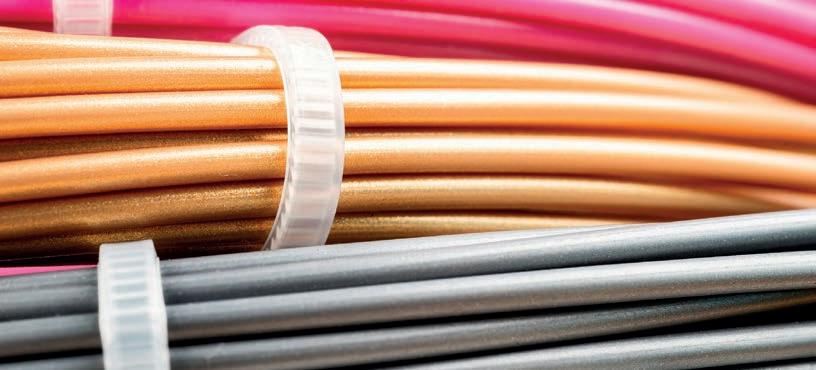
4 minute read
Key Issue
THE RISKS ASSOCIATED WITH POOR QUALITY CABLES
Matthew Nudd, area manager at ERF Electrical, discusses the various checks and procedures that those working in the electrical industry should carry out before cables are installed. He also outlines the importance of sourcing quality cable products and the potentially devastating risks non-compliant cables pose.
Advertisement
With dodgy appliances and wiring being the second most common cause of harmful faults and fires, it is crucial that those working in the electrical industry take all the precautions necessary when sourcing and installing cables. While manufacturers are the ones who produce the cables, electricians, wholesalers and contractors still have a responsibility to understand and recognise the standards cables should adhere to.
Although many people working in the electrical trade are often not involved in the original sourcing of products, it is crucial they are familiar with the safety standards and protocols related to the materials they buy and work with. Carrying out thorough checks on manufacturers and their products is therefore a must. Not only does this mean they’ll be in a better position to advise customers on the most suitable products for their needs, but they’ll also ensure the goods they are selling are fit for purpose and most importantly, safe.
This is particularly crucial when it comes to sourcing cables, as faulty appliances and wiring are known to be the second most common cause of dangerous faults and fires.
Thankfully, there are a few straightforward checks which can be carried out to ensure cables are safe and of good quality.
The first is ensuring the cable complies with the relevant British standard. As is well known by those working in the industry, British Standard (BS) cables are electrical cables which have been manufactured in accordance with specified requirements. This will mean the cable has been built and designed to mitigate common issues which may arise as a result of poor design.
On top of ensuring the cable meets the relevant British Standard, those involved in the sourcing of materials should make sure they are ordering from a reputable manufacturer. Although there will be times when orders need to be placed with new suppliers, a thorough background check on who the manufacturer is and what their reputation within the industry is like should be carried out. The easiest way to do this is to find out whether the cable has been approved by a third party such as the British Approvals Service for Cables (BASEC) or the Loss Prevention Certification Board (LPCB). This will mean the cable has undergone stringent testing and is compliant with the highest standards, including safety.
Manufacturers who are certified by these bodies have their products regularly tested to ensure they conform to safety standards all year round. The LPCB has been working with the industry for more than 100 years to help ensure fire and security products perform effectively. In order to ascertain LPCB certification, products have to meet stringent criteria – providing wholesalers, contractors and electricians with the confidence they are safe and will perform as required. All products that are certified by the LPCB are listed on RedBookLive.
Cables that are approved by BASEC will have the mark ‘BASEC’ printed on the outer sheath of the cable, making it easy to identify the ones which have undergone this thorough testing.
There are also some additional certifications people should look out for, including the Construction Product Regulation (CPR) rating – a mandatory requirement applying to all cable products in Europe – and the UKCA marking (replacing the CE marking), which should be included within the packaging labelling and DoP documentation.
Having explored some of the key checks those working in the electrical industry should carry out, it is important to also highlight the potential consequences of people not exercising this due diligence.
One of the most extreme and dangerous consequences of poor quality cabling is the increased risk of fire. Hotspots caused by damaged or small cables can lead to fires breaking out, resulting in damage to appliances and machinery – increasing the cost implications of any incidents. In more severe circumstances, poor quality cabling can also lead to fires spreading more quickly, with higher quantities of smoke, gas or heat being released, increasing the potential threat of the blaze.
While it is important to note that cables which comply with the strictest safety protocols cannot – by themselves – prevent a fire from breaking out, they can go a long way to reducing the risk and potential threat of a fire. Because of this, there can be little doubt of the importance of checking the quality and accreditations of cables. While the cost for a better quality cable is likely to be higher, it could be suggested those in the industry have a moral and ethical duty of care to ensure that the customer understands the risks involved of not using high-quality products as recommended.
Another consequence of using poor quality cables is that, due to the material they are made from, they are much harder to strip. Not only is spending additional time stripping the outer sheath of a wire a major inconvenience, it also adds extra hours onto a task – ultimately increasing the cost of the job.
As there are many parties involved in the designing, manufacturing, distribution and installation of cables, everyone in the industry has an important role to play in ensuring all cables are safe and fit for purpose. By carrying out detailed and thorough checks, people can not only establish greater trust from their customers but also improve the service they can offer to them. Failure to carry out these critical safety checks could have serious consequences.
There are a few straightforward checks which can be carried out to ensure cables are safe