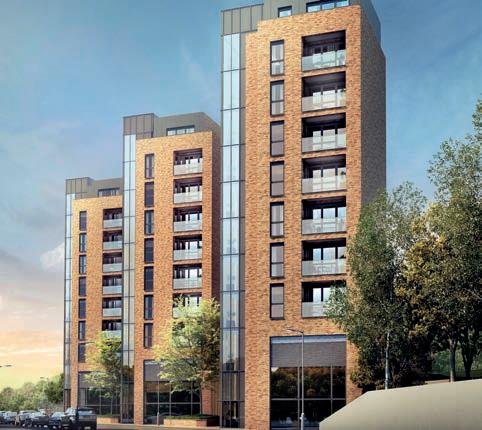
4 minute read
Project Focus
from ECN July 2021
POWERING UP A PRESTIGIOUS HIGH-RISE DEVELOPMENT
Linton Fuels is a new mixed-use development comprising two tower blocks with 109 homes and retail space. Situated close to the River Thames in Wandsworth, South West London, this project is another example of the booming high-rise construction trend currently taking cities across the UK by storm.
Advertisement
To provide electricity to the high-rise towers, the consultant for the project, MCA Consulting Engineers (MCA), and M&E contractors from Box and Charnock required a solution that would deliver on performance quality in line with the rest of the development. However, it also needed to be quick to install and commission, given the demand for developments of this kind to be completed by the end of March 2021.
Connecting the blocks
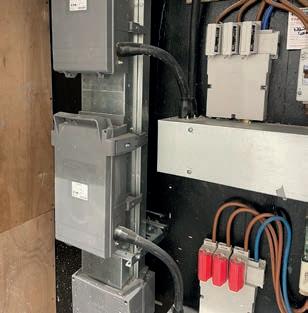
For the electrical installation, one of the main challenges was how to connect the two main high-rise tower blocks to the mains electricity supply. The entire development was to be supplied from the basement plant room for Block A and, as such, busbars were to be installed across an open car park between the buildings, as well as in the risers.
“Given the difficulty posed by installing across the car park, we specified Zucchini MR Busbars from Legrand as a more practical option for this type of installation,” said Michael White, Production Manager at MCA. “It reduced the large number of sub-mains required for the electrical installation within the risers and across the car park, so naturally it was the most practical choice to overcome this challenge.”
In this type of installation – where mains supply derives from one location –busbars can facilitate the easy addition or upgrading of circuits from a tap-off point. This means a new circuit installation would not require a sub-main to be run back to the mains source, saving time and potential disruption later on in the building’s life.
Because of this more complex configuration of busbar installation, standard runs of three metres would not be sufficient and so bespoke components were required. T-shaped elements, for example, were required to connect the horizontal car park runs to the vertical riser runs in Block B, as well as shorter busbar parts to fit the development’s exact measurements.
“Many projects require a bespoke element when it comes to installation, however, it can hold up proceedings if they take a while to be supplied,” said Danny Baldwin, Project Manager at Box and Charnock. “A Legrand engineer came to site very promptly and took the measurements to get our equipment ordered. Despite being required during a time where the pandemic was greatly affecting supply chains, the materials arrived quickly and we were able to get them installed without any issues.”
Space considerations
In any high-rise residential development, building services must occupy minimal space to afford more for apartments. As such, the selected system needed to occupy as little room as possible in the riser areas, as well as deliver on flexibility in the confined space.
In the smaller Block A, the busbar centre feed unit’s positioning within the riser was not accessible within the dimensions of the space if mounted on the back wall, as designed. This meant Box and Charnock had to change the busbar position to ensure there was sufficient access to the unit.
“Within the riser dimensions, fortunately the space was deep enough to house the tap-offs, and mount the solution on the left wall instead of the back as we did for the other block,” said Danny. “There was minimal disruption thanks to the flexibility the busbars provide. It was possibly even easier than the Block B, given we didn’t need to install the supplementary strutting to offset the mounting of the equipment to pass the brackets for the GRP grate floor panels.”
In a further effort to maximise living space available, the plug-in distribution boards were also selected thanks to their size. Michael White explains, “The plug-in boards were a simple and space saving alternative to others available on the market. On top of this, other options would have required tap-offs and sub-main links which are tricky to install neatly with a confined space. The full solution from Legrand was a much better system, thanks to its size and integration with all of the building services areas across the development.”
Thames South Wimpey Taylor Credit:
Quick installation and commissioning
For any contractors and consultants working on high-rise developments, ensuring electrical installations are quick and easy is key when there is pressure to complete projects. The specified busbars along with the compatible plug-in distribution boards provided Danny and his team with a quick-to-fit solution to overcome this.
“Even with challenges posed by the car park installation and limited riser space, the system was simple to fit,” said Danny. “On top of this, we discovered no issues during the commissioning phase, while no equipment needed to be replaced. On a large project such as this, replacements can be time consuming and costly, particularly if other aspects need to be removed to access the services. Having a high-quality busbar and plug-in distribution board system like the Legrand solution gives peace of mind to contractors that replacements will not be required after testing.”
With the London construction market booming, Paul Martin, Lead Marketing Manager for Legrand’s Power Distribution division, said, “We want to support consultants and contractors who are coming under pressure to deliver projects to satisfy growing demand in cities like London. Linton Fuels represents a project where our busbar and plug-in distribution boards can overcome challenges in the design stage as well as during construction.”
Linton Fuels is a new mixed-use development comprising two tower blocks with 109 homes and retail space
FIRE, SAFETY & SECURITY
supported by
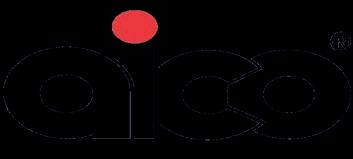
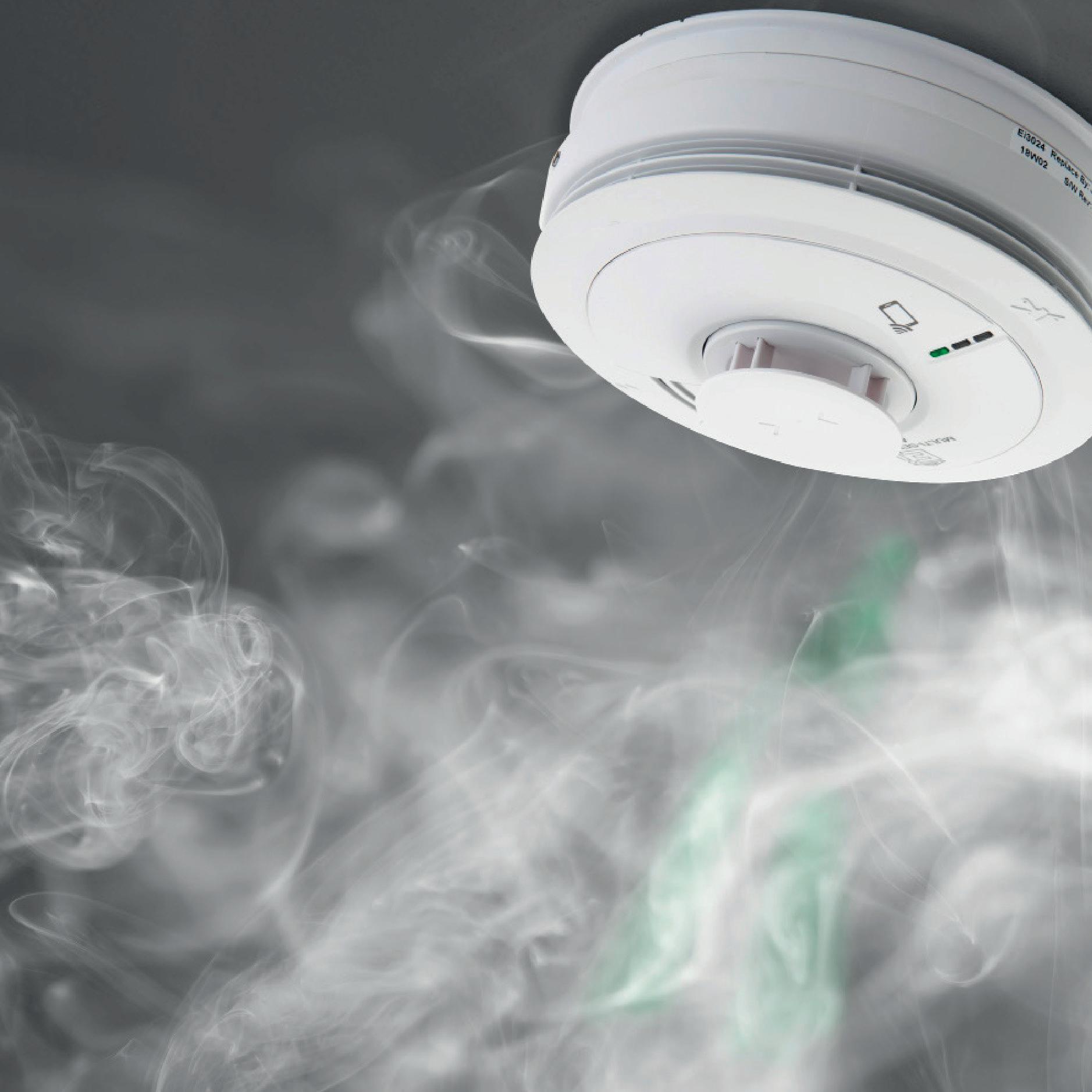