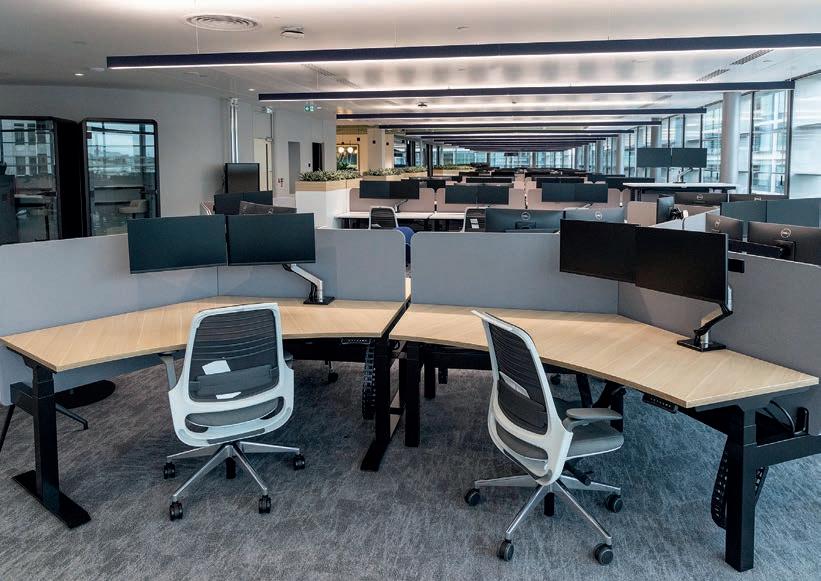
3 minute read
Wiring accessories – a clean bill of health
OFFICE UPGRADE BUILDS ON CMD’S POWERFUL LEGACY
A recent project delivered by London-based electrical contractor, Bancroft, using products from CMD, highlights the importance of selecting high quality products from a trusted manufacturer, along with choosing supply chain partners that can work proactively as an integral part of the delivery team.
Advertisement
A recent project delivered by Bancroft used products from CMD Located in the heart of the City, the project involved the refurbishment of a prestigious London office building for one of the world’s leading professional services firms. The client is based in offices spanning a total of 15 storeys across two towers and the initial plans for the refurbishment had focused on reconfiguration of the desk layouts to meet their revised requirements, along with upgrades to the interior fit out and finishes.
The client’s intention had been to retain the underfloor power distribution networks and focus the refurbishment on cosmetic upgrades to the office interiors, with Bancroft tasked with a light-touch electrical upgrade to include new lighting, kitchen areas and tea points, along with reconfiguration of power sockets for the new layouts.
Ryan Collis, Project Director at Bancroft, explains: “The previous electrical fit out of the building had been specified and installed with flexibility and futureproofing in mind, with a powertrack power distribution network, which offered scalability and adaptability. The legacy system was CMD’s AlphaTrak powertrack, which had been installed 20 years earlier, and, when we tested it, the CMD power distribution system was still fully functional and compliant after two decades of use.
“However, due to the publication of changes to wiring regulations since the previous installation, the existing tap-off leads could not be re-used as originally planned, due to a lack of mechanical protection. We turned to CMD to help us find a solution that would enable the AlphaTrak system to remain in place and be re-used, while updating the tap-offs to deliver a compliant installation.”
CMD’s AlphaTrak powertrack system has been discontinued and replaced by the company’s Betatrak powertrack system since the power distribution networks were installed in the two office towers. However, CMD was able to custom-design and manufacture 3000 new tap-offs for the new interior layout so that the electrical upgrade could go ahead within the original timescale, while re-using the AlphaTrak system and delivering a compliant installation.
Paul Allen, National Sales Manager (Power Distribution) at CMD comments: “Without compatible new tap-offs to make the power distribution network compliant with current wiring regulations, Bancroft would have needed to take out the powertrack on every floor and install a new system, which would have meant a huge additional cost in terms of products, programme length and project scope.
“We were able to adapt our compliant Betatrak tap-off technology to fit the 20-year-old AlphaTrak installation, thereby minimising the impact on costs and programme delivery. And, because we manufacture in-house in the UK, we were also able to fast-track the order, helping Bancroft to keep the project on track.”
Joined-up supply
Alongside the new tap-offs, CMD also supplied new grommets, cleaner’s hives, lighting hives and the company’s fast-fit 20 Series floor boxes, which provide ease of access to power sockets and data.
CMD also supplied the Rotasoc modular workstation power system for the project, which was configured to accommodate the sit/stand desks specified for the new office environment. A 2-gang Rotasoc module with RCD protection was specified for the lower tray of each workstation, with a two metre connector lead to a 4-gang Rotasoc module on the upper tray. In this way, the lower tray module provides RCD protection for the entire workstation, and desk height can be adjusted easily to meet the needs of each user, without any restriction.
As many of the occupier’s team are still working from home, Bancroft has been able to carry out the installation in two phases. All office-based staff were relocated to a single tower to provide vacant possession of the other tower for refurbishment, and then decanted across while the second tower is completed.
Ryan adds: “We completed the west tower by the end of 2021 and are now working on the east tower. Close collaboration with CMD means that we have been able to call down the products we need for each phase in real time as the project progresses. CMD has aligned their manufacturing schedules for the custom-manufactured tap-offs to our programme requirements, which has helped us schedule work aligned to the client’s expectations.”
The project involved the refurbishment of a prestigious London office building