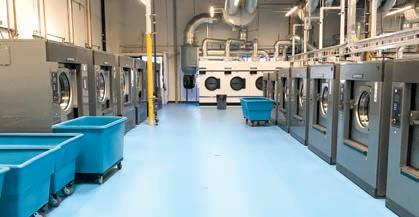
Voytovich chose the washers for their programmability, soft-mount design and high extract speeds. The soft-mount design simplified installation since no bolts or grout were required. And, because the washers generate extract speeds up to 387 G-force, they remove more water per load, cut resulting dry time and lower gas consumption.
They’re also highly flexible in terms of programmability, allowing Revolve to properly clean a wide variety of items and soil levels, according to Voytovich.
“Every hotel is different, so we fine-tune our wash programs to fit them,” he says.
Finally, the washers seamlessly interface with the plant’s Voltea capacitive deionization system.
“Eighty percent of the water is recycled in the laundry and it is twice as clean as tap water,” says Voytovich. “We were the first laundry in the area permitted for water recycling and are among the greenest laundries in North America.”
On the dryer side, a thermal heat recapture system works to minimize gas usage, while moisture sensing eliminates over drying and fabric damage. Altogether, 45% of the thermal exhaust used by Revolve is recycled and nearly 40% of its electricity is generated via solar power.
IRONING & FOLDING MACHINE AUTOMATION
By adding machine automation, Revolve also ensures high-quality results, greater production and reduced labor hours. To expedite the folding process, dried towels and blankets are fed through one of two GI FT-Maxi towel folders, where they are automatically classified, folded and stacked at a rate of 900 pieces per hour.
Meanwhile, damp sheets,
duvets, table linens and pillowcases go straight from the open-pocket washers through a Chicago picker and sorter into one of two finishing lines. Items that demand a highquality finish, like duvets and table linens, run through the GI finishing line, whereas sheets are typically processed by a JENSEN three-roll ironer with cornerless feeder.
The GI ironing line includes a DRF three-station spreader/ feeder, which automatically straightens and feeds linens into a corresponding PC-120 natural gas, heated-chest ironer. The feeder features a vacuum box and feeding table for best-quality feeding and operates with up to three operators.
The GI PC-120 Ironer has two
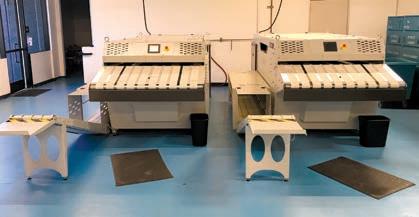
48-inch diameter rolls, operates at up to 93% efficiency and processes items at speeds of up to 164 feet per minute.
Finally, flat goods automatically move from the ironer through an FRB Flatwork Folder. Offering an advanced control and multiprogram operation, the folder performs one or two primary folds
on one, two or four lanes. This results in consistent stacks that are easy to transport and inventory, according to Voytovich.
CLOUD-BASED MANAGEMENT SYSTEM
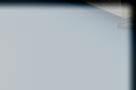
Pulling it all together—from inventory tracking to customer management—is Revolve’s LinenTech Commercial Laundry Management Software.
“We love it and so do our customers,” says Voytovich. “It tracks items by customer as they
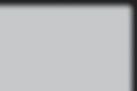

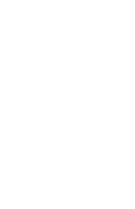

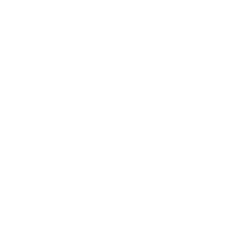
come in the door, move through the laundry and are delivered back to the customer. Customers can log into our web portal to view and pay invoices, view and modify orders, and access the status of orders processing and shipping.”
All laundry systems are hightech by design, ensuring customer goods are never intermingled and inventory is accounted for.
Delivery drivers use tablets and wireless scanners to track goods by customer. Laundry is placed
in color-coded carts by customer and weighed. A computer terminal hooked up to the scale automatically uploads the data into the LinenTech cloud, where it is tracked through the wash and delivery processes.
Thus far, Revolve employs 108 team members while running 2 1/2 eight-hour production shifts.
“This month we hit a million pounds processed,” says Voytovich. Come fall, throughput is expected
to explode with the completion of phase two and the addition of a 13-module tunnel washer.

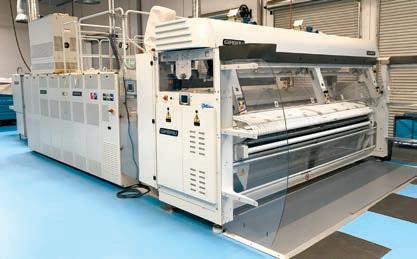
“Our team is fantastic and we are happy with our progress so far,” he says. “We look forward to serving the Southern California market for many years to come.”
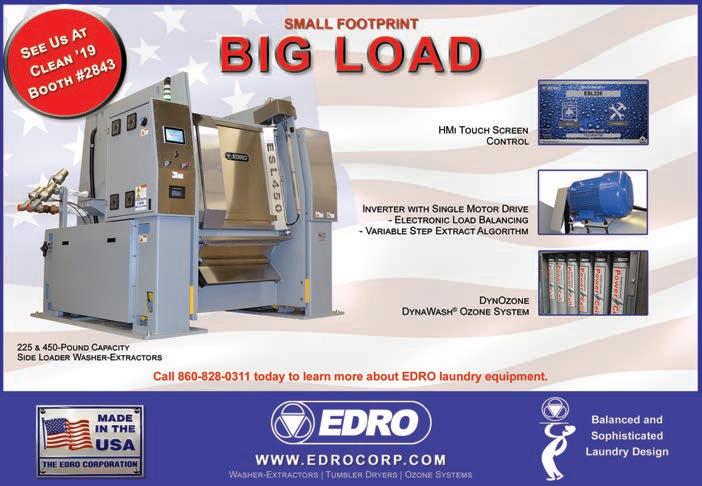
Lapauw USA appoints Marquette president


PARK CITY, Utah — Lapauw USA reports that J.B. Marquette has been named vice president of the company and that he will become president of Lapauw USA effective June 1.
Marquette will succeed David Bernstein, who resigns as president of the company effective May 31, so that he may pursue his desire to return to industry consulting and the formation of a new consulting firm.
“We are all thankful for David’s years of service and leadership and are grateful for his many accomplishments,” says Steven Renders, CEO of Lapauw International, the parent company of Lapauw USA. “Although he will be missed, we understand and support David’s decision to step down and to start his new business. We wish him tremendous success and look forward to working with him as a trusted consultant to the industry.”
Bernstein’s new consulting firm, Propeller Solutions Group LLC, offers services primarily to the laundry industry. He is returning to consulting after a five-year





hiatus during which he established and led Lapauw USA. The new firm will begin offering services immediately.


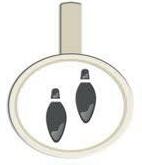
“It has been an honor and a privi lege to work closely with Steven to start, grow and lead Lapauw USA,” Bernstein says. “I appreciate the opportunity and the trust he and Philippe D’heygere (president of Lapauw International) placed in me, and I am proud to have worked with so many wonderful customers, and with our global colleagues, each of whom are committed to excellence in laundry solutions.
“I have tremendous respect and admiration for J.B., and I will be leaving with the knowledge that the company is being led by the right person, has a committed and determined team, and is wellpositioned for enormous success in the market.”
Marquette joined Lapauw USA as regional sales director, but he is known throughout the industry as an accomplished professional with more than 20
years of management, operations, customer service and sales experience. His background as a laundry manager has already proven to be appreciated and respected by Lapauw’s customers and will offer a unique perspective and experience that few in such a position can match, the company says.
“I am honored to have been selected by Steven and Philippe to lead Lapauw USA,” he says. “I appreciate the opportunity to contribute to the success of such a dynamic international organization and laundry industry pioneer.
“I also want to wish David much success as he launches his new endeavor. He has done a tremendous job leading Lapauw USA over the last 5 years, and I look forward to building on the foundation he has created.”
“J.B. has built an impressive industry track record over the past 20-plus years in management, operations and in sales, and we are convinced that he has the skills, talents and experience to lead Lapauw USA for many years to come,” says Renders.
“When J.B. came on board, we knew he would make great contributions to Lapauw’s reputation, market share and long-term success. We are extremely fortunate to have had the perfect candidate inhouse to ensure a smooth transition.”
EDRO announces changes to management structure with new team
EAST BERLIN, Conn. — Laundry equipment manufacturer EDRO Corp. reports that it has a new management team in place.
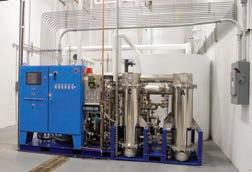

The company’s board of directors say that President Edward Kirejczyk and Caroline Wojcicki, vice president, finance, are no longer with the company. The board says EDRO thanks them for many years of service and wishes them all the best in future endeavors.
In order to ensure continuity moving forward, the company says Joseph Futcher has been appointed as chief executive officer to lead the new management team. His aim is to build a strong foundation for future growth, including refocusing the company brand, evolving its products and marketing, improving its operations, and reducing costs.
The company says Scott Kirejczyk remains as EDRO’s vice president of operations.

He is joined by Ken Bridges, customer service manager, and

Robert Yorski, chief engineer. All three are long-standing EDRO employees.
The new management team is committed to moving EDRO and its iconic brand into an exciting new era, the company says.
Rees retiring from Loomis Bros. Equipment Co.
FENTON, Mo. — Carl Rees, a long-time employee of Loomis Bros. Equipment Co., says he is retiring May 1, 2019.
“Joining our company in 1980, Carl has worked with Loomis Brothers for 39 years—longer than any other employee in our company’s 70-year history,” says Dale Loomis, chairman and CEO of Loomis Bros. “Carl began his career installing machines and working with our service department.”
A few years later, Rees started working in Loomis’s sales department, where he was trained and mentored by his father, Jack Rees. Loomis says the experience proved to be invaluable when Rees started working his own sales territory.
After a long run as a territory sales rep, Rees accepted promotions to several management positions, including sales manager, vice president of sales, and most recently vice president of strategic accounts.
“Carl has been recognized as being one of the premier dealer sales professionals in


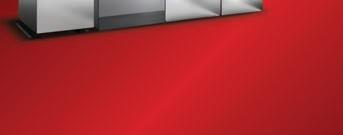
the Milnor/Chicago dealer network,” shares Loomis. “He is the recipient of numerous sales achievement awards from Pellerin Milnor, Chicago Dryer and other leading manufacturers. In particular, Carl has won Milnor’s coveted ‘Key Man’ award for a record 11 times.”
“While the decision to retire from doing something I truly enjoy and from an industry that has given so much to me and my family is a difficult one, my wife Lisa and I are looking forward to more time together with our kids and grandkids,” says Rees.
“I’ve been fortunate to work for an established and respected company like Loomis Bros., and I will truly miss my coworkers and all the close personal friendships I have made over the years with my vendors and customers.”
Huene joins Gurtler as technical services manager

SOUTH HOLLAND, Ill. — Gurtler Industries Inc., a manufacturer of advanced detergents and specialty chemicals for the commercial laundry industry, added Gregory Huene to its team in January.
The company says Huene will be serving in the role of technical services manager. He brings with him 20-plus years of experience in the laundry industry.
Special hot water system needs? Hamilton has the answer…
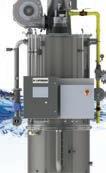
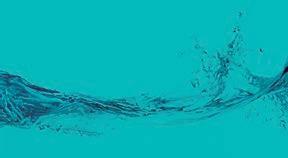
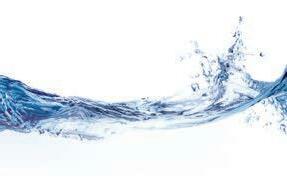
From steam and/or condensate return heated hot water packages, to our direct contact SOLSTREAM™ gas fired systems, we have the products that fit your system design and budget needs. For over 35 years, Hamilton has been providing the proper hot water solution to all facets of the commercial laundry markets.
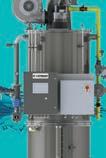
Norchem Corp. appoints Mitchell V.P. of national sales/customer care
LOS ANGELES — Bill Mitchell has been appointed vice president of national sales and customer care of Norchem Corp., a company that provides chemicals, water purification, recycling programs and more offerings to the commercial laundry industry.
Norchem says Mitchell brings 25 years of multi-faceted industry experience with a
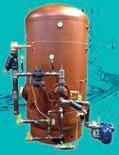


Frederick
but I believe it is not emphasizing our strengths that result in higher turnover.
The laundry industry, like the car rental industry, has a predictable weekly cycle. This allows the employees to gain a weekly sense of accomplishment. The laundry industry, like the car rental industry, provides an opportunity for enjoyable teamwork and pride in group accomplishment. Each employee has production goals and can individually track their progress and know they are contributing to the whole.
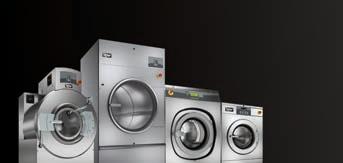
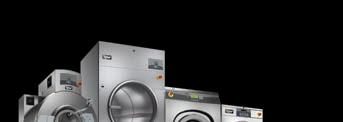
Reducing turnover is dependent on teaching employees to understand what is expected of them, the best production techniques, making them feel a part of
successful track record in product development, market growth strategy, technical service and executive management.
The industry veterain joins Leo Gastelum, who was recently promoted to technical director of customer care, in leading the company’s mentorship and onboarding programs for new customer care technicians nationwide.
ALN
the whole and having a trusted trainer to answer their questions along the way. A trainer can explain the weekly cycle of the laundry business and tell the employee how to realize that the team is meeting their goal.
Failure to properly on board a new employee will result in more frequent turnover and quantity and quality problems for the business.
ALN
Eric Frederick served 44 years in laundry management before retiring and remains active in the industry as a laundry operations consultant. You can contact him by e-mail at elfrederick@cox.net, or by phone at 540-520-6288.

RICHMOND, Ky. — “Is your plant tour ready?”
That’s a vital question if a laundry facility is going to be visited for sales purposes, for the benefit of infection control/preventionist (ICIP) or current customers, for the education of other laundries, or for some type of accreditation.



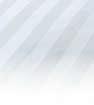




The question was also the title of a webinar presented by the Association for Linen Management (ALM) where Jason Hartsell, director of operations, United Hospital Services in Indianapolis, a cooperative healthcare laundry, offered hints and advice to give the best tour possible.


PREPARING FOR A TOUR
Preparation, in Hartsell’s opinion, is key for a tour.
When a tour is scheduled, it’s important that the person scheduling the tour notify all the parties involved as far out as possible so they can get it on their calendars, and prepare. Also, identify who will be giving the tour and who will be on the tour, what level they are in the organization, and what the goal of the tour is.
“It’s also helpful if you can combine tours,” adds Hartsell. “In our situation here, we will often combine an infection control tour with another infection control tour. That can be beneficial for you as a company because you don’t have to worry about giving two sepa-
rate tours, but it’s also beneficial because a lot of the ICs or IPs network.”

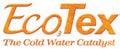
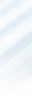
However, he cautions against combining sales tours with two different companies that may be looking to come on board as a customer.
The next phase of preparing for the tour is maintenance prep, says Hartsell. Conduct blow downs, wipe down equipment, fix any leaks or drips, and clean and organize the plant to get it looking good before the tour starts.
Then, he says a laundry should prepare for the customer service aspect of the tour.
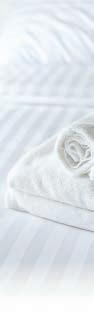
“Here at UHS we like to prepare a little hosting function for the tour with coffee and doughnuts if it’s a morning tour, maybe lunch if it’s an afternoon tour,” he says. “The cost is pretty minimal, and it makes you a good host. It also gives you time after the tour to talk when questions and answers are going on.”
It’s key to do background work and make sure the tour guide understands the group dynamics.
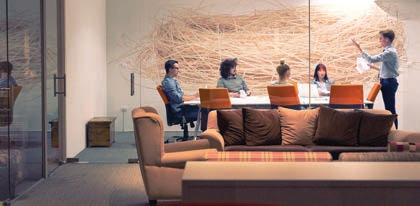
“For example, if you’re looking at selling a new hospital and you have somebody in the C-suite, or you have infection control along on the tour, it’s important to know who’s on this so you can gear your tour toward the right individual,” shares Hartsell.
And make sure that those coming for the tour know special requirements for the plant, such as

no open-toed shoes.
Of course, the production department needs to be prepared for the tour so that each department is functioning well when the guests are there.
“It’s also potentially helpful to reschedule breaks so the tour does not take place in an empty department,” adds Hartsell. “We’ve had it before when we’re going on the tour, we get to soil sort and soil sort is a ghost town. There’s not one person in soil sort because they are on break.
“That kind of makes the tour go cattywampus and we have to swing back around to soil sort. It just doesn’t have that nice of flow if we would have pushed the break back 15 minutes.”
The supervisor of the area that the tour is in should be there to answer any questions and concerns, be there to receive the tour
guides and correct any issues they notice beforehand. Also, the production staff should know where the tour is going and what equipment will be pointed out.
“I find this very helpful to let, for example I have four large-piece ironers, and I always pick a certain ironer that I take the tour group through, so I will let the team know that’s working on, say, ironer three, a tour will be coming in today, that way they know and it won’t take them by surprise when I show up at their machine, pointing things out or demonstrating something,” Hartsell shares.
The day before and the day of the tour, Hartsell says several actions should take place. The tour coordinator needs to confirm with the tour group that the tour is still scheduled, that nothing unexpected came up for the group, and he or she should make sure the
hosting items are in place.
“For example, you don’t want to tell the potential customer that you’ll be serving lunch and you forget to get the lunch and you look kind of like a fool because they didn’t eat lunch,” he points out. “Now they’re upset about you and they take their business elsewhere because of something as simple as giving them sandwiches.”
The tour coordinator should also send reminder messages to production that the tour will be arriving.

“It never hurts to remind production that a tour is arriving because they’ve got 50,000 things they’re working on; it’s not at the front of their minds,” Hartsell says. “When the tour group begins arriving, let production know the tour is here, in the conference room, we’ll be out there in 10

minutes.”



CONDUCTING THE TOUR
After all of the planning, the day of a tour Hartsell recommends several things take place to ensure it goes as smoothly as possible. Before arrival, the tour guide should walk the floor and look for anything that needs to be corrected, such as linen out of place, wet spots on the floor, equipment issues, etc.
“That way you can make any corrections or be prepared to have a potential or current customer ask why the piece of equipment is not working,” he shares.

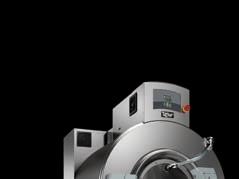
When the guests start arriving, Hartsell finds it’s helpful to move them into an area other than the lobby, like a conference room, with refreshments, since it can be 10 to 15 minutes between the first and last arrival. During this time, hand out business cards and radio the plant that the tour will be beginning soon.
“In my opinion, the first part of the tour is actually still in that conference room you’re assembled in,” he says. “We go into a little pre-tour spiel. Introductions, who we are, what we do. We give a history of our operation, talk about the plant, how many square foot, the equipment, number of employees, operational hours, that type of thing.”
Hartsell recommends that if the tour has a questionnaire, this is the time for them to ask, instead of in the noisy plant.
“As a tour guide, it may tell you things that they may be looking for during the tour, so that if you need to point out a certain piece of equipment or process, you know beforehand,” he adds.
During this time, Hartsell says the point person should be walking the floor, letting the first area or two know the tour’s going to be coming soon.
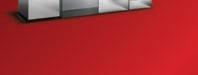
Finally, before leaving the conference room, he suggests giving a safety briefing to the tour group. The next step is the tour.
“We like to follow a set path on the tour,” shares Hartsell. “It kind of follows the flow of linen throughout the plant. Every plant is different, but it makes sense to follow the flow of linen.”
He also suggests that if the group is more than a small handful of people, make sure a person acts as a “herder” to keep the group all together.
“Post tour, while they’re still on the floor, ask the group if there’s anything they want to see again or if there was a process that they weren’t clear on,” says Hartsell. “The majority of groups won’t have anything else that they want to look at.”
Once all questions have been


answered on the floor, he says to head back to the conference room, offer up snacks and lunch to the group, and ask if there are any follow-up questions or if the group needs any clarification about what they saw.
cessing the linen. You don’t want appear arrogant or that you’re putting on a show.”
Hartsell also says it’s helpful if the tour guide is a similar management level or higher than the tour group. This shows respect.
up the tour.
MAKING
THE TOUR
GREAT Hartsell thinks anybody can give a tour, but there are some things that can be done to make a tour great.
The first element is the tour guide. There are several qualities he looks for in a laundry tour guide. The first is knowledge; they must understand the laundry, the equipment (especially if he or she will be giving a demonstration) and be prepared to answer questions.
“It’s also helpful if they are able to build an instant rapport with the group,” Hartsell points out. “You don’t want to have the tour group look at the tour guide in disdain during the tour because that will leave a bad taste in their mouths.”
The guide should also be friendly and greet the plant employees during the tour.
“I’ve been on tours before where the tour guide treats the plant employees like they’re invisible,” he shares. “They won’t acknowledge, they won’t look at the employees who are out there pro-
The ability to communicate with the group during the tour is vital, he points out, so it pays to invest a little in the proper technology.
“We use a headset on large tours,” he shares. “We have a presenter headset and multiple tour headsets, and that way the tour guide doesn’t have to talk over equipment, shout to the person in the back. I can just talk in a normal tone and everybody can hear me. They aren’t expensive. They also show the group that you’re taking the tour seriously. You have, in their minds, this fancy equipment for the tour.”
Hartsell cautions to make sure the batteries are charged and to test the system before the tour in the conference room.
“You don’t want to have the tour group fiddling with their headsets because they don’t work,” he says.
If the laundry is giving a tour to existing customers or infection control/preventionists it has worked with in the past, Hartsell says putting the participants “in the workers’ shoes” can really step

“Giving the tour, I can stop, I can talk about what the employee in the laundry is doing, about how person is going to grab a towel, do a QC inspection, put it in the machine, which will fold it and then stack it, and the employee will then grab another piece,” he says. “I’ll show them how to do it, and then I’ll ask for volunteers, and then I will have them feed four or five towels or a couple blankets.
“Believe it or not, you think it might be awkward, but it does a really good job of making the tour group kind of realize this is laundry, they may think it’s menial, but really it’s something that’s important. I find they like to take pictures of themselves feeding the towels.”
Hartsell stresses put safety first in this instance. For example, don’t put somebody with a big, dangly necklace in front of equipment it may be caught on.
Another way a laundry can make a tour great is to identify the factors that make it special.
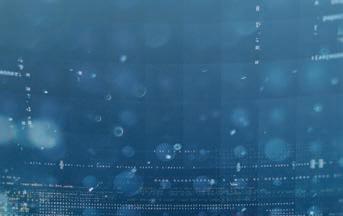

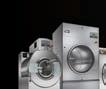
“Know the areas or processes or people that make your facility shine,” says Hartsell. “Figure out a way how to incorporate that into the tour. If you have somebody that does really, really good work, make sure you show them off.
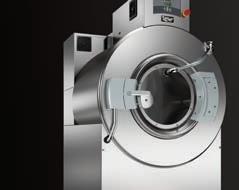
MAXIMUM PERFORMANCE IN LAUNDRY.
If you have a fancy new piece of equipment, make sure you show that off.”
Similarly, if there’s an employee who the tour company regularly works with, whether via or e-mail or phone, have that person come in sometime during the tour.
“A lot of times, putting a face to a name is helpful and is something that everybody likes,” he shares.
Hartsell also recommends that laundries utilize the tools they have to make a tour great.
“For example, if you need a trailer to store your excess stuff, if

Riddle
this is a major tour, pull your trailers in, load up your excess stuff to free up space,” he says. “Do you have to push an outside vendor because you have a tour coming up? Maybe it’s something as simple as repaving your lot, but push the outside vendor to make sure the project is completed before the tour starts.”
Next, Hartsell recommends focusing on areas of interest or concern. For example, if the tour is for operating room (OR) nurses, spend extra time in the OR pack room.
“If you’ve had an issue with a process, this is with an existing customer, be prepared to show them what you’re doing to improve this process,” he points out. “It’s beneficial if they have a concern that
Continued from Page 11
Car Wash Association and Coin Laundry Association. Their trade show was coming to Atlanta in 1981. They’d sell it but wanted him to run it.
“I said I would, and I have been with the Clean Show ever since then.” he shares.
He served the every-other-year event in that way until the opportunity to manage the whole thing came up.
“In ’92, they wanted to put the show out to bid for a management company,” Riddle remembers. “They asked me if I wanted to bid. I said yes. There were, I think, seven management companies and fortunately Riddle & Associates won that bid, and it’s been a blessing ever since.”
Riddle admits that the first Clean Show for which his firm was fully responsible frightened him.
“I was scared to death, tell you the
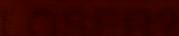


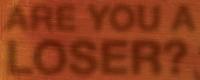
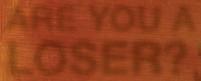
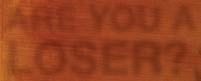
they realize my customer service rep has obviously told the laundry’s production because they have
truth,” he says. “It’s a big job when you put a show of this magnitude together. Things have changed tremendously as far as our ability to communicate, the speed with which we can communicate.”
Selecting a series of dates and a venue to attract the maximum number of attendees from all over the world is always challenging, he says.
While the spotlight is focused on him in these final months leading up to Clean 2019, Riddle readily admits that he couldn’t have organized and managed the event successfully without his loyal Riddle & Associates staff.
“They are my heroes,” he says. “Nobody could do this without a staff. Nobody’s that good, I don’t care who you are. I’ve been blessed for a career in baseball and many things that I’ve been able to do— God has been good to me—and one of the kindest things He’s ever done for me is put me in the midst of these people here.
“Whether it’s Paul (Philips), Beth (Scheuer), Ann (Howell), Jewell (Kowzan), Kayla (Brown), they’re unreal. … What

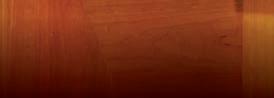
this new system in place. They are taking my concern seriously.”
Be prepared for the hard ques-
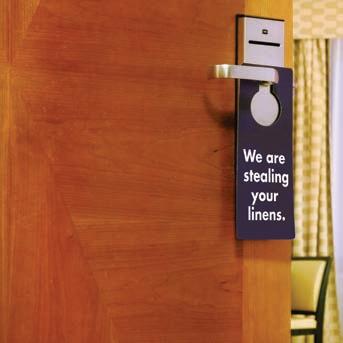
people will see at that show is done by five people. These people are like family to me. These people deserve the credit. They’re the ones who do the work.”
Beyond that group, there are many other people associated with the general contractors and the event venues themselves who contribute to the finished product.
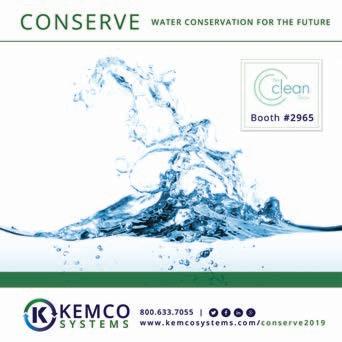
“If someone would walk on the trade show floor at 9:30 or 10 o’clock at night before we open, you would say there is no way this is going to be ready at 8 o’clock in the morning,” Riddle says. “If you don’t believe there is such a thing as miracles, come and spend that last night on a trade show floor, and when you come back the next day, it is spit-shined and polished.”
What will you miss most about the Clean Show?

He takes a deep breath, then says, “People.”
Relationships?
“Yep. … There are so many of you out there I enjoyed friendships with, enjoyed cutting up and kidding with. I’m a big jokester. Love to have fun. I love to work
tions. If the group asks the tour guide something they really don’t know, Hartsell says do not make something up.
“It’s okay to say you don’t know, but tell them you’ll find the answer, and get the answer back to them,” he points out. “If you have to, you can call the person in who can answer the question.”
In conclusion, Hartsell says laundry plant tours are a great opportunity to close, sell or convince a customer how well the laundry is doing, and tours need preparation work in order to be successful.
“Plan your tour and make sure everyone in the facility knows the tour’s coming, and a little bit of work can make your tour great,” he says.
hard but I love to have fun, too. I’m going to miss it. There’s no doubt about me being emotional.”
While Riddle will be slowing down without the Clean Show to manage, he says there are consulting and other opportunities available to Riddle & Associates if he chooses to pursue them.
But he’s not thinking about those just yet.
“I just hope that we can deliver the quality of show that, fortunately and thank God, we’ve been able to deliver, at least in our minds, to date,” Riddle says. “This is a great industry and we like being a part of its future. Hopefully, we can give it another good show.
“These guys that exhibit, they spend a lot of time and a lot of money planning and providing the best information they can for the industry. I’d like to see a large number of people come out and take advantage of that.” ALN
ALNFinding the right folder

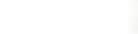
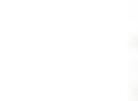
LAS CRUCES, N.M. —
American Linen & Uniform Supply, located here, has two ironers in its plant currently. One is an eight-roll ironer. The other is six-roll.
On the eight-roll ironer, the company has a large-piece folder to handle the goods coming off the ironer. However, American Linen had nothing on the back of its sixroll ironer.
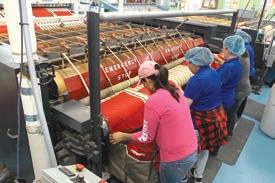
President and CEO Michael Lutz had been searching a long time to find the right piece to back the sixroll ironer. Recently, the company purchased and installed an LF Series Large Piece Folder/Crossfolder from Leonard Automatics to handle the work.
American Linen purchased the LF due to its flexibility between large and small pieces, as the company needed small-piece draping capability, while being a back-up to its large-piece folder if it were to go down for any reason.

“Leonard’s folder allows us the flexibility to quickly change between small pieces and large pieces with the touch of a button,” says Lutz.
He had considered a Leonard Stack-N-Store two years ago, but what ultimately made Lutz decide
on the LF was the versatility to handle any product, any time with one machine.
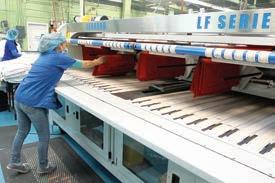
The installation of the LF was seamless, according to Leonard. The site was well-prepared when the team arrived. American Linen & Uniform Supply proved to be a great partner for this installation.
In the linen plant, all ironed product (i.e., sheets, tablecloths, napkins, aprons) flows directly from the wash floor to the clean sling storage system, where they are hoisted into the air and moved to the ironers. When the product is needed, the sling is dropped into a cart and the cart is advanced to the ironer where the operators load the product.
With the new LF folder, American Linen has automated folding, stacking and/or draping without the need for hand folding and stacking.
The employees have been very happy with the machine. The company says the simplicity of the Siemens interface, which is a very intuitive system, and the ability to quickly change products from large piece to small piece and back again has allowed it flexibility that American Linen never had before.
“The precision folding and reli-

ability exceeded our expectations,” Lutz shares. “It has dramatically increased our quality and productivity while significantly reducing our labor. Leonard’s ongoing support is second to none.”
Since the installation, American Linen has increased its productivity by 40% on its six-roll ironer. The LF significantly increased capacity, throughput, reliability and overall on-time processing.
The company can now meet the changing demands of its customers or fill short notice orders easily. ALN


As your appetite for knowledge to improve your business grows, give our American Laundry News Podcast a listen. Join Editor Matt Poe as he engages a special guest in one-on-one conversation about the topic of the day. This free channel provides another convenient way for you to gain laundry and linen management information and insight from industry peers and other experts—no muss, no fuss.


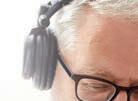
CHECK OUT WHAT YOU’VE MISSED:
How Distributor Partners Help Laundry Operations








Distributors provide essential equipment to laundry/linen services, but there is more to the equation. Find out more from guest Craig Dakauskas, president of CLEC.
Improving Laundry Efficiency Without Losing Quality
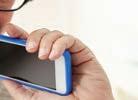
Explore how a laundry can operate at a better level of energy efficiency with guest Seth Willer, national sales manager for Girbau Industrial.
The Man Behind the Clean Show
Retiring show manager John Riddle talks Clean history and reminisces about his long career, including his time in pro baseball, stadium management, rodeo production, and more with guest host Bruce Beggs.

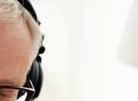
• Brianna Widmark, hospital route service representative, Miller’s Textile Services, Wapakoneta, Ohio (operator).
• Farley Salmon, healthcare sales director, SigmatexLanier Textiles, Suwanee, Ga. (associate).
The other six companies that were overall winners:
• Clean Green Innovation: Prudential Overall Supply, Irvine, Calif. (operator); Ecolab Textile Care, St. Paul, Minn. (associate).
• Community Service: Huebsch Services, Eau Claire, Wis.
• Diversity Recognition: Service Linen Supply, Renton, Wash.
• SafeTRSA Safety Excellence: Quintex Services, Winnipeg, Manitoba, Canada (operator); Kemco Systems Co. LLC, Clearwater, Fla. (associate).
Four of the aforementioned companies also won in other competitions:
• Ecolab Textile Care, hailed for its hot water filtration in its paramount Clean Green victory, won Above and Beyond recognition thanks to its Support and Application Team’s efforts to support customers’ total plant management.
• Huebsch’s overall community service recognition was based on its work with locally based charities as well as local branches of regional, national and international organizations; its Above and Beyond accomplishments were reflected in its 99%
customer service ratings.
• Prudential’s commitment to chain-wide sustainability through Clean Green certification took the designation’s namesake high honor. The company’s Mesa, Ariz., cleanroom team’s dedication to near-miss investigations, audits and training won recognition for safety.
• Quintex, which topped the safety competition thanks to numerous measures, including electronic documentation, return-towork practices and wellness, also was recognized for community service, led by its Q-Crew program that incentivizes employees to give their time.
Service Linen Supply’s overall diversity win recognized its hiring of 20% of its employees through organizations supporting kids
with special needs, refugees and military veterans. Kemco took a top SafeTRSA honor on the strength of a program that led to 442 consecutive days without an OSHA-recordable incident.
Miller’s Textile’s Widmark won praise efforts that led to surgeon satisfaction with the scrub program she manages and her timely problem-solving. Sigmatex-Lanier’s Salmon was hailed for exceptional attention to laundry employees and providing textile inventory in a pinch.
Mission Linen Supply, Santa Barbara, Calif., won two awards: Clean Green for its relentless pursuit of water and energy conservation and Above and Beyond for its compassion for employees and customers in natural disasters.
Other award-winning operator companies included:
• Bates Troy Healthcare Linen Services, Binghamton, N.Y.,
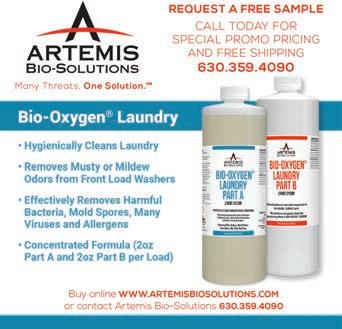
safety, saving a co-worker’s life.
• Paris Cos., DuBois, Pa., community service, hiring inmates on work release.
• Superior Linen Service, Springdale Ark., safety, 2,062 days with no lost-time injuries.
• UniFirst Corp., Wilmington, Mass., diversity, English as a second language classes for employees.
• West Michigan Uniform, Holland, Mich., community service, monthly campaign to support a different employee or employee’s cause.
• White Plains Linen, Peekskill, N.Y., Clean Green, eliminating nonrenewable energy use and capturing rainwater.
in postponing a vacation to assist a laundry in recovering from a catastrophic fire; Meese Inc., Madison, Ind., took a safety award for ergonomically focused products aimed at eliminating a variety of common workplace injuries in laundries; and WSI, Cincinnati, for developing alkalifree wash chemistry.
Also honored in Washington were winners of the Volunteer Leadership Award: individuals active in TRSA who recognize the competitive benefits and overall economic value to their companies of strengthening the industry, including their own competitors.
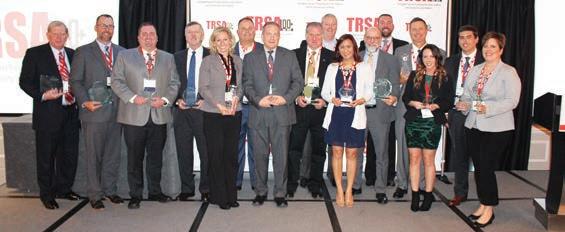
GSM_haul_mp july_aug.pdf 1 2/20/2014 7:42 AM
GSM_haul_mp july_aug.pdf 1 2/20/2014 7:42 AM
Other associate company winners were Colmac Industries Inc., Colville, Wash., as David Rinella went Above and Beyond
This honor for operators went to Liz Remillong, strategic alliance vice president, Crothall Healthcare, Chesterbrook, Pa.; for associates, it went to Mike Diedling, retired applications engineering manager, Pellerin Milnor Corp., Kenner, La. ALN
For more information: G.S.M. Linen Handling Systems 1-800-363-CART (2278) www.gsm-cart.com
For more information: G.S.M. Linen Handling Systems 1-800-363-CART (2278) www.gsm-cart.com
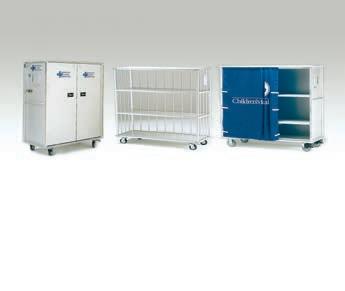
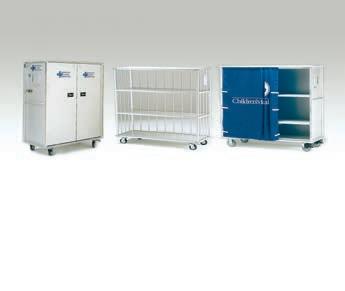
SUCCEED TOGETHER
NETWORK AND CONNECT WITH INDUSTRY LEADERS, EXPERTS AND PEERS.
• 450+ EXHIBITING COMPANIES exhibiting over one-quarter-million net square feet
• 11,000+ PEOPLE from 100 countries
• LIVE DEMONSTRATIONS of the latest equipment and technology
• NETWORKING with manufacturers, suppliers and industry peers
Classified Advertising
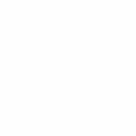





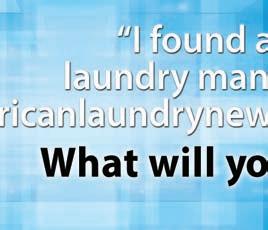
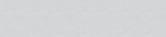

PARTS FOR SALE
PARTS, PARTS, PARTS
Huge stock of parts for most laundry equipment & boilers. Also traps, valves and lubricants. Overnight delivery. Steiner-Atlantic, 800-333-8883 Fax: 305-751-8390 parts@steineratlantic.com www.steineratlantic.com
PARTS & SERVICE
In need of service and or parts for all your finishing equipment manufactured by BB&D, Lavatec, Washex, and Voss? Contact Michael @ 203-232-4004 or E-Mail me: mtenhave66@yahoo.com
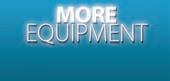


®
Call Deana Griffin 888-235-2365 www.thegriffingroup.cc deana@thegriffingroup.cc

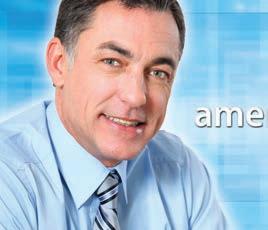
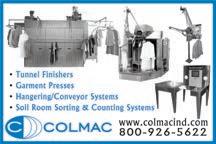
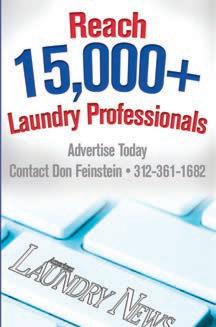
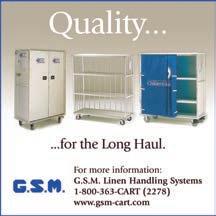


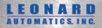





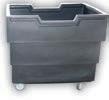

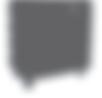

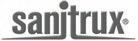






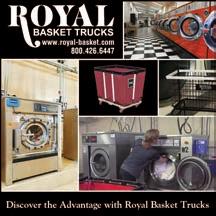
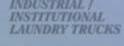
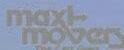
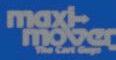
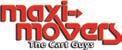
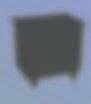














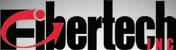










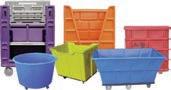

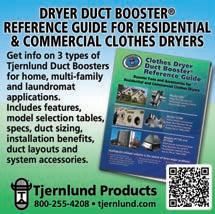



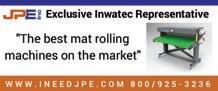
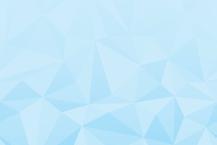










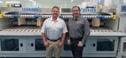



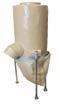
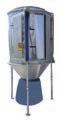



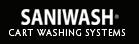
SMALL-PIECE FOLDERS



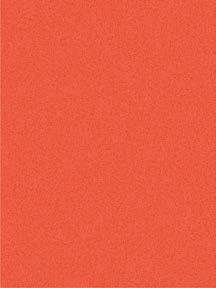
Pellerin Milnor Corp. P.O. Box 400, Kenner, LA 70063 504-467-9591, Fax: 504-468-3094 www.milnor.com
Pellerin Milnor Corp. P.O. Box 400, Kenner, LA 70063 504-467-9591, Fax: 504-468-3094 www.milnor.com
Pellerin Milnor Corp. P.O. Box 400, Kenner, LA 70063 504-467-9591, Fax: 504-468-3094 www.milnor.com
Pellerin Milnor Corp. P.O. Box 400, Kenner, LA 70063 504-467-9591, Fax: 504-468-3094 www.milnor.com
















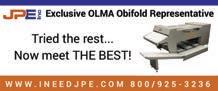

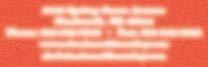


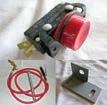

CLM hosts dryer service training

LOS ANGELES — Consolidated Laundry Machinery (CLM) recently hosted a successful dryer service training program for employees of long-time customer Prudential Overall Supply (POS) at CLM factory headquarters in Pomona, Calif., according to the company.
CLM is a “dryer-only” manufacturer that makes industrial dryers capable of being configured in multiple ways to accommodate any installation.
Prudential Overall Supply is determined to wring all the benefits from its dryer features by engaging the company to educate employees, according to CLM.
“POS wanted both classroom instruction and handson training for their corporate and plant engineers to bring everyone up to speed on best operation and maintenance practices for our industrial dryers,” says Gabriel Camacho, CLM president.
Along with a classroom program taking place in CLM’s spacious Training Center, the company was able to utilize production machines on the factory floor, in various stages of completion, to advance hands-on demonstration and training of participants.
“At the end of the day, our training program built confidence in overall use of our machines, and that will translate to better efficiency, longer machine life and more profitability,” Camacho shares.
In memoriam: Seymour Katzson, Katzson Brothers Inc.
DENVER — Seymour Katzson, co-founder of laundry product supplier Katzson Brothers Inc., died March 23 just days away from his 99th birthday.
He was well-known in the dry cleaning and laundry industry not only for his consummate sales and customer relation skills, but also for his broad knowledge of equipment and parts.
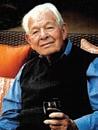
Katzson had a friendly, indefatigable presence in the industry for more than 80 years.
A member of the increasingly shrinking Greatest Generation, Katzson and his brother, Sidney, spent most of their formative years at the Denver Sheltering Home for Jewish Children, as their mother passed away when Seymour was less than a year old.
At the age of 6, Seymour was selling newspapers on “his” 15th and Champa St. corner in Downtown Denver. During World War II, he served as a radio operator in
the Ascension Islands and then returned home after the war to help his brother operate and run the business they established before he left.
Sidney and Seymour founded Denver Tailor Supply (later to become Katzson Brothers) with a $200 loan. Since then, Katzson Brothers has become a national leader in the laundry/dry cleaning and hotel/motel/hospitality industries.
Today, Katzson Brothers is 84 years old and has expanded to three locations, serving a 10-state region.
Katzson is survived by his two daughters Michele Right (Richard), Robyn Levy (Andrew), five grandchildren and eight great grandchildren. He was married to Maxine Price Katzson, who preceded him in death after 64 years of marriage. His daughter Mindy died 11 years ago.
Donations can be made to The Denver Hospice.
WSI earns MVP2 Award from National Pollution Prevention Roundtable for achievement
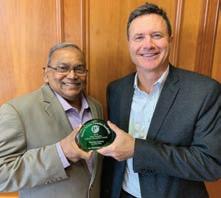
LOVELAND, Ohio — Washing Systems LLC (WSI), a provider of commercial laundry chemicals, reports it was recently presented with the Most Valuable Pollution Prevention (MVP2) Award from the National Pollution Prevention Roundtable (NPPR).
The award is presented annually to companies demonstrating outstanding achievement in pollution prevention by NPPR. WSI says the recognition is for its TRUpath™ technology, which removes the use of sodium hydroxide or caustic soda (alkali) in wash formulas.
“All of the chemicals WSI focuses on eliminating are important to avoid, and if people would follow their example, substantial environmental improvement would result, and discharges to water would be far less harmful than they now are,” says NPPR board member and chair of the awards committee, Rick Reibstein. “Achieving significant reductions in energy and water use make this (TRUpath™) significant, and we want to reward with recognition that broad-based, holistic approach, which is
Calendar
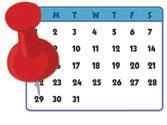
May
23 Association for Linen Management Webinar: Minimizing Cyber Risks Richmond, Ky. Info: 859-624-0177
23 MTSA Wrigley Field Event Chicago, Ill. Info: 888-672-6872
June
5 TRSA
Webinar: Workplace Bullies/ Abrasive Leaders - Why They Act That Way, How to Make Them Stop Alexandria, Va. Info: 703-519-0029
20-23
most efficient and most ethically responsible.
“In addition, sodium hydroxide is a serious workplace hazard, so you are reducing workplace exposures, an aspect of P2 that is not as often pursued. That WSI sees this as a demonstration for others to follow is a contribution to the industry.”
“It is truly gratifying to see our entire company receiving another recognition for TRUpath™,” adds WSI CEO John Walroth. “We challenged our R&D team some five years ago to make this dream a reality. Not only are our customers reaping the benefits of this technology, but our communities and environment will benefit for years to come.
“As a company, we are committed to environmental stewardship, and continue to embrace ‘Doing the Right Things’ … for our customers, our associates, the environment and our communities.”
This is the third time WSI has earned the award. Previous recognitions were for removal of NPEs, phosphates, EDTA and petroleum solvents. ALN
The Clean Show
World Educational Conference for Laundering and Drycleaning New Orleans, La. Info: 404-876-1988
July
18
Association for Linen Management Webinar: Parlez-Vous Español, Bitte? Richmond, Ky. Info: 859-624-0177
31- Textile Care Allied Trades Association
Aug. 3 TCATA 2019 Annual Conference Ojai, Calif. Info: 813-348-0075
August
7 TRSA
Webinar: TRSA’s New Safety & Health Certification Alexandria, Va. Info: 703-519-0029
11-15 TRSA
55th Executive Management Institute (EMI) Hyattsville, Md. Info: 703-519-0029
11-15 TRSA
30th Production Management Institute (PMI) Hyattsville, Md. Info: 703-519-0029
CODED MICROFIBER
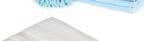

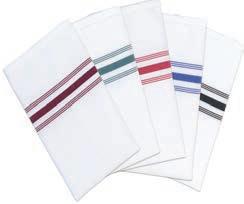
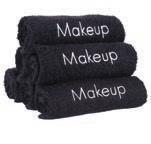




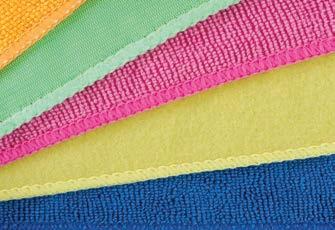
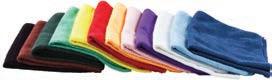
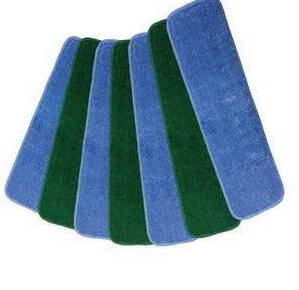
These bar mops are perfect for wipe-and-toss in heavily soiled environments. Weaving defects such as over-stitching or IR cuts reject perfectly good wiping tools from circulation. We buy these at a deep discount and pass the savings on to you. Packed: 100 doz/bale.
When bar mop production runs are over and inspections have been completed, mills have excess yarn. Run Of Mill (ROM) bar mops contain every bar mop that comes o the loom after the first quality run has been finalized, so are more economical than Grade A1 bar mops.
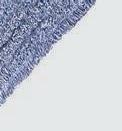
Route Ready bar mops are optically white and packed in bags of 25 so you never have to pre-wash or recount them prior to use. Typically, laundries save 70¢/doz by freeing washroom and finishing floor operators from a whole wash cycle.
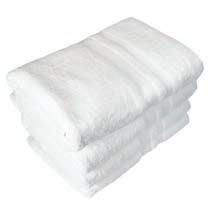
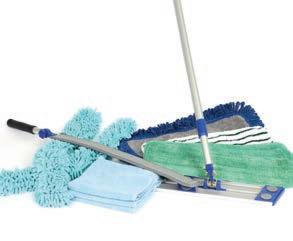
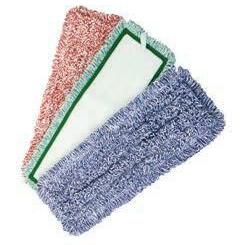
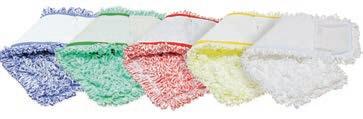
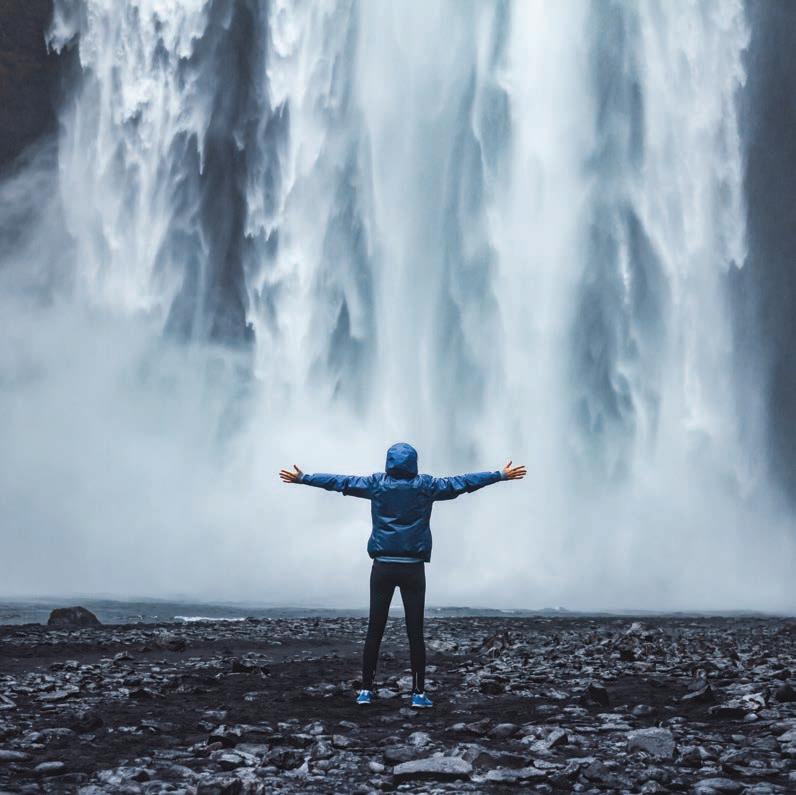
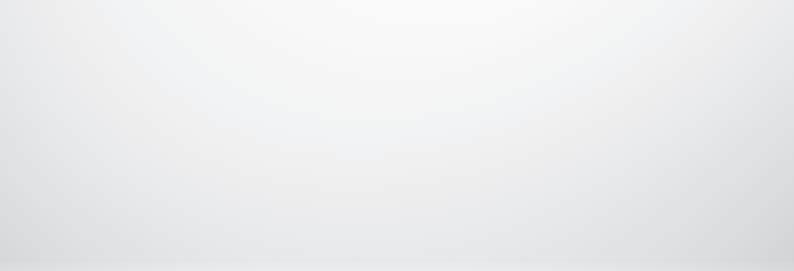