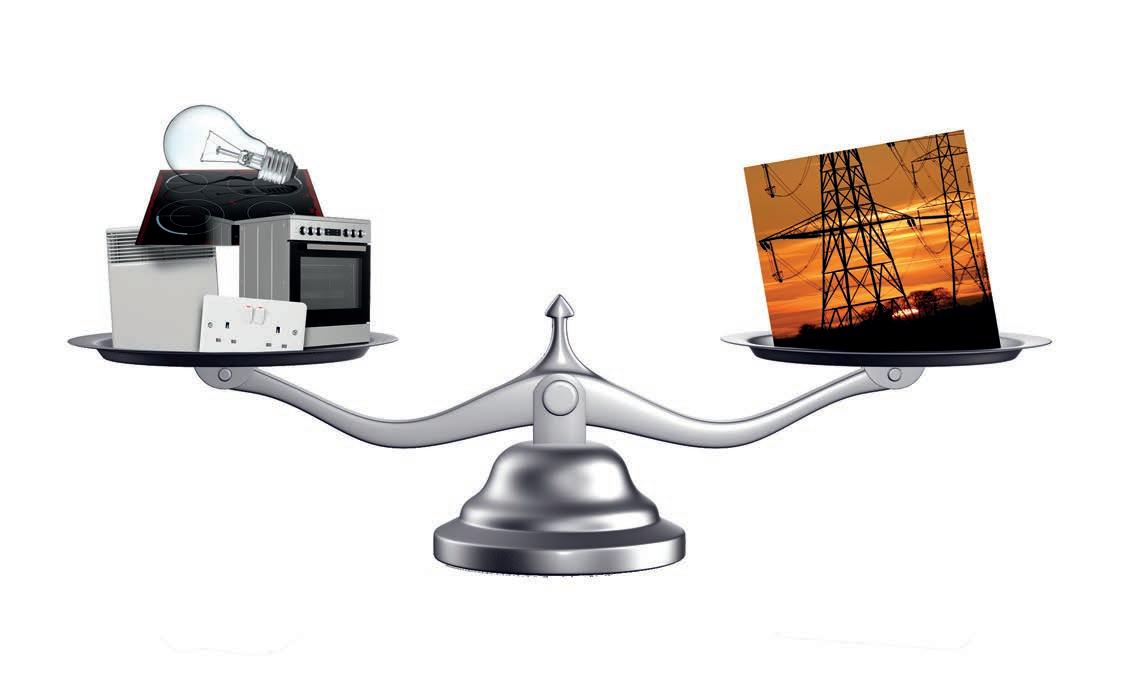
4 minute read
Advertisement Feature
from ECN January 2021
THE BALANCE OF POWER
Prefect Controls takes a look at the confusion regarding the timescale to phase out fossil fuel fired boilers, and the benefits of new technologies and cleaner, greener energy.
Advertisement
There appears to be some confusion as to what the UK Government’s position is on the phasing out of fossil fuel fired boilers. The Clean Growth Strategy launched in 2017 proposed plans to stop the installation of oil or coal heating systems from the mid 2020s where gas isn’t available, and to improve standards on the 1.2 million new boilers installed every year in England.
Philip Hammond, then Chancellor, announced in his spring statement of that year, “We will introduce a Future Homes Standard, mandating the end of fossil-fuel heating systems in all new houses from 2025.” He may have been quoting the Committee for Climate Change which recommended that new homes and commercial premises from 2025 should not be connected to the gas network, and that by 2035 installation of gas boilers be phased out. The committee also recommended that the government concentrates on several other issues including low carbon retrofits, energy networks and green infrastructure.
However, there is no reference to a fossil fuel ban in the Government’s own summary of the spring statement. Instead, there is a commitment to, “future-proofing new-build homes with low carbon heating and world leading levels of energy efficiency”. At the time of writing, mid-December 2020, a further news release announced a ‘mix up’ when 2023 as a pledge to ban gas boilers from new homes from Boris Johnson was withdrawn from the Downing Street website.
The smart use of energy control provides efficiencies that are far beyond simply using less, but by balancing the demand to ensure supply is used effectively
So, since 2012 the timescale quoted has ranged from 2023, through 2035, right up to 2050 when the UK is committed to bringing all greenhouse gas emissions to net zero!
Whatever the timescales, it can be assumed that any such heating policy will also be applied to commercial buildings such as the UK student accommodation estate, which currently comprises over 660,000 rooms.
The largest single source of carbon emissions, responsible for more than one-third of the total, is space heating. Although student accommodation is only a relatively small number, compared with 29 million homes, owners and providers should begin planning the transformation of their old stock by switching from fossil fuelled boilers towards low carbon heating sources. This will help with decarbonisation and, as importantly, maximise their effective use of energy.
One of the hurdles that such upgrades will face is electricity supply. Accommodation that was built in the 70s and 80s with a reliance on fossil fuels for heating will have an electricity supply that, at the time, was adequate for powering the lights, kitchen equipment and power sockets. But roll on 30-40 years, and the cost of upgrading the supply to run a fully electrical heating system could prove inhibitive.
The benefits of new technologies and cleaner, greener energy make controllable electric heating systems more attractive than on/off wet systems. But the additional electrical load this will place on supply must be a consideration that is taken seriously before a refit is given the green light.
Estimating the maximum demand for electricity in a building is an important calculation from both an operational and an energy efficiency perspective. This is a particular issue if a building is being re-purposed or major renovations are afoot.
Heat loss calculations will indicate the size of heaters required for each zone, but what if this adds up to a greater draw than the building’s electricity supply can manage?
A second consideration is procurement. Organisations that are big consumers of electricity will negotiate their tariff directly with their energy provider. Estimating their usage is a balancing act – if they estimate too much they will be paying for unused capacity, too little and they face penalties for going over the agreed limits – in much the same way one predicts annual mileage when negotiating the monthly payments on a new car. Metering will provide the total consumption of power but, it is a blunt instrument when it comes to calculating the ebb and flow of demand.
Prefect Controls has overcome this conundrum with software it has developed and integrated with Irus – its central control heating system designed specifically for student accommodation.
It is unlikely that all electrical equipment, i.e. heaters, cookers, lights etc., will be in use simultaneously. However, Irus steps in if demand rises unusually. Irus is able to use line metering data to calculate the total demand for the site. Nodes connected to each panel heater and water tank communicate with the central control unit. Energy managers access data through the web-based portal and they can adjust parameters accordingly. This provides complete control over room temperatures and water heating. Irus will automatically lower power input to non-essential heaters, such as those in corridors or stairwells and water tanks – or switch them off completely if the pre-set maximum demand limit is being reached.
This technology means sites that previously were unsuitable for electric heating can now benefit from the efficiencies of appropriately sized panel heaters without the need for huge investment in a power supply upgrade.
Data can be collected and stored within the system, from which reports can be run to provide clear indicators of demand patterns. Procurement teams can use this intelligence to make informed decisions and more accurate projections of real energy use when it comes to negotiating tariffs with energy providers.
Once again, this proves that smart use of energy control provides efficiencies that are far beyond simply using less, but by balancing the demand to ensure supply is used effectively.
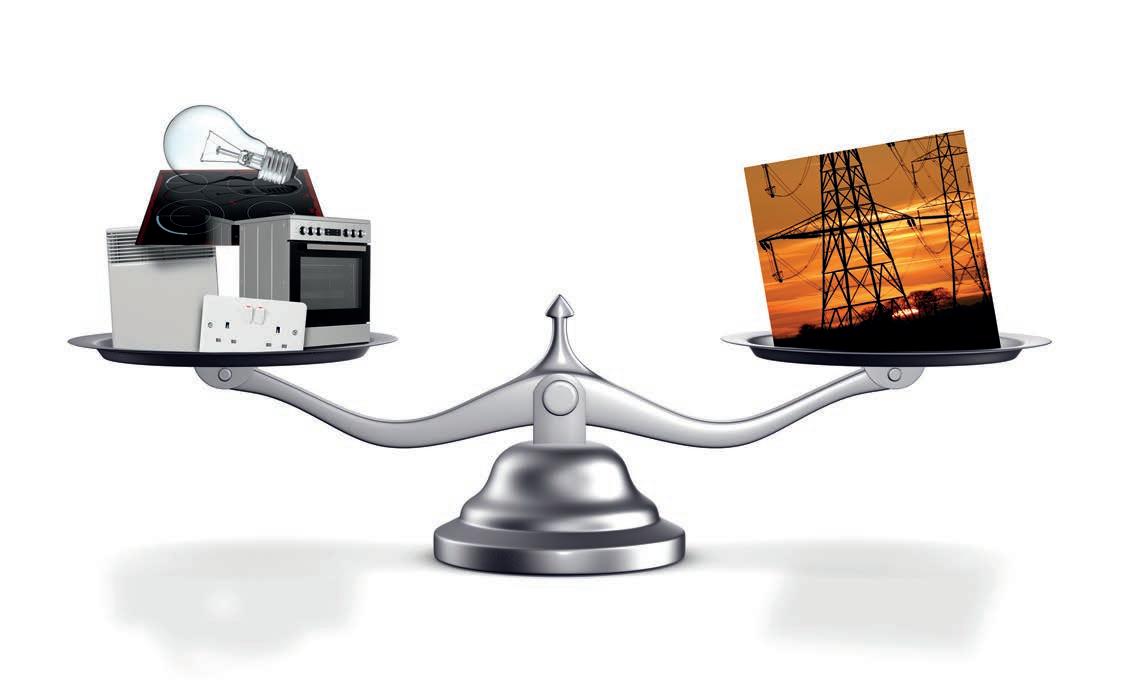