
4 minute read
Key Issue
from ECN January 2021
ELECTRICAL SAFETY COMES FIRST AS BUSINESSES FIGHT TO STAY OPEN
As businesses continue to welcome back customers following forced coronavirus shutdowns, many are juggling a long list of challenges and conflicting priorities. But one focus that can’t be ignored is the need for duty holders to revisit electrical compliance and safety.
Advertisement
With the majority of sites open again, duty holders should pay particular attention to their compliance To help firms in their quest to remain compliant as they fight to stay open, Michael Kenyon, Technical Lead at Bureau Veritas, explores the key obligations for duty holders, from electrical compliance strategies to gap analyses.
It’s been a year like no other for all industries, with forced shutdowns due to the COVID-19 pandemic placing unprecedented pressure on organisations. Even with the go-ahead to reopen, owners and operators across different sectors are faced with a host of obligations, from social distancing and hygiene, to implementing track and trace systems. All this whilst the threat of re-closures looms in the event of further outbreaks.
There were, of course, many consequences of premises closing during the national lockdown period, including the postponement of statutory compliance inspections where sites were left vacant. Some duty holders were unable to keep up to date with inspections and testing through the challenging times, but compliance is still statutory – even in a pandemic.
In the case of electrical safety, organisations have a duty of care to ensure that electrical equipment is maintained in a safe condition; periodic inspection and testing remains a key part of that, as detailed in the Electricity at Work Regulations Reg 4 (EAWR).
Now, with the majority of sites open again, duty holders should pay particular attention to their compliance. This means working with inspection partners to put together a robust plan to manage risk and return to compliant status as soon as practicably possible.
Owners and operators are faced with a host of obligations, from social distancing to implementing track and trace
The importance of electrical safety All businesses have a duty of care to employees to ensure that working environments and equipment are safe. Testing of electrical appliances, emergency lighting along escape routes and ongoing management of distribution boards and control panels are just a few of the routine inspection and maintenance requirements in order to be fully compliant with the EAWR and BS7671 (18th Edition wiring regulations).
Of course, different organisations have vastly different requirements. Some have an in-house capability for periodic inspection and testing works and need only an external audit, while other businesses need a fully bespoke electrical management scheme. However, all duty holders have an obligation to comply with the requirements of the regulations, which apply to all places of work.
Coming out of lockdown It was inevitable as businesses reopened that there would be increased demand for testing and inspection services, and we are seeing the result of this spike now.
In some cases, where skeleton staff remained on site, the Bureau Veritas team was able to complete inspections during closures, which provides a better environment to do full testing with minimum disruption to the business. Even now, with businesses open again but perhaps not operating to full capacity, it remains an ideal time to discharge your duty of care and ensure the safety of staff, customers and visitors.
Dead testing, for example, is more disruptive as it requires isolating supplies. However, the good news given the lower occupancy of many buildings, is that this presents the opportunity to do more dead testing as it is currently a safer and more comprehensive way of testing for many customers. In fact, this means that Bureau Veritas can dead test equipment that it would not otherwise have been able to isolate due to operational demands.
Kenyon’s advice for all duty holders throughout the pandemic has been to continue with inspections and testing as usual wherever possible, because it remains the most effective way to meet your obligations. However, the most important thing is that you must be confident that there is no subsequent risk to employees or customers if you did not have the opportunity to complete inspections by the time of reopening.
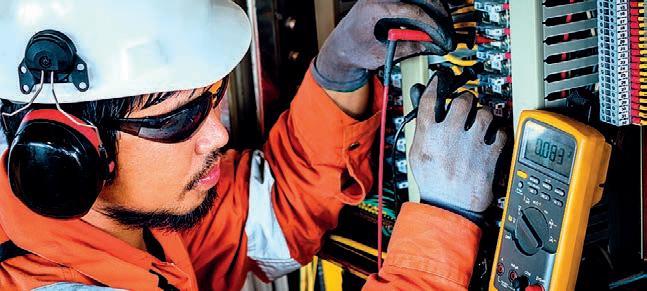
Taking steps to maintain compliance Ultimately, electrical compliance – and the strategy behind it – needs to be realistic, reasonable and achievable. It was inevitable that some inspections would be postponed during the unprecedented COVID-19 shutdowns, but if your compliance strategy has been affected, then there needs to be a gap analysis, which is a documented assessment, in order to get back on track.
As part of this, duty holders must identify how they are going to catch up with compliance and if an incident occurs, then you will have to explain this strategy to the Health & Safety Executive (HSE). It may be that a new, revised strategy is required.
If some equipment hasn’t been tested within specified periods, then you have to set out in writing how it will be. A good testing and inspection partner will be able to offer impartial advice on how to achieve that.