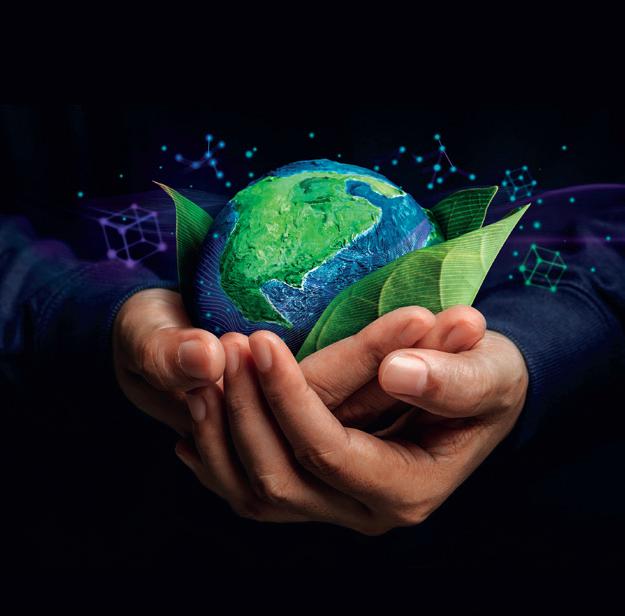
4 minute read
Heavy industries must help themselves to help the planet, and sustainable switchgear is the solution
from ECN May 2022
At least 30% of today’s energy-related emissions could be removed with existing decarbonisation technologies by 2030 – but this is not happening anywhere near as fast as it should. It’s like a patient who delays being treated for their condition until a complete cure is available, says David Hall, VP Power Systems UK & Ireland, Schneider Electric.
The behind-the-scenes power systems infrastructure in industrial facilities, such as low voltage (LV) and medium voltage (MV) switchgear, are fundamental for keeping data flowing across connected systems. They support essential operations and information technology needed to maintain production. As the world becomes increasingly electric, there needs to be a shift towards installing greener, more reliable, and more efficient switchgear.
Advertisement
While some technologies are still in development or need improvement to be implemented at scale and significantly impact climate change, a considerable amount of technology already exists. There is no need to wait – and no time to waste –to put switchgear on its way to helping meet the 2050’s net zero targets. Below, David takes you through the key ways to make a difference and generate the most significant ROI from your switchgear strategy.
SF6: the unintended consequences
Since the mid-20th century, sulphur hexafluoride (SF6) has been widely used to replace oil in electrical equipment insulators. One of its most significant uses is in electrical switchgear. However, while SF6 has proven to be reliable and highly effective in applications where arcing can be expected, it is also the most potent greenhouse gas (GHG) in terms of its global warming potential (GWP). Lurking inside the electrical system, if it escapes, it can remain in the earth’s atmosphere for thousands of years, undoing efforts to tackle climate change.
Until recently, there were no alternatives to SF6, but innovation and regulation are now coming together to help limit its release into the atmosphere. Regulatory activities concerning SF6 use have continued to grow in recent years, centred primarily in California, China and the European Union (EU). Careful accounting of the production and distribution of SF6 and, most recently, new EU regulations to ban the use of F-gases in many new types of equipment where less harmful alternatives are widely available, are making the direction of travel clear. Here in the UK, we keep a keen eye on its progress towards tighter regulation.
Today’s circular economy is the alternative to the ‘take, make and dispose’ industrial model of the past
SF6 alternative – a breath of fresh air
In the past, regulations have mostly granted exemptions for the continued use of SF6 in high- and medium-voltage switchgear because alternative technologies did not exist.
But manufacturers such as Schneider Electric have been thinking long-term to develop more sustainable alternatives to SF6-based technology, and several now offer new approaches to switchgear design, operation, and maintenance.
The new technologies differ from one manufacturer to another, with some choosing to focus on reducing GWP with the help of alternative gases. Many equipment manufacturers have elected to avoid the uncertainties surrounding new and unproven alternative gases and instead use pure air for this green transition. Pure air-based technologies offer all the benefits of F-gas based switchgear equipment but are a superior choice for the environment and operational safety, where there can no longer be room for compromise. In addition to being safe for people and the planet, this air-based approach reduces future regulatory risk. After that, huge improvements can also be seen in ease-of-maintenance, end-of-life treatment, functionality, and performance.
A shift in mindset
Today’s circular economy is the alternative to the ‘take, make and dispose’ industrial model of the past. It has redefined products and services while minimising waste and saving money.
The concept of reusing, refurbishing, recycling, renewing and retrofitting also applies to electrical distribution equipment. To minimise waste, switchboards and accessories can be reused, and obsolete components can be refurbished, repaired, or recycled. As such, the lifecycle of operational equipment is prolonged, and less money is spent.
By refurbishing legacy equipment with modern technologies, IoT can be used to address some of the companies’ most significant pain points and unlock a new source of data on their equipment’s performance. Data can be collected and analysed remotely using sensors embedded in assets to determine how to optimise performance, prevent problems, maximise equipment’s lifespan, and create more resilient and energy efficient operations. For instance, switchgear humidity or partial discharge sensors gather intelligence used to identify and predict potential problems before they become serious. This knowledge reduces maintenance costs by enabling companies to anticipate equipment failure, determine an optimal repair timeline and ultimately help to reduce carbon emissions.
Energy-intensive businesses and industries have a huge responsibility to move forward with decarbonising their production processes with new technology and a modern approach. The result will be a significant reduction in greenhouse gas emissions and, ultimately, an operational boost which is too big an opportunity to miss. The UK’s manufacturing output is stagnating compared to its global counterparts, owing mainly to the legacy equipment that much of the industry still relies on. This represents a huge opportunity to retrofit the UK’s electrical equipment and unleash the full potential of the industrial sector.
Schneider Electric, se.com
Tailored Solutions from Hager
If your enquiry falls out of the standard offer, Tailored Solutions can meet your requirements.
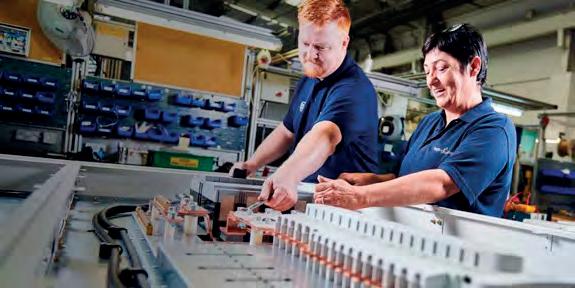