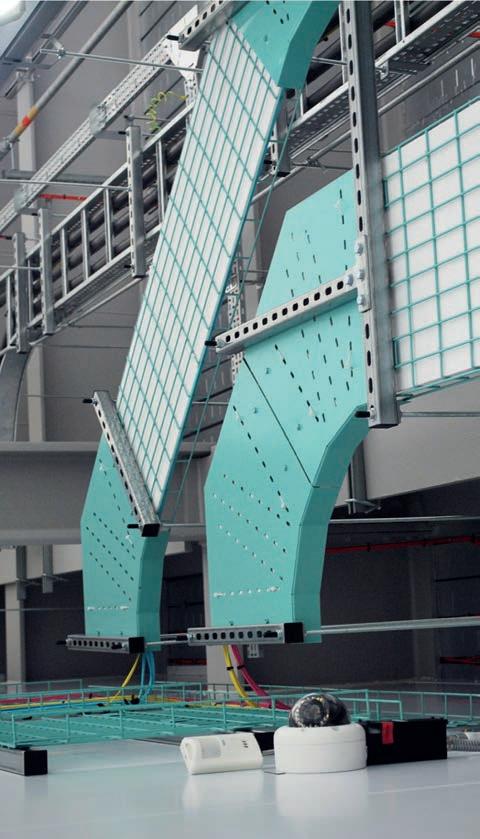
3 minute read
How modular prefabrication can help electrical contractors tackle construction challenges
As pressure grows on the construction industry to build faster and more efficiently, Peter Willsher, Managing Director of RMS Cable Management Systems, discusses the benefits of modular containment solutions for electrical contractors and their clients.
The construction industry, and the delivery of projects large and small, are being shaped by a vast range of factors. Brexit and the pandemic have intensified labour and product shortages. Cost certainty is becoming much harder to achieve, and the ever-increasing focus on health and safety is shifting construction methods, including reducing hot works on site.
Advertisement
Against this challenging backdrop, there continues to be an intense pressure on the industry to build faster and more efficiently, while maintaining the highest quality standards.
To address these issues, the construction industry and its supply chain is quickly adapting to change. This is fuelling the demand for off-site manufacturing, including prefabricated solutions for building services. Containment modules and risers that are designed and manufactured off site can generate significant benefits. From Unistrut brackets through to fully populated frames, there are many solutions available which can save costs, time, waste and labour, and offer installers known embodied carbon content.
Boosting quality and efficiency
Regardless of the type or size of the modular containment system, it will be manufactured under strict factory-controlled conditions, ensuring consistent quality.
Larger modular systems will also save significant man-hours on site, boosting the productivity of the wider construction programme. For example, RMS Cable Management is currently manufacturing 700 prefabricated risers for a project in London. These have been designed to distribute the power, fire and building management systems for a prestigious commercial and retail development. Fabricated by the company’s specialist, in-house coded welding team and transported direct to the building, the assembled risers will save more than 10,000 onsite manhours.
The welding part of the process generates a further benefit. Compared to using traditional bolted brackets, which reduce the workspace volume and width load, welding creates up to 40% more capacity for the cable management in the frames.
For another client, the company manufactured prefabricated cassettes for containment, which were then stacked in towers of 13 before being transported to site. This enabled the equipment to be installed five times quicker than traditional methods.
Reducing environmental impact
The government’s net zero targets are shining a greater spotlight on sustainability in construction. Reducing waste is an important contributor, and this is another area where modular containment can help.
The pre-assembly of cable management solutions is carried out to an exact specification, eliminating any waste on site. At RMS Cable Management, sustainability is enhanced through the use of advanced metal recycling facilities. These enable the company to reuse offcuts of materials in its other manufacturing processes. As well as reducing waste during production, this process provides a fixed carbon cost; the company knows exactly how the system has been manufactured and with what materials, and there is no risk of any cost variations as a result of increased waste or additional labour.
Is prefabrication right for your project?
Prefabrication can be beneficial for projects large or small, however, it must be implemented based on specific needs, including those of the project management team. For M&E installations, that is why it is important to engage with a specialist manufacturer of cable management systems in the early design stages.
Their expertise and knowledge will guide project teams on the most appropriate solution – whether that is using standard cable management products or systems manufactured off site.
Their input can also shape new solutions that add value to a scheme. For example, RMS Cable Management recently completed a project at a large distribution centre where modular containment had been specified. By working closely with the customer and defining their needs, the company created a prefabricated cassette module carrier with forklift entry points, enabling 13 modules to be stacked and transported to site. This provided a more efficient delivery method and reduced the risk of any damage with the design, ensuring each module could be safely unloaded.
There are many solutions available which can save costs, time, waste and labour
Partnering for success
The challenges faced by the construction sector will continue to affect the whole supply chain, including electrical contractors. Although there will always be a place for standard cable management solutions, considering a prefabricated modular solution can help electrical contractors to respond to these challenges and deliver significant efficiency, quality and sustainability benefits.
To make sure the solution ticks all the right boxes, partnering with a cable management specialist is a vital part of the process.