Late News
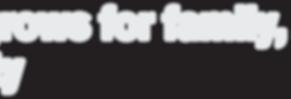
The merged company will continue doing business as NOVO Health Services, and the Paris trade name will continue in use for an indefinite period.
Terms of the deal were not disclosed. Paris Uniform Services is not involved in the merger and will continue as an independent Paris company.
Combined, the new enitity operates seven Healthcare Laundry Accreditation Council (HLAC)accredited or TRSA Hygienically Clean-certified processing facilities in the Eastern United States.
Stern will serve as CEO of NOVO. Karl Fillip will serve as CEO emeritus and will continue as head of sales. Karl Fillip II will serve as chief operating officer. ALN
Laundry grows for family, community
That’s the day the company will open its new 35,000-square-foot facility in North Charleston, which will house a tunnel system.
The new facility, which broke ground in September, is a $9 million expansion designed to handle more than 20 million pounds a year and add 60 full-time jobs.
“We are growing to offer full-service commercial laundry services to all of the upcoming hotels, resorts and medical centers,” says Ann Son, president of Holy City
Linen Services. “This is an exciting time to be in the laundry business in Charleston, South Carolina.”
CHICAGO — There are many studies that examine contamination and sanitary linens. These include past research, current inquiries and there will be studies conducted in the future.
Most are high-quality, objective studies, says Gregory Gicewicz, president of Sterile Surgical Systems in Tumwater, Washington, and past president of the Healthcare Laundry Accreditation Council (HLAC).
“Typical focus areas include the efficacy of the laundry process in removing pathogens and the epidemiology of healthcare associated infections (HAIs) s attributed to laundered healthcare textiles,” he says. “Other more recent research focuses on antimicrobial treatments and residues for healthcare textiles.”
“TRSA continues to build the largest database of results from routine microbiological testing of destination healthcare textiles (HCTs) in North America,” says Joseph Ricci, president and CEO of TRSA, the association for linen, uniform and facility services. “The 150-plus Hygienically Clean Healthcare certified laundries are on a quarterly sampling regimen.”
Dr. Christian Mechel, product manager, environmental economics,
Volume
46, Number 2
Panel of Experts
Research into healthcare laundry cleanliness is ongoing and service providers have to stay informed. (Image licensed by Ingram Publishing)
solutions
Countering concerns in healthcare laundry sanitation
larger than its current facility, which will be converted to solely handle food & beverage and party linen rentals.
Company leaders toured more than a dozen laundries across the country to define what was needed to run a successful laundry, from the employees to the equipment.
Not that Son and her family didn’t have a good amount of knowledge and experience already.
“I am a second-generation dry cleaner and launderer with over 30 years of experience in the business in both of the Carolinas,” she says. “My sister and I grew up in the business. Our bus stop used to be at the cleaners!”
As the dry-cleaning market began evolving in the early 2000s, Son says her family realized that they needed to adapt to the changing needs of the customers as well. Holy City eliminated the use of all dry-cleaning chemicals and converted to using wetcleaning processes at all of its locations.
“A few years ago, we began receiving an overwhelming number of inquiries for commercial laundry services within the market and decided it would be a natural extension of our current operations,” shares Son. “So here we are today.
“We have experienced tremendous growth in both arenas. We are the only company in the marketplace to be able to offer drycleaning and commercial laundry services on a large scale.”
She says that many of their clients prefer a locally owned company that can handle all aspects of textile cleaning under one roof, whether it is dry-cleaning services for guests, cleaning custom-made draperies, or pressing Irish linen sheets and luxury spa robes.
“We are equipped to handle it all,” adds Son.
“I have found Ms. Son to have extensive knowledge and experience in the dry-cleaning and laun-
dry industry,” says Darrell Jones, Charleston Area Small Business Development Center (SBDC) area manager and regional director of the University of South Carolina region of the South Carolina SBDC.
“As a second-generation business owner in the dry-cleaning and laundry industry, she understands the commitment needed to make the business a success.”
“We proudly service the Charleston area because we live here and work here,” says Son.
Holy City Linen Services operates 364 days a year. It’s current facility has 17 employees to process more than 2 million pounds of dirty laundry a year.
“Since Charleston is a tourist destination, we process a good percentage of our poundage from March-September,” Son shares.
“Our current facility relies on washer-extractors and, of course, our ironer. Our facility is small compared to most, but that’s what makes us unique.
“We are incredibly organized and efficient in order to crank out that kind of poundage on time. We have perfected the process.”
Because Holy City Linen is heavily reliant on tourism, business is slow during the winter months into early March. To combat this, Son says the company has focused on customers who cater to locals like massage clinics, doctor’s offices and restaurants.
“We have simplified the laundry process by offering all-in rates and picking up and delivering on time,” Son points out. “We rely heavily on our chemical partners and equipment vendors as well to ensure clean, crisp linen the first time around. This simplicity is the reason for our success.
Holy City Linen is an ecofriendly operation and has implemented changes such as asking hotels to use nylon bags, which the company provides, instead of trash bags for dirty linens. It also assists in repurposing linens that have permanent stains by donating them to a local shelter.
“Our company is family owned and operated,” Son says. “This is what makes us special. But it isn’t just our family here. We have multiple families who have com-
Publisher
Charles Thompson
Phone: 312-361-1680
E-Mail: cthompson@ ATMags.com
Associate
Donald Feinstein
Phone: 312-361-1682
E-Mail: dfeinstein@ ATMags.com
Editorial Director
Bruce Beggs
Phone: 312-361-1683
E-Mail: bbeggs@ ATMags.com
Editor
Matt Poe
Phone: 866-942-5694
E-Mail: mpoe@ ATMags.com
Roger Napiwocki
Digital Media Director
Nathan Frerichs
Phone: 312-361-1681 E-Mail: nfrerichs@ ATMags.com
David Barbe • David Carter
Janice Ayers Davis • Nick Fertig Deana Griffin • Steve Kallenbach Edward McCauley
Main Phone: 312-361-1700 Fax: 312-361-1685
630-739-0900 x100 www.americanlaundrynews.com
American Laundry News (ISSN 1091-9201) is published monthly. Subscription prices, payment in advance: U.S. 1 year $46.00; 2 years $92.00. Foreign, 1 year $109.00; 2 years $218.00.
Single copies: U.S. $9.00; Foreign $18.00.
Published by American Trade Magazines LLC, 650 West Lake Street, Suite 320, Chicago, IL 60661.
Periodicals postage paid at Chicago, IL, and at additional mailing offices.
POSTMASTER, Send changes of address and form 3579 to American Laundry News, Subscription Dept., 440 Quadrangle Drive, Suite E, Bolingbrook, IL 60440. Volume 46, number
2. Editorial, executive and advertising offices are at 650 West Lake Street, Suite 320, Chicago, IL 60661. Charles Thompson, President and Publisher. American Laundry News is distributed selectively to qualified laundry and linen management and distributors in the United States.
© Copyright AMERICAN TRADE MAGAZINES LLC, 2020. Printed in U.S.A. No part of this publication may be transmitted or reproduced in any form, electronic or mechanical, without written permission from the publisher or his representative. American Laundry News does not endorse, recommend or guarantee any article, product, service or information found within.
Opinions expressed are those of the writers and do not necessarily reflect the views of American Laundry News or its staff. While precautions have been taken to ensure the accuracy of the magazine’s contents at time of publication, neither the editors, publishers nor its agents can accept responsibility for damages or injury which may arise therefrom.
mitted to our growth. We rely on each other to get the job done, and when we grow, we grow together.” ALN
When Milnor introduced PulseFlow® technology, CBW® washing was thrust into the future. The idea of balancing time, temperature, mechanical action and chemistry was missing one critical piece of the pie – DILUTION through the efficient use of water.
PulseFlow combines the innovative RecircONE® fast wet down and chemical immersion in the first module with standing bath washing in every spacious process module. Thorough and efficient dilution occurs by way of intermittent high velocity counterflow rinsing and traditional True Top Transfer.
The result is hygienically clean linen using less water (as low as 0.3 gallons per pound/2.5 liters per kilogram) and less energy as proven time and again by hundreds of PulseFlow tunnels in a variety of laundry applications worldwide.
Contact an authorized Milnor distributor or call 504-712-7656 to find out more.
www.milnor.com
O
ne of the top goals, if not the top goal, of laundry and linen services is to provide clean goods to their customers.
But you don’t need me to tell you that.
Each and every one of you knows that if the laundry isn’t clean, you’re probably going to lose customers.
However, the stakes are higher in healthcare laundry. In a setting where eliminating “germs” is essential to patient care, linens have to be more than clean.
They have to be sanitary, or hygienically, clean. They have to be handled properly by laundry and healthcare staff. Even the equipment and facilities need to be more than clean.
While the actual number of incidents where patients have contracted illnesses from linen is
The Editor’s Desk MATT POEinfinitesimally small, in healthcare, perception is the reality. One news item even hinting that healthcare linen might have been involved in an incident with a patient (most often to be proven false) can cause the perception that there’s a flaw in the healthcare laundry system.
That’s why this issue has two stories related to healthcare linens.
You’ve probably already seen the first on page 1. In order to be vigilant, research is ongoing in regards to healthcare laundry processing and handling. In the story, those in the know talk about the research, the concerns and ways for healthcare laundry facilities to do everything possible to ensure patients are receiving and using sanitary linens.
While the first article looks mostly at the laundry plant, missteps can be made at the healthcare facility in terms of cleanliness and usage. That’s where the linen committee comes in (page 8), to make policies, educate and enforce guidelines.
Remember, American Laundry News is all about helping everybody keep it clean! ALN
FRANKFURT AM MAIN, Germany — Texcare International will open its doors here June 20-24, and show organizer Messe Frankfurt says market leaders from all over the world, with products for all areas of textile care, have already signed up.
“Registrations for Texcare International are excellent,” says Kerstin Horaczek, group show director technology at Messe Frankfurt. “Because we are again using Halls 8 and 9, Texcare International will be able to grow in terms of exhibition space and strengthen some of the more dynamic product groups, including, for instance, IT, which has gained greater weight recently, not least as a result of digitalization.”
The driving force in textile care is the development of digital solutions into smart ones, according to organizers. This provides the umbrella for all four major themes at Texcare International: “Smart Factory,” “New Business Models,” “Sustainability” and “New Work–New Learning.”
The “Smart Factory” theme covers the intelligent interlinking of production and data flows, so as to enable a high degree of automation in modern textile care.
Digitalization opens up new ways for textile cleaning services to get in touch with their customers, and “New Business Models” are now emerging that make it possible for consumers to make contact via online
shops or apps, offering innovative collect and delivery services in collaboration with logistics companies.
Another important driver of innovation, says Messe Frankfurt, is “Sustainability.” For laundries, there are many new technologies and processes relating to energy efficiency, the sparing use of washing agents, wastewater treatment and water recovery.
Of course, these technologies bring changes to the world of work and, against the background of a shortage of trained staff, offer attractive possibilities for further training, professional development and staff retention. These aspects are covered by the “New Work–New Learning” theme.
All of these issues will also be covered in the complementary program at Texcare International. The Texcare Forum, to be held from June 20-23, makes a crucial contribution to the international transfer of knowledge and to discussions between experts and business partners.
New for 2020, the last day of the trade fair, June 24, will be devoted to the younger generation in the sector under the heading Young Texcare. Trainees from all over Europe will be divided into mixed teams and will measure themselves against one another in various disciplines.
For more information, visit texcare.messefrankfurt. com. ALN
No matter how perfect your work crew may be, there are always a couple of lower performing or problem employees. As I reflect back over my 45 years of working experience, I have heard a number of reasons why managers do not appropriately deal with these employees. My definition of appropriately dealing with problem employees is to get them to improve their performance or attitudes, or make the decision to move on to greener pastures.
You will note that I did not set a goal to fire the employees. I can honestly say that in my many years in management I never fired anyone but watched a number of employees fire themselves.
The most often cited reason for not dealing with employees is that the organization just makes it too hard for us to discipline or fire an employee. I am the first to admit that there can be a number of steps required in dealing with poor attendance, poor performance or poor attitude of an employee. But most organizations have a well-defined path that can be followed to achieve your goals.
The system wants to be sure that the employee has every chance to improve their behavior. The goal should always be to improve the employee, not fire them. The fact that there are a number of steps that must be followed is not a problem. Failure to understand and use the system only makes you look like an incompetent or lazy manager.
A similar excuse is that if I write the employee up, they will complain to HR about me and I will have to defend my actions and I might look bad. These managers do not understand that failure to use the system established to deal with problem employees makes them look bad to their bosses and hurts morale with their other employees.
This excuse also applies to employee performance reviews. I have seen many reviews scored higher than the employee deserves just to avoid that employee making a complaint. It is our job as managers to ensure that the actions taken are correct and accurate and can be properly defended.
I have heard managers say that an employee is so valuable to my organization that I must protect them at all costs. Appropriate actions are not taken because the manager fears having to run his area without their help. The employee involved knows that and uses that fact to his or her advantage. It is also known by your staff and always leads to unhappy employees.
A similar excuse often heard is that they are my friend or their parents are my friends. Employing friends is always a difficult balancing act. A manager will likely have a problem treating the friend just like they would another employee. They either expect more from them or less than the average employee. No matter how they deal with the situation, their employees will always be talking about it.
The goal or any manager is to reduce turnover and run an efficient operation with the appropriate amount of staff. Employees want to know they are appreciated for their efforts and that they are treated the same as everyone in the organization.
Failure of management to deal with problem employees cause the good employees to wonder why they follow all the rules when others do not and there are no consequences. Some employees delay improving their performances because they know that until management is serious and deals with the real problem employees, they are safe.
From
•
•
•
•
•
•
From AmericanCoinOp.com:
•
Poor management in this area will hurt productivity and increase turnover. In a tight labor market, turnover is expensive and a detriment to production. So as managers, learn your organization’s rules and actively use the system to encourage your employees to improve.
Additional work now will make your job much easier in the future. ALN
Eric Frederick served 44 years in laundry management before retiring and remains active in the industry as a laundry operations consultant. You can contact him by e-mail at elfrederick@cox.net, or by phone at 540-520-6288.
With food recalls making the national headlines, companies are turning to HACCP programs more than ever to help minimize cross contamination risks. American Dawn offers the garments, processes, and training your clients need to implement their own HACCP program. Contact us today to see how you can capitalize on this decade’s biggest opportunity. 800.821.2221 | americandawn.com | imagine@americandawn.com
bioindicators reduction by seven log levels of Staphylococcus aureus and Enterococcus faecium.”
What does this constant research mean for healthcare laundry operations? It’s important to stay on top of the research and to be vigilant about maintaining sanitary laundry from the plant to the patient.
There are always safety concerns when it comes to healthcare textiles contacting the skin of compromised patients.
“Outbreaks attributed to laundered HCT have occurred but are rare,” Gicewicz points out. “Of the billions of pounds of HCT processed annually, I am only aware of 13 outbreaks in 48 years worldwide, impacting roughly 356 patients. While any outbreak is tragic, that is an impressive track record for our industry.”
Of some concern, however, research has shown that HCT can transmit pathogens and reports of microorganisms on HCT textiles are common, he says. Also, he continues, research has proven that multi-drug resistant microorganisms (MDRO) can survive on HCT for weeks, and soiled HCT can contaminate surfaces and medical devices.
More recent concerns Mechel mentions include killing spores on hospital linen and the corresponding recontamination after washing (packaging, storage, transport). In addition, he mentions the topic of microplastic/fibers, which are a result of the washing process of blended fabrics.
TRSA’s annual Healthcare Conference featured a research review, including a live feed from the United Kingdom with Dr. Katie Laird, a biologist and professor at De Montfort University in Leicester, on a new standardized method for determining the antimicrobial efficiency of laundry processes.
“Specifically, Dr. Laird’s research focused on the potential danger of nurses washing their scrubs at home because the home washer may not kill all microorganisms,” Ricci shares.
He goes on to say that another presentation included a discussion by Dr. David Goldsmith of George Washington University on plans to develop a peer-reviewed journal article on the development of TRSA’s Hygienically Clean Healthcare certification program.
A third presenter, Steve Tinker of Gurtler Industries Inc., focused on a peer-reviewed article that confirmed the efficacy of peracetic acid for killing C. difficile spores in a tunnel washer.
While it makes sense for healthcare laundries and facilities to monitor research and concerns, Gicewicz recommends caution when new studies come out.
“Unfortunately, there are a host of biased ‘fake science’ studies funded by organizations with an agenda,” he points out.
Gicewicz says operations need to be vigilant and critical in using research efforts to make business decisions. Make it a practice to analyze the funding source and the actual data, going beyond the headlines.
“Hospital linen is insignificant to HAIs and probably always will be,” adds Ricci. “Based on the two cases in the U.S. reported by the Centers for Disease Control and Prevention in the 2000s, CDC statistics indicate the chance that an American won’t wake up tomorrow because her/ his bed suffocated and strangled the individual to death is 77 times greater than the chance that a U.S. hospital patient will be affected by an HAI transmitted by bed linen.
“If an opportunity to reduce this infinitesimal risk presents itself, however, it’s considered for the standard. The Hygienically Clean standards address each stage of laundry workflow from receiving soil to delivering clean.”
Laundries should regularly test for contamination and challenge their hygiene practices at multiple points throughout the process, shares Gicewicz.
“Remember, consistently producing hygienically clean HCT at their point of use requires constant testing from end to end,” he says. “Think of a symphony where one wrong note from one instrument ruins the entire performance. Establish cleanliness standards and practices in your plant and test against them.”
A few important examples Gicewicz mentions include:
• Are you monitoring your sort process to ensure textiles are sorted into the correct categories? If not, you are risking contamination due to incorrect wash formulas.
• Are you regularly titrating your wash formulas to ensure proper chemical concentrations, pH, water levels, water temperatures, and wash times? If not, you are risking HCT contamination due to incorrect chemistry.
• Do you regularly check wash equipment for proper function?
If not, you are not washing optimally and are potentially producing contaminated HCT.
• Rinse water should be tested for contamination regularly.
An optimal wash process still produces contaminated HCT when there is dirty rinse water.
• Air that comes into contact with clean HCT should be tested regularly for contamination. Clean HCT with dirty air touching them will become contaminated.
• Hard surfaces that touch clean HCT should be tested regularly for contamination. These include carts, conveyers,
shelves, and tables. Clean HCT that touch unclean surfaces become unclean HCT.
• Employees that touch clean HCT should have their hands tested to ensure they are clean. Dirty hands touching clean HCT produces dirty HCT.
• Finally, HCT should be tested for contamination as close to the point of use as possible. While there is no agreed upon standard of hygienically clean HCT, set your own baselines and test methods and manage to them.
Gicewicz says laundry operators can stay up to date on identified contamination/sanitation issues and methods by regularly checking with expert organizations that specialize in HCT contamination/ sanitation issues and methods.
“Stay current on laundry publications, such as American Laundry News,” he shares as an example. “Stay plugged into standards/ accreditation organizations such as HLAC. They will have the inside track on the latest HCT contamination/sanitation issues as well as tools to address them.
“Constantly check with your key vendors for emerging trends and technologies. Your chemical vendor should have the inside track on emerging methods of cleaning HCT through chemistry. Your linen vendor should have insights into newer textiles that resist contamination.”
Effective testing, Mechel adds, includes surface microbial count, bioindicators, visual inspection of order and cleanliness, and continuous training of staff.
“Documentation in a control manual and self-control/internal audit of a plant are effective, as well as external hygiene inspections by independent auditors, like within the Hohenstein Hygienically Clean Certification,” he says.
Ricci points out that TRSA’s Hygienically Clean microbiological tests serve this purpose.
“While Hygienically Clean Healthcare certification continues to focus on outcome-based protocols, inspectors are now implementing hazard analysis and critical control point (HACCP) principles similarly to the Hygienically Clean food programs,” he shares.
“Collection of ATP [adenosine triphosphate] surface testing data at CCPs [critical control points] is expected to provide hundreds of samples for analysis and consideration by the Hygienically Clean Healthcare Advisory Board in 2020.”
Laundry work hits home hardest when laundry employees see the impact of their work on sick hospital patients, says Gicewicz.
“A finish employee may view the gown she is folding as one of a thousand inanimate objects that go somewhere that she does not care about,” he says. “Now go to a critical care part of a hospital and observe a critically ill patient wear-
ing the gown that you processed, while lying on the bedding that you handled, in the room that was cleaned using the microfibers that you processed and delivered earlier.
“Laundry workers that witness the criticality of their work in patient safety are much more likely to view their work as a higher calling rather than just a job. Give them this opportunity by taking them to see their work in action.”
Regularly train laundry employees on the highest standards for infection prevention, Gicewicz recommends. Important topics in this training should include bloodborne pathogens, personal protective equipment (PPE), linen inspecting, wash chemistry, cart cleaning, cart protecting, environmental cleaning, environmental testing, safe linen handling and more.
He also recommends testing employees on the training, having them date and sign the training, and retaining the training records.
“The entire laundry process should be trained, hazards for employees (personal protection) and recontamination of laundry (product protection),” adds Mechel. “Not only the laundry staff but also the cleaning staff and service drivers are to be trained.”
Laundry operators must realize that opportunities for HCT contamination can occur anywhere in the process and must be diligently guarded against, cautions Gicewicz.
“Producing hygienically clean HCT requires much more than a good wash process,” he says. “Getting HCT cleaned in the wash is a complicated process requiring precision. Keeping them clean until point of use can be even more challenging.”
Gicewicz recommends laundries look for opportunities for contamination after the wash process and mitigate all of them. It only takes one contamination occurrence to result in an infection. Trace the entire journey from dryers to conveyers, to tubs, to finishing equipment, to employee hands, to linen carts, to delivery vehicles, to loading docks, to linen rooms, to linen closets, to patient rooms.
“Factor in environmental factors along the journey, including air humidity, air temperature and air cleanliness,” he adds. “Remember, bacteria thrive in moist, warm environments. Wet HCT, even in dry environments, can become contaminated. Hot textiles that are covered will cause condensation when cooled. Test for contamination in all areas on the journey and protect clean HCT at all times from contamination.”
Ricci adds that addressing laundry sanitation concerns is not exclusively a healthcare issue.
“While more than 150 laundries have earned the Hygienically Clean Healthcare certification, another nearly 100 have achieved the Hygienically Clean designations for food safety, food service and hospitality,” he shares. “Food manufacturers are especially concerned about laundries’ use of HACCP, including solid surface (ATP) testing at CCPs, to ensure risk is minimized at each.
“As more laundries earn the food service and hospitality designations, more restaurants and hotels appreciate the value of further risk reduction in laundry even when this risk is tiny.
“For all customers, but moreso for healthcare facilities and especially hospitals, laundries’ concern for producing hygienically clean textiles should extend to how these end users handle these items so they remain clean when customers begin to use them.”
The key is for operations to stay up to date on laundry sanitation issues, constantly evaluate their plants and products (both internally and via third-party testing), and, finally, to be vigilant about communication and training.
“Ensuring proper cleanliness includes hygiene training of employees, keeping order, cleaning and hygiene plans,” shares Mechel. “Also, separation of clean and dirty laundry areas, locks for transport and people between the zones, no crossing of materials and staff routes (employees should not commute between zones), and provision of disinfectants in dispensers at places in the plant where the employee really needs them.” ALN
Cultivate your existing ironer’s production and quality by adding a Girbau Industrial spreader/feeder to your current ironing system. Our series of feeders improve product quality, enhance labor efficiencies and increase production in laundries. Keep pace and grow your laundry with Girbau Industrial. Nurture your growth – one piece at a time – with an investment sure to reap healthy dividends.
Discover how Girbau Industrial works seamlessly with your existing equipment. Call 800-256-1073. We have equipment in inventory and ready for installation.
CHICAGO — For David Balliet, senior director, customer relations, for Hospital Central Services Cooperative Inc. (HCSC) in Allentown, Pennsylvania, linen committees bring awareness to a commodity that may not be obvious to those who manage linen or work in the healthcare industry.
“There are things that hospital employees do with linen every single day, and they may not even realize that their actions could actually be linen abuse and are contributing to unnecessary replacements due to linen loss and damage,” he says. “Patient linen is to be used for patient care only; it’s as simple as that.”
Linen committees, Balliet continues, are also the forum to help develop an education and communication plan that can be impactful in controlling linen loss and abuse.
“Linen is often taken for granted, and as long as nursing has the right products, in the right quantity, at the right time, and of good quality, it can often be an afterthought,” he points out. “Hospital employees don’t always realize the importance of how they utilize this valuable commodity, and the impact and role that they have on the quality and longevity of the hospital linen.”
“An effective linen committee serves as a conduit connecting the laundry and linen services with the customer or end-user,” says Linda Fairbanks, executive director for the Association for Linen Management (ALM). “An active linen committee creates win-win for both the laundry and the hospital and drives success as it controls costs and improves efficiencies for both sides.”
Balliet says two types of policies or guidelines should be revised or adopted in the initial states of a hospital’s linen committee.
The first guideline to establish is a bed change/linen usage policy.
“Within the bed change guidelines, the committee will not only look at what linen items will be used on the patient admission/ discharge beds, but also establish the frequency, and what specific items will be changed on the bed and patient,” explains Balliet. “The communication method to patients and family members must also be created through the linen committee after those guidelines are established.”
Other procedures he recommends be included in this guideline are external patient transports (to control linen utilization and loss through EMS) and rejected linen, so a facility knows what to do with pieces of linen that are not deemed acceptable for patient care.
“The second policy that the committee must adopt would be a scrub suit or employee-wearing apparel policy,” shares Balliet. “It is very important to revise or create this policy, as it has an impact on infection prevention as well as scrub utilization/cost and loss.”
Fairbanks adds, “Developing a policy is only the beginning of a process improvement approach that would measure the effectiveness of the policy toward achieving the goals, analyze the outcomes compared to the predictions and make changes as needed.”
Monitoring fiscal, regulatory, infection prevention and patient satisfaction data will aid greatly to identify potential policy needs, she says. Utilization data, such as pounds per adjusted patient day (PPAD) and loss rates that are outside of industry norms will indicate need for change.
“The committee should analyze each policy consideration with the following three questions: What will the policy accomplish, what will it cost, and will it consistently produce the desired outcomes?” shares Fairbanks.
Before policies/guidelines can be created, the linen com-
mittee needs to be formed. But who should be on the committee? Balliet recommends including several key members, such as the linen manager or supervisor, environmental services management, infection prevention, CFO or executive director of finance, security, clinical resource director, and end users and transport services.
Other key committee members include public relations and education department members— plus the linen provider.
When a healthcare facility’s linen committee first starts, Balliet recommends that it meet on a monthly basis.
“The first meeting should be a kick-off meeting in which the goals of the committee are determined,” he says. “After the kickoff meeting, they should meet on a monthly basis until all policies/ guidelines have been completed.”
After that, the committee can reduce the frequency of the meetings to every other month and then eventually meet once every quarter.
Education and communication are key when it’s time to train and enforce the guidelines and policies to the hospital employees, says Balliet. There are many ways this can be accomplished.
“Linen awareness day in-services are probably one of the more popular and effective ways to educate hospital staff,” he shares.
“The in-services can be done in many ways, including ‘taking the show on the road,’ where the nursing staff can be gathered within their own department for a brief five- to seven-minute in-service using a trifold poster board and eight to nine different talking points.”
These talking points can include proper blanket usage, procedure for rejecting linen, linen abuse including employee actions that may damage linen, excess linen and patient rooms, proper gown wearing, discharge bed make up, linen loss through EMS transports, and loss by throwing linen in the trash.
“Learning is a repetitive process and reminders of policy/practice are effective at the point and time of use,” Fairbanks says. “Utilizing visual cues, posters, and reminders near the linen products point of use are an excellent approach.
Including linen utilization practices and policies in hospital new employee orientation can help to set the stage for proper linen practices that may differ from their previous employers.
“Including instruction on linen
utilization, avoiding linen abuses, and adherence to facility policies in annual employee training programs will help keep linen practice on their mind.”
By having the laundry service provider partnering with the hospital, Balliet says both entities will have a better understanding of the effect each other has on the hospital’s linen program.
“The linen provider is the resource expert to help the committee work toward their goals, and also has product knowledge,” he points out. “The facility and the linen provider both feel the crunch of linen loss and abuse. If the hospital can become more efficient with their use of linen, the laundry provider will also become more efficient.”
Balliet believes it’s important for all linen committee members to have a “homework assignment” to stay engaged between meetings.
“Effective laundry managers note that if a committee approach is utilized, it is important to have staff that are engaged and not assigned,” adds Fairbanks. “If they are only there because a manager instructed them to be there, the committee will fail.” ALN
Results on whites are excellent. On colors, you have nothing more to lose and everything to gain by trying YellowGo. YellowGo may take out color you want to keep. But if it removes the unwanted dye without damaging the underlying color, you win! You won’t have to pay for the dye-stained garments and you won’t disappoint your customers.
So use YellowGo to keep your customers happy and keep them coming back.
ebrated and individual employees understand they are contributing to the success of the business as a whole rather than just being siloed into a narrow role.
As we all know, first impressions last and the onboarding process is critical in setting the stage for successful employment.
those attributes, we find retention lengthens.
to accomplish this goal.
when we meet.
A company’s success is dependent on the engagement of its employees. First and foremost, it is important to hire based on company fit and character, rather than a specific set of skills tailored for a particular job description.
Unlike work ethic and integrity, particularized knowledge or experience can and will be developed over time. A company culture that emphasizes teamwork, cross training and flexibility will also promote a sense of camaraderie among employees and encourage people to remain on the team.
For managerial positions, we rarely recruit using traditional job postings and prefer to either promote people within our organization or draw upon our existing network.
People are the lifeblood of an organization, and it’s helpful to always keep an eye out for the right people to join the team, even if there is not a specific job opening.
For example, one of our key team members was hired over 15 years ago when we weren’t actively looking to fill a particular role. We recognized that this individual’s character would be invaluable to our organization, and he now operates our primary distribution center and is instrumental to the success of our business.
Empowering employees and soliciting feedback also promotes employee retention, as well as improving overall business performance. For us, this has been particularly important among our factory operators and warehouse staff. Not only does this help upper management to recognize and correct potential inefficiencies, this also increases employee engagement, and staff has an opportunity to see their recommendations put into action.
It’s also important to foster a team-oriented work environment where accomplishments are cel-
This starts during the interview process where it is important for employers to be transparent about the duties and responsibilities of the job you are hiring for. It doesn’t do anyone any favors to hide the ball during the interview process only to lose a new employee down the road after you have spent six months or more investing in them.
It is also important to include both supervisors and potential co-workers in the interview process. The more future colleagues a candidate meets, the more prepared they will be to walk in on day one confident with their decision to join the company.
Once a new team member joins the company, set specific goals and targets during the first six months of employment and maintain an open-door policy where new employees feel comfortable coming to their supervisors with questions or concerns.
We also have flat management and an open-door policy. People have to feel that they can go to someone in the organization who is truly listening to them and valuing them. If they bring something up and it is ignored, you will probably not hear from them again until they tell you they are leaving. This goes for both complaints and ideas. It is critical to listen to all ideas.
Achievements, no matter how trivial you think they are, need to be recognized. Maybe not in a big way (though big ideas deserve big recognition), but in a personal way. Treat people how you want to be treated. We all need to work on this!
Onboarding is very important, naturally. Having a clear path, especially in the first 90 days, is critical. Setting clear milestones and expectations helps everyone.
All the above being said, it is especially challenging in the current economy. We all as managers and employers have to challenge ourselves to move people to new roles, new skillsets and new opportunities.
On a direct personal level, I try to constantly let my employees know that I appreciate and recognize their effort and contribution. What I found to be very powerful is taking the time to go out to their work area to thank them. Some other good practices include teambuilding events, luncheons and personally signed birthday cards, along with a gift.
Employee development and advancement opportunities are key. We have a very strong culture of advancing and promoting from within. Our employees know that if they excel, they have a lot of upside opportunity. We also do our best to accommodate our employees’ schedules and personal needs. They know that we care about them on a personal level.
When onboarding new employees, the most important thing is communication. They need to have a very clear picture of what the job is, how we operate, our culture and expectation. It is also imperative that they understand that we welcome questions and want their input.
Using a buddy system for new hires is very effective. It allows them to share more and ask questions they may not be comfortable asking a supervisor. Having regular check-ins with new employees goes along way and can sometimes be the deciding factor whether an employee makes it.
This should come as no surprise when we consider the United States’ record-low unemployment, increasing minimum wage, transgenerational workplace issues, and the time and expense required for industryspecific training, especially for managers and engineering/ maintenance personnel.
Employee retention begins with company culture, and culture is driven from the top. As an owner or senior manager, you already know that leadership does not mean ruling by fear and intimidation, but rather fostering a company culture that demonstrates to employees at all levels that they are valued, appreciated and that their opinions matter.
Some of the most successful and profitable companies in the world subscribe to the philosophy of Lean Management, one of whose core concepts is listening to employees and valuing their input. By doing so, you demonstrate to employees that while payroll may be your biggest line item expense on the P&L, they are the biggest and most important asset your firm has.
These values should also be reflected in your company’s mission and vision statements.
Employee retention, especially in this almost full employment atmosphere, is critical as everyone knows. At Ellis and Ludell (our sister company) we view retention as a reflection of our culture. If you have the right culture, it can go a long way toward retention.
We consciously work on this by hiring people that fit into our culture. We do this by having prospects take a test that looks specifically at the attributes we find most important: Commitment (to us and our customers), Continuous Improvement and Integrity (do things right, do the right thing). When people are aligned with
F
irst and foremost, your compensation package must be competitive. Every single employee needs to know that they are being paid appropriately for their work.
Assuming that is the case, you need to recognize that in the current market, you need to make sure that your employees have a very good reason to stay with you and not be actively seeking or even flirting with the idea of leaving.
Employees will typically stay at a job when they feel appreciated, are connected to the people they work with and have a sense of purpose. To achieve this, we need to constantly strategize on methods to maintain this level of connection. We incorporated a whole bunch of initiatives and practices
In general, the better human connection you maintain with your employees, the happier they will be, their performance will show it, and they will stay with you long term.
Going hand-in-hand with subjective cultural messaging are tangible and objective demonstrations of employee worth through the provision of value benefits and amenities.
Employees and prospective employees have come to expect certain traditional benefits, such as paid time off and health/ dental insurance, but in a competitive hiring environment, it behooves you to consider what other amenities and non-traditional benefits can be offered to attract and retain talent.
Employee retention and engagement are two of the hottest topics in our industry, as evidenced, empirically, by the amount of time these topics are given at industry events and conferences, and anecdotally by the amount of time our clients spend discussing these topics
One example that seems to come up in every discussion of plant design or renovation is ownership/management’s desire to provide their employees with larger, more functional, and, yes, more welcoming breakrooms, locker rooms, and restroom facilities.
In addition to these sorts
“Which activities or methods do you recommend to enhance employee retention? How do you onboard new employees to get the retention effort started effectively?”
B&C Technologies, which focuses on an engineering-driven design to manufacture laundry equipment says its line of large-capacity washers have been proven in the field to offer long life and dependability.
Available in capacities that range from 110 pounds to 475 pounds, these machines utilize a simple design that saves money by keeping repair costs and downtime to a minimum while allowing for easy maintenance, the company says.
The machines also have the allnew, flexible FM7 control that’s Bluetooth compatible and now uses the Washtools Android app for easy programming.
The company says the highextract speed of this soft-mount line ensures less dry time for goods, saving on utility costs and wear and tear on the goods.
All B&C washers feature a solid foundation, a large door opening for easier loading and unloading, and a strong door and hinge system made of 304 stainless steel.
www.bandctech.com 850-249-2222
from manual, semi-automatic, to fully-automatic performance; and in free-standing, system or hygienic pass-through applications.
The company says its design has proven itself with more than 2,000 installations worldwide. While Game Changers are designed around open-pocket wash technology, that’s where the similarities to other typical openpocket machines stop, VEGA says.
Due to its design, Game Changers use approximately 50% less water and 40% less electricity than other washer-extractors, the company says.
A patented balancing system automatically adjusts to any load size. The built-in automatic scale system takes the guesswork out of actual load sizes and accompanying formulas, and operates using true Real Time Ratio Wash.
The result of the Game Changer design minimizes resource consumption and maximizes production throughput and flexibility, according to the company.
www.vegasystems-group.com 855-834-2797
washers and features superior mechanical action like its open pocket washer-extractors.
The company points out that the Advantage® features a patented door locking mechanism and system. Other features include a door switch that communicates positive feedback to the controls, proving the door is completely locked. The machine will not move on to the next step until the door lock has been fully engaged.
Precise encoder and proprietary algorithms are utilized in hydraulic positioning to reduce time to below one minute once reaching low speed. No pin is needed to jam to stop and position the cylinder, Braun says. Inverter and brake are used to precisely position each and every time.
An automated step provides improved ergonomics and alleviates back strain. The company says the wide and large step with a non-skid surface gives operators a very stable platform for loading.
Direct drive vs. sheaves and belts minimizes maintenance. Braun says the washer-extractor has standard high-extract speed functionality.
End-of-stroke tilt limiter stops the machine from tipping forward if the tilt cylinders were to fail when it is tilted forward over center. The no-crush hazard keeps operators safe when the machine is tilting down from unloading, and it has standard fixed fenced safety guarding around three sides.
Lavatec Laundry Technology says the LX-series of large-capacity front-loading washer-extractors includes the Open Pocket LX425.
It features a computerized system with touch-screen management to give operators complete control over time and temperature, level, dosing, drum speed, reversing and cool-down aspects, the company says. An option allows it to be operated it as an automated system or manually where the operator just needs to adjust it to take control.
The washer’s value starts with its 160-pound capacity, perfect for a number of applications, according to the company.
UniMac also provides highperformance features, such as Optispray, an innovative highpressure spray rinse that removes more residual chemistry than bath rinses and speeds cycle times.
Add in superior water efficiency, a super-high 300 G-force final extract, four fast-fill water valves, and an ultra-rugged industrial frame and bearings, and UniMac says the UW160D4 has all the attributes to trim operating costs for years to come.
When equipped with the UniLinc Control and paired with the TotalVue system, UniMac says its UW160D4 gives managers the pinnacle of laundry management and delivers on its maximum performance in laundry promise.
TotalVue is a cloud-based management and reporting system that offers managers unparalleled visibility to laundry operations by monitoring more than 75 data points.
www.unimac.com 800-587-5458
VEGA Systems debuted its line of Game Changer washer-extractors to the U.S. market at the Clean Show last year, where the company continuously balanced a 100-pound block load of linen and extracted it at 400 G-force in a free-standing model GC500 500-pound capacity machine.
VEGA says its Game Changers are available in a variety of versions, from 100- to 1,200-pound load capacity; an operation range
G.A. Braun says its 900-pound Advantage Side Loader® is engineered with the same structural integrity and reliability of all its
A split-panel control box separates high-voltage from low-voltage components. Shell door and tilt functions require two-hand control meeting all ANSI standards for safe operations. Finally, Braun says the unit has exclusive Parker Hannifin hydraulics threeyear, leak-free warranty on Parker fittings and hoses.
www.gabraun.com 800-432-7286
The single inverter-controlled drive motor applies reserve power during wash and spin cycles for the lowest energy consumption at any speed. Thus, when combined with high extraction rates, costs can be lowered even more via reduced drying times, says Lavatec.
The company adds that the LX425 is now available with Lavatec’s Ride-On Shuttle, giving operators the ability to control washers, dryers and rail system from a safety-enabled technology cockpit.
Lavatec’s LX series also includes the LX445 (450 pounds) and LX460 (600 pounds).
www.lltusa.com 203-632-8777
UniMac says its UW160D4 washer-extractor offers a variety of features to help busy on-premises laundries increase throughput, as well as reduce operating costs in the process.
Brim Laundry Machinery says its 66/40 “slim” tilting washer-extractor has an open-pocket stainless steel cylinder (79.2 cu. ft. capacity), a two-way hydraulic tilt system, a single-motor variable speed drive (up to 300 G-force), a large automatic door (40-inch diameter), a touch-screen
Your table linens touch every Customer at every event. Your linen needs to speak their language… fresh, clean, safe, consistent, reliable, and yes elegant. They count on it.
Together, ADI and Milliken have set the standard of linen excellence for decades. USA made Signature Plus fabric. Soft luxurious hand, consistent long-lasting color. Whites that stay white, and colors that stay bright.
ADI American Dawn. The world’s leading supplier of Milliken Signature table linen products. Count on us.
Signature Plus is a registered trademark for Milliken & Company for fabrics.
color microprocessor control, and optional water re-use feature.
Brim adds that its washerextractors are now provided in a new “slim” footprint that minimizes space requirements, with no reduction in capacity. The company says, maximum productivity and quality are achieved with an end-loading open-pocket cylinder, which provides easy access as well as superior mechanical action during the washing process.
www.brimldry.com 214-630-4517
Pellerin Milnor says its industrial M-Series washer-extractor line features fully automated, semiautomated or manually loaded
machines. These large, openpocket washer-extractors include the 48080M7K (275-pound capacity, 42 cu. ft.), the 68036M5K (400-500pound capacity, 75.6 cu. ft.), and the 72046M5K (600-700pound capacity, 108.4 cu. ft.).
The company says the series comes standard with 21-degree, two-way tilting for efficient loading and unloading, intelligent bearing design, and open machine design for easy access and streamlined maintenance. The SmoothCoil™ suspension system allows for vibration dampening
ARTA’s next Education Conference is set for Feb. 26-28, 2020 at the Gaylord Palms Resort in Orlando. Planning is underway to deliver another excellent conference with education that helps your organization thrive and grow.
The conference will follow a Wednesday to Friday format. Wednesday afternoon will feature a plant tour, followed by a Welcome Reception hosted by MIP. Education sessions run all day Thursday and end at noon on Friday.
The room rate is $209 USD per night and is being offered three days before and after the conference for those members who wish to make the trip a vacation. Questions? Contact Nancy Jenkins at njenkins@ARTA1.com
and less wear and tear, promoting consistent vibration isolation, noise reduction, and a durable, long machine life.
Additionally, the intuitive MilTouch-EX™ control utilizes resistive touchscreen technology to display current machine status information and offers complete programming flexibility.
The M-Series washer-extractors also feature an optional integrated load chute door for semi- or fully automated washer-extractor systems, says Pellerin Milnor. A safety-rated light curtain for non-automated M-Series washers allows for safe visual inspection while operating. www.milnor.com 504-467-9591
EDRO says its industry-standard, 400-pound capacity three-pocket end loader washer-extractor, the DynaWash® DW400 Three Pocket End Loader, is now available in a low-profile design offering a 12-inch height reduction over its predecessor.
Built around EDRO’s patented “3-D” basket design, this battleship-quality machine utilizes a single motor variable speed drive with exclusive variable step extract timing for improved balancing and water extraction.
features include:
• DynaTrol HMI touch-screen control with multiple programming options, simple operator interface, and a full array of owner/supervisor productivity reporting.
• New positioning disc-brake system.
• Redesigned AutoIndex cylinder positioning.
• Reinforced inner doors.
• New chemical port manifold. The company says the control panel’s integrated ozone control allows full programmability of EDRO’s optional DynOzone ozone system as a further cleaning process benefit. Laundries that install the system report increased washroom productivity with more loads per day thanks to faster machine turnaround.
Utilizing Power Cell technology, DynOzone is the only spacesaving built-in ozone system that is housed completely within the machine’s footprint, according to EDRO. Because it cleans naturally, DynOzone requires fewer resources to attain high-quality
of amenities, and in a further effort to attract and retain employees, companies around the country are adding nontraditional benefits such as educational assistance (including on-site language and literacy courses), wellness benefits such as discounted or on-site fitness memberships, loyalty/longevity awards, employee referral bonuses, transportation assistance, secure indoor bike parking, discounted food and drinks, and more.
Understanding your employees and the impact of the above ideas on their performance, loyalty/longevity, and issues that could affect these important metrics is what “employee engagement” is all about.
Employee engagement is defined as the extent to which employees are willing to contribute their knowledge, skills, abilities, and effort to help an organization succeed, and is defined by how employees think, feel, and act.
Measuring and affecting employee engagement is made easier through the use of smartphone apps such as redeapp and Nudge Rewards.
Apps such as these provide a unified communication, motivation and optimization platform to allow measurement of employee feedback and insights, communication of work schedules, operational and safety videos, handbooks, and SOPs (standard operating procedures), instant and updated company news, sharing of best practices and ideas, and gamification to ensure continued use of and engagement with the system and, thereby, the company.
One of the eight wastes of Lean is the concept of Underutilized Human Resources. Simply stated this means that we need to ensure that we use our personnel in a way that allows them to fulfill their potential and that allows us to have the most success in our operations.
Attracting, hiring and training new personnel is an expensive and time-consuming process, so we must strive to find ways to ensure that once we have found the right personnel, we are able to retain them for as long as possible. Providing the right balance of culture, benefits and amenities, and engagement will go a long way toward achieving this goal.
O ne of the many benefits of living in our great country is the ability to change occupations at any time. Citizens are not stuck at any pay grade or job. There are always opportunities for employ-
ees at any level to move.
While this is a fantastic ideology for employees, it does put the burden on employers to make their companies as enticing as possible to recruit and keep as many good employees as needed.
Strategies used by companies to
slow turnover differ from department to department. The same incentives used to keep an hourly production employee greatly differ from what it would take to keep management in an organization. I will attempt to limit my suggestions to the hourly production employee.
The first key to keeping employees is to understand there will always be turnover. No matter how great our company is, an employee may not want to run sheets every day. That is not a knock on the employee or the company; it is just facts.
How you treat your current
employees and how satisfying you can make the job will affect how easily you can recruit new employees. Current or former employees are your biggest recruiters.
Working in a laundry can be a tough job. Any effort spent by an organization to improve the working environment can pay huge dividends. I try and use my “grandson” test. Would I want my grandson working in this environment? How would I want my grandson treated by his supervisor?
Following are a few methods we believe have helped our turnover:
1. Give detailed instructions of your expectations from the beginning. Remember, the first days that you are monitoring a new hire, they are also monitoring you to see if they want to be a part of your organization. Communicate hourly with these new hires. Don’t allow a new hire to be put out on an island or machine working by themselves. Whenever possible, put a supervisor or experienced employee with them for the first couple of weeks.
2. Safety. The laundry industry
•
•
results. This greatly reduces hot water requirements, while providing high-quality, low re-wash results for improved washroom efficiency.
www.edrocorp.com 860-828-0311
Girbau Industrial’s HS Series 130-, 190- and 255pound capacity washers feature durability, programmability, high-speed extract and a soft-mount design, according to the company.
Available in stationary and tilt models, for simple loading and unloading, the washers are ergonomically designed and easy to
Continued from Page 15
has long been considered a very dangerous place to work. Most laundries are going to great lengths to change this perception. If a plant looks and feels unsafe to a new hire, they will not feel comfortable staying and putting their health in danger, and worse they will tell their friends how unsafe your plant is.
3. Housekeeping. Keeping your plant clean and organized will help keep the job satisfying for employees. If an employee is forced to look for their reject bin or are struggling with clutter, they will not be satisfied
operate. Generating extract speeds of 387 G-force, up to four times greater than most hard-mount washers, HS Series Washers remove more water from each load, cutting dry time by up to 50%, according to the company.
HS Series Washers boost throughput, while lowering utility and labor costs. They also feature the highly flexible Inteli control,
offering 20 pre-programmed and 79 owner-programmable cycles. GI washer-extractors are backed by a 5/3-year factory warranty.
www.girbauindustrial.com 800-256-1073
JENSEN says its L-Tron, JBW and JWE series washer-extractors are designed for strength and durability, with decades of proven experience.
The L-Tron openpocket series is available in 450- and 800-pound capacities, the JBW splitpocket barrier washer series is available up to 510-pounds, and the JWE open-pocket series up to 250 pounds. All are soft-mount design
and can be used in stand-alone operation.
The L-Tron series can be part of a semi-automated or fully automated wash aisle, says JENSEN. In stand-alone operation, the L-Tron can be manually sling loaded or hand loaded. In semi-automated or fully automated operation, the L-Tron can be loaded via mono-
rail system, shuttle conveyor or stationary conveyor. The L-Tron can be outfitted with either a large door with an observation window or the AutoPro loading hopper. The company says its AutoPro design allows for fast loading times, as fast as one minute.
Standard design features for all series includes touch screen PLC controls, powerful single motor variable frequency drive with extract speeds up to 360 G-force and much more.
www.jensen-group.com 850-271-5959
with the job.
4. Show appreciation. Cookouts for employees is a low-cost, high-return way of showing appreciation. No burger tastes better than the one the boss cooked. We also regularly have doughnut Fridays. Popsicles or watermelon at break on a hot afternoon is always appreciated, too.
5. Communication. Employees need to know about any change that might affect their jobs, whether it’s an equipment issue upstream, process change or a potential new account. Employees have family responsibilities that frequently require them to get off at a set time, so let them know early if this time will change on that day.
6. Clear message. There is nothing more frustrating than
for several managers to give contradictory instructions to an hourly employee. Make sure all the management team is on the same page before anyone communicates with the employees.
Then, I realized we have experienced a generation shift within the company. Many of our new millennial employees have entirely different needs and goals than the existing employees. For that reason, it became apparent that I needed to build a company that has a culture for every generation.
all-company mandatory meeting every month. This gave employees an opportunity to interact, be heard and contribute to the growth of the company.
Additionally, I invited guest speakers to give my employees professional advice with the intent of improving their lives outside of work, the theme being, “what bothers you outside of work, bothers you inside of work.”
2
019 was an eye-opening and transformative year for Equipment International. Like many other multi-generational companies, we have been doing business in a similar way for many years.
Retention starts with understanding the perspective of all of your employees. While compensation may be most important to some employees, flexibility or growth within the company may be more important to others. If we understand what keeps employees engaged, enthusiastic and passionate, employee retention remains high.
Company culture was a central focus in 2019. To that end, we implemented several activities and methods. The first was an
Among these speakers was an expert on health, wellness and nutrition who touched on improved eating decisions and simple exercises you can do anywhere. We also brought in a wealth management expert who discussed personal budgets and ways to save money.
One of our most rewarding activities was a core values exer-
cise in which we uncovered five values that are most important to the entire company.
Another key implementation in 2019 was our company’s 401K plan. This was in response to several employees asking for some sort of investment vehicle. It gave me an opportunity to listen to what is important to the employees and respond accordingly.
As our culture began to shift, so did our approach to onboarding. We felt it was important for new employees to understand how things are done and what we are passionate about.
Preparing new hires with precisely what is expected from them is key to long-term success. We believe in extensive training of any new employee as part of the onboarding process. For employees in the technical field, that means spending time at the manufacturers’ facilities and riding with senior service technicians so they know how we interact with customers.
Helping new hires feel welcome within the company has been a shift in our perspective. Simply eating lunch together, discussing what is going on outside of work, and getting to know new hires personally has helped ease the anxiety of new hires and allowed them to immerse themselves into our company culture.
Finally, giving early feedback and making corrections is important. Understand employees want to do well, and effective constructive criticism helps them accomplish this.
2019 taught me that employee retention and onboarding both start with company culture. Finding out what is important to each employee, familiarizing myself with their needs, and being able to deliver has dramatically improved company culture, which has had a terrific, positive effect on retention.
When onboarding a new employee, setting clear expectations about how things are done and allowing them to grow within the company culture has led to great success.
their guidance counselors, family members and media, fearful of downsizing, automation and off-shoring.
In many cases, firms like ours are managed by long-tenured managers well over 50 and in some cases even more than 70 years old. We have a “missing generation” of 30- and 40somethings who never considered a career in our industries.
Here is the opportunity I lay out for the “Gen Z” 20-somethings I recruit to our firm: dedicated training, educational support and a clear path to rapid advancement in our orga-
nization.
We start with internship programs with local universities and even high schools to find students motivated to work and learn. Many have never considered old industries a viable career path, and many have digital skills we need to understand to modernize our operations.
We let them know we need “young brains” to match up with our experience. We take their suggestions and ideas seriously and integrate them into our operations as quickly as we can. Nothing binds people to an organization more than mak-
ing a positive impact and seeing your ideas taken seriously.
We deliberately seek diversity to re-invigorate our workforce with new talents and perspectives.
We also invest in their training and education. For years, companies cut back on the support given to employees seeking more education and training, expecting them to pay for these expensive investments by themselves. Is it any surprise when employees who took on their own debt to pay for education leave for higher paying jobs elsewhere at their earliest opportunity?
By offering educational support and flexible schedules to employees seeking degrees, we try to make loyalty the two-way street it was when we started our careers.
Foremost, we offer a path to the future for both them and our organization. People are going to use and wash linens and uniforms moving forward. In a sustainable future, there will be fewer disposable items. If they bring their modern talents to us, they should move rapidly into upper management, and they and our organizations will thrive.
A ttracting and retaining top employee talent to “old industry” firms is a continuous challenge for companies like ours and for industrial laundries as well.
It’s safe to say no almost one under 50 grew up dreaming of working in a hot, noisy industrial building. Multiple generations now have been advised to steer away from firms like ours when they plot their career paths by
Field Service Technicians –G. A. Braun, Inc.
Due to the growth of our business, G. A. Braun is seeking Field Service Technicians so we may continue to provide exceptional support to our clients. Braun technicians will install, and repair equipment that is both new and preexisting at the customer site. Other responsibilities include customer training so they may efficiently operate and maintain their Braun equipment.
Required qualifications include but are not limited to; electrical/electronic and mechanical knowledge, hydraulic and pneumatic systems equipment and components. Candidates must be computer literate in Microsoft Office and be capable to lift/move up to 100 pounds.
The Braun Field Service position also requires extensive travel.
Benefits include a competitive salary, 401K plan, medical, dental, vision, disability, and life insurance benefits in addition to paid vacation and personal time.
For a challenging and rewarding career opportunity as a G. A. Braun Field Service Technician, please inquire at sbortoloni@gabraun.com.
Pellerin Milnor Corp. P.O. Box 400, Kenner, LA 70063 504-467-9591, Fax: 504-468-3094 www.milnor.com
Pellerin Milnor Corp. P.O. Box 400, Kenner, LA 70063 504-467-9591, Fax: 504-468-3094 www.milnor.com
Pellerin Milnor Corp.
P.O. Box 400, Kenner, LA 70063 504-467-9591, Fax: 504-468-3094 www.milnor.com
Pellerin Milnor Corp.
P.O. Box 400, Kenner, LA 70063 504-467-9591, Fax: 504-468-3094 www.milnor.com
Sea-lion Co.
JIANGSU, China — Laundry equipment manufacturer Jiangsu Sea-Lion Machinery Co. Ltd. reports it recently held a 50th anniversary celebration here, highlighted by the completion of its new office building complex.
Sea-lion Chairman Chen Hong says that in order to coordinate with the planning and construction of local government, taking into consideration with the overall situation, Sea-lion has made a two-stage relocation since 2014.
The sales center, testing center, and administration and logistics department at the original headquarters have been all moved to the new production campus. The construction and decoration of the new modern office building complex has also been recently completed.
“This new office building, with advanced and complete facilities, is not only a new local landmark, but also sets up a new image of Sea-lion production campus, furthermore, a beautiful scenery of city construction in Leyu Town,” shares Hong.
chased Open Access for this article, which means everyone can easily download and read the study,” says ARTA Past President Brendan O’Neill of London Hospital Linen Service, London, Ontario.
O’Neill adds that this is an important study to share with healthcare clients. He also shares that ARTA will begin work on a follow-up study in 2020.
The published study was funded by ARTA and conducted with assistance from Accuratus Lab. ARTA wishes to thank the authors of the study: Kevin McLaren and Steve Tinker, Gurtler Industries; Ed McCauley, UHS; Brendan O’Neill, London Hospital Textile Service; and Lynne Sehulster, Ph.D., Environmental Infection Prevention LLC.
Nancy Jenkins, executive director of ARTA, served as project manager for the study.
GARLAND, Texas — Three laundry equipment providers in the North, Central and South Texas markets—
AAdvantage Laundry Systems, Scott Equipment and Skyline Equipment—report they recently joined forces to provide commercial and industrial machines to their customers.
As major distributors of Continental Girbau, Dexter Laundry and B&C Technologies laundry equipment, the three companies say they continue to provide innovative solutions while improving how local customers do laundry.
Skyline Equipment offer laundry equipment in Texas, Louisiana, Oklahoma, Arkansas, North Carolina, South Carolina and Virginia.
MIAMI — Commercial laundry and drycleaning equipment distributor EVI Industries reports that it has executed a definitive purchase agreement to acquire all of the outstanding shares of Sevierville, Tennessee-based Laundry Systems of Tennessee and affiliates.
Laundry Systems of Tennessee is a distributor of commercial, industrial and vended laundry products and a provider of related installation and maintenance services to the new and replacement markets of the commercial laundry industry. The company also leases commercial laundry equipment and sells chemicals and other laundry consumables.
Terms of the acquisition were not disclosed, but the purchase includes a combination of cash and EVI common stock.
The acquisition expands EVI’s sales and service presence in the Southeast, which coincides with its strategy to build density in geographic markets to improve customer service and through which it may pursue new growth opportunities.
Laundry Systems of Tennessee will operate under its existing name and remain under the direction of President Jeff Large and Vice President Tonja Large.
“We are honored to join the Large family and their team at Laundry Systems of Tennessee,” says Henry M. Nahmad, EVI chairman and CEO. “Jeff and Tonya are successful entrepreneurs with a continued passion and commitment to growth. We are excited to collaborate with them and their team in the pursuit of our mutual long-term growth goals.”
“We will take the opportunity of the grand opening of the new office building and 50th anniversary celebration to strengthen our service, efficiency and quality. Completion of office building is the end of construction project, but it is also a new start of our business.”
He goes on to say that the past 50 years is “a journey of business development paved with hard work of all Sea-lion employees, and it is also a lifetime glory to all Sea-lion employees.”
Also in celebration of its 50 years in business and everexpanding market presence, Sea-lion Company launched Sea-lion America Co. at the Clean Show in June. This is a joint venture designed to support the company in the North American, Mexican and Caribbean markets.
MISSION, Kan. — The American Reusable Textile Association (ARTA) reports that its study on the effectiveness of per acetic acid (PAA) to kill Clostridioides difficile (C. diff) spores has been published in the American Journal of Infection Control (AJIC) and is now available for download.
ARTA purchased Open Access download rights for the study, “The efficacy of a simulated tunnel washer process on removal and destruction of Clostridioides difficile spores from healthcare textiles,” which means the public is able to access this study at: www.sciencedirect.com/science/ article/pii/S0196655319304638.
AJIC is a peer-reviewed scientific journal produced by the Association for Prevention and Infection Control and Epidemiology (APIC).
“The ability to kill C. diff in healthcare textiles is critical for professional laundries, and ARTA has therefore pur-
AAdvantage Laundry Systems, Scott Equipment and Skyline Equipment, which have been serving the local community for more than 45 years, offer laundry solutions to meet commercial laundry needs that include hotels, spas, salons, hospitals, nursing homes, assisted living centers, correctional and athletic facilities, and Laundromats.
In 2018, the three distributors were acquired by EVI Industries, the largest distributor of commercial laundry and drycleaning equipment, industrial boilers, supplies and technical services.
AAdvantage Laundry Systems, Scott Equipment and
The transaction is expected to close upon satisfaction of closing conditions.
Since November 2016, EVI has acquired 12 businesses. It considers itself “the fastest growing company in the commercial laundry industry,” with a four-year compounded annual growth rate for revenue of over 70%.
“We remain very active in our pursuit of additional acquisitions of and strategic investments in other great businesses in our industry and in those industries that meet our financial and strategic criteria,” Nahmad says. “Given our record, reputation and appetite for significant growth, we believe EVI is well positioned to capitalize on a growing number of opportunities.
Info:
Conference Washington, D.C. Info: 703-519-0029
Batch Tunnel System Spring Service Seminar Panama City, Fla. Info: 850-248-4115
celebrates 50th, opens
AAdvantage Laundry Systems joins forces with Scott Equipment, Skyline Equipment
We carry a full line of Laundry bar mops. Custom colors, weights, and private labeling are available with minimums.
Spun poly napkins perform consistently over time, are wrinkle-free, and are less likely to stain. Custom colors available. 20” x 20” - Packed 25 dozen/case.
Our restaurant linen lines are woven from spun polyester and benefit from being stain resistant, colorfast, and wrinkle-free. Linens are packaged in manageable carton sizes for laundries, and are Internet-ready packs for retail sales opportunities.
Packed four 6 packs/case
These bar mops are perfect for wipe-and-toss in heavily soiled environments. Minor weaving defects such as over-stitching or imperfect cuts reject perfectly good bar mops from circulation. We buy these at a deep discount and pass the savings on to you. Packed: 100 doz/bale.
When bar mop production runs are over and inspections have been completed, mills may still have excess yarn. Run Of Mill (ROM) bar mops contain every bar mop that comes off the loom after the first quality run has been finalized, so are more economical than Grade A1 bar mops.
Spun poly bistro napkins are quickly becoming a staple of restaurants who would like to add a little sophistication to their ambiance. 18” x 22”
Packed 25 dozen/case.
Route Ready bar mops are optically white and packed in bags of 25 so you never have to pre-wash or recount them prior to use. Typically, laundries save 70¢/doz by freeing washroom and finishing floor operators from a wash cycle, you gain production time to focus on other laundry room bottlenecks. STARTING
Color Price
Part Number
TL-42X42-WHITE White $25.75
TL-52X52-WHITE White $40.50
TL-62X62-WHITE White $51.00
TL-72X72-WHITE White $82.25
TL-85X85-WHITE White $106.75
TL-52X114-WHITE White $80.50
TL-42X42-BLACK Black $25.75
TL-52X52-BLACK Black $40.50
TL-62X62-BLACK Black $51.00
TL-72X72-BLACK Black $82.25 TL-85X85-BLACK Black $106.75 TL-52X114-BLACK Black $80.50