
4 minute read
Continuous thermal monitoring is revolutionising electrical fire protection
Organisations such as the European Fire Academy (EFA) and property and insurance companies that track building damages declared that 25% of building fires are electrical in origin, often due to defects in medium or low voltage system wiring. Worryingly, a quarter of these potentially devastating fires are due to loose or faulty connections. As such, identifying and remedying such potentially dangerous faults requires systematic monitoring. Regulatory bodies have set strict standards for thermal surveys, now a core responsibility for facility owners and managers, writes Stewart Gregory, VP of Power Products at Schneider Electric.
These surveys have traditionally relied on scheduled infrared (IR) thermography inspections, where a thermal camera is used by an operative to inspect the highest-risk areas of electrical equipment. IR thermography can be highly effective when conducted in compliance with regulations. However, it is far from a fail-safe option.
Advertisement
Now, a new method of continuous thermal monitoring offers a safer, more effective way to detect thermal risks 24 hours a day. So, how can fire protection professionals, facility owners and managers harness the latest technology to identify electrical fire risks and minimise their threats?
Continuous thermal monitoring uses internet of things (IoT) sensor technology to provide 24/7 insights. One application is the fitting of small, wireless thermal sensors permanently installed on important points throughout the electrical distribution system. Their wireless design simplifies installation, especially in retrofit scenarios. This delivers continuous monitoring of equipment temperatures across a range of infrastructure, from medium voltage/low voltage (MV/LV) switchgear and transformers to LV busways.
For higher-density connections, Insulation Decomposition Detection (IDD) technology offers an effective solution by detecting cable thermal decomposition in a range of temperatures, providing early warning of an imminent risk of fire. IDD offers a simple and reliable way to proactively detect cable connection issues for most LV cable types on the market. Additionally, some IDDs may offer additional capabilities, such as humidity monitoring to further enhance prevention capabilities. Perhaps the most obvious downside of traditional periodic monitoring is that it leaves time between scheduled inspections for systems to deteriorate and faults to become a potential threat, with IR thermography usually conducted every six-24 months.
A key benefit of continuous thermal monitoring is always-on monitoring, alongside near real-time alarming. Where thermal monitoring systems include automated alert capabilities, operations and maintenance teams are immediately alerted to issues, providing greater opportunities to rectify the situation quickly. Wireless connectivity enables 24/7 continuous thermal monitoring, with sensors forming a complete, facility-wide thermal monitoring network. Data from this connected network is easily accessible and continuously available to teams via cloud-based analytic applications, enabling rapid reporting and action.
For example, if a sensor reading shows an abnormal temperature rise at any connection point or in the insulation of any cable, this will generate an automated alert, sending a mobile notification to maintenance teams. The provision of long-term trending thermal data can also help personnel detect slow deterioration, addressing issues before they cause a problem. Bringing together IoT data, analytics, and alert systems in the cloud ensures the swift detection of issues before they lead to equipment failure, major financial losses or worse, loss of human life.
The benefits extend far beyond the continuous delivery of crucial data. It is also important to address the safety of professionals charged with conducting standard IR thermography inspections. Such tests are necessarily performed close to live electrical equipment, and this puts personnel at risk.
IR thermography usually requires an IR window installed in the switchgear door to provide camera access for testing live equipment. For LV equipment, the operator must often open door panels to check connections. Limited accessibility and visibility make it challenging to position the camera correctly, further increasing safety concerns for testing switchgear and transformers. Technicians run the risk of being exposed to an arc flash, which can be a danger to life.
Finally, it is not just safety where this new approach can deliver returns. Improving reliability and uptime, a thermal monitoring system identifies thermal issues faster than typical IR scanning intervals, thanks to its real-time data collection. It also provides higher accuracy, whilst near real-time alarms enable service teams to respond quickly to risks before downtime and damage occur. All these benefits add up to substantial cost savings and increased uptime.
Over the typical 20-year lifetime of most switchgear, continuous thermal monitoring is estimated to be two and a half times more cost-effective than IR thermography. Research by Schneider Electric also suggests that continuous thermal monitoring delivers up to a 10:1 return on investment due to avoided equipment damage and downtime.
While this new approach offers a host of benefits, it is still the case that in some jurisdictions, traditional IR scanning is still required by codes and standards. That does not mean that continuous thermal monitoring should be ignored. It should be seen as an overarching strategy complemented by IR scanning, delivering the kind of insights that provide proactive, safe, and cost-effective fire prevention across the board.

Schneider Electric, se.com
SMART SECURITY PRODUCTS
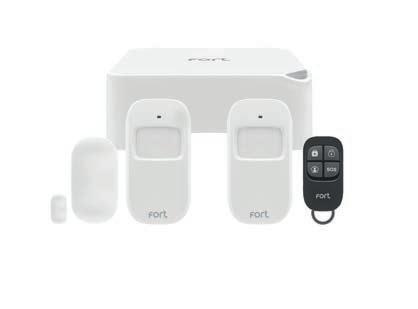
Every device can be controlled from anywhere using the Click Smart+ app.
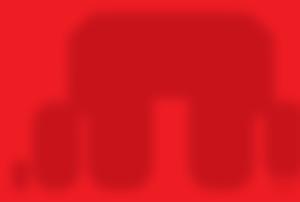
POWERED BY CLICK SMART+